The Role of Robotics in Streamlining the Logistics Industry is exploding! Forget slow, manual processes; we’re talking automated warehouses humming with efficiency. From the early days of clunky robotic arms to today’s AI-powered autonomous vehicles, the transformation is mind-blowing. This isn’t just about faster delivery; it’s a complete overhaul of how goods move around the globe, driven by the need for speed, accuracy, and cost-cutting in a fiercely competitive market. This deep dive explores the robots revolutionizing logistics, the challenges they face, and the incredible future they promise.
This article will dissect the various types of robots employed – think agile AMRs zipping around warehouses, powerful robotic arms meticulously picking and packing, and tireless AGVs transporting goods. We’ll analyze their impact on warehouse efficiency, cost reduction, and worker productivity, addressing concerns about job displacement and the skills gap. Get ready for a look at real-world success stories and a glimpse into a future where logistics is completely redefined by advanced robotics and AI.
The Expanding Role of Robotics in Logistics: The Role Of Robotics In Streamlining The Logistics Industry
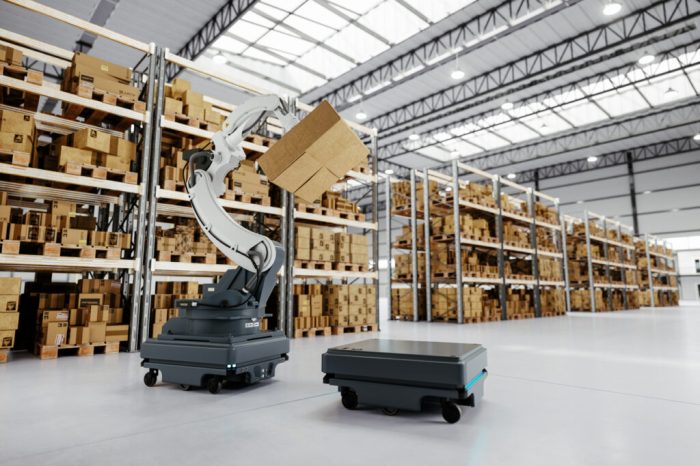
Source: distrelec.com
The logistics industry, a complex network of warehousing, transportation, and delivery, has undergone a dramatic transformation in recent years. This shift is largely driven by the increasing adoption of robotics, automating tasks previously handled manually and significantly improving efficiency and speed. While the integration of automated systems isn’t entirely new, the recent advancements and cost-effectiveness have propelled robotics into a central role in modern logistics.
The early days of robotics in logistics saw the introduction of simple automated guided vehicles (AGVs) in warehouses, primarily for material handling. These early robots followed pre-programmed paths, lacking the sophisticated navigation and adaptability of their modern counterparts. However, these initial forays laid the groundwork for the widespread adoption we see today.
Current State of Robotic Adoption in Logistics
Robotics are now prevalent across various sectors within the logistics industry. Warehouses utilize robots for picking, packing, and sorting, significantly accelerating order fulfillment. Automated guided vehicles (AGVs) and autonomous mobile robots (AMRs) navigate warehouse floors autonomously, transporting goods between different stations. In transportation, autonomous trucks are undergoing testing and limited deployment, promising to revolutionize long-haul trucking and delivery. Even last-mile delivery is seeing robotic solutions, with drones and autonomous delivery robots being explored for faster and more efficient delivery of packages to consumers. The level of adoption varies based on factors such as the size and type of operation, technological readiness, and return on investment. Large e-commerce companies, for example, are leading the charge in robotic integration, while smaller businesses may still rely heavily on manual processes.
Key Drivers of Increased Robotics Use in Logistics
Several factors contribute to the growing integration of robotics in the logistics industry. The rising demand for faster and more efficient delivery, fueled by the growth of e-commerce, is a major catalyst. Consumers expect quick and reliable delivery, putting pressure on logistics companies to optimize their operations. Simultaneously, labor shortages and increasing labor costs are driving the need for automation. Robots can work continuously without breaks, reducing reliance on human workers and mitigating the challenges of finding and retaining staff. Technological advancements, particularly in areas such as artificial intelligence (AI), computer vision, and sensor technology, have made robots more sophisticated, reliable, and cost-effective. Improved navigation systems, advanced grasping mechanisms, and enhanced AI capabilities enable robots to handle a wider range of tasks with greater precision and speed. Furthermore, the decreasing cost of robotic systems makes them increasingly accessible to businesses of all sizes, accelerating their widespread adoption. For example, the cost of industrial robots has fallen significantly over the past decade, making them a viable investment for many logistics companies.
Types of Robots Used in Logistics
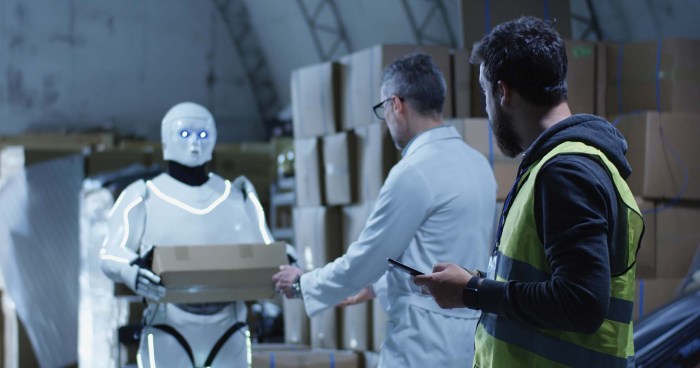
Source: airfreight-logistics.com
The logistics industry is undergoing a massive transformation, driven largely by the increasing adoption of robotics. From sprawling warehouses to bustling distribution centers, robots are streamlining operations and boosting efficiency. But what types of robots are actually making this happen? Let’s delve into the diverse robotic workforce reshaping the logistics landscape.
Several key robotic systems are revolutionizing warehousing and fulfillment. Each possesses unique capabilities and limitations, making them suitable for specific tasks within the complex logistics chain. Understanding these differences is crucial for businesses looking to optimize their operations with automation.
Automated Guided Vehicles (AGVs), The Role of Robotics in Streamlining the Logistics Industry
AGVs are perhaps the most familiar type of robot in logistics. These vehicles follow pre-programmed paths, often using magnetic tape, wires embedded in the floor, or laser guidance systems. They are typically used for transporting materials within a warehouse or factory. Think of them as the reliable workhorses of the robotic fleet, consistently moving pallets or other large loads from point A to point B. While their programming limits flexibility, their dependability and capacity for heavy lifting make them invaluable.
Autonomous Mobile Robots (AMRs)
Unlike AGVs, AMRs navigate dynamically using advanced sensors and AI. They can avoid obstacles, adapt to changing environments, and reroute themselves as needed, offering greater flexibility and efficiency than their guided counterparts. AMRs are commonly used for tasks like picking and delivering items within a warehouse, often interacting directly with human workers. Their adaptability allows for seamless integration into dynamic workflows, but their sophisticated technology comes with a higher initial investment.
Robotic Arms
Robotic arms, or manipulators, are incredibly versatile. These multi-jointed arms, often equipped with grippers or other end-effectors, perform a wide range of tasks, from picking and packing individual items to palletizing and sorting. They are frequently integrated into automated workstations, performing repetitive tasks with speed and precision far exceeding human capabilities. While highly efficient for specific tasks, their implementation requires careful integration and programming, and they are generally less mobile than AGVs or AMRs.
Robotics are revolutionizing logistics, boosting efficiency with automated sorting and delivery. This rise in automated systems is intrinsically linked to the expanding network of connected devices, a growth fueled by advancements like 5G, as detailed in this insightful article: The Future of 5G in Supporting the Growth of IoT Devices. Ultimately, the seamless communication enabled by 5G is crucial for the real-time data flow that powers these robotic systems, making logistics faster and more reliable.
Comparison of Robotic Systems in Logistics
The choice of robotic system depends heavily on the specific needs of the operation. Let’s compare the strengths and weaknesses of each type:
Robot Type | Application | Advantages | Disadvantages |
---|---|---|---|
Automated Guided Vehicles (AGVs) | Material transport along fixed routes | High payload capacity, reliable, cost-effective (relatively) | Limited flexibility, inflexible routing, requires infrastructure modifications |
Autonomous Mobile Robots (AMRs) | Dynamic material handling, picking and delivery | Flexible routing, obstacle avoidance, adaptable to changing environments | Higher initial cost, requires sophisticated software and sensors |
Robotic Arms | Picking, packing, palletizing, sorting | High speed and precision, increased throughput, reduces human error | Limited mobility, requires careful integration, programming expertise needed |
Applications of Robotics in Warehousing and Distribution
The warehousing and distribution sector is undergoing a massive transformation, driven by the relentless pursuit of efficiency and speed. Robotics are no longer a futuristic fantasy; they’re the backbone of modern logistics, automating tasks once considered the sole domain of human workers. This automation is significantly impacting picking, packing, sorting, receiving, shipping, and inventory management, leading to substantial improvements in productivity and cost reduction.
Robotic systems are revolutionizing the way warehouses and distribution centers operate, increasing throughput, minimizing errors, and optimizing resource allocation. This section delves into specific examples of robotic applications within these crucial aspects of the logistics chain.
Robotic Automation in Picking, Packing, and Sorting Operations
Automated picking, packing, and sorting are among the most visible applications of robotics in warehousing. Robots are deployed to handle a wide variety of tasks, from identifying and retrieving items from shelves to packaging them for shipment and sorting them according to destination. For example, collaborative robots (cobots) work alongside human employees, assisting with picking and placing items into boxes, significantly reducing the physical strain on human workers. Advanced vision systems guide these robots, enabling them to identify and grasp items of varying shapes and sizes with impressive accuracy. Automated guided vehicles (AGVs) and autonomous mobile robots (AMRs) transport goods between different areas of the warehouse, streamlining the flow of materials and eliminating bottlenecks. High-speed sorters use advanced sensors and robotic arms to sort packages based on their destination, zip code, or other criteria, significantly increasing sorting efficiency compared to manual processes. Consider Amazon’s extensive use of robotic systems in its fulfillment centers; these robots manage millions of items daily, showcasing the transformative potential of this technology.
Improved Efficiency in Receiving and Shipping Processes
Robotics play a crucial role in optimizing both the receiving and shipping processes. In receiving, robots can automate tasks such as unloading trucks, scanning barcodes, and verifying the quantity and condition of incoming goods. This reduces the time and labor required for receiving operations, allowing for faster processing of shipments. Similarly, in the shipping process, robots can automate the loading of outgoing shipments onto trucks or conveyor belts, ensuring efficient and timely delivery. For example, robotic palletizers can automatically stack and wrap pallets, significantly reducing the risk of injury and improving the overall efficiency of the shipping process. The implementation of these robotic systems minimizes human error, resulting in fewer shipping delays and improved customer satisfaction.
Robotics in Inventory Management and Order Fulfillment
Effective inventory management and order fulfillment are paramount to efficient warehouse operations. Robotics contribute significantly to both. Automated inventory systems, often integrated with robots, provide real-time tracking of inventory levels, enabling precise forecasting and optimized stock management. Robots can automatically scan and update inventory levels, eliminating manual data entry and reducing the potential for errors. Furthermore, robotic systems directly support order fulfillment by automating the picking and packing of orders. Automated storage and retrieval systems (AS/RS) are a prime example; these systems use robots to retrieve items from high-density storage locations, significantly increasing storage capacity and improving order fulfillment speed. This allows for faster processing of customer orders, leading to improved order accuracy and customer satisfaction. The combination of these systems ensures efficient inventory management, faster order fulfillment, and improved overall warehouse efficiency.
Impact on Efficiency and Productivity
The integration of robotics into logistics has dramatically reshaped the industry’s operational landscape, significantly boosting efficiency and productivity. This isn’t just about replacing human workers; it’s about optimizing processes, minimizing errors, and ultimately, delivering goods faster and cheaper. The impact is multifaceted, affecting everything from warehouse throughput to the bottom line.
Robotics reduces operational costs in logistics through several key mechanisms. Firstly, robots automate repetitive, labor-intensive tasks, reducing the need for a large human workforce and the associated costs like wages, benefits, and training. Secondly, they minimize errors, reducing waste from damaged goods, incorrect shipments, and inefficient storage. This translates directly into cost savings on materials, labor for rework, and customer service issues. Finally, the increased speed and accuracy offered by robotics lead to faster order fulfillment, reducing storage costs and improving inventory management. For example, Amazon’s extensive use of robotics in its fulfillment centers has demonstrably lowered its operational costs per unit shipped, allowing it to maintain competitive pricing.
Cost Reduction Through Automation
Automating tasks like picking, packing, and sorting significantly reduces labor costs. Consider a warehouse that previously relied on manual order picking. Implementing robotic picking systems can decrease the number of human pickers needed, resulting in substantial savings on wages, benefits, and associated overhead. Furthermore, robots work around the clock, eliminating the need for multiple shifts and overtime pay, further contributing to cost reduction. The reduction in human error also minimizes the costs associated with damaged goods, returns, and customer service issues. A well-implemented robotic system can lead to a measurable decrease in operational expenditure, freeing up capital for reinvestment and growth.
Improved Speed and Accuracy
Robotics significantly enhances the speed and accuracy of logistics operations. Automated guided vehicles (AGVs) can navigate warehouses much faster than human workers, transporting goods efficiently and without delays. Robotic arms equipped with advanced vision systems can pick and pack items with incredible precision, minimizing errors and improving order accuracy. For instance, a study by the Material Handling Institute found that robotic systems can improve order fulfillment speed by up to 50% and reduce error rates by up to 90%. This translates to faster delivery times, increased customer satisfaction, and a significant competitive advantage.
Positive Effects on Warehouse Throughput and Worker Productivity
The implementation of robotics in logistics has a demonstrably positive effect on warehouse throughput and worker productivity.
- Increased Throughput: Robots can handle a higher volume of tasks in a given timeframe compared to human workers, leading to a significant increase in warehouse throughput. This allows companies to process more orders and handle higher demand without expanding their physical facilities or workforce.
- Improved Worker Productivity: By automating repetitive and physically demanding tasks, robots free up human workers to focus on more complex and value-added activities, such as quality control, inventory management, and customer service. This boosts worker morale and overall productivity.
- Enhanced Safety: Robots can handle hazardous or physically demanding tasks, reducing the risk of workplace injuries to human employees. This leads to a safer work environment and lower workers’ compensation costs.
- Better Space Utilization: Automated storage and retrieval systems (AS/RS) using robots can optimize warehouse space utilization, allowing for more efficient storage and retrieval of goods. This can lead to reduced storage costs and improved overall warehouse efficiency.
Challenges and Limitations of Robotic Implementation
The rosy picture of fully automated warehouses humming with robots might seem a bit too futuristic. While robotics offers incredible potential for streamlining logistics, several significant hurdles stand in the way of widespread adoption. These challenges aren’t insurmountable, but understanding them is crucial for realistic planning and successful implementation. Ignoring these obstacles could lead to costly mistakes and ultimately hinder the benefits of automation.
The high initial investment cost is a major barrier to entry for many companies, especially smaller businesses. Integrating robotic systems into existing infrastructure also presents a complex challenge, requiring significant adjustments to workflows and potentially substantial modifications to physical spaces. Furthermore, ongoing maintenance and repair costs can be unexpectedly high, requiring specialized expertise and potentially leading to unplanned downtime.
High Initial Investment Costs and Return on Investment (ROI)
The price tag for implementing robotic systems in logistics can be substantial. This includes not only the cost of purchasing the robots themselves but also the expenses associated with software, integration, training, and ongoing maintenance. For smaller businesses or those with limited budgets, this significant upfront investment can be a major deterrent. A careful cost-benefit analysis, including a realistic projection of ROI, is essential to justify the expense. For example, a small warehouse might find that the ROI on a fleet of automated guided vehicles (AGVs) is several years out, making the initial investment difficult to justify compared to less expensive, manual processes. Larger companies with greater capital reserves and higher throughput may find the ROI more attractive.
Integration Challenges and Compatibility Issues
Integrating robotic systems into existing warehouse management systems (WMS) and other operational technologies can be incredibly complex. Robots often require specialized software and interfaces, and ensuring seamless communication between different systems is critical for efficient operation. Compatibility issues between different robotic systems from various manufacturers can also create significant headaches. For instance, integrating a new robotic arm from one supplier into a system already using AGVs from another supplier might require extensive custom programming and potentially expensive middleware solutions. This integration complexity can lead to delays, increased costs, and potential disruptions to operations.
Maintenance, Repair, and Skilled Labor Requirements
Robotic systems are sophisticated pieces of machinery that require regular maintenance and occasional repairs. This necessitates a skilled workforce capable of troubleshooting problems, performing preventative maintenance, and carrying out repairs. Finding and retaining technicians with the necessary expertise can be challenging, particularly in regions with limited access to specialized training programs. Furthermore, unplanned downtime due to malfunctioning robots can disrupt operations and lead to significant losses in productivity and revenue. A single malfunctioning robotic arm in a high-throughput sorting facility, for example, could cause a significant backlog and delay shipments. Therefore, robust maintenance programs and readily available skilled technicians are crucial for ensuring the reliability and uptime of robotic systems.
Impact on the Human Workforce
The introduction of robots into the logistics industry inevitably raises concerns about the impact on human workers. While some fear widespread job displacement, the reality is often more nuanced. Many believe that robots will primarily automate repetitive and physically demanding tasks, freeing up human workers to focus on more complex and strategic roles. However, this transition requires retraining and upskilling programs to equip workers with the skills needed for these new roles. Without adequate support for workforce adaptation, the introduction of robotics could lead to job displacement and increased social inequality. For instance, warehouse workers accustomed to manual picking and packing might need training to operate and maintain robotic systems or to take on supervisory or management positions. A well-planned transition strategy that includes reskilling and upskilling initiatives is crucial to mitigate potential negative impacts on the human workforce.
The Future of Robotics in Logistics
The logistics industry, already undergoing a significant transformation through automation, is poised for an even more dramatic shift in the coming decades. The integration of advanced robotics, fueled by breakthroughs in artificial intelligence and machine learning, will redefine how goods are moved, stored, and delivered globally. This isn’t simply about incremental improvements; we’re talking about a fundamental reshaping of the entire supply chain.
The convergence of several key technological advancements will drive this revolution. More sophisticated robots will handle increasingly complex tasks, requiring less human intervention. This will lead to higher efficiency, reduced error rates, and increased throughput. Simultaneously, the rise of autonomous vehicles, drones, and advanced warehouse management systems will create a highly interconnected and responsive logistics network.
Emerging Technologies Revolutionizing Logistics
The next generation of logistics robotics will be characterized by its intelligence and adaptability. Artificial intelligence (AI) will enable robots to learn from experience, optimize their movements, and adapt to changing conditions in real-time. Machine learning algorithms will analyze vast datasets to predict demand, optimize routes, and proactively address potential bottlenecks. For instance, AI-powered predictive maintenance can anticipate equipment failures, minimizing downtime and maximizing operational efficiency. This contrasts sharply with current systems that often rely on scheduled maintenance, potentially leading to unnecessary downtime. Furthermore, the use of computer vision will allow robots to identify and sort items with greater accuracy and speed than human workers, even in cluttered or poorly lit environments. Imagine a warehouse where robots autonomously navigate, identify packages based on visual cues, and sort them with near-perfect accuracy, eliminating the need for manual barcode scanning.
A Hypothetical Future Logistics Scenario
Imagine a world where autonomous trucks, guided by AI and communicating seamlessly with each other and traffic management systems, transport goods across continents. These trucks are equipped with sophisticated sensors and AI-powered route optimization software, ensuring efficient and safe delivery. At the destination, autonomous drones deliver smaller packages directly to customers, bypassing congested urban centers and reducing delivery times. Inside massive, automated warehouses, swarms of collaborative robots work in harmony, handling everything from unloading containers to picking and packing individual items. These robots, guided by AI-powered warehouse management systems, constantly adapt to fluctuating demand, optimizing storage and retrieval processes in real-time. The entire system is interconnected, allowing for seamless tracking and monitoring of goods throughout the entire supply chain, providing unprecedented levels of transparency and control. This highly automated system would lead to significant cost savings, reduced environmental impact through optimized routes and fuel efficiency, and faster delivery times, ultimately benefiting both businesses and consumers.
Case Studies
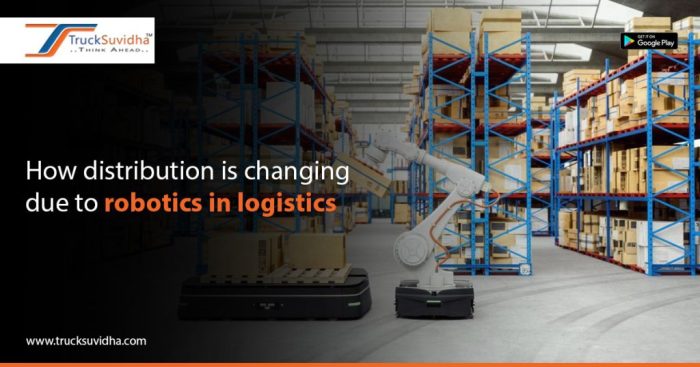
Source: trucksuvidha.com
Real-world examples showcase the transformative power of robotics in logistics. These case studies highlight diverse approaches to integration, demonstrating both the successes and challenges of implementing robotic systems in various operational contexts. Analyzing these deployments offers valuable insights for companies considering similar initiatives.
Amazon Robotics Implementation
Amazon’s extensive use of robotics, particularly Kiva robots (now Amazon Robotics), provides a compelling case study. These autonomous mobile robots (AMRs) revolutionized Amazon’s fulfillment centers by automating the movement of goods within warehouses. Kiva robots retrieve shelves of products and transport them to human workers, significantly reducing the time and effort required for order fulfillment. The impact is measurable: Amazon reported significant improvements in order processing speed and a reduction in operational costs. While precise figures are not publicly available due to competitive sensitivity, industry analysts estimate productivity gains in the range of 20-40%, primarily attributed to the streamlined workflow enabled by the robotic system. The robots themselves, while initially a substantial investment, demonstrate a strong return on investment through increased efficiency and reduced labor costs. The system’s success hinges on a sophisticated integration of hardware, software, and warehouse design, optimized for the specific capabilities of the robots.
DHL’s Use of Automated Guided Vehicles (AGVs)
DHL, a global logistics giant, has implemented AGVs in various facilities worldwide. Unlike Amazon’s AMRs which are more flexible and navigate dynamically, DHL’s AGVs typically follow pre-defined paths, making them suitable for applications requiring precise and repeatable movements, such as transporting pallets or containers within a warehouse or distribution center. This approach is cost-effective for tasks with predictable routes and less need for real-time route adjustments. DHL reports improvements in throughput and reduced transportation times. Specific metrics, while not consistently publicized, often reflect a double-digit percentage increase in efficiency within specific operational segments. The success of DHL’s AGV implementation emphasizes the importance of matching robotic technology to the specific needs and characteristics of the operational environment.
Ocado’s Automated Warehouse
Ocado, an online grocery retailer, has developed a highly automated warehouse system that combines robots, automated conveyors, and sophisticated software. This system is characterized by its incredibly high density storage and extremely efficient order picking processes. The robots work collaboratively, retrieving items from a vast grid of storage locations and delivering them to packing stations. Ocado’s system boasts impressive metrics, with significantly higher throughput and order fulfillment rates compared to traditional warehouse operations. While exact figures are guarded closely, industry analysts suggest significant gains in picking speed and reduced error rates. The high level of automation and sophisticated integration represent a substantial upfront investment, but the long-term efficiency gains are expected to justify the costs. This case study highlights the potential of fully automated warehouse solutions for achieving unparalleled levels of efficiency in high-volume e-commerce operations.
Final Thoughts
The integration of robotics into the logistics industry isn’t just a trend; it’s a fundamental shift. While challenges remain, the potential for increased efficiency, cost savings, and improved accuracy is undeniable. The future of logistics is undeniably robotic, promising a faster, more precise, and ultimately, more sustainable supply chain. As technology continues to evolve, expect even more sophisticated robots and AI-driven solutions to redefine how we move goods, creating a seamless global network of automated efficiency.