The Role of Robotics in Revolutionizing the Mining Industry is no longer a futuristic fantasy; it’s the present. Forget dusty, dangerous mineshafts – think sleek, automated operations humming with efficiency. This isn’t just about replacing humans with machines; it’s about boosting safety, slashing costs, and maximizing resource extraction. We’re diving deep into how robots are transforming this historically grueling industry, from autonomous trucks hauling ore to AI-powered drilling systems that pinpoint the richest veins. Get ready to witness the mining industry’s exciting robotic makeover.
From autonomous haulage trucks navigating treacherous terrain to microscopic robots inspecting pipelines for leaks, the applications of robotics in mining are diverse and rapidly evolving. The integration of AI and data analytics further enhances efficiency, allowing for predictive maintenance and optimized resource allocation. This technological shift promises not only increased productivity and reduced operational costs but also significantly improved worker safety in inherently hazardous environments. But this transformation also brings its own set of challenges, from the economic implications of job displacement to the need for robust regulatory frameworks. We’ll explore all of this and more.
The Evolving Mining Landscape
The mining industry, a cornerstone of global economies, faces a perfect storm of challenges. Declining ore grades necessitate digging deeper and processing more material to extract the same amount of valuable minerals. Simultaneously, environmental regulations are tightening, demanding more sustainable practices and minimizing the industry’s ecological footprint. Labor shortages, coupled with the inherent dangers of underground and surface mining, add further complexity. These factors combine to drive up operational costs and hinder profitability, creating a ripe environment for technological disruption. Robotics offers a powerful solution, promising to enhance efficiency, improve safety, and promote environmentally responsible mining.
The potential benefits of robotics in mining are transformative. Autonomous vehicles, robotic arms, and drone-based surveying systems can drastically increase productivity by automating repetitive, hazardous tasks. This not only speeds up operations but also reduces the risk of human error and workplace accidents, leading to significant cost savings and improved worker safety. Furthermore, robotics can facilitate the adoption of more precise extraction methods, reducing waste and minimizing environmental impact. This aligns perfectly with the growing demand for sustainable and responsible mining practices.
A Brief History of Robotics in Mining
Early applications of robotics in mining were limited to simple tasks like remote-controlled vehicles for hazardous environments. However, advancements in artificial intelligence, sensor technology, and autonomous navigation systems have revolutionized the field. Key milestones include the development of autonomous haulage trucks, which are now commonplace in large-scale open-pit mines, significantly improving efficiency and safety in transportation. The introduction of robotic drilling systems has enhanced precision and reduced the risk of human error in drilling operations. More recently, the use of drones for surveying and inspection has streamlined these processes, offering real-time data acquisition and analysis. These advancements demonstrate a clear trajectory towards increasingly sophisticated robotic systems in the mining sector, with ongoing research and development pushing the boundaries of what’s possible.
Types of Robots Used in Mining
The mining industry, traditionally reliant on human labor and heavy machinery, is undergoing a significant transformation driven by technological advancements. Robotics is at the forefront of this revolution, offering solutions to improve safety, efficiency, and productivity in often hazardous and challenging environments. Different types of robots are being deployed to tackle various tasks, each designed with specific capabilities to optimize mining operations.
Several key robotic systems are currently revolutionizing mining processes, from autonomous hauling to precise drilling and critical infrastructure inspections. Each robot type offers unique advantages and disadvantages depending on the specific mining environment and operational needs.
Robots are automating dangerous mining tasks, boosting efficiency and safety. This data-driven approach mirrors the retail revolution, where understanding consumer behavior is key, as highlighted in this insightful article on The Role of Big Data in Enhancing Consumer Experience in Retail. Similarly, mining companies leverage data analytics from robotic operations to optimize resource extraction and minimize environmental impact.
Autonomous Haulage Trucks
Autonomous haulage trucks (AHTs) are self-driving vehicles that transport materials like ore and waste rock across mine sites. These trucks use a combination of GPS, sensors, and onboard computers to navigate without human intervention. They operate along pre-programmed routes, optimizing their paths to maximize efficiency and minimize downtime. AHTs are particularly useful in large open-pit mines where long haul distances are common.
Drilling Robots
Drilling robots are used for various tasks, including blast hole drilling and exploration drilling. These robots offer increased precision and consistency compared to traditional drilling methods, leading to improved blast fragmentation and reduced drilling time. Some advanced drilling robots can adapt to varying ground conditions, ensuring optimal drilling performance even in challenging terrains. They are particularly beneficial in underground mining where precise drilling is crucial for safety and efficiency.
Inspection Robots
Inspection robots are crucial for maintaining the structural integrity of mines and ensuring worker safety. These robots can access confined spaces and hazardous areas that are difficult or dangerous for humans to reach. They are equipped with cameras, sensors, and other tools to inspect infrastructure such as tunnels, pipelines, and equipment, identifying potential hazards and providing valuable data for maintenance planning. This minimizes risks associated with manual inspections and allows for proactive maintenance.
Robot Type | Tasks | Advantages | Disadvantages |
---|---|---|---|
Autonomous Haulage Trucks | Transporting ore and waste rock | Increased efficiency, reduced labor costs, improved safety, higher productivity | High initial investment cost, dependence on reliable infrastructure (GPS, communication networks), potential for software glitches |
Drilling Robots | Blast hole drilling, exploration drilling | Increased precision and consistency, reduced drilling time, improved blast fragmentation, enhanced safety | High initial cost, specialized maintenance requirements, limited adaptability to extremely challenging geological conditions |
Inspection Robots | Inspection of tunnels, pipelines, and equipment | Improved safety, access to hazardous areas, reduced downtime, early detection of potential hazards | Limited operational range depending on battery life, potential for damage in extremely harsh environments, specialized training required for operation and maintenance |
Automation and Remote Operation
The mining industry, traditionally reliant on manual labor and heavy machinery, is undergoing a dramatic transformation thanks to advancements in automation and remote operation. These technologies are not merely improving efficiency; they’re fundamentally reshaping safety protocols and operational strategies, paving the way for a more sustainable and productive future. This shift is driven by the need to increase output, reduce operational costs, and most importantly, prioritize worker safety in often treacherous environments.
Automation significantly enhances mining efficiency and productivity by optimizing various processes. Automated systems can perform repetitive tasks with greater speed and precision than human workers, leading to increased throughput and reduced downtime. Furthermore, automation allows for continuous operation, even during unfavorable weather conditions or outside of standard working hours. This translates to higher yields and better resource utilization. For instance, automated drilling systems can operate around the clock, consistently achieving precise drilling patterns, which minimizes material waste and maximizes ore extraction. Similarly, automated haulage systems can transport materials efficiently and safely, reducing the risk of accidents and delays.
Remote Operation Systems in Hazardous Environments
Remote operation systems are crucial for mitigating risks in hazardous mining environments. These systems allow operators to control machinery from a safe, remote location, minimizing their exposure to dangerous conditions such as underground tunnels with unstable rock formations, or open-pit mines with steep slopes and heavy equipment. This approach is particularly vital in scenarios involving explosive materials, toxic gases, or unstable ground. The use of advanced sensors, cameras, and communication networks enables operators to monitor equipment performance and the surrounding environment in real-time, allowing for immediate responses to potential hazards. Furthermore, remote operation allows for the use of smaller, more maneuverable robots in confined spaces, improving access to difficult-to-reach areas and enhancing the overall efficiency of operations.
Hypothetical Scenario: Remote Operation in an Underground Coal Mine
Imagine an underground coal mine prone to methane gas accumulation. Traditionally, miners would risk exposure to potentially explosive gas while operating heavy machinery like longwall shearers. With a remote operation system, however, a skilled operator situated in a safe control room miles away can monitor gas levels and control the shearer via a high-definition camera feed and sophisticated control interface. Sensors on the shearer provide real-time data on gas concentration, ground stability, and equipment performance. If a gas leak is detected, the system automatically shuts down the shearer and initiates ventilation procedures, preventing potential explosions. This remote operation significantly reduces the risk of accidents and fatalities while maintaining high productivity. The operator can also adjust the shearer’s cutting parameters based on real-time data, optimizing the extraction process and minimizing material waste. This setup dramatically improves both safety and efficiency, showcasing the transformative potential of remote operation in hazardous mining environments. The increased safety leads to improved worker morale and reduced insurance costs, while the enhanced efficiency translates to higher output and lower operational expenses. This scenario highlights the compelling economic and social benefits of implementing remote operation technologies in modern mining operations.
Data Analytics and AI Integration: The Role Of Robotics In Revolutionizing The Mining Industry
The marriage of robotics and artificial intelligence (AI) in mining isn’t just a futuristic fantasy; it’s rapidly becoming the industry standard. Data analytics, fueled by the massive datasets generated by mining robots, provides the crucial intelligence AI needs to optimize every aspect of the operation, from resource extraction to equipment maintenance. This synergy leads to significant improvements in efficiency, safety, and profitability.
The sheer volume of data generated by modern mining operations – sensor readings from robots, geological surveys, weather patterns, and more – is overwhelming for human analysis. AI algorithms, however, can sift through this data, identify patterns, and make predictions that would be impossible for humans to discern. This enables more informed decision-making at every level, leading to smarter resource allocation and reduced operational costs.
AI-Enhanced Robot Performance and Decision-Making
AI algorithms are revolutionizing robot performance in several key ways. Machine learning models, for instance, allow robots to adapt to changing conditions in real-time. Imagine a robot drilling through rock; an AI system can analyze sensor data from the drill bit, adjusting pressure and speed to optimize drilling efficiency based on the rock’s hardness and composition. This dynamic adaptation significantly reduces wear and tear on equipment and increases overall productivity. Furthermore, AI-powered path planning algorithms optimize the routes robots take, minimizing travel time and fuel consumption. This is particularly impactful in large, open-pit mines where distances can be considerable. For example, Rio Tinto’s autonomous haulage system uses AI to optimize the routes of its autonomous trucks, resulting in significant fuel savings and increased efficiency.
Predictive Maintenance Through Data Analysis
Predictive maintenance, powered by AI, is a game-changer in mining. By analyzing sensor data from mining robots and other equipment, AI algorithms can predict potential failures before they occur. This allows for proactive maintenance, preventing costly downtime and ensuring operational continuity. For example, an AI system might detect subtle changes in the vibration patterns of a robot’s motor, indicating impending failure. This early warning allows for scheduled maintenance, preventing a catastrophic breakdown that could halt operations for days. This proactive approach not only saves money but also enhances safety by reducing the risk of equipment malfunctions.
Data Analysis Leading to Improved Mining Efficiency and Resource Management
Data analytics has demonstrably improved mining efficiency and resource management. By analyzing geological data, AI can identify high-value ore deposits more accurately, optimizing extraction strategies. This precision mining approach reduces waste and maximizes the recovery of valuable resources. For instance, BHP Billiton has utilized AI to improve the accuracy of ore grade estimation, leading to a significant increase in the recovery of valuable minerals. Similarly, the analysis of sensor data from robots can identify areas where operational improvements can be made, leading to increased productivity and reduced costs. A detailed analysis of operational data might reveal bottlenecks in the workflow, enabling managers to optimize processes and improve overall efficiency. This data-driven approach ensures that mining operations are constantly evolving and adapting to maximize efficiency and profitability.
Safety and Environmental Impact
The integration of robotics into mining operations presents a compelling case study in balancing technological advancement with safety and environmental responsibility. While automation offers significant improvements in worker safety and the potential for reduced environmental impact, it’s crucial to acknowledge and address the potential downsides. A holistic approach, considering both benefits and drawbacks, is essential for responsible implementation.
Robotic mining systems dramatically reduce the risks faced by human miners. Traditional mining exposes workers to dangerous conditions such as collapses, explosions, and exposure to harmful substances. Robots, however, can operate in hazardous environments, performing tasks like drilling, blasting, and hauling ore, minimizing human exposure to these dangers. This translates to fewer workplace accidents, injuries, and fatalities, ultimately creating a safer working environment and fostering a more positive impact on the well-being of the mining workforce. The economic benefits of reduced worker’s compensation claims and increased productivity further solidify the case for robotic adoption.
Reduced Risks to Human Workers
The use of robots significantly mitigates several key risks in mining. Autonomous vehicles, for instance, can navigate challenging terrain and operate in low-visibility conditions without the need for human operators in immediate proximity. Remotely operated equipment allows for tasks to be performed from a safe distance, reducing the chance of injury from equipment malfunctions or unexpected events. Furthermore, robots can be deployed for tasks involving hazardous materials, such as handling toxic chemicals or radioactive substances, further shielding human workers from potential harm. The reduction in human exposure to these hazards directly translates into lower injury rates and improved worker safety statistics. Consider, for example, the significant decrease in fatalities reported in mines that have adopted extensive robotic systems compared to those relying solely on human labor.
Potential Environmental Impacts of Robotic Mining, The Role of Robotics in Revolutionizing the Mining Industry
Robotic mining presents a complex picture regarding environmental impact, with both positive and negative aspects. On the positive side, increased precision and control afforded by robotic systems can lead to less waste rock generation and more efficient extraction of valuable minerals. This minimizes the land disturbed during mining operations and reduces the overall environmental footprint. Furthermore, autonomous systems can optimize energy consumption, leading to lower greenhouse gas emissions compared to traditional methods. However, the manufacturing and disposal of robotic equipment themselves can generate waste and pollution. The potential for increased mining activity due to improved efficiency could also lead to an expansion of mining operations and subsequent environmental impacts if not carefully managed. Careful consideration of the entire lifecycle of robotic mining systems is therefore crucial for minimizing overall environmental harm.
Comparison of Environmental Impacts
The following points compare the environmental impact of traditional and robotic mining methods:
The table below summarizes the key environmental differences between traditional and robotic mining:
Factor | Traditional Mining | Robotic Mining |
---|---|---|
Land Disturbance | High; often extensive surface area affected. | Potentially lower; increased precision can minimize land disturbance. |
Waste Generation | High; significant amounts of waste rock and tailings. | Potentially lower; more efficient extraction can reduce waste. |
Greenhouse Gas Emissions | High; energy-intensive processes contribute significantly to emissions. | Potentially lower; optimized energy use and reduced fuel consumption. |
Water Consumption | High; significant water usage for processing and dust suppression. | Potentially lower; more efficient processes could reduce water needs. |
Biodiversity Impact | High; habitat loss and fragmentation. | Potentially lower; reduced land disturbance could minimize impact. |
Economic Considerations and Return on Investment
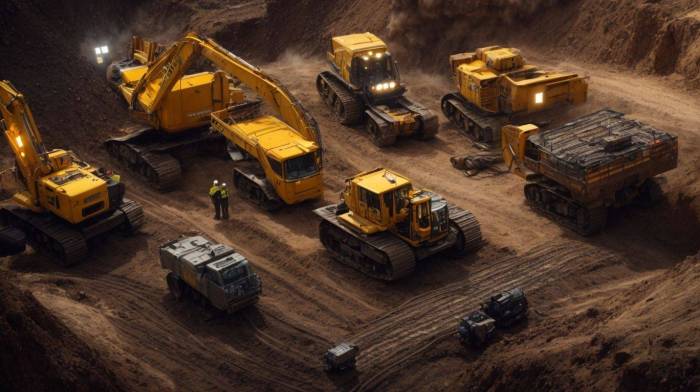
Source: dig8italx.com
The integration of robotics into mining operations presents a compelling economic proposition, albeit one requiring careful consideration of both upfront investments and long-term gains. While initial costs can be substantial, the potential for increased efficiency, reduced operational expenses, and enhanced safety profiles often translates to significant returns over the lifespan of the robotic systems. Understanding these financial dynamics is crucial for mining companies looking to leverage robotic technologies effectively.
The economic viability of robotic mining hinges on a thorough cost-benefit analysis. This analysis must encompass not only the acquisition and implementation costs of robotic systems but also factors like maintenance, repair, and the potential need for workforce retraining. Crucially, it needs to weigh these costs against the projected improvements in productivity, reduced labor costs (partially offset by the cost of robots and maintenance), minimized downtime, and decreased environmental impact. A robust ROI calculation is essential for justifying the investment.
Return on Investment Calculation for Robotic Mining
Calculating the ROI for robotic mining requires a multifaceted approach. First, the total initial investment must be determined. This includes the purchase price of robotic equipment, installation costs, integration with existing infrastructure, and initial training for personnel. Then, projected operational cost savings must be estimated. This might include reduced labor costs, decreased fuel consumption, lower maintenance costs on certain equipment due to less wear and tear, and increased output. Finally, the increased revenue generated by the higher productivity and potentially higher quality of ore extraction needs to be factored in.
A simplified ROI calculation can be represented as follows:
ROI = (Net Present Value of Benefits – Initial Investment) / Initial Investment * 100%
For example, consider a hypothetical scenario where a mining company invests $10 million in a fleet of autonomous haulage trucks. Over five years, these trucks reduce labor costs by $2 million annually, increase output leading to an extra $1 million in revenue annually, and reduce maintenance costs by $500,000 annually. The net annual benefit would be $3.5 million. Using a discounted cash flow analysis (to account for the time value of money), the net present value of these benefits over five years might be approximately $14 million (this is a simplified example and a proper discounted cash flow analysis would be needed for accuracy). In this case, the ROI would be (($14 million – $10 million) / $10 million) * 100% = 40%.
Job Displacement and Workforce Retraining
The introduction of robotic systems into mining inevitably raises concerns about job displacement. While some roles may become redundant, the overall impact is complex. Robotic technologies often create new job opportunities in areas such as robotics maintenance, programming, data analysis, and remote operation. However, existing workers may require retraining to adapt to these evolving roles. Proactive workforce development initiatives are crucial to mitigating the negative impacts of automation and ensuring a smooth transition for the workforce. This might involve partnerships between mining companies, educational institutions, and government agencies to provide training programs in relevant skills, such as programming, data analytics, and robotics maintenance. Furthermore, companies might need to invest in upskilling their existing workforce to manage and maintain these new robotic systems. This approach can ensure that the workforce is equipped to thrive in the changing landscape of the mining industry.
Future Trends and Challenges
The integration of robotics into mining is still in its relatively early stages, but the pace of innovation is accelerating. Looking ahead, we can anticipate significant shifts in how mines operate, driven by both technological advancements and the need to address persistent challenges. This section explores the emerging trends shaping the future of robotic mining and the hurdles that must be overcome for widespread adoption.
The next generation of robotic mining systems will be characterized by increased autonomy, enhanced dexterity, and seamless integration with data analytics and AI. This will lead to more efficient and productive operations, while also improving safety and reducing environmental impact. However, realizing this vision requires addressing significant challenges related to infrastructure, regulation, and the skilled workforce needed to manage these complex systems.
Emerging Trends in Robotic Mining
Several key trends are poised to revolutionize the mining industry. Increased autonomy in robots will allow for more complex tasks to be performed without direct human supervision, leading to greater efficiency and reduced downtime. Advances in sensor technology and AI-powered decision-making systems will enable robots to adapt to changing conditions in real-time, improving their overall performance and reliability. The rise of collaborative robots (cobots) will facilitate safer and more efficient human-robot interactions within mining environments. For instance, Rio Tinto’s autonomous haulage system, utilizing driverless trucks, already demonstrates the potential for increased productivity and reduced operational costs. Further advancements in this area could lead to fully autonomous mining operations, from extraction to processing.
Challenges to Widespread Adoption
Despite the clear potential, the widespread adoption of robotic technologies in mining faces significant obstacles. Existing mining infrastructure in many locations may not be compatible with the needs of advanced robotic systems. Upgrading this infrastructure can be a costly and time-consuming process. Regulatory frameworks often lag behind technological advancements, creating uncertainty and potential delays in the deployment of new robotic technologies. Ensuring the safety and reliability of these systems in harsh and unpredictable environments remains a critical challenge. Finally, the need for skilled technicians and engineers to operate and maintain these complex systems represents a significant workforce development challenge. The lack of readily available trained personnel could hinder the widespread adoption of robotic mining technologies.
Potential Future Advancements in Robotic Mining
The future of robotic mining holds the promise of transformative advancements. We can anticipate the development of more sophisticated robots capable of performing intricate tasks, such as precise ore extraction and complex maintenance operations. The integration of advanced sensor technologies, including hyperspectral imaging and LiDAR, will allow for more accurate and efficient resource mapping and exploration. The use of swarm robotics, where multiple robots collaborate to accomplish complex tasks, holds immense potential for optimizing mining operations. More speculative advancements include the development of robots capable of operating in extreme environments, such as deep sea mining or mining on other planets. This could unlock access to previously unreachable resources and significantly expand the scope of mining activities. Imagine robots that can autonomously navigate complex underground tunnels, autonomously repair equipment, and even predict potential equipment failures before they occur. These are not just science fiction concepts; they represent realistic possibilities that are rapidly becoming a reality.
Final Conclusion
The mining industry is on the cusp of a robotic revolution. While challenges remain – including infrastructure upgrades, regulatory hurdles, and workforce retraining – the potential benefits of increased efficiency, safety, and resource optimization are undeniable. The integration of robotics, AI, and data analytics is paving the way for a more sustainable, profitable, and significantly safer future for mining. It’s not just about digging deeper; it’s about digging smarter. The future of mining is automated, and it’s looking bright.