The Role of Robotics in Revolutionizing the Logistics and Supply Chain Industry is no longer a futuristic fantasy; it’s rapidly becoming the new reality. From automated warehouses buzzing with robotic arms to autonomous delivery drones navigating city streets, the impact of robotics is reshaping how goods move around the globe. This transformation promises increased efficiency, reduced costs, and a more resilient supply chain—but it also presents challenges, including workforce displacement and regulatory hurdles. Let’s dive into the exciting and complex world of robotics in logistics.
This deep dive will explore how robots are automating warehousing, optimizing last-mile delivery, enhancing supply chain visibility, and even changing the nature of work itself. We’ll examine the various types of robots used, the technological advancements driving this revolution, and the potential impact on jobs and the workforce. We’ll also look at the challenges and opportunities this presents, from regulatory hurdles to the ethical considerations of automation.
Automation in Warehousing and Distribution
The logistics and supply chain industry is undergoing a dramatic transformation, driven by the increasing adoption of robotics and automation. Warehousing and distribution centers, traditionally reliant on manual labor, are now embracing robotic solutions to enhance efficiency, reduce costs, and improve overall operational performance. This shift is not just about replacing human workers; it’s about creating a more dynamic and responsive supply chain capable of meeting the demands of today’s fast-paced e-commerce environment.
Automated Guided Vehicles (AGVs) and Autonomous Mobile Robots (AMRs) in Warehouse Efficiency
Automated Guided Vehicles (AGVs) and Autonomous Mobile Robots (AMRs) are revolutionizing material handling within warehouses. AGVs follow pre-programmed paths, often using wires or magnetic strips embedded in the floor, to transport goods between different locations. AMRs, on the other hand, utilize advanced sensors and AI-powered navigation systems to move independently, adapting to dynamic environments and obstacles. This flexibility allows AMRs to optimize routes in real-time, significantly improving efficiency compared to the rigid pathways of AGVs. The impact is a reduction in transportation time, improved throughput, and a minimized risk of human error in material handling. For instance, a large e-commerce fulfillment center using AMRs might see a 20-30% increase in order fulfillment speed compared to a similar facility relying solely on human workers and forklifts. This translates directly into faster delivery times and increased customer satisfaction.
Robotic Picking and Packing Systems: Benefits and Challenges
Robotic picking and packing systems represent a significant advancement in warehouse automation. These systems can handle a wide range of tasks, from identifying and selecting individual items from shelves to packaging and labeling them for shipment. The benefits are substantial: increased accuracy, reduced labor costs, and the ability to handle high-volume orders with greater speed and consistency. However, challenges remain. The initial investment in robotic picking and packing systems can be significant. Furthermore, these systems often struggle with the variability of items and packaging encountered in real-world logistics operations. Items that are irregularly shaped, fragile, or require delicate handling may pose difficulties for current robotic technologies. Adapting the systems to handle such complexities requires ongoing investment in software and hardware upgrades. Despite these challenges, the ongoing development of advanced computer vision and machine learning algorithms is steadily improving the capabilities of robotic picking and packing systems, paving the way for wider adoption.
Cost-Effectiveness of Robotic Solutions versus Human Labor
The cost-effectiveness of robotic solutions versus human labor in warehousing is a complex issue. While the initial investment in robots can be substantial, the long-term operational costs can be lower. Robots don’t require wages, benefits, or overtime pay, and they can operate continuously for extended periods without breaks. However, the cost of maintenance, repairs, and software updates must be considered. Furthermore, the implementation of robotic systems often requires significant upfront investment in infrastructure modifications and employee training. A detailed cost-benefit analysis, considering factors such as warehouse size, order volume, and the specific types of tasks to be automated, is crucial to determining the optimal approach. In some cases, a hybrid model combining human workers and robots might prove to be the most cost-effective solution. For example, Amazon’s extensive use of robots in their fulfillment centers demonstrates the potential for significant long-term cost savings, although the initial investment was substantial.
Comparison of Different Types of Warehouse Robots
The following table compares different types of warehouse robots based on their capabilities and limitations:
Robot Type | Capabilities | Limitations | Typical Applications |
---|---|---|---|
Automated Guided Vehicles (AGVs) | High payload capacity, reliable operation along fixed routes, cost-effective for repetitive tasks | Limited flexibility, inflexible to changes in layout, require pre-programmed paths | Material transport, pallet movement |
Autonomous Mobile Robots (AMRs) | Flexible navigation, adaptable to dynamic environments, can optimize routes in real-time | Higher initial cost than AGVs, potential for software glitches, may require more sophisticated infrastructure | Order picking, goods-to-person systems, inventory management |
Collaborative Robots (Cobots) | Can work safely alongside humans, adaptable to various tasks, relatively easy to program | Lower payload capacity than AGVs or AMRs, limited dexterity in some applications, require careful safety protocols | Picking and packing, assembly, quality control |
Articulated Robots | High precision and speed, capable of complex movements, high payload capacity in some models | Requires significant programming expertise, limited mobility outside their work envelope, safety concerns when working near humans | Pallet loading/unloading, complex assembly tasks |
Last-Mile Delivery and Transportation
The final leg of the delivery journey, the last mile, is often the most expensive and complex part of the supply chain. Traditional methods struggle with rising fuel costs, traffic congestion, and delivery window constraints. Robotics and automation offer a compelling solution to optimize this crucial stage, promising increased efficiency, reduced costs, and improved customer satisfaction.
The integration of delivery robots and drones is rapidly transforming last-mile delivery, offering a compelling alternative to traditional methods. These autonomous systems navigate streets and airspace, carrying packages directly to customers’ doorsteps. This not only streamlines the delivery process but also offers the potential for significant cost reductions, particularly in densely populated urban areas.
The Role of Delivery Robots and Drones in Optimizing Last-Mile Delivery
Delivery robots, ranging from small, wheeled units to larger, autonomous vehicles, are increasingly being deployed for last-mile delivery. These robots navigate sidewalks and streets, utilizing GPS, sensors, and AI to avoid obstacles and reach their destinations safely. Drones, on the other hand, offer a unique advantage in overcoming geographical challenges, particularly in areas with limited road access or congested traffic. They can deliver packages directly to designated drop-off points, significantly reducing delivery times and operational costs. The combined use of both robots and drones can create a highly efficient and flexible last-mile delivery network. For example, a drone might transport packages from a central distribution hub to a neighborhood, where ground robots then handle the final delivery to individual customers.
Regulatory and Infrastructure Challenges Associated with Autonomous Delivery Systems
The widespread adoption of autonomous delivery systems faces several significant hurdles. Regulations surrounding the operation of autonomous vehicles, both on the ground and in the air, are still evolving. Ensuring safety and liability in the event of accidents is a key concern. Furthermore, the existing infrastructure may not be adequately equipped to support the widespread deployment of these technologies. Sidewalks and roads need to be designed to accommodate robots, and airspace needs to be managed effectively to prevent drone collisions. The development of robust communication networks is also crucial for the seamless operation of autonomous delivery systems. Clear legal frameworks and infrastructure improvements are essential to facilitate the safe and efficient integration of these technologies.
Examples of Successful Implementations of Robotic Delivery Solutions, The Role of Robotics in Revolutionizing the Logistics and Supply Chain Industry
Several companies have successfully implemented robotic delivery solutions in various geographical contexts. In urban environments, Starship Technologies’ robots are used for grocery deliveries in multiple cities across the globe, navigating busy streets and sidewalks. In suburban areas, Nuro’s autonomous vehicles are delivering groceries and other goods, showcasing their ability to operate in less densely populated environments. In rural areas, where road infrastructure is limited, drones are being explored for the delivery of essential goods and medical supplies, demonstrating their potential in bridging geographical gaps. These examples highlight the adaptability of robotic delivery solutions to different environments, paving the way for widespread adoption.
Flowchart of a Typical Robotic Last-Mile Delivery Operation
A typical robotic last-mile delivery operation involves several key steps. The following flowchart illustrates this process:
[Imagine a flowchart here. The flowchart would begin with “Order Placement” and branch to “Order Processing” then to “Dispatch to Robot/Drone”. From “Dispatch”, there are two branches, one for “Ground Robot Delivery” and one for “Drone Delivery”. Both branches would converge at “Delivery Confirmation” and finally end at “Order Completion”. Each step would have a brief description of the activities involved, such as GPS navigation for robots and obstacle avoidance for drones.]
Supply Chain Optimization and Visibility
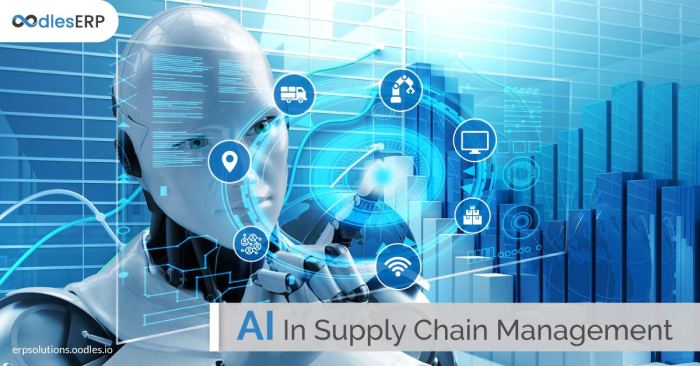
Source: oodles.io
Robots are automating warehouses, optimizing delivery routes, and boosting efficiency in logistics. This precision extends beyond shipping; the same principles drive innovation in other sectors, like healthcare, where advancements are being made thanks to smart sensors, as detailed in this insightful article: How Smart Sensors are Changing the Healthcare Landscape. Ultimately, the quest for data-driven optimization fuels both robotic logistics and the healthcare revolution.
The integration of robotics and artificial intelligence (AI) is no longer a futuristic fantasy; it’s rapidly reshaping the logistics and supply chain landscape. This revolution isn’t just about faster delivery; it’s about achieving unprecedented levels of efficiency, transparency, and predictive capability, ultimately leading to significant cost savings and improved customer satisfaction. The key to unlocking this potential lies in enhanced supply chain visibility and optimization, areas where robotics and AI shine.
Robotics and AI dramatically improve supply chain visibility by providing real-time data tracking and analysis across the entire process. Imagine a world where you know the exact location of every package, every component, at every stage of its journey, from raw material sourcing to final delivery. This granular level of detail, powered by connected sensors, automated data collection, and sophisticated AI algorithms, allows businesses to proactively identify bottlenecks, predict potential disruptions, and optimize resource allocation in ways previously unimaginable. This predictive capability minimizes delays, reduces waste, and allows for more agile responses to changing market demands.
Robotic Process Automation in Streamlining Administrative Tasks
Robotic Process Automation (RPA) is quietly revolutionizing the often-overlooked administrative side of supply chain management. RPA bots handle repetitive, rule-based tasks like data entry, invoice processing, order management, and inventory reconciliation with incredible speed and accuracy. This frees up human employees to focus on more strategic and complex activities, boosting overall efficiency and reducing the risk of human error. For instance, an RPA bot can automatically process thousands of invoices daily, cross-referencing them with purchase orders and payment terms, ensuring accurate and timely payments to suppliers. This automation not only speeds up processes but also minimizes discrepancies and improves cash flow. Similarly, RPA can streamline order fulfillment by automatically updating inventory levels, generating shipping labels, and coordinating with logistics providers.
Key Performance Indicators for Robotic Implementation
Measuring the success of robotic implementation in supply chain management requires focusing on specific, quantifiable metrics. Key Performance Indicators (KPIs) should reflect improvements in efficiency, accuracy, and cost reduction. Some crucial KPIs include: order fulfillment rate, inventory turnover rate, on-time delivery rate, processing time for invoices and orders, reduction in error rates, and return on investment (ROI) for robotic systems. Tracking these KPIs provides a clear picture of the impact of robotic implementation and allows for continuous improvement and optimization of processes. For example, a significant increase in the on-time delivery rate, coupled with a reduction in processing time for orders, clearly demonstrates the positive effects of robotic integration.
Risks and Mitigation Strategies Associated with Robotic Integration
Integrating robots into supply chain operations presents both opportunities and challenges. Careful consideration of potential risks and the development of robust mitigation strategies are crucial for successful implementation.
- High Initial Investment Costs: Implementing robotic systems requires significant upfront investment in hardware, software, and integration. Mitigation: Thorough cost-benefit analysis, phased implementation, and exploration of leasing options can mitigate this risk.
- Job Displacement Concerns: Automation may lead to job displacement for certain roles. Mitigation: Reskilling and upskilling initiatives, focusing on roles requiring human judgment and problem-solving skills, are essential.
- Integration Complexity: Integrating robotic systems into existing infrastructure can be complex and require specialized expertise. Mitigation: Partnering with experienced integration specialists and adopting a phased approach to implementation can minimize disruption and ensure seamless integration.
- Cybersecurity Risks: Connected robotic systems are vulnerable to cyberattacks. Mitigation: Implementing robust cybersecurity measures, including regular security audits and employee training, is crucial.
- Dependence on Technology: Over-reliance on robotic systems can create vulnerabilities if systems fail. Mitigation: Developing robust backup systems and contingency plans is vital to ensure operational continuity.
Impact on Employment and Workforce
The rise of robotics in logistics is undeniably transforming the industry, leading to both exciting opportunities and significant challenges. While automation promises increased efficiency and productivity, it also raises concerns about job displacement and the need for a reskilling revolution within the workforce. Understanding the evolving landscape of employment in this sector is crucial for navigating this technological shift successfully.
The integration of robots into warehousing, transportation, and delivery systems is already impacting the job market. Many repetitive and physically demanding tasks, previously performed by humans, are now being automated. This shift necessitates a proactive approach to retraining and upskilling the existing workforce to prepare them for the new roles emerging within the automated logistics ecosystem. The good news is that robotics also creates entirely new job opportunities, requiring specialized skills and knowledge.
Job Displacement and Retraining Needs
The automation of tasks like picking, packing, and sorting in warehouses is a prime example of job displacement. However, this doesn’t necessarily translate to a net loss of jobs. The key lies in anticipating these shifts and investing in comprehensive retraining programs. For example, warehouse workers previously focused on manual handling could be retrained as robot technicians, maintenance specialists, or data analysts, all crucial roles in a robotic warehouse environment. Government initiatives, industry collaborations, and educational institutions must work together to create effective retraining programs that equip displaced workers with the skills demanded by the evolving job market. A successful transition requires early planning, investment in training infrastructure, and ongoing support for workers during the adaptation process. This proactive approach can minimize disruption and maximize the benefits of automation for both individuals and the economy.
New Job Roles and Required Skills
The expanding use of robotics in logistics is generating a demand for a new breed of skilled professionals. These roles often require a blend of technical expertise and soft skills. For instance, robot programmers need to design and implement efficient robotic systems, while AI specialists are needed to manage and optimize the algorithms driving automated processes. Data scientists play a vital role in analyzing the vast amounts of data generated by robotic systems to improve efficiency and decision-making. Furthermore, technicians specializing in the maintenance and repair of robotic equipment are becoming increasingly important. Beyond the technical skills, professionals in the field will also need strong problem-solving abilities, collaborative skills, and the adaptability to navigate a constantly evolving technological landscape. These skills will be crucial for managing and integrating robots effectively within the logistics ecosystem.
Human-Robot Collaboration: Benefits and Drawbacks
The future of logistics isn’t about humans versus robots, but rather humans and robots working collaboratively. This synergistic approach offers significant advantages. Humans excel at tasks requiring adaptability, complex decision-making, and problem-solving in unpredictable situations, while robots are highly efficient at repetitive, physically demanding tasks. For example, robots can handle heavy lifting and precise movements, freeing up human workers to focus on tasks requiring judgment, creativity, and critical thinking. However, challenges exist. Integrating humans and robots requires careful planning and consideration of safety protocols. Effective communication and coordination between human workers and robotic systems are paramount to ensure seamless operations and prevent accidents. Moreover, the initial investment in robotic systems and the ongoing maintenance costs can be substantial. The long-term benefits of human-robot collaboration, however, are expected to outweigh the initial challenges, leading to improved efficiency, reduced costs, and a safer working environment.
A Collaborative Future: A Scenario
Imagine a futuristic logistics warehouse. Automated guided vehicles (AGVs) navigate the warehouse floor, transporting goods efficiently between different stations. Robots equipped with advanced vision systems and gripping mechanisms perform tasks such as picking and packing items with speed and precision. Human workers oversee the operations, monitoring the performance of the robotic systems, troubleshooting issues, and handling exceptions that require human judgment. They collaborate closely with the robots, ensuring seamless integration and efficient workflows. For example, a human worker might be responsible for quality control, inspecting items picked and packed by robots to ensure accuracy. Another might manage the inventory system, analyzing data generated by the robotic systems to optimize stock levels and prevent shortages. This collaborative approach allows for optimal utilization of both human skills and robotic capabilities, resulting in a more efficient, productive, and safer work environment. This scenario represents a realistic vision of the future, where humans and robots work side-by-side, complementing each other’s strengths to achieve a common goal.
Technological Advancements and Future Trends: The Role Of Robotics In Revolutionizing The Logistics And Supply Chain Industry
The logistics and supply chain industry is undergoing a rapid transformation driven by advancements in robotics and related technologies. These innovations are not merely incremental improvements; they represent a fundamental shift towards greater efficiency, transparency, and resilience within the industry. This section explores the latest technological advancements shaping the future of logistics and their potential impact.
Robotics, propelled by artificial intelligence (AI) and machine learning (ML), are becoming increasingly sophisticated. This sophistication translates to improved capabilities in tasks previously requiring human intervention, such as picking, packing, and sorting. Beyond individual robots, the concept of swarm robotics—where multiple robots coordinate their actions to achieve a common goal—is gaining traction, allowing for greater flexibility and adaptability in dynamic warehouse environments.
AI-Powered Robots and Swarm Robotics
AI-powered robots are now equipped with advanced vision systems, enabling them to identify and manipulate objects with greater precision and speed than ever before. This is particularly beneficial in handling diverse and irregularly shaped items. Swarm robotics leverages the collective intelligence of multiple robots, allowing for efficient task allocation and collaboration. Imagine a warehouse where hundreds of small robots work in concert, autonomously navigating and fulfilling orders, adapting to changing demands in real-time. This eliminates bottlenecks and optimizes throughput, surpassing the capabilities of traditional automated systems.
Blockchain and IoT Integration
The integration of blockchain technology and the Internet of Things (IoT) with robotics offers significant potential for enhancing supply chain security and transparency. Blockchain provides an immutable record of every stage of the supply chain, from origin to delivery, minimizing the risk of fraud and counterfeiting. IoT sensors embedded in packages and transportation vehicles provide real-time data on location, temperature, and other crucial parameters, enhancing visibility and enabling proactive management of potential disruptions.
For example, imagine a shipment of pharmaceuticals. IoT sensors monitor temperature throughout the journey, and any deviation from optimal conditions is immediately flagged on the blockchain, alerting stakeholders and preventing spoilage or loss of efficacy. This level of transparency and traceability builds trust and improves accountability across the entire supply chain.
Innovative Applications Across Sectors
The application of robotics is rapidly expanding across various logistics sectors. In e-commerce, automated warehouses utilizing robotic arms and autonomous mobile robots (AMRs) are becoming increasingly common, enabling faster order fulfillment and reduced operational costs. In healthcare, robots are used to transport medical supplies and specimens within hospitals, improving efficiency and reducing the risk of human error. Manufacturing facilities are leveraging robotic systems for material handling, assembly, and quality control, enhancing productivity and consistency.
A Futuristic Vision of Fully Automated Logistics
Envision a future where a fully automated logistics system seamlessly integrates AI-powered robots, autonomous vehicles, and drone delivery. Orders are placed digitally, and AI algorithms optimize routes and delivery schedules in real-time. Autonomous trucks transport goods across long distances, while drones handle last-mile deliveries, reaching even the most remote locations. Warehouses operate autonomously, with robots handling every aspect of order fulfillment, from receiving and sorting to packing and shipping. Blockchain technology ensures complete transparency and traceability, while IoT sensors monitor every step of the process, providing real-time insights into inventory levels, transportation status, and potential disruptions. This futuristic system would represent a significant leap forward in efficiency, cost-effectiveness, and sustainability, redefining the landscape of the logistics and supply chain industry.
Conclusion
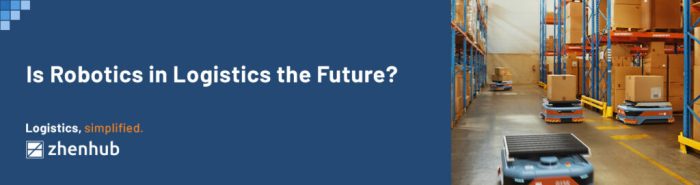
Source: zhenhub.com
The integration of robotics into the logistics and supply chain industry is undeniably transforming the sector, creating a more efficient, responsive, and data-driven system. While challenges remain, the potential benefits—from cost savings and improved efficiency to enhanced security and sustainability—are immense. As technology continues to advance, we can expect even more innovative applications of robotics, paving the way for a future where seamless, automated logistics are the norm. The key lies in strategic implementation, careful workforce planning, and a proactive approach to addressing the ethical and societal implications of this technological revolution.