The Role of Robotics in Reducing Manufacturing Costs: Forget clunky, expensive robots of the past. Today’s automated workforce is sleek, efficient, and poised to revolutionize how we manufacture everything from smartphones to cars. This isn’t just about replacing human workers; it’s about optimizing processes, slashing waste, and boosting profits in ways previously unimaginable. We’re diving deep into the world of robotic manufacturing, exploring the cost savings, the challenges, and the exciting future this technology promises.
From collaborative robots working alongside humans to autonomous guided vehicles (AGVs) zipping across factory floors, the applications are vast and constantly evolving. We’ll unpack how robots are transforming specific manufacturing processes, crunching the numbers to show you exactly how much money businesses are saving—and how you can too. Get ready to see manufacturing in a whole new light.
Introduction to Robotics in Manufacturing
The integration of robotics into manufacturing processes is no longer a futuristic fantasy; it’s a rapidly evolving reality reshaping global industries. From automotive giants to smaller-scale operations, businesses are increasingly recognizing the transformative potential of automation to boost efficiency and slash costs. This shift is driven by advancements in robotics technology, making automation more accessible and affordable than ever before. This section explores the current landscape of robotic adoption and the diverse types of robots revolutionizing manufacturing.
The current state of robotics adoption in manufacturing shows a significant upward trend. While precise global figures are challenging to obtain due to varying reporting standards, industry analysts consistently report substantial growth in robot installations across various sectors. The automotive industry remains a major adopter, leveraging robots for tasks like welding, painting, and assembly. However, the adoption is expanding rapidly into electronics, food processing, pharmaceuticals, and logistics, among others. This widespread adoption is fueled by the demonstrable return on investment (ROI) that many businesses are experiencing.
Types of Robots Used in Manufacturing
Robotics in manufacturing encompasses a diverse range of technologies designed for specific tasks and operational environments. These robots are not just simple automated arms; they represent sophisticated engineering solutions tailored to optimize efficiency and precision.
- Industrial Robots (Articulated Arms): These are the workhorses of many manufacturing plants, characterized by their multiple joints and axes of movement, allowing for complex manipulation of parts. They are typically large, powerful, and designed for high-speed, repetitive tasks such as welding, painting, and material handling. A common example is the robotic arm used in car assembly lines, precisely welding components together at a high rate of speed.
- Collaborative Robots (Cobots): Unlike traditional industrial robots, cobots are designed to work alongside human workers in shared workspaces. They are smaller, lighter, and often equipped with safety features to prevent accidents. Cobots are particularly useful for tasks requiring human-robot interaction, such as assembly, inspection, and packaging. Imagine a cobot assisting a human worker by handing them parts, reducing strain and improving efficiency.
- Automated Guided Vehicles (AGVs): These are mobile robots used for material handling and transportation within a factory or warehouse. They can follow pre-programmed routes or use advanced navigation systems to move materials efficiently between different workstations. AGVs can significantly reduce transportation time and labor costs, optimizing the flow of materials through the manufacturing process. Picture a fleet of AGVs autonomously transporting raw materials from storage to assembly lines.
Potential Benefits of Robotics Integration in Manufacturing
The integration of robotics into manufacturing offers a multitude of benefits that contribute to significant cost reductions and increased efficiency. These advantages are not limited to simple cost-cutting; they encompass a holistic improvement in the manufacturing process.
- Increased Productivity and Throughput: Robots can operate continuously without breaks, significantly increasing production rates compared to human workers. This translates to higher output and faster delivery times, meeting increased market demands.
- Improved Product Quality and Consistency: Robots perform tasks with high precision and repeatability, minimizing errors and improving product quality. This consistency leads to reduced waste and rework, saving both time and resources.
- Enhanced Safety: Robots can handle dangerous or repetitive tasks, reducing the risk of workplace injuries to human workers. This contributes to a safer working environment and lowers insurance costs.
- Reduced Labor Costs: While initial investment in robotics can be substantial, the long-term cost savings from reduced labor, improved efficiency, and decreased waste often outweigh the initial expenditure. This is especially true for tasks that are repetitive, dangerous, or require high precision.
Cost Reduction Mechanisms through Robotics: The Role Of Robotics In Reducing Manufacturing Costs
The integration of robotics into manufacturing processes isn’t just a futuristic fantasy; it’s a powerful tool driving down costs and boosting efficiency. This section delves into the specific ways robots contribute to significant cost reductions, moving beyond the theoretical and into the tangible benefits experienced by businesses across various industries. We’ll explore how robots tackle labor costs, enhance productivity, and minimize material waste, all leading to a healthier bottom line.
Robotics significantly impact manufacturing costs through several key mechanisms, offering a compelling return on investment for businesses willing to embrace automation. These mechanisms are not isolated events but rather interconnected processes that collectively optimize the manufacturing workflow, ultimately resulting in substantial savings.
Labor Cost Reduction in Specific Manufacturing Processes
Robots are particularly effective in replacing human labor in repetitive, high-precision tasks, leading to considerable cost savings. The following table illustrates this impact in specific manufacturing processes, comparing human labor costs with robotic alternatives. Note that these figures are estimates and can vary significantly based on factors like geographical location, specific robot model, and task complexity.
Process | Human Labor Cost (USD per unit) | Robotic Labor Cost (USD per unit) | Cost Savings Percentage |
---|---|---|---|
Welding | $5.00 | $1.50 | 70% |
Painting | $4.00 | $0.75 | 81% |
Material Handling | $3.00 | $0.50 | 83% |
Assembly | $6.00 | $2.00 | 67% |
Improved Efficiency and Throughput
Beyond direct labor cost reductions, robots significantly improve manufacturing efficiency and throughput. Their tireless operation, consistent speed, and precision minimize downtime and errors, resulting in faster production cycles. For example, a robotic welding system can operate continuously for extended periods without fatigue, unlike human welders who require breaks and have varying levels of skill and consistency. This increased throughput directly translates to lower production costs per unit, as fixed overhead costs are spread across a larger number of produced goods. Consider a factory producing 1000 units daily. By increasing production to 1200 units with robots, the cost per unit decreases even if the overall operational costs increase slightly.
Material Waste Reduction
Robots contribute to cost savings by reducing material waste. Their precision in tasks such as cutting, trimming, and assembly minimizes errors that lead to scrap materials. For instance, a robot-controlled cutting machine can achieve higher accuracy than a human operator, resulting in less material waste. This reduction in waste not only saves on the direct cost of materials but also minimizes disposal costs and reduces the environmental impact of the manufacturing process. A company producing plastic parts might see a 15% reduction in waste after implementing robotic cutting, translating to significant savings over time considering the volume of production.
Robotics and Increased Productivity
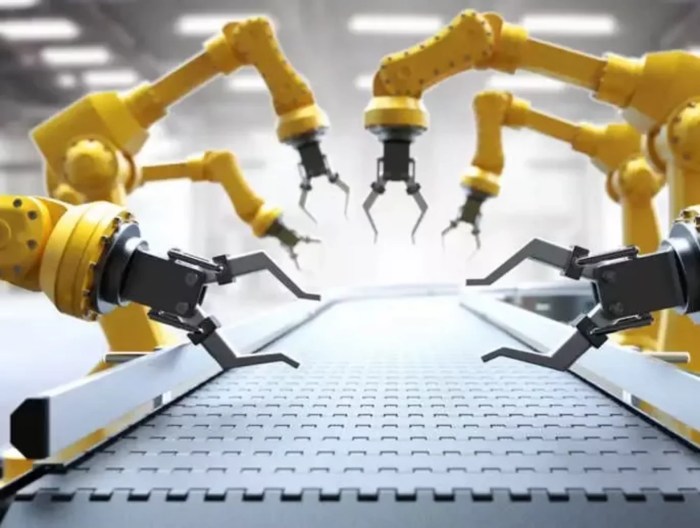
Source: bizclikmedia.net
The integration of robots into manufacturing processes isn’t just about cost-cutting; it’s a fundamental shift towards significantly higher productivity. Robots, unlike human workers, don’t experience fatigue, require breaks, or suffer from decreased performance due to illness. This consistent output translates directly into increased production volume and efficiency. Let’s delve into the specifics of how robotic systems outperform human counterparts in certain scenarios and contribute to a leaner, more efficient manufacturing landscape.
The difference in productivity between human workers and robotic systems is stark, particularly in repetitive tasks. The speed, consistency, and endurance of robots far surpass human capabilities in these scenarios, leading to substantial gains in output.
Productivity Comparison: Humans vs. Robots in Repetitive Tasks
The following comparison highlights the key differences in productivity between human workers and robotic systems when performing repetitive tasks. While human workers excel in adaptability and complex problem-solving, robots shine in speed, consistency, and tireless operation.
- Speed: Robots can perform repetitive actions significantly faster than humans. A robotic arm, for example, can weld or assemble parts at a rate many times greater than a human worker, leading to a substantial increase in units produced per hour.
- Consistency: Robots maintain consistent quality and speed throughout their operation, unlike humans who may experience fatigue or reduced focus over time. This consistency minimizes errors and defects.
- Endurance: Robots can operate continuously for extended periods without breaks, maximizing production time. Human workers, on the other hand, require rest periods and breaks to maintain productivity and prevent fatigue.
- Error Rate: Human error is inevitable, particularly in repetitive tasks. Robots, with their programmed precision, have significantly lower error rates, leading to less waste and rework.
Enhanced Precision and Accuracy: Minimizing Defects and Rework
Beyond sheer speed, robots excel in precision and accuracy. Their movements are controlled with micro-level precision, leading to a reduction in defects and the associated costs of rework. This is especially crucial in industries where even minor imperfections can render a product unusable or require costly repairs.
The enhanced precision translates to less material waste, fewer rejected products, and a significant reduction in the time and resources spent on quality control and rework. This contributes to lower overall manufacturing costs and improved profitability.
Examples of Robotics-Driven Production Output Improvements, The Role of Robotics in Reducing Manufacturing Costs
The impact of robotics on production output is evident across numerous industries. The automotive industry, for example, has long relied on robots for welding, painting, and assembly, dramatically increasing production speed and consistency. Similarly, electronics manufacturing utilizes robots for high-precision tasks like component placement and soldering, ensuring consistent product quality.
In the pharmaceutical industry, robots handle delicate tasks with precision and sterility, ensuring accurate dosage and minimizing contamination risks. The food processing industry also employs robots for tasks such as packaging and palletizing, boosting efficiency and hygiene.
Consider the example of a major automotive manufacturer that implemented robotic welding systems. Before the implementation, human welders produced approximately 500 welds per day with a 2% defect rate. After implementing robotic welding, production increased to 1500 welds per day with a defect rate of less than 0.5%. This significant increase in productivity and reduction in defects demonstrates the transformative power of robotics in manufacturing.
Return on Investment (ROI) of Robotic Systems
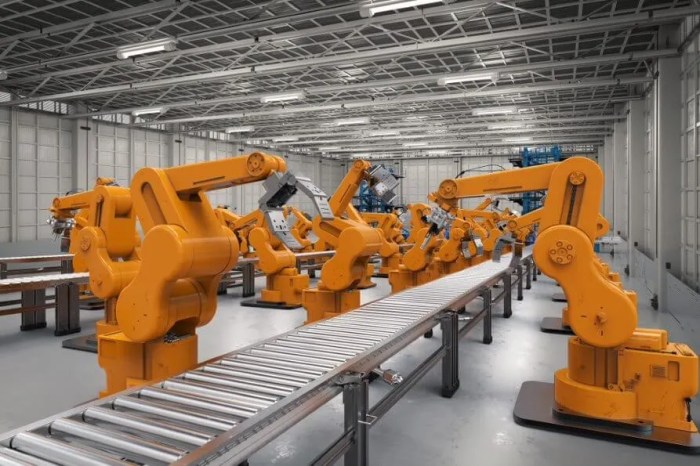
Source: meticulousresearch.com
Implementing robotic systems in manufacturing isn’t a small undertaking; it requires significant upfront investment. However, the potential for long-term cost savings and increased efficiency makes it a compelling proposition for many businesses. Understanding the return on investment (ROI) is crucial for justifying the expenditure and ensuring a successful integration. This section will break down the costs, factors influencing ROI, and offer a simplified model for calculating potential returns.
The initial investment in robotic automation can be substantial, encompassing various components. A thorough cost analysis is essential before proceeding.
Initial Investment Costs
The cost of implementing robotic systems varies greatly depending on the complexity of the application, the type of robots used, and the level of customization required. Here’s a breakdown of the major cost components:
- Hardware Costs: This includes the cost of the robots themselves, which can range from tens of thousands to hundreds of thousands of dollars depending on the model, capabilities, and payload capacity. End-of-arm tooling (EOAT), such as grippers or welding tools, adds to this cost. Consideration should also be given to safety equipment, such as light curtains and safety fences, which are crucial for worker safety.
- Software Costs: Programming and control software is necessary to operate the robots. This can involve purchasing specialized software packages, hiring programmers to develop custom software, or a combination of both. The cost of software can significantly vary depending on the complexity of the tasks the robots will perform and the level of integration required.
- Integration Costs: This involves integrating the robots into the existing manufacturing process. This includes engineering and design work, installation, and testing. This can be a significant cost, especially if the existing infrastructure needs modifications to accommodate the robots. The expertise of specialized integrators can often be required, adding to the overall expense.
Factors Influencing ROI
Several factors influence the speed and magnitude of the ROI of a robotic system. Careful consideration of these factors is critical for accurate ROI projections.
- Production Volume: Higher production volumes generally lead to faster ROI, as the fixed costs of the robotic system are spread over a larger number of units produced. A high-volume manufacturing environment will see quicker returns than a low-volume one.
- Labor Costs: The cost of labor is a key driver in justifying robotic automation. In regions with high labor costs, the potential for savings through robot implementation is significantly higher, leading to faster ROI. This is especially true for repetitive, labor-intensive tasks.
- Maintenance Costs: Regular maintenance is essential for ensuring the continued operation of robotic systems. Maintenance costs should be factored into the ROI calculation. Regular preventative maintenance can help minimize unexpected downtime and costly repairs.
- Downtime and Repair Costs: Unexpected downtime due to malfunction or breakdowns can significantly impact ROI. A robust maintenance plan and readily available spare parts can mitigate this risk.
Simple ROI Calculation Model (5-Year Period)
A simplified model can help illustrate the ROI calculation. This example assumes a consistent production volume and excludes factors like inflation and potential increases in labor costs.
Let’s assume:
- Initial Investment (Hardware + Software + Integration): $200,000
- Annual Labor Cost Savings: $50,000
- Annual Maintenance Cost: $10,000
The annual net savings would be $50,000 (labor savings) – $10,000 (maintenance) = $40,000.
Over 5 years, the total net savings would be $40,000/year * 5 years = $200,000.
In this simplified scenario, the ROI after 5 years would be:
ROI = (Total Net Savings – Initial Investment) / Initial Investment * 100%
ROI = ($200,000 – $200,000) / $200,000 * 100% = 0%
This illustrates a break-even point. In reality, factors like increased productivity and reduced waste would contribute to a positive ROI.
Challenges and Considerations in Robotics Implementation
Integrating robotic systems into manufacturing, while promising significant cost reductions and productivity boosts, isn’t a smooth, straightforward process. Numerous challenges need careful consideration and proactive mitigation strategies to ensure a successful and profitable implementation. Ignoring these hurdles can lead to significant setbacks, wasted investment, and ultimately, failure to realize the expected benefits.
Implementing robotics requires a holistic approach that considers not only the technical aspects but also the human and financial implications. A successful integration hinges on meticulous planning, robust risk management, and a commitment to ongoing maintenance and adaptation.
Initial Investment Costs
The upfront cost of robotic systems can be substantial, encompassing the purchase price of the robots themselves, specialized tooling, integration with existing infrastructure, and necessary software. This significant capital expenditure can be a major deterrent, especially for smaller manufacturing businesses with limited budgets. For example, a single industrial robot arm, depending on its capabilities and features, can cost anywhere from $25,000 to well over $100,000. Adding the costs of programming, installation, and integration easily pushes the total investment into the hundreds of thousands of dollars. This high initial investment necessitates a thorough cost-benefit analysis and a clear understanding of the expected return on investment (ROI) over the robot’s operational lifespan.
Employee Training and Reskilling
Introducing robots into the workplace inevitably leads to changes in job roles and responsibilities. Employees may need retraining to operate and maintain the new robotic systems, requiring investment in training programs and potentially causing temporary disruptions in productivity. This necessitates a proactive approach to employee engagement and upskilling, ensuring that the workforce feels supported and involved in the transition. Failure to address this aspect can lead to resistance, decreased morale, and even skilled labor leaving the company. Companies like FANUC offer extensive training programs for their robotic systems, but internal training programs and partnerships with educational institutions are also crucial for successful integration.
Integration Complexities
Integrating robotic systems into existing manufacturing processes is often complex, requiring careful planning and coordination. The robot needs to seamlessly interact with other machines and systems, potentially requiring modifications to existing infrastructure and processes. This integration process can be time-consuming and costly, potentially leading to delays in project completion and unexpected expenses. For instance, integrating a new robotic welding system into an existing assembly line might necessitate adjustments to the conveyor system, safety protocols, and even the layout of the production floor. Careful planning and the expertise of experienced integration specialists are crucial to minimize these complexities.
Safety Protocols and Risk Mitigation
Robotic systems, while highly efficient, can pose safety risks if not properly implemented and managed. Comprehensive safety protocols, including emergency stop mechanisms, safety guards, and operator training, are essential to mitigate these risks. Regular safety audits and adherence to industry safety standards are crucial to prevent accidents and ensure the well-being of employees. The Occupational Safety and Health Administration (OSHA) in the United States, for example, provides detailed guidelines on the safe operation of industrial robots. Ignoring safety protocols can lead to serious injuries, costly legal battles, and damage to the company’s reputation.
Long-Term Maintenance and Operational Costs
While robots offer long-term cost savings, ongoing maintenance and operational costs are inevitable. These costs include regular maintenance checks, repairs, software updates, and the replacement of worn-out parts. Unexpected breakdowns can also lead to costly downtime and lost production. Developing a proactive maintenance plan, including regular inspections and preventative maintenance, is crucial to minimize these costs and ensure the continued smooth operation of the robotic systems. For instance, regular lubrication of robot joints, periodic calibration, and timely replacement of worn-out components can significantly extend the lifespan of the robotic system and reduce the likelihood of costly breakdowns. This requires establishing a dedicated maintenance team or outsourcing maintenance to specialized service providers.
Future Trends in Robotics and Manufacturing Costs
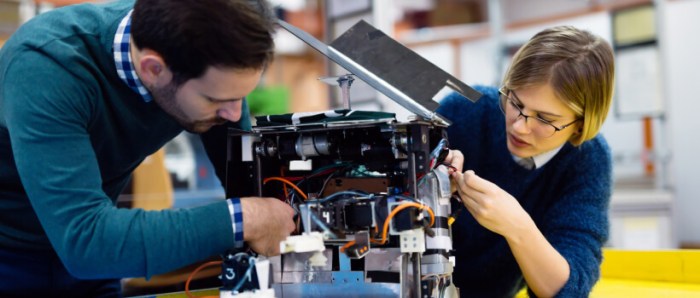
Source: cloudfront.net
The integration of robotics in manufacturing is rapidly evolving, promising even greater cost reductions and increased efficiency in the coming years. Emerging technologies are blurring the lines between traditional automation and intelligent systems, leading to a manufacturing landscape that’s both more productive and adaptable. This section explores these advancements and their implications for the future of work and global competitiveness.
The convergence of several technological advancements is poised to revolutionize manufacturing cost structures. This isn’t just about incremental improvements; we’re talking about paradigm shifts driven by artificial intelligence, advanced sensing, and collaborative robotics.
Emerging Technologies Driving Cost Reduction
The next generation of robots will be far more sophisticated than their predecessors. AI-powered robots, for example, are capable of learning and adapting to changing conditions on the factory floor. This means less downtime due to reprogramming and greater flexibility in handling variations in product design or manufacturing processes. Advanced sensor technologies, such as computer vision and force feedback, enable robots to perform more complex tasks with greater precision, reducing waste and improving product quality. Imagine a robot capable of identifying and correcting minor defects in real-time, eliminating the need for extensive manual quality control checks. This translates directly to lower labor costs and reduced material waste. Furthermore, the development of more robust and durable robots promises to reduce maintenance costs and extend operational lifespans, contributing significantly to long-term cost savings. For instance, self-diagnosing robots capable of predicting maintenance needs can prevent costly unplanned downtime.
Automation’s Impact on the Manufacturing Workforce
The increasing automation of manufacturing processes inevitably raises questions about the future of jobs. While some roles may be displaced by robots, the overall impact is likely to be more nuanced. The demand for skilled workers to program, maintain, and manage robotic systems will increase, requiring a shift in the workforce’s skillset. Reskilling and upskilling initiatives will be crucial to ensure a smooth transition. Companies are already investing in training programs to equip their employees with the necessary expertise to work alongside robots. This collaborative approach, where humans and robots work together, will become increasingly prevalent, leveraging the strengths of both. For example, a human worker might oversee a robotic assembly line, intervening only when necessary, while the robot handles the repetitive and physically demanding tasks. This collaborative model not only boosts productivity but also improves workplace safety.
Long-Term Effects on Manufacturing Costs and Global Competitiveness
The long-term effects of robotics on manufacturing costs are predicted to be substantial. As robotic systems become more sophisticated and affordable, we can expect to see a continuous decline in manufacturing costs across various industries. This will enhance the global competitiveness of regions that embrace robotic automation. Countries that successfully integrate robotics into their manufacturing sectors will be better positioned to attract foreign investment and capture a larger share of the global market. Consider the automotive industry, where robotic automation has already significantly reduced production costs and improved product quality. This has allowed manufacturers to compete effectively on a global scale, offering higher-quality products at competitive prices. However, the full realization of these benefits hinges on effective workforce adaptation and a supportive regulatory environment that fosters innovation and adoption. The successful integration of robotics will depend not only on technological advancements but also on the ability of nations to adapt their workforce and create policies that encourage the widespread adoption of these technologies.
Concluding Remarks
The integration of robotics in manufacturing isn’t just a trend; it’s the future of efficient and cost-effective production. While initial investments can seem daunting, the long-term ROI is undeniable, promising significant returns through increased productivity, reduced waste, and improved precision. As technology continues to advance, we can expect even more dramatic cost reductions and innovative applications, reshaping the manufacturing landscape and pushing the boundaries of what’s possible. The question isn’t *if* you should embrace robotics, but *when* and *how* you’ll integrate them into your operations for maximum impact.