The Role of Robotics in Reducing Human Error in Manufacturing: Forget clunky assembly lines and human-prone mistakes. We’re diving deep into the world of automated precision, where robots aren’t just replacing humans, but enhancing productivity and safety. From collaborative robots teaming up with their human counterparts to AI-powered quality control, this isn’t your grandpa’s factory floor. Get ready for a revolution in efficiency.
This exploration will cover the history of robotics in manufacturing, showcasing the evolution from simple automation to the sophisticated systems we see today. We’ll examine specific examples across various sectors, detailing how robots tackle common human errors in assembly, quality control, and material handling. We’ll also weigh the economic benefits against the challenges, like initial investment and potential job displacement, painting a realistic picture of this rapidly evolving landscape.
Introduction to Robotics in Manufacturing
The integration of robots into manufacturing processes has revolutionized the industry, significantly impacting efficiency, precision, and safety. From its humble beginnings as simple automated arms, robotics has evolved into a sophisticated technology driving innovation across various sectors. This evolution has not only increased production rates but also addressed challenges related to human error and worker safety.
The use of robots in manufacturing isn’t a recent phenomenon; it’s a journey spanning decades. Early industrial robots, primarily hydraulically powered, emerged in the 1960s, performing simple repetitive tasks like welding and material handling. These early adopters, primarily in the automotive industry, paved the way for broader integration across manufacturing sectors. The subsequent decades witnessed significant advancements in robotic capabilities, driven by improvements in computing power, sensor technology, and control systems. This led to the development of more sophisticated robots capable of handling complex tasks with greater precision and flexibility.
The Current State of Robotic Integration in Manufacturing
Currently, robots are deeply embedded in various manufacturing sectors. Automotive manufacturing remains a major user, employing robots extensively in assembly lines, painting, and welding. However, the application of robotics extends far beyond automobiles. Electronics manufacturing utilizes robots for tasks such as circuit board assembly and component placement. The food and beverage industry employs robots for packaging, palletizing, and quality control. Even the pharmaceutical industry uses robots for precise dispensing and handling of delicate medications. This widespread adoption underscores the versatility and increasing importance of robotics in modern manufacturing. The trend is towards collaborative robots (cobots), which work alongside human workers, sharing tasks and enhancing overall efficiency.
Types of Robots Used in Manufacturing and Their Applications
Several types of robots cater to the diverse needs of manufacturing processes. Articulated robots, with their multiple rotary joints, are highly versatile and suitable for a wide range of tasks, from welding and painting to assembly and packaging. Cartesian robots, also known as gantry robots, are characterized by their linear movements along three axes. They excel in applications requiring precise positioning and movement, such as pick-and-place operations in electronics manufacturing. SCARA robots, with their selective compliance articulated robot arm design, are particularly adept at handling tasks requiring both speed and precision, often found in assembly and packaging processes. Finally, collaborative robots (cobots) are designed to work safely alongside human workers, enhancing productivity and improving workplace ergonomics. They are particularly useful in tasks requiring human-robot interaction, such as assisting with assembly or performing quality inspections. For example, a cobot might guide a human worker through a complex assembly process, reducing the chance of errors while improving the worker’s speed and efficiency.
Types of Human Error Reduced by Robotics
Human error is a significant factor in manufacturing, leading to defects, production delays, and even safety hazards. The inherent variability in human performance, coupled with fatigue, distraction, and even simple oversight, makes automation through robotics a compelling solution for enhancing precision and consistency. By replacing humans in certain tasks, or augmenting their capabilities, robots significantly reduce the impact of these common errors.
Robotic systems are designed to perform repetitive tasks with unwavering accuracy and speed, eliminating many sources of human error. This leads to improved product quality, increased efficiency, and a safer work environment. Let’s examine specific types of human error and how robots mitigate them.
Robots are revolutionizing manufacturing, slashing human error rates in assembly and quality control. This precision extends beyond the factory floor; consider how AI is optimizing other processes, like hiring, as detailed in this insightful article: The Role of AI in Streamlining the Hiring Process for Employers. Ultimately, both robotics and AI aim to boost efficiency and minimize costly mistakes, improving overall output and bottom lines.
Assembly Errors
Inconsistent assembly is a frequent problem in manufacturing. Human fatigue, lack of focus, and even slight variations in hand-eye coordination can lead to incorrectly assembled components or missed steps. Robots, programmed with precise assembly sequences, eliminate these inconsistencies. They consistently perform the same actions with the same level of precision, reducing the likelihood of assembly errors dramatically. For example, in electronics manufacturing, robots are crucial for placing tiny components onto circuit boards with sub-millimeter accuracy, a task prone to human error due to the small size and high density of the components.
Quality Control Deficiencies
Human inspectors, while capable of identifying many defects, can suffer from fatigue-induced oversight, leading to inconsistencies in quality control. Robots equipped with vision systems and other sensors can perform consistent and thorough inspections, identifying even minor defects that might escape human notice. These robotic systems can perform continuous monitoring, checking for dimensional accuracy, surface flaws, and other quality parameters, ensuring a higher level of product quality. For instance, a robotic arm with a vision system can inspect car bodies for paint imperfections, detecting inconsistencies far more efficiently than human inspectors.
Material Handling Mistakes
Material handling, involving the movement and storage of raw materials and finished goods, is another area prone to human error. Incorrect placement, damage to materials during handling, and inefficient logistics are common problems. Automated guided vehicles (AGVs) and robotic arms can handle materials with greater precision and efficiency, reducing the risk of damage and improving workflow. For instance, in a warehouse, AGVs can autonomously transport pallets of goods to their designated locations, minimizing the chance of misplacement or damage compared to manual handling.
Task | Human Error Rate | Robotic Error Rate | Improvement Percentage |
---|---|---|---|
Assembly of small electronic components | 5-10% | <1% | 80-90% |
Visual inspection of painted surfaces | 15-20% | 5-7% | 50-70% |
Material handling in a warehouse | 3-5% (damage/misplacement) | <1% | 60-80% |
Specific Robotic Applications and Error Reduction

Source: robotiq.com
The integration of robotics into manufacturing processes isn’t just about automation; it’s a strategic move towards significantly reducing human error and boosting overall efficiency. By automating repetitive tasks and enhancing precision, robots contribute to a higher quality product and a safer work environment. Let’s delve into specific robotic applications showcasing their error-reduction capabilities.
Collaborative Robots (Cobots) in Assembly Lines
Cobots, designed for safe human-robot collaboration, are revolutionizing assembly lines. Their ability to work alongside human workers minimizes the risk of human error in complex assembly tasks. For example, in electronics manufacturing, cobots can precisely place tiny components, a task prone to human fatigue and error. The collaborative nature reduces the need for humans to perform monotonous, high-precision operations, leading to fewer assembly errors and improved overall throughput. This symbiotic relationship allows humans to focus on more complex tasks requiring judgment and problem-solving, while cobots handle the repetitive, precision-oriented steps.
Vision Systems and AI in Quality Control
Vision systems integrated with artificial intelligence (AI) are transforming quality control. These systems use cameras and sophisticated algorithms to inspect products for defects at speeds and accuracies far exceeding human capabilities. For instance, a vision system can identify minute scratches or imperfections on a painted car body that a human inspector might miss, leading to a significant reduction in the number of defective products shipped. AI algorithms further enhance this process by learning from past inspections, continuously improving their accuracy in identifying and classifying defects. This automated quality control drastically reduces the reliance on human inspection, minimizing human error and ensuring consistently high product quality.
Automated Guided Vehicles (AGVs) in Material Handling
Automated Guided Vehicles (AGVs) are playing a crucial role in optimizing material handling and minimizing human error in logistics. AGVs autonomously transport materials within a manufacturing facility, eliminating the risk of human error associated with manual material handling, such as misplacement or damage. These vehicles follow pre-programmed routes, ensuring timely and accurate delivery of materials to different workstations. This streamlined material flow minimizes delays and reduces the likelihood of production disruptions caused by human error in logistics. For example, in a large warehouse, AGVs can precisely deliver parts to assembly lines, reducing the risk of shortages or incorrect materials being used, thereby increasing overall efficiency and product quality.
Robotic-Assisted Manufacturing Process Flowchart
The following flowchart illustrates a simplified robotic-assisted manufacturing process, highlighting error reduction at each stage:
[Imagine a flowchart here. The flowchart would begin with “Raw Material Input,” followed by “Robotic Material Handling (AGVs),” where the error reduction would be noted as “Reduced risk of misplacement or damage.” The next step would be “Robotic Assembly (Cobots),” with error reduction noted as “Increased precision and consistency, reduced human fatigue errors.” Then, “Quality Control (Vision Systems & AI),” with error reduction noted as “Automated defect detection, higher accuracy than human inspection.” Finally, “Finished Product Output,” with error reduction implicitly shown through the previous steps.] Each step in this process utilizes robotic technologies to minimize human intervention and the associated risks of human error. The cumulative effect is a significant improvement in product quality and manufacturing efficiency.
Economic and Safety Benefits of Robotics
The integration of robots into manufacturing processes isn’t just about improving accuracy; it’s a significant investment yielding substantial economic and safety returns. Reduced human error translates directly into lower operational costs, increased productivity, and a dramatically safer work environment. Let’s delve into the specifics of these benefits, exploring how robots are reshaping the manufacturing landscape for the better.
The financial advantages of robotic automation are compelling. By minimizing human error, companies can avoid the substantial costs associated with defects, rework, scrap materials, and downtime. This translates into increased efficiency and higher profit margins. Moreover, the long-term investment in robotics often outweighs the short-term expenses, leading to a positive return on investment (ROI) over time. This is particularly true when considering the increasing costs of labor and the ever-present risk of human error in complex manufacturing processes.
Cost Savings from Reduced Human Error
Studies have consistently shown a significant correlation between robotic automation and cost reduction in manufacturing. A report by the Boston Consulting Group (BCG) estimated that companies using advanced robotics could reduce their manufacturing costs by up to 20% by 2025. This reduction stems primarily from decreased waste, improved efficiency, and the elimination of errors associated with manual labor. For example, a car manufacturer implementing robotic welding systems experienced a 15% reduction in defects, directly translating to a 10% decrease in production costs. This cost reduction includes not only the direct cost of fixing errors but also the indirect costs associated with lost time, customer dissatisfaction, and potential legal liabilities.
Improved Workplace Safety through Automation of Hazardous Tasks
Robotics plays a crucial role in enhancing workplace safety by automating dangerous or repetitive tasks. This is particularly beneficial in industries involving heavy machinery, hazardous materials, or physically demanding operations. Robotic systems can handle tasks such as welding, painting, and material handling in environments unsuitable for humans, reducing the risk of injuries such as burns, chemical exposure, and musculoskeletal disorders. For instance, in the automotive industry, robots perform spot welding, a process that exposes workers to high temperatures and potential burns. Replacing human workers with robots eliminates this risk, resulting in a safer working environment and lower workers’ compensation costs.
Real-World Case Studies
Consider the case of a large electronics manufacturer that implemented robotic assembly lines. Prior to automation, human error led to a significant number of defective products, resulting in substantial rework costs and customer complaints. After the implementation of robots, the defect rate dropped by 30%, leading to a 20% increase in production efficiency and a 15% reduction in overall manufacturing costs. Similarly, a chemical plant using robotic systems for handling hazardous materials reported a 50% reduction in workplace accidents, resulting in significant savings on medical expenses and insurance premiums.
Financial Impact Comparison: Human Error vs. Robotic Solutions, The Role of Robotics in Reducing Human Error in Manufacturing
The following table compares the financial impact of human error with the investment in robotic solutions, illustrating the long-term benefits of automation:
Factor | Human Error Costs | Robotic Solution Costs |
---|---|---|
Initial Investment | Relatively low (initial training, wages) | High (purchase, installation, maintenance) |
Recurring Costs | High (wages, benefits, training, error correction) | Moderate (maintenance, repairs, software updates) |
Defect Rate | High (leading to rework, scrap, customer dissatisfaction) | Low (resulting in higher quality and reduced waste) |
Productivity | Variable, susceptible to fatigue and errors | High and consistent (24/7 operation) |
Safety Incidents | High potential for workplace accidents | Significantly reduced (automation of hazardous tasks) |
Long-Term ROI | Potentially negative due to accumulating error costs | Generally positive due to efficiency gains and reduced costs |
Challenges and Future Trends: The Role Of Robotics In Reducing Human Error In Manufacturing
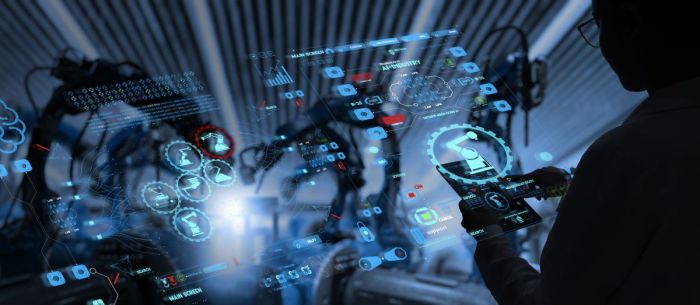
Source: nividous.com
The integration of robotics into manufacturing, while promising significant advancements, isn’t without its hurdles. Successfully navigating these challenges and capitalizing on future trends will be crucial for reaping the full benefits of robotic automation. A balanced approach, addressing both the immediate obstacles and long-term possibilities, is essential for a smooth transition towards a more efficient and error-reduced manufacturing landscape.
Implementing robotics requires a strategic approach that considers various factors beyond simply purchasing and installing the machines. This involves careful planning, substantial investment, and a commitment to ongoing adaptation as technology evolves.
Initial Investment Costs and Integration Complexities
The high upfront costs associated with robotic systems, including purchase, installation, and integration, can be a significant barrier to entry, particularly for smaller manufacturers. This initial investment often includes specialized programming, training for personnel, and potentially modifications to existing infrastructure. For example, a small-batch manufacturer might find the cost of a fully automated robotic welding cell prohibitive compared to their current manual processes. Furthermore, integrating robots into existing production lines can be complex, requiring careful planning and potentially disrupting ongoing operations. This integration process often necessitates modifications to existing workflows and potentially retraining of existing staff.
Job Displacement Concerns and Workforce Adaptation
The introduction of robots into manufacturing naturally raises concerns about job displacement. While robots automate certain tasks, they also create new opportunities in areas like robotics maintenance, programming, and system integration. A proactive approach to workforce retraining and upskilling is crucial to mitigate these concerns and ensure a smooth transition for employees. For instance, companies like FANUC offer extensive training programs for their robotic systems, enabling existing workers to transition into roles related to robotic maintenance and programming. Ignoring this aspect can lead to resistance and hinder the successful implementation of robotic systems.
Advancements in Artificial Intelligence and the Internet of Things
The convergence of AI and IoT is poised to revolutionize manufacturing robotics. AI-powered robots can adapt to changing conditions, learn from experience, and make independent decisions, leading to further error reduction. IoT integration allows for real-time monitoring of robotic systems, predictive maintenance, and enhanced data analysis for continuous improvement. For example, a smart factory utilizing IoT sensors and AI-powered robots can detect anomalies in a production line in real-time, allowing for immediate intervention and preventing potential errors from escalating. This proactive approach minimizes downtime and ensures consistent product quality.
Strategies for Addressing Challenges and Maximizing Benefits
Successfully integrating robotics requires a multi-faceted strategy. This includes careful financial planning, thorough risk assessment, and a strong focus on employee training and development. Phased implementation, starting with specific tasks or processes, can help mitigate risks and allow for gradual adaptation. Collaboration between manufacturers, robotics companies, and educational institutions is crucial for developing tailored training programs and ensuring a skilled workforce. Furthermore, government incentives and support programs can play a vital role in encouraging wider adoption of robotic technologies.
Augmented Reality and Human-Robot Collaboration
Augmented reality (AR) is emerging as a powerful tool for enhancing human-robot collaboration. AR overlays digital information onto the real world, providing workers with real-time data, guidance, and instructions during tasks involving robots. This improves efficiency, reduces errors, and ensures safer interactions between humans and robots. For instance, AR headsets can guide technicians through complex robot maintenance procedures, reducing the risk of errors and improving overall productivity. The combination of AR and collaborative robots (cobots) enables a seamless integration of human expertise and robotic capabilities, leading to a more efficient and safer work environment.
Final Review
The integration of robotics in manufacturing isn’t just about efficiency; it’s about creating a safer, more productive, and ultimately, more innovative future. While challenges remain, the potential for error reduction, cost savings, and enhanced workplace safety is undeniable. As AI and other technologies continue to advance, the collaboration between humans and robots will only become more seamless, ushering in a new era of precision and efficiency in the manufacturing world. The future is automated, and it’s looking pretty bright.