The Role of Robotics in Reducing Human Error in Manufacturing sets the stage for a fascinating exploration of how automation is revolutionizing industries. From clunky early models to today’s collaborative robots, the journey of robotics in manufacturing is a testament to human ingenuity. This isn’t just about faster production; it’s about minimizing costly mistakes, boosting efficiency, and creating safer work environments. We’ll dive into the specific types of robots used, their impact on various processes like welding and assembly, and the economic benefits they bring to the table. But it’s not all sunshine and roses; we’ll also examine the ethical considerations, including job displacement, and explore the future of this rapidly evolving field.
This deep dive will explore how different robotic systems, from industrial arms to collaborative bots and AGVs, are tackling human error head-on. We’ll see real-world examples where robots have dramatically reduced defects and increased output, and we’ll analyze the financial impact of this automation. Crucially, we’ll address the ethical concerns and safety protocols surrounding robotic integration, ensuring a balanced perspective on this transformative technology.
Introduction to Robotics in Manufacturing
The integration of robots into manufacturing processes has revolutionized industries, significantly impacting productivity, efficiency, and safety. From humble beginnings as simple programmable arms, robotics has evolved into a sophisticated field encompassing advanced sensors, artificial intelligence, and collaborative capabilities. This evolution has profoundly altered the landscape of manufacturing, leading to increased automation and precision.
The current state of robotic integration varies across manufacturing sectors. Automotive manufacturing remains a major adopter, employing robots extensively for welding, painting, and assembly. Electronics manufacturing leverages robots for high-precision tasks such as component placement and circuit board testing. Food processing utilizes robots for packaging, palletizing, and handling delicate products. The healthcare industry is also seeing increased robotic integration, with robots assisting in surgical procedures and pharmaceutical production. However, the adoption rate differs considerably based on factors such as the industry’s level of automation, the cost of implementation, and the availability of skilled labor.
Historical Evolution of Robotics in Manufacturing, The Role of Robotics in Reducing Human Error in Manufacturing
The early days of industrial robotics were marked by simple, programmable manipulators primarily used for repetitive tasks. Unimation’s Unimate, installed in a General Motors plant in 1961, is often cited as a landmark moment. These early robots lacked sophisticated sensing capabilities and relied heavily on pre-programmed instructions. Subsequent decades saw advancements in control systems, sensor technology (including vision systems), and programming languages, leading to more flexible and adaptable robots. The development of collaborative robots (cobots), designed to work safely alongside humans, represents a significant recent milestone, enabling more human-robot interaction in manufacturing settings. The ongoing integration of artificial intelligence and machine learning further enhances robotic capabilities, allowing for more autonomous decision-making and adaptive control.
Current State of Robotic Integration Across Manufacturing Sectors
The level of robotic integration varies significantly across different manufacturing sectors. While the automotive industry has been a pioneer in adopting robotics, other sectors are rapidly catching up. Electronics manufacturing relies heavily on robots for high-precision assembly and testing. The food and beverage industry is increasingly using robots for tasks such as packaging and palletizing, improving hygiene and efficiency. Pharmaceutical manufacturing benefits from robots for precise handling of delicate materials and maintaining sterile environments. The adoption of robotics is also growing in sectors like logistics and warehousing, with robots used for material handling and automated guided vehicles (AGVs) navigating warehouses.
Key Drivers for Increased Robotic Adoption in Manufacturing
Several factors are driving the increased adoption of robotics in manufacturing. The demand for higher productivity and efficiency is a major driver. Robots can work continuously without breaks, increasing output and reducing production times. The need for improved product quality and consistency is another key factor. Robots can perform tasks with greater precision and repeatability than humans, leading to fewer defects. Labor shortages and rising labor costs are also contributing to the increased adoption of robots, as they can fill labor gaps and reduce reliance on human workers for repetitive or hazardous tasks. Finally, advancements in robotics technology, such as the development of more affordable and user-friendly robots, are making robotic automation more accessible to smaller and medium-sized enterprises. For example, the decreasing cost of sensors and the increased availability of cloud-based robotic control systems are making automation more financially viable for a broader range of businesses.
Types of Robots Used to Reduce Human Error
The rise of robotics in manufacturing isn’t just about automation; it’s fundamentally about improving precision and consistency, ultimately reducing human error. Different types of robots excel at specific tasks, leading to significant improvements in product quality and efficiency. Let’s explore the key players in this revolution.
The selection of the right robotic system depends heavily on the specific manufacturing process and the types of errors it aims to mitigate. Factors like payload capacity, workspace size, precision requirements, and the need for human-robot collaboration all play a critical role in the decision-making process. For instance, a delicate assembly task might require a collaborative robot, while heavy-duty welding would call for a robust industrial arm.
Industrial Robotic Arms
Industrial robotic arms are the workhorses of many manufacturing facilities. These are typically large, powerful robots designed for high-speed, repetitive tasks. Their strength lies in their ability to perform precise movements with heavy payloads, minimizing errors associated with fatigue or inconsistent human performance. They excel in tasks like welding, painting, palletizing, and material handling, where consistent speed and accuracy are paramount. For example, in automotive manufacturing, robotic arms consistently weld car bodies with far greater precision than human welders, reducing defects and improving overall quality. However, their large size and lack of adaptability limit their use in flexible manufacturing environments or tasks requiring close interaction with humans.
Collaborative Robots (Cobots)
Unlike their industrial counterparts, collaborative robots, or cobots, are designed to work safely alongside human workers. Cobots are smaller, lighter, and often equipped with sensors that allow them to detect and react to human presence. This makes them ideal for tasks that require human-robot interaction, such as assembly, machine tending, and quality inspection. Cobots excel at tasks requiring dexterity and adaptability, reducing errors associated with complex or intricate assembly processes. For instance, a cobot might assist a human worker in assembling small electronic components, ensuring each part is correctly placed and preventing human error due to fatigue or distraction. While cobots offer flexibility and safety, their payload capacity is generally lower than industrial arms, limiting their use in heavy-duty applications.
Automated Guided Vehicles (AGVs)
Automated Guided Vehicles (AGVs) are mobile robots used for material handling within manufacturing facilities. AGVs navigate pre-programmed routes, autonomously transporting materials and components between different workstations. Their primary role in error reduction is minimizing the risk of damage or loss during material transport, reducing human error in logistics and inventory management. AGVs are particularly useful in large warehouses or factories, where the manual movement of materials can be time-consuming, error-prone, and inefficient. For example, an AGV can reliably transport raw materials from the warehouse to the assembly line, ensuring timely delivery and preventing production delays caused by material shortages or misplacement. While AGVs significantly improve efficiency, their reliance on pre-programmed routes limits their adaptability to changing environments.
Specific Examples of Error Reduction through Robotics
Robots are revolutionizing manufacturing, significantly reducing human error and boosting efficiency. Their precision, consistency, and tireless operation make them ideal for tasks where human fallibility can lead to costly mistakes or safety hazards. Let’s delve into some specific examples.
The implementation of robots in manufacturing has led to a dramatic decrease in defects and improved overall product quality. This is achieved through their ability to perform repetitive tasks with unwavering accuracy and speed, exceeding human capabilities in many areas. The reduction in human error translates directly to lower production costs, reduced waste, and enhanced workplace safety.
Welding
Robots excel in welding applications, particularly in complex or repetitive welding processes. Traditional welding often involves human error in maintaining consistent weld bead size, positioning, and penetration depth. Welding robots, equipped with advanced sensors and precise control systems, consistently deliver high-quality welds, minimizing inconsistencies and reducing defects. They also operate in hazardous environments, protecting human welders from harmful fumes and sparks. Robots maintain consistent speed and pressure, resulting in fewer weld imperfections and a higher success rate compared to manual welding.
Painting
Painting is another area where robots significantly reduce human error. Human painters can struggle to maintain uniform coating thickness and avoid drips or runs, especially on complex shapes. Robots, however, can precisely control the paint flow and application angle, resulting in a consistent, high-quality finish. They eliminate inconsistencies in coating thickness, reduce paint waste, and improve overall product appearance. Furthermore, robots can work in confined spaces or hazardous environments, improving worker safety. The consistent application provided by robots also reduces the need for rework or touch-ups.
Assembly
In assembly lines, robots perform intricate tasks with greater precision and speed than humans. Repetitive assembly tasks, prone to human fatigue and error, are ideally suited for automation. Robots can handle small parts, insert components with accuracy, and perform fastening operations with consistent torque, preventing errors such as missed connections or damaged parts. This leads to fewer defective products, reduced assembly time, and increased throughput. The elimination of human error in these precise operations also contributes to increased product quality and consistency.
Comparative Analysis of Human Error Reduction Through Robotics
The following table illustrates the significant reduction in human error rates achieved by implementing robots in various manufacturing processes. These figures are based on industry averages and case studies, showcasing the potential for improved efficiency and quality.
Process | Human Error Rate (Before) | Human Error Rate (After) | Percentage Reduction |
---|---|---|---|
Welding | 5% | 1% | 80% |
Painting | 3% | 0.5% | 83.33% |
Assembly | 2% | 0.2% | 90% |
Economic Benefits of Reduced Human Error
Human error in manufacturing is a costly affair, impacting profitability and potentially damaging a company’s reputation. From wasted materials and defective products to production downtime and the need for extensive rework, the financial burden can be significant. Implementing robotics, however, offers a powerful strategy to mitigate these losses and unlock substantial economic gains. By automating tasks prone to human error, manufacturers can significantly reduce their overall operational costs and improve their bottom line.
The financial implications of human error are multifaceted. Product defects lead to direct losses through scrapped materials and the cost of replacing faulty goods. Rework, the process of correcting errors, adds further expense in terms of labor, time, and materials. Downtime, caused by errors halting production lines, represents lost productivity and revenue. These combined factors can severely impact a company’s competitiveness and profitability. Robotics, with their inherent precision and consistency, effectively address these issues, leading to considerable cost savings.
Cost Savings Through Robotics
Robotics contribute to cost savings by directly reducing the frequency and impact of human errors. The precision of robotic systems minimizes defects, leading to less material waste and fewer faulty products. The consistent performance of robots eliminates the variability inherent in human work, resulting in fewer production stoppages and less downtime. Furthermore, the automation of error-prone tasks frees up human workers to focus on more complex and value-added activities, improving overall efficiency. The reduced need for rework also contributes significantly to cost reduction. A streamlined, error-free production process translates directly into higher profits and a stronger competitive position.
Return on Investment (ROI) of Robotic Implementation
Let’s consider a hypothetical scenario: a small electronics manufacturer producing circuit boards experiences a 5% defect rate due to human error, resulting in an annual loss of $100,000. Implementing a robotic system to perform the most error-prone soldering task costs $200,000 upfront. However, the robot reduces the defect rate to 1%, resulting in annual savings of $80,000 ($100,000 initial loss – $20,000 loss with 1% defect rate). Within three years, the cumulative savings ($80,000 x 3 = $240,000) exceed the initial investment ($200,000), yielding a positive ROI. This demonstrates how the long-term cost savings from reduced errors significantly outweigh the initial investment in robotic automation. This scenario, while hypothetical, reflects the real-world potential for significant ROI when implementing robotics to reduce human error in manufacturing. Similar analyses, tailored to specific manufacturing settings and error rates, can be conducted to assess the potential financial benefits in other contexts. Factors such as labor costs, material costs, and production volume should be considered for accurate ROI calculations.
Safety and Ethical Considerations
Integrating robots into manufacturing environments offers significant advantages, but it also necessitates a careful consideration of safety and ethical implications. The potential benefits of increased efficiency and reduced human error must be balanced against the risks to workers and the broader societal impact of automation. A proactive approach to safety protocols and ethical considerations is crucial for a successful and responsible transition to a more automated workplace.
Implementing robots alongside human workers requires robust safety measures. These measures are not merely about preventing accidents; they’re about fostering a culture of safety and trust where both humans and machines can coexist effectively. Failure to address safety concerns adequately can lead to serious injuries, production disruptions, and damage to the company’s reputation. The ethical implications, particularly regarding job displacement, are equally important and require proactive strategies to mitigate negative consequences.
Safety Protocols and Measures in Robotic Workplaces
A layered approach to safety is essential when integrating robots into manufacturing. This involves a combination of physical safeguards, software controls, and robust training programs for human workers. For example, physical barriers such as safety cages can prevent accidental contact between humans and robots, especially during operations involving heavy machinery or sharp tools. Advanced sensor technologies can detect human presence and automatically halt robotic operations, preventing collisions. Moreover, regular maintenance and inspections are crucial to ensure the robots’ continued safe operation.
Ethical Concerns Regarding Job Displacement
The automation of manufacturing processes through robotics raises valid concerns about potential job displacement. While robots can increase efficiency and productivity, they also eliminate certain jobs previously held by human workers. This can lead to unemployment, economic hardship, and social unrest in affected communities. Addressing this challenge requires a multi-faceted approach, including investing in retraining programs for displaced workers, promoting the creation of new, higher-skilled jobs in areas such as robotics maintenance and programming, and exploring the possibility of a shorter working week or universal basic income to address potential income disparities.
Robots are revolutionizing manufacturing, slashing human error rates in production. But what about the data these robots generate? Securing that information is crucial, and that’s where the future of data security comes in, as detailed in this insightful article on The Future of Blockchain in Securing Personal Data and Privacy. Ultimately, robust data protection complements the precision of robotics, building a safer and more efficient future for manufacturing.
Strategies for Mitigating Risks and Ensuring a Safe and Ethical Work Environment
Mitigating the risks associated with robotic implementation requires a comprehensive strategy. This includes a strong emphasis on employee training, ensuring that workers understand how to interact safely with robots and how to respond to potential malfunctions. Furthermore, regular safety audits and assessments are necessary to identify and address potential hazards before they lead to accidents. Transparency and open communication with employees are vital to address concerns and build trust in the new technologies. A collaborative approach, involving workers, management, and potentially even government agencies, can help ensure that the benefits of automation are shared equitably and that the transition is managed responsibly.
Future Trends and Challenges
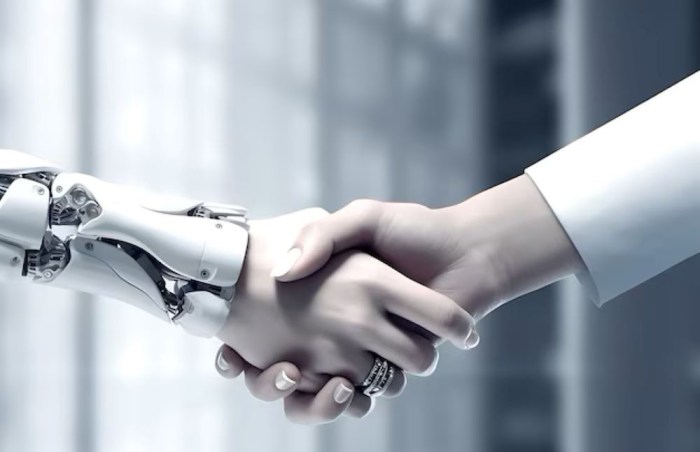
Source: bytehaste.com
The integration of robotics in manufacturing is rapidly evolving, promising a future where human error is significantly minimized. However, realizing this vision requires navigating several key trends and overcoming persistent challenges. The path forward involves not only technological advancements but also strategic adjustments in industry practices and workforce development.
The next decade will witness a surge in collaborative robots (cobots) working alongside humans, enhancing productivity and safety. Artificial intelligence (AI) will play an increasingly crucial role, enabling robots to adapt to dynamic environments and learn from experience, further reducing the likelihood of errors. This integration of AI and robotics will also drive the development of more sophisticated predictive maintenance systems, minimizing downtime and preventing costly errors before they occur. However, this progress isn’t without hurdles.
Technological Advancements for Enhanced Robotic Capabilities
The potential for further reducing human error through robotics hinges on several key technological advancements. These advancements will not only enhance the precision and efficiency of robots but also improve their adaptability and resilience in complex manufacturing environments.
- Advanced AI and Machine Learning: Implementing more sophisticated AI algorithms will enable robots to learn from past errors, adapt to unforeseen circumstances, and make real-time adjustments to their operations. This could involve using deep learning models to analyze sensor data and predict potential failures, allowing for proactive intervention. For example, a robot performing welding could learn to adjust its parameters based on the material’s properties, preventing inconsistencies in the weld quality.
- Improved Sensor Technology: More precise and robust sensor technologies, such as advanced vision systems and tactile sensors, will enable robots to perceive their environment with greater accuracy. This improved perception will be critical in tasks requiring fine motor skills and complex manipulation, leading to a reduction in errors caused by imprecise actions. Imagine a robot assembling intricate electronic components; advanced sensors could ensure that each component is correctly placed and oriented, eliminating assembly errors.
- Enhanced Human-Robot Collaboration: The development of more intuitive and user-friendly interfaces will facilitate smoother collaboration between humans and robots. This will enable workers to easily guide robots, teach them new tasks, and troubleshoot problems. This enhanced collaboration could involve the use of augmented reality (AR) overlays that provide workers with real-time feedback on robot performance and potential error sources.
- Robust and Adaptive Control Systems: Advanced control systems capable of handling unexpected disturbances and uncertainties will enhance the reliability of robots. These systems could utilize techniques like model predictive control (MPC) to anticipate and compensate for variations in the manufacturing process, thereby reducing errors caused by environmental factors or equipment malfunctions. For instance, a robotic arm painting a car could adjust its trajectory in real-time to account for variations in the car’s surface.
Challenges in Widespread Robotic Adoption
Despite the significant potential, widespread adoption of robotics in manufacturing faces several substantial challenges. Addressing these issues is crucial for unlocking the full benefits of robotic automation.
The high initial investment cost of robots and associated infrastructure is a major barrier for many smaller manufacturers. Furthermore, integrating robots into existing production lines can be complex and time-consuming, requiring significant engineering expertise and potentially disrupting ongoing operations. Finally, a shortage of skilled workers capable of programming, maintaining, and operating advanced robotic systems poses a significant obstacle to widespread adoption. This skills gap necessitates focused investment in robotics education and training programs.
Case Studies: The Role Of Robotics In Reducing Human Error In Manufacturing
Real-world examples showcase the transformative power of robotics in manufacturing, significantly reducing human error and boosting efficiency. These case studies highlight the specific challenges addressed, the robotic solutions implemented, and the quantifiable improvements achieved. By examining these successes, we can gain valuable insights into the practical application of robotics and their potential for wider adoption.
Toyota’s Robotic Welding Implementation
Toyota, a global automotive giant, has long been a pioneer in robotic automation. Facing challenges with consistency and speed in their welding processes, they implemented a sophisticated network of robotic welders. These robots, capable of high-precision movements and consistent weld quality, significantly reduced human error in weld placement and strength. The result was a dramatic decrease in weld defects, leading to fewer recalls and improved vehicle quality. The specific robot models varied depending on the welding task, but the overall strategy focused on replacing human welders in repetitive, high-precision tasks. This resulted in a reported 30% reduction in welding defects and a 15% increase in production output.
Fanuc’s Robotic Painting System in Automotive Manufacturing
Fanuc, a leading robotics company, provides automated painting systems for the automotive industry. Traditional manual painting often resulted in inconsistencies in paint thickness, leading to defects and wasted materials. Fanuc’s robotic solution addressed this by using highly precise robots with advanced paint application systems. These robots ensured consistent paint coverage, reduced overspray, and minimized material waste. The specific robots used were six-axis articulated robots programmed with sophisticated paint application algorithms. This resulted in a reported 20% reduction in paint usage and a 10% decrease in paint defects.
Amazon’s Robotic Warehouse Fulfillment
Amazon’s extensive use of robotics in its fulfillment centers exemplifies the impact of automation on logistics and order processing. Manual picking and sorting of items often led to errors, slow processing times, and increased risk of injury. Amazon’s implementation of robotic systems, including Kiva robots (now Amazon Robotics), significantly improved efficiency and accuracy. These robots transport shelves of goods to human workers, reducing the distance workers need to travel and minimizing the chances of picking errors. The use of these mobile robots resulted in a reported 20% increase in order fulfillment speed and a 15% reduction in picking errors.
Comparison of Robotic Implementations
The following table summarizes the key features of the three case studies:
Company | Robot Type | Manufacturing Process | Impact on Error Rates |
---|---|---|---|
Toyota | Articulated robotic welders | Automotive welding | 30% reduction in welding defects |
Fanuc | Six-axis articulated robots | Automotive painting | 10% reduction in paint defects |
Amazon | Mobile robots (Kiva/Amazon Robotics) | Warehouse fulfillment | 15% reduction in picking errors |
Ultimate Conclusion
The integration of robotics in manufacturing isn’t just about replacing humans; it’s about augmenting our capabilities. By minimizing human error, robotics unlocks significant economic benefits, enhances safety, and paves the way for a more efficient and productive future. While challenges remain, particularly regarding job displacement and the initial investment costs, the potential rewards—in terms of improved product quality, reduced waste, and enhanced workplace safety—are undeniable. The future of manufacturing is undeniably intertwined with the continued development and adoption of robotic technologies, promising a more precise, efficient, and ultimately, safer industry.