The Role of Robotics in Modern Manufacturing isn’t just about machines; it’s a revolution reshaping how we build everything. From the assembly line’s rhythmic whir to the precision of a robotic welder, automation’s impact is undeniable. This isn’t your grandpa’s factory floor – we’re talking AI-powered systems, collaborative robots working alongside humans, and a future where the only limit is our imagination. Get ready to explore the fascinating world where metal meets mind-blowing tech.
This deep dive examines the history of robotics in manufacturing, exploring the different types of robots used, their applications, and the economic and societal ripples they create. We’ll also peek into the future, envisioning a manufacturing landscape dominated by advanced robotics and the challenges we’ll need to overcome to get there. Buckle up, it’s going to be a wild ride!
Introduction to Robotics in Modern Manufacturing
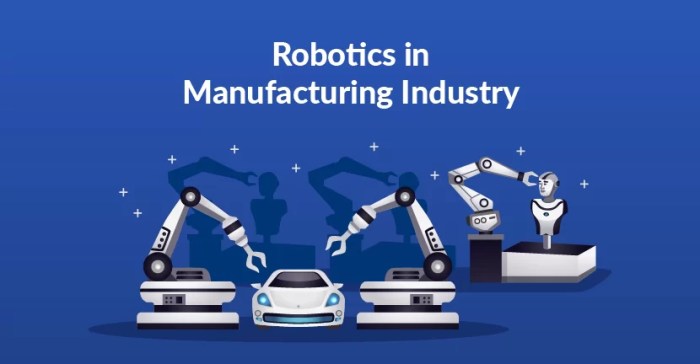
Source: alp.consulting
The integration of robots into manufacturing processes has revolutionized the industry, transforming how goods are produced and impacting global economies. From its humble beginnings as simple automated arms, robotics has evolved into a sophisticated field, driving efficiency and innovation across various sectors. This section explores the historical progression of robotics in manufacturing, the factors fueling its widespread adoption, and the diverse types of robots currently employed.
Historical Evolution of Robotics in Manufacturing
The journey of robotics in manufacturing began in the mid-20th century, initially driven by the need for automation in repetitive and dangerous tasks. Early industrial robots were primarily large, hydraulically powered manipulators designed for simple pick-and-place operations. The development of microprocessors and advanced control systems in the late 20th century marked a significant turning point, leading to more flexible, programmable robots capable of performing complex tasks. The rise of computer vision and artificial intelligence further propelled advancements, enabling robots to interact more intelligently with their environments and adapt to changing conditions. Today, collaborative robots (cobots) are emerging, designed to work safely alongside human workers, fostering a new era of human-robot collaboration in manufacturing.
Key Drivers for Increased Robotics Adoption in Manufacturing
Several key factors have significantly accelerated the adoption of robotics in modern manufacturing. The relentless pursuit of increased productivity and efficiency is a major driver. Robots can work continuously without breaks, performing tasks with greater speed and precision than humans, leading to higher output and reduced production times. Furthermore, the demand for improved product quality and consistency is another significant push. Robots minimize human error, leading to more consistent product quality and reduced waste. The rising cost of labor in many countries has also made automation, through robotics, a more economically viable option. Finally, the ongoing advancements in robotics technology, such as improved sensors, more sophisticated software, and increased affordability, have made robots more accessible and versatile for a wider range of manufacturing applications.
Types of Robots Used in Modern Manufacturing
The following table showcases some of the prevalent types of robots used in modern manufacturing environments, highlighting their applications, advantages, and disadvantages.
Robot Type | Application | Advantages | Disadvantages |
---|---|---|---|
Articulated Robots | Welding, painting, assembly, material handling | High dexterity, flexibility, wide range of motion | Can be complex to program, requires significant workspace |
Cartesian Robots (Gantry Robots) | Pick and place, dispensing, packaging | Simple design, high speed and accuracy, large workspace | Limited dexterity, less flexible than articulated robots |
SCARA Robots | Assembly, pick and place, packaging | High speed and accuracy in a planar motion, cost-effective | Limited dexterity, less flexible than articulated robots |
Collaborative Robots (Cobots) | Machine tending, assembly, quality inspection | Safe to work alongside humans, easy to program, flexible deployment | Lower payload capacity compared to industrial robots, relatively higher cost |
Types of Robotic Applications in Manufacturing
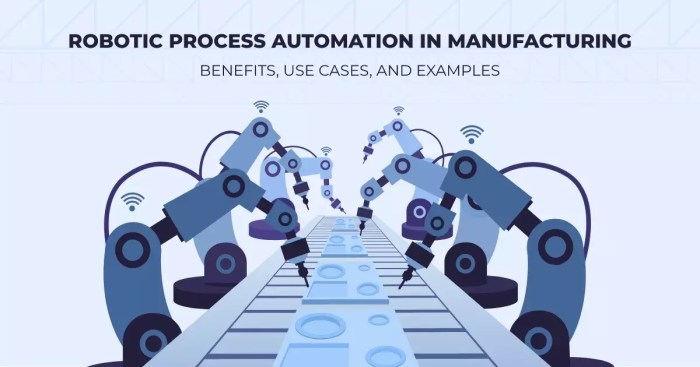
Source: imaginovation.net
Robotics are revolutionizing modern manufacturing, boosting efficiency and precision. This same robotic prowess extends beyond Earth; check out The Role of Robotics in Space Exploration to see how they’re tackling the challenges of the cosmos. Ultimately, the innovations driving robotic advancements in space directly impact the development of more sophisticated manufacturing robots here on Earth, creating a fascinating feedback loop of progress.
Robots are no longer just sci-fi fantasies; they’re the backbone of modern manufacturing, boosting efficiency and precision in ways previously unimaginable. Their applications span a wide range of processes, revolutionizing how goods are produced. Let’s dive into the specifics of how robots are transforming various aspects of the manufacturing landscape.
Robotic Assembly Line Operations
Robots have become indispensable in assembly line operations, performing repetitive tasks with speed and accuracy far exceeding human capabilities. This not only increases production rates but also minimizes errors, leading to higher quality products. The use of robots in assembly allows manufacturers to optimize their production lines for maximum efficiency.
- Part feeding and placement: Robots precisely pick and place components onto the assembly line, ensuring accurate positioning for subsequent operations.
- Fastening and joining: Robots perform tasks such as screwing, bolting, riveting, and welding with consistent force and precision.
- Material dispensing: Robots apply adhesives, sealants, or other materials with accuracy and consistency, vital for product quality.
- Inspection and quality control: Equipped with vision systems, robots can inspect parts for defects, ensuring only high-quality products proceed down the line.
- Packaging and palletizing: Robots efficiently handle packaging materials, filling boxes and placing finished products onto pallets for shipping.
Material Handling and Logistics in Factories
Beyond the assembly line, robots play a crucial role in material handling and logistics within factories. They streamline the movement of materials, raw components, and finished goods, significantly improving workflow and reducing bottlenecks. This automated handling contributes to optimized space utilization and reduced labor costs.
Robots handle tasks like transporting materials between workstations, loading and unloading machines, and managing inventory. Automated guided vehicles (AGVs) and autonomous mobile robots (AMRs) navigate factory floors, transporting goods efficiently and safely, even in dynamic environments. This automated system minimizes human intervention in potentially hazardous or repetitive tasks.
Welding, Painting, and Finishing Processes
Robots are particularly well-suited for tasks involving welding, painting, and other finishing processes that require precision, consistency, and often, work in hazardous environments. These applications improve both the quality and safety of the manufacturing process.
Process | Robot Type | Benefits | Challenges |
---|---|---|---|
Welding | Articulated arm robots, collaborative robots (cobots) | Increased speed and precision, consistent weld quality, improved worker safety | Programming complexity, high initial investment, potential for weld defects if not properly programmed and maintained |
Painting | Six-axis robots, spray painting robots | Uniform coating, reduced material waste, improved worker health and safety (reduced exposure to harmful chemicals) | Maintaining consistent paint flow, cleaning and maintenance of the robot and paint system, programming for complex shapes |
Finishing (e.g., sanding, polishing) | Collaborative robots (cobots), small articulated robots | Improved surface quality, increased throughput, reduced worker fatigue | Precise force control required, potential for damage to delicate surfaces, programming complexity for intricate shapes |
Collaborative Robots (Cobots) in Human-Robot Workspaces
Collaborative robots, or cobots, are designed to work alongside humans in shared workspaces. Unlike traditional industrial robots, cobots are equipped with safety features that allow them to operate safely near human workers. This integration enhances productivity by combining the strengths of both humans and robots.
Cobots excel at tasks requiring dexterity and human-robot interaction. For example, in assembly, a cobot might handle repetitive tasks while a human worker performs more complex or nuanced operations. This collaborative approach improves efficiency and allows for a more flexible and adaptable manufacturing process. Examples include cobots assisting with machine tending, parts assembly, and quality inspection tasks, working alongside human colleagues.
Economic and Societal Impacts of Robotics in Manufacturing: The Role Of Robotics In Modern Manufacturing
The integration of robotics into modern manufacturing processes has profoundly reshaped the economic and social landscape, triggering a complex interplay of benefits and challenges. While offering unprecedented opportunities for increased productivity and efficiency, the widespread adoption of robotics also raises crucial questions about job displacement and the need for workforce adaptation. Understanding these multifaceted impacts is vital for navigating the future of manufacturing and ensuring a just transition for all stakeholders.
Robotics’ influence on manufacturing is multifaceted, impacting everything from production output to the very nature of work itself. The economic effects are particularly significant, driving changes in both the micro-level (individual factories) and macro-level (national economies). Simultaneously, the societal implications are far-reaching, necessitating proactive strategies to mitigate potential negative consequences and harness the full potential of this technological revolution.
Robotics’ Impact on Manufacturing Productivity and Efficiency
The introduction of robots into manufacturing facilities has demonstrably boosted productivity and efficiency. Robots can operate continuously without breaks, reducing downtime and increasing output. They perform repetitive tasks with precision and speed far exceeding human capabilities, minimizing errors and improving product quality. This enhanced efficiency translates directly into lower production costs and increased profitability for businesses. For example, in the automotive industry, robotic welding and painting systems have significantly sped up assembly lines, leading to higher production volumes and reduced labor costs. Furthermore, robots can handle hazardous or ergonomically challenging tasks, improving worker safety and reducing workplace injuries. This leads to a healthier and more productive workforce, further contributing to overall efficiency gains.
The Effect of Robotics on Job Displacement and Workforce Retraining
While robotics enhances productivity, a common concern is job displacement. The automation of manufacturing tasks undeniably reduces the need for human labor in certain areas. However, this isn’t necessarily a net loss of jobs. The shift is more about a transformation of the workforce, requiring a move toward higher-skilled roles. The introduction of robots creates new job opportunities in areas such as robotics programming, maintenance, and system integration. Therefore, proactive workforce retraining programs are crucial to equip workers with the skills needed for these emerging roles. A successful transition requires collaboration between governments, educational institutions, and businesses to provide accessible and effective retraining opportunities, focusing on areas like AI, data analytics, and advanced manufacturing techniques. Without such initiatives, the societal benefits of robotic adoption will be unevenly distributed, leading to potential social unrest.
Costs and Benefits of Implementing Robotic Systems
The decision to implement robotic systems involves careful consideration of costs and benefits.
It’s crucial to weigh the initial investment against the long-term returns. A comprehensive cost-benefit analysis should be conducted before implementation.
- Costs: High initial capital expenditure for robot purchase and installation; ongoing maintenance and repair costs; integration with existing systems; potential need for specialized personnel (programmers, technicians); retraining existing workforce.
- Benefits: Increased productivity and output; improved product quality and consistency; reduced labor costs (in the long run); enhanced worker safety; increased flexibility and adaptability to changing market demands; potential for 24/7 operation.
Hypothetical Scenario: Robotic Adoption in the Apparel Manufacturing Sector, The Role of Robotics in Modern Manufacturing
Imagine a scenario where a major apparel manufacturer, currently relying heavily on manual labor in its garment production facilities, decides to implement a comprehensive robotic system. Initially, there would be significant upfront costs associated with purchasing and integrating automated sewing and cutting machines. However, over time, the increased efficiency and precision of the robotic systems would lead to a significant reduction in production time and material waste. This would translate into lower production costs and higher profit margins. While some low-skilled jobs in sewing and cutting might be displaced, the company could create new, higher-skilled positions in robotics maintenance, programming, and quality control. The success of this transition would depend heavily on the company’s investment in retraining programs for its existing workforce, ensuring a smooth transition and minimizing potential job losses. If handled effectively, this scenario could demonstrate the potential for robotic automation to drive economic growth while simultaneously creating new, higher-paying jobs. However, without adequate planning and investment in retraining, the outcome could be quite different, leading to job losses and social disruption.
Technological Advancements and Future Trends
The future of manufacturing is inextricably linked to the advancements in robotics. We’re moving beyond simple automation towards a highly interconnected, intelligent, and adaptive manufacturing landscape, driven by converging technologies. This shift promises increased efficiency, reduced costs, and the creation of entirely new possibilities within the industry.
Emerging technologies are rapidly transforming the role of robotics in modern manufacturing. The integration of artificial intelligence (AI), machine learning (ML), and the Internet of Things (IoT) is creating a new generation of robots capable of far more sophisticated tasks than ever before. Simultaneously, improvements in sensor technology and robotic dexterity are revolutionizing production lines, paving the way for flexible and adaptable manufacturing processes.
Artificial Intelligence, Machine Learning, and the Internet of Things in Robotics
AI, ML, and IoT are not merely add-ons; they are foundational elements reshaping robotic capabilities. AI enables robots to learn from data, adapt to changing conditions, and make decisions autonomously. Machine learning algorithms allow robots to improve their performance over time, refining their movements and decision-making processes based on experience. The IoT connects robots to a vast network of sensors, machines, and systems, enabling real-time data exchange and collaborative operations. For example, a smart factory might use IoT sensors to monitor the status of equipment, predict maintenance needs, and optimize production schedules based on real-time data analysis, all managed and coordinated by AI-powered robotic systems. This integration reduces downtime, improves efficiency, and enhances overall productivity.
Advanced Sensor Technologies and Their Integration
The precision and adaptability of robotic systems are directly tied to the sophistication of their sensors. Advanced sensor technologies, including vision systems, force/torque sensors, and proximity sensors, provide robots with a richer understanding of their environment and the objects they manipulate. For instance, advanced vision systems allow robots to identify and classify objects with high accuracy, even in complex and cluttered environments. Force/torque sensors enable robots to perform delicate tasks requiring precise control of force and pressure, such as assembly operations. This enhanced sensory input, combined with AI-powered processing, allows robots to perform tasks previously considered impossible for automation, such as handling fragile items or working in unstructured environments.
Advancements in Robot Dexterity and Manipulation
The ability of robots to perform complex manipulation tasks is rapidly improving. New designs incorporate more degrees of freedom, enabling robots to move and interact with objects in more nuanced ways. Advances in soft robotics and gripper technologies are enabling robots to handle a wider range of objects, from delicate electronics components to irregularly shaped parts. For example, collaborative robots (cobots) equipped with advanced grippers and force sensors can work safely alongside human workers, performing tasks that require both precision and dexterity, such as assembling intricate products or conducting quality inspections. This human-robot collaboration enhances efficiency and allows for a more flexible and adaptable manufacturing process.
A Futuristic Manufacturing Facility
Imagine a futuristic manufacturing facility where autonomous mobile robots navigate a dynamic environment, seamlessly collaborating with human workers and advanced machinery. AI-powered systems optimize production schedules in real-time, predicting potential bottlenecks and adjusting workflows accordingly. Robots equipped with advanced vision systems and dexterous manipulators perform complex assembly tasks, while collaborative robots assist human workers with more intricate operations. The entire facility is connected through the IoT, providing a continuous stream of data that is used to monitor performance, predict maintenance needs, and improve efficiency. This facility is a testament to the transformative power of advanced robotics and the convergence of multiple technologies. The production process is flexible, adaptable, and highly efficient, producing high-quality goods at a reduced cost while minimizing waste and maximizing resource utilization. This is not just science fiction; elements of this vision are already being implemented in cutting-edge manufacturing facilities around the world.
Challenges and Considerations in Robotics Implementation
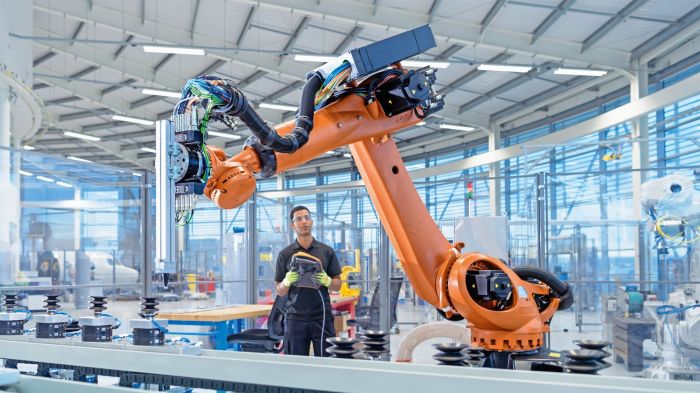
Source: siemens.com
Integrating robots into manufacturing isn’t a simple plug-and-play operation. It requires careful planning, substantial investment, and a proactive approach to potential hurdles. Successfully navigating these challenges is crucial for reaping the benefits of automation while mitigating risks. This section delves into the key considerations for a smooth and effective robotic implementation.
The integration of robotics into existing manufacturing processes presents a unique set of challenges. These challenges span technical, economic, and social domains, requiring a holistic approach to address them effectively. Overcoming these obstacles is paramount to achieving a successful and profitable automation strategy.
Safety Protocols and Risk Mitigation
Implementing robust safety protocols is paramount in robotic environments. The potential for accidents involving heavy machinery and complex algorithms necessitates a multi-layered approach to risk mitigation. This involves careful consideration of workspace design, emergency shutdown mechanisms, and operator training. Failing to prioritize safety can lead to costly downtime, injuries, and legal ramifications. A comprehensive risk assessment should be conducted prior to implementation, identifying potential hazards and developing appropriate control measures. This assessment should encompass all aspects of the robotic system, including its mechanical components, software, and integration with existing equipment. Furthermore, regular safety audits and employee training are essential to maintain a safe working environment.
Programming and Maintenance Procedures
Effective robotic systems require sophisticated programming and diligent maintenance. Programming encompasses not only the robot’s movements and tasks but also the integration with other systems, such as supervisory control and data acquisition (SCADA) systems. This demands skilled programmers with expertise in robotics and manufacturing processes. Regular maintenance is equally critical for optimal performance and longevity. Neglecting maintenance can lead to malfunctions, reduced efficiency, and increased downtime.
- Regular lubrication of moving parts to prevent wear and tear.
- Inspection of sensors and actuators for damage or malfunction.
- Software updates and bug fixes to ensure optimal performance and security.
- Calibration of robotic arms and other components to maintain accuracy.
- Periodic replacement of worn-out parts to prevent unexpected failures.
Data Security and Privacy
Modern robotic systems generate vast amounts of data, creating both opportunities and challenges. Data security and privacy are crucial concerns in a manufacturing environment utilizing robotics and data analytics. Protecting sensitive data from unauthorized access, breaches, and misuse is vital for maintaining operational integrity and complying with regulations. This requires implementing robust cybersecurity measures, including access controls, encryption, and regular security audits. Furthermore, the collection and use of employee data must comply with relevant privacy laws and regulations. Companies should develop clear data governance policies that define how data is collected, stored, used, and protected. Consideration should also be given to potential vulnerabilities in connected devices and the potential for cyberattacks targeting the robotic systems. For example, a ransomware attack could cripple production by locking down the entire robotic system.
Wrap-Up
So, there you have it: the robotic revolution in manufacturing is in full swing. While challenges remain – from job displacement to ethical considerations – the potential benefits are too significant to ignore. Increased productivity, improved quality, and the creation of entirely new possibilities are all on the table. The future of manufacturing is automated, collaborative, and undeniably exciting. The question isn’t *if* robots will take over, but *how* we’ll work together to build a brighter, more efficient future.