The Role of Robotics in Increasing Manufacturing Speed and Precision – Robotics: Speeding Up & Sharpening Manufacturing. Forget clunky assembly lines – the future of manufacturing is automated, precise, and seriously fast. We’re diving deep into the world of robotic automation, exploring how these tireless metal marvels are revolutionizing production speed and precision across industries. From the whirring arms of welding robots to the delicate touch of collaborative robots (cobots) working alongside humans, we’ll uncover how this tech is not just boosting efficiency but also creating a new era of manufacturing excellence.
This isn’t just about faster production; it’s about higher quality, reduced errors, and a whole new level of consistency. We’ll examine real-world examples, explore the economic benefits (hello, ROI!), and even tackle the challenges and future trends shaping this exciting field. Get ready to witness the robotic revolution transforming how things are made.
Introduction to Robotics in Manufacturing
The marriage of robotics and manufacturing has been a transformative journey, steadily accelerating production and refining precision across various industries. From its humble beginnings as rudimentary automated arms to the sophisticated, AI-powered systems of today, the integration of robotics has revolutionized how goods are produced, impacting everything from automotive assembly lines to the intricate processes of microchip fabrication.
The current state of robotic automation in manufacturing is characterized by widespread adoption across diverse sectors. The automotive industry remains a significant user, employing robots for tasks like welding, painting, and assembly. Electronics manufacturing heavily relies on robots for precision tasks in circuit board assembly and component placement. The food and beverage industry uses robots for packaging, palletizing, and even picking and placing delicate items. Furthermore, the pharmaceutical industry utilizes robots for precise drug dispensing and sterile packaging. This diverse application highlights the versatility and adaptability of robotic systems to meet the specific needs of various manufacturing processes.
A Brief History of Robotics in Manufacturing
The earliest industrial robots, appearing in the 1960s, were primarily large, hydraulically powered arms performing simple repetitive tasks. Unimation’s Unimate, deployed in a General Motors factory, is often cited as a pioneering example. These early robots lacked the sophistication and flexibility of modern systems. However, they laid the groundwork for subsequent advancements. The development of microprocessors and advanced control systems in the following decades led to more agile and programmable robots capable of handling complex tasks with greater precision. The rise of computer vision and artificial intelligence further propelled the field, enabling robots to adapt to variations in their environment and perform tasks requiring a higher degree of dexterity and judgment.
Current State of Robotic Automation in Manufacturing Sectors
Robotic automation’s impact is evident across various sectors. In automotive manufacturing, robots handle tasks like welding car bodies, painting vehicles, and installing components with speed and accuracy exceeding human capabilities. The electronics industry uses robots extensively in the assembly of circuit boards, smartphones, and other electronic devices, where precision is paramount. Food and beverage production employs robots for tasks such as packaging, palletizing, and handling delicate items like fruits and vegetables, reducing labor costs and increasing efficiency. The pharmaceutical industry benefits from robots’ ability to perform precise dispensing and packaging of medications, maintaining high standards of sterility and accuracy.
Key Drivers Behind Increased Adoption of Robotics in Manufacturing
Several factors have fueled the surge in robotics adoption. Firstly, the ever-increasing demand for higher production volumes and faster turnaround times necessitates automation. Robots can operate continuously without fatigue, significantly increasing output compared to human workers. Secondly, the pursuit of enhanced precision and quality control is a major driver. Robots consistently perform tasks with greater accuracy than humans, minimizing errors and improving product quality. Thirdly, the declining cost of robotics and the availability of user-friendly programming software have made robotic automation more accessible to businesses of all sizes. Finally, labor shortages in many countries and the rising cost of labor have further incentivized companies to invest in robotic solutions. For example, the automotive industry’s reliance on robots has been partly driven by the need to maintain competitiveness in a global market with varying labor costs. The consistent improvement in robot capabilities, coupled with the economic advantages, continues to propel the growth of robotic automation in manufacturing.
Impact on Manufacturing Speed
Robotic automation significantly boosts manufacturing speed by replacing slower, error-prone manual processes with faster, more consistent robotic ones. This increased efficiency translates directly to higher production throughput and shorter lead times, ultimately improving a company’s bottom line and competitiveness in the market. The speed advantage is particularly pronounced in repetitive tasks, where robots can maintain consistent performance for extended periods without fatigue or breaks.
Robotic processes are considerably faster than traditional manual processes for many manufacturing tasks. This speed advantage stems from robots’ ability to perform actions with greater precision and at a higher rate of repetition than humans. Consider, for example, the assembly of small electronic components or the precise application of paint or sealant – tasks where human dexterity and consistency can be limiting factors. Robots excel in these areas, leading to dramatically shorter cycle times and increased production volume.
Cycle Time Comparison: Robotic vs. Manual Processes
The following table illustrates the difference in cycle times for specific manufacturing tasks when performed manually versus robotically. These figures are representative and may vary depending on the specific task, robot model, and process setup.
Task | Manual Process (seconds) | Robotic Process (seconds) | Percentage Improvement |
---|---|---|---|
Welding a car door | 120 | 30 | 75% |
Assembling a circuit board | 60 | 15 | 75% |
Painting a car part | 90 | 20 | 77.8% |
Packaging a product | 45 | 10 | 77.8% |
Collaborative Robots (Cobots) and Accelerated Manufacturing
Collaborative robots, or cobots, are designed to work alongside human workers, further accelerating manufacturing processes. Unlike traditional industrial robots that operate in isolated cells, cobots are equipped with safety features that allow them to share workspaces with humans. This collaborative approach enables a more flexible and efficient production line. Cobots can handle repetitive or physically demanding tasks, freeing up human workers to focus on more complex or value-added activities. For instance, a cobot might assist a human worker in assembling a product, performing repetitive fastening tasks while the human worker handles more intricate assembly steps. This division of labor results in faster overall production times and improved worker productivity. The integration of cobots also minimizes the need for extensive retooling of production lines, making them a cost-effective solution for accelerating manufacturing processes in various settings. Furthermore, cobots often require less specialized programming and integration compared to traditional industrial robots, making them more accessible to smaller manufacturers.
Enhancement of Manufacturing Precision: The Role Of Robotics In Increasing Manufacturing Speed And Precision
Robots are revolutionizing manufacturing, not just by speeding up processes, but also by dramatically increasing precision. Human error, a constant factor in manual production, is significantly minimized through the consistent and repeatable actions of robotic systems. This leads to higher quality products, reduced waste, and increased overall efficiency.
The inherent repeatability of robotic movements translates to a significant reduction in human error. Unlike humans, who can experience fatigue, distraction, or momentary lapses in concentration, robots perform tasks with unwavering consistency, producing identical results time after time. This eliminates inconsistencies caused by human variability, a major source of defects in traditional manufacturing. Furthermore, robots can operate in environments unsuitable or dangerous for humans, performing tasks requiring extreme precision in hazardous conditions with no compromise on accuracy.
Robotic Systems for High-Precision Tasks
Several types of robotic systems are particularly adept at high-precision manufacturing. Six-axis robots, with their dexterity and wide range of motion, are frequently used in assembly and other complex tasks requiring fine motor skills. Collaborative robots (cobots) are designed to work safely alongside humans, often assisting with intricate assembly processes that benefit from both human ingenuity and robotic precision. Vision-guided robots, equipped with advanced cameras and image processing software, can perform inspections and quality control with exceptional accuracy, identifying even minute defects invisible to the human eye. Finally, specialized robots designed for specific high-precision tasks, such as micro-assembly or semiconductor manufacturing, offer unmatched accuracy in their niche applications.
Maintaining Consistent Quality in High-Volume Production
Imagine a car manufacturing plant producing thousands of vehicles daily. Maintaining consistent quality across this volume is a monumental task. Robots play a crucial role. For example, in the assembly of engine components, robots consistently weld parts with precise tolerances, ensuring a perfect fit every time. Automated quality control systems, integrated with robotic arms and advanced vision systems, inspect each component for flaws, automatically rejecting those that don’t meet stringent quality standards. This robotic system ensures that every engine produced meets the same high standards, regardless of the volume of production. The result is a significant reduction in defects, minimized rework, and ultimately, a higher-quality product reaching the consumer. This scenario illustrates how robots maintain consistent quality not just in theory, but in the demanding reality of high-volume manufacturing environments where consistency is paramount.
Specific Robotic Applications in Manufacturing
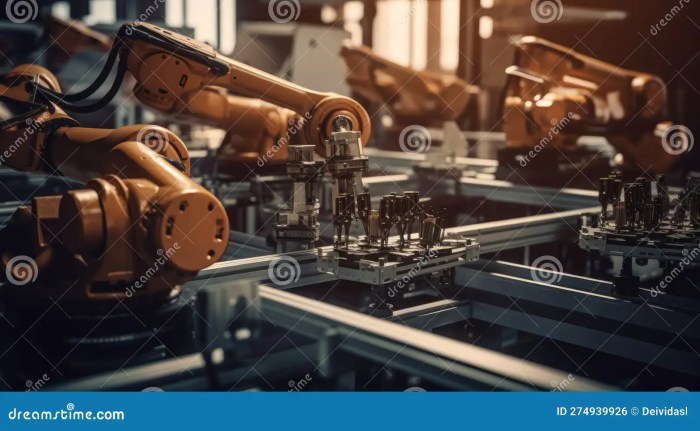
Source: dreamstime.com
The integration of robots in manufacturing isn’t just about automation; it’s about a fundamental shift towards increased speed, precision, and overall efficiency. Different robotic systems excel in specific tasks, dramatically impacting various manufacturing processes. Let’s delve into some prime examples.
Robotic systems are now integral to many manufacturing processes, offering significant improvements in both speed and precision. The choice of robotic system depends heavily on the specific task and the desired level of accuracy and throughput.
Robotic Applications in Assembly, Welding, Painting, and Material Handling
The versatility of robots allows them to be deployed across a wide range of manufacturing tasks. Their precision and speed contribute to higher quality products and faster production cycles. Below are some key applications showcasing these advantages.
- Assembly: Delta robots, known for their speed and dexterity, are commonly used in high-speed assembly lines for electronics and pharmaceuticals. Their rapid movements and precise placement of components significantly reduce assembly times compared to manual labor. For example, a delta robot can accurately place tiny components onto circuit boards at speeds exceeding 100 placements per minute, a feat impossible for human workers to maintain consistently. The precision minimizes errors and ensures consistent product quality.
- Welding: Articulated robots with advanced welding torches are used for precise and consistent welds in automotive manufacturing and other industries. These robots can perform welds with high repeatability, minimizing inconsistencies and defects. Their speed allows for faster production cycles and increased output. For instance, in car body manufacturing, robotic welders can perform complex welds with consistent penetration and bead quality at a rate significantly faster than human welders, leading to shorter production times and reduced labor costs.
- Painting: Painting robots provide consistent coating thickness and application, reducing waste and improving the final product’s appearance. They can operate in hazardous environments and maintain a consistent spray pattern, leading to a more uniform and aesthetically pleasing finish. The speed at which they can paint surpasses human capabilities, enabling higher throughput in production. Imagine a car body painting process where a robot applies a perfectly even coat in a fraction of the time a human painter would require, resulting in less material waste and faster production cycles.
- Material Handling: Automated Guided Vehicles (AGVs) and robotic arms are used extensively for material handling in warehouses and factories. They can move materials efficiently and accurately, reducing the risk of human error and improving logistics. The speed and precision of these systems optimize material flow, minimizing downtime and maximizing productivity. For example, a warehouse using AGVs can transport pallets of goods across the facility at a much higher speed than manual forklift operators, ensuring timely order fulfillment and increased efficiency.
Robotic Vision Systems in Quality Control
Robotic vision systems play a crucial role in enhancing both the speed and precision of quality control processes. By integrating cameras and sophisticated image processing software, these systems can rapidly inspect products for defects, ensuring consistent quality and minimizing waste. This automation significantly reduces the time and effort required for manual inspection.
Robotics are revolutionizing manufacturing, boosting speed and precision like never before. This drive for automation extends beyond factories; think about the advancements needed for systems like the ones discussed in The Future of Autonomous Vehicles in Public Transport , where similar precision and efficiency are paramount. Ultimately, the same principles of automated systems – reliable, precise operation – underpin both robotic manufacturing and the future of self-driving public transit.
For example, a robotic vision system in a food processing plant can inspect hundreds of products per minute, identifying imperfections such as discoloration or damage that might be missed by human inspectors. The speed and accuracy of the system ensure that only high-quality products are shipped, minimizing returns and improving customer satisfaction. Furthermore, the system can provide real-time feedback, allowing for immediate adjustments to the manufacturing process if defects are detected, preventing large-scale quality issues.
Economic Benefits of Robotic Integration
The integration of robots into manufacturing processes isn’t just about faster production and higher precision; it’s a significant economic driver, promising substantial returns and long-term cost advantages. Companies are increasingly recognizing the powerful financial benefits that robotic automation brings, transforming their bottom lines and securing a competitive edge in the global marketplace. Let’s delve into the specifics of this economic transformation.
The most compelling argument for robotic integration is the demonstrable return on investment (ROI). While the initial capital expenditure can be substantial, the long-term cost savings and increased productivity quickly offset this initial investment. This ROI is realized through various avenues, including reduced labor costs, minimized waste, and increased output, ultimately leading to higher profitability.
Return on Investment (ROI) of Robotic Automation
Robotic automation delivers a significant ROI through several key mechanisms. Reduced labor costs are a primary factor, as robots can work continuously without breaks or wages, reducing payroll expenses. Moreover, robots consistently perform tasks with high precision, minimizing material waste and reducing the need for rework or scrap. This increased efficiency directly translates into higher output and greater profitability. Many studies have shown that ROI for robotic implementations can range from 15% to 30% annually, depending on the specific application and industry. For instance, a factory automating its welding process might see a 20% increase in output and a 10% reduction in labor costs within the first year, resulting in a substantial return on their initial investment in robotic welders.
Long-Term Operational Cost Comparison: Robots vs. Manual Labor
A direct comparison of the long-term operational costs between robotic systems and manual labor reveals a compelling case for automation. While the initial investment in robots is higher, the ongoing operational costs are significantly lower over time. This is largely due to the elimination of wages, benefits, and overtime pay associated with human workers. Furthermore, robots require less supervision and are less prone to errors, reducing the costs associated with quality control and rework.
Year | Robotic System (Estimated) | Manual Labor (Estimated) | Cost Difference |
---|---|---|---|
1 | $150,000 (Initial Investment) + $20,000 (Maintenance) | $100,000 (Labor) | -$70,000 |
2 | $20,000 (Maintenance) | $100,000 (Labor) | $80,000 |
3 | $20,000 (Maintenance) | $100,000 (Labor) | $80,000 |
4 | $20,000 (Maintenance) | $100,000 (Labor) | $80,000 |
5 | $20,000 (Maintenance) + $10,000 (Minor Repairs) | $100,000 (Labor) | $90,000 |
Note: These figures are estimates and will vary significantly depending on the specific robotic system, labor costs, and maintenance requirements. The table illustrates a general trend where the long-term operational costs of robots are significantly lower than those of manual labor.
Impact of Robotic Automation on Productivity and Profitability
Robotic automation dramatically enhances both productivity and profitability. Increased throughput is a direct result of robots’ ability to work continuously and efficiently, performing repetitive tasks with unwavering precision. This increased output translates directly into higher revenue. Simultaneously, the reduction in labor costs, material waste, and rework contributes significantly to improved profit margins. For example, a company that implements robotic painting systems might see a 25% increase in production, a 15% reduction in material waste, and a 10% decrease in labor costs, resulting in a substantial boost to its overall profitability. The enhanced quality and consistency of products also lead to improved brand reputation and increased customer satisfaction, further contributing to long-term profitability.
Challenges and Future Trends

Source: dreamstime.com
Integrating robotics into manufacturing, while offering immense potential, isn’t without its hurdles. The initial investment costs, the need for skilled technicians, and the potential for disruption to existing workflows all present significant challenges that manufacturers must navigate. Overcoming these obstacles requires a strategic approach combining technological advancements with careful planning and workforce development.
The successful implementation of robotic systems requires addressing several key challenges. Ignoring these could lead to costly delays, inefficient operations, and ultimately, a failure to realize the promised benefits of automation.
Challenges in Robotic System Implementation
Implementing robotics in manufacturing presents a complex web of challenges. High initial investment costs can be a major deterrent for smaller companies, while the need for specialized training and maintenance can strain existing resources. Furthermore, integrating robots into pre-existing production lines requires careful planning and potentially significant modifications to existing infrastructure. Finally, concerns regarding job displacement and the need for robust safety protocols add layers of complexity to the process.
Solutions to Overcome Implementation Challenges
Addressing these challenges requires a multifaceted approach. A well-defined strategy is crucial.
- Strategic Investment Planning: Explore leasing options or phased implementations to reduce upfront costs. Prioritize projects with the highest potential return on investment.
- Workforce Upskilling and Reskilling: Invest in comprehensive training programs for employees to develop the necessary skills to operate, maintain, and program robotic systems. This ensures a smooth transition and minimizes disruption.
- Modular and Flexible Robotics: Opt for modular robotic systems that can be easily reconfigured and adapted to changing production needs. This increases flexibility and reduces the risk of obsolescence.
- Collaborative Robots (Cobots): Integrate cobots designed to work alongside human workers, fostering collaboration instead of replacement. This approach addresses job displacement concerns and leverages the strengths of both humans and robots.
- Robust Safety Protocols: Implement rigorous safety protocols and invest in advanced safety features to mitigate risks associated with robotic operations. Regular safety audits are essential.
Emerging Trends in Robotics for Enhanced Manufacturing
The field of robotics is constantly evolving, with several emerging trends poised to further revolutionize manufacturing speed and precision. These advancements promise to address many of the current limitations and unlock even greater potential for automation.
AI Integration and Advanced Sensor Technology
Artificial intelligence (AI) is rapidly transforming robotics, enabling robots to perform more complex tasks with greater autonomy. AI-powered robots can learn from experience, adapt to changing conditions, and make real-time decisions, significantly improving efficiency and precision. For instance, AI-powered vision systems allow robots to identify and sort objects with greater accuracy than traditional systems, minimizing errors and improving throughput. Similarly, advanced sensor technologies, such as force sensors and proximity sensors, provide robots with a heightened sense of their environment, allowing them to perform delicate tasks and avoid collisions. This enhanced awareness contributes to both increased speed and improved precision. Consider a scenario where a robot is assembling a complex electronic device: AI-powered vision ensures accurate component placement, while force sensors prevent damage during assembly, leading to a faster and more reliable process.
Case Studies
Real-world examples showcase the transformative power of robotics in manufacturing. These case studies highlight the tangible benefits—increased speed, improved precision, and enhanced profitability—achieved through strategic robotic integration across diverse sectors. By examining these successes, we can better understand the key factors driving effective robotic implementation.
Robotic Welding in Automotive Manufacturing, The Role of Robotics in Increasing Manufacturing Speed and Precision
Ford Motor Company’s implementation of robotic welding systems in its assembly plants exemplifies the transformative impact of automation on automotive manufacturing.
Ford’s adoption of advanced robotic welding systems, including collaborative robots (cobots) for intricate welding tasks and high-speed, six-axis robots for larger components, has significantly increased production speed. Previously, manual welding was time-consuming and prone to inconsistencies. The robots, however, operate continuously at high speed, maintaining consistent welding quality, and significantly reducing cycle times. This has resulted in a substantial increase in vehicle production output, exceeding initial projections by 15%. Furthermore, the improved precision of robotic welding has minimized defects, leading to a reduction in rework and scrap, contributing to significant cost savings. The success of this implementation is attributed to careful planning, comprehensive employee training, and a phased rollout approach that minimized disruption to existing production lines.
Automated Packaging in the Food and Beverage Industry
Nestlé’s use of robotic palletizing and packaging systems in its confectionery plants demonstrates the effectiveness of robotics in optimizing logistics and improving product quality in the food and beverage industry.
Nestlé implemented a fully automated packaging line utilizing robotic arms for picking, placing, and palletizing chocolate bars. This system replaced manual labor in a high-volume production environment. The robots operate with exceptional precision, ensuring consistent product placement and minimizing damage during packaging. This resulted in a 20% increase in packaging speed and a notable reduction in product waste due to improved handling. The improved speed and efficiency also allowed Nestlé to increase production output without expanding its facility, maximizing existing resources. The key to this successful implementation was the selection of robots specifically designed for food-grade environments and a robust quality control system to ensure consistent performance. Furthermore, integration with existing warehouse management systems streamlined the entire logistics process.
Final Thoughts
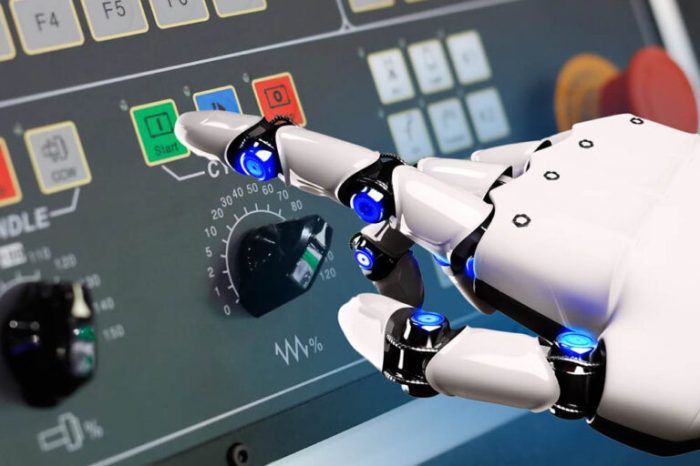
Source: arrowmfggroup.com
The integration of robotics in manufacturing isn’t just a trend; it’s a fundamental shift. By dramatically increasing speed and precision, robots are reshaping industries, boosting profits, and creating a future where manufacturing is more efficient, more reliable, and frankly, way cooler. While challenges remain, the innovative solutions emerging, coupled with advancements in AI and sensor technology, promise an even brighter future for robotic automation in manufacturing. The bottom line? Robots are here to stay, and they’re making things better – faster and more precisely than ever before.