The Role of Robotics in Improving the Efficiency of the Logistics Industry is exploding. Forget slow, manual processes – we’re talking automated warehouses humming with robots, self-driving trucks navigating city streets, and drones whizzing packages to your doorstep. This isn’t science fiction; it’s the future of logistics, and it’s happening now. This deep dive explores how robots are transforming everything from warehouse management to last-mile delivery, uncovering the massive efficiency gains and the exciting – and sometimes unsettling – implications for the workforce.
From automated guided vehicles (AGVs) meticulously navigating warehouse aisles to robotic arms swiftly picking and packing orders, the integration of robotics is streamlining operations at an unprecedented rate. We’ll examine the specific technologies driving this change, analyze the economic impact, and discuss the crucial adaptations needed for a human workforce navigating this new automated landscape. Get ready for a ride into the robotic heart of the logistics revolution.
The Expanding Role of Robotics in Logistics
The logistics industry, a backbone of global commerce, is undergoing a significant transformation fueled by the rapid advancement and adoption of robotics. No longer a futuristic fantasy, robots are becoming increasingly prevalent in warehouses, distribution centers, and transportation networks, streamlining operations and boosting efficiency in ways previously unimaginable. This integration isn’t just about automation; it’s about optimizing entire logistical processes for speed, accuracy, and cost-effectiveness.
The rise of e-commerce, the demand for faster delivery times, and the persistent challenge of labor shortages are key drivers pushing the logistics sector towards greater robotics implementation. Companies are facing pressure to deliver goods quickly and efficiently, while simultaneously battling rising labor costs and a shrinking pool of available workers. Robotics offers a solution by automating repetitive, labor-intensive tasks, increasing throughput, and improving overall productivity. Furthermore, the decreasing cost of robotics and the development of more sophisticated and adaptable robotic systems have made them a financially viable option for a broader range of logistics businesses.
Types of Robots Used in Logistics Operations
Several types of robots are currently revolutionizing various aspects of the logistics process. These robots are designed to perform specific tasks, from moving goods to sorting packages, enhancing overall efficiency and accuracy. The diverse applications showcase the versatility and adaptability of robotics within the industry.
- Automated Guided Vehicles (AGVs): These mobile robots follow pre-programmed paths within warehouses and distribution centers, transporting goods between different locations. They can be equipped with sensors to navigate around obstacles and optimize their routes for maximum efficiency. Imagine a fleet of AGVs silently and efficiently moving pallets of goods across a warehouse floor, avoiding human workers and navigating complex layouts with ease. This eliminates the need for manual forklift operation, reducing the risk of accidents and improving speed.
- Autonomous Mobile Robots (AMRs): Unlike AGVs, AMRs use advanced sensors and AI to navigate dynamically, adapting to changing environments and avoiding obstacles without pre-programmed paths. This allows for greater flexibility and efficiency in dynamic warehouse settings. Picture an AMR deftly maneuvering around a human worker or an unexpected pallet obstruction, autonomously finding the most efficient route to its destination, a task impossible for a traditional AGV.
- Articulated Robots: These multi-jointed robots are often used for tasks like palletizing, depalletizing, and picking and placing items. Their dexterity allows them to handle a wide range of goods with precision and speed. Think of a robotic arm swiftly and accurately placing individual items onto a pallet, performing a task that would take a human worker significantly longer and with a higher risk of error.
- Sorting Robots: These robots are designed to sort packages and parcels based on their destination or other criteria. They often utilize advanced vision systems and AI to identify and classify items quickly and accurately. Envision a conveyor belt feeding packages to a robotic sorter that rapidly scans barcodes, identifies destinations, and diverts each package to the correct chute, dramatically speeding up the sorting process.
Warehouse Automation
The logistics industry’s relentless pursuit of efficiency has led to a significant surge in warehouse automation. This isn’t just about faster processing; it’s about optimizing space, minimizing errors, and ultimately, reducing costs. The integration of robots, particularly automated guided vehicles (AGVs) and autonomous mobile robots (AMRs), robotic arms, and collaborative robots (cobots), is revolutionizing warehouse operations, transforming them from labor-intensive environments to highly efficient, technologically driven hubs.
Automated Guided Vehicles (AGVs) and Autonomous Mobile Robots (AMRs) in Warehouse Optimization
AGVs and AMRs are the workhorses of automated warehousing, tirelessly moving goods across vast spaces. AGVs, following pre-programmed paths using wires, magnetic tape, or laser guidance, are reliable and predictable. AMRs, on the other hand, navigate using advanced sensors and artificial intelligence, adapting to dynamic environments and rerouting themselves around obstacles in real-time. This adaptability makes AMRs particularly beneficial in fast-changing warehouse conditions. Their combined impact on warehouse operations is significant, leading to reduced transportation times, improved throughput, and minimized human intervention in repetitive tasks. For example, a large e-commerce fulfillment center using a fleet of AMRs can drastically reduce order processing time, leading to faster delivery and higher customer satisfaction.
Robotic Arms and Cobots in Order Fulfillment and Picking
Robotic arms and cobots are transforming order fulfillment and picking processes. Traditional picking involves manual selection of items from shelves, a process prone to errors and susceptible to worker fatigue. Robotic arms, with their precision and speed, can significantly reduce these issues. They can handle a wide range of items, from small electronics to bulky appliances, picking and placing them with accuracy and speed far exceeding human capabilities. Cobots, designed to collaborate with human workers, offer a unique advantage. They can handle the more repetitive and physically demanding aspects of picking, freeing up human workers to focus on more complex tasks requiring judgment and problem-solving. Amazon, for example, extensively uses robotic arms in its fulfillment centers to improve picking efficiency.
Robotic Systems for Inventory Management and Warehouse Organization
Efficient inventory management is crucial for smooth warehouse operations. Robotic systems play a vital role here. Automated inventory tracking systems, often integrated with robots, provide real-time visibility into stock levels, reducing the risk of stockouts or overstocking. Robots can also assist in organizing and optimizing warehouse layout, ensuring efficient storage and retrieval of goods. This includes tasks like automated pallet stacking and retrieval, optimizing shelf space, and identifying and removing obsolete or damaged items. A well-integrated robotic system can significantly improve warehouse space utilization, leading to cost savings and increased storage capacity.
Feature | AGVs | AMRs | Application |
---|---|---|---|
Navigation | Pre-programmed paths (wires, magnets, lasers) | AI-powered navigation, sensor-based | Material handling, transportation of goods |
Flexibility | Low; requires reprogramming for route changes | High; adapts to dynamic environments | Adaptable to changing warehouse layouts |
Cost | Generally lower initial investment | Higher initial investment, but potential for long-term savings | Cost-effective for high-volume operations |
Maintenance | Relatively low maintenance | Requires more sophisticated maintenance | Ensuring operational efficiency |
Transportation and Delivery
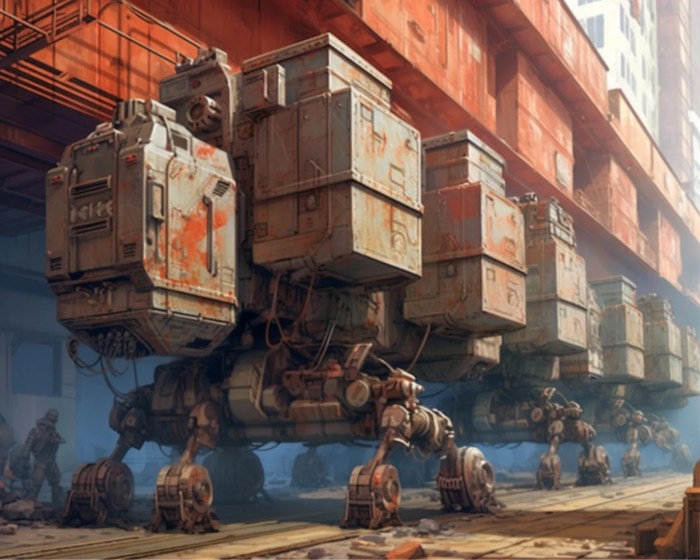
Source: sctechinsights.com
The last mile—that final leg of a delivery journey—is often the most expensive and inefficient part of the logistics process. Traditional methods struggle with traffic congestion, unpredictable delivery times, and high labor costs. Enter robotics, offering a potential revolution in last-mile delivery, promising speed, efficiency, and cost reduction. This section explores the emerging role of robotics in this crucial phase of the supply chain.
Robotic systems are rapidly transforming how goods reach their final destination. From autonomous trucks navigating highways to nimble drones soaring through the skies, the landscape of last-mile delivery is undergoing a significant makeover. This shift is driven by the increasing demand for faster, more reliable, and cost-effective delivery solutions, particularly in densely populated urban areas.
Robots are revolutionizing logistics, optimizing warehouse operations and streamlining delivery routes. But to truly maximize their potential, real-time data is key, and that’s where the magic of IoT comes in. Check out this article on How IoT is Improving Real-Time Data Analytics for Businesses to see how it fuels smarter, more efficient robotic deployments. This data-driven approach allows for predictive maintenance and optimized task allocation, ultimately boosting the overall efficiency of the logistics industry.
Automated Trucking and Drone Delivery Systems
The application of robotics in transportation extends beyond just the last mile; however, its impact on this final stage is particularly noteworthy. Automated trucking systems, utilizing advanced sensors, GPS, and AI-powered navigation, are already being tested on specific routes, aiming to optimize long-haul transportation and reduce driver fatigue and associated risks. Simultaneously, drone delivery services are gaining traction, particularly in areas with limited road access or congested urban environments. Companies like Amazon and UPS are actively investing in and testing drone delivery fleets, showcasing the potential for faster and more efficient deliveries, especially for smaller packages. For instance, a hypothetical scenario could involve a drone delivering a package from a central warehouse to a customer in a high-rise building, bypassing traffic congestion and accessing areas inaccessible to traditional delivery vehicles.
Challenges and Opportunities in Robotic Last-Mile Delivery
Implementing robotic systems for last-mile delivery presents several challenges. Regulatory frameworks for autonomous vehicles and drones are still evolving, creating uncertainties for businesses. Technological hurdles, such as ensuring reliable navigation in complex urban environments, battery life limitations for drones, and cybersecurity concerns, also need to be addressed. Public acceptance and trust in autonomous delivery systems are also crucial for widespread adoption. However, the opportunities are equally significant. Cost savings from reduced labor costs and fuel consumption are substantial. Improved delivery speeds and reliability enhance customer satisfaction and open up new possibilities for businesses. The ability to reach remote or difficult-to-access areas expands the reach of e-commerce and other delivery services.
Hypothetical Scenario: Robotic Delivery in a Dense Urban Environment
Imagine a densely populated city like Manhattan, New York. Currently, last-mile delivery faces significant challenges due to heavy traffic, limited parking, and high labor costs. Let’s consider a scenario where a network of small, autonomous delivery robots, each capable of carrying several packages, operates within a designated zone in Manhattan. These robots navigate sidewalks and pedestrian areas using advanced sensors and AI to avoid obstacles and pedestrians. A central control system manages the robots’ routes and schedules deliveries efficiently, optimizing for speed and minimizing conflicts. Compared to traditional delivery methods, this robotic system could reduce delivery times by 50%, lower labor costs by 40%, and decrease fuel consumption significantly, resulting in substantial environmental benefits. This hypothetical scenario, though simplified, illustrates the potential for significant efficiency gains through the adoption of robotic last-mile delivery systems in densely populated urban areas. Real-world examples, while not yet at this scale, are demonstrating the feasibility of such systems in controlled environments and gradually expanding into more complex urban landscapes.
Impact on Human Workers and the Workforce
The rise of robotics in logistics is undeniably transforming the industry, leading to both exciting opportunities and understandable anxieties about the future of work. While automation promises increased efficiency and productivity, it also raises crucial questions about the impact on the existing human workforce. Understanding this dual nature—the potential for displacement alongside the creation of new roles—is vital for a smooth and equitable transition.
The integration of robots into warehousing and transportation is causing some level of job displacement, particularly for roles involving repetitive manual tasks. This is not a new phenomenon; technological advancements throughout history have often led to shifts in employment. However, the speed and scale of robotic adoption in logistics necessitate proactive strategies to mitigate the negative consequences for workers. Retraining and upskilling initiatives are crucial to equip displaced workers with the skills needed for the emerging job market within the logistics sector and beyond.
Job Displacement and Retraining Needs
The automation of tasks like order picking, sorting, and palletizing has the potential to significantly reduce the need for human labor in these areas. For example, Amazon’s extensive use of robotic systems in its fulfillment centers has already demonstrably altered the nature of warehouse work. To address this, proactive retraining programs focusing on skills such as robotic maintenance, data analysis, and software programming are becoming increasingly important. These programs should be industry-led, government-supported, and tailored to the specific skills gaps created by automation. A successful transition requires a collaborative effort to ensure that workers are not left behind. Successful examples include partnerships between logistics companies and educational institutions offering customized training programs directly relevant to the evolving needs of the automated warehouse.
New Job Roles Created by Robotics
While some jobs are being automated, the integration of robotics also creates a demand for new skill sets. The need for specialists in robotics maintenance, programming, and system integration is growing rapidly. Furthermore, roles focused on data analysis and optimization of robotic systems are becoming increasingly crucial. For instance, roles like robotic process automation (RPA) developers, AI trainers for logistics robots, and cybersecurity specialists focused on protecting automated systems are emerging. These new roles require a higher level of technical expertise and often command higher salaries, representing a potential upward mobility path for workers willing to adapt and learn new skills.
Human-Robot Collaboration: Advantages and Disadvantages
The future of logistics is not solely about robots replacing humans, but increasingly about human-robot collaboration. This collaborative approach leverages the strengths of both: the precision and efficiency of robots alongside the adaptability, problem-solving skills, and complex decision-making capabilities of humans.
Advantages of human-robot collaboration include increased productivity through the division of labor (humans handling complex tasks, robots handling repetitive ones), improved safety by reducing the risk of human injury in hazardous environments, and enhanced efficiency by optimizing workflows. For example, a human worker might oversee a fleet of automated guided vehicles (AGVs) in a warehouse, managing their routes and addressing any unexpected issues.
Disadvantages include the initial investment costs associated with integrating robotic systems, the need for robust safety protocols to prevent accidents, and the potential for disruptions if robotic systems malfunction. Furthermore, the effective integration of human-robot teams requires careful planning, training, and ongoing management to ensure seamless collaboration and prevent conflict between human workers and automated systems. Careful consideration of ergonomic factors is also crucial to minimize worker strain and injury even in collaborative settings.
Cost-Benefit Analysis of Robotics Implementation
Implementing robotic systems in logistics isn’t a whimsical decision; it’s a strategic investment demanding careful consideration of costs and benefits. This analysis explores the financial implications, highlighting both the initial outlay and the potential long-term returns. Understanding this balance is crucial for businesses weighing the adoption of automation.
Initial Investment Costs
The upfront costs associated with robotic systems in logistics can be substantial. These costs vary significantly depending on the scale of implementation, the type of robots chosen (e.g., AGVs, AMRs, robotic arms), and the level of integration required with existing warehouse management systems (WMS). Major components include the purchase price of the robots themselves, the cost of installation and setup, the necessary infrastructure upgrades (such as improved power supplies and network connectivity), and the cost of training personnel to operate and maintain the new systems. Furthermore, ongoing maintenance contracts, software licensing fees, and potential integration costs with existing systems must be factored in. A small warehouse might invest tens of thousands, while a large distribution center could spend millions.
Long-Term Cost Savings and Efficiency Gains
While the initial investment is significant, the long-term cost savings and efficiency gains from robotic systems often outweigh the initial expenditure. Robotics significantly reduces labor costs by automating repetitive tasks such as picking, packing, and transporting goods. This leads to a decrease in human error, resulting in fewer damaged products and reduced waste. Improved efficiency translates to faster order fulfillment, leading to increased customer satisfaction and potentially higher sales. Moreover, optimized warehouse space utilization, enabled by efficient robotic systems, can lead to lower rental or property costs. The reduction in operational expenses, coupled with increased productivity and revenue, generates a substantial return on investment over time.
Cost-Benefit Analysis Table: Hypothetical Warehouse Automation Project
The following table illustrates a hypothetical five-year cost-benefit analysis for a warehouse automation project. This example assumes a moderate-sized warehouse implementing a combination of automated guided vehicles (AGVs) and robotic picking arms. Remember, actual figures will vary considerably based on specific circumstances.
Year | Initial Investment & Ongoing Costs | Cost Savings (Labor, Waste Reduction, etc.) | Net Benefit (Savings – Costs) |
---|---|---|---|
0 (Initial Investment) | -$500,000 | $0 | -$500,000 |
1 | -$50,000 | $100,000 | $50,000 |
2 | -$40,000 | $120,000 | $80,000 |
3 | -$40,000 | $140,000 | $100,000 |
4 | -$40,000 | $160,000 | $120,000 |
5 | -$40,000 | $180,000 | $140,000 |
Note: This is a simplified example. A comprehensive cost-benefit analysis should include detailed projections of all costs and savings, considering factors such as inflation, potential downtime, and the lifespan of the robotic equipment. Consulting with logistics automation experts is highly recommended.
Future Trends and Technological Advancements
The logistics industry is on the cusp of a transformative era, driven by rapid advancements in robotics and related technologies. These innovations promise to not only enhance existing automation but also create entirely new possibilities for efficiency, scalability, and resilience within supply chains. The integration of sophisticated AI and machine learning algorithms is particularly pivotal in this evolution.
The next generation of logistics robots will be far more intelligent and adaptable than their predecessors. This isn’t just about faster picking and packing; it’s about systems that can learn, optimize, and respond to unexpected situations in real-time. For example, a warehouse robot equipped with advanced AI could autonomously reroute itself around an obstacle, predict potential bottlenecks, or even adjust its picking strategy based on real-time inventory data and order patterns. This level of autonomous decision-making significantly reduces human intervention and maximizes operational fluidity.
Robotic Swarms and Collaborative Networks
The concept of robotic swarms, where multiple robots coordinate their actions to achieve a common goal, is rapidly moving from theoretical research into practical application. Imagine a warehouse where dozens of small, agile robots work collaboratively to sort, move, and package goods. Each robot specializes in a specific task, communicating seamlessly with its peers and the central control system to optimize overall efficiency. This approach allows for increased flexibility and scalability, as the number of robots can be easily adjusted to meet fluctuating demand. Companies like Amazon are already exploring similar technologies for improved warehouse management, showcasing the practical potential of these collaborative systems. The coordinated movement of these robots, akin to a well-orchestrated dance, minimizes congestion and maximizes throughput.
Advanced Data Analytics and Robotic Optimization
Advanced data analytics plays a crucial role in unlocking the full potential of robotic systems in logistics. By collecting and analyzing vast amounts of data from various sources – sensor readings from robots, inventory management systems, transportation tracking data, and customer order information – companies can gain invaluable insights into operational bottlenecks and areas for improvement. This data-driven approach allows for predictive maintenance of robots, preventing costly downtime and ensuring consistent performance. Furthermore, AI-powered algorithms can analyze data to optimize robot routing, task allocation, and even the design of warehouse layouts, resulting in significant gains in efficiency and cost savings. For instance, analyzing historical data on delivery routes can reveal optimal routes, minimizing travel time and fuel consumption. This proactive approach, informed by data-driven insights, transforms reactive problem-solving into predictive optimization.
Case Studies: The Role Of Robotics In Improving The Efficiency Of The Logistics Industry
Real-world examples showcase the transformative power of robotics in logistics. These case studies highlight the tangible benefits – increased efficiency, reduced costs, and improved overall operational effectiveness – achieved through strategic robotic implementation across diverse logistical settings. Let’s dive into some compelling examples.
Amazon Robotics Implementation
Amazon, a global e-commerce giant, has extensively integrated robotics into its fulfillment centers. Their Kiva robots (now Amazon Robotics) are autonomous mobile robots that retrieve shelves of products and transport them to human workers for picking and packing. This system significantly reduces the time and distance workers need to travel, leading to faster order fulfillment.
Company Name | Type of Implementation | Results | Challenges Faced |
---|---|---|---|
Amazon | Autonomous Mobile Robots (AMRs) for order fulfillment | Increased picking speed by 2-3x, reduced order fulfillment time, improved worker productivity, and optimized warehouse space utilization. | High initial investment costs, integration complexities, and the need for robust safety protocols to ensure worker safety alongside robots. |
DHL’s Use of Automated Guided Vehicles (AGVs), The Role of Robotics in Improving the Efficiency of the Logistics Industry
DHL, a leading global logistics company, employs Automated Guided Vehicles (AGVs) in its warehouses to transport goods efficiently. These vehicles follow pre-programmed routes, carrying heavy pallets or containers, optimizing material flow and reducing manual labor. This automation minimizes human error, improves delivery times, and allows for increased throughput.
Company Name | Type of Implementation | Results | Challenges Faced |
---|---|---|---|
DHL | Automated Guided Vehicles (AGVs) for material handling | Improved warehouse throughput, reduced transportation time, minimized human error in material handling, and enhanced safety by reducing manual handling of heavy loads. | Initial investment costs, adapting existing warehouse infrastructure to accommodate AGVs, and ensuring seamless integration with existing warehouse management systems. |
JD.com’s Drone Delivery System
JD.com, a major Chinese e-commerce company, has pioneered drone delivery in remote areas. Their drones autonomously transport packages, overcoming geographical limitations and significantly reducing delivery times compared to traditional methods. This innovative approach expands delivery reach and enhances customer satisfaction, especially in areas with limited road infrastructure.
Company Name | Type of Implementation | Results | Challenges Faced |
---|---|---|---|
JD.com | Drone delivery system for remote areas | Faster delivery times to remote locations, expanded delivery reach, increased customer satisfaction, and reduced reliance on traditional transportation methods. | Regulatory hurdles related to drone operation, ensuring safe and reliable drone flights, and managing weather-related disruptions. |
Last Recap
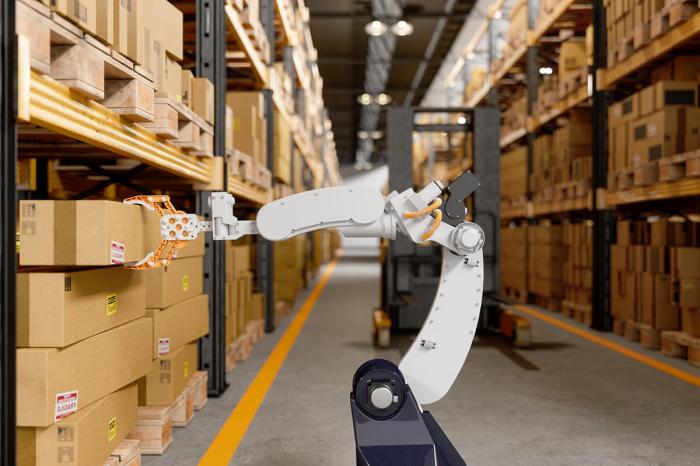
Source: indatalabs.com
The rise of robotics in the logistics industry isn’t just about faster delivery; it’s a complete overhaul of how goods move around the world. While challenges remain – from workforce adaptation to ethical considerations – the benefits are undeniable: increased efficiency, reduced costs, and the potential for a more sustainable supply chain. The future is automated, and the logistics industry is leading the charge. Buckle up, because this is just the beginning of the robotic revolution.