The Role of Robotics in Improving Productivity in the Workplace is no longer a futuristic fantasy; it’s the present reality reshaping industries worldwide. From the whirring arms of assembly lines to the precision instruments of robotic surgery, automation is revolutionizing how we work. This isn’t just about replacing humans with machines; it’s about a collaborative evolution, where robots handle the repetitive, dangerous, or incredibly precise tasks, freeing up human workers for more creative and strategic roles. We’ll dive into the nitty-gritty, exploring how robotics is boosting efficiency, impacting various sectors, and even raising some interesting ethical questions along the way.
We’ll explore the historical journey of robotics in the workplace, showcasing the diverse types of robots currently employed and how they’re enhancing productivity across manufacturing, logistics, healthcare, and beyond. We’ll also analyze the economic and social consequences, addressing concerns about job displacement while highlighting the exciting new career opportunities this technological leap creates. Get ready for a deep dive into the fascinating world of workplace robotics – it’s more exciting than you think!
Introduction to Robotics in the Workplace: The Role Of Robotics In Improving Productivity In The Workplace
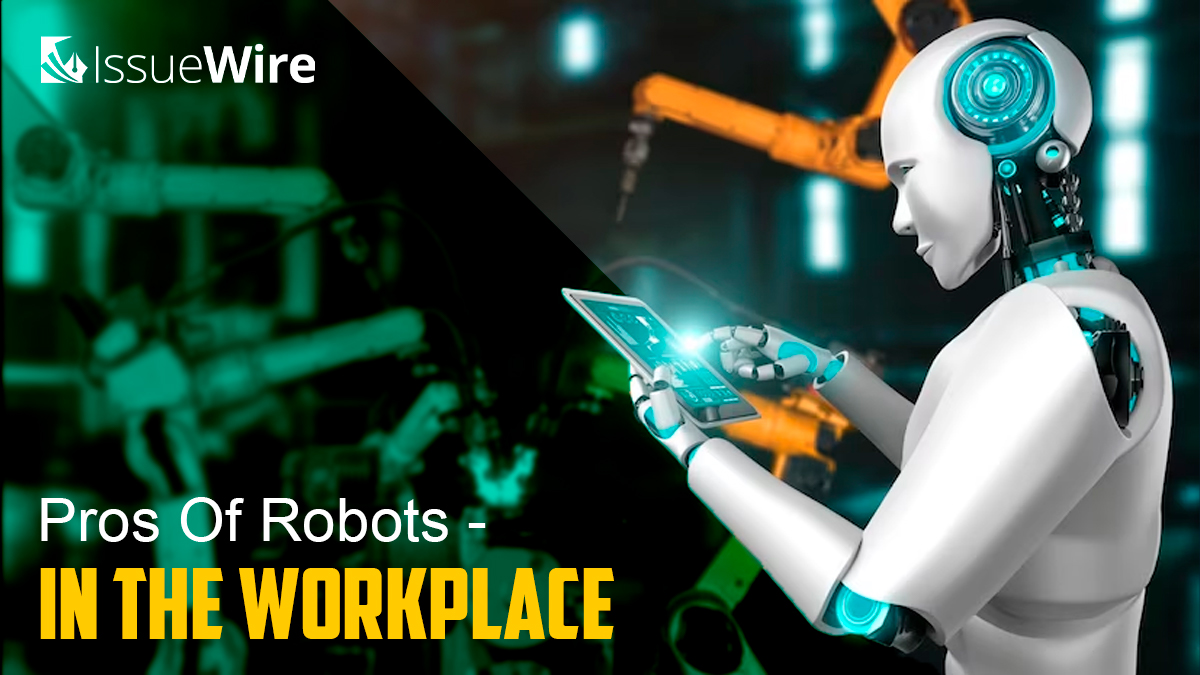
Source: amazonaws.com
Robots are boosting workplace efficiency, streamlining tasks from assembly lines to data analysis. This automation revolution mirrors advancements in other fields, like medicine, where AI is making huge strides. Check out how The Role of Artificial Intelligence in Advancing Drug Discovery is accelerating breakthroughs. Ultimately, both robotics and AI promise a future of increased productivity across various sectors, improving lives and shaping the world around us.
The integration of robots into various work environments is no longer a futuristic fantasy; it’s a rapidly evolving reality. From manufacturing giants to small-scale businesses, the adoption of robotics is reshaping industries, boosting productivity, and altering the very nature of work itself. This shift reflects a confluence of factors: advancements in artificial intelligence, decreasing robot costs, and the growing need for automation in a competitive global market.
Robotics has profoundly impacted the industrial landscape, gradually transforming from simple, repetitive-task machines to sophisticated, adaptable systems capable of complex operations. This evolution hasn’t been a linear progression, but rather a series of breakthroughs spurred by technological advancements and evolving industry demands. The journey has seen a significant increase in both the capabilities and affordability of robots, making them accessible to a broader range of businesses.
Types of Robots Used in Workplaces, The Role of Robotics in Improving Productivity in the Workplace
The world of industrial robotics is incredibly diverse. Robots are no longer simply hulking arms performing welds on assembly lines. The variety of robotic systems deployed across industries reflects the specialized needs of different tasks and environments.
- Articulated Robots: These are the most common type, resembling a human arm with multiple joints allowing for a wide range of motion. They’re frequently used in manufacturing for tasks like welding, painting, and assembly.
- Cartesian Robots (Gantry Robots): These robots move along three linear axes (X, Y, and Z), ideal for precise movements in a defined workspace. They are often used in pick-and-place operations, 3D printing, and CNC machining.
- SCARA Robots (Selective Compliance Assembly Robot Arm): Designed for high-speed assembly tasks, these robots excel at vertical movement and are commonly found in electronics manufacturing and packaging.
- Collaborative Robots (Cobots): Designed to work alongside human employees, cobots are equipped with safety features that allow for close interaction. They are used in various settings, assisting with tasks that require human-robot collaboration, such as machine tending or quality inspection.
- Mobile Robots (AGVs and AMRs): Autonomous Guided Vehicles (AGVs) follow pre-programmed paths, while Autonomous Mobile Robots (AMRs) use advanced sensors and AI to navigate dynamically. They are increasingly used in warehouses and logistics for material handling and transportation.
Historical Evolution of Industrial Robotics
The history of industrial robots is marked by several key phases. Early industrial robots, appearing in the mid-20th century, were primarily large, programmable machines capable of performing repetitive tasks. The development of microprocessors and advancements in computer programming in the 1970s and 80s led to more sophisticated robots with improved dexterity and control. The advent of sensors and AI in recent decades has further revolutionized the field, enabling robots to adapt to changing environments and collaborate effectively with humans. For instance, the introduction of Unimation’s Unimate in the 1960s marked a pivotal moment, automating tasks in General Motors’ assembly lines. This early adoption laid the foundation for widespread industrial robotics adoption.
Current State of Robotics Adoption Across Industries
The adoption of robotics varies significantly across different sectors. Manufacturing remains the largest adopter, with robots widely used in automotive, electronics, and food processing. However, the use of robots is expanding rapidly into other areas, including healthcare (surgical robots), logistics (warehouse automation), agriculture (harvesting robots), and even the service industry (robotic waiters). The increasing affordability and versatility of robots are driving this wider adoption, alongside the growing need for increased efficiency and productivity in various industries. Companies like Amazon, with its vast network of fulfillment centers, exemplify the transformative power of robotics in logistics. The deployment of thousands of robots significantly accelerates order processing and delivery times.
Productivity Enhancement through Robotics
The integration of robots into the workplace isn’t just a futuristic fantasy; it’s a tangible reality driving significant productivity gains across various industries. Robots are revolutionizing how work gets done, offering solutions that enhance efficiency, safety, and precision, ultimately boosting the bottom line. This section explores the key ways robots contribute to increased productivity.
Improved Efficiency in Repetitive Tasks
Robots excel at performing repetitive tasks with unwavering consistency and speed. Human workers, prone to fatigue and occasional errors, can’t match the tireless efficiency of a robot on assembly lines, packaging operations, or data entry. For instance, in automotive manufacturing, robots weld car bodies with pinpoint accuracy and speed, far exceeding the capabilities of human welders. This increased speed translates directly to a higher output of finished vehicles per day, significantly improving overall factory productivity. The elimination of human error in these repetitive tasks also minimizes waste and rework, further enhancing efficiency.
Handling of Hazardous Materials
Robots play a crucial role in handling hazardous materials, protecting human workers from exposure to dangerous substances or environments. In industries like nuclear power, chemical processing, and waste management, robots can safely perform tasks involving radioactive materials, toxic chemicals, or explosive compounds. This eliminates the risk of human injury or illness, ensuring worker safety while maintaining productivity. For example, robots are used in bomb disposal squads to disarm explosive devices, minimizing the risk to human life. Similarly, in nuclear power plants, robots are employed for maintenance and repair tasks in high-radiation areas.
Increased Precision and Reduced Errors in Manufacturing
The precision of robotic systems far surpasses that of human capabilities in many manufacturing processes. Robots can perform tasks with microscopic accuracy, resulting in higher quality products and reduced waste due to defects. In electronics manufacturing, for example, robots are used for assembling microchips and other delicate components with incredible precision, minimizing the risk of damage or malfunction. This improved precision leads to fewer defects, less rework, and higher overall yield, directly contributing to increased productivity. The consistent accuracy of robots also ensures that products meet stringent quality standards, enhancing brand reputation and customer satisfaction.
Comparative Analysis: Human vs. Robotic Performance
Task | Human Performance | Robotic Performance | Notes |
---|---|---|---|
Welding Car Bodies | Moderate speed, prone to fatigue and inconsistencies | High speed, consistent precision, tireless operation | Robots significantly increase output and reduce defects. |
Microchip Assembly | Low speed, high error rate, susceptible to hand tremors | High speed, extremely high precision, minimal errors | Robots enable mass production of high-quality electronics. |
Packaging | Moderate speed, prone to errors and inconsistencies | High speed, consistent accuracy, high throughput | Robots increase packaging efficiency and reduce waste. |
Hazardous Waste Handling | High risk of injury or illness, slow and limited operations | Safe and efficient operation in hazardous environments | Robots protect human workers from dangerous exposure. |
Impact on Different Industries
Robotics is rapidly transforming various sectors, boosting productivity and efficiency in ways previously unimaginable. Its impact isn’t limited to a single industry; rather, it’s a widespread revolution affecting how we manufacture goods, deliver services, and even perform complex medical procedures. The versatility of robotics allows for tailored applications across diverse fields, leading to significant improvements in output and quality.
Robotics in Manufacturing and Logistics
The manufacturing and logistics sectors have embraced robotics with open arms, experiencing a surge in productivity and reduced operational costs. In manufacturing, robots perform repetitive tasks like welding, painting, and assembly with unparalleled precision and speed, minimizing human error and maximizing output. Think of car assembly lines, where robots flawlessly weld car bodies together at incredible speeds, a feat impossible to replicate consistently with human labor alone. In logistics, robots handle tasks such as warehousing, order fulfillment, and transportation. Automated guided vehicles (AGVs) navigate warehouses efficiently, transporting goods to their designated locations, while robotic arms swiftly sort and package items for shipment. This automated system optimizes warehouse space and accelerates order processing times, leading to faster delivery and improved customer satisfaction.
Benefits of Robotic Surgery in Healthcare
Robotic surgery represents a significant advancement in the healthcare sector, offering numerous benefits over traditional methods. Robotic surgical systems provide surgeons with enhanced precision, dexterity, and control, leading to smaller incisions, reduced trauma, less pain, and faster recovery times for patients. The magnified, high-definition 3D visualization capabilities of robotic systems allow surgeons to operate with greater accuracy, particularly in complex procedures. For instance, in minimally invasive cardiac surgery, robotic systems allow surgeons to perform intricate procedures with smaller incisions, leading to reduced blood loss, shorter hospital stays, and improved patient outcomes. The minimally invasive nature of robotic surgery also reduces the risk of infection and complications.
Robotics in Agriculture versus Construction
The applications of robotics in agriculture and construction differ significantly, reflecting the unique challenges of each sector. In agriculture, robots are increasingly used for tasks such as planting, harvesting, and spraying crops. Automated tractors and drones equipped with sensors and cameras can monitor crop health, optimize irrigation, and apply pesticides precisely, minimizing waste and maximizing yields. For example, autonomous tractors can navigate fields autonomously, planting seeds at optimal depths and spacing. In construction, robots are used for tasks such as bricklaying, welding, and demolition. Robotic arms can perform these tasks with greater speed and precision than human workers, improving efficiency and safety. However, the unstructured and unpredictable nature of construction sites presents greater challenges for robotics than the more controlled environment of a farm.
- Manufacturing: Increased production speed and precision, reduced human error, improved product quality, enhanced worker safety.
- Logistics: Optimized warehouse space utilization, faster order fulfillment, reduced transportation costs, improved delivery times.
- Healthcare (Robotic Surgery): Minimally invasive procedures, enhanced precision and control, smaller incisions, faster patient recovery, reduced risk of infection.
- Agriculture: Optimized resource utilization, increased crop yields, reduced labor costs, improved crop monitoring and management.
- Construction: Increased construction speed and efficiency, enhanced worker safety, improved precision in construction tasks, reduced material waste.
Economic and Social Implications
The integration of robotics into the workplace presents a complex interplay of economic and social consequences. While offering significant productivity boosts and economic growth, it also raises concerns about job displacement and the need for workforce adaptation. Understanding these implications is crucial for navigating the transition to a more automated future and ensuring a just and equitable distribution of benefits.
The introduction of robots undeniably impacts employment. While some jobs are automated, leading to displacement, the robotics industry itself creates numerous new opportunities. This shift necessitates proactive strategies for retraining and upskilling the workforce to meet the demands of the evolving job market. Furthermore, increased productivity through robotics translates into economic benefits, potentially leading to higher overall economic output and improved standards of living. However, the distribution of these benefits needs careful consideration to prevent exacerbating existing inequalities.
Robotics’ Effect on Employment Rates and Job Displacement
The automation of tasks through robotics inevitably leads to job displacement in certain sectors. Manufacturing, for example, has seen a significant reduction in the need for assembly line workers due to the widespread adoption of robotic arms and automated systems. Similarly, warehousing and logistics have witnessed the introduction of automated guided vehicles (AGVs) and robotic picking systems, reducing the demand for human labor in these areas. However, it’s important to note that the extent of job displacement varies across industries and depends on factors such as the level of automation implemented and the adaptability of the workforce. The impact is not solely negative; some jobs become safer, and repetitive strain injuries are reduced.
New Job Creation in Robotics-Related Fields
The growth of the robotics industry itself generates a significant number of new jobs. These range from robotics engineers and technicians responsible for designing, building, and maintaining robots to programmers developing the software that controls them, and data scientists analyzing the vast amounts of data generated by robotic systems. Furthermore, there is a growing demand for specialists in areas like artificial intelligence (AI), machine learning, and cybersecurity, all crucial for the effective operation and security of robotic systems. The rise of service robots also creates roles in areas like maintenance, repair, and customer service. For instance, companies specializing in robotic process automation (RPA) are constantly hiring software developers and consultants to implement and manage these systems.
Economic Benefits of Increased Productivity from Robotic Integration
Increased productivity resulting from robotic integration translates into significant economic benefits. Companies can achieve higher output with reduced labor costs, leading to increased profitability and competitiveness. This increased efficiency can also result in lower prices for consumers, making goods and services more accessible. Furthermore, the automation of dangerous or repetitive tasks improves workplace safety and reduces the risk of workplace injuries, leading to lower healthcare costs and improved employee well-being. For example, the automotive industry has seen substantial productivity gains from robotic welding and painting, leading to higher production volumes and lower costs.
Cost-Benefit Analysis of Implementing Robots
Factor | Cost | Benefit | Net Benefit |
---|---|---|---|
Initial Investment (Robot Purchase & Installation) | $100,000 – $500,000 (depending on robot type and complexity) | Increased Productivity, Reduced Labor Costs | Variable, depends on ROI period |
Maintenance & Repair | $5,000 – $20,000 annually | Reduced downtime, extended robot lifespan | Positive if maintenance is proactive |
Training & Integration | $10,000 – $50,000 | Improved efficiency, faster implementation | Positive if training is effective |
Reduced Labor Costs | N/A | Savings from reduced human workforce | Significant, depending on labor costs and automation level |
Challenges and Future Trends
Integrating robots into the workplace isn’t a simple plug-and-play operation. It requires careful planning, significant investment, and a proactive approach to address potential hurdles. Successfully navigating these challenges is crucial for reaping the full benefits of robotic automation.
The path to a fully automated future isn’t without its bumps. Several key obstacles stand in the way of widespread robotic integration, ranging from the technical to the social and economic. Overcoming these obstacles requires a multi-faceted approach, combining technological innovation with strategic workforce planning and policy adjustments.
Integration Challenges in Existing Workflows
Integrating robots into existing workflows often necessitates significant modifications to production lines, factory layouts, and even the overall business processes. This can be costly and time-consuming, requiring extensive planning and potentially disrupting ongoing operations. For instance, a manufacturing plant might need to redesign its assembly line to accommodate a new robotic arm, requiring downtime and retraining of personnel. Moreover, ensuring seamless communication and data exchange between robots and existing systems can be technically complex. Compatibility issues between different robotic systems and legacy software can also pose significant integration challenges.
The Need for Skilled Labor
The operation and maintenance of advanced robotic systems demand a highly skilled workforce. This isn’t simply about operating a machine; it requires expertise in programming, troubleshooting, repair, and system integration. The shortage of skilled technicians and engineers capable of handling these complex systems presents a major bottleneck to wider adoption. Training programs and educational initiatives are crucial to address this skills gap and prepare the workforce for the demands of the robotic age. Companies are increasingly investing in apprenticeship programs and partnerships with educational institutions to develop a pipeline of skilled technicians. For example, FANUC, a leading robotics company, offers extensive training programs for its robotic systems, ensuring that technicians have the necessary skills to maintain and repair their equipment.
Advancements in AI and Machine Learning for Robotics
Artificial intelligence (AI) and machine learning (ML) are revolutionizing the capabilities of robots, enabling them to perform increasingly complex tasks with greater autonomy and adaptability. AI-powered robots can learn from experience, adapt to changing environments, and even make decisions without human intervention. For example, advancements in computer vision allow robots to “see” and interpret their surroundings, enabling them to navigate complex environments and perform tasks that require visual recognition. Similarly, machine learning algorithms enable robots to improve their performance over time, learning from past mistakes and optimizing their actions. This increased autonomy is leading to the development of collaborative robots (cobots) that can work safely alongside human workers, enhancing productivity and efficiency.
Emerging Robotic Technologies and Their Potential Impact
Several emerging robotic technologies are poised to reshape industries and redefine the future of work. One example is the rise of soft robotics, which utilizes flexible materials to create robots that are safer and more adaptable to unstructured environments. These robots can be used in delicate tasks, such as surgery or handling fragile objects, where traditional rigid robots would be unsuitable. Another exciting area is the development of swarm robotics, where multiple robots work together to accomplish a common goal. This approach is particularly promising for tasks that require coordination and distributed intelligence, such as search and rescue operations or environmental monitoring. Furthermore, advancements in human-robot interaction are enabling robots to understand and respond to human commands and gestures more effectively, leading to more intuitive and user-friendly robotic systems. The increasing use of cloud computing and edge computing is also transforming robotics, enabling robots to access vast amounts of data and processing power, leading to improved performance and adaptability. Amazon’s use of sophisticated robotics in its fulfillment centers exemplifies the transformative potential of these technologies in enhancing productivity and efficiency across various sectors.
Case Studies
Successful robotic implementations aren’t just theoretical concepts; they’re real-world examples of increased efficiency and productivity across diverse industries. These case studies highlight how companies strategically integrated robots, navigated implementation challenges, and ultimately reaped significant rewards. Examining these successes provides valuable insights for businesses considering similar ventures.
Amazon’s Fulfillment Center Robotics
Amazon’s extensive use of robotics in its fulfillment centers is a prime example of large-scale robotic integration. They utilize Kiva robots (now Amazon Robotics) to transport shelves of goods to human workers, significantly reducing the time and effort spent on order fulfillment. This system optimizes warehouse layout and workflow, leading to faster order processing and delivery times. The initial investment was substantial, requiring significant infrastructure changes and employee retraining, but the return on investment has been substantial, demonstrably increasing order fulfillment speed and lowering operational costs.
- Significant reduction in order fulfillment time.
- Improved warehouse efficiency and space utilization.
- Increased employee productivity by automating repetitive tasks.
- High initial investment cost offset by long-term operational savings.
FANUC Robotics in Automotive Manufacturing
FANUC, a leading robotics company, provides automated solutions for various industries, with a strong presence in automotive manufacturing. Their robots perform tasks such as welding, painting, and assembly with high precision and speed, far exceeding human capabilities in these repetitive, high-precision applications. Challenges included integrating the robots seamlessly into existing production lines and ensuring worker safety alongside the robots. FANUC addressed these through advanced safety protocols and collaborative robot designs. The result is increased production output, improved product quality, and reduced labor costs.
- Substantial increase in production output and speed.
- Improved product quality and consistency through precise robotic actions.
- Reduced labor costs and improved worker safety through automation.
- Successful integration required careful planning and implementation.
Tesla’s Gigafactory Automation
Tesla’s Gigafactories exemplify a highly automated approach to manufacturing electric vehicles and batteries. Robots handle a wide array of tasks, from assembling battery packs to installing vehicle components. The scale of automation presents significant logistical challenges, including ensuring smooth coordination between various robotic systems and minimizing downtime. Tesla overcame these by implementing sophisticated software and control systems, resulting in high production volumes and faster manufacturing cycles. While initial investment was immense, the payoff lies in increased production capacity and reduced manufacturing costs per vehicle.
- Massive increase in vehicle production capacity.
- Reduced manufacturing time and costs per vehicle.
- Implementation required sophisticated software and control systems.
- High initial investment, but substantial return on investment due to increased production.
Ethical Considerations
The rise of robotics in the workplace presents a fascinating paradox: while promising increased productivity and efficiency, it also raises complex ethical questions that demand careful consideration. Balancing the potential benefits with the potential drawbacks requires a proactive approach, ensuring that technological advancements serve humanity’s best interests. This involves scrutinizing the societal, economic, and individual impacts of widespread automation.
The integration of robots into the workplace necessitates a comprehensive ethical framework, addressing concerns ranging from job displacement to algorithmic bias. Failing to address these concerns could lead to significant social unrest and exacerbate existing inequalities.
Workplace Safety Protocols Around Robots
Safeguarding human workers in robotic environments is paramount. This involves implementing rigorous safety protocols, including robust emergency stop mechanisms, physical barriers to prevent accidental contact, and comprehensive training programs for employees working alongside robots. Regular maintenance and inspections of robotic systems are also crucial to prevent malfunctions that could lead to accidents. Companies should invest in advanced safety technologies like sensor systems that detect human presence and automatically adjust robot behavior to avoid collisions. Furthermore, clear communication protocols and emergency response plans are essential to ensure a swift and effective response in case of incidents. Consider, for instance, the automotive industry, where collaborative robots (cobots) work alongside human assembly line workers. The success of these implementations relies heavily on stringent safety measures, including light curtains, pressure sensors, and speed limiting systems to prevent injuries.
Potential for Bias in Robotic Systems and Mitigation Strategies
Robotic systems, particularly those utilizing artificial intelligence (AI), are trained on data. If this data reflects existing societal biases, the resulting robotic system may perpetuate or even amplify those biases. For example, a facial recognition system trained primarily on images of one demographic may struggle to accurately identify individuals from other demographics, potentially leading to discriminatory outcomes in security or hiring processes. Mitigating this requires careful curation of training data to ensure representation from diverse groups and the implementation of algorithmic auditing to identify and correct biased outputs. Transparency in the development and deployment of robotic systems is also crucial, allowing for independent scrutiny and the identification of potential biases. Furthermore, regular updates and retraining of robotic systems can help adapt to evolving societal norms and address any emerging biases. For instance, a recruitment robot trained on historical hiring data might inadvertently discriminate against women or minorities if the historical data reflects gender or racial bias. By actively addressing this bias in the training data and through ongoing monitoring, companies can work towards fairer and more equitable outcomes.
Hypothetical Ethical Dilemma: The Case of the Automated Factory
Imagine a fully automated factory, producing essential medical equipment. Due to a software glitch, the robotic system malfunctions, resulting in a significant production slowdown. The company faces a critical ethical dilemma: prioritize repairing the system, potentially leading to a temporary shortage of vital medical supplies, or implement a temporary, less efficient, human-led process, impacting profitability and potentially delaying the delivery of life-saving equipment. This scenario highlights the intricate ethical considerations involved in relying on automated systems for critical processes. The decision requires weighing the potential negative consequences of both options – a shortage of essential medical supplies versus financial losses and production delays – and choosing the course of action that minimizes harm while upholding ethical principles. This choice necessitates careful consideration of the potential impact on patients and the wider community, alongside the economic implications for the company.
Final Thoughts
The integration of robotics into the workplace isn’t just about increased efficiency; it’s about a fundamental shift in how we approach work itself. While challenges remain – from ethical considerations to the need for skilled labor – the potential benefits are undeniable. As robotic technology continues its rapid advancement, driven by AI and machine learning, we can anticipate even more transformative impacts on productivity and the very nature of jobs. The future of work is collaborative, and robots are key players in this exciting new chapter.