The Role of Robotics in Enhancing Supply Chain Efficiency – Robotics: Boosting Supply Chain Efficiency. Forget clunky, slow processes – the future of supply chains is automated, streamlined, and seriously smart. We’re talking robots zipping around warehouses, autonomous trucks hitting the highway, and AI optimizing every single move. This isn’t science fiction; it’s the reality reshaping how goods get from point A to point Z, faster and more efficiently than ever before. This deep dive explores the role of robotics in revolutionizing supply chain management, from warehouse automation to last-mile delivery.
The current challenges facing modern supply chains are numerous: increasing customer demands for faster delivery, escalating labor costs, and the ever-present risk of disruptions. Robotics offers a powerful solution, automating repetitive tasks, optimizing workflows, and improving overall efficiency. This article will examine different types of robots used in supply chain operations, their applications, advantages, and disadvantages. We’ll also delve into the integration of data analytics, the crucial human-robot collaboration aspect, and the economic and societal impacts of this technological shift.
Introduction
The modern supply chain is a complex beast, a global network humming with activity to get products from factory floor to consumer doorstep. But this intricate system is facing unprecedented challenges. Globalization, fluctuating demand, geopolitical instability, and the ever-present specter of disruptions – from pandemics to natural disasters – are putting immense pressure on companies to deliver efficiently and reliably. These pressures translate to increased costs, delayed shipments, and ultimately, unhappy customers. The need for a more resilient and agile supply chain is no longer a luxury; it’s a necessity for survival in today’s competitive landscape.
Supply chain efficiency, at its core, is about optimizing the flow of goods and information throughout the entire process. It’s about minimizing waste, reducing costs, and maximizing speed and responsiveness. Key performance indicators (KPIs) used to measure this efficiency include on-time delivery rates, inventory turnover, order fulfillment cycle time, and overall supply chain costs. Improving these metrics directly impacts a company’s profitability and customer satisfaction.
A Brief History of Robotics in Industrial Settings and Their Increasing Relevance to Supply Chains
The use of robots in industrial settings isn’t new; early industrial robots emerged in the 1960s, primarily performing simple, repetitive tasks in manufacturing. However, recent advancements in artificial intelligence (AI), machine learning, and computer vision have revolutionized robotics, enabling them to handle more complex and nuanced operations. This has led to a significant increase in their deployment across various supply chain stages, from warehousing and logistics to last-mile delivery. The rise of e-commerce and the increasing demand for faster, more reliable delivery has further accelerated the adoption of robotics, making them a critical component of modern supply chain strategies. For example, Amazon’s extensive use of robotic systems in its fulfillment centers is a prime example of this transformation, showcasing how automation can drastically increase efficiency and throughput. These advancements allow robots to handle a wider range of tasks, from picking and packing to sorting and transporting goods, with greater speed and accuracy than human workers alone.
Types of Robots in Supply Chain Operations
Forget the clunky robots of science fiction; today’s supply chain relies on a diverse fleet of automated helpers, each with its own strengths and weaknesses. These robotic workhorses are revolutionizing everything from warehousing to last-mile delivery, boosting efficiency and slashing costs. Let’s dive into the main players.
Automated Guided Vehicles (AGVs)
AGVs are the seasoned veterans of the robotic supply chain. These programmable vehicles follow a predetermined path, usually marked by wires, magnetic tape, or lasers. Think of them as the reliable delivery trucks of the warehouse, consistently moving pallets and materials along set routes. Their functionality is straightforward: transport goods from point A to point B. Applications include transporting materials between warehouse sections, loading and unloading trucks, and moving goods to packing stations. While AGVs are cost-effective for simple, repetitive tasks and highly reliable, their inflexibility – they can’t adapt to changing environments easily – and limited navigation capabilities are key drawbacks. Scalability can also be a challenge as adding more AGVs requires modifying existing infrastructure.
Autonomous Mobile Robots (AMRs)
AMRs are the next generation, the smart kids on the block. Unlike AGVs, AMRs navigate dynamically using sensors, cameras, and sophisticated software. They can map their surroundings, avoid obstacles, and even reroute themselves if needed. This adaptability makes them ideal for dynamic environments where layouts change frequently. Their functionalities are far more extensive than AGVs, including tasks such as picking, sorting, and delivering items within a warehouse. For example, an AMR might pick up a package from a shelf, scan its barcode, and then autonomously deliver it to the correct shipping bay. AMRs boast superior efficiency and scalability compared to AGVs, but their initial investment cost is higher. The sophisticated technology also demands more maintenance and skilled technicians for operation.
Collaborative Robots (Cobots)
Cobots are designed to work alongside human employees, not replace them. These robots are smaller, safer, and more flexible than AGVs or AMRs, designed for collaborative tasks that require human dexterity and judgment. Their functionality centers on assisting humans with repetitive or physically demanding tasks. For example, a cobot might assist a worker in assembling products, packaging items, or lifting heavy objects. The advantages of cobots lie in their ability to enhance human capabilities, increasing productivity without requiring extensive re-engineering of the workspace. However, their application is more limited than AGVs or AMRs, and the initial investment, while lower than AMRs, can still be significant for businesses. Scalability is relatively easier compared to AGVs but not as seamless as AMRs.
Robotics in Warehousing and Distribution
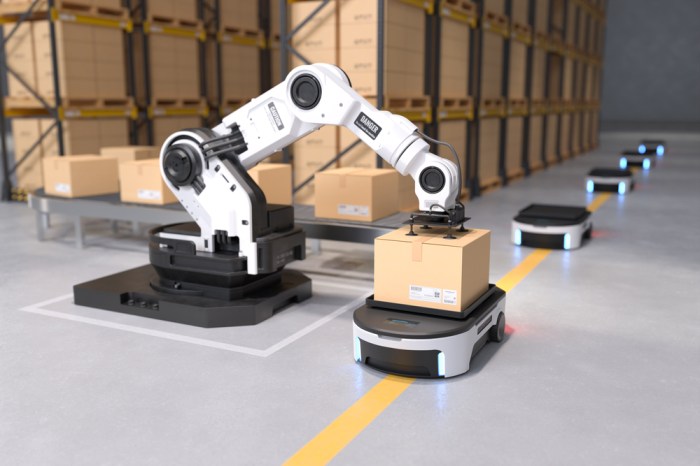
Source: igps.net
The warehouse, once a sprawling landscape of human-powered activity, is undergoing a dramatic transformation. Robotics are no longer a futuristic fantasy; they’re rapidly becoming the backbone of efficient and scalable warehousing and distribution operations, significantly impacting how goods are moved, stored, and shipped. This shift is driven by the increasing demands of e-commerce, the need for faster delivery times, and the persistent challenge of managing labor costs.
The integration of robotics into warehouse processes is revolutionizing picking, packing, and sorting, leading to increased throughput, reduced errors, and improved overall efficiency. Automation is addressing the inherent challenges of these tasks, which are often repetitive, physically demanding, and prone to human error.
Streamlining logistics with robotics is revolutionizing supply chain efficiency, boosting speed and accuracy. This precision mirrors the advancements in healthcare, where AI plays a crucial role, as detailed in this insightful article on The Role of AI in Advancing Precision Medicine. Ultimately, both fields demonstrate how intelligent automation leads to better outcomes – faster deliveries in one, and personalized treatments in the other.
Impact of Robotics on Warehouse Operations
Robotic systems are dramatically reshaping warehouse operations. Automated guided vehicles (AGVs) and autonomous mobile robots (AMRs) navigate warehouse floors, transporting goods between storage locations and packing stations with precision and efficiency. This eliminates the time and effort spent on manual transportation, freeing up human workers to focus on more complex tasks. Simultaneously, robotic arms equipped with advanced vision systems are rapidly picking and placing items, achieving speeds and accuracy far beyond human capabilities. Sophisticated sorting systems, often incorporating robotic arms and conveyor belts, quickly categorize and route packages based on destination, further streamlining the process. The net result is a significant increase in order fulfillment speed and accuracy, crucial elements in today’s fast-paced logistics environment.
Hypothetical Automated Warehouse Layout
Imagine a state-of-the-art warehouse, seamlessly integrating various robotic systems. The layout would be optimized for efficient material flow, minimizing travel distances and maximizing throughput. Upon arrival, goods are unloaded by robotic arms and automatically sorted by a high-speed robotic sorter. AMRs then transport these goods to designated storage locations within the warehouse, utilizing a sophisticated warehouse management system (WMS) for optimal space utilization. When an order is received, the WMS directs robotic picking arms to retrieve the required items. These items are then conveyed to a packing station, where another robotic arm packages them for shipment. Finally, AGVs transport the packaged orders to the shipping dock for dispatch.
Robot Type | Location | Tasks | Example Vendor |
---|---|---|---|
Automated Guided Vehicle (AGV) | Warehouse floor, shipping dock | Transporting goods between locations | Seegrid, KUKA |
Autonomous Mobile Robot (AMR) | Warehouse floor, storage areas | Material handling, transporting goods to storage | Locus Robotics, Fetch Robotics |
Robotic Arm (with vision system) | Picking stations, packing stations, sorting areas | Picking, placing, packing, sorting | Fanuc, ABB |
High-speed Robotic Sorter | Receiving dock, sorting area | Sorting incoming goods by type or destination | Dematic, Interroll |
Improved Order Fulfillment Speed and Accuracy
The implementation of robotic systems leads to a considerable improvement in both order fulfillment speed and accuracy. Robotic picking and packing systems operate at significantly higher speeds than human workers, leading to faster order processing and shorter lead times. Furthermore, robots are less prone to errors than humans, resulting in a reduction in picking and packing mistakes. This enhanced accuracy minimizes order discrepancies and returns, improving customer satisfaction and reducing operational costs. For instance, a large online retailer might see a 20-30% increase in order fulfillment speed and a 10-15% reduction in error rates after implementing a fully automated warehouse system. This translates directly into significant cost savings and a competitive advantage in a market driven by speed and accuracy.
Robotics in Transportation and Logistics
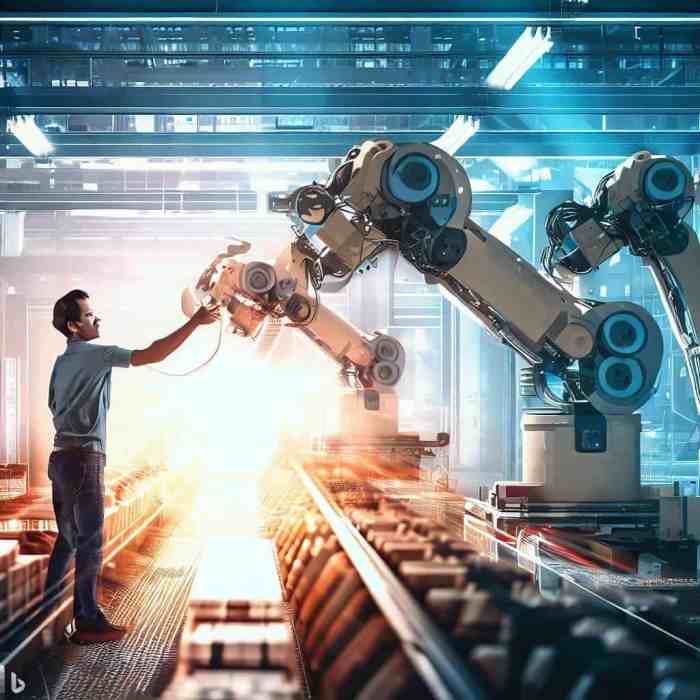
Source: automatedwarehouse.net
The integration of robotics into transportation and logistics is revolutionizing how goods are moved, from sprawling warehouses to the doorstep of the consumer. This shift is driven by the need for increased efficiency, reduced costs, and enhanced delivery speed in an increasingly demanding e-commerce landscape. Autonomous systems are no longer a futuristic fantasy; they’re actively reshaping the industry, promising a more streamlined and responsive supply chain.
Autonomous vehicles and drones are rapidly emerging as key players in last-mile delivery and broader transportation networks. These technologies offer the potential to significantly optimize delivery times, reduce operational costs, and improve overall supply chain resilience. However, their implementation also presents unique challenges that require careful consideration and strategic planning.
Autonomous Vehicles in Last-Mile Delivery
The final leg of the delivery journey, often the most expensive and time-consuming, is ripe for disruption by autonomous vehicles. Self-driving trucks and delivery vans can navigate complex urban environments, making multiple stops efficiently and operating around the clock. This reduces reliance on human drivers, mitigating labor shortages and associated costs. Imagine a fleet of self-driving vans smoothly navigating city streets, precisely delivering packages without the delays associated with traffic or driver fatigue. This vision is becoming a reality, albeit gradually, with companies actively testing and deploying these technologies. The potential for reduced delivery times, improved fuel efficiency, and enhanced safety are substantial.
Drones in Logistics and Transportation
Drones offer a unique solution for last-mile delivery, particularly in remote or challenging terrains. Their ability to bypass traffic congestion and access difficult-to-reach locations makes them ideal for delivering time-sensitive goods or those requiring specialized handling. Consider the use of drones for delivering medical supplies to remote hospitals or transporting urgent packages to customers in areas with limited road access. This agility offers significant advantages, although regulatory hurdles and concerns about safety and security need careful management.
Benefits and Challenges of Integrating Autonomous Vehicles
The integration of autonomous vehicles into existing supply chain networks presents numerous benefits, including increased efficiency, reduced labor costs, improved safety, and enhanced delivery speed. However, challenges remain. These include the high initial investment costs, the need for robust infrastructure (like charging stations and reliable communication networks), regulatory uncertainties, and concerns regarding cybersecurity and data privacy. Successfully navigating these challenges requires collaborative efforts between technology providers, logistics companies, and policymakers.
Examples of Successful Robotic Implementations
Several companies are leading the charge in integrating robotic solutions into their transportation and logistics operations. For instance, Amazon utilizes a large fleet of autonomous robots in its fulfillment centers, significantly improving warehouse efficiency. Companies like FedEx and UPS are actively testing and deploying autonomous delivery vehicles in select markets. While widespread adoption is still underway, these early adopters demonstrate the transformative potential of robotics in the industry. Their experiences offer valuable lessons for other businesses considering similar implementations. The success stories highlight the importance of strategic planning, careful integration, and a phased approach to adoption.
Data Analytics and Robotics Integration: The Role Of Robotics In Enhancing Supply Chain Efficiency
The synergy between data analytics and robotics is revolutionizing supply chain efficiency. By harnessing the power of data, businesses can optimize robotic operations, leading to significant improvements in speed, accuracy, and cost-effectiveness. This integration allows for proactive problem-solving and predictive maintenance, minimizing disruptions and maximizing ROI.
Data analytics provides the crucial intelligence needed to fine-tune robotic systems and optimize their performance within the dynamic environment of a supply chain. Real-time data streams from robots offer unparalleled insights into operational bottlenecks, areas for improvement, and potential future challenges. This allows for more informed decision-making, leading to a more agile and responsive supply chain.
Real-time Data Improves Decision-Making and Predicts Disruptions
Real-time data from robotic systems offers a powerful predictive capability. For instance, if a robotic arm in a warehouse consistently experiences slower-than-average pick rates, data analytics can identify the root cause – perhaps a malfunctioning sensor or a poorly designed workflow. This early detection allows for preventative maintenance or process adjustments, preventing larger disruptions later on. Similarly, analyzing data on robotic transportation movements can reveal patterns indicative of potential delays, allowing for proactive rerouting or alternative transportation arrangements. Consider a scenario where a fleet of autonomous delivery robots experiences a surge in traffic congestion during peak hours. Data analytics can predict this congestion based on historical traffic patterns and real-time traffic data, enabling the system to adjust delivery routes and schedules to minimize delays and maintain on-time delivery rates.
Key Data Points for Efficient Supply Chain Management
Effective data collection is paramount. The right data points, gathered and analyzed correctly, paint a clear picture of robotic system performance and overall supply chain health. Below are some key data points robotic systems should collect:
- Robot operational uptime: Tracking the percentage of time robots are actively functioning versus downtime due to maintenance, repairs, or malfunctions.
- Task completion rates: Measuring the number of tasks successfully completed within a given timeframe, indicating efficiency and accuracy.
- Error rates: Recording instances of errors, such as incorrect picking, placement, or sorting, allowing for identification of areas needing improvement.
- Energy consumption: Monitoring energy usage to identify potential inefficiencies and optimize energy management.
- Maintenance schedules and costs: Tracking maintenance activities, including preventative maintenance, repairs, and associated costs.
- Inventory levels and location: Real-time tracking of inventory levels and locations within the warehouse, providing accurate inventory visibility.
- Throughput and processing times: Measuring the volume of goods processed and the time taken to complete various tasks within the supply chain.
- Transportation routes and times: Tracking the routes taken by robotic transportation systems and the time taken to complete deliveries.
By meticulously collecting and analyzing these data points, businesses can gain a comprehensive understanding of their robotic systems’ performance and overall supply chain efficiency. This data-driven approach facilitates continuous improvement and optimization, leading to a more robust and responsive supply chain.
The Human Element
The integration of robotics into supply chains isn’t about replacing human workers; it’s about augmenting their capabilities and creating a more efficient, safer, and ultimately, more productive system. Human expertise remains crucial for tasks requiring adaptability, critical thinking, and complex problem-solving – skills that current robotic technology struggles to replicate effectively. The future of supply chain management lies in a collaborative partnership between humans and robots, leveraging the strengths of both.
The successful implementation of robotics necessitates a shift in the roles and responsibilities of human workers. Instead of performing repetitive, physically demanding tasks, humans will focus on higher-level functions requiring cognitive skills and emotional intelligence. This transition requires investment in training and upskilling programs to equip the workforce with the necessary skills to effectively interact with and manage robotic systems.
Required Skills for Human-Robot Collaboration
The successful integration of robots into the supply chain demands a workforce equipped with a specific skill set. This isn’t just about technical proficiency; it also encompasses soft skills essential for effective human-robot interaction. Workers need to understand the capabilities and limitations of the robotic systems they are working alongside, and know how to troubleshoot and maintain them. Crucially, they need to be comfortable working in a dynamic environment where roles and responsibilities are constantly evolving.
A Collaborative Work Environment
Imagine a modern warehouse where autonomous mobile robots (AMRs) swiftly transport goods across the facility, guided by sophisticated software. Human workers, equipped with augmented reality (AR) headsets, oversee the robots’ movements and intervene only when necessary, perhaps to resolve unexpected obstacles or handle delicate items that require a human touch. Meanwhile, advanced AI systems analyze real-time data from the robots and other sensors to optimize workflows, predict potential bottlenecks, and proactively adjust operations to maximize efficiency. In this scenario, humans are not simply operators; they are managers, strategists, and problem-solvers, working alongside robotic colleagues to achieve a common goal. This collaborative environment prioritizes safety, with robots equipped with sensors to prevent collisions with human workers, and clear protocols in place to manage any potential incidents. The result is a significantly more efficient and productive supply chain, where human ingenuity and robotic precision complement each other perfectly. Amazon’s fulfillment centers provide a real-world example, although their level of automation and human-robot collaboration is constantly evolving and improving.
Economic and Societal Impacts of Robotics in Supply Chains
The integration of robotics into supply chains presents a complex interplay of economic benefits and societal adjustments. While automation promises increased efficiency and reduced costs, it also raises concerns about job displacement and the need for workforce retraining. Understanding this dual impact is crucial for navigating the transition to a more automated future.
Cost-Benefit Analysis of Robotic Systems, The Role of Robotics in Enhancing Supply Chain Efficiency
Implementing robotic systems involves significant upfront investment in hardware, software, integration, and ongoing maintenance. However, the long-term benefits often outweigh these initial costs. Automated systems can operate 24/7, minimizing downtime and increasing throughput. They reduce labor costs associated with repetitive tasks, improve accuracy, and minimize errors leading to less waste and rework. For example, a large e-commerce fulfillment center might see a 20-30% reduction in operational costs within two to three years of implementing robotic picking and sorting systems, offsetting the initial investment. The return on investment (ROI) is highly dependent on factors like the scale of operations, the specific robotic systems deployed, and the efficiency gains achieved. A detailed cost-benefit analysis, considering both tangible and intangible factors, is essential before committing to such a significant technological upgrade.
Impact of Widespread Robotics Adoption on Employment
The widespread adoption of robotics in supply chains inevitably raises concerns about job displacement. While some jobs involving repetitive or physically demanding tasks are likely to be automated, this doesn’t necessarily translate to overall job losses. New roles will emerge in areas like robotics maintenance, programming, and system integration. Furthermore, the increased efficiency and productivity driven by robotics can lead to business expansion and the creation of new jobs in other sectors. However, a proactive approach to workforce retraining and upskilling is crucial to mitigate potential negative impacts. Government initiatives and industry partnerships can play a vital role in providing training programs that equip workers with the skills needed for the evolving job market. For instance, Amazon’s investment in robotics has led to the creation of new jobs in areas like software development, data analysis, and robotics maintenance, even as it automates some warehouse tasks.
Long-Term Economic Benefits of Improved Supply Chain Efficiency
Improved supply chain efficiency, driven by robotics, translates to significant long-term economic benefits. Reduced operational costs, faster delivery times, and increased accuracy lead to higher profitability for businesses. Consumers benefit from lower prices and increased product availability. Furthermore, enhanced supply chain resilience, enabled by automation, can mitigate disruptions caused by unforeseen events, such as natural disasters or pandemics. For example, the automotive industry’s adoption of robotic welding and assembly has significantly increased production efficiency and reduced manufacturing costs, leading to more competitive pricing and increased global market share. The overall economic impact is a boost in productivity, economic growth, and improved global competitiveness.
Future Trends and Challenges
The integration of robotics into supply chains is rapidly evolving, driven by advancements in technology and the ever-increasing demand for efficiency and speed. However, this journey isn’t without its hurdles. Understanding the emerging trends and anticipating the challenges is crucial for businesses aiming to leverage robotics effectively.
The coming years will witness a significant shift in how robotics are deployed and managed within supply chains, largely shaped by advancements in artificial intelligence and related technologies. This will not only enhance existing robotic capabilities but also unlock entirely new possibilities for automation and optimization. However, successful implementation requires careful consideration of integration complexities, workforce adaptation, and the broader economic and societal impacts.
Emerging Technologies Enhancing Robotics in Supply Chain Management
Artificial intelligence (AI) and machine learning (ML) are poised to revolutionize robotics in supply chains. AI empowers robots with cognitive abilities, enabling them to learn from data, adapt to changing conditions, and make independent decisions. For instance, AI-powered robots can optimize picking and packing strategies in real-time, reacting to unexpected inventory fluctuations or order surges. ML algorithms can predict equipment failures, allowing for proactive maintenance and minimizing downtime. The synergy between AI, ML, and robotics creates a self-learning, adaptive system capable of continuously improving its performance and efficiency. This surpasses the capabilities of traditional, pre-programmed robots significantly. Furthermore, advancements in computer vision are enabling robots to identify and handle a wider variety of items with greater precision, reducing errors and improving throughput.
Challenges Associated with Robotics Integration in Complex Supply Chains
Integrating robotics into existing supply chain infrastructure presents significant challenges. One key hurdle is the substantial upfront investment required for purchasing, installing, and maintaining robotic systems. This includes not only the cost of the robots themselves but also the necessary infrastructure upgrades, software integration, and employee training. Furthermore, ensuring seamless interoperability between different robotic systems and existing enterprise resource planning (ERP) systems can be technically complex and time-consuming. The need for robust cybersecurity measures to protect robotic systems from malicious attacks is also paramount. Finally, adapting existing workflows and retraining employees to work alongside robots requires careful planning and execution to avoid disruptions and maintain employee morale. A phased approach, focusing on high-impact areas first, can help mitigate these challenges.
Predictions for the Future of Robotics in Supply Chain Efficiency
The future of robotics in supply chains points towards increased autonomy, intelligence, and collaboration. We can expect to see a rise in autonomous mobile robots (AMRs) navigating warehouses and distribution centers without human intervention, collaborative robots (cobots) working safely alongside human employees, and AI-powered systems optimizing entire supply chains in real-time. For example, Amazon’s extensive use of robotics in its fulfillment centers demonstrates the potential for significant efficiency gains. Similarly, the increasing adoption of autonomous trucking for long-haul transportation suggests a future where goods are moved more efficiently and with reduced reliance on human drivers. However, the full realization of this potential depends on overcoming the aforementioned challenges and fostering a collaborative ecosystem involving technology providers, logistics companies, and policymakers. The next decade will likely see a dramatic increase in robotic adoption across various segments of the supply chain, leading to significant improvements in speed, accuracy, and overall efficiency.
Wrap-Up
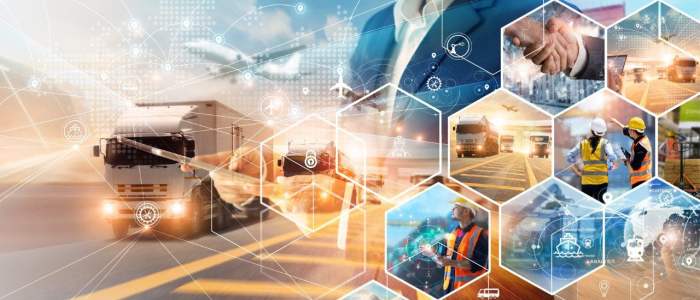
Source: primerobotics.com
The integration of robotics into supply chains isn’t just about faster delivery; it’s a complete overhaul of how we manage logistics. From automated warehouses to autonomous delivery fleets, robots are enhancing efficiency, reducing costs, and improving accuracy across the board. While challenges remain—like the need for skilled human-robot collaboration and addressing potential job displacement—the long-term benefits of embracing this technology are undeniable. The future of supply chain management is robotic, and it’s shaping up to be a seriously efficient one.