The Role of Robotics in Enhancing Manufacturing Efficiency isn’t just a buzzphrase; it’s a revolution reshaping industries. From the whirring arms of assembly lines to the precision of automated welding, robots are no longer futuristic fantasies, but crucial players in boosting production speed, slashing errors, and ultimately, driving down costs. This deep dive explores how robotic automation is transforming manufacturing, examining its impact, challenges, and the exciting future it promises.
We’ll unpack the different types of robots used – think articulated arms, nimble SCARA robots, and collaborative bots working hand-in-hand (literally!) with humans. We’ll also crunch the numbers, comparing the cost-effectiveness of robotic automation versus traditional manual labor. Prepare for a rollercoaster ride through real-world examples, uncovering how companies across various sectors are leveraging robotics to achieve unprecedented efficiency gains.
Introduction: The Role Of Robotics In Enhancing Manufacturing Efficiency
Industrial robots are revolutionizing manufacturing, boosting efficiency and productivity like never before. They’re essentially programmable machines designed to perform repetitive tasks, often in environments unsuitable for humans. Think of them as tireless, precise workers, constantly churning out products with unwavering consistency. Their applications span a huge range, from welding car bodies to assembling tiny electronics components, significantly impacting nearly every manufacturing sector.
The journey of robotics in manufacturing is a fascinating one. Early industrial robots, appearing in the late 1950s and early 1960s, were primarily large, hydraulically powered behemoths. Unimate, a pioneering robot arm developed by George Devol and Joseph Engelberger, found its first application in a General Motors factory, marking a significant turning point. Subsequent decades witnessed remarkable advancements, including the introduction of microprocessors, leading to more sophisticated control systems and enhanced dexterity. The rise of computer-aided design (CAD) and computer-aided manufacturing (CAM) further fueled this growth, enabling the creation of more complex and adaptable robots. Today, we see collaborative robots (cobots) working safely alongside humans, a testament to the ongoing evolution.
Types of Robots Used in Manufacturing
Different manufacturing processes demand different robotic solutions. This has led to the development of various robot types, each suited to specific tasks and environments. Choosing the right robot is crucial for optimizing efficiency and return on investment.
- Articulated Robots: These are the most common type, resembling a human arm with multiple rotating joints. Their flexibility allows them to reach into confined spaces and perform complex maneuvers, making them ideal for tasks like welding, painting, and material handling. Imagine a robot arm with six axes of movement, capable of reaching and manipulating objects in a three-dimensional workspace. This versatility is key to their widespread adoption across diverse industries.
- SCARA Robots: SCARA (Selective Compliance Assembly Robot Arm) robots are characterized by their two parallel arms that move vertically and rotate horizontally. Their design excels in high-speed assembly operations requiring precise movements within a two-dimensional plane. Think of them as incredibly nimble and quick, perfect for assembling small electronic components or placing parts on circuit boards.
- Collaborative Robots (Cobots): Cobots represent a significant leap forward, designed to work directly alongside human operators. Equipped with safety features to prevent accidents, they are often used for tasks requiring human-robot interaction, such as assisting with assembly or performing quality control checks. They’re not replacing human workers, but rather augmenting their capabilities and improving overall efficiency.
Enhanced Efficiency Through Automation
Robotic automation is revolutionizing manufacturing, dramatically boosting efficiency and reshaping the industry landscape. By replacing or augmenting human labor in repetitive or hazardous tasks, robots are unlocking unprecedented levels of productivity and quality control. This section delves into the specific ways robotic systems enhance efficiency, examining speed improvements, error reduction, and cost-effectiveness.
Robots significantly improve production speed and throughput. Their tireless operation, 24/7 availability, and consistent performance allow for continuous production runs without the interruptions associated with human breaks, shifts, or fatigue. This continuous operation translates directly into increased output, shorter lead times, and faster order fulfillment. For example, in automotive assembly lines, robots perform welding, painting, and part installation with far greater speed and precision than human workers, resulting in a substantial increase in vehicles produced per day. This increased throughput allows manufacturers to meet higher demands and increase market share.
Reduced Human Error and Improved Product Quality
Robotic automation drastically minimizes human error, a major contributor to production inefficiencies and product defects. Robots execute programmed tasks with unwavering precision, eliminating inconsistencies caused by fatigue, distraction, or lack of training. This precision translates directly into improved product quality, reduced waste from defective items, and lower rework costs. Consider the microchip manufacturing industry, where even minor imperfections can render a chip unusable. Robots’ consistent and accurate movements are crucial in ensuring the flawless production of these intricate components. The result is higher yields, less scrap, and ultimately, higher profit margins.
Cost Comparison: Manual Labor vs. Robotic Automation
While the initial investment in robotic automation can be substantial, the long-term operational costs often prove significantly lower than relying solely on manual labor. The following table compares these costs, considering factors like labor wages, maintenance, and training. It’s crucial to remember that these figures are illustrative and vary widely based on specific applications, robot types, and labor costs in a given region.
Process | Manual Labor Cost (per unit) | Robotic Automation Cost (per unit) | Cost Savings (per unit) |
---|---|---|---|
Welding | $15 | $5 | $10 |
Painting | $12 | $4 | $8 |
Assembly | $8 | $3 | $5 |
Note: These figures are simplified examples and do not include factors like initial robot purchase price, software licensing, or potential downtime for maintenance. A comprehensive cost-benefit analysis is necessary for each specific manufacturing application.
Specific Applications of Robotics in Manufacturing
Robotics have moved beyond science fiction and firmly established themselves as crucial tools in modern manufacturing. Their precision, speed, and tireless work ethic are transforming production lines across various industries, leading to significant boosts in efficiency and overall output. This section delves into specific applications and their impact.
The integration of robotics into manufacturing processes offers a multitude of benefits, from increased productivity and improved product quality to enhanced worker safety and reduced operational costs. Let’s examine several key areas where robots are making a real difference.
Robotic Applications in Manufacturing Processes, The Role of Robotics in Enhancing Manufacturing Efficiency
Several manufacturing processes benefit significantly from robotic integration. The advantages are numerous and contribute to a more streamlined, efficient, and profitable operation.
Robots are boosting manufacturing efficiency, optimizing processes from assembly to packaging. But true optimization needs end-to-end visibility, which is where How Blockchain is Reinventing the Concept of Supply Chain Transparency comes in. By tracking materials’ journey, blockchain enhances robotic efficiency by ensuring timely supply and reducing production disruptions, ultimately leading to smarter, more responsive factories.
- Welding: Robots excel at consistent, high-quality welds, especially in complex or repetitive tasks.
- Increased speed and throughput.
- Improved weld quality and consistency.
- Enhanced worker safety by removing humans from hazardous environments.
- Reduced material waste due to precise welding.
- Painting: Robotic painting systems provide even coats, minimizing waste and improving the final finish.
- Consistent paint application, reducing defects.
- Minimized paint waste through precise control.
- Improved worker health and safety by eliminating exposure to harmful chemicals.
- Increased production speed compared to manual painting.
- Assembly: Robots handle intricate assembly tasks with speed and precision, particularly in electronics and automotive manufacturing.
- Increased assembly speed and throughput.
- Improved accuracy and consistency in assembly.
- Reduced human error and associated costs.
- Ability to handle delicate components with care.
- Packaging: Robots automate the packaging process, improving speed, efficiency, and consistency.
- Increased packaging speed and throughput.
- Improved packaging consistency and quality.
- Reduced labor costs associated with manual packaging.
- Enhanced product protection through precise handling.
- Material Handling: Robots efficiently move materials throughout the factory floor, optimizing workflow and reducing bottlenecks.
- Increased efficiency in material movement.
- Reduced labor costs and worker fatigue.
- Improved safety by automating potentially hazardous tasks.
- Optimized workflow and reduced bottlenecks.
Robotics Revolutionizing Industries
The impact of robotics is felt across numerous sectors. Here are some key examples of how robotic automation has dramatically improved efficiency.
Industry | Robotic Application | Efficiency Improvement | Example Company |
---|---|---|---|
Automotive | Welding, painting, assembly | Increased production speed, improved quality control | Tesla, Toyota |
Electronics | Assembly, component placement, testing | Higher precision, reduced defect rates, increased throughput | Foxconn, Samsung |
Pharmaceuticals | Packaging, dispensing, quality control | Improved accuracy, reduced contamination risk, increased production capacity | Pfizer, Novartis |
Food and Beverage | Packaging, palletizing, material handling | Faster processing, reduced waste, improved hygiene | Nestlé, Coca-Cola |
Hypothetical Scenario: Optimizing a Manufacturing Process with Robotics
Consider a small electronics manufacturer struggling with inconsistent soldering quality and slow assembly times. By integrating a robotic soldering system and automated assembly line, they could achieve significant improvements. The robot would perform precise soldering, eliminating inconsistencies and reducing defects. The automated assembly line would speed up the process, allowing for higher production volume and potentially a 20-30% increase in output within six months, assuming appropriate investment and training.
Challenges and Limitations of Robotic Implementation
Integrating robots into manufacturing isn’t a simple plug-and-play operation. It requires careful planning and consideration of several significant hurdles, impacting both the initial investment and long-term operational efficiency. Successfully navigating these challenges is crucial for reaping the full benefits of robotic automation.
High upfront costs and ongoing maintenance are major barriers. Robots themselves are expensive, and their implementation demands specialized infrastructure, including programming, integration, and safety systems. This can be particularly daunting for smaller businesses with limited capital. Furthermore, ongoing maintenance, repairs, and software updates add to the total cost of ownership, requiring a robust budget allocation.
High Initial Investment Costs and Return on Investment (ROI)
The substantial financial commitment required for robotic implementation is a significant deterrent. Purchasing robots, integrating them into existing systems, and training personnel all represent considerable expenses. A thorough cost-benefit analysis is essential to determine the viability of robotic integration, projecting the ROI based on anticipated efficiency gains and reduced labor costs. For example, a small manufacturing company might find the initial investment in a robotic welding system prohibitive, while a larger company with higher production volumes could see a quicker return on investment. Careful planning and securing appropriate financing are key factors in mitigating this challenge.
Workforce Retraining and Reskilling Needs
Introducing robots often necessitates retraining or reskilling the existing workforce. Employees accustomed to manual tasks might need to learn to operate, maintain, and program robotic systems. This requires investment in training programs and potentially necessitates adapting job roles and responsibilities. Failing to address this aspect can lead to resistance from employees and decreased morale. Successful implementation involves proactive retraining initiatives, ensuring employees feel valued and empowered in the new automated environment. For instance, a factory introducing automated packaging robots might offer its existing workers training to become robot technicians or programmers, thus leveraging their existing experience and skills.
Safety Concerns and Risk Mitigation
Safety is paramount when working with robots. Industrial robots operate with significant power and speed, posing potential risks to human workers if safety protocols are not meticulously followed. Implementing robust safety measures, such as safety cages, light curtains, and emergency stop mechanisms, is crucial. Furthermore, ongoing safety training and adherence to strict operational procedures are essential to minimize risks. Regular safety audits and inspections can help identify and address potential hazards proactively. For example, a company implementing collaborative robots (cobots) might prioritize training programs focusing on safe human-robot interaction, ensuring employees understand the robot’s capabilities and limitations.
Limitations of Current Robotic Technology
Despite significant advancements, current robotic technology has limitations. Many robots lack the dexterity and adaptability of human workers, making them unsuitable for tasks requiring fine motor skills or significant variations in the work environment. Furthermore, integrating advanced AI capabilities into robots remains a challenge, limiting their ability to handle unexpected situations or learn from experience. This necessitates careful task selection, focusing on repetitive and predictable operations where robots excel. Ongoing research and development are focusing on improving robot dexterity, adaptability, and AI integration, promising to overcome these limitations in the future. For example, advancements in soft robotics and AI-powered vision systems are steadily expanding the range of tasks robots can perform effectively.
The Future of Robotics in Manufacturing
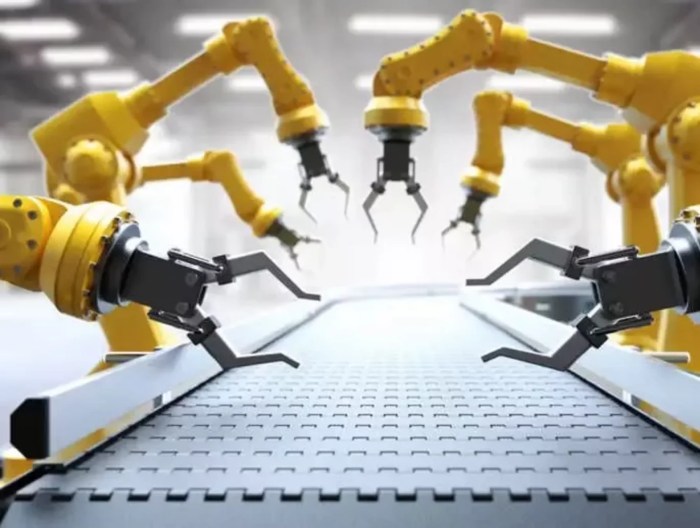
Source: bizclikmedia.net
The manufacturing landscape is poised for a dramatic transformation, driven by relentless advancements in robotics and related technologies. We’re moving beyond simple automation towards a future where robots are intelligent, adaptable, and deeply integrated into every stage of the production process, leading to unprecedented levels of efficiency and productivity. This evolution will reshape not only how goods are made but also the very nature of work in the manufacturing sector.
The convergence of robotics with artificial intelligence (AI) and machine learning (ML) is the key driver of this transformation. This synergy allows robots to learn from experience, adapt to changing conditions, and make decisions autonomously, moving beyond pre-programmed tasks. This means robots will become more versatile, capable of handling a wider range of tasks with greater precision and speed. Imagine a factory where robots not only assemble products but also predict and prevent malfunctions, optimize production lines in real-time, and even design and improve their own processes.
AI and Machine Learning Enhancements
AI and ML will empower robots with capabilities previously considered the realm of science fiction. For example, computer vision systems, powered by AI, will allow robots to “see” and interpret their environment with unprecedented accuracy, enabling them to handle complex tasks involving visual inspection, quality control, and even customized product assembly. Similarly, ML algorithms will enable robots to learn from vast datasets of production data, identifying patterns and anomalies to optimize processes, predict equipment failures, and minimize downtime. Companies like Tesla are already leveraging AI-powered robots in their manufacturing processes, demonstrating the real-world application of this technology. Their robots can adapt to variations in parts and adjust their actions accordingly, increasing production speed and reducing errors.
The Impact of Robotics on the Future of Work
The increasing integration of robots in manufacturing will undoubtedly reshape the workforce. While there are concerns about job displacement, the reality is likely more nuanced. Many believe that robots will primarily take over repetitive, dangerous, or physically demanding tasks, freeing human workers to focus on more complex, creative, and strategic roles. This shift will require reskilling and upskilling initiatives to equip workers with the skills needed to manage and collaborate with robots. Examples include roles in robotics maintenance, programming, and data analysis, creating new opportunities within the manufacturing sector. The focus will shift from manual labor to human-robot collaboration, leveraging the strengths of both to achieve optimal efficiency and productivity. A study by the World Economic Forum predicts that while some jobs will be lost, the net effect will be job creation in new and emerging areas related to robotics and automation. This transition will require investment in education and training to ensure a smooth and equitable shift in the manufacturing workforce.
Case Studies
Real-world applications are the ultimate test of any technology’s worth. The following case studies demonstrate how robotic integration has significantly boosted manufacturing efficiency across diverse industries, offering compelling evidence of the transformative potential of automation. These examples highlight not just the increased output, but also the improvements in quality, safety, and overall operational efficiency.
Fanuc Robotics in Automotive Manufacturing
Fanuc, a leading robotics company, has been instrumental in revolutionizing automotive manufacturing. Their robots are extensively used in various processes, from welding and painting to assembly and material handling. One notable example involves a major automaker that implemented Fanuc robots in its assembly line. The result was a substantial reduction in production time, improved precision in welding, and a significant decrease in defects.
The key elements contributing to this success include:
- High-precision robots: Fanuc’s robots are renowned for their accuracy and repeatability, leading to fewer errors and higher quality products.
- Integrated automation systems: The seamless integration of robots with existing manufacturing systems optimized workflow and minimized downtime.
- Data-driven optimization: Continuous monitoring and data analysis allowed for fine-tuning of robotic processes, leading to ongoing efficiency improvements.
- Skilled workforce integration: The company invested in training its workforce to effectively operate and maintain the robotic systems.
Amazon’s Robotic Fulfillment Centers
Amazon’s extensive use of robotics in its fulfillment centers is a prime example of how automation can dramatically enhance efficiency in logistics and warehousing. The implementation of Kiva robots (now Amazon Robotics) has revolutionized order fulfillment, enabling faster picking, packing, and shipping of products. The sheer scale of Amazon’s operations makes the impact of this robotic integration particularly significant.
Key success factors in this case include:
- Automated material handling: Kiva robots efficiently transport shelves of goods to human workers, minimizing travel time and improving picking speed.
- Scalability and flexibility: The robotic system can easily adapt to changing order volumes and product assortments.
- Improved worker safety: Robots handle heavy lifting and repetitive tasks, reducing the risk of workplace injuries for human employees.
- Enhanced accuracy and speed: Robotic automation minimizes errors in order picking and packing, resulting in faster delivery times.
Yaskawa Motoman Robots in Electronics Manufacturing
Yaskawa Motoman robots are widely used in the electronics industry for tasks such as circuit board assembly, component placement, and testing. One notable example involves a company that implemented Yaskawa Motoman robots in its smartphone assembly line. This resulted in a significant increase in production throughput, improved product quality, and reduced labor costs. The precision and speed of these robots are particularly advantageous in the intricate assembly processes of electronics manufacturing.
The key elements of their success are:
- High-speed and precision movements: Yaskawa Motoman robots offer exceptional speed and precision, crucial for handling delicate electronic components.
- Flexible programming and adaptability: The robots can be easily reprogrammed to handle different products and assembly processes.
- Vision systems integration: The incorporation of advanced vision systems enables the robots to identify and handle components with high accuracy.
- Reduced human error: Automation minimizes the risk of human error in assembly, leading to improved product quality and yield.
Summary
The integration of robotics in manufacturing isn’t just about faster production; it’s a strategic move towards smarter, more resilient, and ultimately, more profitable operations. While challenges like initial investment and workforce retraining exist, the potential rewards – increased output, improved quality, and reduced operational costs – far outweigh the hurdles. As AI and machine learning continue to refine robotic capabilities, the future of manufacturing promises an even more seamless and efficient synergy between human ingenuity and robotic precision. The age of the automated factory is here, and it’s only getting more exciting.