The Role of Robotics in Enhancing Automation in Retail is rapidly changing the face of the industry. Forget slow-moving checkouts and manual stock counting – robots are streamlining operations, boosting efficiency, and creating a smoother shopping experience. From collaborative robots assisting human workers to autonomous mobile robots zipping around warehouses, the integration of robotics is proving to be a game-changer. This exploration delves into the various applications, challenges, and future trends shaping the retail landscape through automation.
We’ll examine how robots are revolutionizing inventory management, enhancing customer service, and even improving store security. We’ll also tackle the inevitable concerns: job displacement, the cost of implementation, and the ethical considerations surrounding increased automation. But don’t worry, we’ll balance the potential downsides with real-world examples of successful robotic integration and the incredible ROI these systems can offer.
Introduction to Robotics in Retail Automation
The retail landscape is undergoing a dramatic transformation, fueled by the increasing adoption of automation technologies. Robotics, once a futuristic concept, is rapidly becoming a key player in enhancing efficiency, productivity, and the overall customer experience within retail operations. From large-scale warehouse automation to in-store customer assistance, robots are proving their worth in a variety of applications.
Robotics offers significant advantages to retailers seeking to optimize their operations and compete in a rapidly evolving market. These benefits translate to substantial cost savings, improved accuracy, increased efficiency, and a better shopping experience for customers. By automating repetitive and labor-intensive tasks, retailers can free up human employees to focus on more complex and customer-facing roles.
Types of Robots Used in Retail Automation
Several types of robots are revolutionizing retail operations. Collaborative robots (cobots), designed to work alongside human employees, are increasingly common in tasks like order fulfillment and inventory management. Autonomous mobile robots (AMRs), on the other hand, navigate warehouse and store environments independently, performing tasks such as transporting goods, scanning shelves, and delivering items to customers. Other robotic systems include automated guided vehicles (AGVs) following pre-programmed paths and robotic arms used for precise tasks such as picking and packing. These varied applications cater to diverse needs within the retail ecosystem, enhancing various aspects of the supply chain and in-store experience.
Comparison of Robotic Systems in Retail
The choice of robotic system depends heavily on the specific needs and operational context of the retailer. The following table compares the capabilities and limitations of different robotic systems commonly used in retail:
Robotic System | Capabilities | Limitations | Retail Applications |
---|---|---|---|
Collaborative Robots (Cobots) | Precise manipulation, adaptable to various tasks, safe interaction with humans | Limited payload capacity, requires programming and integration, relatively high initial cost | Assembly, packaging, quality control, customer service |
Autonomous Mobile Robots (AMRs) | Independent navigation, flexible routing, efficient material handling | Potential for collisions, requires sophisticated software and infrastructure, susceptible to environmental changes | Inventory management, order fulfillment, delivery, shelf scanning |
Automated Guided Vehicles (AGVs) | Reliable and consistent movement along pre-programmed paths, high payload capacity | Inflexible routing, requires fixed infrastructure, limited adaptability to changing environments | Warehouse transportation, material handling in large spaces |
Robotic Arms | High precision and speed, capable of handling delicate items | Limited mobility, requires fixed installation, susceptible to errors in programming | Picking and packing, quality inspection, automated assembly |
Specific Applications of Robotics in Retail
The integration of robotics into retail operations is no longer a futuristic fantasy; it’s rapidly becoming the new normal. From streamlining inventory management to enhancing customer experiences and bolstering security, robots are proving their worth across various retail functions, boosting efficiency and profitability. This section delves into the specific applications transforming the retail landscape.
Robotics in Inventory Management
Efficient inventory management is crucial for retail success. Robots are significantly improving this process, reducing costs and minimizing errors. Automated systems handle tasks previously reliant on manual labor, freeing up human employees for more strategic roles.
For example, automated guided vehicles (AGVs) navigate warehouse aisles, autonomously transporting goods from storage to packing stations. These robots use sensors and navigation systems to avoid obstacles and optimize their routes. Simultaneously, robotic arms perform picking and packing tasks with speed and precision, accurately selecting items and packaging them for shipment. This automation dramatically accelerates order fulfillment, improving delivery times and customer satisfaction. Another application involves automated stock replenishment systems, where robots monitor shelf levels and automatically restock items from storage, ensuring shelves are always fully stocked and minimizing the risk of stockouts.
Robotics in Customer Service
Robots are increasingly interacting directly with customers, enhancing their shopping experience and streamlining transactions. This isn’t about replacing human interaction entirely, but rather augmenting it to create a more efficient and enjoyable shopping environment.
Automated checkout systems, such as self-checkout kiosks, allow customers to scan and bag their own groceries, reducing wait times at traditional checkout counters. These systems are often equipped with advanced features like object recognition and weight sensors to prevent theft and ensure accurate billing. Interactive kiosks provide customers with information about products, store layouts, and promotions. These kiosks can answer frequently asked questions, assist with product comparisons, and even offer personalized recommendations based on customer preferences. In some high-end retail settings, robotic assistants are even employed to provide personalized guidance and assistance to shoppers on the shop floor.
Robots are revolutionizing retail, from automated checkout to inventory management. This efficiency boost isn’t just about speed; it’s about freeing up human employees for more engaging tasks. Think about how this same principle applies to personal assistance, as explored in this insightful article: How Robotics is Improving the Future of Personal Assistance. Ultimately, the increased efficiency gained through robotics in both retail and personal assistance leads to a better customer experience and a more productive workforce.
Robotics in Store Security and Safety
Beyond inventory and customer service, robots are contributing to a safer and more secure retail environment. These robotic solutions are proactive in identifying and mitigating potential risks.
Security robots patrol store aisles and parking lots, monitoring for suspicious activity and deterring theft. Equipped with cameras and sensors, these robots can detect unusual behavior, such as loitering or unauthorized access, and alert security personnel immediately. Moreover, robots can assist in maintaining a safe environment by identifying and reporting potential hazards, such as spills or obstructions, reducing the risk of accidents and injuries for both staff and customers. This proactive approach minimizes risks and ensures a secure shopping experience.
Workflow Diagram: Robot Integration in a Retail Store
Imagine a diagram depicting a typical retail store workflow. The diagram would show the flow of goods from receiving to shelving, highlighting the integration of robots at various stages. For instance, AGVs would be shown transporting incoming inventory from the receiving dock to the warehouse. Robotic arms would be depicted in the warehouse, picking and packing orders. Automated shelving systems would be shown replenishing stock on shelves. Self-checkout kiosks would be positioned near the exits, and security robots would be patrolling the store perimeter and aisles. The diagram would visually represent how robots seamlessly integrate with existing systems and human staff, creating a more efficient and secure retail operation. This visualization would clearly illustrate the streamlined and optimized workflow achieved through robotic integration.
Challenges and Considerations in Robotic Implementation
Rolling out robots in retail isn’t just about slapping down some shiny new tech; it’s a complex undertaking with potential pitfalls that need careful navigation. From hefty upfront costs to the anxieties surrounding job displacement, retailers need a strategic approach to ensure successful robotic integration. This section delves into the key challenges and offers practical solutions for a smoother transition.
The reality is, robotic implementation in retail isn’t a simple plug-and-play operation. Several factors need careful consideration to avoid costly mistakes and ensure a positive return on investment. This includes not only the technical aspects but also the human element, which is crucial for successful integration and long-term sustainability.
Financial Investment and Return on Investment, The Role of Robotics in Enhancing Automation in Retail
Implementing robotic systems demands significant upfront capital expenditure. This includes the purchase price of the robots themselves, specialized software, integration with existing systems, and ongoing maintenance. The cost can vary drastically depending on the type of robot, its capabilities, and the scale of deployment. For example, a single automated checkout system might cost tens of thousands of dollars, while a fleet of shelf-scanning robots could run into the hundreds of thousands. Comparing this to traditional methods, such as manual stocktaking or human cashiers, reveals a complex picture. While initial costs are higher for robotic systems, potential long-term savings from increased efficiency, reduced labor costs, and minimized human error can lead to a positive ROI over time. However, a thorough cost-benefit analysis, factoring in all associated expenses and potential revenue gains, is crucial before committing to such investments. A successful ROI hinges on careful planning and a clear understanding of the specific needs and operational context of the retail environment.
Integration with Existing Systems and Infrastructure
Seamless integration with existing IT infrastructure is paramount. Robots aren’t standalone units; they need to communicate effectively with inventory management systems, point-of-sale systems, and other crucial retail technologies. A poorly integrated system can lead to data inconsistencies, operational inefficiencies, and even system crashes, negating the benefits of automation. This necessitates significant upfront planning and potentially substantial modifications to existing systems. For instance, integrating a robotic inventory management system with an outdated point-of-sale system might require costly upgrades or even complete replacements, adding unexpected expenses to the project. Moreover, the physical infrastructure must also be adapted to accommodate robotic systems. This could involve modifications to store layouts, the installation of charging stations, and the implementation of safety protocols to prevent accidents.
Maintenance and Support
Robotic systems require regular maintenance and technical support. Malfunctions can lead to downtime, operational disruptions, and increased costs. Retailers need to factor in the cost of maintenance contracts, spare parts, and skilled technicians capable of handling repairs. A proactive maintenance strategy, including regular inspections and preventative measures, is crucial for minimizing downtime and maximizing the lifespan of the robotic systems. For example, a retailer deploying a fleet of autonomous mobile robots (AMRs) for delivery needs to have a dedicated team or contract with a specialized service provider for maintenance and repair, including the availability of replacement parts. Failure to account for these ongoing costs can significantly impact the overall ROI.
Addressing Job Displacement Concerns
The introduction of robots into retail inevitably raises concerns about job displacement. While some tasks will undoubtedly be automated, this doesn’t necessarily translate to widespread job losses. Instead, the focus should shift towards reskilling and upskilling the workforce to manage and maintain these new technologies. This could involve training employees in robotics maintenance, data analysis, or customer service roles that require a more human touch. Furthermore, the adoption of robots can create new job opportunities in areas such as robotics engineering, software development, and data science. Amazon, for instance, has invested heavily in robotics but has also expanded its workforce to manage and support its automated systems. This proactive approach to workforce adaptation is crucial for mitigating negative impacts and fostering a positive perception of automation.
Future Trends and Developments
The retail landscape is undergoing a rapid transformation, driven largely by advancements in robotics and artificial intelligence. We’re moving beyond simple automated tasks to a future where robots play increasingly sophisticated roles, impacting everything from customer experience to supply chain management. This evolution presents exciting opportunities but also necessitates careful consideration of ethical implications and potential societal shifts.
The integration of AI and robotics is poised to revolutionize retail operations. We’re seeing a move towards more autonomous systems capable of learning and adapting to changing environments, leading to more efficient and personalized shopping experiences. This includes robots that can not only handle inventory but also engage directly with customers, providing assistance and information. For instance, imagine a robot capable of understanding complex customer queries, guiding them to specific products, and even processing transactions autonomously.
AI-Powered Robots and Swarm Robotics
AI is no longer a futuristic concept; it’s actively shaping the capabilities of retail robots. Robots equipped with advanced AI algorithms can analyze vast amounts of data to optimize tasks, predict customer behavior, and personalize interactions. This leads to improved inventory management, reduced labor costs, and enhanced customer satisfaction. Furthermore, the emergence of swarm robotics – where multiple robots collaborate on complex tasks – promises to significantly improve efficiency and scalability in warehousing and distribution centers. Imagine a coordinated team of robots collaboratively sorting, packing, and transporting goods, working in perfect harmony to optimize the entire process. This collaborative approach will drastically improve efficiency compared to individual robot operation.
Impact of Advanced Robotics on the Future of Retail
Advanced robotics will fundamentally reshape the retail experience. Expect to see a significant increase in automation across all aspects of the retail supply chain, from automated warehouses to in-store robots assisting customers. This will lead to more efficient operations, reduced costs, and potentially even the creation of new retail models. For example, Amazon’s use of robots in its fulfillment centers has already demonstrated the potential for increased speed and efficiency in order fulfillment. This level of automation is likely to become the standard across the industry. The focus will shift towards creating seamless, personalized shopping experiences, both online and in-store, driven by intelligent robotic systems.
Ethical Considerations of Increasing Robot Use in Retail
The increasing use of robots in retail raises several ethical considerations. Job displacement is a major concern, requiring proactive measures to reskill and upskill the workforce. Data privacy is another critical issue, as robots collect vast amounts of customer data. Ensuring responsible data handling and transparent data usage policies is paramount. Furthermore, algorithmic bias in AI-powered robots could lead to unfair or discriminatory practices. Robust testing and continuous monitoring are crucial to mitigate such risks. Finally, the potential for increased social isolation due to reduced human interaction in retail settings needs to be carefully considered. Striking a balance between automation and human interaction will be crucial to maintaining a positive customer experience.
Potential Advancements in Robotic Technology for Enhanced Retail Automation
The future of retail robotics holds immense potential. Several advancements could further enhance automation:
- Improved Navigation and Mapping: More sophisticated navigation systems enabling robots to operate effectively in complex and dynamic environments, including crowded retail spaces.
- Enhanced Object Recognition and Manipulation: Robots capable of accurately identifying and handling a wider range of products with greater dexterity.
- Advanced Human-Robot Interaction: More intuitive and natural interactions between robots and humans, enabling seamless collaboration and assistance.
- Increased Robot Autonomy: Robots capable of performing more complex tasks independently, minimizing the need for human intervention.
- Cloud-Based Robotics: Utilizing cloud computing to enable remote monitoring, control, and data analysis of robotic systems, leading to improved efficiency and scalability.
Case Studies of Successful Robotic Implementations: The Role Of Robotics In Enhancing Automation In Retail
The integration of robotics into retail operations is no longer a futuristic fantasy; it’s a tangible reality transforming efficiency and customer experience. Several retailers have successfully implemented robotic systems, achieving significant improvements in various key performance indicators. Examining these case studies reveals valuable insights into best practices and potential pitfalls.
Amazon Robotics in Fulfillment Centers
Amazon, a pioneer in retail automation, has extensively utilized robotics in its fulfillment centers. Their Kiva robots (now Amazon Robotics), for example, are autonomous mobile robots that transport shelves of products to human workers, drastically reducing the time and distance employees need to travel to retrieve items. This system optimizes picking processes, significantly speeding up order fulfillment. The impact is measurable: Amazon reports significant increases in order fulfillment speed and a reduction in operational costs, although precise figures aren’t publicly released for competitive reasons. The key to Amazon’s success lies in integrating robotics seamlessly into its existing infrastructure and workflows, rather than attempting a complete overhaul.
Walmart’s Automated Grocery Sorting System
Walmart, facing the challenge of efficiently handling the increasing volume of online grocery orders, has implemented automated sorting systems in its distribution centers. These systems employ a combination of conveyor belts, robotic arms, and sophisticated software to quickly and accurately sort groceries based on order details. This automated process minimizes human error, increases throughput, and enhances order accuracy. While specific KPIs like percentage improvement in order accuracy or reduction in fulfillment time aren’t consistently released by Walmart, industry analysts cite significant gains in efficiency compared to manual sorting processes, contributing to the retailer’s ability to compete effectively in the rapidly growing online grocery market. Walmart’s approach demonstrates the power of targeted automation, focusing on specific bottlenecks in the supply chain.
Ocado’s Automated Warehouse
Ocado, a British online grocery retailer, has built a highly automated warehouse utilizing a complex network of robots and automated systems. Their system involves robots that retrieve items from storage, transport them to packing stations, and manage inventory. This sophisticated approach results in extremely high throughput and efficiency. Ocado publicly boasts significant improvements in order fulfillment speed and reduced operational costs, although exact figures are often kept confidential. However, industry reports suggest that Ocado’s automation has enabled them to handle a significantly higher volume of orders with fewer human workers, resulting in substantial cost savings and a competitive advantage. Ocado’s case highlights the potential for fully automated warehouses, although the significant upfront investment required presents a considerable barrier to entry for smaller retailers.
Summary of Key Lessons Learned
Retailer | Robotic Application | Key KPI Improvement | Key Lesson Learned |
---|---|---|---|
Amazon | Autonomous Mobile Robots (Kiva) | Increased order fulfillment speed, reduced operational costs | Seamless integration with existing workflows is crucial. |
Walmart | Automated Grocery Sorting System | Improved order accuracy, increased throughput | Targeted automation addressing specific bottlenecks is effective. |
Ocado | Fully automated warehouse | High throughput, reduced operational costs | Significant upfront investment is required, but potential returns are high. |
Visual Representation of Robotic Integration
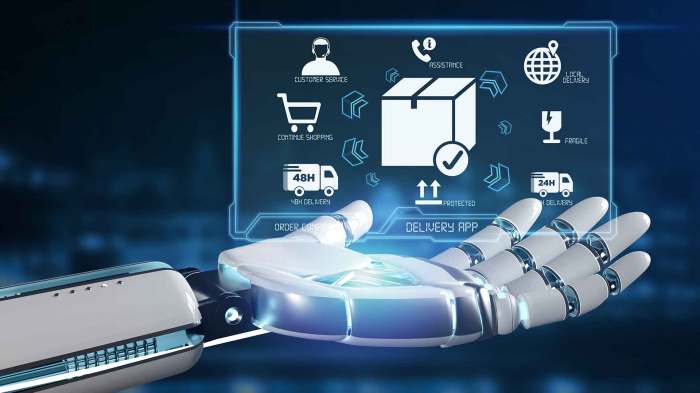
Source: brainvire.com
Visualizing the integration of robotics in retail requires understanding not just the technology, but also the human experience and the overall operational flow. This section provides detailed scenarios and descriptions to illustrate the practical application of robots in various retail settings.
A customer approaches a sleek, white kiosk in a bustling electronics store. Soft blue LED lights pulse gently around the touchscreen interface. The air hums quietly with the low thrum of the internal mechanisms. A friendly, synthesized voice greets the customer, “Hello! How can I assist you today?” The customer asks about a specific smartphone model. The robot smoothly rotates its display, showcasing the phone from various angles. High-resolution images and videos appear on the screen, accompanied by detailed specifications read aloud by the robot in a clear, concise tone. The customer can even interact with the robot using natural language, asking clarifying questions or requesting comparisons to other models. The entire interaction is smooth, efficient, and surprisingly engaging, blending seamlessly into the shopping experience. The faint scent of ozone from the robot’s internal components is barely noticeable amidst the usual retail aromas.
Internal Mechanisms of a Retail Kiosk Robot
This retail kiosk robot utilizes a sophisticated system of interconnected components. At its core is a powerful computer system running advanced AI algorithms for natural language processing, image recognition, and data retrieval. This system is linked to the store’s inventory management system, allowing the robot to provide accurate and up-to-date information. A high-resolution touchscreen serves as the primary interface, while multiple cameras provide visual input for object recognition and customer interaction tracking. Internal motors control the robot’s movements, allowing it to smoothly rotate its display and adjust its position. Sensors detect the proximity of customers and other obstacles, ensuring safe and efficient operation. Finally, a network connection enables seamless communication with the store’s central systems and cloud-based resources. The entire system is housed within a sleek, user-friendly casing designed to blend seamlessly into the store environment.
Automated Guided Vehicles (AGVs) in a Warehouse
Imagine a large, brightly lit warehouse, the air filled with the quiet hum of machinery. Rows upon rows of towering shelves stretch into the distance, stocked with various retail goods. Navigating this complex landscape are several AGVs, resembling small, autonomous forklifts. These AGVs are equipped with sophisticated sensors, including lidar and cameras, which allow them to precisely map their environment and navigate autonomously along pre-programmed routes. Each AGV carries a designated load of inventory, transporting it efficiently between storage locations, packing stations, and shipping docks. The warehouse floor is marked with clear visual indicators, such as magnetic strips or QR codes, which guide the AGVs along their designated paths. Supervisory personnel monitor the AGV fleet remotely via a central control system, which provides real-time tracking and status updates. The overall workflow is optimized for speed and efficiency, minimizing human intervention while ensuring the accurate and timely movement of inventory throughout the warehouse. The AGVs move silently and efficiently, their orange safety lights blinking rhythmically as they navigate the warehouse, a ballet of automated logistics. The entire scene is one of controlled precision and efficient movement, a stark contrast to the often chaotic nature of traditional warehouse operations.
Conclusion
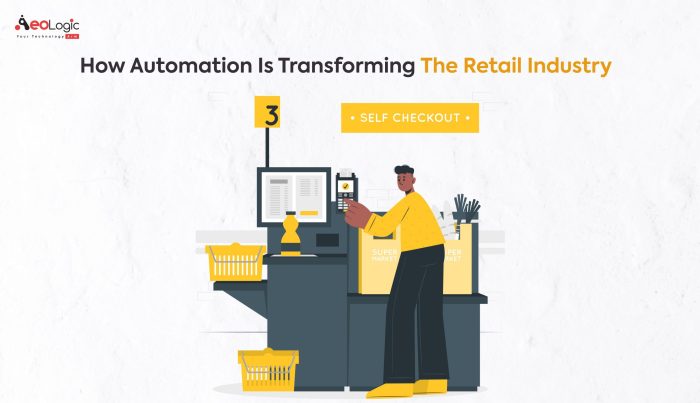
Source: aeologic.com
Ultimately, the role of robotics in enhancing automation in retail isn’t just about replacing human workers; it’s about creating a more efficient, safer, and ultimately, more enjoyable shopping experience. While challenges remain, the potential benefits – from increased productivity and reduced costs to improved customer service and enhanced safety – are undeniable. As technology continues to advance, we can expect even more sophisticated and integrated robotic systems to transform the retail industry in the years to come. The future of retail is automated, and it’s looking pretty robotic.