The Role of Robotics in Disaster Recovery and Emergency Services is exploding. Forget cheesy robot movies; this is real-life stuff. We’re talking about drones zipping through rubble, robotic arms defusing bombs, and AI analyzing damage faster than a caffeinated squirrel. It’s a game-changer, and this deep dive explores how these metal marvels are saving lives and reshaping disaster response.
From earthquake-ravaged cities to chemical spills, robots are stepping up. This isn’t just about cool tech; it’s about efficiency, safety, and ultimately, giving hope where it’s needed most. We’ll unpack the different types of robots involved, the challenges they face, and the incredible potential for the future – think self-healing robots and AI-powered prediction. Buckle up, it’s going to be a fascinating ride.
Types of Robots in Disaster Response

Source: searchandrescuerobots.com
Disaster recovery and emergency services are increasingly reliant on robots to perform tasks too dangerous or difficult for humans. These robotic systems offer a crucial advantage in saving lives and mitigating damage during crises, ranging from earthquakes and floods to hazardous material spills. The diversity of robots deployed reflects the multifaceted nature of disaster scenarios.
Various types of robots, each with unique capabilities, are employed in disaster response. Their functionalities are tailored to specific needs, ranging from search and rescue to environmental monitoring and debris removal. The choice of robot depends heavily on the specific nature of the disaster and the tasks required.
Types of Robots and Their Applications
Robot Type | Functionality | Strengths | Weaknesses |
---|---|---|---|
Aerial Robots (Drones) | Search and rescue, aerial surveillance, damage assessment, communication relay | Wide area coverage, rapid deployment, relatively low cost, ability to access inaccessible areas | Susceptible to weather conditions, limited payload capacity, range limitations, potential for signal interference |
Ground Robots | Hazardous environment exploration, debris removal, search and rescue in confined spaces, bomb disposal | Robust construction, ability to navigate rough terrain, can carry heavy payloads, can operate in hazardous environments | Limited mobility in highly cluttered environments, susceptible to damage, relatively slow speed, operational range limitations |
Aquatic Robots (AUVs/ROVs) | Underwater search and rescue, underwater inspection, mapping submerged structures, environmental monitoring | Ability to operate in submerged environments, can access areas inaccessible to humans, can carry specialized sensors | Limited operational depth, susceptible to damage from underwater debris, communication challenges in deep water, high cost |
Humanoid Robots | Search and rescue in complex environments, manipulation of objects in hazardous areas, interaction with survivors | Dexterous manipulation capabilities, ability to navigate complex environments, potential for human-robot interaction | High cost, complex control systems, limited robustness, susceptibility to damage |
Aerial Robots in Search and Rescue
Aerial robots, commonly known as drones, have revolutionized search and rescue operations. Their ability to quickly cover large areas, access difficult terrain, and provide real-time visual information is invaluable. For example, drones equipped with thermal imaging cameras can locate survivors trapped under debris by detecting their body heat, even in low-light conditions. During the 2011 Tohoku earthquake and tsunami in Japan, drones were used to assess the extent of damage and locate survivors in areas inaccessible by ground vehicles. Similarly, in the aftermath of Hurricane Katrina, drones were deployed to map flooded areas and assess infrastructure damage, providing crucial information for rescue and recovery efforts.
Ground Robots in Hazardous Environment Exploration
Ground robots are essential for exploring hazardous environments, such as collapsed buildings or areas contaminated with hazardous materials. Their robust construction allows them to navigate challenging terrain and withstand harsh conditions. For instance, during the Fukushima Daiichi nuclear disaster, robots were used to inspect the damaged reactors and assess the radiation levels, providing critical data for cleanup and recovery efforts. In situations involving bomb disposal, specialized ground robots allow technicians to safely disarm explosive devices from a safe distance, minimizing risk to human life. The use of ground robots equipped with manipulators allows for the remote handling of hazardous materials, preventing exposure and injury to human personnel. Examples include the PackBot, used extensively by the military and emergency services, and the ANYmal robot, known for its robust locomotion capabilities in challenging environments.
Robotics in Search and Rescue: The Role Of Robotics In Disaster Recovery And Emergency Services
Robots are increasingly vital in search and rescue operations, offering a crucial advantage in hazardous environments where human access is limited or dangerous. However, deploying these technological marvels isn’t without its hurdles. The complex interplay of technology, ethics, and the unpredictable nature of disaster zones presents unique challenges that demand careful consideration.
The challenges robots face in search and rescue missions are multifaceted. Navigating rubble-strewn landscapes, for example, requires robots with robust locomotion systems capable of traversing uneven terrain, climbing stairs, and squeezing through narrow openings. This often involves sophisticated AI algorithms for path planning and obstacle avoidance, which can be computationally intensive and prone to errors in unpredictable environments. Furthermore, maintaining reliable communication in disaster zones is often difficult. Damaged infrastructure can disrupt signal transmission, leaving robots isolated and unable to relay crucial information to rescue teams. Power limitations also pose a significant constraint, particularly in prolonged operations where battery life becomes a critical factor.
Challenges in Robotics for Search and Rescue
Terrain navigation and communication are major obstacles. Robots need advanced sensors (like lidar and cameras) and AI to map and navigate complex, unstable environments. Maintaining consistent communication links, especially in areas with damaged infrastructure, requires robust and adaptable communication systems. This might involve multiple communication channels or the use of relay robots to extend the range. Finally, robots must be durable enough to withstand the harsh conditions often found in disaster areas, including dust, debris, and extreme temperatures.
Ethical Considerations in Using Robots for Search and Rescue
The use of robots in search and rescue raises ethical questions. One key concern is algorithmic bias. The AI algorithms guiding these robots are trained on data, and if that data reflects existing societal biases, the robots’ actions might inadvertently discriminate against certain groups. For instance, a robot trained primarily on images of adult males might be less effective at identifying children or elderly individuals. Furthermore, there are limitations to what robots can currently do. They cannot independently assess complex situations or make nuanced judgments that require human empathy and experience. Therefore, relying solely on robots might delay or hinder rescue efforts if their capabilities are misunderstood or overestimated. The decision-making process regarding robot deployment and the balance between robotic assistance and human intervention needs careful ethical consideration.
Hypothetical Earthquake Scenario and Robot Deployment
Imagine a devastating earthquake strikes a densely populated city. Buildings have collapsed, trapping survivors beneath tons of rubble. A team of specialized robots is deployed. First, a fleet of small, agile robots equipped with cameras and microphones are sent into the affected areas to quickly survey the damage and locate potential survivors. These robots use advanced image recognition to identify signs of life, such as movement or sounds, and relay their findings to the central command center. Larger, more robust robots, capable of lifting heavy debris, are then deployed to clear pathways and access survivors trapped in collapsed structures. These robots are remotely controlled by human operators who guide their actions, ensuring that the robots’ interventions are safe and effective. Finally, smaller robots equipped with medical sensors are deployed to assess the condition of survivors and provide preliminary medical assistance until human rescuers can reach them. The robots’ swift action significantly reduces response time and improves the chances of survival for trapped individuals. Their objective data collection and ability to reach inaccessible areas prove instrumental in coordinating the rescue effort and saving lives.
Robotics in Hazardous Material Handling

Source: b-cdn.net
Disaster response often involves dealing with hazardous materials, posing significant risks to human life. Robots offer a crucial solution, enabling safe and efficient handling of these materials, minimizing human exposure and maximizing the effectiveness of cleanup operations. Their deployment is particularly vital in situations where the risks are too high for human intervention.
The use of robots in hazardous material handling is driven by the need to protect human responders while ensuring swift and effective remediation. Various robotic systems are designed to handle different types of hazardous materials, each with specific capabilities and safety features. These features, such as remote operation, specialized sensors, and robust construction, allow robots to operate in environments that are far too dangerous for human workers.
From navigating rubble in earthquake zones to defusing bombs, robots are proving invaluable in disaster recovery. This same robotic precision and adaptability are also revolutionizing other sectors, like manufacturing, as seen in this insightful article on The Role of Robotics in Revolutionizing Manufacturing Automation. The advancements driving efficiency in factories are directly applicable to enhancing the capabilities of robots used in search and rescue operations, leading to faster and safer responses to emergencies.
Types of Robots Used in Hazardous Material Handling
A range of robots are employed in hazardous material handling, each tailored to specific tasks and hazards. These include remotely operated vehicles (ROVs) for underwater operations, unmanned aerial vehicles (UAVs) for aerial surveillance and sample collection, and robotic arms for manipulation and neutralization of hazardous substances. These robots often incorporate features such as radiation shielding, chemical-resistant materials, and redundant systems to ensure reliable operation even in harsh conditions. For example, PackBot, a tracked robot developed by iRobot, has been used extensively in various hazardous environments, including nuclear disasters, demonstrating its versatility and robustness.
Comparing Robotic Approaches for Chemical Spills and Nuclear Leaks
The robotic approaches to chemical spills and nuclear leaks differ significantly due to the nature of the hazards involved. Chemical spills often require robots equipped with sensors to identify the specific chemical, followed by specialized tools for containment and neutralization. These robots might use manipulators to plug leaks, deploy absorbent materials, or spray neutralizing agents. In contrast, nuclear leaks necessitate robots with robust radiation shielding, allowing them to operate in high-radiation environments for extended periods. These robots are often equipped with radiation detectors to map contamination levels and manipulators to handle radioactive materials safely. The design considerations, including materials, shielding, and sensor types, are fundamentally different in these two scenarios.
Step-by-Step Procedure for Neutralizing a Simulated Hazardous Material Spill Using a Robotic Arm
The following procedure Artikels the safe neutralization of a simulated hazardous material spill using a robotic arm, emphasizing safety and methodical execution. This process highlights the importance of careful planning and the step-wise approach crucial for successful hazardous material response.
- Assessment and Planning: Analyze the spill, identifying the type and extent of the hazardous material, and the surrounding environment. Develop a detailed plan, including robot deployment strategy and safety protocols.
- Robot Deployment: Carefully deploy the robotic arm to the spill site, ensuring its safe operation and avoiding any potential hazards.
- Sensor Data Acquisition: Utilize the robot’s sensors to gather data about the hazardous material, including its concentration and properties. This information informs the neutralization strategy.
- Neutralization Procedure: Based on the sensor data, execute the planned neutralization procedure using the robotic arm. This may involve applying neutralizing agents, containing the spill, or collecting samples.
- Monitoring and Adjustment: Continuously monitor the spill’s status and adjust the neutralization procedure as needed, ensuring effective containment and neutralization.
- Post-Neutralization Assessment: Once the spill is neutralized, conduct a thorough assessment to confirm the effectiveness of the procedure and the safety of the environment.
- Robot Retrieval: Safely retrieve the robotic arm from the spill site, ensuring decontamination procedures are followed to prevent any further contamination.
Robotics in Infrastructure Assessment
Post-disaster infrastructure assessment is a critical, time-sensitive, and often dangerous task. Traditional methods are slow, expose human personnel to significant risks, and may not provide the comprehensive data needed for effective recovery planning. Robotics offers a compelling solution, providing a faster, safer, and more accurate way to evaluate damage to buildings and other crucial infrastructure.
Robots equipped with various sensors can access hazardous areas inaccessible or too dangerous for humans, providing crucial data on structural integrity, damage extent, and potential hazards. This allows for quicker decisions on rescue efforts, resource allocation, and rebuilding strategies, ultimately accelerating the recovery process and minimizing long-term economic and social consequences.
Benefits of Robotic Infrastructure Assessment
The advantages of employing robots for post-disaster infrastructure assessment are threefold: speed, safety, and accuracy. Robots can be deployed rapidly to disaster zones, often reaching areas before human teams can safely access them. This speed is vital in time-critical situations, where rapid assessment informs immediate rescue operations and prevents further damage. Furthermore, using robots eliminates the risk to human life in dangerous environments, reducing the human cost of disaster response. Finally, robots equipped with advanced sensors can provide more detailed and precise assessments than human inspectors, leading to better-informed decisions and more efficient resource allocation. For instance, a robot could assess a collapsed building’s stability far more accurately than a human, allowing engineers to plan demolition or stabilization safely and effectively.
Limitations of Current Robotic Technology
Despite the considerable advantages, current robotic technology faces limitations in assessing complex infrastructure damage. The ability of robots to navigate highly damaged environments, especially those with unstable debris fields, remains a challenge. Processing and interpreting the vast amounts of data collected by robots also requires sophisticated algorithms and powerful computing resources. Additionally, the cost of specialized robots and the expertise needed to operate and maintain them can be a barrier for some organizations. For example, a robot might struggle to navigate a collapsed building with uneven terrain and shifting debris, limiting its ability to fully assess the damage. The complexity of the data analysis required to interpret the sensor readings can also pose a challenge.
Sensors and Data Analysis Techniques in Robotic Infrastructure Assessment
The effectiveness of robotic infrastructure assessment relies heavily on the sensors used and the techniques employed for data analysis. The data gathered is crucial for accurate damage assessment and informed decision-making.
- LiDAR (Light Detection and Ranging): Creates 3D point clouds of the environment, providing detailed measurements of building geometry and damage extent. This data can reveal cracks, collapses, and other structural weaknesses that might be missed by human inspection.
- Cameras (Visual Inspection): High-resolution cameras, sometimes equipped with thermal imaging capabilities, capture visual data of the damaged infrastructure. This data allows for visual inspection of cracks, debris, and other damage indicators, complementing the data obtained from other sensors.
- Ground Penetrating Radar (GPR): Detects subsurface structures and voids, helping to assess foundation damage and the presence of potential hazards like unstable ground or buried utilities. This is particularly useful for identifying hidden damage that isn’t visible on the surface.
- Acoustic Sensors: Detect sounds indicative of structural instability, such as cracking or shifting materials. This information helps to identify potentially hazardous areas that require immediate attention.
- Gas Sensors: Detect the presence of hazardous gases, such as methane or carbon monoxide, which can be released after a disaster. This information is vital for ensuring the safety of rescue personnel and guiding recovery efforts.
The data collected by these sensors is then processed using advanced algorithms and techniques such as:
- 3D Modeling and Visualization: Creating detailed 3D models of the damaged infrastructure allows for a comprehensive understanding of the damage extent and facilitates effective planning for repairs or demolition.
- Machine Learning and AI: Automated damage detection and classification using machine learning algorithms helps to accelerate the assessment process and improve accuracy. AI can analyze vast datasets to identify patterns and anomalies that might be missed by human inspectors.
- Finite Element Analysis (FEA): Used to simulate the structural behavior of the damaged infrastructure and predict its stability. This helps to guide decisions on stabilization and repair strategies.
Human-Robot Collaboration in Disaster Response
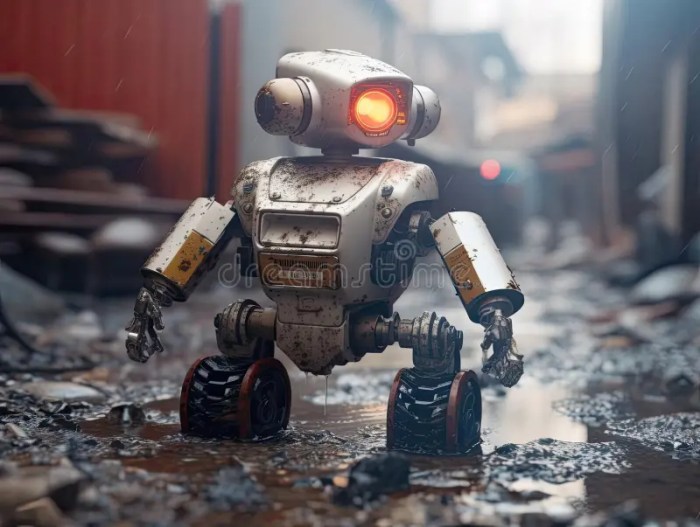
Source: dreamstime.com
The synergy between human ingenuity and robotic capabilities is revolutionizing disaster response. Integrating human expertise with the strengths of robots creates a powerful force for efficient and effective rescue operations, particularly in hazardous or unpredictable environments. This collaboration leverages the best of both worlds: human judgment, adaptability, and empathy combined with the robot’s strength, endurance, and precision in dangerous situations.
Human-robot teams offer significant advantages in disaster scenarios. Robots can access and navigate areas too dangerous or difficult for humans, providing crucial information and performing tasks like debris removal or delivering supplies. Meanwhile, human operators can provide critical decision-making, contextual understanding, and ethical considerations that robots currently lack. This partnership not only enhances speed and efficiency but also significantly reduces risks to human life.
Advantages of Human-Robot Collaboration in Disaster Response
The integration of human expertise and robotic capabilities yields several key benefits. Robots excel at performing repetitive, dangerous, or physically demanding tasks, freeing up human responders to focus on more complex problem-solving and decision-making. This division of labor optimizes resource allocation and enhances overall operational efficiency. Furthermore, robots can provide real-time data and situational awareness through sensors and cameras, allowing human operators to make more informed decisions. The combined approach minimizes human exposure to harm, thereby safeguarding valuable personnel and maximizing the effectiveness of rescue operations.
Design Considerations for Human-Robot Interfaces in High-Stress Situations
Designing effective human-robot interfaces for disaster response requires careful consideration of the high-stress environment. Interfaces must be intuitive, reliable, and easy to use, even under pressure. Simplicity is paramount; complex controls can lead to errors and delays. Robust communication systems are essential to ensure seamless information flow between human operators and robots, even in areas with limited connectivity. Feedback mechanisms are crucial, allowing operators to understand the robot’s status and actions. Furthermore, the design should minimize cognitive load on the operator, presenting information clearly and efficiently to reduce decision-making fatigue. The interface should also account for potential physical limitations, such as wearing protective gear. For instance, voice commands and haptic feedback can be more effective than traditional controls in such scenarios.
Examples of Successful Human-Robot Collaborations in Real-World Disaster Response Operations, The Role of Robotics in Disaster Recovery and Emergency Services
Several real-world examples highlight the effectiveness of human-robot collaboration in disaster response. During the Fukushima Daiichi nuclear disaster, robots were deployed to assess radiation levels and inspect damaged reactor buildings, providing crucial data for human decision-makers. Similarly, robots have been used in earthquake rescue operations to search for survivors in collapsed buildings, often navigating through rubble and confined spaces inaccessible to humans. In the aftermath of Hurricane Katrina, unmanned aerial vehicles (UAVs) provided aerial surveys of flooded areas, mapping damage and assisting in search and rescue efforts. These successful deployments showcase the significant potential of human-robot teams to improve the speed, efficiency, and safety of disaster response operations, saving lives and minimizing further damage.
Future Trends in Disaster Robotics
The field of disaster robotics is poised for a dramatic leap forward, driven by advancements in artificial intelligence (AI), machine learning (ML), and materials science. We’re moving beyond robots that simply follow pre-programmed instructions to autonomous systems capable of adapting to unpredictable and hazardous environments, significantly enhancing the speed and effectiveness of disaster relief efforts. This evolution promises to save lives and minimize the long-term impact of natural disasters and other emergencies.
The integration of AI and ML is revolutionizing disaster robotics. AI algorithms can process vast amounts of sensor data in real-time, allowing robots to make more informed decisions, navigate complex terrain, and identify survivors more efficiently. Machine learning enables robots to learn from past experiences, improving their performance over time and adapting to new challenges without human intervention. For instance, a robot trained on data from past earthquakes could learn to identify the most stable paths through rubble, improving search and rescue operations.
Advancements in Robotic Dexterity, Autonomy, and Resilience
Future disaster response robots will boast significantly improved dexterity, enabling them to perform more complex tasks such as delicate manipulation of debris to access survivors or precise operation of valves in hazardous material situations. Increased autonomy will allow robots to operate independently for longer periods, reducing the reliance on human operators in dangerous environments. This autonomy will be coupled with enhanced resilience, enabling robots to withstand harsh conditions, including extreme temperatures, water damage, and physical impacts, ensuring continued operation even in the face of significant damage. Imagine robots that can self-repair minor damage or adapt their locomotion to navigate unpredictable terrain, extending their operational lifespan and effectiveness. For example, a robot equipped with advanced self-diagnostic capabilities could detect and isolate a malfunctioning component, allowing it to continue operating with reduced functionality until repairs are possible.
A Futuristic Disaster Response Robot: The “Resilient Responder”
Imagine the Resilient Responder, a quadrupedal robot approximately the size of a large dog. Its body is constructed from a lightweight yet incredibly strong carbon fiber composite, capable of withstanding significant impacts and extreme temperatures. Its four legs, each equipped with multiple independently actuated joints and advanced sensors, allow it to traverse uneven terrain, climb stairs, and navigate rubble piles with ease. The robot’s head houses a suite of advanced sensors, including high-resolution cameras with thermal imaging, lidar for 3D mapping, and microphones for sound localization. These sensors feed data to an onboard AI system that enables the robot to autonomously navigate, identify survivors, and assess structural damage. Manipulator arms, located on either side of its body, are equipped with sensitive tactile sensors and multiple degrees of freedom, allowing it to delicately handle objects, open doors, and even administer basic medical aid. The robot’s power system utilizes a combination of high-capacity batteries and fuel cells, ensuring extended operational time in the field. Its communication system utilizes multiple redundant channels, ensuring reliable communication even in areas with limited connectivity. Furthermore, its modular design allows for easy replacement of damaged components, maximizing its operational lifespan. The Resilient Responder exemplifies the future of disaster response, a future where robots are not just tools but vital partners in saving lives and mitigating the impact of disaster.
Last Recap
The integration of robotics into disaster recovery isn’t just a technological advancement; it’s a humanitarian imperative. As we’ve seen, these machines are already proving their worth in search and rescue, hazardous material handling, and infrastructure assessment. The future holds even greater potential – imagine swarms of autonomous robots collaborating seamlessly, powered by AI, to minimize damage and maximize survival rates. The role of robotics in disaster response is evolving rapidly, offering a brighter, safer future for those facing unimaginable crises.