The Role of Digital Twins in Industrial Revolution 4.0 isn’t just hype; it’s the real deal. Imagine a perfect digital mirror of your entire factory, predicting breakdowns before they happen, optimizing production in real-time, and even designing new products virtually. That’s the power of digital twins, and it’s reshaping how industries operate, from manufacturing to energy. This isn’t science fiction; it’s the future of efficiency and innovation, and we’re diving deep into how it’s all happening.
This deep dive explores the core concepts of digital twins, from data acquisition and integration to sophisticated modeling and simulation. We’ll look at practical applications across various sectors, examining the challenges and exploring the exciting future trends that promise to revolutionize industrial processes even further. Get ready to unlock the secrets behind this game-changing technology.
Defining Digital Twins in Industry 4.0
Industry 4.0, the current stage of the industrial revolution, is characterized by the convergence of physical and digital worlds. Central to this convergence is the concept of the digital twin, a virtual representation of a physical object or system. These aren’t just simple 3D models; they’re dynamic, data-driven simulations that evolve alongside their real-world counterparts.
Digital twins in Industry 4.0 are sophisticated virtual models that mirror real-world assets, processes, or systems. They incorporate various data streams from sensors, simulations, and historical data to provide a comprehensive understanding of the physical entity’s behavior, performance, and potential issues. Core components include a 3D model, real-time data integration, sophisticated algorithms for data analysis and prediction, and a user interface for visualization and interaction. The level of complexity varies drastically depending on the application.
Digital Twin Variations Across Industries
The application of digital twins differs significantly across industrial sectors. In manufacturing, digital twins might focus on individual machines, entire production lines, or even the complete factory. This allows for predictive maintenance, optimized production processes, and improved quality control. For example, a digital twin of a turbine in an energy plant could predict potential failures based on vibration data, enabling proactive maintenance and preventing costly downtime. In the healthcare sector, digital twins of organs or patients can aid in surgical planning and personalized medicine. The focus always remains on leveraging the virtual model to optimize performance, predict issues, and improve decision-making in the physical world. The common thread is the ability to simulate, analyze, and predict the behavior of the physical asset or process.
Real-World Applications of Digital Twins
Digital twins are already making a tangible impact across multiple sectors. Consider a large-scale wind farm. A digital twin of this farm can analyze wind patterns, turbine performance, and energy output, optimizing energy production and reducing maintenance costs. Similarly, in the automotive industry, digital twins are used to simulate vehicle performance under various conditions, leading to improved designs and enhanced safety features. A manufacturer of complex machinery might use a digital twin to simulate the assembly process, identifying potential bottlenecks and optimizing the workflow before the physical implementation. These are just a few examples highlighting the versatile applications of this technology.
Types of Digital Twins: A Comparison
The functionality and data sources used to create digital twins vary considerably. This table summarizes some key differences:
Type of Digital Twin | Functionality | Data Sources | Example |
---|---|---|---|
Product Twin | Simulates product performance and behavior throughout its lifecycle. | CAD data, simulation results, sensor data from real-world products. | Predictive maintenance of an aircraft engine. |
Process Twin | Models and optimizes industrial processes. | Production line data, sensor data, operational parameters. | Optimizing a chemical reaction process in a refinery. |
System Twin | Represents complex systems, integrating multiple components. | Data from various subsystems, external environmental data. | Managing a smart city’s energy grid. |
Asset Twin | Focuses on individual assets and their performance. | Sensor data, maintenance records, operational history. | Monitoring the condition of a bridge. |
Data Acquisition and Integration for Digital Twins: The Role Of Digital Twins In Industrial Revolution 4.0
Building a truly effective digital twin requires a constant influx of real-time data, acting as its lifeblood. This data paints a picture of the physical asset’s current state, performance, and environment, allowing for accurate modeling and predictive analysis. Without a robust data acquisition and integration strategy, your digital twin remains a static representation, failing to deliver the dynamic insights crucial for Industry 4.0.
The accuracy and usefulness of a digital twin hinges directly on the quality and completeness of the data feeding it. Various sources contribute to this data stream, each presenting unique challenges in terms of format, volume, and reliability. Successfully integrating these disparate sources into a unified, consistent model is key to unlocking the full potential of the digital twin technology.
Data Sources for Digital Twins
Data for a digital twin comes from a variety of sources, each offering a unique perspective on the physical asset. Sensors embedded within the equipment provide real-time measurements of operational parameters such as temperature, pressure, vibration, and power consumption. These readings, often captured at high frequency, form the backbone of the digital twin’s operational model. In addition to sensor data, simulations, often based on physics-based models or historical data, provide insights into potential scenarios and “what-if” analyses. Finally, databases, containing historical operational data, maintenance logs, and design specifications, provide context and a historical perspective, enabling the digital twin to learn and adapt over time. The integration of these diverse sources, however, is a significant challenge.
Challenges of Data Integration and Standardization
Integrating data from these diverse sources presents several significant hurdles. Different sensors may use different communication protocols, data formats, and units of measurement, leading to incompatibility issues. Data from simulations might be presented in a different format than sensor data, requiring careful transformation and reconciliation. Furthermore, ensuring data consistency and accuracy across all sources is crucial, as inconsistencies can lead to inaccurate modeling and flawed predictions. Establishing a common data model and standardized data formats is essential to overcome these challenges and facilitate seamless data integration. This often involves implementing robust data cleaning and transformation processes to ensure data quality and consistency. Consider the example of a wind turbine digital twin; integrating sensor data on wind speed from different manufacturers, each with their own data formats, requires careful standardization and data transformation.
Data Pipeline Architecture for Digital Twins
A well-designed data pipeline is critical for efficiently and reliably feeding data into a digital twin. A typical architecture might involve several stages. First, data from various sources is collected and pre-processed. This involves cleaning, transforming, and validating the data to ensure consistency and quality. Next, the pre-processed data is stored in a central data lake or warehouse, providing a unified repository for all digital twin data. From there, data is ingested into the digital twin platform, where it is used to update the model and perform analyses. Real-time data streams, such as sensor data, might bypass the data lake and be directly streamed to the digital twin platform for immediate analysis. This architecture allows for scalability and flexibility, accommodating increasing data volumes and diverse data sources.
Data Security and Privacy in the Digital Twin Ecosystem
Security and privacy are paramount concerns when dealing with sensitive operational data. Implementing robust security measures is crucial to protect the digital twin from unauthorized access and cyberattacks. This involves implementing secure communication protocols, access control mechanisms, and data encryption techniques. Furthermore, adhering to relevant data privacy regulations, such as GDPR, is essential, especially when dealing with personally identifiable information or sensitive operational data. For example, access to the digital twin should be restricted to authorized personnel only, and all data transmissions should be encrypted to prevent unauthorized access. Regular security audits and penetration testing can help identify and address potential vulnerabilities.
Modeling and Simulation Capabilities
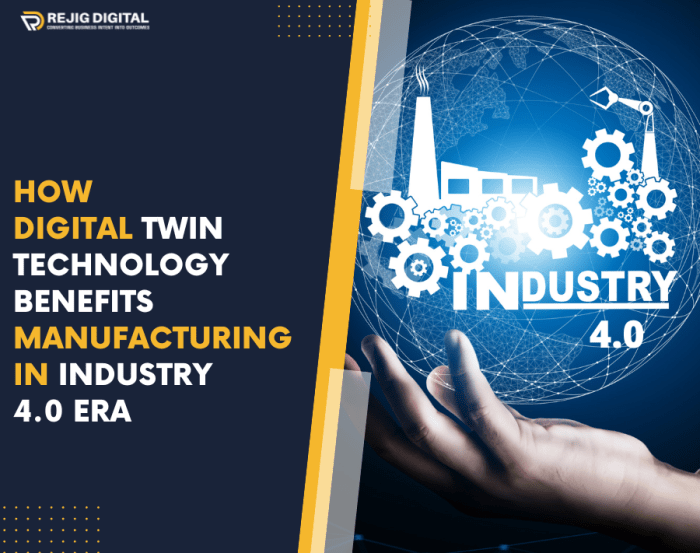
Source: rejigdigital.com
Digital twins aren’t just static representations; they’re dynamic simulations capable of predicting future behavior and optimizing performance. The power of a digital twin lies in its ability to model complex systems and run simulations to understand how they’ll react under various conditions. This allows for proactive decision-making and prevents costly downtime or failures.
Modeling Techniques for Digital Twins
Creating accurate digital twins requires sophisticated modeling techniques. Three primary approaches stand out: physics-based, data-driven, and hybrid models. Physics-based modeling relies on fundamental physical laws and equations to represent the system’s behavior. This approach offers high accuracy but can be computationally intensive and require detailed knowledge of the underlying physics. Data-driven modeling, on the other hand, uses historical data and machine learning algorithms to build a model. It’s less reliant on explicit physical knowledge but can be less accurate for predicting behavior outside the range of the training data. Hybrid models combine the strengths of both approaches, using physics-based models for fundamental behavior and data-driven models to refine the predictions and account for uncertainties. For instance, a hybrid model of a wind turbine might use physics-based equations to simulate aerodynamics but use data-driven models to account for unpredictable weather patterns.
The Role of Simulation in Predicting Asset Behavior
Simulation is the heart of digital twin technology. By creating a virtual replica of a physical asset or process, engineers can test different scenarios, predict potential problems, and optimize operations without affecting the real-world counterpart. For example, a digital twin of a manufacturing plant can simulate the impact of changing production parameters, allowing for optimization of throughput and resource allocation. Simulations also enable engineers to test different maintenance strategies, predict equipment failures, and schedule preventative maintenance to minimize downtime. This proactive approach to maintenance significantly reduces operational costs and improves overall efficiency.
Simulation for Optimization, What-If Analysis, and Predictive Maintenance
Simulations empower a variety of powerful applications within the industrial setting. Optimization involves running numerous simulations with varying parameters to identify the optimal configuration for maximum efficiency. For example, a digital twin of a chemical process can be used to optimize reaction parameters, minimizing waste and maximizing yield. What-if analysis allows engineers to explore the consequences of different events or decisions. For instance, a digital twin of a power grid can simulate the impact of a sudden surge in demand or a component failure, helping to develop strategies to prevent blackouts. Predictive maintenance uses simulations to forecast equipment failures based on real-time data and historical patterns. By identifying potential problems before they occur, companies can schedule maintenance proactively, avoiding unexpected downtime and costly repairs. Consider a scenario where a digital twin of a jet engine predicts a potential bearing failure in a few weeks. This allows the airline to schedule maintenance during a planned downtime, preventing a potentially catastrophic mid-flight failure.
Comparison of Simulation Software Packages
Choosing the right simulation software is crucial for building effective digital twins. Several packages cater to industrial applications, each with its strengths and weaknesses.
Software | Strengths | Weaknesses | Typical Applications |
---|---|---|---|
ANSYS | Wide range of physics-based simulation capabilities, strong community support | Can be expensive, steep learning curve | Structural analysis, fluid dynamics, electromagnetics |
MATLAB/Simulink | Versatile platform for modeling and simulation, extensive toolboxes | Requires programming skills, can be complex for beginners | Control systems, signal processing, algorithm development |
Siemens NX | Integrated CAD/CAM/CAE software, suitable for complex product development | High cost, complex interface | Product design, manufacturing simulation |
COMSOL Multiphysics | Powerful multiphysics simulation capabilities, user-friendly interface | Can be computationally intensive for large models | Multiphysics simulations (e.g., fluid-structure interaction) |
Applications of Digital Twins in Manufacturing
Digital twins are revolutionizing manufacturing, offering unprecedented opportunities for optimization and innovation. By creating a virtual replica of a physical asset or process, manufacturers gain valuable insights that were previously impossible to obtain, leading to significant improvements in efficiency, productivity, and profitability. This virtual representation allows for testing, analysis, and optimization before implementing changes in the real world, minimizing risk and maximizing return on investment.
The applications of digital twins span various aspects of the manufacturing lifecycle, from initial product design to ongoing maintenance and optimization. Let’s explore some key areas where digital twins are making a significant impact.
Optimizing Manufacturing Processes Through Production Planning and Scheduling
Digital twins provide a dynamic and interactive model of the entire manufacturing process, enabling real-time monitoring and analysis of production flows. This allows for the identification of bottlenecks, inefficiencies, and potential disruptions before they impact production. For example, a digital twin of an assembly line can simulate different production schedules, allowing manufacturers to optimize resource allocation, minimize lead times, and maximize throughput. By incorporating real-time data from sensors and other sources, the digital twin can adapt to unforeseen events, such as machine breakdowns or material shortages, automatically adjusting the production schedule to minimize delays. This predictive capability is a key advantage over traditional planning methods.
Improving Product Design and Development Through Virtual Prototyping
Virtual prototyping using digital twins significantly accelerates the product development process and reduces costs associated with physical prototypes. Designers can test different design iterations in the virtual world, evaluating performance under various conditions and identifying potential flaws before committing to physical production. This allows for iterative design improvements, leading to higher-quality products with shorter development cycles. For instance, a digital twin of a new engine can be used to simulate its performance under different operating conditions, helping engineers optimize its design for efficiency and durability. This virtual testing significantly reduces the need for expensive and time-consuming physical testing.
Predictive Maintenance and Reducing Downtime in Manufacturing Facilities
Digital twins enable predictive maintenance by monitoring the performance of equipment in real-time and predicting potential failures before they occur. By analyzing data from sensors embedded in machinery, the digital twin can identify patterns that indicate impending failures, allowing for proactive maintenance to be scheduled, preventing costly downtime. For example, a digital twin of a critical piece of equipment in a chemical plant can monitor its operating parameters and predict when maintenance is needed, based on historical data and machine learning algorithms. This allows for planned maintenance to be scheduled during off-peak hours, minimizing disruptions to production. This proactive approach leads to substantial cost savings by preventing unexpected breakdowns and reducing the need for emergency repairs.
Implementing a Digital Twin for Assembly Line Optimization: A Step-by-Step Procedure, The Role of Digital Twins in Industrial Revolution 4.0
Implementing a digital twin for assembly line optimization involves a structured approach. Consider optimizing a car assembly line as an example.
- Data Acquisition and Integration: Gather data from various sources, including sensors on the assembly line (robot speeds, conveyor belt status, etc.), production management systems (work orders, inventory levels), and quality control systems (defect rates). Integrate this data into a central platform.
- Model Creation: Develop a 3D model of the assembly line, including all machines, robots, and conveyors. This model will be the foundation of the digital twin.
- Simulation and Validation: Simulate different scenarios (e.g., increased production rate, different worker assignments) to test the impact on throughput and efficiency. Validate the model against real-world data to ensure accuracy.
- Optimization and Deployment: Identify bottlenecks and inefficiencies through simulation. Implement changes to the real-world assembly line based on the simulation results. Monitor the performance of the optimized line using the digital twin and make further adjustments as needed.
- Continuous Monitoring and Improvement: Continuously monitor the performance of the assembly line using the digital twin, updating the model with real-time data. Use this information to identify new opportunities for improvement and further optimize the process.
The Role of Digital Twins in Supply Chain Management
Forget spreadsheets and endless phone calls – the future of supply chain management is digital. Digital twins offer unprecedented visibility and control, transforming how businesses manage their goods, from raw materials to finished products. By creating a virtual replica of a physical supply chain, businesses gain powerful insights to optimize processes, reduce risks, and ultimately, boost efficiency and profitability.
Digital twins in supply chain management aren’t just about tracking packages; they’re about creating a holistic, real-time understanding of the entire network. This allows businesses to proactively address potential issues, improve decision-making, and react swiftly to unexpected disruptions, making their supply chains more resilient and responsive to the ever-changing demands of the market.
Improved Supply Chain Visibility and Traceability
Digital twins provide a single source of truth for all supply chain data. This means every component, from the origin of raw materials to the final delivery to the customer, can be tracked and monitored in real-time. This level of visibility drastically improves transparency, allowing businesses to identify bottlenecks, inefficiencies, and potential problems before they escalate into major disruptions. For example, a digital twin might highlight a delay at a specific port, allowing the business to reroute shipments and avoid significant delays. The detailed tracking also enhances traceability, crucial for meeting regulatory compliance requirements and responding quickly to product recalls.
Risk Management and Disruption Mitigation in Supply Chains
The predictive power of digital twins is invaluable for risk management. By simulating various scenarios, businesses can anticipate potential disruptions, such as natural disasters, geopolitical instability, or supplier failures. This allows for the development of contingency plans and proactive mitigation strategies. For instance, a digital twin might simulate the impact of a port closure, allowing a business to explore alternative shipping routes and secure backup suppliers, minimizing the impact on production and customer deliveries. This proactive approach to risk management transforms reactive firefighting into strategic planning.
Optimization of Logistics and Transportation
Digital twins optimize logistics and transportation by providing real-time data on vehicle location, cargo status, and potential delays. This allows for dynamic route optimization, reducing transportation costs and delivery times. For example, a digital twin might suggest a faster route based on real-time traffic conditions or identify opportunities to consolidate shipments, reducing the number of trucks on the road and lowering fuel consumption. Furthermore, predictive maintenance capabilities within the digital twin can prevent vehicle breakdowns, minimizing downtime and improving overall operational efficiency.
Digital Twin Architecture for Tracking Goods in Transit
Consider a scenario where a company needs to track goods in transit from a manufacturing facility to a distribution center. A digital twin architecture for this could involve:
1. Data Acquisition: Sensors on shipping containers provide real-time location data (GPS), temperature, and humidity levels. This data is integrated with information from the transportation management system (TMS) and the warehouse management system (WMS).
Digital twins are revolutionizing Industry 4.0, offering unprecedented predictive capabilities and optimization opportunities. This virtual mirroring extends beyond manufacturing; consider how similar principles power immersive experiences, like those explored in The Future of Augmented Reality in Retail and Marketing , where virtual try-ons and interactive displays enhance customer engagement. Ultimately, the core concept—creating a virtual representation to improve real-world processes—remains key to both industrial efficiency and future retail strategies.
2. Data Integration and Processing: A central platform collects and processes data from various sources, using algorithms to analyze patterns and predict potential issues.
3. Digital Twin Model: A virtual representation of the shipping container, including its contents, location, and environmental conditions, is created and updated in real-time.
4. Simulation and Prediction: The digital twin simulates different scenarios, such as unexpected delays or extreme weather conditions, allowing for proactive adjustments to the shipping route or delivery schedule.
5. Visualization and Reporting: A user-friendly interface provides real-time visibility into the status of the shipment, enabling proactive decision-making and improved communication with stakeholders.
Challenges and Future Trends
The widespread adoption of digital twins in Industry 4.0, while promising a revolution in efficiency and productivity, faces significant hurdles. Overcoming these challenges will unlock the technology’s full potential and shape its future trajectory. The journey to a fully integrated digital twin ecosystem requires addressing cost, complexity, and security concerns, while simultaneously leveraging emerging technologies like AI and VR/AR.
The path to seamless digital twin integration across all industrial operations isn’t without its bumps. High initial investment costs, the complexity of data integration from disparate systems, and concerns about data security and privacy are major obstacles. However, the potential rewards – improved efficiency, reduced downtime, and enhanced product quality – far outweigh these challenges. Innovative solutions are emerging to mitigate these risks and accelerate adoption.
Cost and Complexity of Implementation
Implementing digital twins requires substantial upfront investment in software, hardware, and skilled personnel. The complexity of integrating data from various sources, including sensors, machines, and enterprise systems, adds another layer of challenge. For smaller businesses, the high initial cost can be a significant barrier to entry. However, the long-term cost savings from optimized processes and reduced downtime can provide a compelling return on investment. Modular implementation strategies and cloud-based solutions are emerging to reduce the initial financial burden and complexity.
Data Security and Privacy Concerns
Digital twins often handle sensitive operational data, raising significant security and privacy concerns. Protecting this data from unauthorized access, cyberattacks, and breaches is paramount. Robust cybersecurity measures, including encryption, access control, and regular security audits, are crucial for maintaining data integrity and complying with relevant regulations like GDPR. The increasing adoption of blockchain technology offers promising solutions for enhanced data security and traceability within the digital twin ecosystem.
The Role of Artificial Intelligence and Machine Learning
AI and machine learning are poised to significantly enhance digital twin capabilities. AI algorithms can analyze vast amounts of data from the digital twin to identify patterns, predict failures, and optimize processes. Machine learning models can be trained to improve the accuracy of simulations and predictions over time, leading to more informed decision-making. For instance, AI could predict potential equipment malfunctions based on real-time sensor data, allowing for proactive maintenance and minimizing downtime in manufacturing plants. This predictive maintenance capability, enabled by AI, represents a significant advancement in operational efficiency.
Future Trends in Digital Twin Technology
The future of digital twins will be shaped by several key trends. The integration of augmented reality (AR) and virtual reality (VR) will create immersive experiences for interacting with and visualizing digital twins. AR overlays can provide real-time insights and instructions to technicians performing maintenance, while VR can simulate complex scenarios for training purposes. Furthermore, the increasing use of edge computing will enable real-time processing of data closer to the source, reducing latency and improving responsiveness. The convergence of digital twins with other Industry 4.0 technologies, such as the Industrial Internet of Things (IIoT), will create even more powerful and interconnected systems.
A Future Scenario: Seamlessly Integrated Digital Twins
Imagine a future where a global manufacturing company uses digital twins across its entire value chain. From the design phase, engineers utilize digital twins to simulate and optimize product designs, predicting potential manufacturing challenges before they arise. During manufacturing, real-time sensor data feeds into digital twins, providing insights into machine performance and identifying potential issues. Supply chain management is optimized through digital twins that simulate logistics, predict disruptions, and dynamically adjust shipping routes. Finally, digital twins enable proactive maintenance, reducing downtime and extending the lifespan of equipment. This integrated approach delivers significant improvements in efficiency, productivity, and profitability. In this scenario, AR overlays provide real-time data to technicians on the factory floor, allowing for immediate identification and resolution of problems. VR simulations train workers on new processes and equipment, enhancing safety and reducing errors. The entire operation is optimized, with AI-powered predictive analytics providing continuous improvement.
Outcome Summary
Digital twins aren’t just a technological advancement; they’re a fundamental shift in how we approach industrial operations. By creating virtual replicas of real-world assets and processes, we’re gaining unprecedented levels of insight, control, and predictive power. From optimizing supply chains to revolutionizing manufacturing, the potential is limitless. As technology continues to evolve, we can expect even more sophisticated and integrated digital twin applications, ushering in a new era of efficiency, sustainability, and innovation in Industry 4.0. The future is digital, and it’s incredibly exciting.