The Role of Digital Twins in Creating Virtual Models of Physical Objects is revolutionizing how we design, build, and manage everything from jet engines to hospitals. Forget static blueprints; imagine a constantly updating, interactive replica of a physical object, mirroring its every move and change in real-time. This is the power of the digital twin, offering unprecedented insights and predictive capabilities across industries.
This technology isn’t just futuristic hype; it’s already impacting sectors like manufacturing, where digital twins optimize production lines and predict potential failures. In healthcare, they’re personalizing treatments and improving surgical outcomes. And in infrastructure, they’re ensuring bridges stand strong and power grids remain stable. We’ll dive deep into how these virtual models are built, the data fueling them, and the astonishing possibilities they unlock.
Introduction to Digital Twins and Virtual Models
Imagine a perfect replica of a physical object, existing entirely in the digital realm. That’s essentially what a digital twin is – a virtual representation of a real-world entity, process, or system. It’s not just a static model; it’s a dynamic, evolving simulation that updates in real-time based on data collected from its physical counterpart. This allows for unprecedented insights and capabilities, transforming how we design, monitor, and optimize everything from jet engines to entire cities.
Digital twins offer a multitude of advantages when it comes to modeling physical objects. By creating a virtual environment, engineers and designers can experiment with different scenarios, test modifications, and predict potential failures without risking damage to the actual physical asset. This leads to significant cost savings, improved efficiency, and enhanced product performance. The ability to simulate real-world conditions within the digital twin allows for predictive maintenance, preventing costly downtime and extending the lifespan of equipment. Moreover, digital twins facilitate collaboration among stakeholders, providing a shared platform for visualization, analysis, and decision-making.
Examples of Digital Twin Applications Across Industries
Digital twins are revolutionizing various sectors. In manufacturing, they’re used to optimize production lines, predict equipment failures, and improve product quality. For example, a car manufacturer might use a digital twin of a vehicle assembly line to simulate the impact of different production schedules or robotic arm placements, optimizing for speed and efficiency. In the aerospace industry, digital twins are employed to model aircraft performance under various flight conditions, enabling engineers to identify potential design flaws and enhance safety. The healthcare sector utilizes digital twins to simulate the human body, helping doctors plan surgeries and personalize treatments. Even smart cities are leveraging digital twins to model traffic flow, energy consumption, and other urban systems, enabling more efficient resource management and improved infrastructure planning.
Types of Digital Twins: A Comparison
The complexity and application of digital twins vary widely. They can range from simple models focusing on a single aspect of a physical object to highly sophisticated simulations incorporating vast amounts of data and complex interactions. The following table provides a comparison of different types:
Type of Digital Twin | Complexity | Application Examples | Data Sources |
---|---|---|---|
Data-driven Twin | Low to Medium | Monitoring equipment performance, predicting maintenance needs | Sensors, IoT devices |
Physics-based Twin | Medium to High | Simulating fluid dynamics, stress analysis, aerodynamic performance | CAD models, simulation software, sensor data |
Process Twin | Medium to High | Optimizing manufacturing processes, simulating supply chains | ERP systems, SCADA systems, sensor data |
System Twin | High | Modeling complex systems like power grids, smart cities | Multiple data sources, including sensor data, simulations, and historical data |
Data Acquisition and Integration for Digital Twin Creation: The Role Of Digital Twins In Creating Virtual Models Of Physical Objects
Building a digital twin isn’t just about slapping some virtual bits together; it’s about meticulously capturing the essence of a physical object. This involves a complex dance of data acquisition and integration, ensuring that the virtual model accurately reflects its real-world counterpart, down to the tiniest detail. Think of it as creating a high-fidelity replica, not just a rough sketch. Getting this right is crucial for the digital twin to be useful for predictive maintenance, performance optimization, or any other intended application.
Data acquisition forms the bedrock of any successful digital twin. It’s the process of gathering information from the physical object, transforming raw data into usable digital information. This data is then integrated to form a comprehensive and accurate virtual representation. The quality and completeness of this process directly impact the digital twin’s effectiveness.
Methods for Acquiring Data from Physical Objects
Several methods exist for gathering data from physical objects, each offering unique advantages depending on the object’s characteristics and the desired level of detail. For instance, a simple object might only need measurements, while a complex machine might require a far more intricate data collection process. The key is to choose the right tools and techniques to capture the relevant information.
Direct measurement techniques involve physically interacting with the object to collect data. This can include using tools like calipers, laser scanners, or 3D cameras to obtain geometric data. Sensors embedded within the object itself, or strategically placed nearby, provide real-time information on operational parameters like temperature, pressure, vibration, and more. These measurements form the backbone of a functional digital twin, providing the dynamic aspect of the model.
Data Integration Process, The Role of Digital Twins in Creating Virtual Models of Physical Objects
Integrating data from various sources into a cohesive digital twin is a crucial step. It’s like assembling a complex puzzle where each piece—sensor data, CAD models, simulation results—must fit perfectly. This involves data cleaning, transformation, and validation to ensure consistency and accuracy. Specialized software and algorithms are often used to handle this process, ensuring that the different data sources are harmonized into a unified digital twin model. The goal is to create a seamless and accurate representation that can be used for analysis and simulation.
Examples of Data Types Used in Digital Twin Creation
The data fueling a digital twin is diverse, reflecting the multifaceted nature of the physical object. Sensor data provides real-time insights into the object’s operational parameters. This could include temperature readings from a turbine blade, vibration data from a motor, or pressure readings from a pipeline. CAD models offer precise geometric information, providing the static structure of the digital twin. Simulation results, obtained from computational fluid dynamics (CFD) or finite element analysis (FEA), provide insights into the object’s behavior under various conditions. All these data types, when integrated effectively, create a rich and informative digital twin.
Data Integration Pipeline Flowchart
Imagine a flowchart with several distinct stages. First, we have Data Acquisition, where different sources like sensors, CAD models, and simulations contribute raw data. This data then flows into Data Preprocessing, where cleaning and formatting occur, ensuring compatibility. Next is Data Fusion, where the different datasets are combined using appropriate algorithms. Finally, Data Validation checks the accuracy and consistency of the integrated data before populating the digital twin model. This final stage ensures the model’s integrity and reliability. This process, while seemingly linear, often involves iterative refinement and adjustments to ensure accuracy.
Modeling and Simulation Techniques in Digital Twin Development
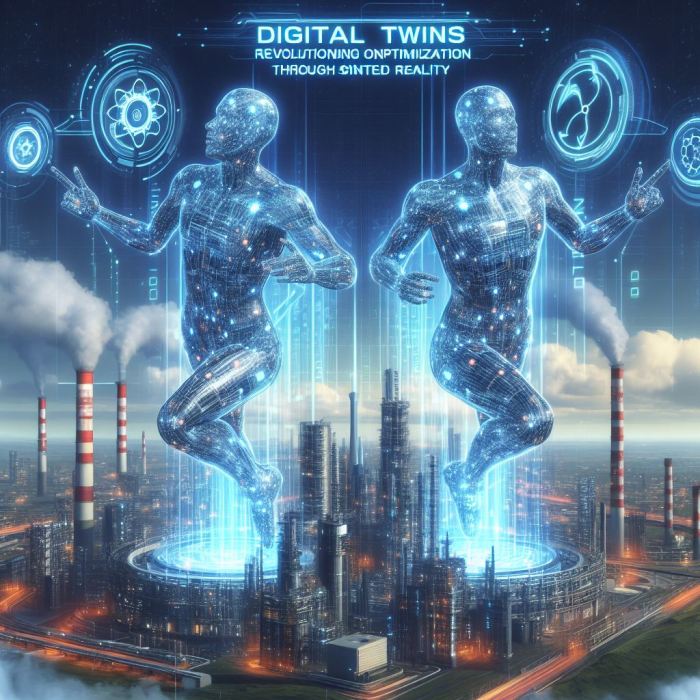
Source: electroferretera.com
Digital twins are all the rage, creating incredibly detailed virtual representations of real-world objects. This mirroring extends beyond engineering; think about the leap in realism we’re seeing in film – check out how 3D animation is revolutionizing the film industry by reading this article: How 3D Animation Is Revolutionizing the Film Industry. The same principles of precise modeling and simulation, though applied to different scales, power both digital twins and the stunning visuals now dominating the big screen.
Building a truly representative digital twin requires sophisticated modeling techniques that accurately capture the physical object’s characteristics and behavior. This involves selecting the right approach based on the complexity of the object, the desired level of accuracy, and available computational resources. Different methods offer varying strengths and weaknesses, impacting both the fidelity of the virtual model and the time and resources needed to create it.
Several modeling techniques are employed in digital twin creation, each with its own strengths and limitations. The choice depends heavily on the specific application and the level of detail required. These techniques are often used in conjunction to achieve a comprehensive representation.
3D Modeling Techniques in Digital Twin Development
3D modeling forms the visual foundation of most digital twins. It provides a geometric representation of the physical object, laying the groundwork for more complex simulations. Techniques like CAD (Computer-Aided Design) modeling allow for precise representation of shapes, dimensions, and material properties. This geometric model then serves as the basis for further analysis and simulation. For example, a 3D model of an aircraft engine can precisely capture its intricate internal components, providing a visual framework for simulating airflow and thermal dynamics. However, 3D modeling alone lacks the capacity to predict the object’s dynamic behavior under various conditions. Its strength lies in accurate geometric representation, while its limitation is the lack of physics-based predictions.
Finite Element Analysis (FEA) in Digital Twin Development
Finite Element Analysis (FEA) is a powerful computational technique used to predict the structural behavior of objects under various loads and conditions. It divides the 3D model into smaller elements, applying mathematical equations to analyze stress, strain, and deformation. FEA is particularly useful for analyzing the strength and durability of components, predicting failure points, and optimizing designs. For instance, FEA can simulate the stress distribution on a bridge under heavy traffic, helping engineers identify potential weak points and ensure structural integrity. The strength of FEA lies in its ability to predict structural responses accurately, but it can be computationally expensive, especially for complex geometries.
Computational Fluid Dynamics (CFD) in Digital Twin Development
Computational Fluid Dynamics (CFD) simulates fluid flow and heat transfer. It’s invaluable for analyzing systems involving liquids or gases, such as airflow around an aircraft wing, blood flow in arteries, or the cooling system of an electronic device. CFD uses numerical methods to solve the Navier-Stokes equations, providing detailed information about pressure, velocity, and temperature distributions. For example, CFD can be used to optimize the design of a car’s aerodynamic profile, reducing drag and improving fuel efficiency. The strength of CFD lies in its ability to simulate complex fluid behavior, but it can be computationally intensive, demanding significant processing power and time, especially for high-resolution simulations.
Simulation and Prediction within Digital Twins
Simulation is the heart of a digital twin’s predictive capabilities. By combining the geometric data from 3D modeling with the physics-based predictions of FEA and CFD, engineers can simulate the object’s behavior under various operating conditions. This allows for virtual testing, optimization, and predictive maintenance. For example, a digital twin of a wind turbine can simulate its performance under different wind speeds and predict potential failures based on stress analysis and fatigue calculations. This predictive capability enables proactive maintenance, reducing downtime and maximizing efficiency. Another example would be simulating the effect of different operating parameters on a chemical reactor using CFD, optimizing reaction yield and minimizing byproduct formation.
Software Tools for Digital Twin Modeling and Simulation
Choosing the right software is crucial for effective digital twin development. The selection depends on the specific modeling and simulation needs.
Several software packages are commonly used for digital twin modeling and simulation. These tools provide a comprehensive suite of capabilities, from 3D modeling to advanced simulation techniques.
- ANSYS: A comprehensive suite of engineering simulation software, including FEA, CFD, and multiphysics simulations.
- Autodesk Fusion 360: A cloud-based CAD/CAM/CAE software that integrates design, simulation, and manufacturing.
- Siemens NX: A powerful CAD/CAM/CAE software widely used in various industries for product development and simulation.
- MATLAB/Simulink: A powerful platform for modeling, simulation, and analysis, particularly useful for control systems and dynamic systems modeling.
- OpenFOAM: An open-source CFD software package known for its flexibility and versatility.
Visualization and Interaction with Digital Twins
Bringing a digital twin to life goes beyond just creating a virtual replica; it’s about making it accessible and insightful. Effective visualization and intuitive interaction are crucial for unlocking the full potential of these virtual models, transforming them from static representations into dynamic tools for analysis, prediction, and decision-making.
Several methods facilitate visualization and interaction, transforming complex datasets into easily understandable information. This allows users to explore, analyze, and even manipulate the virtual model, gaining valuable insights into the physical counterpart’s behavior and performance.
3D Rendering and Augmented Reality Overlays
Visualizing digital twins often involves sophisticated 3D rendering techniques. These techniques create photorealistic or stylized representations of the physical object, incorporating details like texture, lighting, and even animation to reflect real-world dynamics. For instance, a digital twin of a jet engine might show the airflow patterns in real-time, highlighted by color-coded velocity vectors. Augmented reality (AR) overlays enhance this visualization further by superimposing the digital twin onto the physical object itself, enabling users to see virtual data overlaid on the real-world counterpart. Imagine a technician using AR glasses to see the internal temperature distribution of a machine overlaid on the machine itself during maintenance.
User Interaction Methods for Digital Twin Exploration and Analysis
Effective interaction is paramount. Users need intuitive tools to explore and analyze the digital twin. This might involve using intuitive interfaces that allow for zooming, rotating, and panning within the 3D model. More advanced interactions could include slicing through the model to examine internal structures, running simulations to predict future behavior under different conditions, or even using virtual probes to measure parameters at specific points within the model. Data visualization tools, such as charts and graphs, can be integrated to display key performance indicators (KPIs) and other relevant data extracted from the digital twin.
Examples of User Interfaces for Effective Digital Twin Interaction
Many user interfaces are designed for effective interaction, ranging from simple web-based dashboards to complex, immersive virtual environments. A simple dashboard might display key metrics in real-time, allowing for quick monitoring of the physical object’s performance. More sophisticated interfaces might allow users to interact with the digital twin using virtual controllers, manipulating parameters and observing the resulting changes in the model. For example, a wind turbine digital twin might allow users to adjust blade pitch angles and observe the impact on power generation.
Mock-up User Interface for a Wind Turbine Digital Twin
Imagine a user interface for a wind turbine digital twin. The main screen displays a 3D rendering of the turbine, rotating realistically based on real-time wind speed data. A sidebar presents a series of interactive controls: a slider to adjust wind speed, buttons to simulate different weather conditions (rain, ice, etc.), and graphs showing power output, blade stress levels, and rotational speed. A map displays the turbine’s location and surrounding wind patterns. An alert system highlights potential issues, such as high stress levels or unusual vibrations, and provides detailed information and suggested actions. The interface is designed with a clean, intuitive layout and uses clear, concise visualizations to make data readily accessible to both expert and non-expert users.
Applications of Digital Twins in Various Industries
Digital twins are rapidly transforming industries by offering virtual representations of physical assets, enabling predictive maintenance, optimized operations, and enhanced decision-making. Their applications span a wide range of sectors, each benefiting from the unique capabilities of this technology. Let’s explore some key examples and their impact.
Digital Twins in Manufacturing
The manufacturing sector is a prime beneficiary of digital twin technology. By creating virtual models of production lines, individual machines, or even entire factories, manufacturers gain unprecedented insights into their operational efficiency. This allows for proactive identification of potential bottlenecks, optimization of production processes, and the prediction of equipment failures before they occur. For example, a digital twin of a robotic arm on an assembly line can simulate different operating parameters, identifying optimal speeds and movements to minimize wear and tear and maximize productivity. This predictive maintenance significantly reduces downtime and associated costs, while simultaneously improving product quality and consistency. Furthermore, digital twins allow for virtual testing of new designs and manufacturing processes, reducing the need for expensive and time-consuming physical prototypes. A company could, for example, virtually test a new assembly process on a digital twin before implementing it in the real world, thereby minimizing risks and maximizing efficiency.
Digital Twins in Healthcare
In healthcare, digital twins are revolutionizing patient care and medical research. These virtual representations of patients, organs, or even entire biological systems enable personalized medicine and improved surgical planning. For instance, a digital twin of a patient’s heart can be created using medical imaging data, allowing doctors to simulate the effects of different treatments before administering them. This personalized approach minimizes risks and improves treatment outcomes. Similarly, surgeons can use digital twins to plan complex procedures, practicing virtual surgeries and optimizing surgical techniques to reduce operation time and improve patient recovery. The ability to model disease progression using digital twins also accelerates medical research, facilitating the development of new drugs and therapies. Imagine a researcher using a digital twin of a cancerous tumor to test the efficacy of different chemotherapeutic agents before clinical trials, thereby saving time and resources.
Digital Twins in Infrastructure Management
Infrastructure management is another area where digital twins are making a significant difference. By creating virtual representations of bridges, buildings, or entire transportation networks, engineers can monitor the structural integrity of assets, predict potential failures, and optimize maintenance schedules. For example, a digital twin of a bridge can be used to simulate the effects of different weather conditions and traffic loads, allowing engineers to identify potential weak points and implement preventative measures. This proactive approach significantly reduces the risk of catastrophic failures and minimizes maintenance costs. Furthermore, digital twins enable efficient planning and execution of infrastructure projects. A city could, for example, use a digital twin of its transportation network to simulate the impact of new road construction on traffic flow, optimizing the design to minimize disruption and maximize efficiency.
Challenges and Limitations of Digital Twin Implementation
Despite the numerous benefits, implementing digital twins presents challenges. Data acquisition and integration can be complex and expensive, requiring the use of multiple sensors and data sources. The development and maintenance of accurate and reliable digital twin models also require significant expertise and computational resources. Furthermore, the security and privacy of sensitive data used to create digital twins need careful consideration. The successful implementation of digital twins requires careful planning, investment, and collaboration across different teams and organizations.
Potential Impact of Digital Twins on Future Technological Advancements
The potential impact of digital twins on future technological advancements is vast. As computing power continues to increase and data acquisition technologies improve, digital twins will become even more sophisticated and widely adopted. This will lead to breakthroughs in various fields, including personalized medicine, sustainable manufacturing, and smart cities. The integration of digital twins with artificial intelligence and machine learning will further enhance their capabilities, enabling autonomous decision-making and proactive problem-solving. The future of digital twins is bright, promising a more efficient, sustainable, and innovative world.
Future Trends and Developments in Digital Twin Technology
The world of digital twins is rapidly evolving, driven by advancements in computing power, data analytics, and connectivity. We’re moving beyond simple representations of physical assets to highly sophisticated, AI-powered systems capable of predicting behavior, optimizing performance, and driving unprecedented levels of efficiency across various industries. The future of digital twins is bright, promising a revolution in how we design, operate, and maintain everything from individual products to entire cities.
Several key trends are shaping this evolution, profoundly impacting the accuracy, scalability, and accessibility of digital twin technology. The convergence of artificial intelligence, edge computing, and the Internet of Things (IoT) is creating a new generation of digital twins that are more intelligent, responsive, and capable of handling vast amounts of data in real-time. This allows for a more dynamic and predictive understanding of the physical world.
AI Integration in Digital Twins
Artificial intelligence is no longer a futuristic concept; it’s rapidly becoming integral to the functionality of digital twins. Machine learning algorithms are being used to analyze data from various sources, identify patterns, predict failures, and optimize operations. For instance, in manufacturing, AI-powered digital twins can analyze sensor data from machines to predict potential equipment failures, allowing for proactive maintenance and minimizing downtime. This predictive capability moves beyond simple monitoring to proactive problem-solving, significantly increasing efficiency and reducing costs.
The Role of Edge Computing in Digital Twin Scalability
Edge computing, the processing of data closer to its source, is crucial for scaling digital twin applications. Processing massive datasets generated by IoT devices in the cloud can be slow and expensive. Edge computing allows for real-time analysis and decision-making, even in environments with limited or unreliable network connectivity. This is particularly important for applications involving remote assets or locations with poor internet access, such as offshore wind farms or remote infrastructure monitoring.
Consider the example of a large-scale smart city project. Edge computing allows for localized processing of traffic data from numerous sensors, enabling real-time traffic optimization without the latency associated with cloud-based processing. This improves traffic flow, reduces congestion, and enhances the overall efficiency of the city’s transportation system. The scalability achieved through edge computing enables the creation of digital twins for incredibly complex systems.
Enhanced Accuracy and Accessibility through Data Fusion
The accuracy of digital twins is directly related to the quality and quantity of data used in their creation. Future trends point towards increased data fusion – combining data from multiple sources, including sensors, simulations, and human expertise – to create more comprehensive and accurate digital twin models. This improved accuracy leads to better predictions and more informed decision-making. Furthermore, advancements in cloud computing and data visualization techniques are making digital twins more accessible to a wider range of users, regardless of their technical expertise.
Future Applications of Digital Twins Across Industries
The future role of digital twins extends far beyond current applications. We can anticipate widespread adoption in areas like personalized medicine, where digital twins of individual patients can be used to simulate the effects of different treatments, leading to more effective and personalized healthcare. In the realm of sustainable infrastructure, digital twins will play a crucial role in optimizing energy consumption, managing resources, and reducing environmental impact. Furthermore, the development of digital twins for entire ecosystems could provide invaluable insights into climate change and its effects.
Conceptual Illustration: A Future Digital Twin Application for Sustainable Agriculture
Imagine a digital twin of a large-scale farm. This digital twin integrates data from various sources: soil sensors measuring moisture and nutrient levels, weather stations providing real-time climate data, drone imagery assessing crop health, and even AI-powered image recognition systems identifying pests and diseases. The digital twin uses this data to create a dynamic model of the farm, predicting crop yields, optimizing irrigation and fertilization strategies, and identifying potential problems before they impact crop production. The system also incorporates predictive maintenance for farm equipment, ensuring optimal operational efficiency. This integrated approach allows farmers to maximize yields, minimize resource usage, and improve overall sustainability, leading to a more efficient and environmentally responsible agricultural system.
Final Summary
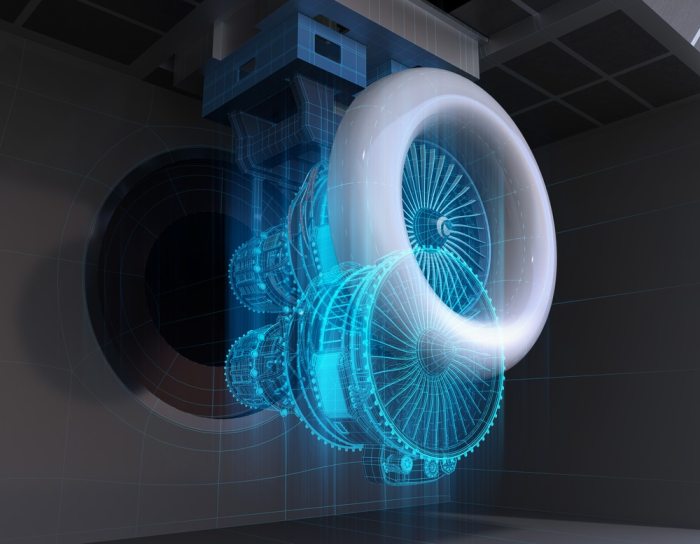
Source: bosch-digital.com
From concept to reality, digital twins are transforming how we interact with the physical world. The ability to simulate, analyze, and predict the behavior of complex systems opens doors to unprecedented levels of efficiency, safety, and innovation. As data acquisition methods improve and AI integration deepens, the applications of digital twins will only become more sophisticated and widespread, shaping a future where virtual and physical realities are seamlessly intertwined.