The Role of Automation in Transforming Manufacturing Industries is reshaping the global landscape. Forget smokestacks and assembly lines – we’re talking smart factories, AI-powered optimization, and robots working alongside humans. This isn’t just about faster production; it’s about revolutionizing efficiency, quality, safety, and even the future of work itself. We’ll dive deep into how automation is impacting everything from the factory floor to the supply chain, exploring the challenges and incredible opportunities this technological shift presents.
From increased productivity and improved product quality to enhanced safety and a changing workforce, the impact of automation on manufacturing is profound and far-reaching. We’ll examine real-world examples, explore cost considerations, and address the ethical implications of this rapidly evolving field, painting a clear picture of the transformative power of automation in today’s manufacturing world. Get ready for a deep dive into the future of making things.
Increased Efficiency and Productivity in Manufacturing
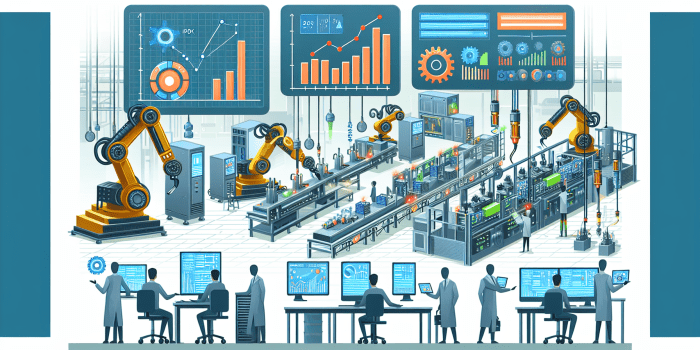
Source: praxie.com
The manufacturing landscape is undergoing a dramatic transformation, driven by the relentless march of automation. No longer a futuristic fantasy, automated systems are becoming the backbone of modern factories, significantly boosting efficiency and productivity. This shift isn’t just about faster production; it’s about optimizing entire processes, minimizing waste, and ultimately, delivering higher quality goods at lower costs.
Automation technologies, particularly robotics and artificial intelligence (AI), are revolutionizing manufacturing speed and output. Robots perform repetitive tasks with unparalleled precision and speed, tirelessly working around the clock without breaks or errors. AI, meanwhile, provides the intelligence to optimize these processes, analyzing data in real-time to identify bottlenecks, predict failures, and adjust parameters for optimal performance. This synergistic combination of robotic dexterity and AI intelligence is driving unprecedented levels of efficiency.
Examples of Automation Tools and Their Impact
Several automation tools are reshaping manufacturing processes. Industrial robots, for instance, handle tasks like welding, painting, and assembly with greater speed and accuracy than human workers. Computer Numerical Control (CNC) machines automate machining processes, creating precise parts with minimal waste. Automated Guided Vehicles (AGVs) transport materials efficiently throughout the factory floor, eliminating delays and optimizing logistics. And advanced vision systems, powered by AI, inspect products for defects with incredible accuracy, ensuring high quality control.
Efficiency Gains in Different Manufacturing Sectors, The Role of Automation in Transforming Manufacturing Industries
The impact of automation varies across sectors, but the overall trend is clear: automation significantly boosts efficiency. The table below compares the efficiency gains of automated versus manual processes across three key sectors.
Sector | Process | Manual Efficiency (%) | Automated Efficiency (%) |
---|---|---|---|
Automotive | Welding | 70 | 95 |
Electronics | Component Placement | 80 | 98 |
Food Processing | Packaging | 65 | 90 |
Note: These figures are illustrative and based on industry averages. Actual efficiency gains can vary depending on specific implementation and factors.
Case Studies Demonstrating Return on Investment
The financial benefits of automation are substantial. Many companies have reported significant returns on their automation investments. For example, a leading automotive manufacturer reported a 20% increase in production output and a 15% reduction in labor costs after implementing robotic welding systems. Similarly, an electronics company saw a 25% improvement in product quality and a 10% reduction in defects after integrating AI-powered vision systems into its production line. These case studies highlight the strong ROI potential of automation in manufacturing, showcasing its ability to deliver both cost savings and improved productivity.
Improved Product Quality and Consistency
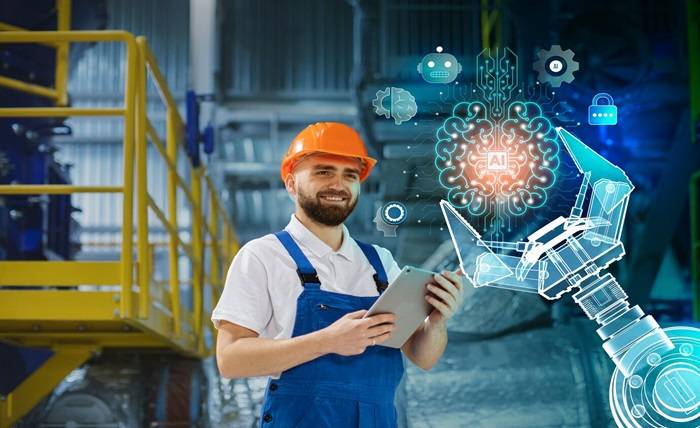
Source: powerthinkers.net
Automation’s impact on manufacturing extends beyond just speed and efficiency; it significantly elevates product quality and consistency. By minimizing human error and implementing rigorous automated quality control, manufacturers can produce products that meet – and often exceed – predefined standards, leading to increased customer satisfaction and brand loyalty. This results in a more reliable and predictable production process, reducing waste and rework.
The inherent variability in human performance is a major source of defects in traditional manufacturing. Fatigue, distraction, and even subtle variations in skill can all lead to inconsistencies in product quality. Automation, however, eliminates these variables. Robots and automated systems perform tasks with unwavering precision and repeatability, consistently adhering to pre-programmed parameters. This leads to a dramatic reduction in defects and a significant improvement in overall product quality.
Automated Quality Control Systems and Consistent Product Standards
Automated quality control (AQC) systems play a pivotal role in ensuring consistent product standards. These systems utilize various technologies, including computer vision, sensors, and machine learning, to inspect products at various stages of the manufacturing process. Instead of relying on manual inspection, which is prone to human error and inconsistencies, AQC systems provide objective and consistent evaluations. For example, a computer vision system can identify even minute imperfections on a surface that might be missed by a human inspector, ensuring only perfect products move on to the next stage. This leads to higher yield rates and reduced waste associated with defective products.
Automated Quality Inspection and Feedback Mechanisms
A typical automated quality inspection process involves several key steps. Imagine a system inspecting car parts for defects.
The flowchart above illustrates a simplified automated quality inspection process. Parts arrive at the inspection station (1), undergo automated testing (2) using various sensors and vision systems. The system analyzes the data (3) comparing it against pre-defined quality parameters. If the part meets standards (4), it proceeds to the next stage of manufacturing. If defects are detected (5), the system flags the part as defective (6), triggering a feedback mechanism that might involve adjustments to the manufacturing process (7) or discarding the defective part (8). This closed-loop system ensures continuous improvement and minimizes the production of substandard products. Real-world examples include automated vision systems in automotive manufacturing, checking for paint imperfections or weld flaws, or automated weight checks in food processing to ensure consistent product size and weight.
Enhanced Safety and Reduced Workplace Hazards
Automation in manufacturing isn’t just about faster production; it’s a game-changer for workplace safety. The inherent risks in many manufacturing processes – from heavy machinery to hazardous materials – are significantly mitigated through the strategic implementation of automated systems. This shift towards automation leads to a healthier and safer work environment, boosting employee morale and reducing the financial burden of workplace accidents.
Hazardous tasks in manufacturing, often involving repetitive strain, exposure to harmful substances, or proximity to dangerous machinery, are prime candidates for automation. Think about the tireless work of welders constantly exposed to intense heat and fumes, or the repetitive motions of assembly line workers potentially leading to carpal tunnel syndrome. Automation steps in, taking over these high-risk activities and allowing human workers to focus on tasks requiring more complex skills and judgment, improving overall safety and reducing the likelihood of injuries.
Smart factories are booming, thanks to automation boosting efficiency and productivity in manufacturing. But this revolution needs lightning-fast connectivity, which is where 5G Technology: What It Means for the Future of Connectivity comes in. 5G’s low latency and high bandwidth are game-changers, enabling real-time data exchange crucial for optimizing automated systems and driving further advancements in manufacturing’s digital transformation.
Automated Systems and Safety Features
Numerous safety features are built into modern automated systems to minimize risks to human operators. These features often include emergency stop mechanisms easily accessible to workers, light curtains and pressure sensors that detect human presence and halt operations if necessary, and robust interlocks preventing machinery from operating unless safety protocols are met. Robotic systems often incorporate advanced sensors and AI-driven collision avoidance systems, minimizing the chance of accidental contact with human workers. Furthermore, automated systems can operate in environments unsuitable for humans, such as extreme temperatures or hazardous chemical exposure, further enhancing overall safety. For example, automated guided vehicles (AGVs) used in warehouses reduce the risk of collisions and injuries associated with manual forklift operation.
Safety Records Comparison: Automated vs. Manual Processes
A direct comparison of safety records between automated and manual processes in high-risk manufacturing environments reveals a clear advantage for automation. While precise figures vary depending on the industry and specific processes, several studies consistently demonstrate a significant reduction in workplace accidents and injuries with the implementation of automated systems. The following points highlight this difference:
- Reduced incidence of repetitive strain injuries (RSIs): Automated systems handling repetitive tasks dramatically lower the occurrence of RSIs, a common ailment in manual assembly lines. Studies have shown a decrease of up to 70% in RSI cases after automation implementation in certain sectors.
- Lower rates of machinery-related accidents: Automated systems with integrated safety features drastically reduce the risk of accidents involving heavy machinery. Data from the National Safety Council, for instance, shows a significant correlation between increased automation and a decrease in machinery-related fatalities and injuries across various industries.
- Minimized exposure to hazardous substances: Automation allows for remote handling of hazardous materials, significantly reducing worker exposure to harmful chemicals and substances. This leads to a considerable decrease in occupational illnesses linked to such exposure.
- Improved overall safety statistics: Overall, comprehensive analyses of safety data from various manufacturing plants show a consistent trend: facilities with higher levels of automation experience significantly lower rates of workplace accidents and injuries compared to those relying heavily on manual labor.
Addressing the Skills Gap and Workforce Reskilling
The automation revolution in manufacturing isn’t just about robots replacing humans; it’s about a fundamental shift in the types of jobs needed. While some roles are indeed displaced, automation simultaneously creates new opportunities requiring different skill sets. Understanding this dynamic and proactively addressing the skills gap is crucial for a smooth transition and a thriving manufacturing sector.
Automation’s impact on employment is complex. Traditional roles involving repetitive, manual tasks are most susceptible to automation. Think assembly line workers performing highly structured, easily programmable actions. These jobs are often replaced by robots, automated systems, and advanced machinery. However, the rise of automation also generates demand for skilled professionals to design, implement, maintain, and manage these sophisticated systems. This includes roles like robotics engineers, data scientists, AI specialists, and cybersecurity experts. The shift isn’t simply about replacing workers; it’s about a metamorphosis of the workforce.
Types of Jobs Created and Displaced by Automation
Automation in manufacturing leads to a shift in job demand. While jobs requiring repetitive manual tasks decline, a need for skilled professionals to operate and maintain automated systems arises. For example, the decline in simple assembly line jobs is offset by the growth in roles such as robotics technicians, programmers specializing in industrial automation software, and data analysts who interpret the massive datasets generated by smart factories. This transition necessitates a focus on reskilling and upskilling initiatives to equip the existing workforce with the competencies needed for these emerging roles. The automotive industry, for instance, has seen a significant decrease in traditional assembly line jobs but a corresponding increase in software engineers and data scientists responsible for autonomous driving systems and predictive maintenance.
Strategies for Reskilling and Upskilling the Manufacturing Workforce
Addressing the skills gap requires a multifaceted approach. One key strategy is investing in robust training programs that equip workers with the necessary technical skills for automation-driven roles. This might involve apprenticeships, vocational training, online courses, and partnerships between educational institutions and manufacturing companies. Furthermore, focusing on soft skills like problem-solving, critical thinking, and adaptability is equally crucial. These skills are transferable and valuable across various roles, making workers more resilient to future technological advancements. Companies can also implement mentorship programs, pairing experienced workers with those undergoing reskilling to facilitate knowledge transfer and practical experience. Government initiatives offering financial incentives for workforce development and training programs can also play a vital role. For example, Germany’s “Industry 4.0” initiative emphasizes comprehensive training programs to support its manufacturing workforce’s adaptation to advanced technologies.
The Role of Education and Training Programs in Preparing Workers for Automation-Driven Roles
Education and training programs are pivotal in bridging the skills gap. Curriculum needs to be updated to incorporate relevant technologies, such as robotics, AI, and data analytics. This requires collaboration between educational institutions and industry leaders to ensure the curriculum aligns with current and future industry needs. Furthermore, programs should emphasize hands-on learning, providing students with practical experience working with automation technologies. Simulations and virtual reality training can also offer valuable opportunities for skill development in a safe and controlled environment. Community colleges and vocational schools play a crucial role in providing accessible and affordable training options, while universities can focus on advanced degrees and research in areas directly relevant to automation in manufacturing. Successful examples include programs that combine classroom instruction with on-the-job training, allowing students to gain practical experience while earning a credential.
The Impact of Automation on Supply Chain Management
Automation is revolutionizing supply chain management, transforming it from a reactive, often opaque system into a proactive, highly visible, and responsive network. This shift allows manufacturers to optimize processes, reduce costs, and ultimately deliver products faster and more efficiently to consumers. The integration of automated systems across the entire supply chain leads to significant improvements in visibility, responsiveness, and overall efficiency.
The implementation of automation technologies drastically improves the efficiency and transparency of the supply chain. Real-time data tracking and analysis provide a clear picture of inventory levels, production progress, and shipment status, enabling better decision-making and faster response to unforeseen events. This increased visibility reduces uncertainty and allows for proactive adjustments to mitigate potential disruptions.
Improved Supply Chain Visibility and Responsiveness
Automated systems, such as RFID tracking, GPS monitoring, and sophisticated software platforms, provide real-time data on the location and status of goods throughout the entire supply chain. This granular level of visibility allows companies to identify bottlenecks, delays, or potential disruptions early on, enabling proactive interventions to minimize their impact. For instance, a manufacturer might use real-time data to reroute shipments around a traffic jam or proactively adjust production schedules to meet unexpected demand. This enhanced responsiveness minimizes delays, reduces waste, and ultimately improves customer satisfaction.
Automated Systems for Optimized Inventory Management and Reduced Lead Times
Automation plays a crucial role in optimizing inventory management. Automated warehouse systems, including automated guided vehicles (AGVs) and robotic picking systems, significantly improve the efficiency of storage, retrieval, and order fulfillment. This reduces storage costs, minimizes the risk of stockouts, and ensures that the right amount of inventory is available at the right time. Furthermore, automated production scheduling and planning systems optimize manufacturing processes, reducing lead times and accelerating product delivery. For example, a company using an automated inventory management system can predict demand fluctuations based on historical data and adjust production accordingly, ensuring sufficient inventory without overstocking.
Automation Enhancing Logistics and Distribution Processes
Automation is transforming logistics and distribution processes through the use of automated guided vehicles (AGVs), automated sorting systems, and advanced transportation management systems (TMS). AGVs move materials efficiently within warehouses and distribution centers, minimizing manual handling and improving speed. Automated sorting systems quickly and accurately sort packages according to destination, streamlining the shipping process. Advanced TMS optimize routes, consolidate shipments, and track deliveries in real-time, ensuring timely and efficient delivery of goods. A prominent example is the use of automated container terminals in major ports, which significantly speed up the unloading and loading of cargo ships, reducing congestion and improving overall efficiency of global shipping.
Cost Considerations and Return on Investment (ROI) of Automation
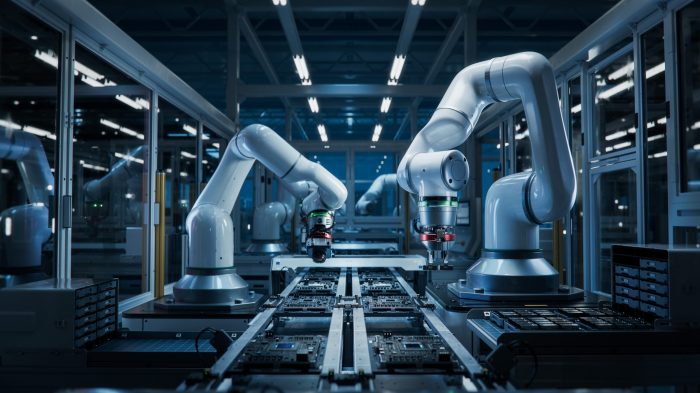
Source: gov.my
Automating your manufacturing processes isn’t a flick of a switch; it’s a significant investment demanding careful consideration of both upfront and ongoing costs. Understanding the financial implications is crucial for making informed decisions and ensuring a successful transition. This section delves into the cost landscape of automation, exploring initial investments, ongoing maintenance, and ultimately, the potential return on investment.
Initial Investment Costs
Implementing automation involves substantial upfront expenses. These costs vary greatly depending on the specific technologies adopted, the scale of the automation project, and the existing infrastructure. Major cost components include the purchase or lease of automated equipment (robots, automated guided vehicles (AGVs), Computer Numerical Control (CNC) machines, etc.), software licenses, integration costs (connecting new systems with existing ones), and the necessary infrastructure upgrades (power, network, safety systems). For instance, a small-scale implementation might involve the purchase of a single robotic arm for a specific task, while a large-scale project could involve a complete overhaul of the production line, requiring millions of dollars in investment. Careful planning and a detailed cost analysis are essential at this stage to avoid unexpected expenses.
Ongoing Maintenance and Operational Expenses
Beyond the initial investment, ongoing costs are an essential part of the total cost of ownership (TCO). These recurring expenses include routine maintenance and repairs of automated systems, software updates and licenses, energy consumption, skilled labor for operation and maintenance, and potential downtime costs. Automated systems, while generally more efficient, require regular maintenance to ensure optimal performance and prevent costly breakdowns. The complexity of the system will dictate the frequency and cost of maintenance, with more sophisticated systems demanding more frequent and specialized attention. Similarly, software updates are essential for security and performance, adding to the ongoing operational costs.
Comparative Analysis of Total Cost of Ownership (TCO)
The following table provides a hypothetical comparison of the TCO for automated versus manual processes over a 5-year period. Note that these figures are illustrative and will vary significantly based on specific circumstances. The ROI calculation assumes a consistent level of production and incorporates factors such as increased output, reduced labor costs, and improved product quality.
Year | Manual Cost (USD) | Automated Cost (USD) | ROI (USD) |
---|---|---|---|
1 | 100,000 | 250,000 | -150,000 |
2 | 100,000 | 120,000 | -20,000 |
3 | 100,000 | 110,000 | 10,000 |
4 | 100,000 | 105,000 | 15,000 |
5 | 100,000 | 100,000 | 20,000 |
Note: This table represents a simplified example. Actual costs will vary depending on factors such as production volume, labor rates, equipment costs, and maintenance requirements. A thorough cost-benefit analysis should be conducted before implementing automation.
Ethical Considerations and the Future of Automation in Manufacturing: The Role Of Automation In Transforming Manufacturing Industries
The rise of automation in manufacturing presents a compelling narrative of progress, but it’s not without its shadows. While boosting efficiency and productivity, the transformative power of robots and AI also raises crucial ethical questions, particularly concerning the human element – the workers whose jobs might be displaced, and the potential widening of the existing economic inequality. Navigating this complex landscape requires a proactive and responsible approach, ensuring that the benefits of automation are shared equitably and that the transition is managed fairly.
Job Displacement and Workforce Inequality
The automation of manufacturing processes inevitably leads to job displacement in certain sectors. This isn’t a new phenomenon; technological advancements have always reshaped the job market. However, the scale and speed of automation’s impact are unprecedented. The concern isn’t just about the loss of jobs; it’s about the unequal distribution of that loss. Low-skilled workers are often disproportionately affected, exacerbating existing inequalities. This can lead to social unrest, increased poverty, and a widening gap between the wealthy and the working class. Addressing this requires proactive measures such as robust reskilling and upskilling programs, government support for displaced workers, and a focus on creating new, higher-skilled jobs in the evolving manufacturing landscape. Companies themselves have a crucial role to play in providing training and support for their employees during this transition.
Responsible Automation Implementation for Fairness and Equity
Responsible automation implementation hinges on a multi-pronged strategy. Firstly, it demands transparent and open communication between companies, governments, and workers. This ensures that the potential impacts of automation are understood and addressed proactively. Secondly, investments in education and training are paramount. This includes equipping workers with the skills needed for the new jobs created by automation, as well as providing support for those whose jobs are displaced. Thirdly, ethical guidelines and regulations are needed to ensure fairness and equity. These guidelines could address issues such as algorithmic bias, data privacy, and the appropriate level of human oversight in automated systems. Finally, a focus on creating a just transition for affected workers is crucial, involving social safety nets, income support, and opportunities for retraining and re-employment. Examples of responsible implementation include companies partnering with educational institutions to offer reskilling programs and governments providing financial assistance to workers undergoing retraining.
Future Trends and Advancements in Manufacturing Automation
The future of manufacturing automation is brimming with exciting possibilities. We can expect to see a convergence of technologies, leading to even more sophisticated and efficient automated systems. Artificial intelligence (AI) will play an increasingly crucial role, enabling machines to learn, adapt, and make decisions with minimal human intervention. Robotics will become more advanced, with robots capable of performing more complex tasks and collaborating more effectively with human workers. The Internet of Things (IoT) will further enhance connectivity and data analysis, allowing for real-time monitoring and optimization of manufacturing processes. Additive manufacturing (3D printing) will become more widespread, enabling the production of customized products on demand. Furthermore, the use of augmented and virtual reality (AR/VR) will improve training, maintenance, and remote collaboration.
A Futuristic Automated Factory: A Descriptive Illustration
Imagine a futuristic automated factory, a gleaming testament to technological prowess. Rows of collaborative robots (cobots) work alongside human technicians, seamlessly integrating human expertise with robotic precision. AI-powered systems monitor every aspect of the production process, optimizing efficiency and predicting potential issues before they arise. 3D printers create customized components on demand, minimizing waste and maximizing flexibility. Augmented reality overlays provide real-time data and instructions to technicians, guiding them through complex tasks. The factory floor is a symphony of coordinated movements, a ballet of human ingenuity and technological sophistication. Data is collected and analyzed in real-time, informing decisions about production scheduling, resource allocation, and even product design. The entire operation is powered by renewable energy sources, minimizing its environmental impact. This futuristic factory represents not only a leap in manufacturing efficiency but also a model for responsible and sustainable automation. The integration of human workers and advanced technologies fosters a collaborative and equitable environment, showcasing the potential for automation to enhance, not replace, human capabilities.
Final Review
The automation revolution in manufacturing isn’t just a trend; it’s a fundamental shift. While challenges like workforce adaptation and ethical considerations remain, the potential benefits – increased efficiency, improved quality, enhanced safety, and optimized supply chains – are undeniable. Embracing automation strategically, with a focus on reskilling and responsible implementation, will be crucial for manufacturers to thrive in this new era. The future of manufacturing is automated, and it’s brighter than ever.