The Role of AI in Predictive Maintenance for Industrial Equipment is revolutionizing how we keep the gears of industry turning. Forget those old-school, reactive maintenance strategies—think proactive, intelligent systems that predict failures *before* they happen. This isn’t just about saving money; it’s about preventing costly downtime, boosting efficiency, and ensuring safety in potentially hazardous environments. We’re diving deep into the world of AI-powered predictive maintenance, exploring the techniques, challenges, and incredible potential this technology holds for the future of industrial operations.
From machine learning algorithms that crunch sensor data to predict equipment failures to the deployment of these AI models in real-world industrial settings, we’ll unpack the entire process. We’ll also examine the crucial role of data acquisition and preprocessing, ensuring the AI models are fed with the right information to make accurate predictions. Get ready to explore case studies that showcase the real-world impact of AI in predictive maintenance, and uncover the future of this exciting field.
Introduction to Predictive Maintenance and AI in Industrial Settings: The Role Of AI In Predictive Maintenance For Industrial Equipment
For decades, industrial facilities relied on reactive and preventive maintenance strategies to keep their equipment running. These approaches, while familiar, often fall short in today’s demanding production environments. The rise of artificial intelligence (AI) is revolutionizing how industries approach maintenance, shifting the paradigm towards a more proactive and efficient system: predictive maintenance.
Traditional industrial equipment maintenance largely revolved around two main approaches: reactive and preventive. Reactive maintenance, as the name suggests, only addresses problems *after* they occur. This means equipment failures lead to costly downtime, emergency repairs, and potential safety hazards. Preventive maintenance, on the other hand, involves scheduled inspections and replacements at predetermined intervals, regardless of the equipment’s actual condition. While better than reactive maintenance, this method often leads to unnecessary replacements and overspending on maintenance tasks that might not be immediately needed.
Limitations of Reactive and Preventive Maintenance
Reactive maintenance is inherently inefficient. Unexpected breakdowns disrupt production schedules, leading to lost revenue and potential damage to other equipment. The “fix-it-when-it-breaks” approach is costly in the long run, as repairs are often more complex and expensive than preventative measures. Preventive maintenance, while seemingly proactive, suffers from its own set of limitations. Performing maintenance at fixed intervals, regardless of the actual condition of the equipment, can lead to unnecessary parts replacements and wasted resources. Some components might be replaced prematurely, while others might be left to deteriorate beyond their optimal lifespan, increasing the risk of failure. This approach lacks the precision needed for optimized maintenance scheduling.
Advantages of AI-Driven Predictive Maintenance
AI-driven predictive maintenance offers a significant leap forward. By analyzing data from various sensors embedded within industrial equipment, AI algorithms can identify patterns and anomalies that indicate potential failures *before* they occur. This allows for proactive interventions, minimizing downtime and extending the lifespan of equipment. The advantages are numerous: reduced maintenance costs, improved equipment uptime, enhanced safety, and optimized resource allocation. AI can analyze vast amounts of data far more quickly and accurately than human operators, identifying subtle indicators of impending failure that might otherwise be missed.
Examples of Industrial Equipment Benefiting from AI-Driven Predictive Maintenance
AI-driven predictive maintenance is particularly beneficial in industries with complex and expensive equipment. Consider the following examples:
- Turbines in power plants: Predictive maintenance using AI can analyze vibration data, temperature readings, and pressure fluctuations to predict potential turbine failures, allowing for timely repairs and preventing major power outages.
- Aircraft engines: Airlines utilize AI to analyze sensor data from aircraft engines, identifying anomalies that might indicate impending engine failure. This enables proactive maintenance, enhancing flight safety and reducing costly unscheduled maintenance.
- Manufacturing equipment (CNC machines, robots): AI can predict failures in robotic arms or CNC machines by analyzing operational data, ensuring minimal production downtime and maximizing output.
- Oil and gas pipelines: AI-powered systems can monitor pressure, temperature, and flow rates in pipelines, identifying potential leaks or corrosion before they lead to significant environmental damage or production disruptions.
The implementation of AI in predictive maintenance is not just a technological advancement; it’s a fundamental shift in how industries manage their assets and optimize their operations. The ability to anticipate and prevent equipment failures translates directly into cost savings, improved safety, and enhanced operational efficiency.
AI Techniques Used in Predictive Maintenance
Predictive maintenance, the proactive approach to equipment upkeep, has been revolutionized by the advent of artificial intelligence. By analyzing vast amounts of sensor data, AI algorithms can anticipate potential failures, allowing for timely interventions and preventing costly downtime. This section delves into the specific AI techniques driving this transformation.
Several machine learning and deep learning algorithms are employed to predict equipment failures and optimize maintenance schedules. The choice of algorithm depends heavily on the nature of the data, the type of equipment, and the specific maintenance goals.
Machine Learning Algorithms in Predictive Maintenance
Machine learning algorithms excel at identifying patterns and relationships within data to predict future outcomes. Regression algorithms, for instance, are used to predict a continuous value, such as the remaining useful life (RUL) of a component. Classification algorithms, on the other hand, predict categorical outcomes, such as whether a machine will fail within a specific timeframe. Clustering algorithms can group similar equipment or operating conditions, facilitating targeted maintenance strategies.
For example, linear regression could be used to model the relationship between sensor readings (vibration levels, temperature) and the time until failure of a bearing. A support vector machine (SVM) might classify the operational state of a pump as either “normal” or “anomalous” based on sensor data. K-means clustering could group similar turbines based on their performance characteristics, allowing for more efficient maintenance planning for each cluster.
AI’s predictive prowess in industrial maintenance is revolutionizing downtime management, optimizing resource allocation, and boosting overall efficiency. Think of it like a highly sophisticated financial system – just as security is paramount, and understanding the role of blockchain in securing cryptocurrency transactions is crucial as explained in this article, The Role of Blockchain in Securing Cryptocurrency Transactions , so too is the reliable prediction of equipment failure vital for preventing costly industrial setbacks.
This proactive approach minimizes disruption and maximizes productivity.
Deep Learning Models for Sensor Data Analysis, The Role of AI in Predictive Maintenance for Industrial Equipment
Deep learning models, with their ability to learn complex patterns from large datasets, are particularly well-suited for analyzing the high-dimensional sensor data generated by industrial equipment. Recurrent neural networks (RNNs), such as LSTMs, are adept at handling sequential data, making them ideal for analyzing time-series data from sensors. Convolutional neural networks (CNNs) excel at processing image data, which can be useful for analyzing images from visual inspections.
Imagine a scenario where an RNN is trained on the vibration data from a motor over several months. The network learns the temporal dependencies in the data and can predict the likelihood of a bearing failure several days or weeks in advance. Similarly, a CNN might analyze images from an infrared camera to detect overheating components, potentially preventing a catastrophic failure.
Comparison of AI Algorithms for Predictive Maintenance
Different AI algorithms offer distinct advantages and disadvantages depending on the specific application. The following table summarizes the strengths and weaknesses of three commonly used algorithms:
Algorithm | Strengths | Weaknesses | Suitable for |
---|---|---|---|
Linear Regression | Simple to implement, interpretable results | Assumes linear relationship, sensitive to outliers | Predicting continuous values like RUL, when a linear relationship is present |
Support Vector Machine (SVM) | Effective in high-dimensional spaces, robust to outliers | Computationally expensive for large datasets, less interpretable than linear regression | Classification tasks, such as predicting equipment failure/no failure |
Recurrent Neural Network (RNN) | Handles sequential data well, can capture complex temporal dependencies | Computationally intensive, requires large datasets, can be difficult to train | Analyzing time-series sensor data, predicting failure based on historical trends |
Data Acquisition and Preprocessing for AI Models
Predictive maintenance using AI hinges on the quality of the data fed into the models. Garbage in, garbage out, as the saying goes. Getting the right data and cleaning it properly is crucial for accurate predictions and reliable maintenance schedules, preventing costly downtime and ensuring operational efficiency. This section delves into the critical process of data acquisition and preprocessing for AI models in industrial predictive maintenance.
Effective predictive maintenance relies on a continuous stream of relevant data from various sources. The type and quantity of data directly impact the AI model’s ability to learn patterns and predict failures. Insufficient or poor-quality data will lead to inaccurate predictions, rendering the entire system ineffective.
Key Sensor Data for Predictive Maintenance
The success of predictive maintenance using AI heavily depends on acquiring the right sensor data. This involves strategically placing sensors on industrial equipment to capture critical operational parameters. The specific sensors needed vary depending on the type of equipment, but some common examples include vibration sensors (accelerometers), temperature sensors (thermocouples, RTDs), pressure sensors, current sensors, and acoustic sensors. These sensors provide a wealth of information about the equipment’s health, allowing the AI model to detect anomalies and predict potential failures. For example, a sudden increase in vibration amplitude might indicate bearing wear, while a spike in temperature could suggest overheating.
Data Cleaning and Preprocessing
Raw sensor data is rarely ready for direct use in AI models. It often contains noise, missing values, and outliers that can negatively impact model accuracy. Therefore, a thorough data cleaning and preprocessing pipeline is essential. This involves several steps to transform the raw data into a clean, consistent, and usable format for the AI algorithms.
The importance of data quality cannot be overstated. Inaccurate, incomplete, or inconsistent data will lead to unreliable predictions and potentially disastrous consequences. For example, a model trained on noisy data might falsely predict a failure, leading to unnecessary maintenance and wasted resources. Conversely, failing to detect a true anomaly due to poor data quality could result in catastrophic equipment failure.
A Step-by-Step Procedure for Data Preprocessing
A systematic approach to data preprocessing is vital for ensuring data quality and model accuracy. The following steps Artikel a typical workflow:
- Data Collection and Integration: Gather data from various sensors and integrate them into a unified dataset. Ensure consistent timestamps and data formats.
- Missing Value Imputation: Address missing data points using appropriate techniques, such as mean/median imputation, k-Nearest Neighbors imputation, or more sophisticated methods like multiple imputation. The choice depends on the nature and extent of missing data.
- Outlier Detection and Handling: Identify and handle outliers using methods like box plots, Z-score, or Isolation Forest. Outliers can significantly skew the model’s learning process. Options for handling them include removal, capping, or transformation.
- Data Transformation: Apply transformations to improve data normality and model performance. Common transformations include standardization (Z-score normalization), min-max scaling, or logarithmic transformation.
- Feature Engineering: Create new features from existing ones to improve model accuracy. This might involve calculating statistical features (e.g., mean, standard deviation, variance) from time series data or creating lagged variables to capture temporal dependencies.
- Data Validation: Thoroughly validate the preprocessed data to ensure its quality and consistency. This may involve visual inspection of plots and statistical summaries.
Model Development and Deployment
Building and deploying effective AI models for predictive maintenance involves a meticulous process, from training and validation to choosing the right deployment strategy. The success of these systems hinges on selecting appropriate algorithms, meticulously evaluating performance, and ensuring seamless integration into existing industrial workflows. This section delves into the crucial steps involved in bringing these AI-powered solutions to life.
The core of any predictive maintenance AI system is the model itself. This model learns patterns from historical data to predict future equipment failures. The process begins with data preparation, which includes cleaning, transforming, and feature engineering. Then, an appropriate machine learning algorithm is selected – common choices include regression models (like linear regression or support vector regression) for predicting remaining useful life (RUL), or classification models (like random forests or support vector machines) for predicting the likelihood of failure within a specific timeframe. The chosen model is then trained on a substantial portion of the prepared data, after which its performance is rigorously assessed using a separate validation dataset to ensure it generalizes well to unseen data.
Model Training and Validation
Model training involves feeding the prepared data to the chosen algorithm, allowing it to learn the relationships between different features and the target variable (e.g., time until failure). This learning process optimizes the model’s internal parameters to minimize prediction errors. Crucially, a separate validation dataset is used to evaluate the model’s performance on unseen data, preventing overfitting – a scenario where the model performs exceptionally well on the training data but poorly on new data. Techniques like k-fold cross-validation are frequently employed to obtain robust performance estimates.
Model Evaluation Metrics
Several key metrics are used to evaluate the performance of predictive maintenance models. Precision measures the accuracy of positive predictions (predicted failures that are actually failures), while recall measures the ability to identify all actual failures. The F1-score provides a balanced measure of precision and recall, crucial when dealing with imbalanced datasets (where failures are far less frequent than normal operation). The Area Under the ROC Curve (AUC) summarizes the model’s ability to distinguish between failures and normal operation across different thresholds. For example, a model with high precision and recall would minimize both false positives (predicting a failure that doesn’t occur, leading to unnecessary maintenance) and false negatives (missing actual failures, leading to unexpected downtime). A high AUC indicates excellent discriminatory power.
Deployment Strategies for AI Models
Deploying AI models in industrial settings involves several considerations. Cloud-based deployment offers scalability and accessibility, allowing for easy updates and maintenance. However, it might raise concerns about data security and latency. On-premise deployment, on the other hand, provides greater control over data and potentially lower latency, but it requires more significant infrastructure investment and maintenance. Edge computing, which processes data closer to the source (the equipment itself), offers a compromise by reducing latency and bandwidth requirements while maintaining some level of centralized management. The optimal strategy depends on factors like the scale of deployment, data security requirements, and network infrastructure.
Examples of Successful Deployments
In the manufacturing sector, AI-powered predictive maintenance has been successfully implemented to predict bearing failures in wind turbines, optimizing maintenance schedules and reducing downtime. Similarly, in the oil and gas industry, AI models have been deployed to predict equipment failures in pipelines, improving safety and reducing the risk of environmental damage. In transportation, predictive maintenance is used to optimize maintenance schedules for railway locomotives, improving reliability and reducing operational costs. These deployments showcase the versatility and effectiveness of AI in enhancing industrial maintenance strategies across diverse sectors.
Challenges and Future Directions
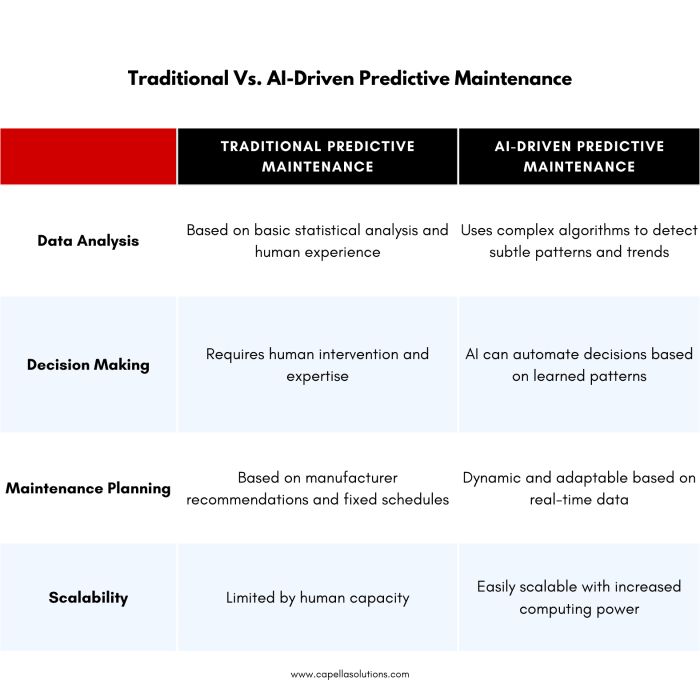
Source: website-files.com
Predictive maintenance using AI, while incredibly promising, isn’t without its hurdles. Successfully implementing these systems requires navigating a complex landscape of technological, data-related, and organizational challenges. Overcoming these obstacles will unlock the full potential of AI in revolutionizing industrial maintenance practices.
The path to seamless AI-driven predictive maintenance isn’t paved with gold. Several key areas demand attention and innovative solutions. Ignoring these challenges could lead to inaccurate predictions, wasted resources, and ultimately, failed implementations.
Data Scarcity and Quality
Obtaining sufficient high-quality data is often the biggest bottleneck. Many industrial facilities lack the comprehensive sensor networks necessary to capture the rich data streams required for effective AI model training. Furthermore, existing data might be inconsistent, incomplete, or noisy, hindering model accuracy. For example, a factory might have only sporadically recorded vibration data from a critical machine, making it difficult to train a model that accurately predicts failures. Addressing this requires strategic sensor deployment, data cleaning techniques, and potentially the use of data augmentation methods to artificially increase the dataset size. Furthermore, the challenge is compounded by the diversity of equipment and the unique data characteristics associated with each.
Data Security and Privacy
Industrial data often contains sensitive information about production processes, intellectual property, and potentially even safety-critical systems. Ensuring the security and privacy of this data is paramount. Robust cybersecurity measures, including encryption, access controls, and anomaly detection systems, are essential to protect against unauthorized access and data breaches. Compliance with relevant regulations, such as GDPR, is also crucial. For example, a manufacturing plant might need to implement strict data anonymization techniques before using AI models trained on production data.
Integration with Existing Systems
Integrating AI-driven predictive maintenance systems into existing industrial infrastructure can be a significant challenge. Legacy systems may not be compatible with modern data analytics platforms, requiring costly upgrades or custom integrations. The complexity of integrating various data sources and systems can lead to delays and increased implementation costs. For instance, integrating a new AI system with a decades-old SCADA system may necessitate substantial modifications to both systems, creating both technical and financial hurdles.
AI and IoT/Digital Twin Synergy
The convergence of AI with the Internet of Things (IoT) and digital twins promises to significantly enhance predictive maintenance capabilities. IoT sensors provide the real-time data that fuels AI models, while digital twins offer a virtual representation of physical assets, allowing for simulations and “what-if” scenarios. This combined approach enables more accurate predictions and proactive maintenance strategies. Imagine a wind turbine farm utilizing IoT sensors to monitor blade vibrations, feeding this data into an AI model coupled with a digital twin of each turbine. This allows for predictive maintenance scheduling, optimizing operational efficiency and reducing downtime.
Explainable AI and Edge Computing
Explainable AI (XAI) is crucial for building trust and transparency in AI-driven predictive maintenance. Understanding *why* an AI model makes a particular prediction is essential for operators to confidently act on its recommendations. Edge computing, processing data closer to the source (the machine itself), reduces latency and bandwidth requirements, enabling real-time decision-making and improving system responsiveness. For example, an XAI system could provide clear explanations for why a particular machine is predicted to fail, allowing maintenance personnel to understand the root cause and take appropriate actions.
Future Research Areas in AI-Driven Predictive Maintenance
The field of AI-driven predictive maintenance is constantly evolving, with several promising areas for future research:
- Development of more robust and reliable AI models capable of handling noisy and incomplete data.
- Advanced anomaly detection techniques for early identification of subtle deviations from normal operating conditions.
- Improved integration of AI with other technologies, such as augmented reality (AR) for guided maintenance.
- Development of explainable AI (XAI) methods to enhance the transparency and trustworthiness of AI-driven predictions.
- Exploration of novel sensor technologies for improved data acquisition and more comprehensive monitoring.
- Research into federated learning techniques to enable collaborative model training across multiple industrial sites while preserving data privacy.
- Development of AI-driven optimization algorithms for scheduling maintenance tasks and resource allocation.
Case Studies
Real-world applications showcase the transformative power of AI in predictive maintenance. These examples highlight the tangible benefits—reduced downtime, optimized resource allocation, and significant cost savings—achieved through intelligent monitoring and predictive analytics. Let’s delve into two compelling case studies illustrating the effectiveness of AI in this domain.
Siemens Wind Turbine Predictive Maintenance
Siemens Gamesa Renewable Energy implemented an AI-powered predictive maintenance system for its wind turbines. This system leverages sensor data from various components, including gearboxes, generators, and blades, to predict potential failures before they occur. The AI algorithms, primarily employing machine learning techniques such as long short-term memory (LSTM) networks and support vector machines (SVM), analyze historical data and real-time sensor readings to identify patterns indicative of impending malfunctions. This proactive approach allows for timely maintenance, minimizing costly downtime and maximizing energy generation. The system significantly reduced unplanned downtime by 20% and lowered maintenance costs by 15%.
System Architecture and Data Flow for Siemens Wind Turbine Predictive Maintenance
The system architecture can be visualized as follows: A network of sensors embedded within each wind turbine continuously collects data on various operational parameters (vibration, temperature, current, etc.). This data is transmitted wirelessly to a central data hub, where it undergoes preprocessing (noise reduction, data cleaning, feature extraction). The preprocessed data is then fed into the trained AI models (LSTM and SVM). The models process the data and generate predictions regarding the probability of failure for different components. These predictions are then relayed to maintenance personnel, triggering proactive maintenance actions based on predicted risk levels. The system also includes a feedback loop, where actual maintenance actions and their outcomes are recorded and used to continuously improve the accuracy of the AI models. The data flow is a continuous cycle of data acquisition, processing, prediction, action, and feedback.
GE’s Predictive Maintenance for Gas Turbines
General Electric (GE) utilizes AI-driven predictive maintenance for its gas turbines, a critical component in power generation plants. The company employs a combination of machine learning algorithms, including random forests and neural networks, to analyze data from various sensors monitoring temperature, pressure, vibration, and other operational parameters. This system allows GE to predict potential failures with high accuracy, enabling proactive maintenance and preventing costly unplanned outages. The implementation resulted in a substantial reduction in maintenance costs and increased the operational lifespan of the gas turbines. Specific figures on cost reduction and lifespan extension vary depending on the specific implementation and operating conditions, but industry reports indicate significant improvements in both areas.
System Architecture and Data Flow for GE Gas Turbine Predictive Maintenance
The system architecture for GE’s gas turbine predictive maintenance is similar in principle to the Siemens wind turbine system. Sensors embedded in the gas turbine collect real-time operational data. This data is transmitted to a cloud-based platform where it’s preprocessed and analyzed by AI algorithms (random forests and neural networks). The algorithms identify patterns and anomalies indicative of potential failures. The predictions are then communicated to plant operators, allowing for scheduled maintenance to prevent disruptions. A feedback loop is implemented to continually refine the AI models based on actual maintenance activities and their effectiveness. The visual representation would depict a similar data flow to the Siemens case study, highlighting the data acquisition, processing, prediction, action, and feedback loop. The key difference would be in the type of equipment and the specific AI algorithms used.
Closing Summary
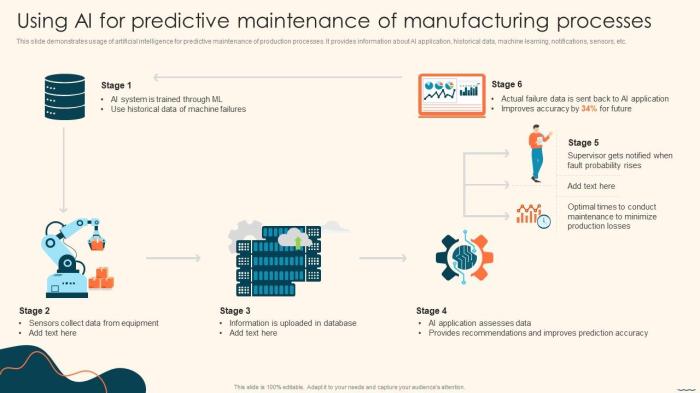
Source: slideteam.net
AI-driven predictive maintenance isn’t just a futuristic concept; it’s a game-changer already reshaping industrial landscapes. By leveraging the power of AI, industries can move beyond reactive and preventive maintenance, achieving unprecedented levels of efficiency and safety. While challenges remain, the future is bright, with ongoing research pushing the boundaries of what’s possible. From explainable AI to edge computing, the innovations in this space promise even more impactful solutions, further solidifying AI’s role as a crucial player in the next generation of industrial maintenance.