The Role of AI in Advancing Predictive Maintenance in Manufacturing is no longer a futuristic fantasy; it’s the present reality reshaping how factories operate. Forget those days of reactive maintenance, scrambling to fix broken machinery after the fact. AI is changing the game, predicting potential failures *before* they happen, saving companies time, money, and a whole lot of headaches. This revolution leverages the power of machine learning and deep learning algorithms to analyze massive datasets from sensors, logs, and historical records, uncovering hidden patterns that signal impending equipment trouble. Think of it as giving your factory a crystal ball, but instead of predicting the future, it predicts the next machine breakdown.
This deep dive explores how various AI techniques are applied, the crucial role of data, the challenges of implementation, and the exciting future possibilities of AI-powered predictive maintenance. From identifying the best AI algorithms for specific manufacturing scenarios to mastering the art of data preprocessing, we’ll cover it all. We’ll even look at real-world examples showcasing the tangible benefits of this technology – think reduced downtime, increased efficiency, and significantly lower maintenance costs.
Introduction to Predictive Maintenance and AI in Manufacturing
The manufacturing world, once ruled by reactive and preventative maintenance schedules, is undergoing a significant transformation. For decades, factories relied on fixing problems as they arose (reactive) or adhering to strict, pre-determined maintenance cycles (preventative), often leading to unnecessary downtime or unexpected breakdowns. The rise of predictive maintenance, powered by Artificial Intelligence, is changing this landscape dramatically, offering a more efficient and cost-effective approach.
Predictive maintenance uses data analysis to predict when equipment is likely to fail, allowing for proactive interventions before problems occur. This contrasts sharply with traditional methods, offering significant advantages in terms of efficiency and cost savings.
Traditional Maintenance Approaches in Manufacturing
Traditional maintenance strategies, primarily reactive and preventative, have inherent limitations. Reactive maintenance, involving fixing equipment only after failure, leads to unexpected downtime, lost production, and potentially costly repairs. Preventative maintenance, while better, involves scheduled maintenance at fixed intervals, regardless of the actual condition of the equipment. This can lead to unnecessary maintenance, wasting resources and potentially causing disruptions when scheduled maintenance conflicts with peak production periods. For example, a factory might shut down an entire production line for a scheduled overhaul, even if some components are still functioning perfectly. This represents lost production time and labor costs.
Limitations of Traditional Maintenance Approaches
The limitations of traditional methods are clear. Reactive maintenance results in unpredictable disruptions, impacting production schedules and customer satisfaction. Preventative maintenance, while aiming for reliability, often results in over-maintenance, leading to wasted resources and potential inefficiencies. Both approaches lack the precision and optimization offered by predictive maintenance. Consider a scenario where a critical component requires replacement only after a specific wear threshold is reached; preventative maintenance might replace it prematurely, while reactive maintenance would cause a complete shutdown.
Benefits of Implementing Predictive Maintenance Strategies
Predictive maintenance offers a compelling alternative. By leveraging data from sensors and other sources, it anticipates potential failures, allowing for timely repairs and minimizing downtime. This translates into significant cost savings through reduced repair costs, increased equipment lifespan, and optimized production schedules. Further benefits include improved safety, as potential hazards are identified and addressed before they escalate, and enhanced resource allocation, ensuring maintenance resources are used efficiently. A well-implemented predictive maintenance program can lead to a significant reduction in unplanned downtime, which can represent millions of dollars in savings for large manufacturing facilities.
AI’s Enhancement of Predictive Maintenance
Artificial intelligence plays a pivotal role in enabling predictive maintenance. AI algorithms, particularly machine learning, can analyze vast amounts of data from various sources—sensor readings, operational logs, historical maintenance records—to identify patterns and predict equipment failures with remarkable accuracy. This capability allows for proactive maintenance scheduling, minimizing disruptions and optimizing resource allocation. For instance, AI can analyze vibration data from a machine to predict bearing failure days or even weeks in advance, allowing for a scheduled replacement during a planned downtime period, avoiding costly emergency repairs and production halts. AI’s ability to learn and adapt from new data also means that the predictive models constantly improve over time, becoming more accurate and reliable.
AI Techniques Used in Predictive Maintenance: The Role Of AI In Advancing Predictive Maintenance In Manufacturing
Predictive maintenance, the holy grail of manufacturing efficiency, is getting a serious upgrade thanks to artificial intelligence. AI’s ability to analyze vast amounts of data and identify patterns invisible to the human eye is revolutionizing how we predict and prevent equipment failures. This section dives into the specific AI techniques driving this transformation.
Machine Learning Algorithms in Predictive Maintenance
Machine learning (ML) algorithms form the backbone of many predictive maintenance systems. These algorithms learn from historical data to build predictive models, enabling proactive maintenance scheduling and minimizing downtime. Different algorithms excel at different tasks. Regression models, for instance, predict a continuous value, such as the remaining useful life (RUL) of a machine component. Classification algorithms, on the other hand, categorize data into discrete classes, like “failure imminent” or “functioning normally.” Clustering algorithms can group similar machines or components together, allowing for more targeted maintenance strategies. For example, a regression model might predict the exact number of operating hours before a motor fails, while a classification model might flag a sensor reading as indicating a high probability of an impending bearing failure.
Deep Learning Models for Predictive Maintenance
Deep learning, a subset of machine learning, leverages artificial neural networks with multiple layers to extract complex features from data. This allows for more accurate predictions, especially when dealing with noisy or high-dimensional data, common in industrial settings. Recurrent Neural Networks (RNNs) are particularly useful for analyzing time-series data, such as sensor readings collected over time, to identify patterns indicative of impending failure. Convolutional Neural Networks (CNNs), known for their prowess in image processing, can be applied to analyze images from machine vision systems to detect anomalies or signs of wear and tear. For example, a CNN might analyze images from a thermal camera to detect overheating in a motor, a key indicator of potential failure. RNNs, meanwhile, could analyze vibration sensor data over time to predict bearing failure.
Comparison of AI Algorithms for Predicting Equipment Failures
Choosing the right AI algorithm is crucial for effective predictive maintenance. The best choice depends on the specific application, data characteristics, and desired outcomes. Some algorithms are more computationally intensive than others, requiring more powerful hardware and longer processing times. The accuracy and interpretability of the results also vary significantly across different algorithms.
Algorithm | Strengths | Weaknesses | Manufacturing Context Example |
---|---|---|---|
Linear Regression | Simple, fast, interpretable | Assumes linear relationship, sensitive to outliers | Predicting energy consumption based on machine load |
Support Vector Machine (SVM) | Effective in high-dimensional spaces, versatile | Can be computationally expensive for large datasets, parameter tuning can be complex | Classifying sensor readings as normal or abnormal |
Random Forest | Robust to outliers, high accuracy | Can be less interpretable than linear models | Predicting the probability of a pump failure |
Recurrent Neural Network (RNN) | Excellent for time-series data, can capture complex patterns | Computationally intensive, requires large datasets for training | Predicting bearing failure based on vibration data |
Data Acquisition and Preprocessing for AI-Driven Predictive Maintenance
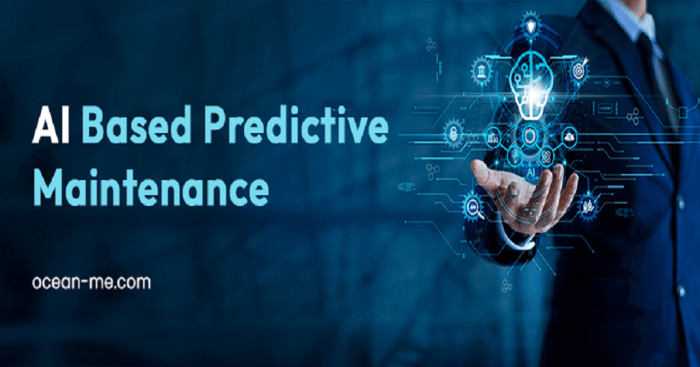
Source: ocean-me.com
AI’s predictive prowess in manufacturing is revolutionizing maintenance, minimizing downtime and boosting efficiency. This data-driven approach mirrors the larger trend of leveraging data science to anticipate future scenarios, as explored in this insightful article: Exploring the Role of Data Science in Predicting Global Trends. Ultimately, the ability to foresee potential equipment failures, just like predicting global market shifts, relies on sophisticated algorithms and the power of big data analysis.
Predictive maintenance using AI hinges on the quality and quantity of data fed into the system. Garbage in, garbage out, as the saying goes. This section explores the crucial steps of data acquisition and preprocessing, laying the groundwork for accurate and reliable predictive models. Getting this right is paramount for successful implementation.
Data acquisition for AI-driven predictive maintenance involves gathering information from various sources within a manufacturing environment. The success of the AI model directly depends on the completeness and reliability of this data.
Key Data Sources for Predictive Maintenance
Manufacturing facilities generate a wealth of data relevant to predictive maintenance. These data sources provide insights into equipment performance and potential failures, enabling proactive maintenance strategies. Effective data acquisition involves strategically selecting and integrating these diverse sources.
- Sensor Data: Sensors embedded in machinery continuously monitor various parameters like temperature, vibration, pressure, and current. This real-time data provides crucial indicators of equipment health.
- Machine Logs: Operational logs from machines record events, errors, and performance metrics. Analyzing these logs can reveal patterns indicative of impending failures.
- Historical Maintenance Records: Past maintenance activities, including repair times, replacement parts, and associated costs, offer valuable context for understanding equipment lifespan and failure modes. This historical data provides a baseline for comparison with current sensor readings and operational logs.
- Environmental Data: Factors such as ambient temperature and humidity can significantly influence equipment performance and failure rates. Incorporating environmental data can improve the accuracy of predictive models.
Data Cleaning and Preprocessing
Raw data acquired from various sources is often messy and incomplete, requiring extensive cleaning and preprocessing before it can be used to train AI models. This stage is critical for ensuring the accuracy and reliability of predictions.
- Handling Missing Data: Missing data points are common and can be addressed using various imputation techniques, such as mean/median imputation, k-nearest neighbors imputation, or more sophisticated methods like multiple imputation. The choice depends on the nature and extent of missing data.
- Outlier Detection and Treatment: Outliers, data points significantly deviating from the norm, can skew model training. Techniques like box plots, scatter plots, and statistical methods like the Z-score can help identify outliers. Treatment strategies include removal, transformation (e.g., logarithmic transformation), or winsorization (capping outliers at a certain percentile).
- Data Transformation: Raw data may need transformation to improve model performance. Techniques like normalization (scaling data to a specific range) or standardization (centering data around zero with unit variance) are commonly used.
- Feature Engineering: This involves creating new features from existing ones to improve model accuracy. For example, combining sensor readings to create a composite health index or calculating rolling averages to smooth out noisy data.
- Data Consistency and Format: Ensuring data consistency across different sources is essential. This involves standardizing data formats, units, and naming conventions.
Challenges Associated with Data Quality and its Impact on Model Accuracy
Data quality significantly influences the accuracy and reliability of AI-driven predictive maintenance models. Poor data quality can lead to inaccurate predictions, resulting in ineffective maintenance strategies and increased downtime.
- Inconsistent Data: Inconsistent data formats, units, or naming conventions can lead to errors and inconsistencies in analysis.
- Incomplete Data: Missing data points can limit the ability to build accurate predictive models. Imputation techniques can help, but they can also introduce bias.
- Noisy Data: Sensor noise and other sources of error can obscure underlying patterns and lead to inaccurate predictions. Data smoothing techniques can mitigate this issue.
- Data Bias: Biased data can lead to biased models that make inaccurate predictions for certain subsets of data. Careful data collection and preprocessing are crucial to minimize bias.
Model Development and Deployment
Building and implementing an AI model for predictive maintenance in a manufacturing setting isn’t a simple plug-and-play operation. It’s a multi-stage process requiring careful consideration of data, algorithms, and integration with existing systems. Success hinges on choosing the right tools and techniques, and understanding the nuances of deploying AI in a real-world industrial environment.
The development process involves selecting appropriate AI algorithms based on the available data and the specific maintenance needs. This selection is crucial because different algorithms are better suited for different types of data and predictive tasks. For instance, time-series data, common in sensor readings, might benefit from recurrent neural networks (RNNs) or long short-term memory (LSTM) networks, while data exhibiting clear patterns might be better handled by simpler models like support vector machines (SVMs) or decision trees. The complexity of the model should be balanced against the need for interpretability and ease of deployment. Overly complex models can be difficult to understand and maintain, hindering their practical application.
AI Model Selection and Training
Choosing the right AI model is paramount. Factors influencing this decision include the type of data available (e.g., sensor data, historical maintenance records), the complexity of the system being monitored, and the desired level of accuracy and interpretability. Commonly used models include Support Vector Machines (SVMs) for classifying equipment health, Random Forests for handling high-dimensional data, and Recurrent Neural Networks (RNNs) for analyzing time-series data from sensors. The training process involves feeding the chosen model with a large, representative dataset of sensor readings, maintenance logs, and other relevant information. The model learns to identify patterns and relationships that indicate impending equipment failures. Regular hyperparameter tuning is essential to optimize model performance. For example, adjusting the learning rate in a neural network can significantly impact its accuracy and training speed. A poorly trained model, even with a sophisticated algorithm, will lead to inaccurate predictions and ineffective maintenance strategies.
Model Validation and Performance Evaluation
Rigorous validation is critical to ensure the model’s reliability and accuracy. This involves splitting the dataset into training, validation, and testing sets. The training set is used to train the model, the validation set is used to tune hyperparameters and prevent overfitting, and the testing set is used to evaluate the final model’s performance on unseen data. Key metrics for evaluating model performance include precision, recall, F1-score, and AUC (Area Under the Curve) for classification tasks, and RMSE (Root Mean Squared Error) or MAE (Mean Absolute Error) for regression tasks. A robust validation process ensures the model generalizes well to new, unseen data and provides accurate predictions in real-world scenarios. For example, a model with high precision but low recall might miss many actual failures, while a model with high recall but low precision might generate many false alarms. Finding the right balance depends on the specific application and the cost of false positives versus false negatives.
Deployment and Integration Strategies
Deploying the trained AI model into the existing manufacturing system requires careful planning and execution. Several strategies exist, including cloud-based deployment, on-premise deployment, and edge computing. Cloud-based deployment offers scalability and flexibility, but raises concerns about data security and latency. On-premise deployment provides greater control and security but requires significant infrastructure investment. Edge computing, processing data closer to the source (e.g., on the factory floor), minimizes latency and bandwidth requirements, making it ideal for real-time applications. Integration with existing systems such as Manufacturing Execution Systems (MES) and Enterprise Resource Planning (ERP) systems is crucial for seamless data flow and automated maintenance scheduling. This integration might involve developing custom APIs or using existing integration tools. For example, the model’s predictions could trigger automated alerts to maintenance personnel or automatically schedule preventive maintenance tasks.
Model Development and Deployment Workflow
The diagram illustrates a typical workflow. Data acquisition and preprocessing (covered in previous sections) feed into the model training phase. The trained model then undergoes rigorous validation before final deployment and integration into the manufacturing system. This iterative process often involves feedback loops to refine the model and improve its performance.
Case Studies and Examples of AI in Predictive Maintenance
AI-driven predictive maintenance isn’t just a futuristic concept; it’s revolutionizing manufacturing across various sectors. From preventing costly downtime to optimizing resource allocation, real-world applications showcase the tangible benefits of integrating AI into maintenance strategies. Let’s dive into some compelling examples that highlight the power of this technology.
Predictive Maintenance in the Automotive Industry
The automotive industry, with its complex assembly lines and high-precision machinery, is a prime candidate for AI-driven predictive maintenance. One prominent example involves a major automaker using machine learning algorithms to analyze sensor data from robots on their assembly lines. By identifying subtle changes in vibration patterns and energy consumption, the system accurately predicted potential failures days in advance, allowing for proactive maintenance and preventing costly production halts. This resulted in a 20% reduction in unplanned downtime and a 15% decrease in maintenance costs.
AI-Powered Predictive Maintenance in Aerospace Manufacturing
The aerospace industry demands exceptionally high reliability and safety standards. Here, AI plays a crucial role in predicting failures in critical components of aircraft engines. Companies are using deep learning models to analyze data from various sensors, including temperature, pressure, and vibration sensors, to detect anomalies indicative of impending failures. Early detection enables timely repairs, preventing catastrophic failures and ensuring the safety of flight operations. One case study shows a 30% reduction in engine maintenance costs through early fault detection.
Implementing AI in the Energy Sector for Predictive Maintenance
Power generation plants, with their intricate network of turbines, generators, and other equipment, are vulnerable to unexpected failures. AI-driven predictive maintenance is proving invaluable in mitigating these risks. By analyzing data from various sensors, AI algorithms can predict equipment failures with remarkable accuracy. This allows for scheduled maintenance during off-peak hours, minimizing disruption to power supply. A notable example involves a power company that reduced unplanned outages by 40% and saved millions of dollars in repair costs.
Case Study Summary Table
Industry | AI Techniques | Key Results |
---|---|---|
Automotive | Machine Learning (vibration analysis, energy consumption monitoring) | 20% reduction in unplanned downtime, 15% decrease in maintenance costs |
Aerospace | Deep Learning (sensor data analysis for anomaly detection) | 30% reduction in engine maintenance costs |
Energy | Machine Learning (predictive modeling for equipment failure) | 40% reduction in unplanned outages, significant cost savings |
Challenges and Future Directions
Implementing AI-driven predictive maintenance, while promising, isn’t without its hurdles. The journey towards truly smart factories requires navigating complex technical and organizational challenges, while simultaneously anticipating and adapting to the rapid evolution of AI itself. Success hinges on understanding these obstacles and proactively developing strategies to overcome them.
Data security, integration complexities, and skill gaps represent significant barriers to widespread adoption. Furthermore, the ongoing development of AI algorithms and the integration of emerging technologies will continuously reshape the landscape of predictive maintenance.
Data Security Concerns in AI-Driven Predictive Maintenance
The reliance on vast amounts of sensor data introduces significant security risks. Manufacturing facilities often house sensitive operational data, intellectual property, and potentially even personally identifiable information (PII) if employee performance is being tracked. Cyberattacks targeting this data could lead to significant financial losses, operational disruptions, and reputational damage. Robust cybersecurity measures, including data encryption, access control, and intrusion detection systems, are crucial to mitigating these risks. Implementing a multi-layered security approach, regularly auditing systems, and investing in employee cybersecurity training are essential steps. For example, a breach in a chemical plant’s predictive maintenance system could lead to compromised process control data, potentially causing safety hazards or production delays costing millions.
Integration Complexities and Interoperability Issues
Integrating AI-driven predictive maintenance systems into existing manufacturing infrastructure can be a complex undertaking. Legacy systems often lack the necessary interoperability to seamlessly exchange data with modern AI platforms. This requires significant investment in upgrading existing equipment, developing custom integration solutions, and potentially replacing outdated systems. The challenge is compounded by the diversity of equipment and software used in manufacturing facilities, making standardization and seamless data flow a significant hurdle. For instance, integrating a new AI-powered predictive maintenance platform with a decades-old CNC machine might require extensive custom software development and potentially hardware upgrades.
Skill Gaps and the Need for Specialized Expertise
The successful implementation and management of AI-driven predictive maintenance requires a workforce with specialized skills. This includes data scientists, machine learning engineers, and IT professionals with expertise in cybersecurity and system integration. A shortage of skilled professionals in these areas can hinder the adoption of AI-based solutions. Addressing this requires investments in education and training programs to develop the necessary talent pool. Companies need to attract and retain skilled professionals by offering competitive salaries and opportunities for professional development. For example, a manufacturing company might partner with a local university to create a specialized training program focused on AI for predictive maintenance, addressing the skills gap within their workforce and the broader community.
Future Advancements in AI for Predictive Maintenance
The field of AI is constantly evolving, and this translates into continuous advancements in predictive maintenance capabilities. Future developments will likely focus on enhancing the accuracy, efficiency, and explainability of AI models. The integration of advanced machine learning techniques, such as deep learning and reinforcement learning, will improve the ability of AI systems to detect subtle anomalies and predict equipment failures with greater precision. Furthermore, research into explainable AI (XAI) will make it easier to understand the reasoning behind AI-driven predictions, increasing trust and acceptance among manufacturing personnel. For example, future AI models might incorporate sensor data from various sources (vibration, temperature, pressure, etc.) along with real-time operational data to predict not only the likelihood of failure but also the optimal time for maintenance intervention, minimizing downtime and maximizing efficiency.
The Role of Edge Computing and IoT in Enhancing AI-Based Predictive Maintenance
Edge computing, the processing of data closer to the source (e.g., on factory floor devices), offers significant advantages for AI-driven predictive maintenance. It reduces latency, bandwidth requirements, and data transmission costs associated with sending large volumes of sensor data to a central cloud server. The Internet of Things (IoT) provides the infrastructure for collecting and transmitting this data from various sensors and devices throughout the manufacturing facility. Combining edge computing and IoT allows for real-time analysis of sensor data, enabling immediate responses to potential equipment failures. For instance, an edge device on a production line could analyze sensor data from a specific machine and trigger an alert if it detects an anomaly, allowing for immediate intervention before the problem escalates.
Digital Twins and Augmented Reality in Predictive Maintenance, The Role of AI in Advancing Predictive Maintenance in Manufacturing
Digital twins, virtual representations of physical assets, provide valuable insights into the performance and condition of equipment. By integrating sensor data with digital twin models, manufacturers can simulate different scenarios and predict the impact of various maintenance strategies. Augmented reality (AR) can further enhance predictive maintenance by providing technicians with real-time information and guidance during maintenance tasks. AR overlays can display diagnostic information, repair instructions, and 3D models of equipment directly onto the technician’s view, reducing downtime and improving the efficiency of repairs. For example, a technician using AR glasses while working on a malfunctioning pump could see an overlay showing the exact location of the problem, step-by-step repair instructions, and a 3D model of the pump’s internal components, guiding them through the repair process with increased efficiency and accuracy.
Final Review
Ultimately, the integration of AI into predictive maintenance isn’t just about optimizing processes; it’s about transforming the entire manufacturing landscape. By embracing AI-driven strategies, manufacturers can move from reactive firefighting to proactive problem-solving, ensuring smoother operations, reduced waste, and a significant competitive edge. The journey may present challenges, but the rewards—a more efficient, resilient, and profitable manufacturing future—are undeniably worth the effort. The future of manufacturing is predictive, and it’s powered by AI.