The Role of AI in Advancing Autonomous Robotics in Manufacturing – AI’s Role in Advancing Autonomous Robotics in Manufacturing: Forget clunky, predictable robots. We’re talking about a manufacturing revolution fueled by AI-powered machines that learn, adapt, and collaborate like never before. This isn’t just about increased efficiency; it’s about a smarter, safer, and more responsive production process, transforming how goods are made and delivered.
From AI-enhanced vision systems guiding robots through complex assembly lines to machine learning predicting equipment failures before they happen, the impact is undeniable. Imagine robots collaborating seamlessly with human workers, sharing tasks and boosting productivity without compromising safety. That’s the future AI is building, right now, in factories across the globe.
Introduction to Autonomous Robotics in Manufacturing
The manufacturing landscape is undergoing a significant transformation, driven by the increasing adoption of autonomous robotics. These robots, unlike their predecessors requiring extensive human programming and oversight for each task, are capable of operating independently, adapting to changing conditions, and performing complex tasks with minimal human intervention. This shift promises a future of increased efficiency, productivity, and safety within factories worldwide.
Autonomous robots in manufacturing currently encompass a range of technologies, from collaborative robots (cobots) working alongside human workers to fully autonomous mobile robots (AMRs) navigating complex factory floors and performing tasks like material handling and quality inspection. While some sectors have embraced these technologies more fully than others, the overall trend points towards a significant increase in deployment across various manufacturing processes. This adoption, however, is not without its challenges.
Challenges in Deploying Autonomous Robots in Manufacturing Environments
The integration of autonomous robots into existing manufacturing processes presents several significant hurdles. High initial investment costs for both the robots themselves and the necessary supporting infrastructure (such as advanced sensor networks and sophisticated software systems) often represent a major barrier to entry for smaller companies. Furthermore, the need for robust and reliable safety mechanisms to ensure the safety of human workers operating alongside autonomous robots is paramount. Ensuring seamless integration with existing production lines and legacy systems also poses a significant technological challenge. Finally, the development and maintenance of the sophisticated software and algorithms that govern the robots’ decision-making processes require specialized expertise, which can be difficult and expensive to acquire. The lack of standardized interfaces and protocols also hampers the smooth integration of robots from different vendors.
Potential Benefits of Increased Automation in Manufacturing Through Robotics
Despite the challenges, the potential benefits of increased automation in manufacturing through robotics are substantial. Increased productivity is perhaps the most immediate advantage; autonomous robots can operate continuously without breaks, leading to significantly higher output compared to human workers. Furthermore, the consistency and precision of robotic operations lead to improved product quality and reduced defects. This reduction in errors translates directly into lower waste and improved efficiency. Autonomous robots can also be deployed in hazardous or repetitive tasks, improving worker safety and reducing the risk of workplace injuries. Finally, the enhanced flexibility offered by autonomous robots allows manufacturers to adapt quickly to changing market demands and production requirements, boosting overall agility and competitiveness. For example, a company like Tesla has leveraged robotics extensively in its automotive manufacturing process, achieving significant gains in production efficiency and consistency. The ability to quickly reconfigure robotic systems to accommodate new product designs also gives a considerable competitive edge.
AI’s Role in Enhancing Perception and Navigation
The integration of Artificial Intelligence (AI) is revolutionizing autonomous robotics in manufacturing, significantly boosting their perception and navigation capabilities. No longer confined to structured, predictable environments, robots are now navigating increasingly dynamic and complex factory floors, thanks to AI’s ability to process vast amounts of sensory data in real-time and make intelligent decisions. This enhanced perception and navigation allows for greater flexibility, efficiency, and safety in manufacturing processes.
AI-powered computer vision is transforming how robots perceive their surroundings. Traditional robotic systems relied on pre-programmed paths and limited sensory input, making them inflexible and prone to errors in unpredictable situations. AI, however, empowers robots with the ability to “see” and understand their environment, adapting their actions based on real-time observations. This is crucial in dynamic manufacturing settings where objects and obstacles are constantly changing position.
AI-Enhanced Computer Vision for Robot Navigation
AI-powered computer vision systems utilize deep learning algorithms, particularly convolutional neural networks (CNNs), to analyze images and videos captured by cameras mounted on the robots. These algorithms allow robots to identify objects, assess distances, and detect obstacles with remarkable accuracy. For example, a robot tasked with picking and placing parts on a conveyor belt can use computer vision to identify the specific part it needs, determine its orientation, and plan a precise grasping motion, even if the parts are slightly misaligned or obscured. This level of precision and adaptability is unattainable with traditional, rule-based approaches.
AI Algorithms for Object Recognition and Manipulation
Object recognition is a critical component of AI-driven robotic systems. AI algorithms not only identify objects but also classify them, understand their properties (size, shape, weight), and predict their future movements. This information is crucial for successful manipulation. For instance, a robotic arm equipped with an AI-powered vision system can identify a specific type of screw from a bin containing various fasteners, determine its optimal gripping point, and then precisely insert it into the designated location. This process goes beyond simple pick-and-place operations; it involves sophisticated understanding of the object and its interaction with the environment.
AI-Based Approaches for Robot Path Planning and Obstacle Avoidance
Several AI-based approaches are used for robot path planning and obstacle avoidance. Reinforcement learning (RL) allows robots to learn optimal paths through trial and error, adapting to dynamic environments and unexpected obstacles. Simultaneous Localization and Mapping (SLAM) algorithms enable robots to build a map of their surroundings while simultaneously tracking their location within that map. These algorithms are crucial for navigating complex and unstructured environments. A-star and Dijkstra’s algorithms, while not strictly AI, are often combined with AI-powered perception to create efficient and safe navigation strategies. These algorithms allow the robot to calculate the shortest or most efficient path to its destination, avoiding collisions with obstacles detected by the AI-powered vision system.
AI-Driven Sensor Fusion Techniques
Effective robot navigation often requires integrating data from multiple sensors to gain a comprehensive understanding of the environment. AI plays a vital role in sensor fusion, combining information from different sources (e.g., LiDAR, cameras, ultrasonic sensors) to create a more robust and accurate representation of the robot’s surroundings. This enhanced situational awareness allows for safer and more reliable navigation.
Sensor Type | Advantages | Disadvantages | Applications in Manufacturing |
---|---|---|---|
LiDAR | Precise distance measurement, good for 3D mapping | Expensive, susceptible to environmental factors (e.g., fog, rain) | Autonomous guided vehicles (AGVs), precise part placement |
Camera | Cost-effective, provides rich visual information | Performance can be affected by lighting conditions, requires significant processing power | Object recognition, quality inspection, robotic manipulation |
Ultrasonic | Simple, inexpensive, robust to lighting conditions | Limited range and accuracy, susceptible to noise | Obstacle avoidance, proximity sensing |
AI for Advanced Control and Decision-Making
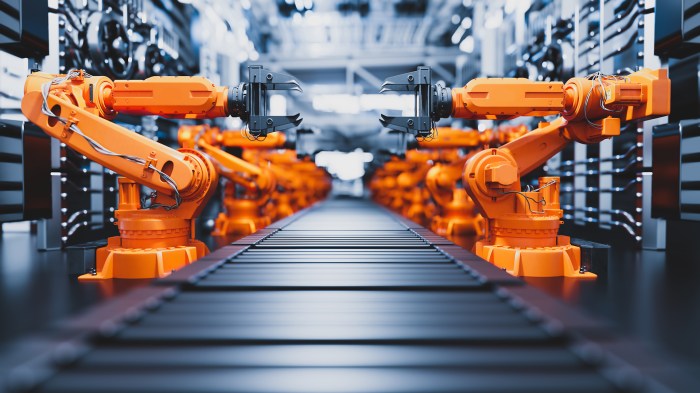
Source: website-files.com
The integration of artificial intelligence (AI) is revolutionizing autonomous robotics in manufacturing, moving beyond basic tasks to encompass sophisticated control and decision-making capabilities. This allows robots to adapt to dynamic environments, optimize performance, and even learn from experience, significantly increasing efficiency and productivity. This section delves into the key roles AI plays in achieving this advanced level of robotic control.
AI empowers autonomous robots to handle the complexity and variability inherent in real-world manufacturing scenarios. This surpasses the limitations of traditional, pre-programmed robotic systems, enabling a new era of flexible and adaptable automation.
Reinforcement Learning for Complex Manufacturing Tasks
Reinforcement learning (RL) is a powerful machine learning technique particularly well-suited for training robots to perform intricate manufacturing tasks. Unlike supervised learning, which requires vast amounts of labeled data, RL allows robots to learn through trial and error. The robot interacts with its environment, receives rewards for desirable actions and penalties for undesirable ones, and gradually learns an optimal policy – a strategy for maximizing its cumulative reward. For example, RL can be used to train a robot to assemble complex components with varying orientations and tolerances, a task difficult to program explicitly. The robot learns through repeated attempts, adjusting its actions based on the feedback it receives, ultimately achieving a high level of precision and speed. This iterative learning process allows the robot to adapt to unforeseen circumstances and handle unexpected variations in the manufacturing process.
Machine Learning for Predictive Maintenance of Robotic Systems
Predictive maintenance leverages machine learning algorithms to anticipate potential failures in robotic systems. By analyzing sensor data from various components like motors, actuators, and sensors, ML models can identify patterns indicative of impending malfunctions. This allows for proactive maintenance, preventing costly downtime and improving the overall lifespan of the robotic equipment. For example, an ML model trained on historical data of motor vibrations and temperature readings can accurately predict when a motor is likely to fail, allowing for timely replacement before it causes a production halt. This approach significantly reduces unexpected maintenance costs and enhances the reliability of the entire manufacturing process. The accuracy of these predictions increases with the amount of data collected and the sophistication of the ML model used.
AI Integration with Robotic Control Systems
A typical system architecture integrating AI with robotic control systems comprises several key components. First, sensors collect data from the robot’s environment and its internal state. This data is then processed by AI algorithms, such as those based on reinforcement learning or predictive maintenance. The output of the AI algorithms informs the robot’s control system, adjusting its actions and parameters in real-time. A feedback loop ensures continuous monitoring and adaptation. For instance, a vision system might identify a defect in a workpiece, which is then communicated to the AI, leading to an adjustment in the robot’s gripping force or trajectory to compensate for the defect. This closed-loop system enables dynamic adaptation and optimized performance. The architecture can be visualized as a layered system, with the AI layer sitting on top of the traditional robotic control system, providing higher-level decision-making capabilities.
Examples of AI-Powered Adaptive Control Systems
Several real-world examples demonstrate the effectiveness of AI-powered adaptive control systems. In the automotive industry, robots equipped with AI-powered vision systems can adjust their welding parameters based on the variations in the shape and position of car bodies. In the electronics industry, robots performing delicate assembly tasks can adapt their movements in response to slight variations in component placement, ensuring consistent quality. Furthermore, AI can optimize the robot’s trajectory in response to changing environmental conditions, such as temperature fluctuations or vibrations, maintaining optimal performance even under challenging circumstances. These adaptive systems enhance the robustness and flexibility of robots, allowing them to handle unexpected events and maintain high levels of productivity. The use of AI is not just about improving efficiency; it’s about creating more resilient and adaptable manufacturing processes.
AI-Driven Collaboration Between Robots and Humans
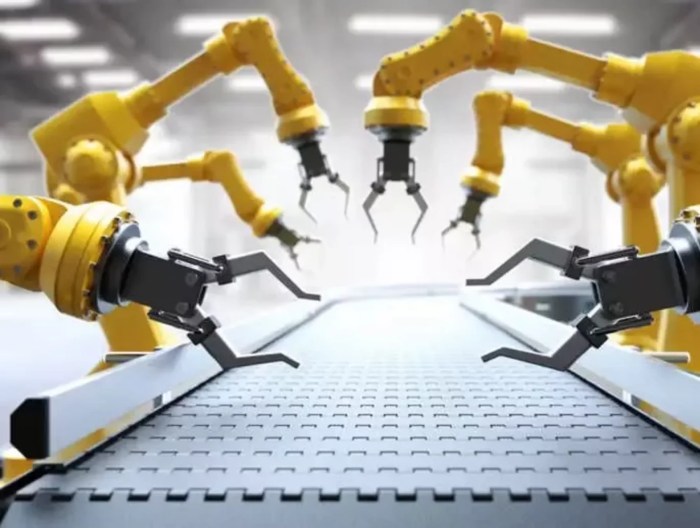
Source: bizclikmedia.net
AI’s impact on manufacturing is huge, driving autonomous robots to new levels of efficiency. This precision, mirroring the advancements in healthcare, is strikingly similar to the breakthroughs discussed in The Role of AI in Advancing Precision Medicine , where AI personalizes treatments. Ultimately, both fields leverage AI’s ability to analyze complex data for incredibly precise outcomes, boosting productivity and improving lives.
The integration of artificial intelligence into manufacturing is rapidly transforming the relationship between humans and robots, moving beyond simple automation towards collaborative workspaces. This shift necessitates a careful consideration of safety, efficiency, and the overall impact on the human workforce. AI plays a crucial role in facilitating this transition, enabling smoother interaction and boosting productivity in ways previously unimaginable.
AI’s contribution to human-robot collaboration goes beyond simply making robots “smarter.” It’s about creating a shared environment where humans and robots can work together effectively and safely, leveraging the strengths of both. This requires sophisticated AI algorithms that can predict human actions, understand human intentions, and adapt robot behavior accordingly. The result is a more flexible, efficient, and safer manufacturing process.
Safety Considerations and Protocols for Human-Robot Collaboration
Implementing safe human-robot collaboration (HRC) requires a multi-faceted approach. This includes incorporating physical safety features like sensors, emergency stops, and speed limiting mechanisms on robots. Beyond hardware, AI algorithms are essential for monitoring the workspace, predicting potential collisions, and reacting accordingly. For example, AI-powered vision systems can detect human presence and adjust robot movements to maintain a safe distance, while predictive algorithms can anticipate human actions and proactively adjust robot behavior to prevent accidents. This proactive approach is crucial, minimizing the risk of injury and maximizing the potential of collaborative robotics.
AI’s Role in Enabling Seamless Interaction Between Humans and Robots
AI significantly enhances human-robot interaction through intuitive interfaces and adaptive robot behavior. Natural language processing (NLP) allows humans to communicate with robots using everyday language, simplifying task instructions and troubleshooting. Machine learning (ML) enables robots to learn from human actions and adapt their behavior to optimize collaboration. For example, a robot might learn the preferred working style of a particular human worker and adjust its movements or speed accordingly. This personalized approach increases efficiency and reduces the learning curve for human operators. Moreover, AI-powered systems can track robot performance and identify areas for improvement, leading to continuous optimization of the human-robot team.
Benefits and Challenges of Human-Robot Teams in Manufacturing
Human-robot teams offer several advantages in manufacturing environments. Robots can handle repetitive, physically demanding tasks, freeing up human workers for more complex and creative roles. This combination leads to increased productivity, improved product quality, and reduced workplace injuries. However, challenges remain. The initial investment in AI-powered HRC systems can be significant, and integrating robots into existing workflows requires careful planning and training. Addressing worker concerns about job displacement is also crucial for successful implementation. Successfully navigating these challenges requires a holistic approach that considers both technological advancements and the social implications of automation.
Best Practices for Designing Safe and Effective Human-Robot Collaboration Systems
Prioritizing safety is paramount when designing HRC systems. The following best practices ensure a secure and productive collaborative environment:
- Risk Assessment and Mitigation: Conduct thorough risk assessments to identify potential hazards and implement appropriate safety measures.
- Layered Safety Systems: Employ multiple layers of safety mechanisms, including hardware safety features, software safeguards, and AI-based monitoring.
- Intuitive Human-Robot Interfaces: Design user-friendly interfaces that enable seamless communication and collaboration between humans and robots.
- Comprehensive Training Programs: Provide comprehensive training to workers on safe operation procedures and collaboration techniques.
- Regular Maintenance and Monitoring: Implement regular maintenance and monitoring procedures to ensure the continued safety and reliability of the HRC system.
- Adaptive AI Algorithms: Utilize AI algorithms that can adapt to changing conditions and learn from human behavior to optimize safety and efficiency.
Case Studies of AI in Autonomous Robotics for Manufacturing
The integration of artificial intelligence (AI) into autonomous robots is revolutionizing manufacturing processes. These case studies showcase real-world examples of how AI is enhancing efficiency, precision, and safety across various sectors. The successful implementation of these technologies highlights the transformative potential of AI in driving the future of manufacturing.
Amazon Robotics’ Kiva System, The Role of AI in Advancing Autonomous Robotics in Manufacturing
Amazon’s Kiva system (now Amazon Robotics) exemplifies the impact of AI in warehouse automation. This system utilizes autonomous mobile robots to transport goods within fulfillment centers. The robots navigate complex warehouse layouts using a combination of computer vision, SLAM (Simultaneous Localization and Mapping), and path planning algorithms. These algorithms allow the robots to avoid obstacles, locate specific shelves, and efficiently transport them to human workers for order picking. The challenges overcome included the need for robust navigation in dynamic environments and efficient coordination of multiple robots. The benefits have been significant, including increased order fulfillment speed, reduced labor costs, and improved warehouse efficiency.
Fanuc’s AI-Powered Robots for Welding
Fanuc, a leading robotics company, integrates AI into its industrial robots for welding applications. These robots use computer vision to identify and adapt to variations in workpiece positioning and geometry. Machine learning algorithms are used to optimize welding parameters, such as current, voltage, and travel speed, based on real-time feedback. This adaptive approach addresses the challenge of inconsistent workpiece quality and variations in the manufacturing process. The benefits include improved weld quality, reduced scrap rates, and increased productivity. The AI’s ability to learn and adapt makes it highly efficient in dealing with diverse welding tasks.
Siemens’ AI-Driven Predictive Maintenance
Siemens utilizes AI for predictive maintenance of its industrial robots and automated systems. Sensors embedded in the robots collect data on various parameters, such as vibration, temperature, and motor current. Machine learning models analyze this data to predict potential equipment failures before they occur. This predictive approach addresses the challenge of unplanned downtime, a significant cost factor in manufacturing. By predicting failures, Siemens can schedule maintenance proactively, minimizing disruptions and extending the lifespan of its equipment. The benefits include reduced downtime, lower maintenance costs, and improved overall equipment effectiveness (OEE).
Company | Application | AI Technology Used | Results Achieved |
---|---|---|---|
Amazon Robotics | Warehouse Automation (Kiva System) | Computer Vision, SLAM, Path Planning | Increased order fulfillment speed, reduced labor costs, improved warehouse efficiency |
Fanuc | AI-Powered Welding Robots | Computer Vision, Machine Learning | Improved weld quality, reduced scrap rates, increased productivity |
Siemens | Predictive Maintenance for Industrial Robots | Machine Learning, Sensor Data Analysis | Reduced downtime, lower maintenance costs, improved OEE |
Future Trends and Challenges: The Role Of AI In Advancing Autonomous Robotics In Manufacturing
The integration of AI in autonomous robotics within manufacturing is poised for explosive growth, but this advancement isn’t without its hurdles. Understanding the technological leaps on the horizon, the ethical considerations they raise, and the practical challenges they present is crucial for navigating this transformative period responsibly. The future of AI-powered manufacturing hinges on addressing these complexities proactively.
Technological Advancements Shaping the Future
Several key technological advancements are expected to significantly impact the future of AI in autonomous robotics for manufacturing. These advancements will lead to more sophisticated, adaptable, and efficient robotic systems. Increased computing power, coupled with advancements in machine learning algorithms and sensor technologies, will be pivotal.
- Enhanced Machine Learning Algorithms: The development of more robust and adaptable machine learning algorithms, such as reinforcement learning and deep learning techniques, will allow robots to learn complex tasks faster and with greater accuracy. This will enable them to handle more unpredictable situations and adapt to changing manufacturing environments. For instance, imagine robots learning to identify and correct defects in real-time, improving product quality dramatically.
- Advanced Sensor Integration: The integration of more sophisticated sensors, including advanced vision systems, force sensors, and proximity sensors, will provide robots with a richer understanding of their environment. This will enable more precise manipulation, improved navigation, and safer human-robot collaboration. Think of robots equipped with 3D vision capable of navigating cluttered warehouses and assembling intricate components with pinpoint accuracy.
- Edge Computing and Decentralized AI: Processing data closer to the source (edge computing) will reduce latency and improve real-time responsiveness, crucial for autonomous operations. Decentralized AI architectures will enhance robustness and fault tolerance, ensuring continuous operation even if parts of the system fail. This means robots can make quicker decisions without relying on a central server, enhancing efficiency and resilience.
Ethical and Societal Implications
The widespread adoption of AI-powered robots in manufacturing raises significant ethical and societal concerns. These concerns must be addressed proactively to ensure a just and equitable transition. Job displacement is a major concern, alongside the potential for bias in AI algorithms and the need for robust safety protocols.
- Job Displacement and Workforce Reskilling: Automation through AI-powered robots may lead to job displacement in certain manufacturing sectors. Proactive measures, such as workforce reskilling and retraining programs, are essential to mitigate this impact and ensure a smooth transition for affected workers. Examples include government-funded programs teaching displaced workers new skills in areas like AI maintenance or data analysis.
- Bias in AI Algorithms and Algorithmic Transparency: AI algorithms are trained on data, and if this data reflects existing biases, the algorithms will perpetuate and even amplify those biases. Ensuring fairness and transparency in AI algorithms is critical to avoid discriminatory outcomes. This requires careful data curation and ongoing monitoring of algorithm performance to identify and correct biases.
- Safety and Security Protocols: Robust safety protocols are crucial to ensure the safe operation of AI-powered robots in manufacturing environments. This includes developing fail-safe mechanisms, implementing robust security measures to prevent unauthorized access or manipulation, and establishing clear guidelines for human-robot interaction. Imagine a system that automatically shuts down a robot if it detects an unsafe condition or human interaction.
Data Security and Privacy Challenges
AI-driven manufacturing systems generate and process vast amounts of data, raising significant concerns about data security and privacy. Protecting sensitive data from unauthorized access and ensuring compliance with data privacy regulations are paramount.
The interconnected nature of these systems creates vulnerabilities. Cyberattacks could disrupt operations, compromise intellectual property, or even cause physical damage. Robust cybersecurity measures, including encryption, access control, and intrusion detection systems, are crucial to mitigate these risks. Furthermore, anonymization and data minimization techniques should be employed to protect the privacy of workers and other stakeholders whose data is collected and processed by the system. Implementing rigorous data governance frameworks, adhering to regulations like GDPR, and conducting regular security audits are essential for maintaining data integrity and user trust.
A Future Scenario: The AI-Powered Factory
Imagine a fully automated factory in 2040. AI-powered robots perform all tasks, from design and production to quality control and logistics. This leads to increased efficiency, reduced waste, and higher-quality products. However, this scenario also presents challenges. Job displacement requires proactive societal adjustments, including retraining initiatives and social safety nets. Data security remains paramount, requiring constant vigilance against cyber threats. The potential for bias in AI algorithms necessitates ongoing monitoring and adjustments to ensure fairness. While increased productivity and reduced costs are significant benefits, the ethical considerations and societal impacts must be carefully managed to ensure a future where AI benefits all members of society. The success of this future hinges on responsible development and deployment of these technologies.
Wrap-Up
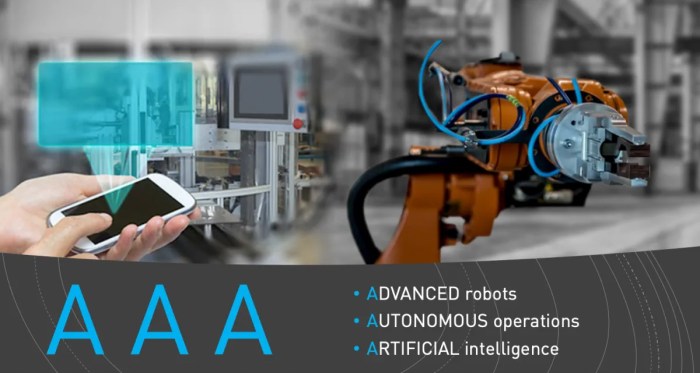
Source: versabox.eu
The integration of AI into autonomous robotics is no longer a futuristic fantasy; it’s reshaping the manufacturing landscape today. While challenges remain—ethical considerations, data security, and the need for robust safety protocols—the potential benefits are too significant to ignore. The future of manufacturing is intelligent, automated, and collaborative, a future powered by the incredible synergy between AI and autonomous robots.