The Role of AI in Advancing Autonomous Manufacturing Processes is revolutionizing industries. Forget clunky, predictable assembly lines; AI is injecting intelligence into manufacturing, leading to smarter, faster, and more efficient processes. From predictive maintenance that minimizes downtime to robots with unprecedented dexterity, AI is transforming how things are made, paving the way for a future where factories operate with minimal human intervention and maximum output.
This shift isn’t just about automation; it’s about optimization. AI algorithms analyze massive datasets, identifying bottlenecks, predicting failures, and ultimately improving quality and reducing waste. This article dives into the specifics of AI’s role, exploring its applications, benefits, challenges, and the exciting future it promises for the manufacturing landscape.
Introduction to Autonomous Manufacturing and AI
Autonomous manufacturing is the holy grail of industrial efficiency – a system where factories operate with minimal to no human intervention. Think robots collaborating seamlessly, machines self-diagnosing and repairing, and production lines optimizing themselves in real-time. It’s a future fueled by artificial intelligence (AI), and while not fully realized, it’s rapidly changing how we make things. Key characteristics include self-regulation, predictive maintenance, real-time optimization, and adaptive responses to changing conditions.
Autonomous manufacturing leverages AI in various ways, from sophisticated algorithms controlling robotic arms to machine learning models predicting equipment failures. This synergy allows for increased productivity, reduced downtime, and improved product quality. The extent of AI’s influence varies across sectors; some industries, like automotive and electronics, are further along the path to complete automation than others. However, the overall trend points towards increased AI integration across the manufacturing landscape.
Current State of Autonomous Manufacturing Adoption
The adoption of autonomous manufacturing varies considerably across industries. Automotive manufacturers, for instance, are leading the charge, extensively utilizing robots in assembly lines and implementing AI-powered quality control systems. The electronics industry also showcases significant progress, with automated warehouses and AI-driven supply chain management becoming increasingly common. Conversely, industries like textiles or food processing, often characterized by more complex and less standardized processes, lag behind in their implementation of fully autonomous systems. However, even in these sectors, we see a growing integration of AI-powered solutions for tasks like predictive maintenance and quality inspection. The rate of adoption is accelerating, driven by factors like falling AI development costs and increasing pressure for improved efficiency and cost reduction.
Limitations of Traditional Manufacturing Processes
Traditional manufacturing often relies on manual labor, leading to inconsistencies in quality, higher error rates, and slower production speeds. Human fatigue and the inherent limitations of human capabilities contribute to bottlenecks and inefficiencies. Predictive maintenance is often reactive, leading to unexpected downtime and costly repairs. Furthermore, traditional manufacturing struggles with real-time adaptability; adjusting production lines to meet changing demands can be time-consuming and resource-intensive. AI-powered autonomous systems address these limitations by offering consistent quality, reduced error rates, faster production cycles, and the ability to dynamically adapt to changing conditions, optimizing resource allocation and minimizing downtime. For example, a car manufacturer using AI-powered predictive maintenance can anticipate potential equipment failures and schedule maintenance proactively, preventing costly production halts.
AI Applications in Autonomous Manufacturing
Autonomous manufacturing, the holy grail of industrial efficiency, is rapidly becoming a reality thanks to the power of Artificial Intelligence. AI isn’t just automating tasks; it’s optimizing entire production lines, predicting failures before they happen, and ensuring consistent, high-quality output. Let’s dive into the specific ways AI is transforming the manufacturing landscape.
AI’s integration into autonomous manufacturing processes isn’t just about replacing human workers; it’s about augmenting their capabilities and creating a smarter, more resilient system. This involves sophisticated algorithms learning from vast datasets to make real-time decisions and improve efficiency across various aspects of production.
AI’s role in autonomous manufacturing is revolutionizing efficiency, but its impact extends far beyond the factory floor. The potential for AI to boost productivity directly ties into broader societal advancements; consider how its application in resource management could significantly aid developing nations, as explored in this insightful piece on The Potential of Artificial Intelligence in Tackling Global Poverty.
Ultimately, AI-driven manufacturing improvements can contribute to a more equitable global economy.
Predictive Maintenance using AI
Predictive maintenance, powered by AI, is revolutionizing how manufacturers handle equipment upkeep. Instead of relying on scheduled maintenance or reactive repairs after a breakdown, AI algorithms analyze sensor data from machines to predict potential failures. This allows for proactive interventions, minimizing downtime and maximizing productivity. For instance, an AI system might analyze vibration patterns in a motor to predict an impending bearing failure days in advance, allowing for a timely replacement before production is disrupted. This approach significantly reduces maintenance costs and improves overall equipment effectiveness (OEE).
AI-Driven Quality Control
Maintaining consistent product quality is paramount in manufacturing. AI-powered vision systems and machine learning algorithms are rapidly enhancing quality control processes. These systems can inspect products at high speeds and with greater accuracy than human inspectors, identifying defects that might be missed by the human eye. For example, an AI system could analyze images of circuit boards to detect microscopic solder flaws, ensuring that only perfect products leave the factory. This leads to reduced waste, improved product quality, and enhanced customer satisfaction.
Robotic Process Automation (RPA) with AI, The Role of AI in Advancing Autonomous Manufacturing Processes
Robots are no longer just performing repetitive tasks; they’re becoming intelligent agents capable of adapting to changing circumstances. AI-powered RPA integrates machine learning into robotic systems, allowing them to learn from experience and optimize their actions. This allows for greater flexibility and adaptability in manufacturing processes. For example, a robotic arm equipped with AI can learn to pick and place items of varying shapes and sizes, adapting its approach based on the specific object it’s handling. This increases the efficiency and versatility of robotic systems in the factory.
AI-Powered Supply Chain Optimization
AI algorithms are transforming supply chain management by analyzing vast datasets to predict demand, optimize inventory levels, and improve logistics. This helps manufacturers reduce costs, improve delivery times, and avoid stockouts or overstocking. For instance, AI can predict fluctuations in demand for a particular product based on historical sales data, seasonality, and external factors like economic trends. This allows for more accurate forecasting and proactive adjustments to production schedules and inventory management.
AI in Autonomous Vehicle Navigation within Factories
Autonomous guided vehicles (AGVs) are becoming increasingly prevalent in factories, transporting materials and goods efficiently. AI plays a crucial role in enabling these vehicles to navigate complex factory environments, avoiding obstacles and optimizing their routes. Sophisticated algorithms using computer vision and sensor fusion allow AGVs to perceive their surroundings, make real-time decisions, and adapt to changing conditions. This leads to improved efficiency in material handling and reduced transportation costs.
Comparison of AI Algorithms in Manufacturing
Different AI algorithms are suited to different manufacturing contexts. Machine learning (ML) excels in tasks involving pattern recognition and prediction, while deep learning (DL), a subset of ML, is particularly effective in processing large, complex datasets like images and sensor readings. ML might be used for predictive maintenance based on historical machine data, while DL might be employed for advanced quality control using image analysis. The choice of algorithm depends on the specific application, data availability, and computational resources.
AI Application | Description | Benefits | Challenges |
---|---|---|---|
Predictive Maintenance | AI algorithms analyze sensor data to predict equipment failures. | Reduced downtime, lower maintenance costs, improved OEE. | Requires high-quality sensor data, algorithm training and validation. |
AI-Driven Quality Control | AI-powered vision systems detect defects in products. | Improved product quality, reduced waste, enhanced customer satisfaction. | High initial investment, algorithm accuracy depends on data quality. |
Robotic Process Automation (RPA) | AI enhances robotic systems, allowing for greater flexibility and adaptability. | Increased efficiency, improved productivity, reduced labor costs. | Integration challenges, need for skilled workforce to manage systems. |
Supply Chain Optimization | AI analyzes data to predict demand, optimize inventory, and improve logistics. | Reduced costs, improved delivery times, avoided stockouts. | Data accuracy and availability, algorithm complexity. |
Autonomous Vehicle Navigation | AI enables AGVs to navigate complex factory environments. | Improved efficiency in material handling, reduced transportation costs. | Sensor accuracy, environmental variability, safety considerations. |
AI-Powered Robotics and Automation
The integration of artificial intelligence (AI) is revolutionizing industrial robotics, pushing the boundaries of what’s possible in manufacturing. No longer are robots simply programmed automatons; they’re becoming increasingly intelligent, adaptable, and collaborative partners, leading to significant improvements in efficiency, safety, and overall productivity. This transformative shift is driven by advancements in machine learning, computer vision, and natural language processing, allowing robots to perform complex tasks with greater precision and autonomy.
AI enhances industrial robots by significantly boosting their dexterity, adaptability, and collaborative potential. Traditional robots excel at repetitive tasks in structured environments. However, AI allows them to handle variations, uncertainties, and unstructured environments more effectively. This is achieved through advanced algorithms that enable robots to learn from data, adapt to changing conditions, and even make decisions in real-time. The result is a more flexible and responsive manufacturing process.
Enhanced Dexterity and Adaptability in Industrial Robots
AI algorithms, particularly those based on deep learning, empower robots with enhanced dexterity. Computer vision systems enable robots to “see” and interpret their surroundings, identifying objects of varying shapes, sizes, and orientations with greater accuracy than ever before. This allows for precise manipulation of delicate parts or complex assemblies, tasks previously beyond the capabilities of traditional robots. Furthermore, machine learning enables robots to adapt to variations in materials, components, or environmental conditions, making the manufacturing process more robust and less susceptible to disruptions. For example, a robot tasked with assembling electronic components can learn to adjust its grip and movements based on subtle differences in the size or shape of individual components, ensuring consistent assembly quality.
AI-Powered Robots Improving Efficiency and Safety in Assembly Lines
Imagine a car assembly line where AI-powered robots collaborate seamlessly with human workers. These robots, equipped with advanced sensors and computer vision, can identify and pick up parts from a disorganized bin, accurately place them in the designated locations, and even perform quality checks along the way. This eliminates the need for humans to perform repetitive, potentially hazardous tasks, reducing the risk of workplace injuries. Simultaneously, the robots’ ability to adapt to variations in part placement or assembly procedures ensures a consistent and efficient workflow, minimizing downtime and maximizing output. The collaborative nature of these robots further enhances safety by allowing them to work alongside humans without the need for extensive safety barriers, promoting a more fluid and efficient production environment.
Real-World Examples of AI-Driven Robotics in Manufacturing
Several companies are already reaping the benefits of AI-driven robotics in their manufacturing processes. FANUC, a leading robotics manufacturer, utilizes AI-powered vision systems to enable robots to identify and handle a wider variety of parts, improving the flexibility and efficiency of their automated production lines. Similarly, companies like Tesla employ AI in their assembly lines, leveraging machine learning to optimize robot movements and improve the precision of their assembly processes. These implementations demonstrate the tangible benefits of AI in boosting productivity, enhancing safety, and creating more adaptable manufacturing environments. The trend toward AI-powered robotics is expected to continue accelerating, transforming manufacturing processes globally.
Data Analytics and AI in Manufacturing Optimization
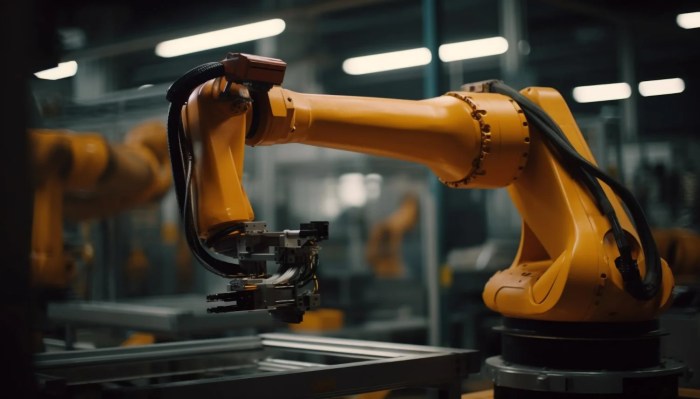
Source: the-newshub.com
The marriage of AI and data analytics is revolutionizing manufacturing, moving beyond simple automation to a realm of proactive optimization. By leveraging the power of sophisticated algorithms to sift through massive datasets generated by sensors and machines, manufacturers gain unprecedented insights into their processes, leading to significant improvements in efficiency, productivity, and profitability. This data-driven approach allows for the identification of bottlenecks, the prediction of potential failures, and the fine-tuning of processes for optimal performance.
AI algorithms are particularly adept at analyzing the complex, high-volume data streams generated by modern manufacturing environments. These algorithms can identify patterns and correlations that would be impossible for human analysts to discern, revealing hidden inefficiencies and opportunities for improvement. This includes everything from identifying optimal machine settings to predicting potential equipment failures before they occur, minimizing costly downtime and maximizing equipment lifespan. The analytical power of AI is transforming how manufacturers understand and interact with their operational data, enabling a level of precision and control previously unimaginable.
AI-Driven Predictive Maintenance
Predictive maintenance, powered by AI, represents a significant leap forward in manufacturing efficiency. Instead of relying on scheduled maintenance or reactive repairs after equipment failure, AI algorithms analyze sensor data (vibration, temperature, pressure, etc.) to predict when a machine is likely to malfunction. This allows for proactive maintenance, preventing costly downtime and extending the lifespan of expensive equipment. For example, a factory using AI-powered predictive maintenance on its robotic arms might identify a subtle change in vibration patterns indicating impending bearing failure. This allows for a timely replacement of the bearing, preventing a complete robotic arm shutdown and avoiding costly production delays. The cost savings from preventing unexpected equipment failures often far outweigh the investment in AI-powered predictive maintenance systems. Real-world examples demonstrate significant reductions in downtime – often by 30% or more – and substantial increases in equipment lifespan, leading to substantial ROI.
Real-Time Data Analysis vs. Batch Processing
The choice between real-time data analysis and batch processing in autonomous manufacturing depends heavily on the specific application and the desired level of responsiveness. Real-time analysis provides immediate feedback, enabling adjustments to be made instantly to optimize processes and prevent issues from escalating. This is crucial in dynamic environments where rapid changes can significantly impact production. For example, a real-time system might immediately detect a deviation in product quality and automatically adjust machine parameters to correct the problem before a significant number of defective products are produced. Batch processing, on the other hand, involves collecting and analyzing data over a period, providing a more holistic view but with a delay in insights. While less immediate, batch processing can be more efficient for analyzing large datasets that might overwhelm a real-time system. The optimal approach often involves a hybrid strategy, combining real-time analysis for critical processes with batch processing for more comprehensive, long-term analysis. The key is to tailor the approach to the specific needs of each manufacturing process.
Challenges and Future Trends in AI-Driven Autonomous Manufacturing: The Role Of AI In Advancing Autonomous Manufacturing Processes
The journey towards fully autonomous manufacturing, powered by artificial intelligence, is paved with both immense potential and significant hurdles. While AI promises unprecedented efficiency and productivity, its successful implementation requires addressing critical challenges and leveraging emerging technologies to navigate the complexities ahead. This section explores the key obstacles and promising future trends shaping the landscape of AI-driven autonomous manufacturing.
Data Security and Privacy in Autonomous Manufacturing
The reliance on vast datasets for training and operating AI systems in manufacturing presents significant security and privacy concerns. Data breaches can expose sensitive intellectual property, compromise operational integrity, and lead to significant financial losses. Robust cybersecurity measures, including encryption, access control, and anomaly detection systems, are crucial. Furthermore, compliance with regulations like GDPR and CCPA is paramount to protect the privacy of employee and customer data used in AI algorithms. The implementation of blockchain technology for secure data management and provenance tracking is gaining traction as a potential solution to enhance data integrity and traceability.
Integration Complexities and Legacy Systems
Integrating AI systems into existing manufacturing environments often proves challenging, particularly when dealing with legacy systems that lack the necessary infrastructure for seamless data exchange and real-time analytics. These systems may require significant upgrades or replacements, leading to substantial costs and potential disruptions to production. A phased approach to integration, focusing on modular solutions and incremental improvements, can mitigate these challenges. Moreover, the adoption of standardized communication protocols and data formats can facilitate smoother integration across different systems and platforms.
Cost and Return on Investment
The high initial investment required for implementing AI-driven autonomous manufacturing systems, including hardware, software, and skilled personnel, presents a significant barrier to entry for many manufacturers. Accurate cost-benefit analyses are essential to justify the investment and ensure a favorable return on investment (ROI). Factors such as reduced labor costs, improved efficiency, and minimized waste need to be carefully considered. Government incentives and subsidies can play a crucial role in encouraging the adoption of AI technologies by smaller businesses. For instance, tax breaks for implementing energy-efficient AI-powered robots can encourage adoption and accelerate the shift towards sustainable manufacturing practices.
Ethical Considerations in AI-Driven Manufacturing
The widespread adoption of AI in manufacturing raises several ethical considerations. Job displacement due to automation is a major concern. Retraining and upskilling initiatives are crucial to help workers adapt to the changing job market and acquire new skills relevant to the AI-driven manufacturing sector. Furthermore, algorithmic bias in AI systems can lead to unfair or discriminatory outcomes. Rigorous testing and validation processes are essential to ensure fairness and transparency in AI-driven decision-making. Implementing explainable AI (XAI) techniques allows for better understanding of how AI systems arrive at their conclusions, promoting accountability and trust. The development of ethical guidelines and standards for AI in manufacturing is crucial to address these concerns proactively.
Impact of Edge Computing and Digital Twins
Edge computing, which processes data closer to the source, can significantly enhance the responsiveness and reliability of AI-driven autonomous manufacturing systems. By reducing latency and bandwidth requirements, edge computing enables real-time decision-making and control, crucial for tasks such as predictive maintenance and quality control. Digital twins, virtual representations of physical assets and processes, provide valuable insights into system performance and potential failures, enabling proactive interventions and optimizing production processes. The combination of edge computing and digital twins offers a powerful approach to improve efficiency, reduce downtime, and enhance overall productivity in autonomous manufacturing environments. For example, a digital twin of a robotic arm can simulate various scenarios and predict potential failures, allowing for preventative maintenance before production disruptions occur, minimizing costly downtime.
Case Studies of Successful AI Integration
AI’s impact on autonomous manufacturing is no longer theoretical; numerous companies are reaping the benefits. This section dives into specific examples, showcasing how AI implementation translates into tangible improvements in efficiency, productivity, and overall profitability. These case studies illustrate the practical application of AI and the strategic considerations for successful integration.
Siemens’ AI-Powered Predictive Maintenance
Siemens, a global powerhouse in industrial automation, leveraged AI to optimize its manufacturing processes through predictive maintenance. Instead of relying on scheduled maintenance, they implemented a system that analyzes sensor data from their machinery in real-time. This allows them to predict potential equipment failures before they occur, minimizing downtime and maximizing production efficiency.
The following points detail Siemens’ AI integration journey:
- AI Technologies Used: Machine learning algorithms (specifically, time series analysis and anomaly detection) were employed to process sensor data and predict equipment failures.
- Challenges Faced: Integrating diverse data sources from legacy systems and ensuring data quality presented initial hurdles. Training the AI models required significant data sets and expert knowledge.
- Results Achieved: Siemens reported a 20% reduction in unplanned downtime and a 15% increase in overall equipment effectiveness (OEE) following the implementation of their AI-powered predictive maintenance system. This translated into significant cost savings and improved production output.
To achieve this success, Siemens invested in comprehensive employee training programs, upskilling their workforce to manage and interpret the data generated by the AI system. They also established cross-functional teams to ensure seamless integration across different departments.
Fanuc’s AI-Driven Robot Optimization
Fanuc, a leading robotics company, has integrated AI into its robotic systems to improve their performance and adaptability. Their AI-powered robots can learn and adapt to changing conditions on the factory floor, optimizing their movements and actions for greater efficiency and precision.
Here’s a breakdown of Fanuc’s approach:
- AI Technologies Used: Reinforcement learning algorithms enabled the robots to learn optimal movement patterns through trial and error, improving their efficiency and precision over time. Computer vision was also implemented to allow the robots to better perceive their environment.
- Challenges Faced: Developing robust algorithms that could handle the complexity and variability of real-world manufacturing environments proved challenging. Ensuring the safety and reliability of AI-powered robots was also a crucial consideration.
- Results Achieved: Fanuc reported significant improvements in robot cycle times, leading to increased production throughput. The AI-powered robots also demonstrated improved accuracy and consistency in their tasks, resulting in reduced waste and higher quality products.
Fanuc’s successful implementation involved investing in advanced robotics research and development and collaborating with leading AI experts. They also focused on creating a culture of continuous improvement and innovation, encouraging their engineers to explore and implement new AI technologies.
Bosch’s AI-Enhanced Quality Control
Bosch, a global manufacturing giant, implemented AI-powered quality control systems to detect defects in their products with greater accuracy and speed. Their system analyzes images and sensor data from the production line, identifying even subtle defects that might be missed by human inspectors.
The key aspects of Bosch’s AI integration are:
- AI Technologies Used: Computer vision algorithms, combined with deep learning models, were used to analyze images and identify defects with high accuracy. This system was integrated with existing production line sensors to provide a comprehensive quality control solution.
- Challenges Faced: Creating a robust AI model that could handle the variability of product appearances and lighting conditions presented a challenge. Integrating the AI system with existing legacy systems also required significant effort.
- Results Achieved: Bosch reported a significant reduction in the number of defective products leaving their factories. The AI-powered system also improved the efficiency of their quality control process, reducing inspection times and freeing up human inspectors to focus on more complex tasks. They estimated a 10% reduction in product defects and a 15% increase in inspection efficiency.
Bosch’s success was underpinned by a strategic approach to workforce integration. Instead of replacing human inspectors, they retrained them to work alongside the AI system, leveraging their expertise to handle complex or unusual situations. This fostered collaboration and ensured a smooth transition.
Wrap-Up
The integration of AI into autonomous manufacturing processes is no longer a futuristic fantasy; it’s the present reality reshaping industries. While challenges remain – from data security concerns to ethical considerations – the potential benefits are undeniable. The future of manufacturing is intelligent, adaptive, and efficient, driven by the power of AI to optimize every stage of the production process. Companies embracing this technological leap are positioning themselves for a competitive edge in the global market, unlocking unprecedented levels of productivity and innovation.