The Potential of AI in Predictive Maintenance for Manufacturing Industries is no longer a futuristic fantasy; it’s the present, reshaping how factories operate. Imagine a world where machines predict their own failures, allowing for proactive repairs before costly downtime strikes. This isn’t science fiction—it’s the reality AI is creating, using sophisticated algorithms to analyze sensor data and predict potential problems with incredible accuracy. This leap forward promises increased efficiency, reduced operational costs, and a significant boost to the bottom line for manufacturers worldwide.
From identifying subtle anomalies in machinery vibrations to predicting the lifespan of critical components, AI is revolutionizing predictive maintenance. This means fewer unexpected breakdowns, less wasted time and resources on reactive repairs, and a smoother, more profitable production process. But it’s not just about fixing things; AI allows manufacturers to optimize their operations, reducing waste and maximizing efficiency across the board. We’ll delve into the specific techniques, case studies, and future implications of this transformative technology, exploring both the opportunities and challenges it presents.
Introduction to Predictive Maintenance and AI in Manufacturing: The Potential Of AI In Predictive Maintenance For Manufacturing Industries
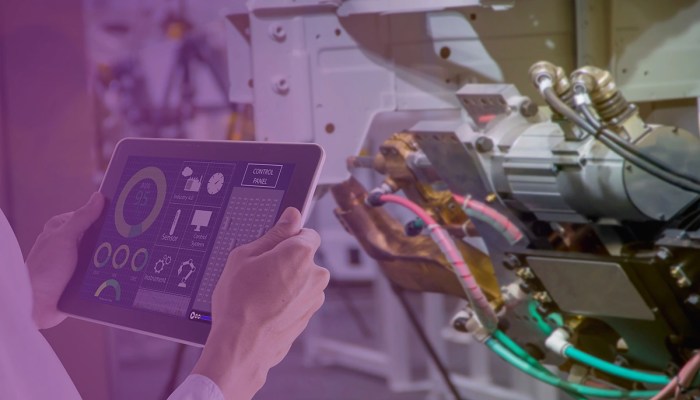
Source: ttpsc.com
Predictive maintenance (PdM) is revolutionizing how manufacturers approach equipment upkeep. Instead of relying on fixed schedules or reactive repairs after a breakdown, PdM uses data analysis to predict when equipment is likely to fail. This proactive approach minimizes downtime, reduces maintenance costs, and extends the lifespan of valuable assets. In essence, it’s about moving from firefighting to fire prevention in the world of industrial machinery.
The integration of Artificial Intelligence (AI) significantly boosts the effectiveness of PdM strategies. AI algorithms, particularly machine learning, excel at identifying patterns and anomalies in vast datasets generated by industrial sensors. These algorithms can analyze data from various sources – vibration sensors, temperature gauges, pressure monitors – to pinpoint potential failures before they occur. This allows for timely interventions, preventing costly breakdowns and maximizing operational efficiency.
AI Adoption in Predictive Maintenance for Manufacturing
The adoption of AI-powered PdM in manufacturing is steadily increasing, albeit at varying rates across different industries and companies. Early adopters, particularly in sectors like aerospace and automotive, have already seen significant returns on investment. These companies are leveraging AI to optimize maintenance schedules, reduce unplanned downtime, and improve overall equipment effectiveness (OEE). For example, a major automotive manufacturer might use AI to predict when a specific robotic arm on their assembly line is likely to malfunction, allowing for preventative maintenance during a scheduled downtime period, thus avoiding costly production halts. However, the widespread adoption faces challenges such as data integration complexities, the need for skilled personnel to manage and interpret AI-driven insights, and the initial investment required for implementing AI-powered systems. Despite these challenges, the potential benefits are driving further adoption, with many manufacturers actively exploring and implementing AI-based PdM solutions. The future likely holds more sophisticated AI models capable of handling even more complex data sets and providing even more accurate predictions.
AI Techniques for Predictive Maintenance
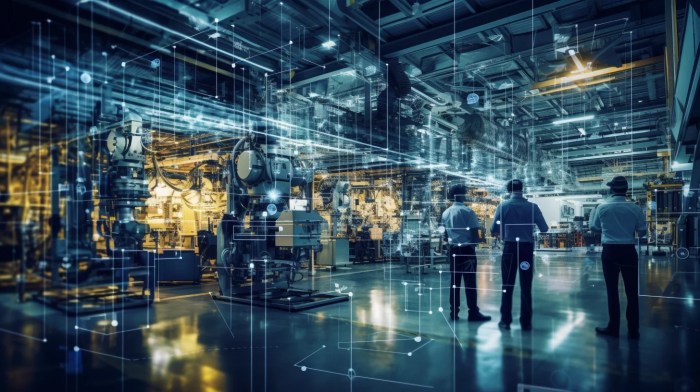
Source: ilikeai.ai
Predictive maintenance, powered by AI, is revolutionizing manufacturing. By leveraging the power of algorithms to analyze data and predict equipment failures, manufacturers can significantly reduce downtime, optimize maintenance schedules, and ultimately boost profitability. This section delves into the specific AI techniques driving this transformation.
AI Algorithms in Predictive Maintenance
Several AI algorithms are employed in predictive maintenance, each with its strengths and weaknesses. The choice of algorithm depends heavily on factors like the complexity of the data, the desired accuracy, and the available computational resources. A key consideration is the trade-off between accuracy and computational cost; highly accurate models often demand more processing power and longer training times.
Algorithm | Accuracy | Computational Cost | Data Requirements |
---|---|---|---|
Machine Learning (e.g., Regression, Support Vector Machines) | Moderate to High, depending on model and data | Relatively Low | Moderate; requires labelled data for supervised learning |
Deep Learning (e.g., Recurrent Neural Networks, Convolutional Neural Networks) | High, capable of handling complex patterns | High; requires significant computing power | Large datasets; can handle both labelled and unlabelled data (with unsupervised or semi-supervised techniques) |
Bayesian Networks | Moderate to High, good for probabilistic reasoning | Moderate | Moderate; requires understanding of relationships between variables |
Ensemble Methods (e.g., Random Forest, Gradient Boosting) | High, combines multiple models for improved accuracy | Moderate to High, depending on the number of base models | Moderate to High; benefits from larger datasets |
Sensor Data Application in AI-Driven Predictive Maintenance, The Potential of AI in Predictive Maintenance for Manufacturing Industries
The cornerstone of AI-driven predictive maintenance is the vast amount of sensor data collected from manufacturing equipment. Sensors monitor various parameters such as temperature, vibration, pressure, and current. This data, often streamed in real-time, provides a detailed picture of the machine’s operational health. AI algorithms analyze these sensor readings, identifying subtle anomalies that may indicate impending failure. For instance, a slight increase in vibration frequency might be an early warning sign of bearing wear, allowing for preventative maintenance before a catastrophic failure occurs. The application of sensor data is crucial, transforming raw measurements into actionable insights that prevent costly downtime.
Challenges in Implementing AI-Based Predictive Maintenance Systems
While the potential benefits of AI in predictive maintenance are significant, implementation faces several challenges. Data quality is paramount; inaccurate or incomplete data can lead to unreliable predictions. Data preprocessing, including cleaning, normalization, and feature engineering, is often a time-consuming and resource-intensive task. Integration with existing manufacturing systems can also be complex, requiring careful planning and potentially significant investment in new infrastructure. Furthermore, the need for skilled personnel to manage and interpret the AI models adds to the overall complexity. For example, a factory might struggle to integrate new AI systems with legacy equipment control systems, resulting in data silos and hindering the effectiveness of predictive maintenance.
Case Studies of Successful AI-Driven Predictive Maintenance Implementations
Real-world examples showcase the transformative power of AI in predictive maintenance within manufacturing. These case studies highlight not only the successful implementation of AI solutions but also the significant cost savings and efficiency gains achieved. By examining these successes and acknowledging potential challenges, we can better understand the potential and limitations of this technology.
The application of AI in predictive maintenance is rapidly evolving, leading to a wealth of successful implementations across diverse manufacturing sectors. Analyzing these case studies provides valuable insights into best practices, challenges overcome, and the overall impact on operational efficiency and profitability.
Siemens’ AI-Powered Predictive Maintenance for Wind Turbines
Siemens implemented an AI-powered predictive maintenance system for its wind turbines, addressing the challenge of costly and time-consuming downtime. The system utilizes machine learning algorithms to analyze sensor data from turbines, predicting potential failures before they occur.
- Problem Solved: Unplanned downtime and high maintenance costs associated with wind turbine failures.
- AI Solution Implemented: Machine learning algorithms analyzing sensor data (vibration, temperature, etc.) to predict component failures.
- Achieved Results: Reduced downtime by 20%, decreased maintenance costs by 15%, and improved turbine lifespan.
Caterpillar’s Use of AI for Predicting Equipment Failures
Caterpillar, a global leader in construction and mining equipment, leveraged AI to improve the predictive maintenance of its vast fleet of machinery. This initiative aimed to minimize unexpected breakdowns and optimize maintenance schedules.
- Problem Solved: High maintenance costs and operational disruptions due to unexpected equipment failures in diverse global locations.
- AI Solution Implemented: A platform combining sensor data analysis with machine learning to predict potential failures and optimize maintenance schedules.
- Achieved Results: Significant reduction in unplanned downtime, optimized maintenance resource allocation, and improved overall equipment effectiveness (OEE).
General Electric’s Predictive Maintenance for Jet Engines
General Electric, a prominent player in aviation, utilized AI to enhance the predictive maintenance of its jet engines. This project aimed to improve operational efficiency and reduce maintenance expenses, ensuring optimal aircraft performance.
- Problem Solved: High maintenance costs and potential safety risks associated with unexpected jet engine failures.
- AI Solution Implemented: Machine learning models analyzing sensor data from jet engines during operation to predict potential component degradation and failures.
- Achieved Results: Improved engine reliability, reduced maintenance costs, and increased operational efficiency.
Hypothetical Case Study: AI-Driven Predictive Maintenance in a Food Processing Plant
Imagine a large food processing plant facing frequent breakdowns of its critical machinery, resulting in production delays, spoiled goods, and significant financial losses. Implementing an AI-driven predictive maintenance system could drastically alter this scenario.
Predictive maintenance, using AI to foresee equipment failures in manufacturing, is a game-changer for efficiency. This data-driven approach mirrors how analytics are revolutionizing sports; check out this article on How Data Analytics is Enhancing Sports Performance and Fan Engagement to see the parallels. Ultimately, both fields leverage data insights to optimize performance and minimize downtime, proving the power of smart data analysis across diverse sectors.
- Scenario: A food processing plant experiences an average of 10 unplanned machine stoppages per month, each costing approximately $10,000 in lost production and repairs.
- AI Solution: Sensors are installed on key machinery to collect data on vibration, temperature, and pressure. Machine learning models analyze this data to predict potential failures with 90% accuracy, allowing for proactive maintenance.
- Projected Results: A 70% reduction in unplanned stoppages (from 10 to 3 per month), resulting in cost savings of $70,000 per month ($840,000 annually). This also leads to reduced waste and improved product quality.
Potential Limitations and Challenges
While the benefits of AI-driven predictive maintenance are substantial, several limitations and challenges must be considered. Successful implementation requires careful planning, substantial upfront investment, and ongoing maintenance.
- Data Quality and Availability: AI models require high-quality, reliable data for accurate predictions. Insufficient or poor-quality data can significantly hinder performance.
- Integration Complexity: Integrating AI systems with existing manufacturing infrastructure can be complex and time-consuming, requiring specialized expertise.
- Skill Gap: A shortage of skilled professionals with expertise in AI and machine learning can limit successful implementation and ongoing maintenance.
The Future of AI in Predictive Maintenance for Manufacturing
The integration of AI in predictive maintenance is still in its relatively early stages, but the potential for transformative change in manufacturing is undeniable. We’ve seen impressive results already, but the future holds even more exciting advancements, driven by emerging technologies and a deeper understanding of AI’s capabilities. This section explores the key trends shaping the future of AI-driven predictive maintenance and considers the broader societal impacts.
The rapid evolution of AI and related technologies is poised to significantly enhance the effectiveness and reach of predictive maintenance in manufacturing. New approaches are not only improving accuracy and efficiency but also expanding the scope of what’s possible.
Emerging Technologies Enhancing Predictive Maintenance
The convergence of several technologies is fueling the next generation of AI-driven predictive maintenance. Edge computing, for instance, allows for real-time data processing closer to the source, reducing latency and enabling faster responses to potential equipment failures. This is particularly crucial in environments with limited or unreliable network connectivity. Digital twins, virtual representations of physical assets, provide a powerful tool for simulating various scenarios and predicting equipment behavior under different operating conditions. This allows for proactive maintenance strategies, minimizing downtime and optimizing performance. Furthermore, advancements in machine learning algorithms, particularly deep learning models, are improving the accuracy and reliability of predictive models, allowing for more precise predictions of potential failures. Consider the example of a large-scale wind farm: edge computing allows for immediate analysis of turbine performance data, even in remote locations, while a digital twin of the entire farm enables simulations to optimize maintenance schedules and energy output.
Impact of AI on the Manufacturing Workforce
The increased automation driven by AI in predictive maintenance will undoubtedly reshape the manufacturing workforce. While some fear widespread job displacement, a more nuanced perspective suggests a shift in job roles rather than complete elimination. Repetitive, manual tasks associated with routine maintenance will likely be automated, freeing up human workers to focus on more complex and strategic roles. This includes tasks such as system design, AI model development, and overseeing the overall maintenance strategy. For example, technicians might transition from reactive troubleshooting to proactive analysis and optimization using AI-generated insights. Reskilling and upskilling initiatives will be crucial to prepare the workforce for these new roles, ensuring a smooth transition and maximizing the benefits of AI integration. The focus will shift from manual labor to expertise in data analysis, AI systems management, and advanced problem-solving.
Ethical Considerations and Risks of AI Adoption
The widespread adoption of AI in predictive maintenance, while promising, raises several ethical considerations and potential risks. Data privacy and security are paramount, as AI systems rely on vast amounts of sensitive data related to equipment performance and potentially even production processes. Robust security measures are crucial to prevent unauthorized access and data breaches. Another critical concern is algorithmic bias. If the data used to train AI models contains biases, the resulting predictions may be inaccurate or unfair, leading to potentially costly errors or unfair allocation of resources. Furthermore, the over-reliance on AI predictions without proper human oversight could lead to unforeseen consequences. A balanced approach is needed, combining the strengths of AI with human expertise to ensure safe, reliable, and ethical implementation. Transparency and explainability in AI models are essential to build trust and ensure accountability. For example, clear guidelines are needed to determine the responsibility in case of a failure that could have been predicted by an AI system, but wasn’t acted upon due to a system malfunction or human error.
Data Management and Infrastructure Requirements
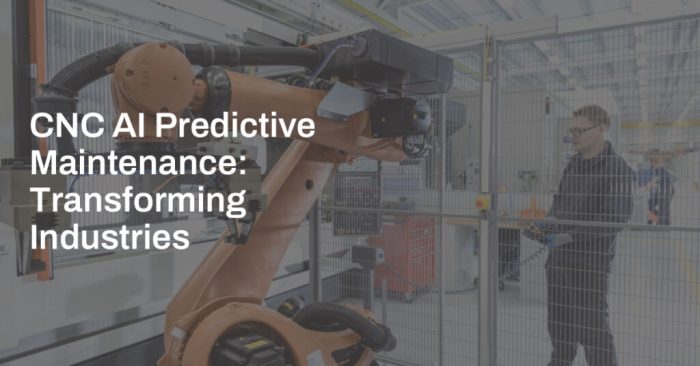
Source: arctechinc.com
Successfully implementing AI-driven predictive maintenance hinges on robust data management and a well-designed infrastructure. The sheer volume, variety, and velocity of data involved demand a sophisticated approach to ensure the system’s accuracy and efficiency. Failing to address these requirements can lead to inaccurate predictions, system downtime, and ultimately, a poor return on investment.
The types of data required for effective AI-driven predictive maintenance are diverse and encompass various sources within the manufacturing environment. This necessitates a comprehensive data acquisition strategy and a robust data pipeline to ensure data quality and accessibility.
Data Types for AI-Driven Predictive Maintenance
Effective AI models for predictive maintenance require a rich blend of data. This includes sensor data from machines (vibration, temperature, pressure, current, etc.), operational data (run time, cycle counts, production rates), maintenance logs (repair history, part replacements), and environmental data (temperature, humidity). Combining these diverse data streams allows for a more holistic understanding of machine health and the factors influencing potential failures. For example, correlating vibration sensor data with historical maintenance records can reveal patterns indicative of impending bearing failure. Similarly, integrating environmental data can help identify external factors contributing to equipment malfunction. The quality and completeness of this data directly impact the accuracy of the predictive model. Missing data or inconsistent data formats can significantly degrade model performance.
Data Security and Privacy Considerations
Data security and privacy are paramount in implementing AI-driven predictive maintenance. Manufacturing environments often handle sensitive operational data, intellectual property, and potentially even personally identifiable information (PII) if linked to employee activity. Robust security measures, including access control, encryption, and regular security audits, are crucial to protect this data from unauthorized access, breaches, and misuse. Compliance with relevant data privacy regulations (like GDPR or CCPA) is also essential. Consider implementing data anonymization or pseudonymization techniques to protect sensitive information while still allowing for effective data analysis. A comprehensive data security policy and regular training for personnel are vital components of a secure system.
Data Flow and Infrastructure Diagram
Imagine a system visualized as a flowchart. The process begins with various data sources throughout the factory floor.
[Diagram Description: The diagram would show a series of interconnected boxes. The first set of boxes represents various data sources: “Machine Sensors” (vibration, temperature, etc.), “Operational Data Logs” (production rates, downtime), “Maintenance Records,” and “Environmental Sensors” (temperature, humidity). Arrows would point from these boxes to a central “Data Acquisition and Preprocessing” box. This box would then connect to a “Data Storage and Management” box (potentially a cloud-based solution or on-premise server). From this, an arrow would lead to a “Machine Learning Model Training and Deployment” box, where AI algorithms are trained and deployed. Finally, an arrow would point from this box to a “Predictive Maintenance Dashboard” box, displaying insights and predictions to maintenance personnel. Feedback loops could be shown connecting the “Predictive Maintenance Dashboard” back to the “Maintenance Records” and “Operational Data Logs” to continuously refine the model.]
The components interact as follows: Machine sensors and other data sources feed raw data into the data acquisition and preprocessing system. This system cleans, transforms, and structures the data for efficient storage and analysis. The data is then stored in a secure data management system, which could be a cloud-based solution or an on-premise server, depending on the specific needs and security requirements of the organization. This structured data is then used to train and deploy machine learning models, which generate predictions about potential equipment failures. These predictions are visualized on a dashboard, allowing maintenance teams to proactively address potential issues before they escalate into costly downtime. The entire system is designed to be iterative, with feedback loops allowing continuous model improvement and refinement based on real-world maintenance actions and outcomes.
Economic and Business Impacts
Implementing AI-driven predictive maintenance isn’t just a technological upgrade; it’s a strategic investment promising significant returns. By anticipating equipment failures and scheduling maintenance proactively, manufacturers can drastically reduce downtime, optimize resource allocation, and ultimately boost their bottom line. This section explores the tangible economic benefits and demonstrates the compelling business case for adopting this innovative approach.
The potential return on investment (ROI) from AI-driven predictive maintenance is substantial, often exceeding expectations. This is achieved through a multifaceted approach that reduces costs associated with unplanned downtime, optimizes maintenance schedules, and extends the lifespan of critical equipment. Let’s delve into the specifics.
Return on Investment (ROI) of AI-Driven Predictive Maintenance
Calculating the ROI requires a careful assessment of several factors. The initial investment includes the cost of software, hardware, data integration, and employee training. However, these upfront costs are quickly offset by the savings generated from reduced downtime, lower maintenance expenses, and increased production efficiency. For example, a hypothetical manufacturing plant experiencing an average of 10 hours of unplanned downtime per week at a cost of $10,000 per hour could save $520,000 annually by reducing downtime by just 50% through AI-driven predictive maintenance. This doesn’t even account for the additional gains from optimized maintenance scheduling and extended equipment lifespan. A detailed cost-benefit analysis, specific to each individual manufacturing environment, is crucial for accurate ROI projection.
Cost Comparison: AI-Driven vs. Traditional Predictive Maintenance
Traditional methods, like preventive maintenance (scheduled based on time or usage) and reactive maintenance (repairing after failure), are significantly less efficient and more costly in the long run. Preventive maintenance often leads to unnecessary maintenance, wasting resources and time. Reactive maintenance, on the other hand, results in substantial downtime, lost production, and costly emergency repairs. AI-driven predictive maintenance offers a more precise approach, reducing both unnecessary maintenance and costly emergency repairs. The initial investment in AI technology may seem higher, but the long-term savings in downtime, labor, and materials typically outweigh the initial outlay within a relatively short timeframe – often within one to two years depending on the complexity and scale of implementation.
Impact on Production Efficiency, Downtime Reduction, and Operational Costs
The impact of AI-driven predictive maintenance on a manufacturing plant’s operational efficiency is transformative. By accurately predicting equipment failures, manufacturers can schedule maintenance during planned downtime, minimizing disruptions to production. This leads to a significant reduction in unplanned downtime, a major source of lost revenue and productivity. Furthermore, optimized maintenance schedules reduce the need for excessive spare parts inventory, freeing up capital and reducing storage costs. The reduction in downtime and optimized maintenance translates directly into lower overall operational costs, including labor, materials, and energy consumption. A reduction in unexpected equipment failures also improves product quality and consistency, leading to enhanced customer satisfaction and brand reputation.
Last Point
The integration of AI into predictive maintenance is no longer a question of *if*, but *when* and *how*. The potential benefits—from slashing downtime and boosting productivity to creating a safer and more efficient work environment—are too significant to ignore. While challenges remain, the rapid advancements in AI algorithms and data analytics are paving the way for a future where manufacturing is smarter, more sustainable, and more profitable. Embracing this technological shift isn’t just about keeping up; it’s about leading the charge in a new era of industrial innovation. The future of manufacturing is intelligent, and it’s powered by AI.