The Impact of Digital Twins on Manufacturing and Simulation is nothing short of revolutionary. Forget clunky, outdated models – digital twins are creating a whole new world of possibilities. Imagine a perfect virtual replica of your factory floor, allowing you to test new processes, predict failures, and optimize efficiency before even touching a single machine. This isn’t science fiction; it’s the rapidly evolving reality of modern manufacturing, offering unprecedented levels of control and insight.
From streamlining product design and development to revolutionizing supply chain management, digital twins are reshaping the manufacturing landscape. We’ll dive into the specifics of how these virtual counterparts are enhancing simulation accuracy, enabling predictive maintenance, and ultimately driving significant cost savings and improved product quality. Get ready to witness the future of manufacturing, one digital twin at a time.
Introduction to Digital Twins in Manufacturing
Forget science fiction; digital twins are revolutionizing manufacturing. They’re virtual representations of physical assets, processes, or systems, mirroring their real-world counterparts in astonishing detail. This allows manufacturers to test, optimize, and predict performance before ever touching a physical component, saving time, money, and resources. Think of it as having a perfect, always-updated digital clone of your factory floor, ready to answer any “what if” scenario.
Digital twins are far more than just advanced simulations. Their evolution from basic computer-aided design (CAD) models to sophisticated, data-driven platforms reflects a paradigm shift in manufacturing. Early simulations focused primarily on individual components or simple processes. Today’s digital twins leverage the power of IoT (Internet of Things) sensors, machine learning, and big data analytics to create dynamic, real-time representations that continuously learn and adapt. This allows for far more accurate predictions and a deeper understanding of complex systems.
Digital Twin Components
A comprehensive digital twin requires a combination of key elements. These include a detailed 3D CAD model of the physical asset, a data acquisition system to gather real-time information from sensors and other sources, a simulation engine to model the behavior of the asset under various conditions, and a powerful analytics platform to process and interpret the vast amounts of data generated. Furthermore, advanced digital twins often incorporate AI and machine learning algorithms for predictive maintenance and optimization. The integration of all these components is crucial for creating a truly accurate and useful representation.
Types of Digital Twins in Manufacturing
The application of digital twin technology spans a wide range of manufacturing scenarios. Different types of digital twins address specific needs and provide unique benefits.
Product Digital Twins
Product digital twins are virtual representations of individual products. They allow manufacturers to simulate product performance under various conditions, identify potential design flaws, and optimize product design for durability, efficiency, and cost-effectiveness. For example, a car manufacturer might use a product digital twin to simulate crash tests or predict the lifespan of specific components, reducing the need for expensive and time-consuming physical prototypes.
Process Digital Twins
Process digital twins focus on modeling and optimizing manufacturing processes. These twins allow manufacturers to simulate entire production lines, identify bottlenecks, and improve efficiency. For instance, a pharmaceutical company might use a process digital twin to simulate drug manufacturing processes, optimize parameters such as temperature and pressure, and predict potential quality control issues. This leads to reduced waste and improved product quality.
System Digital Twins
System digital twins encompass the entire manufacturing ecosystem, including machines, processes, and even the supply chain. They provide a holistic view of the manufacturing operation, allowing for improved coordination and optimization across all aspects of the business. Imagine a smart factory where a system digital twin monitors everything from individual machine performance to energy consumption and material flow, enabling proactive adjustments and predictive maintenance to minimize downtime and maximize efficiency. This integrated approach leads to significant cost savings and enhanced operational resilience.
Applications of Digital Twins in Simulation
Digital twins are revolutionizing manufacturing by offering a powerful tool for simulation and optimization. They go beyond traditional methods by creating a virtual representation of a physical asset, allowing for highly accurate and efficient simulations that provide crucial insights into performance, potential failures, and optimization opportunities. This allows manufacturers to test and refine processes in the virtual world, minimizing costly real-world experimentation.
Digital twins enhance simulation accuracy and efficiency by integrating real-time data from sensors and other sources. This constant feedback loop ensures that the virtual model accurately reflects the state of the physical asset, leading to more reliable predictions. Traditional simulation methods often rely on static data and assumptions, which can lead to inaccuracies and less effective optimization strategies. The dynamic nature of digital twins, coupled with their ability to incorporate diverse data sources, provides a significant advantage in creating highly realistic and detailed simulations.
Enhanced Simulation Accuracy and Efficiency
The integration of real-time data from the physical asset into the digital twin significantly improves simulation accuracy. This contrasts with traditional simulation methods, which often rely on estimations and historical data, leading to potential discrepancies between the simulation results and actual performance. For instance, a digital twin of a robotic arm can incorporate data on its current temperature, wear and tear, and operational speed, leading to a much more accurate simulation of its performance under various conditions compared to a model based solely on design specifications. Furthermore, the ability to perform “what-if” scenarios quickly and efficiently, without impacting the physical asset, makes digital twins significantly more efficient for testing and optimization.
Comparison of Digital Twin and Traditional Simulation Methods
Traditional simulation methods, while valuable, often struggle with the complexity and dynamic nature of modern manufacturing processes. They typically use simplified models and static data, which can lead to inaccuracies. Digital twins, on the other hand, offer a much more detailed and dynamic representation. They incorporate real-time data from the physical asset, allowing for a much more accurate reflection of its behavior. This means that digital twin simulations can provide more reliable predictions and lead to more effective optimization strategies. The ability to integrate various data sources, such as sensor data, CAD models, and process parameters, further enhances the accuracy and detail of the simulation.
Predictive Maintenance and Fault Detection using Digital Twins
Digital twins are exceptionally useful for predictive maintenance. By continuously monitoring the digital twin’s performance, manufacturers can identify potential issues before they lead to costly downtime. For example, a digital twin of a machine might detect an anomaly in its vibration patterns, indicating potential bearing failure. This early warning allows for preventative maintenance, minimizing the risk of unexpected breakdowns. This contrasts sharply with traditional reactive maintenance strategies, where maintenance is only performed after a failure has occurred. The predictive capabilities of digital twins significantly reduce downtime, increase efficiency, and lower maintenance costs.
Optimizing a Manufacturing Process using a Digital Twin: A Hypothetical Scenario
Let’s consider a hypothetical scenario involving a bottling plant. The plant uses a filling line with a target filling rate of 100 bottles per minute. Before implementing a digital twin, the filling line frequently experienced bottlenecks, leading to inconsistent filling rates and increased waste. After implementing a digital twin, engineers could simulate various changes to the line, such as adjusting conveyor belt speeds or optimizing valve settings. The simulation identified optimal settings that improved the filling rate and reduced waste.
Parameter | Before Optimization | After Optimization | Improvement Percentage |
---|---|---|---|
Bottles per minute | 90 | 105 | 16.67% |
Waste percentage | 5% | 1% | 80% |
Downtime (hours/week) | 8 | 2 | 75% |
Energy Consumption (kWh/hour) | 150 | 135 | 10% |
Impact on Manufacturing Processes
Digital twins are revolutionizing manufacturing, offering a virtual mirror of real-world processes that allows for unprecedented optimization and efficiency. This virtual representation enables manufacturers to test, analyze, and improve their operations before implementing changes in the physical world, minimizing risk and maximizing return on investment. The impact spans across various stages of the manufacturing lifecycle, from design and development to supply chain management and final product delivery.
The integration of digital twins significantly enhances several key manufacturing processes. Their impact is particularly profound in areas where real-world experimentation is costly, time-consuming, or simply impossible.
Impact on Product Design and Development
Digital twins accelerate product design and development by allowing engineers to virtually test and refine designs before physical prototypes are created. This iterative process significantly reduces development time and costs, enabling faster time-to-market. For instance, a manufacturer of automotive parts could use a digital twin to simulate the performance of a new engine component under various stress conditions, identifying potential weaknesses and optimizing its design for durability and efficiency. This virtual testing reduces the need for expensive and time-consuming physical prototypes, saving both time and resources. Moreover, the digital twin can be used to explore different design iterations, leading to improved product performance and reduced material waste.
Improved Supply Chain Management and Logistics
Digital twins provide real-time visibility into the entire supply chain, from raw material sourcing to finished product delivery. This enhanced visibility enables manufacturers to proactively identify and mitigate potential disruptions, such as delays or shortages. Imagine a manufacturer of electronics using a digital twin to simulate the impact of a factory closure due to a natural disaster. The twin could predict the ripple effects on the supply chain, allowing the manufacturer to quickly identify alternative sourcing options and minimize production downtime. Furthermore, digital twins can optimize logistics by simulating different transportation routes and warehouse layouts, identifying the most efficient and cost-effective solutions. This leads to reduced transportation costs and improved on-time delivery.
Challenges in Implementing Digital Twin Technology
Implementing digital twin technology in manufacturing presents several challenges. Overcoming these hurdles is crucial for successful adoption and realization of the technology’s full potential.
- Data Acquisition and Integration: Creating an accurate digital twin requires collecting and integrating vast amounts of data from various sources, which can be complex and time-consuming.
- Computational Resources: Simulating complex manufacturing processes requires significant computing power, potentially leading to high infrastructure costs.
- Data Security and Privacy: Protecting sensitive manufacturing data is crucial, and robust security measures are essential to prevent unauthorized access or breaches.
- Skills Gap: Implementing and managing digital twin technology requires specialized skills and expertise, which may be in short supply.
- Interoperability: Ensuring seamless data exchange between different software systems and hardware components is critical for effective digital twin implementation.
Data Acquisition and Management for Digital Twins: The Impact Of Digital Twins On Manufacturing And Simulation
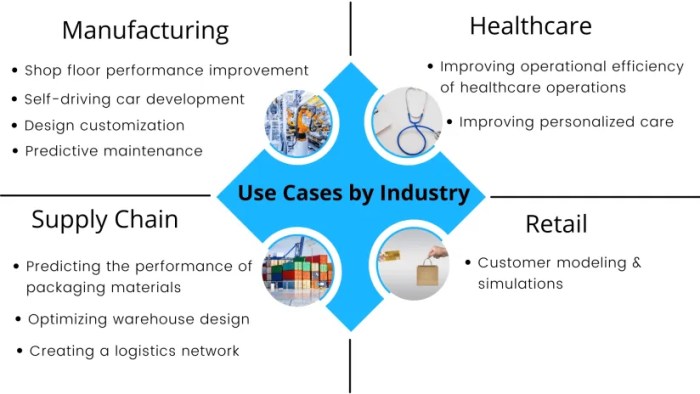
Source: aimultiple.com
Digital twins are revolutionizing manufacturing, offering unparalleled simulation capabilities before physical production. This mirrors the evolution of personalized experiences, much like the sophisticated AI driving digital assistants, as detailed in The Evolution of Digital Assistants and Their Impact on Daily Life. Ultimately, both technologies promise increased efficiency and optimized outcomes, impacting everything from factory floors to our smartphones.
Building a robust and reliable digital twin requires a constant influx of accurate data. This data fuels the twin’s ability to mirror real-world processes and predict future behavior. Effective data acquisition and management are therefore critical for the success of any digital twin initiative in manufacturing and simulation. Without a well-defined strategy, the twin risks becoming an inaccurate, unusable representation of reality.
Data sources for creating and updating a digital twin are diverse and often complex. They range from traditional sensors and manufacturing equipment to advanced simulation tools and external databases. The ability to integrate and harmonize data from these disparate sources is a key challenge, but also a crucial component for building a holistic and useful digital twin.
Data Sources for Digital Twins, The Impact of Digital Twins on Manufacturing and Simulation
Digital twins draw data from a variety of sources, each contributing a unique piece of the overall picture. These sources can be broadly categorized into direct and indirect data streams. Direct data comes directly from the physical asset being mirrored, while indirect data is derived from other sources, providing contextual information.
- Sensors and Instrumentation: Sensors embedded in machinery, equipment, and products provide real-time data on temperature, pressure, vibration, speed, and other crucial parameters. Examples include temperature sensors on a production line, vibration sensors on a robot arm, or pressure sensors in a hydraulic system.
- Manufacturing Execution Systems (MES): MES systems provide detailed information about production processes, including work orders, production schedules, and machine utilization. This data is crucial for understanding the context of the sensor data and for predicting potential bottlenecks.
- Computer-Aided Design (CAD) Models: CAD models provide the initial geometric and structural information for the digital twin. They serve as the foundational blueprint, onto which real-time data is overlaid.
- Enterprise Resource Planning (ERP) Systems: ERP systems provide high-level information about the business context, including inventory levels, sales forecasts, and supply chain data. This data can be used to optimize production schedules and predict future demand.
- Simulation Models: Simulation models can provide predictions about the behavior of the physical asset under different operating conditions. These predictions can be used to refine the digital twin and improve its accuracy.
- External Databases: Data from external sources, such as weather data (affecting outdoor equipment), market trends, or material specifications, can also be incorporated to provide a broader context for the digital twin.
Ensuring Data Accuracy and Reliability
The accuracy and reliability of the data feeding the digital twin are paramount. Inaccurate data leads to flawed predictions and ultimately, poor decision-making. Several strategies are crucial for maintaining data quality.
- Data Validation and Cleaning: Implementing robust data validation and cleaning processes is essential to identify and correct errors before they impact the digital twin. This includes checking for inconsistencies, outliers, and missing values.
- Sensor Calibration and Maintenance: Regular calibration and maintenance of sensors are crucial for ensuring the accuracy of the data they collect. Calibration procedures should be clearly defined and documented.
- Data Redundancy and Cross-Verification: Using multiple sensors to measure the same parameter allows for cross-verification and detection of faulty readings. Redundancy enhances data reliability.
- Data Quality Metrics: Tracking key data quality metrics, such as accuracy, completeness, and consistency, allows for continuous monitoring and improvement of data quality.
Managing and Securing Large Volumes of Data
Digital twins generate massive amounts of data. Effective management and security strategies are vital to handle this volume efficiently and securely.
- Data Storage and Retrieval: Employing efficient data storage solutions, such as cloud-based storage or specialized databases optimized for time-series data, is essential. Efficient data retrieval mechanisms are equally important for timely access to information.
- Data Compression and Aggregation: Techniques like data compression and aggregation can reduce the storage space required and improve data processing speed. Aggregation involves summarizing data into higher-level representations.
- Data Security and Access Control: Implementing robust security measures, including encryption, access control, and regular security audits, is crucial to protect sensitive data from unauthorized access and cyber threats. This is especially important in manufacturing environments where sensitive operational data is involved.
Data Flow in a Digital Twin
A flowchart depicting the data flow would show various data sources (sensors, MES, CAD, ERP, simulation models, external databases) converging into a central data hub. This hub preprocesses, validates, and cleans the data before feeding it into the digital twin model. The digital twin then processes this data, generating insights, predictions, and visualizations. Feedback loops would show how the insights generated by the digital twin can influence the real-world processes, creating a continuous cycle of data acquisition, analysis, and action. The system would also include mechanisms for data security and access control throughout the entire process.
Economic and Business Impacts
Digital twins are rapidly transforming manufacturing, offering significant economic and business advantages beyond simply improved efficiency. The potential return on investment (ROI) is substantial, driven by reduced costs, enhanced quality, and improved workforce capabilities. This section explores the tangible financial benefits and strategic advantages realized through digital twin implementation.
The potential return on investment (ROI) from implementing digital twins varies depending on the specific application and industry. However, numerous case studies demonstrate significant cost savings and efficiency gains. These gains stem from optimized processes, reduced waste, and proactive problem-solving enabled by the virtual representation of physical assets. The long-term benefits often outweigh the initial investment costs, making digital twins a compelling strategic investment for forward-thinking manufacturers.
Return on Investment (ROI) and Cost Savings
Realizing a strong ROI with digital twins requires a well-defined strategy and meticulous implementation. Cost savings are typically realized through several key mechanisms. Firstly, the ability to simulate various scenarios before physical implementation drastically reduces the risk of costly errors and rework. Secondly, predictive maintenance capabilities, enabled by the twin’s real-time data analysis, minimize downtime and extend the lifespan of equipment. Thirdly, optimized production processes, identified through simulations and data analysis, lead to reduced material waste and energy consumption. For instance, a hypothetical automotive manufacturer might reduce paint waste by 15% and machine downtime by 10% annually through effective digital twin implementation, resulting in significant cost savings. A similar scenario could be seen in the aerospace industry, where simulations could reduce the number of prototypes needed for testing and validation, resulting in substantial cost savings.
Improved Product Quality and Reduced Waste
Digital twins play a pivotal role in enhancing product quality and minimizing waste throughout the manufacturing lifecycle. By simulating the entire production process virtually, manufacturers can identify potential defects and bottlenecks early on, leading to proactive corrective actions. This preemptive approach significantly reduces the likelihood of producing defective products and minimizes the need for costly rework or scrap. Imagine a pharmaceutical company using a digital twin to simulate the drug manufacturing process. The twin could pinpoint potential contamination risks or inefficiencies in the process, leading to higher product quality and reduced waste of expensive raw materials. This level of precision translates directly into higher profit margins and enhanced brand reputation.
Impact on Workforce Training and Skill Development
Digital twins offer a revolutionary approach to workforce training and skill development. They provide a safe and cost-effective environment to simulate real-world scenarios, allowing employees to practice complex tasks and troubleshoot problems without risking damage to physical equipment or production delays. This immersive learning experience improves employee competency, fosters innovation, and prepares the workforce for the demands of advanced manufacturing technologies. For example, a factory worker can use a digital twin to practice operating a complex piece of machinery, identifying potential issues and resolving them before working on the actual equipment. This reduces the learning curve, improves safety, and enhances productivity. Furthermore, digital twins can be used to train employees on new processes and procedures, ensuring a smooth transition to new technologies and minimizing disruptions to production.
Future Trends and Challenges
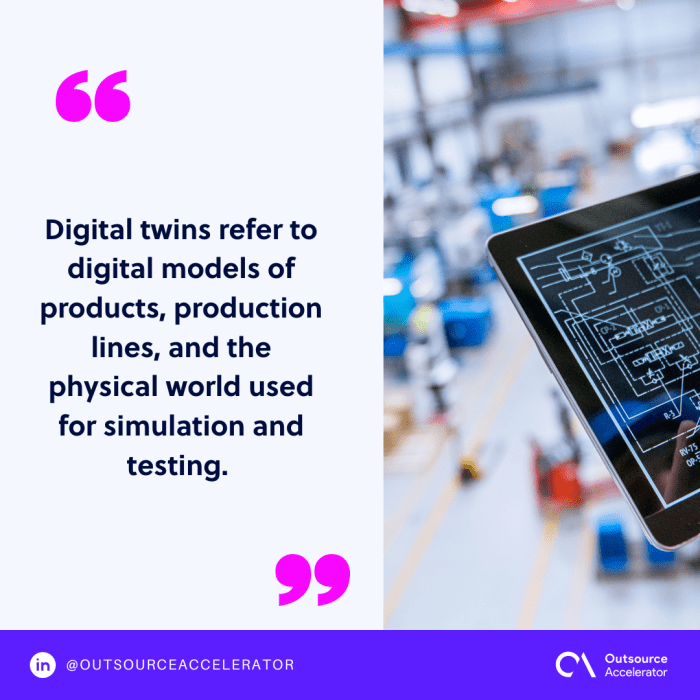
Source: outsourceaccelerator.com
The world of digital twins in manufacturing is rapidly evolving, presenting both exciting opportunities and significant hurdles. While the current applications are impressive, the future holds even more transformative potential, demanding innovative solutions to address emerging challenges. The path forward requires a concerted effort in technological advancement, data management, and collaborative standardization.
The integration of digital twins into manufacturing processes is poised for exponential growth, driven by advancements in AI, IoT, and cloud computing. However, realizing this potential hinges on overcoming obstacles related to data interoperability and the standardization of data formats. Successfully navigating these challenges will unlock a new era of efficiency, productivity, and innovation in the manufacturing sector.
Emerging Trends in Digital Twin Technology
Several key trends are shaping the future of digital twin technology. The increasing sophistication of AI and machine learning algorithms is enabling the creation of more accurate and predictive digital twins. This includes the use of advanced simulation techniques to model complex manufacturing processes with greater fidelity. Furthermore, the rise of edge computing is allowing for real-time data processing and analysis, leading to faster response times and improved decision-making. Finally, the development of more user-friendly interfaces is making digital twin technology more accessible to a wider range of users, accelerating its adoption across various industries. For instance, General Electric’s use of digital twins for jet engine maintenance allows for predictive maintenance, minimizing downtime and maximizing operational efficiency.
Challenges Related to Interoperability and Data Standardization
A major challenge facing the widespread adoption of digital twins is the lack of interoperability between different software systems and data formats. Different manufacturers often use proprietary systems, making it difficult to integrate data from various sources into a unified digital twin. This necessitates the development of standardized data formats and protocols to ensure seamless data exchange between different systems. Without standardization, the cost and complexity of creating and maintaining digital twins will remain high, hindering their widespread adoption. The lack of a universal standard for data exchange significantly impacts the efficiency and effectiveness of digital twin implementation.
Innovative Applications in Advanced Manufacturing
Digital twins are revolutionizing advanced manufacturing techniques. In additive manufacturing, digital twins enable the simulation and optimization of the 3D printing process, predicting potential defects and improving the quality of the final product. Robotics benefits from digital twins through improved robot programming and control, enabling the creation of more flexible and efficient robotic systems. For example, a company might use a digital twin to simulate the assembly process of a complex product using robots, optimizing the robot movements to minimize cycle time and prevent collisions. Similarly, in additive manufacturing, a digital twin can predict potential defects based on the printing parameters and material properties, leading to a higher success rate and reduced waste.
A Future Manufacturing Facility Utilizing Digital Twin Technology
Imagine a future manufacturing facility where every machine, robot, and process is represented by a highly accurate digital twin. These twins are constantly updated with real-time data from sensors and other monitoring systems, providing a comprehensive view of the facility’s operations. AI-powered algorithms analyze this data to identify potential problems before they occur, enabling proactive maintenance and preventing costly downtime. The facility utilizes advanced simulation capabilities to optimize production processes, reducing waste and improving efficiency. Robots work collaboratively with human operators, guided by digital twins that provide real-time feedback and guidance. The entire production process is seamlessly integrated, with digital twins facilitating communication and coordination between different departments and systems. This results in a highly efficient, flexible, and responsive manufacturing environment, capable of adapting quickly to changing market demands.
Wrap-Up
The integration of digital twins into manufacturing and simulation processes isn’t just a trend; it’s a necessity for staying competitive in today’s rapidly evolving industrial world. By leveraging the power of virtual representations, businesses can unlock unprecedented levels of efficiency, reduce waste, and anticipate challenges before they arise. The potential for cost savings, improved product quality, and enhanced decision-making is immense, paving the way for a future where manufacturing is smarter, faster, and more sustainable. The journey towards fully realizing the potential of digital twins is ongoing, but the impact is already undeniable.