The Growing Role of Smart Sensors in Industrial Automation – Smart Sensors: Revolutionizing Industrial Automation. Forget clunky, outdated systems; the industrial world is undergoing a seismic shift thanks to the rise of smart sensors. These aren’t your grandpappy’s sensors – we’re talking about sophisticated devices that collect, analyze, and transmit data in real-time, leading to unprecedented levels of efficiency and optimization across various sectors. From manufacturing floors humming with predictive maintenance to smart grids powering our cities, the impact is undeniable. This deep dive explores how these intelligent tools are transforming industries and what the future holds.
This article will unpack the evolution of smart sensors, exploring their key characteristics and diverse applications across manufacturing, energy, and logistics. We’ll delve into data acquisition and analysis techniques, communication protocols, and the crucial aspect of cybersecurity in this interconnected world. Finally, we’ll weigh the benefits against the challenges, examining the ROI and exploring future trends powered by IoT, AI, and cloud computing.
Introduction to Smart Sensors in Industrial Automation
The industrial landscape has undergone a dramatic transformation, fueled by the relentless march of technological advancement. This evolution is nowhere more apparent than in the realm of sensors, the unsung heroes quietly collecting data that drives efficiency and innovation. From simple, analog devices to the sophisticated smart sensors of today, the journey reflects a paradigm shift in how we monitor and control industrial processes.
Smart sensors represent a significant leap forward, offering capabilities far beyond their predecessors. They are no longer mere data collectors; they are intelligent nodes within a larger network, capable of processing information, making decisions, and communicating their findings autonomously. This intelligence significantly enhances their value in industrial automation, enabling proactive maintenance, improved process optimization, and enhanced safety measures.
Key Characteristics of Smart Sensors
Smart sensors are distinguished by a combination of features that set them apart from their less sophisticated counterparts. These characteristics include embedded microprocessors for data processing, self-diagnostic capabilities for identifying and reporting malfunctions, and communication protocols (like wireless technologies) for seamless integration into larger networks. Furthermore, smart sensors often incorporate advanced algorithms for data analysis, enabling them to identify trends and anomalies that might otherwise go unnoticed. This level of sophistication allows for more accurate and timely responses to changing conditions within an industrial environment.
Examples of Smart Sensors in Industrial Automation
A variety of smart sensor types are employed across diverse industrial applications. Their specific capabilities are tailored to meet the unique demands of each environment. The following table provides a snapshot of some common examples:
Sensor Type | Application | Advantages | Limitations |
---|---|---|---|
Temperature Sensor (with wireless communication) | Monitoring temperature in ovens, furnaces, and other high-heat processes; early detection of overheating. | Real-time monitoring, remote access to data, early warning of potential failures. | Susceptibility to electromagnetic interference, potential for drift over time requiring recalibration. |
Pressure Sensor (with built-in diagnostics) | Monitoring pressure in pipelines, hydraulic systems, and pneumatic equipment. | Accurate and reliable pressure readings, self-diagnosis of sensor faults, reduced downtime. | Limited lifespan due to wear and tear, potential for damage from extreme pressure fluctuations. |
Proximity Sensor (with integrated safety features) | Detecting the presence of objects near machinery, preventing collisions and injuries. | Enhanced safety, increased productivity by preventing collisions, reduced maintenance costs. | Limited range, potential for false readings due to environmental factors (dust, moisture). |
Vibration Sensor (with predictive maintenance algorithms) | Monitoring vibrations in rotating machinery (motors, pumps, turbines) to detect early signs of wear. | Predictive maintenance, reduced downtime, optimized maintenance schedules, improved equipment lifespan. | Complexity of data analysis, requires specialized software and expertise for interpretation. |
Applications of Smart Sensors Across Industries
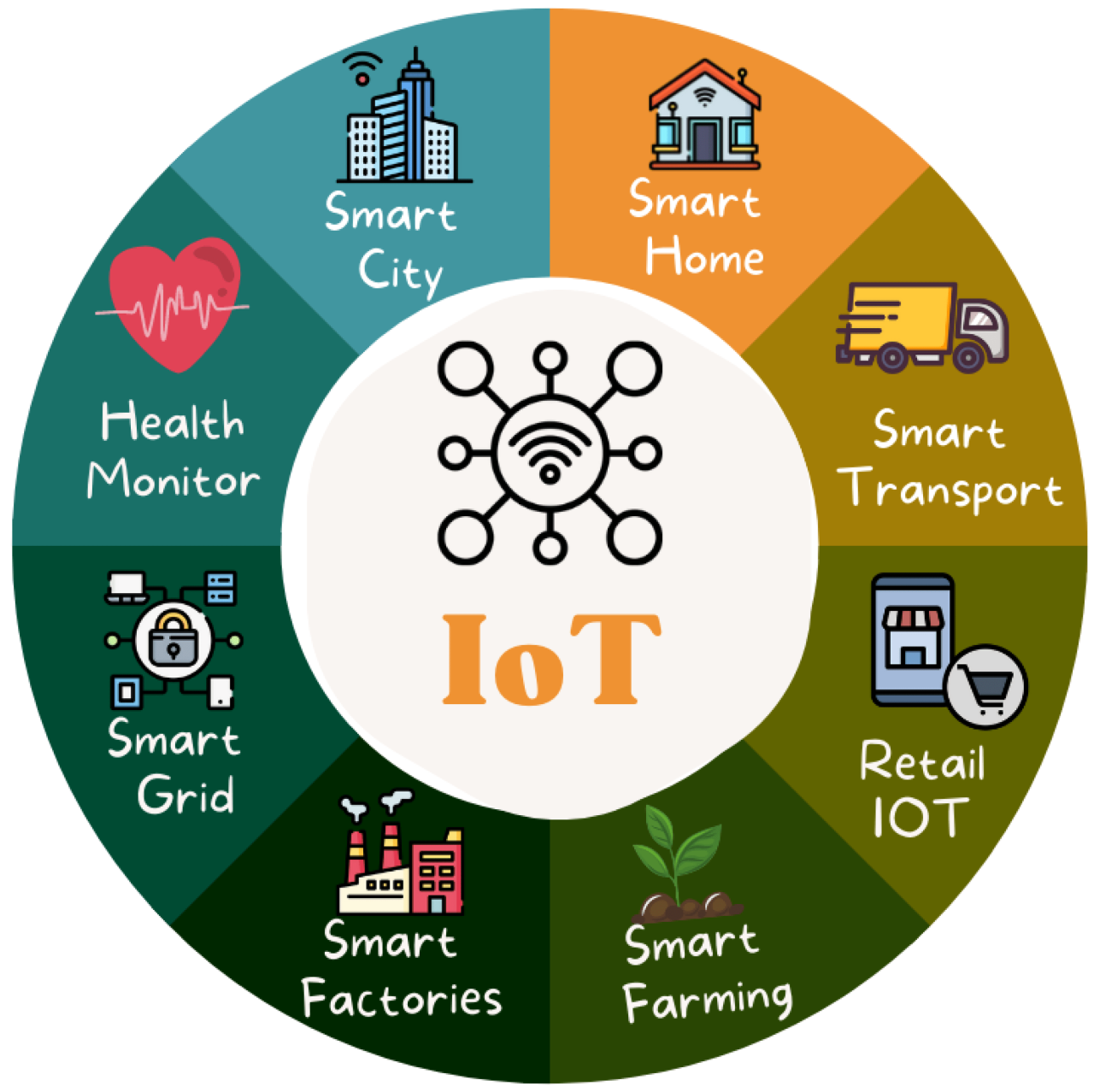
Source: mdpi-res.com
Smart sensors are no longer a futuristic fantasy; they’re revolutionizing industries, driving efficiency, and boosting productivity in ways previously unimaginable. Their ability to collect, analyze, and transmit data in real-time is transforming how businesses operate, from manufacturing floors to sprawling energy grids. This section delves into the diverse applications of smart sensors across key sectors.
Smart Sensors in Manufacturing Processes
The integration of smart sensors in manufacturing is leading to significant improvements in quality control and predictive maintenance, ultimately boosting production efficiency and reducing downtime. These advancements allow manufacturers to move beyond reactive maintenance to a proactive, data-driven approach.
- Quality Control: Smart sensors embedded within production lines provide real-time data on product dimensions, material properties, and other critical quality parameters. This allows for immediate identification and correction of defects, minimizing waste and ensuring consistent product quality. For instance, vision systems equipped with smart sensors can detect minute flaws in manufactured components, preventing faulty products from reaching the market.
- Predictive Maintenance: By monitoring the operational parameters of machinery (vibration, temperature, pressure), smart sensors can predict potential equipment failures before they occur. This allows for scheduled maintenance to be performed proactively, minimizing unplanned downtime and reducing costly repairs. Imagine a scenario where a sensor detects an unusual vibration pattern in a critical machine, alerting maintenance personnel to a potential bearing failure days in advance.
- Process Optimization: Smart sensors can optimize manufacturing processes by providing real-time feedback on variables such as temperature, pressure, and flow rate. This data allows manufacturers to fine-tune their processes, improving efficiency and reducing energy consumption. A smart sensor network monitoring a chemical reaction can automatically adjust parameters to maintain optimal reaction conditions.
Smart Sensors in the Energy Sector
The energy sector is undergoing a significant transformation driven by the adoption of smart sensors. From optimizing energy grids to monitoring renewable energy sources, smart sensors are playing a crucial role in enhancing efficiency, reliability, and sustainability.
Energy Sector | Sensor Applications | Benefits |
---|---|---|
Oil & Gas | Monitoring pipeline pressure and flow, detecting leaks, optimizing extraction processes, predictive maintenance of drilling equipment. | Improved safety, reduced environmental impact, enhanced efficiency, minimized downtime. |
Solar | Monitoring solar panel performance (power output, temperature), detecting faults, optimizing energy harvesting. | Increased energy generation, reduced maintenance costs, improved grid integration. |
Wind | Monitoring wind turbine performance (speed, power output, vibration), detecting faults, optimizing energy capture. | Enhanced energy generation, reduced downtime, improved safety. |
Smart Sensors in Logistics and Supply Chain Management
Smart sensors are revolutionizing logistics and supply chain management by providing real-time visibility into the movement and condition of goods. This enhanced visibility enables companies to optimize their operations, reduce costs, and improve customer satisfaction.
Real-world applications include:
- Real-time Tracking: GPS-enabled smart sensors attached to shipping containers or individual packages provide real-time location data, allowing companies to monitor the progress of their shipments and anticipate potential delays. This information can be used to optimize routes and improve delivery times.
- Inventory Management: Smart sensors can be used to monitor inventory levels in warehouses, providing real-time data on stock levels. This helps companies to avoid stockouts and overstocking, improving inventory management efficiency. Imagine a warehouse where sensors automatically track the number of items on shelves, sending alerts when stock falls below a certain threshold.
- Condition Monitoring: Smart sensors can monitor the environmental conditions (temperature, humidity) within shipping containers, ensuring that goods are transported under optimal conditions. This prevents damage to temperature-sensitive goods, reducing losses and improving product quality. A sensor monitoring temperature inside a refrigerated truck can alert drivers to potential issues, preventing spoilage of perishable goods.
Data Acquisition and Analysis from Smart Sensors
Smart sensors aren’t just passively collecting data; they’re the nervous system of modern industrial automation, constantly feeding a stream of information that needs to be effectively captured and interpreted to drive efficiency and innovation. The methods used for data acquisition and the subsequent analysis are crucial for unlocking the full potential of these intelligent devices. This section delves into the practicalities of getting data from sensors and turning that raw information into actionable insights.
Data acquisition from smart sensors involves a multi-step process tailored to the specific sensor type and the overall industrial environment. Different sensors employ various communication protocols, ranging from simple analog signals to sophisticated digital interfaces like Ethernet/IP, Modbus, or Profibus. The method of data acquisition directly impacts the speed, accuracy, and efficiency of the overall system.
Methods for Data Acquisition from Smart Sensors
Data acquisition techniques are diverse, reflecting the variety of smart sensors used in industrial settings. For example, sensors with analog outputs often require analog-to-digital converters (ADCs) to translate continuous signals into discrete digital values that computers can understand. Digital sensors, conversely, often transmit data directly via established communication protocols. Wireless sensors rely on radio frequency (RF) or other wireless technologies, requiring specialized receivers and data handling protocols. The choice of acquisition method depends on factors like sensor type, required data rate, distance to the data acquisition system, and environmental considerations.
Data Analysis Techniques for Sensor Data Interpretation
Raw sensor data is essentially meaningless without interpretation. Sophisticated data analysis techniques are employed to extract valuable information. Statistical methods, such as descriptive statistics (mean, standard deviation, etc.) and hypothesis testing, can identify trends and anomalies. More advanced techniques leverage machine learning (ML) algorithms. For example, supervised learning models can be trained on historical sensor data to predict equipment failures or optimize processes. Unsupervised learning techniques, such as clustering, can help identify patterns and groupings within the data that might not be immediately apparent. Predictive maintenance, for instance, heavily relies on machine learning algorithms trained on sensor data to forecast equipment failures and schedule maintenance proactively. A real-world example is a manufacturing plant using sensor data from vibration sensors on machines to predict bearing failures, enabling preventative maintenance and minimizing costly downtime.
Workflow Diagram for Sensor Data in a Factory Environment, The Growing Role of Smart Sensors in Industrial Automation
Consider a simplified workflow for a factory setting utilizing smart sensors for predictive maintenance on a robotic arm:
Imagine a diagram showing the following steps:
- Sensor Data Acquisition: Multiple sensors (vibration, temperature, pressure) on the robotic arm continuously collect data.
- Data Transmission: This data is transmitted wirelessly via a secure network (e.g., Industrial IoT platform) to a central server.
- Data Preprocessing: The data undergoes cleaning, filtering, and transformation to remove noise and inconsistencies.
- Feature Engineering: Relevant features are extracted from the data (e.g., frequency components from vibration data).
- Machine Learning Model Application: A trained machine learning model (e.g., a recurrent neural network) analyzes the features to predict potential failures.
- Alert Generation and Action: If the model predicts a high probability of failure, an alert is generated, triggering preventative maintenance actions.
This diagram visually represents the seamless flow of data from the sensors to actionable insights, highlighting the crucial role of data analysis in optimizing factory operations and preventing costly disruptions. The specific technologies and algorithms used would vary based on the complexity and requirements of the factory environment.
Communication Protocols and Network Infrastructure
The heart of any successful smart sensor implementation in industrial automation lies in its communication network. Choosing the right protocols and designing a robust infrastructure are crucial for efficient data transfer, system reliability, and overall operational success. The wrong choices can lead to bottlenecks, data loss, and even complete system failure. This section delves into the various communication protocols and the critical considerations for building a resilient network infrastructure for smart sensors.
Smart sensors employ a variety of communication protocols, each with its own strengths and weaknesses. The selection of a protocol depends heavily on factors like the application’s requirements for speed, distance, cost, and complexity. Choosing the wrong protocol can significantly impact efficiency and cost-effectiveness.
Comparison of Industrial Communication Protocols
Several protocols are commonly used for industrial communication. The following table compares key features of some popular options, highlighting their suitability for different applications.
Protocol | Speed | Distance | Topology | Cost | Typical Applications |
---|---|---|---|---|---|
Modbus | Low to Medium | Short to Medium | Master-Slave | Low | Simple SCADA systems, smaller automation projects |
Profibus | Medium to High | Medium to Long | Various (bus, ring, star) | Medium | Process automation, factory automation, robotics |
Ethernet/IP | High | Long | Various (bus, star, ring) | High | Complex automation systems, large-scale industrial networks, IIoT applications |
Profinet | High | Long | Various (bus, star, ring) | Medium to High | Complex automation systems, large-scale industrial networks, requiring high speed and determinism |
Network Infrastructure Design Considerations
Designing a reliable network infrastructure for a large number of smart sensors requires careful planning. Key considerations include network topology, redundancy, security, and scalability. A poorly designed network can lead to significant downtime and data loss, impacting productivity and potentially causing safety hazards.
For instance, a ring topology offers redundancy; if one segment fails, the network can still function. However, it’s more complex to implement than a simpler bus topology. Redundancy, achieved through mechanisms like dual network cards or backup network paths, is essential for ensuring high availability and preventing single points of failure. Scalability is crucial for accommodating future growth and expansion of the sensor network.
Cybersecurity Challenges and Mitigation Strategies
The interconnected nature of smart sensors introduces significant cybersecurity risks. Unauthorized access, data breaches, and malicious attacks can have severe consequences, including operational disruptions, financial losses, and safety hazards. Robust security measures are therefore paramount.
Smart sensors are revolutionizing industrial automation, optimizing processes with unprecedented precision. This same sensor technology is rapidly transforming our homes, as seen in the exciting advancements detailed in this article on Exploring the Future of Smart Appliances in Modern Homes. Ultimately, the miniaturization and affordability of smart sensors are driving innovation across both industrial and domestic applications, promising a more connected and efficient future for all.
Strategies to mitigate these risks include implementing strong authentication mechanisms (like passwords and multi-factor authentication), using encryption to protect data in transit and at rest, employing firewalls to control network access, and regularly updating firmware and software to patch vulnerabilities. Regular security audits and penetration testing can help identify and address weaknesses before they are exploited. A well-defined security policy and employee training are also crucial components of a comprehensive cybersecurity strategy.
Benefits and Challenges of Implementing Smart Sensors
The integration of smart sensors into industrial processes is transforming operations, promising a future of heightened efficiency and reduced costs. However, this technological leap isn’t without its hurdles. Understanding both the advantages and drawbacks is crucial for businesses considering this significant investment.
Economic Benefits of Smart Sensors
Smart sensors offer substantial economic advantages by optimizing various aspects of industrial operations. Reduced downtime is a key benefit; predictive maintenance, enabled by real-time sensor data, allows for proactive repairs, preventing costly unplanned outages. Improved efficiency stems from the ability to monitor and control processes with greater precision, leading to less waste, optimized resource allocation, and higher output. Furthermore, enhanced product quality, resulting from consistent monitoring and control, translates to fewer defects and higher customer satisfaction. These factors collectively contribute to a significant boost in overall profitability.
Challenges of Implementing Smart Sensors
While the potential benefits are compelling, the implementation of smart sensors presents several challenges. High initial investment costs are a significant barrier to entry, particularly for smaller businesses. The complexity of integrating sensor data into existing systems can also be daunting, requiring specialized expertise and potentially significant IT infrastructure upgrades. Data security and privacy concerns are paramount, especially when handling sensitive operational data. Finally, the need for robust and reliable communication networks to support the large volume of data generated by smart sensors is another critical consideration. Addressing these challenges requires careful planning, strategic investment, and a phased implementation approach.
Return on Investment (ROI) of Smart Sensor Implementation Across Industries
The ROI of smart sensor implementation varies significantly across industries, depending on factors such as the specific application, the scale of deployment, and the existing infrastructure. While a precise ROI calculation requires detailed cost-benefit analysis tailored to each specific scenario, we can illustrate potential differences with a simplified comparison.
Industry | Typical ROI (Years) | Illustrative Example |
---|---|---|
Manufacturing | 2-3 | A manufacturing plant implementing smart sensors for predictive maintenance might reduce downtime by 15%, leading to significant cost savings within two years. |
Oil & Gas | 3-5 | In the oil and gas sector, smart sensors can optimize extraction processes, reducing waste and improving efficiency, potentially resulting in a positive ROI within three to five years. However, the higher initial investment costs for robust sensors designed to withstand harsh environments will increase this timeframe. |
Agriculture | 1-2 | Precision agriculture applications, using smart sensors to monitor soil conditions and optimize irrigation, can lead to significant yield improvements and reduced resource consumption, often resulting in a rapid ROI. |
Future Trends and Developments: The Growing Role Of Smart Sensors In Industrial Automation

Source: ultdb.net
The convergence of smart sensor technology with emerging digital ecosystems is poised to revolutionize industrial automation, pushing the boundaries of efficiency, productivity, and innovation. We’re moving beyond simple data collection towards a world where sensors are integral parts of intelligent, self-optimizing systems. This shift is driven by advancements in several key areas, leading to a future where industrial processes are more agile, responsive, and insightful than ever before.
The next generation of industrial automation will be profoundly shaped by the integration of the Internet of Things (IoT), Artificial Intelligence (AI), and cloud computing. IoT provides the connectivity backbone, enabling seamless data flow from a vast network of sensors. AI algorithms analyze this data to extract meaningful insights, driving real-time decision-making and predictive maintenance. Cloud computing provides the scalable infrastructure needed to store, process, and manage the massive datasets generated by these interconnected sensors. This synergistic relationship promises to unlock unprecedented levels of automation and optimization across various industries.
Smart Sensor Technological Advancements
Miniaturization, enhanced accuracy, and increased functionality are key drivers in the evolution of smart sensor technology. Smaller sensors enable deployment in previously inaccessible locations, expanding monitoring capabilities and providing more granular data. Improved accuracy leads to more precise process control and reduced waste. Increased functionality, incorporating features like self-calibration and built-in diagnostics, minimizes downtime and simplifies maintenance. For example, the development of MEMS (Microelectromechanical Systems) sensors has drastically reduced the size and cost of sensors while improving their performance and reliability. Similarly, advancements in material science are leading to the creation of sensors that can operate in extreme environments, previously considered unsuitable for sensor deployment. These technological leaps are crucial for pushing the boundaries of industrial automation.
Innovative Smart Sensor Applications
The potential applications of smart sensors are constantly expanding. Several innovative applications are currently under development or expected to emerge in the near future. These applications will redefine how we approach industrial processes, leading to significant improvements in efficiency, safety, and sustainability.
- Predictive Maintenance in Manufacturing: Smart sensors embedded in machinery monitor vibrations, temperature, and pressure in real-time. AI algorithms analyze this data to predict potential equipment failures, allowing for proactive maintenance and minimizing downtime. This approach is already being implemented in various industries, including aerospace and automotive manufacturing, significantly reducing maintenance costs and improving operational efficiency. For instance, a leading aircraft manufacturer is using smart sensors to predict engine failures with remarkable accuracy, enabling scheduled maintenance before potential breakdowns occur.
- Smart Agriculture: Sensors monitor soil conditions, weather patterns, and crop health, providing farmers with real-time data to optimize irrigation, fertilization, and pest control. This precision agriculture approach improves yields, reduces resource consumption, and enhances sustainability. An example of this is the use of soil moisture sensors to precisely control irrigation, minimizing water waste and optimizing crop growth.
- Autonomous Robotics and Industrial Control Systems: Smart sensors are crucial components in autonomous robots and advanced industrial control systems. They provide the sensory input necessary for robots to navigate complex environments, perform intricate tasks, and interact safely with human workers. Consider the use of 3D vision sensors in robotic assembly lines, enabling robots to precisely identify and manipulate objects with greater dexterity and speed.
- Enhanced Safety and Security in Industrial Environments: Smart sensors can monitor worker safety, detect hazardous conditions (such as gas leaks or fires), and enhance security by detecting unauthorized access. For instance, wearable sensors can monitor worker vital signs and alert emergency personnel in case of an accident. Similarly, smart sensors integrated into security systems can detect intrusions and alert authorities, preventing theft and sabotage.
Final Review
The integration of smart sensors marks a pivotal moment in industrial automation. While initial investments might seem daunting, the long-term benefits – increased efficiency, reduced downtime, and data-driven decision-making – are undeniable. As technology continues to advance, we can expect even more innovative applications and a further blurring of lines between the physical and digital worlds. The future of industry is smart, connected, and undeniably sensor-driven.