The Future of 3D Printing in the Aerospace Industry is taking flight. Forget clunky, outdated manufacturing—additive manufacturing is revolutionizing how we design, build, and even *think* about aircraft and spacecraft. From lightweight, high-strength components to entirely new design possibilities, 3D printing is no longer a futuristic fantasy; it’s reshaping the industry, one meticulously crafted part at a time. This isn’t just about faster production; it’s about unlocking innovation on a scale we’ve never seen before.
This journey into the heart of aerospace 3D printing will explore the current applications, the cutting-edge material science pushing boundaries, and the challenges of scaling up production to meet the demands of this rapidly evolving sector. We’ll delve into the impact on design, the rigorous quality control measures, and the broader economic and environmental implications. Buckle up, because this is one wild ride.
Current Applications of 3D Printing in Aerospace
3D printing, or additive manufacturing, is rapidly transforming the aerospace industry, moving beyond prototyping and into the realm of producing flight-ready components. This shift is driven by the technology’s unique ability to create complex geometries and lightweight, high-strength parts that are impossible or prohibitively expensive to manufacture using traditional methods. The benefits extend beyond just production; 3D printing also offers significant advantages in terms of design flexibility, reduced lead times, and on-demand manufacturing capabilities.
The aerospace industry currently utilizes 3D printing for a wide array of applications, focusing primarily on components where its advantages shine brightest. This includes the production of intricate internal structures, lightweight parts requiring complex geometries, and tooling for manufacturing processes. The ability to create these components directly from a digital design eliminates many of the limitations and complexities associated with subtractive manufacturing methods.
Examples of 3D-Printed Aerospace Components
3D printing is already producing a range of parts for aircraft and spacecraft. Examples include engine components like fuel nozzles and turbine blades, which benefit from the ability to create complex internal cooling channels for improved efficiency. Lightweight brackets, mounts, and other structural components are also being produced using additive manufacturing, resulting in significant weight savings and improved fuel economy. Furthermore, customized tools and fixtures used in aircraft assembly are increasingly being 3D printed, streamlining the manufacturing process and reducing costs. Specific examples include GE’s use of 3D-printed fuel nozzles in their LEAP engines and Airbus’s incorporation of 3D-printed parts in their aircraft interiors.
Comparison of Traditional and Additive Manufacturing in Aerospace
Traditional manufacturing methods, such as machining and casting, have been the mainstay of aerospace production for decades. These methods, however, often involve significant material waste, complex tooling, and lengthy lead times. In contrast, 3D printing offers several key advantages. It allows for the creation of complex geometries that would be impossible or extremely difficult to achieve using traditional techniques. This translates to lighter, stronger, and more efficient parts. Furthermore, 3D printing significantly reduces lead times and material waste, leading to cost savings and improved production efficiency. However, additive manufacturing is not without its limitations. The production rate for large components can be slower than traditional methods, and the quality and consistency of the finished product can be dependent on the printing parameters and material used. The cost of the 3D printing equipment itself can also be a significant barrier to entry for smaller companies.
Material Properties of Commonly 3D-Printed Aerospace Materials
The choice of material is crucial in aerospace applications, where performance and reliability are paramount. Several materials are commonly used in 3D printing for aerospace components, each with its own set of properties. The table below compares some of the most frequently used materials.
Material | Strength (Tensile Strength, MPa) | Weight (Density, g/cm³) | Cost (Relative) |
---|---|---|---|
Titanium Alloys (Ti6Al4V) | >900 | 4.5 | High |
Aluminum Alloys (AlSi10Mg) | >250 | 2.7 | Medium |
Polymers (e.g., ULTEM, PEEK) | Variable, typically lower than metals | 1.2 – 1.4 | Low |
Note: The values provided in the table are approximate and can vary depending on the specific alloy and printing process. Cost is a relative measure and depends on factors such as material price, printing time, and post-processing requirements.
Lightweight, customized parts? That’s the 3D printing aerospace revolution. But imagine the legal complexities of intellectual property rights for these designs – a whole new ballgame, especially when considering how secure and transparent transactions need to be, as highlighted in this article on How Blockchain is Transforming the Legal Industry. Blockchain could be the key to streamlining the legal side of this booming 3D printing sector, paving the way for faster innovation and safer skies.
Material Science Advancements for Aerospace 3D Printing
The aerospace industry’s relentless pursuit of lighter, stronger, and more efficient aircraft has fueled significant advancements in material science, particularly within the realm of 3D printing. This additive manufacturing technique offers unparalleled design freedom and the potential to create complex geometries impossible with traditional methods. However, realizing the full potential of 3D printing in aerospace requires the development of new materials specifically tailored for this process, capable of withstanding the extreme conditions encountered during flight.
The ongoing research and development focuses on overcoming the limitations of existing materials and exploring novel alloys, polymers, and composites. Challenges include achieving the necessary mechanical properties, ensuring consistent material quality across large builds, and addressing issues related to thermal stability and fatigue resistance. The opportunities, however, are immense, promising lighter and more fuel-efficient aircraft, improved safety features, and reduced manufacturing costs.
Key Properties of Aerospace 3D Printing Materials
Achieving optimal performance in aerospace applications demands materials with specific properties. High strength-to-weight ratio is paramount for minimizing fuel consumption and maximizing payload capacity. Furthermore, materials must exhibit exceptional fatigue resistance to withstand the repetitive stress cycles experienced during flight. Thermal stability is crucial for operation in high-temperature environments, while corrosion resistance protects against degradation in harsh atmospheric conditions. Finally, the materials need to be easily printable with consistent microstructure and properties throughout the 3D printed part. These properties are achieved through careful alloying, processing techniques, and post-processing treatments like heat treatments or surface coatings. For example, advanced aluminum alloys are being developed with enhanced strength and printability, while titanium alloys are refined to reduce porosity and improve fatigue life.
A Hypothetical Novel Aerospace Material: “Aerogel-Reinforced Carbon Nanotube Composite”
Imagine a new material, tentatively named “Aerogel-Reinforced Carbon Nanotube Composite” (ARCC). This hypothetical material combines the ultra-low density of aerogel with the exceptional strength and stiffness of carbon nanotubes. The aerogel matrix provides lightweight structural support, while the interwoven carbon nanotubes enhance the material’s tensile strength, compressive strength, and stiffness. The ARCC would be designed for 3D printing using a specialized binder system to ensure proper layer adhesion and structural integrity during the build process. This approach would enable the creation of complex, lightweight components for aircraft structures, potentially leading to significant weight reduction compared to existing materials like titanium or aluminum alloys. Potential applications include lightweight structural components for aircraft wings, fuselage sections, and engine parts. The high strength-to-weight ratio would translate to increased fuel efficiency, extended flight range, and improved payload capacity. Furthermore, the inherent properties of the aerogel and carbon nanotubes could contribute to excellent thermal insulation and vibration damping capabilities, enhancing both performance and passenger comfort. The ARCC material would be designed to undergo post-processing treatments such as high-temperature curing to optimize its mechanical properties and ensure long-term stability in aerospace environments. Its unique combination of properties would represent a significant advancement in aerospace material science, pushing the boundaries of what is currently possible with 3D printing.
Scaling Up 3D Printing for Aerospace Production: The Future Of 3D Printing In The Aerospace Industry
The aerospace industry, always pushing the boundaries of innovation, is increasingly looking to 3D printing, or additive manufacturing, to revolutionize its production processes. However, transitioning from prototyping and niche applications to large-scale manufacturing presents a unique set of challenges. Successfully scaling up 3D printing for aerospace demands addressing several key limitations across various aspects of the production pipeline.
Material Cost and Availability, The Future of 3D Printing in the Aerospace Industry
The high cost of specialized materials suitable for aerospace applications remains a significant hurdle. Many 3D printing processes require materials with exceptional strength, lightweight properties, and resistance to extreme temperatures and pressures – characteristics often found in high-performance alloys, composites, and polymers. These materials are inherently more expensive than those used in conventional manufacturing. Furthermore, the availability of these materials in forms suitable for additive manufacturing can be limited, impacting production scalability. For example, the development and production of titanium alloys specifically formulated for laser powder bed fusion (LPBF) processes requires significant investment and optimization. The scarcity of qualified suppliers further exacerbates this challenge.
Production Speed and Throughput
Current 3D printing technologies, while advancing rapidly, still struggle to match the speed and throughput of traditional subtractive manufacturing methods for large-scale production runs. The layer-by-layer nature of additive manufacturing inherently limits the speed at which components can be built. For instance, producing a large, complex aerospace part using selective laser melting (SLM) can take days or even weeks, significantly impacting overall production efficiency. This slow build rate directly translates into higher production costs and longer lead times. Addressing this challenge requires exploring and implementing faster printing techniques and optimizing the printing parameters to maximize build speeds without compromising part quality.
Quality Control and Inspection
Maintaining consistent quality across a large number of additively manufactured parts is crucial in the aerospace industry, where safety and reliability are paramount. The inherent complexity of 3D printing processes introduces potential variations in part geometry, material properties, and internal microstructure. Detecting and mitigating these variations requires robust quality control measures, including advanced inspection techniques like X-ray computed tomography (CT) scanning and non-destructive testing methods. The implementation of sophisticated automated inspection systems and the development of real-time process monitoring tools are essential to ensure high-quality production at scale. The costs associated with these quality control measures also need to be factored into the overall scalability assessment.
Strategies for Increasing Speed and Efficiency
Several strategies are being employed to increase the speed and efficiency of 3D printing for aerospace components. These include the development of faster printing technologies, such as multi-laser systems and binder jetting methods, which can significantly reduce build times. Optimization of printing parameters, such as laser power, scan speed, and layer thickness, can also improve throughput. Furthermore, the use of advanced software tools for process simulation and optimization can help minimize build times and material waste. Exploring alternative printing processes, such as large-scale vat polymerization and continuous fiber deposition, offers further potential for increased production rates.
Automation and Robotics in Aerospace 3D Printing
Automation and robotics play a critical role in improving the scalability and cost-effectiveness of 3D printing in the aerospace sector. Automated systems can handle tasks such as powder handling, part removal, and post-processing, reducing manual labor and improving consistency. Robotic arms can be used to perform complex operations like multi-part assembly and surface finishing, accelerating the overall production cycle. The integration of automated quality control systems further enhances efficiency and reduces human error. For example, robotic systems can be programmed to automatically inspect parts for defects using vision systems and other non-destructive testing methods. The adoption of these automated systems requires substantial upfront investment but ultimately leads to significant cost savings and improved productivity in the long run. Companies like Boeing and Airbus are already actively integrating robotic systems into their additive manufacturing workflows.
The Role of 3D Printing in Aerospace Design
3D printing, or additive manufacturing, is revolutionizing aerospace design, moving beyond simply producing parts to fundamentally altering the way engineers conceive and create aircraft and spacecraft components. It’s no longer about adapting designs to the limitations of traditional manufacturing; instead, designers are leveraging the unique capabilities of 3D printing to create entirely new possibilities. This shift allows for the development of lighter, stronger, and more efficient aerospace vehicles.
3D printing allows for the creation of complex geometries and internal structures that are impossible to manufacture using traditional subtractive methods like milling or casting. This opens up a world of design possibilities, leading to innovations that were previously confined to the realm of science fiction.
Design Freedom Enabled by Additive Manufacturing
The ability to create intricate lattice structures, internal channels for cooling or fuel lines, and complex shapes with internal features is a game-changer. Consider the design of a lightweight aircraft component. Traditional methods might result in a solid, heavy part. With 3D printing, designers can create a part with a lattice internal structure, achieving the same strength with significantly reduced weight. This translates to fuel efficiency gains and increased payload capacity. Another example is the creation of complex cooling channels within turbine blades. These channels can be precisely tailored to optimize cooling performance, leading to higher engine efficiency and longer lifespan. These designs are simply not feasible using traditional manufacturing techniques. The ability to create customized, patient-specific implants using 3D printing provides a parallel example. The same design flexibility allows aerospace engineers to optimize performance based on specific mission parameters or environmental conditions.
Topology Optimization in Aerospace Component Design
Topology optimization uses software algorithms to analyze stress and strain on a component under specific loads. The software then iteratively removes material from areas of low stress, leaving behind only the essential structural elements needed to withstand the load. The result is a component that is significantly lighter and stronger than a conventionally designed part, while maintaining its structural integrity. This process is particularly beneficial when combined with 3D printing, as it allows for the creation of complex, organic shapes that are impossible to manufacture using traditional methods. For example, topology optimization can be used to design lightweight brackets, internal support structures, or even entire airframes.
However, topology optimization isn’t without its challenges. The resulting designs can be very complex, making them difficult to manufacture using traditional methods. Moreover, the optimized designs may introduce manufacturing complexities or require specialized support structures during the 3D printing process, potentially increasing costs. Despite these limitations, the advantages of weight reduction and improved structural performance often outweigh the challenges. The aerospace industry is actively exploring and refining topology optimization techniques to further enhance their effectiveness and reduce associated challenges.
Advantages of 3D Printing in Aerospace Part Creation
The advantages of 3D printing in creating aerospace components are numerous and significant. The ability to create lightweight, strong, and complex parts leads to numerous improvements across the board.
- Reduced Weight: Lattice structures and topology optimization allow for the creation of parts that are significantly lighter than their traditionally manufactured counterparts, leading to improved fuel efficiency and increased payload capacity.
- Increased Strength: The ability to create complex internal structures and precisely control material deposition allows for the creation of parts with superior strength-to-weight ratios.
- Enhanced Complexity: 3D printing allows for the creation of parts with intricate geometries and internal features that are impossible to manufacture using traditional methods, leading to innovative designs and improved functionality.
- Reduced Lead Times: 3D printing can significantly reduce the time required to manufacture parts, accelerating the development and deployment of new aerospace vehicles and systems.
- Cost Savings: While the initial investment in 3D printing technology can be significant, the potential for reduced material waste, simplified tooling, and faster production can lead to substantial cost savings in the long run.
Quality Control and Certification of 3D-Printed Aerospace Parts
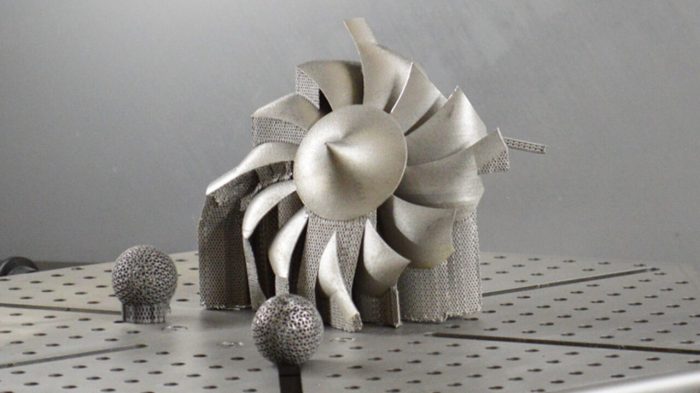
Source: 3dnatives.com
The aerospace industry demands unwavering reliability and safety. This necessitates rigorous quality control and certification processes for all components, especially those produced using additive manufacturing, or 3D printing. While 3D printing offers significant advantages, it also introduces unique challenges in ensuring consistent part quality and meeting the stringent requirements of aerospace applications. The certification process for 3D-printed parts differs significantly from traditional methods, requiring a more comprehensive approach to material characterization, process validation, and non-destructive testing.
The certification of 3D-printed aerospace parts is a multifaceted process aimed at guaranteeing the structural integrity and performance of the final product. This involves extensive testing and documentation to verify that the manufacturing process consistently produces parts that meet the required specifications. This contrasts sharply with traditional manufacturing, where established processes and extensive historical data often provide a stronger basis for initial certification. The novelty of 3D printing necessitates a more thorough and rigorous approach to ensure compliance with safety standards.
Specific Quality Control Measures for 3D-Printed Aerospace Components
Maintaining consistent quality in 3D-printed aerospace components requires a multi-layered approach encompassing the entire production lifecycle. This starts with rigorous material selection and qualification, ensuring that the chosen material meets all relevant aerospace standards for strength, fatigue resistance, and other critical properties. Precise control of the 3D printing process itself is crucial, including parameters such as laser power, scanning speed, and layer thickness. Real-time monitoring of these parameters, coupled with advanced process control software, helps to minimize variations and maintain consistency. Post-processing steps, such as heat treatment or surface finishing, are also carefully controlled and documented to further enhance part quality and performance. Finally, comprehensive inspection and testing procedures are essential to identify and rectify any defects before the parts are deemed suitable for use. For example, Airbus uses a combination of in-process monitoring and post-processing inspection techniques, including X-ray computed tomography (CT) scanning, to ensure the quality of their 3D-printed parts.
Comparison of Certification Processes for Traditionally Manufactured and 3D-Printed Aerospace Parts
Traditional manufacturing processes, like forging or casting, benefit from decades of established quality control procedures and extensive historical data. Certification often relies on demonstrating consistency based on this historical performance. In contrast, 3D printing is a relatively newer technology, demanding a more rigorous and data-driven approach. Certification for 3D-printed parts requires a detailed process qualification, demonstrating the repeatability and consistency of the manufacturing process under various conditions. This involves extensive testing to verify the mechanical properties, dimensional accuracy, and surface finish of the printed components. Furthermore, the traceability of materials and the entire production process is crucial for certification, necessitating meticulous record-keeping and data management. The regulatory requirements for 3D-printed parts are often more stringent, reflecting the need for increased assurance of their reliability and safety. For instance, the FAA and EASA have established specific guidelines for the certification of additively manufactured parts, requiring detailed documentation of the entire process and extensive testing to validate the performance of the components.
Non-Destructive Testing Methods for 3D-Printed Aerospace Components
Ensuring the integrity of 3D-printed aerospace components relies heavily on non-destructive testing (NDT) methods. These methods allow for the inspection of parts without causing damage, enabling the detection of internal flaws or inconsistencies. Commonly used NDT techniques include:
X-ray computed tomography (CT) scanning: This technique uses X-rays to create detailed 3D images of the internal structure of the part, allowing for the detection of internal voids, cracks, or other defects. It’s particularly useful for identifying porosity, a common concern in 3D-printed parts.
Ultrasonic testing: This method uses high-frequency sound waves to detect internal flaws. The reflection of the sound waves reveals the presence of discontinuities such as cracks or inclusions. It’s effective in detecting both surface and subsurface defects.
Dye penetrant inspection: This surface inspection method utilizes a dye that penetrates into surface-breaking cracks. A developer then draws the dye to the surface, making the cracks visible. It’s a relatively simple and cost-effective method for detecting surface cracks.
These NDT methods are crucial for ensuring that 3D-printed aerospace components meet the highest standards of quality and safety, providing confidence in their structural integrity and performance. The choice of specific NDT techniques depends on the part geometry, material properties, and the type of defects being sought. Often, a combination of techniques is employed to provide a comprehensive assessment of part integrity.
Economic and Environmental Impacts of 3D Printing in Aerospace
The adoption of 3D printing, or additive manufacturing, in the aerospace industry presents a complex interplay of economic advantages and challenges, alongside significant environmental implications. While offering the potential for substantial cost savings and reduced environmental impact, it also necessitates careful consideration of initial investment costs and the need for robust quality control measures. This section will delve into the economic benefits and drawbacks of this technology, as well as its environmental footprint compared to traditional methods.
Economic Benefits and Challenges of Aerospace 3D Printing
3D printing offers several compelling economic advantages for aerospace manufacturers. The ability to produce highly complex parts with intricate geometries, previously impossible or prohibitively expensive with traditional subtractive manufacturing, leads to significant cost reductions in tooling and production time. This is particularly beneficial for low-volume, high-value components, and customized parts. Reduced material waste, as discussed later, also contributes to cost savings. However, the high initial investment in 3D printing equipment, specialized materials, and skilled personnel presents a significant barrier to entry for smaller companies. Furthermore, the need for rigorous quality control and certification processes adds to the overall cost. Successfully navigating these challenges is crucial for realizing the full economic potential of 3D printing in the aerospace sector. A successful implementation requires careful planning, strategic investment, and a clear understanding of the technology’s limitations.
Environmental Impact of 3D Printing Compared to Traditional Manufacturing
The environmental impact of 3D printing in aerospace is a multifaceted issue, demanding a comparative analysis against traditional methods. While additive manufacturing offers potential advantages in reducing material waste and energy consumption, its overall environmental footprint depends heavily on the specific materials used and the energy source powering the 3D printers. The following table provides a general comparison, acknowledging that precise figures vary greatly depending on the specific application and technology:
Process | Material Waste | Energy Consumption | Carbon Footprint |
---|---|---|---|
Traditional Casting | High; significant material loss during machining and finishing | High; energy-intensive processes like melting and forging | High; significant greenhouse gas emissions from energy consumption and material production |
Traditional Machining (e.g., Milling) | High; large amounts of material removed as waste | Moderate to High; energy used for cutting and shaping | Moderate to High; emissions from energy use and material production |
3D Printing (Selective Laser Melting) | Low; only the necessary material is used | Moderate; energy for laser and machine operation | Moderate; lower emissions due to reduced material waste, but depends on material and energy source |
3D Printing (Fused Deposition Modeling) | Low to Moderate; some support material waste | Low; less energy intensive than laser-based methods | Low to Moderate; lower emissions than traditional methods, particularly if using recycled materials |
Weight Reduction and Fuel Efficiency Through 3D Printing
One of the most significant environmental benefits of 3D printing in aerospace is its contribution to weight reduction. The ability to create lightweight, high-strength parts with complex internal structures allows for optimized designs that minimize unnecessary material. This translates directly into improved fuel efficiency for aircraft, leading to lower fuel consumption and, consequently, reduced greenhouse gas emissions. For instance, the use of lattice structures created via 3D printing can significantly reduce the weight of aircraft components like engine brackets or interior panels, without compromising structural integrity. This translates to tangible reductions in fuel burn and a smaller carbon footprint for each flight. The resulting economic benefits from reduced fuel costs further incentivize the adoption of this technology.
Summary
The aerospace industry’s embrace of 3D printing isn’t just about incremental improvements; it’s a fundamental shift in how we approach design and manufacturing. From lighter, stronger aircraft to more efficient production processes and a reduced environmental footprint, the future of flight is being written in layers of meticulously printed material. The challenges are real, but the potential rewards – safer, more sustainable, and incredibly innovative aircraft – are simply too compelling to ignore. The sky’s the limit, and 3D printing is showing us how to reach for it.