How Robotics is Transforming the Future of Precision Agriculture? Forget dusty overalls and back-breaking labor; the future of farming is sleek, smart, and seriously automated. We’re talking robots – not the clunky kind from sci-fi flicks, but sophisticated machines using AI, computer vision, and more to revolutionize how we grow our food. From planting seeds with pinpoint accuracy to harvesting crops with gentle precision, robotics is poised to reshape agriculture as we know it, promising higher yields, lower costs, and a more sustainable future for our planet.
This isn’t just about fancy tech; it’s about addressing critical challenges facing modern agriculture. A shrinking workforce, rising food demands, and the urgent need for sustainable farming practices are driving the adoption of robotics. This deep dive explores the current state of robotic agriculture, its applications, the technological advancements fueling its growth, and the exciting possibilities – and challenges – that lie ahead. Get ready to witness the robotic revolution in farming.
Introduction
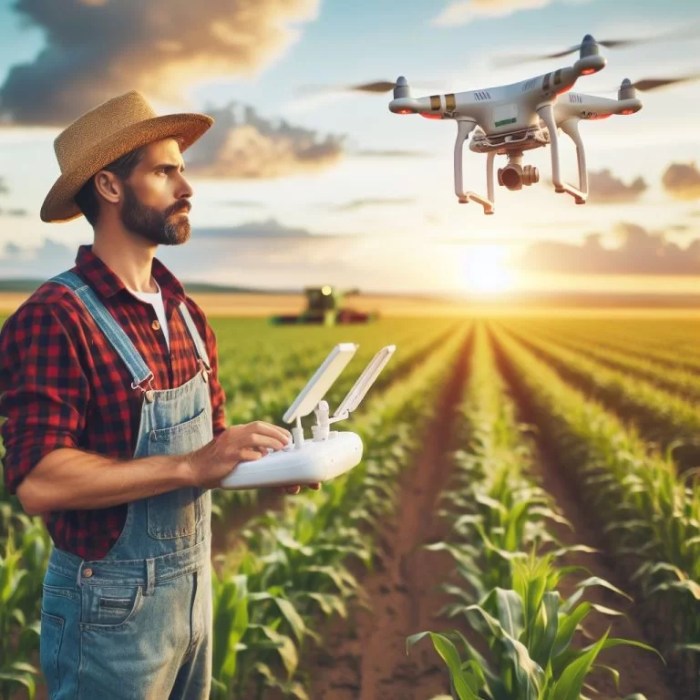
Source: thefarminginsider.com
Forget the image of a lone farmer toiling in the fields. The future of agriculture is being rewritten by robots, ushering in an era of precision farming that promises higher yields, reduced waste, and greater sustainability. While still in its relatively early stages of widespread adoption, the integration of robotics in agriculture is rapidly accelerating, driven by a confluence of technological advancements and pressing global challenges. This transformation is poised to redefine how we cultivate our food, making farming more efficient and environmentally responsible.
The increasing adoption of robotics in precision agriculture is fueled by several key factors. Firstly, the global population is growing, demanding a significant increase in food production to meet future needs. Simultaneously, arable land is becoming increasingly scarce and expensive, necessitating more efficient use of existing resources. Secondly, labor shortages in many agricultural regions are forcing farmers to seek automated solutions to manage their operations. Finally, the rising costs of fertilizers, pesticides, and water are pushing farmers to adopt precision techniques that minimize waste and maximize resource utilization. These factors are converging to create a compelling case for the widespread adoption of robotic technologies in agriculture.
Types of Robots Used in Precision Agriculture
Several types of robots are already making their mark on modern farms. These machines, ranging from autonomous tractors to small, specialized drones, are performing a variety of tasks with remarkable precision. For instance, autonomous tractors equipped with GPS and advanced sensors can navigate fields without human intervention, performing tasks like plowing, seeding, and spraying with exceptional accuracy. These robots can work around the clock, maximizing efficiency and reducing reliance on human labor. Another example is the use of drones equipped with multispectral cameras. These drones can fly over fields, capturing high-resolution images that are then analyzed to assess crop health, identify areas needing attention, and optimize irrigation and fertilization strategies. Furthermore, smaller, more specialized robots are being developed for tasks such as weeding, harvesting, and pruning, allowing for targeted interventions that minimize environmental impact and increase yield. These robots often use computer vision and AI to identify individual plants and perform precise actions. For example, a robotic weeder might identify and remove only weeds, leaving the crop plants unharmed.
Applications of Robotics in Precision Agriculture
Precision agriculture, the practice of farming with meticulous data-driven techniques, is undergoing a radical transformation thanks to robotics. Robots are no longer a futuristic fantasy; they’re actively enhancing efficiency, sustainability, and profitability across various farming operations. Their precision and tireless work ethic are revolutionizing traditional methods, offering a glimpse into the future of food production.
Robotic Planting
Robotic systems are proving invaluable in the planting process. Unlike traditional methods which rely on human labor or less precise machinery, robots can precisely plant seeds at optimal depths and spacing, minimizing seed wastage and maximizing germination rates. Equipped with GPS and sensors, they can navigate fields autonomously, adapting to varying terrain and soil conditions. This level of precision leads to more uniform crop growth and higher yields. Furthermore, robotic planters can integrate data from soil sensors to adjust planting depth and seed spacing according to specific soil conditions, optimizing plant establishment. This contrasts with traditional methods where planting is often uniform regardless of soil variability.
Robotic Harvesting
Harvesting is another area significantly impacted by robotics. Robots equipped with advanced vision systems and robotic arms can identify ripe fruits or vegetables, carefully pick them, and gently place them in containers, minimizing damage. This is particularly crucial for delicate produce like strawberries or tomatoes. Compared to manual harvesting, which is labor-intensive, prone to inconsistencies, and can lead to significant crop damage, robotic harvesting offers greater efficiency, consistency, and reduced post-harvest losses. For example, a robotic strawberry picker can work continuously without breaks, maintaining a consistent picking rate, unlike human harvesters who may tire or experience variations in speed and precision throughout the day.
Robotic Spraying
Robotic sprayers are revolutionizing pesticide and fertilizer application. These robots use GPS and sensors to precisely target the application, reducing chemical usage and minimizing environmental impact. Unlike traditional methods which often involve blanket spraying, leading to chemical runoff and potential harm to beneficial insects and the environment, robotic sprayers apply chemicals only where needed, optimizing efficacy and minimizing waste. This targeted approach reduces the overall cost of chemicals and contributes to more sustainable farming practices. Imagine a robotic sprayer that only targets weeds, leaving the crop unharmed, saving both money and the environment.
Economic Considerations of Robotic Systems in Agriculture
Implementing robotic systems presents both economic benefits and challenges. While the initial investment can be substantial, the long-term returns can be significant, particularly considering labor costs, reduced waste, and increased yields. However, factors such as maintenance, repair, and the need for specialized technical expertise must be considered.
Task | Robotic System Cost (per hectare) | Traditional Method Cost (per hectare) | Cost Effectiveness |
---|---|---|---|
Planting | $500 – $1000 | $300 – $500 | Higher initial cost, but potential for long-term savings due to increased yields and reduced labor. |
Harvesting | $800 – $1500 | $600 – $1000 | Higher initial cost, but potential for significant savings on labor costs, especially for high-value crops. |
Spraying | $400 – $800 | $200 – $400 | Higher initial cost, but significant savings on chemical usage and reduced environmental impact. |
*Note: These cost estimates are approximate and can vary depending on factors such as farm size, crop type, and specific robotic system used. The actual cost-effectiveness will depend on individual circumstances.*
Technological Advancements Driving Robotic Adoption
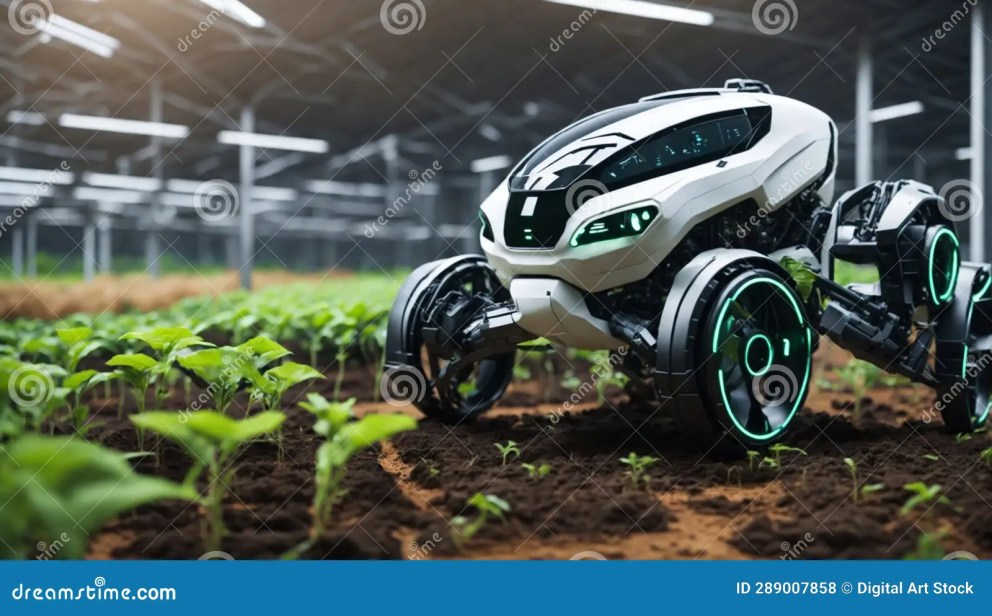
Source: dreamstime.com
The rapid advancement of several key technologies is fueling the burgeoning adoption of robotics in precision agriculture. These advancements are not only improving the capabilities of existing robotic systems but also enabling the development of entirely new and more sophisticated solutions to address the challenges faced by modern farming. This synergy between robotics and cutting-edge technologies is transforming how crops are cultivated, monitored, and harvested, ultimately boosting efficiency and sustainability.
The integration of artificial intelligence (AI), computer vision, and machine learning (ML) is revolutionizing the intelligence and adaptability of agricultural robots. These technologies allow robots to perceive their environment, make decisions, and learn from experience, leading to greater autonomy and precision in their operations. This is moving beyond pre-programmed routines to a future where robots can dynamically adjust their actions based on real-time data analysis.
The Role of AI, Computer Vision, and Machine Learning
AI, computer vision, and ML are the brains behind the increasing sophistication of agricultural robots. AI provides the overarching intelligence, enabling robots to perform complex tasks and make informed decisions. Computer vision acts as the “eyes,” allowing robots to see and interpret their surroundings through cameras and sensors. This visual information is then processed using ML algorithms, allowing the robot to learn from past experiences and improve its performance over time. For example, a robotic sprayer using computer vision can identify weeds and precisely apply herbicide only to the targeted plants, minimizing chemical usage and environmental impact. ML algorithms, trained on vast datasets of images, can identify subtle variations in plant health, enabling early detection of diseases or nutrient deficiencies.
Key Sensor Technologies in Agricultural Robots
A wide array of sensor technologies is critical to the operation of agricultural robots. These sensors provide the robots with the information they need to navigate, monitor crops, and perform tasks.
- GPS and GNSS: These systems provide precise location data, allowing robots to navigate fields autonomously and follow pre-programmed paths. High-precision GPS, such as RTK-GPS, is often used to ensure centimeter-level accuracy.
- LiDAR: Light Detection and Ranging (LiDAR) sensors create 3D maps of the environment, enabling robots to perceive obstacles and navigate uneven terrain. This is crucial for robots operating in fields with varying topography.
- Cameras: Multispectral and hyperspectral cameras capture images across a wider range of wavelengths than the human eye can see. This allows robots to detect subtle variations in plant health, stress levels, and even the presence of pests or diseases that might be invisible to the naked eye. RGB cameras provide standard visual information for navigation and object recognition.
- Infrared Sensors: These sensors detect heat signatures, which can be used to identify areas of stress in plants, monitor soil moisture, and even detect the presence of animals.
- Soil Sensors: These sensors measure various soil properties, including moisture content, nutrient levels, and temperature. This information is crucial for optimizing irrigation and fertilization practices.
Innovative Robotic Designs for Agricultural Challenges
The design of agricultural robots is constantly evolving to meet the specific challenges of different farming environments and crop types.
- Robots for uneven terrain: Robots designed for vineyards or orchards often incorporate specialized suspension systems and articulated chassis to navigate uneven terrain. Some robots use multiple smaller wheels or tracks to improve stability and traction on slopes and uneven surfaces. For instance, some robotic harvesters are equipped with adaptable arms and grippers that can handle the varied shapes and sizes of fruits on uneven branches.
- Robots for different crop types: Robotic designs are tailored to specific crops. For example, robots for harvesting delicate fruits like strawberries use soft grippers to avoid damaging the fruit, while robots for harvesting grains might utilize cutting blades or vacuum systems. Row crop robots often have different designs compared to those for orchards or vineyards, reflecting the different spatial arrangements of the crops.
- Autonomous weeding robots: These robots utilize computer vision and precision mechanics to identify and remove weeds without harming the desired crops. Some employ targeted herbicide application, while others utilize mechanical methods such as cutting or hoeing. The design includes careful consideration of crop spacing and weed morphology for effective and precise weeding.
Impact on Crop Yields and Efficiency
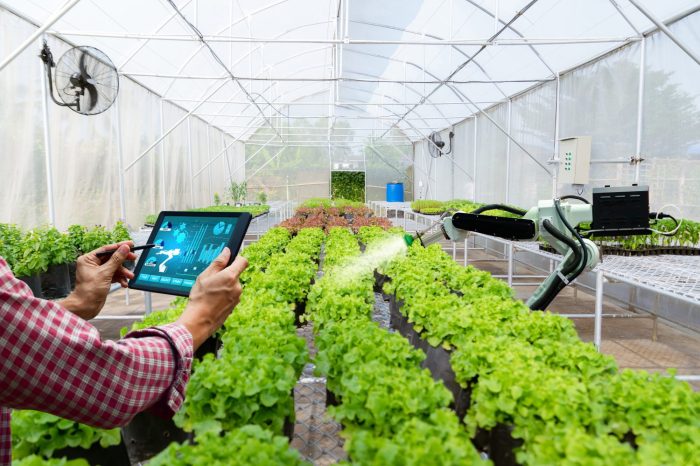
Source: ukri.org
Robotics is revolutionizing precision agriculture, optimizing yields and resource use. This smart tech approach mirrors the advancements in urban mobility, like those explored in The Future of Autonomous Vehicles in Reducing Urban Congestion , where autonomous systems streamline complex processes. Ultimately, both sectors showcase how intelligent automation promises a more efficient and sustainable future, driving innovation across various fields.
The integration of robotics into agriculture isn’t just about futuristic farming; it’s about tangible improvements in crop yields and overall farm efficiency. By automating tasks and providing precise data-driven insights, robotic systems are revolutionizing how we cultivate our food, leading to significant gains in productivity and resource management. This translates directly to higher profits for farmers and a more sustainable approach to food production.
Robotic systems dramatically improve crop yields through the precise application of inputs. Unlike traditional methods which often lead to over-application or uneven distribution, robots can target specific areas needing attention. This precision reduces waste, optimizes resource use, and allows for targeted interventions that maximize plant health and productivity. For instance, a robotic sprayer can identify individual weeds and apply herbicide only to those plants, minimizing the impact on beneficial crops and reducing herbicide use. Similarly, robotic harvesters can selectively pick only ripe fruits or vegetables, ensuring optimal quality and reducing post-harvest losses.
Precise Input Application and Resource Optimization
The ability of robots to precisely apply inputs like water, fertilizers, and pesticides leads to significant resource optimization. Imagine a robotic system equipped with sensors that can monitor soil moisture levels in real-time. This allows for targeted irrigation, delivering water only where and when it’s needed, conserving water resources and preventing water stress on crops. Similarly, robots can analyze soil nutrient levels and apply fertilizer only to areas with deficiencies, reducing fertilizer runoff and improving nutrient use efficiency. This precision application minimizes environmental impact while maximizing crop yield. Studies have shown that precision application techniques, facilitated by robotics, can reduce fertilizer use by up to 30% without compromising yield. For example, a study conducted by the University of California, Davis, demonstrated that using robotic systems for fertilizer application resulted in a 25% reduction in fertilizer use and a 10% increase in yield compared to traditional broadcasting methods.
Impact on Labor Costs and Farm Efficiency
The increasing labor costs and the shortage of skilled farm labor are major challenges facing the agricultural industry. Robotic systems offer a solution by automating labor-intensive tasks, reducing reliance on manual labor, and improving overall farm efficiency.
- Reduced Labor Costs: Robots can perform tasks like planting, weeding, spraying, and harvesting, reducing the need for manual labor and associated costs. This is especially beneficial in regions with high labor costs or labor shortages.
- Increased Efficiency: Robotic systems can work continuously, 24/7, without breaks, increasing the speed and efficiency of farming operations. This allows for faster turnaround times and increased output.
- Improved Crop Quality: Precise robotic handling reduces crop damage during harvesting and transportation, leading to improved crop quality and reduced post-harvest losses.
- Enhanced Data Collection: Robots equipped with sensors collect vast amounts of data on crop health, soil conditions, and other factors, providing valuable insights for optimizing farm management.
- Better Resource Allocation: Data collected by robotic systems helps farmers make informed decisions about resource allocation, optimizing the use of water, fertilizers, and pesticides.
For example, a large-scale farming operation in Iowa reported a 20% reduction in labor costs and a 15% increase in yield after implementing a robotic harvesting system. This demonstrates the significant economic benefits of integrating robotics into precision agriculture. The initial investment in robotic systems may be substantial, but the long-term return on investment can be significant, especially considering the increasing costs of labor and the potential for increased yields and efficiency.
Environmental Considerations and Sustainability: How Robotics Is Transforming The Future Of Precision Agriculture
The integration of robotics into precision agriculture presents a complex interplay of environmental benefits and potential drawbacks. While offering significant opportunities for sustainable farming practices, careful consideration and proactive mitigation strategies are crucial to ensure responsible adoption. The long-term goal is to harness the technological advancements while minimizing any negative impacts on the environment.
Robotic systems in agriculture offer several pathways towards environmental sustainability. By optimizing resource use and minimizing environmental pollution, they contribute to a more eco-friendly approach to food production.
Reduced Pesticide and Fertilizer Use
Precision application technologies, a key feature of many agricultural robots, allow for targeted delivery of pesticides and fertilizers. This reduces the overall quantity needed compared to traditional broadcast methods, minimizing environmental contamination of soil and water resources. For example, robotic sprayers equipped with sensors can identify individual weeds or diseased plants, applying treatment only where necessary. This targeted approach drastically reduces the amount of herbicide or pesticide needed compared to blanket spraying across an entire field, thus decreasing runoff and minimizing harm to beneficial insects and wildlife. Similarly, robotic systems can monitor nutrient levels in the soil and apply fertilizer only where and when needed, optimizing nutrient uptake by plants and reducing nutrient runoff into waterways.
Decreased Soil Compaction
Heavy machinery, a staple of traditional farming, contributes significantly to soil compaction. This compaction reduces soil aeration, water infiltration, and root growth, ultimately impacting crop yields and soil health. The use of lighter robots, often designed for autonomous operation, significantly reduces soil compaction compared to traditional tractors and harvesters. Smaller robots can navigate fields with less pressure on the soil, preserving soil structure and improving water management. This leads to healthier soils, better water retention, and increased resilience to erosion. Studies have shown that the reduction in soil compaction translates directly into improved yields and reduced need for irrigation.
Potential Environmental Drawbacks and Mitigation Strategies
While the benefits are substantial, the widespread adoption of agricultural robots presents potential environmental challenges. One concern is the energy consumption associated with manufacturing, operation, and disposal of these robots. Many robots rely on batteries, which require energy-intensive manufacturing and disposal processes. Mitigation strategies include focusing on energy-efficient designs, utilizing renewable energy sources for charging, and implementing robust recycling programs for robot components.
Another potential concern is the increased reliance on rare earth minerals in the construction of robotic components. The extraction and processing of these minerals can have significant environmental consequences. Developing robots using more sustainable materials, exploring alternative components, and promoting responsible sourcing practices are essential for mitigating this risk. Finally, the potential for increased plastic waste from robot components requires careful planning for end-of-life management and recycling.
Sustainable Integration Plan
A sustainable integration of robotics into agricultural practices necessitates a holistic approach. This includes:
- Life Cycle Assessment (LCA): Conducting comprehensive LCAs of robotic systems to identify environmental hotspots throughout their life cycle, from manufacturing to disposal. This allows for targeted improvements and informed decision-making.
- Sustainable Material Selection: Prioritizing the use of recycled and recyclable materials in robot construction, minimizing reliance on rare earth minerals and reducing plastic waste.
- Energy Efficiency Optimization: Designing robots with enhanced energy efficiency and utilizing renewable energy sources for charging and operation.
- Responsible Disposal and Recycling Programs: Implementing robust programs for the responsible disposal and recycling of robot components at the end of their lifespan.
- Farmer Training and Education: Providing farmers with comprehensive training on the proper use and maintenance of robotic systems to maximize their environmental benefits and minimize potential risks.
- Policy and Regulation: Developing supportive policies and regulations that incentivize the adoption of environmentally friendly robotic systems and discourage practices that could lead to environmental degradation.
By addressing these considerations proactively, we can ensure that the transformative potential of robotics in agriculture is realized while safeguarding environmental sustainability for future generations.
Challenges and Future Trends
The rapid advancement of agricultural robotics presents a compelling vision for the future of farming, but several hurdles must be overcome before widespread adoption becomes a reality. The path to a fully automated, robotically-driven agricultural landscape is paved with both technological and economic challenges, requiring innovative solutions and strategic investments.
High initial investment costs and a lack of readily available skilled labor represent significant barriers to entry for many farmers, particularly smaller operations. Furthermore, the complex and often unpredictable nature of agricultural environments necessitates robust and adaptable robotic systems capable of handling diverse terrains, weather conditions, and crop types. Addressing these challenges will require a multifaceted approach involving technological innovation, economic incentives, and educational initiatives.
High Initial Investment Costs and Return on Investment
The high cost of purchasing and maintaining advanced agricultural robots is a major deterrent for many farmers. The price tag for a single robotic system can range from tens of thousands to hundreds of thousands of dollars, representing a significant upfront investment that may not be immediately recoupable. This is particularly true for smaller farms with limited capital. However, the potential long-term return on investment (ROI) through increased efficiency, reduced labor costs, and improved yields needs to be carefully evaluated. Successful implementation relies on thorough cost-benefit analyses and potentially innovative financing models to make the technology more accessible. For example, leasing programs or government subsidies could alleviate the financial burden and encourage wider adoption.
Lack of Skilled Labor and Training Programs
Operating and maintaining sophisticated agricultural robots requires specialized skills and knowledge. A shortage of skilled labor capable of programming, troubleshooting, and repairing these systems poses a significant challenge. Addressing this requires investment in education and training programs to equip farmers and technicians with the necessary expertise. Curriculum development focusing on robotics, automation, and data analysis in agricultural contexts is crucial. Furthermore, industry-academia collaborations can foster the development of skilled professionals and promote knowledge transfer between researchers and practitioners. Successful examples include apprenticeship programs offered by robotics companies in collaboration with agricultural colleges.
Technological Advancements and Predictions
Future developments in agricultural robotics will likely focus on enhancing autonomy, improving sensor technology, and increasing the adaptability of robotic systems. We can expect to see more sophisticated AI-powered systems capable of making real-time decisions based on environmental conditions and crop needs. Advances in computer vision and machine learning will enable robots to better identify weeds, pests, and diseases, leading to more precise and targeted interventions. The development of more robust and versatile robotic platforms capable of operating in various terrains and weather conditions will also be crucial. For instance, we can anticipate advancements in robotic locomotion systems that allow robots to navigate uneven fields and overcome obstacles more efficiently.
Increased Automation and Collaborative Robots (Cobots), How Robotics is Transforming the Future of Precision Agriculture
The future of farming will likely involve a significant increase in automation, with robots taking on a wider range of tasks. Collaborative robots, or cobots, are expected to play an increasingly important role, working alongside human farmers to enhance efficiency and productivity. Cobots can handle repetitive or physically demanding tasks, freeing up human workers to focus on more complex and strategic aspects of farm management. This collaborative approach combines the strengths of human intelligence and judgment with the precision and efficiency of robotic systems. Examples include cobots assisting with harvesting delicate fruits or vegetables, or performing tasks requiring fine motor skills that are difficult for fully autonomous robots to replicate.
The long-term vision for robotics in precision agriculture is a future where intelligent robotic systems seamlessly integrate into farming operations, optimizing resource utilization, minimizing environmental impact, and ensuring food security for a growing global population. This will involve a shift towards more sustainable and resilient agricultural practices, powered by advanced technologies and human expertise working in harmony.
Case Studies
Successful implementation of robotic systems in agriculture isn’t just a theoretical concept; it’s a reality shaping farms worldwide. Several compelling case studies highlight the tangible benefits of this technological shift, demonstrating increased efficiency, improved yields, and reduced environmental impact. These examples showcase the versatility of robotics across diverse agricultural settings.
Naïo Technologies’ Oz Robot in Grape Vineyards
Naïo Technologies’ Oz robot is a prime example of robotic success in precision viticulture. This autonomous robot, designed for use in vineyards, performs tasks such as weeding and spraying. Equipped with GPS and various sensors, Oz navigates rows of grapevines precisely, applying herbicides or pesticides only where needed. This targeted approach significantly reduces chemical usage compared to traditional methods, minimizing environmental impact and lowering operational costs. Furthermore, Oz’s consistent operation ensures uniform weed control, leading to healthier vines and improved grape yield. In trials, Oz has demonstrated a significant reduction in herbicide use (up to 90% in some cases) while maintaining or even improving weed control compared to manual methods. The consistent and precise application of treatments also resulted in a noticeable improvement in grape quality.
Harvest Automation’s HV-100 Robot in Berry Picking
Harvest Automation’s HV-100 robot tackles the labor-intensive task of harvesting berries. This robot, designed for use in greenhouses and fields, uses a combination of computer vision and robotic arms to identify and gently pick ripe berries. The HV-100 addresses the significant labor shortages often experienced in berry farming, providing a reliable and consistent harvesting solution. While the technology is still under development and refinement, early results show promise in improving picking efficiency and reducing labor costs. The robot’s careful handling minimizes damage to the berries, ensuring higher-quality produce and reducing waste. Furthermore, the consistent picking process allows for better yield estimations and optimized harvesting schedules.
Bosch’s Automated Tractor System in Large-Scale Farming
Bosch’s automated tractor system represents a different approach to robotic agriculture, focusing on large-scale operations. This system utilizes advanced sensors, GPS, and AI to enable autonomous tractor operation across vast fields. Tasks include planting, spraying, and harvesting, all performed with precision and efficiency. The system’s ability to operate continuously, even at night, dramatically increases productivity. Data collected by the system provides valuable insights into soil conditions and crop health, enabling farmers to make informed decisions regarding irrigation, fertilization, and pest control. In real-world deployments, Bosch’s system has demonstrated significant increases in efficiency, reducing labor costs and fuel consumption while improving crop yields. The ability to work continuously and collect real-time data provides farmers with a competitive edge.
Summary of Case Studies
Case Study | Robot Type | Tasks Performed | Outcomes |
---|---|---|---|
Naïo Technologies’ Oz | Autonomous vineyard robot | Weeding, spraying | Reduced herbicide use (up to 90%), improved weed control, higher grape yield |
Harvest Automation’s HV-100 | Autonomous berry-picking robot | Berry harvesting | Reduced labor costs, improved picking efficiency, minimized berry damage |
Bosch’s Automated Tractor System | Autonomous tractor system | Planting, spraying, harvesting | Increased productivity, reduced labor and fuel costs, improved crop yields, enhanced data collection |
Conclusive Thoughts
The integration of robotics into precision agriculture isn’t just a trend; it’s a necessity. The benefits – increased efficiency, reduced waste, enhanced sustainability, and improved crop yields – are too compelling to ignore. While challenges like high initial investment costs and the need for skilled labor remain, the ongoing advancements in AI, sensor technology, and robotic design are paving the way for a future where farming is smarter, more efficient, and environmentally responsible. The robotic revolution in agriculture is here, and it’s changing the game, one perfectly planted seed at a time.