How Robotics is Transforming the Future of Logistics and Supply Chains? It’s not just sci-fi anymore. From automated warehouses humming with robotic arms to self-driving delivery trucks navigating city streets, the logistics industry is undergoing a radical transformation. This revolution isn’t just about efficiency; it’s about reshaping how goods move, impacting everything from global trade to your daily online shopping experience. We’ll explore how robotics is optimizing every stage of the supply chain, from the warehouse to your doorstep, and what that means for the future of work.
This deep dive will cover the impact of automated guided vehicles (AGVs) and autonomous mobile robots (AMRs) in warehouses, the rise of drone and autonomous delivery, and how robotic process automation (RPA) streamlines supply chain management. We’ll also address the crucial questions around job displacement, the need for workforce reskilling, and the safety considerations of integrating robots into our logistics systems. Get ready to explore the exciting, and sometimes unsettling, future of logistics.
Automation in Warehousing and Distribution Centers
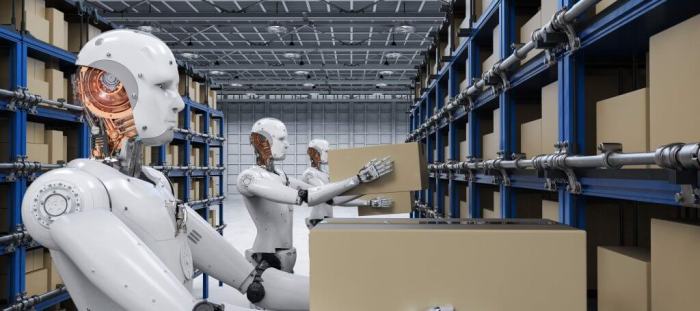
Source: mohebilogistics.com
The modern warehouse is undergoing a radical transformation, driven by the relentless pursuit of efficiency and speed. Automation is no longer a futuristic concept; it’s the backbone of many successful logistics operations, enabling companies to meet the ever-increasing demands of e-commerce and global supply chains. This shift towards automation involves a complex interplay of robotic systems, sophisticated software, and optimized workflows, all working in concert to streamline processes and minimize costs.
Automated Guided Vehicles (AGVs) and Autonomous Mobile Robots (AMRs)
AGVs and AMRs are revolutionizing material handling within warehouses. AGVs follow pre-programmed paths, often using magnetic tape or wires embedded in the floor, making them ideal for repetitive tasks like transporting pallets between storage areas and loading docks. AMRs, however, possess advanced navigation capabilities, using sensors and artificial intelligence to dynamically adjust their routes based on real-time conditions. This adaptability allows AMRs to navigate more complex warehouse layouts and react to obstacles or changes in workflow more efficiently than their AGV counterparts. The result is a significant increase in throughput and a reduction in labor costs associated with manual material handling. For example, a large online retailer might deploy a fleet of AMRs to transport goods from receiving docks to picking stations, optimizing the flow of inventory and ensuring timely order fulfillment.
Robotic Arms and Automated Picking Systems
The repetitive and often physically demanding tasks of picking and packing orders are now being increasingly automated. Robotic arms, equipped with advanced vision systems and grippers, can accurately pick items from shelves or conveyors at a much faster rate than human workers. These robotic arms are integrated into automated picking systems that can handle a wide variety of items, from small packages to bulky goods. Automated picking systems often utilize sophisticated algorithms to optimize picking routes, minimizing travel time and maximizing efficiency. Companies like Amazon have extensively deployed robotic arms in their fulfillment centers, significantly improving order fulfillment speed and accuracy, leading to faster delivery times and increased customer satisfaction.
Warehouse Management Systems (WMS) Integration
The seamless integration of robotic systems with Warehouse Management Systems (WMS) is crucial for maximizing efficiency. WMS software acts as the central nervous system of the warehouse, providing real-time visibility into inventory levels, order status, and the location of robotic systems. This integration allows for dynamic task assignment, optimized routing, and real-time monitoring of performance metrics. The WMS can direct robotic systems to prioritize urgent orders, optimize picking routes based on real-time inventory location, and track the progress of each order throughout the fulfillment process. This integrated approach ensures that robotic systems are working in harmony with other warehouse operations, maximizing efficiency and minimizing errors.
Cost-Benefit Analysis of Robotic Solutions in Warehousing
Robotic Solution | Initial Investment | Ongoing Maintenance | Benefits |
---|---|---|---|
AGVs | High | Moderate | Increased throughput, reduced labor costs, improved safety |
AMRs | Higher | Higher | Greater flexibility, adaptable to changing workflows, improved efficiency |
Robotic Arms | High | Moderate | Increased picking speed and accuracy, reduced labor costs, improved order fulfillment |
Automated Picking Systems | Very High | High | Significant increase in throughput, reduced errors, improved scalability |
Last-Mile Delivery and Transportation
The final leg of the delivery journey, the last mile, is often the most expensive and complex part of the logistics chain. Traditional methods are struggling to keep up with the demands of e-commerce and the expectation of fast, convenient delivery. Enter robotics: drones, autonomous vehicles, and robotic sorting systems are poised to revolutionize last-mile delivery, offering solutions to rising costs and improving delivery speed and efficiency.
The integration of robotics into last-mile delivery promises significant improvements in speed, cost-effectiveness, and overall customer satisfaction. By automating tasks previously reliant on human drivers and couriers, businesses can streamline their operations, reduce labor costs, and enhance the precision and predictability of their delivery networks. This shift towards automation is not merely a technological advancement; it’s a necessary evolution to meet the ever-growing demands of modern consumers.
The Role of Drones and Autonomous Delivery Vehicles
Drones and autonomous delivery vehicles represent a significant shift in last-mile logistics. Drones, capable of navigating complex urban environments and delivering smaller packages directly to customers’ doorsteps, offer a faster and more efficient alternative to traditional delivery methods, especially in areas with challenging terrain or dense populations. Autonomous vehicles, meanwhile, are capable of handling larger and heavier packages, potentially reducing the reliance on human drivers and lowering delivery costs. These technologies are not mutually exclusive; a combined approach, using drones for smaller packages and autonomous vehicles for larger ones, could optimize the entire last-mile delivery process. For example, a drone could deliver a small package from a central distribution hub to a designated drop-off point, where an autonomous vehicle could then take over for the final delivery to the customer.
Challenges and Opportunities in Implementing Autonomous Delivery Systems
Implementing autonomous delivery systems presents several challenges. Regulatory hurdles, including airspace regulations for drones and road safety regulations for autonomous vehicles, need to be addressed. Technological limitations, such as ensuring reliable navigation in all weather conditions and dealing with unexpected obstacles, also need to be overcome. Furthermore, public acceptance and trust in autonomous systems are crucial for widespread adoption. However, the opportunities are equally significant. Reduced delivery times, lower operational costs, and increased delivery efficiency can lead to significant improvements in customer satisfaction and profitability for businesses. The potential for 24/7 delivery, regardless of weather or traffic conditions, opens up new possibilities for businesses and consumers alike.
Examples of Successful Robotics in Last-Mile Delivery
Several companies are already making strides in the field of robotic last-mile delivery. Amazon, for instance, has been testing drone deliveries for several years, aiming to provide faster and more efficient delivery options to customers in select areas. Nuro, a robotics company, is developing autonomous delivery vehicles designed specifically for last-mile deliveries, partnering with various retailers to provide automated delivery services. These examples showcase the growing potential of robotics in transforming the last-mile delivery landscape.
Robotic Last-Mile Delivery Process Flowchart, How Robotics is Transforming the Future of Logistics and Supply Chains
The following flowchart illustrates a simplified version of a robotic last-mile delivery process:
[Imagine a flowchart here. The flowchart would begin with an order being placed online. This would lead to a box being prepared and labeled in a warehouse. Next, the box would be loaded onto an autonomous vehicle or drone. The vehicle/drone would then navigate to the delivery location using GPS and other navigation technologies. Upon arrival, the vehicle/drone would either deliver the package directly to the customer’s doorstep or to a designated drop-off point. Finally, the delivery would be confirmed, and the system would update the order status.]
Supply Chain Optimization and Visibility: How Robotics Is Transforming The Future Of Logistics And Supply Chains
Robotics is revolutionizing supply chain management, offering unprecedented levels of efficiency and transparency. By automating tasks and providing real-time data, robots are transforming how businesses track goods, predict demand, and optimize their operations, ultimately leading to significant cost savings and improved customer satisfaction. This section delves into the specific ways robotics enhances supply chain visibility and streamlines operations.
The integration of robotics dramatically improves supply chain visibility and traceability. Imagine a scenario where every package, pallet, and even individual item is equipped with a unique RFID tag, constantly tracked by robotic systems throughout the entire journey. This real-time data flow eliminates the guesswork associated with traditional methods, providing complete transparency into the location and status of goods at every stage. For instance, a retailer can instantly see where a specific shipment is located, identify potential delays, and proactively address any issues before they impact customers. This level of precision allows for better inventory management, reduced stockouts, and improved order fulfillment accuracy.
Robotic Process Automation in Supply Chain Administration
Robotic Process Automation (RPA) significantly streamlines administrative tasks within supply chain management. RPA bots can handle repetitive, rule-based processes such as invoice processing, order entry, data entry, and reconciliation. This frees up human employees to focus on more strategic and complex tasks, increasing overall efficiency and reducing the risk of human error. For example, an RPA bot can automatically process thousands of invoices each day, extracting key information and updating accounting systems without human intervention. This leads to faster payment cycles, improved cash flow, and a reduction in administrative costs.
Key Performance Indicators for Robotic Supply Chain Solutions
Measuring the effectiveness of robotic solutions requires a focus on specific Key Performance Indicators (KPIs). These metrics provide quantifiable data to assess the return on investment (ROI) and overall impact of robotic implementation. Crucial KPIs include order fulfillment rate, inventory accuracy, lead times, warehouse throughput, and overall operational costs. By tracking these metrics, businesses can identify areas for improvement and optimize their robotic systems for maximum efficiency. For example, a significant increase in warehouse throughput, coupled with a decrease in operational costs, demonstrates the positive impact of robotic automation.
Robotics Across Different Supply Chain Sectors
The application of robotics varies across different sectors of the supply chain. In manufacturing, robots are extensively used in automated assembly lines, performing tasks such as welding, painting, and packaging. In transportation, autonomous vehicles and drones are transforming last-mile delivery and optimizing logistics networks. In retail, robots are employed in warehousing and distribution centers to automate picking, packing, and sorting processes. While the specific applications differ, the overarching goal remains the same: to improve efficiency, reduce costs, and enhance overall supply chain performance. For instance, Amazon’s extensive use of robotics in its fulfillment centers exemplifies the transformative potential of automation in the retail sector, allowing them to handle massive order volumes with remarkable speed and accuracy.
Impact on Employment and the Workforce
The rise of robotics in logistics is undeniably reshaping the employment landscape. While fears of widespread job displacement are valid, the reality is more nuanced. Automation will undoubtedly alter the types of jobs available, demanding a shift in skills and potentially leading to job losses in certain sectors. However, it will also create new opportunities and necessitate a proactive approach to workforce adaptation.
The integration of robots and automated systems in warehouses and transportation networks will inevitably lead to a reduction in demand for certain manual labor roles. For instance, jobs involving repetitive tasks like picking, packing, and sorting are particularly vulnerable to automation. This transition, while potentially disruptive, is not unprecedented; technological advancements have always shifted the nature of work, albeit at varying paces. The key lies in anticipating these changes and preparing the workforce for the jobs of the future.
Job Displacement and New Roles
Automation in logistics will undoubtedly displace some workers, primarily those performing repetitive, physically demanding tasks. However, the impact isn’t solely negative. The shift towards automation will create a demand for new roles requiring specialized skills in areas like robotics maintenance, software programming, data analysis, and logistics management. For example, instead of solely focusing on picking orders, warehouse workers might oversee and maintain automated picking systems, requiring expertise in robotics and system troubleshooting. Similarly, the need for skilled technicians to repair and maintain automated guided vehicles (AGVs) and other robotic systems will increase. The transition requires proactive strategies to mitigate job displacement and prepare the workforce for these emerging roles.
Reskilling and Upskilling Initiatives
Addressing the potential for job displacement requires a strategic approach to reskilling and upskilling the existing workforce. Government initiatives, industry partnerships, and educational institutions need to collaborate to provide training programs focused on the skills needed in a robotics-driven logistics environment. These programs should encompass both technical skills, such as programming and robotics maintenance, and soft skills, such as problem-solving, critical thinking, and teamwork. For example, a program might offer warehouse workers the opportunity to learn coding and data analysis to transition into roles managing warehouse automation systems. Companies can also play a crucial role by investing in internal training programs and apprenticeships, ensuring their employees possess the necessary skills to adapt to the changing demands. Amazon, for instance, has invested heavily in its own training programs to upskill its workforce for roles related to warehouse automation.
Benefits for Workers in a Robotics-Driven Logistics Environment
While job displacement is a concern, the integration of robotics can also bring significant benefits to workers. Automation can reduce the physical strain of repetitive tasks, leading to improved worker safety and reduced workplace injuries. Robots can handle heavy lifting and hazardous tasks, leaving human workers to focus on more complex and rewarding activities. Furthermore, automation can lead to increased efficiency and productivity, potentially resulting in higher wages and better working conditions. For example, the implementation of automated guided vehicles in a warehouse can reduce the time spent on transporting goods, allowing human workers to focus on value-added tasks like order fulfillment and quality control. This increased efficiency can translate into higher productivity and potentially higher compensation for workers. The improved safety and ergonomic benefits alone can lead to a healthier and more satisfying work environment.
The Future of Robotics in Logistics
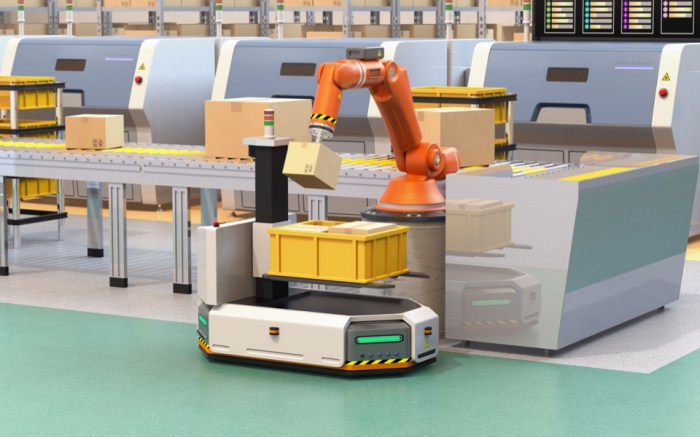
Source: ekathimerini.com
Robots are revolutionizing logistics, optimizing warehouse operations and streamlining delivery. This efficiency boost mirrors the personalized marketing revolution, fueled by AI; check out this insightful piece on The Future of AI-Powered Personalization in Marketing to see how data-driven insights are transforming customer experiences. Ultimately, both robotics and AI-driven personalization aim to create smoother, more efficient processes, from product movement to customer engagement.
The next decade will witness a dramatic reshaping of logistics and supply chain management, driven by increasingly sophisticated robotics and artificial intelligence. We’re moving beyond simple automation to a future where robots, guided by AI, will handle complex tasks, optimize operations in real-time, and significantly enhance efficiency and responsiveness. This isn’t just about replacing human workers; it’s about creating a collaborative ecosystem where humans and robots work together to achieve unprecedented levels of productivity and accuracy.
Future Trends in Robotics and Their Application
Over the next 5-10 years, we can expect to see several key trends. Autonomous mobile robots (AMRs) will become more prevalent, navigating warehouses and distribution centers with greater dexterity and intelligence. Their navigation systems will improve, allowing them to operate in more dynamic and unpredictable environments. We’ll also see a rise in the use of robotic arms with advanced gripping capabilities, enabling them to handle a wider variety of goods, including fragile or irregularly shaped items. Simultaneously, advancements in AI-powered vision systems will allow robots to identify and sort items with unprecedented speed and accuracy, minimizing errors and maximizing throughput. Companies like Amazon are already heavily investing in this area, and their advancements will likely set the pace for the industry. For example, their use of robotic arms in fulfillment centers has significantly increased efficiency in picking and packing orders.
Collaborative Robots (Cobots) in Logistics
Cobots, designed to work safely alongside human workers, will play a crucial role in the future of logistics. Instead of replacing human employees entirely, they will augment their capabilities, handling repetitive or physically demanding tasks. This collaborative approach will lead to increased productivity and improved worker safety. Imagine a scenario where a human worker focuses on the more complex aspects of order fulfillment, while a cobot handles the repetitive tasks of picking and placing items onto conveyor belts. This division of labor leverages the strengths of both humans and robots, creating a more efficient and safer work environment. The integration of haptic feedback systems will further enhance this collaboration, allowing for more seamless interaction between human and robot.
Advancements in AI and Machine Learning Enhancing Robotic Capabilities
AI and ML are the brains behind the increasing intelligence of logistics robots. These technologies enable robots to learn from data, adapt to changing conditions, and optimize their performance over time. For instance, ML algorithms can analyze vast amounts of data to predict demand, optimize inventory levels, and improve route planning for delivery vehicles. AI-powered vision systems will become even more sophisticated, allowing robots to identify and classify objects with greater accuracy, even in cluttered or poorly lit environments. The ability of robots to learn and adapt will be crucial for handling the complexities of real-world logistics operations, making them more robust and reliable. This will also allow for predictive maintenance, reducing downtime and improving the overall lifespan of the robotic systems.
A Hypothetical Advanced Logistics Facility
Imagine a fully automated warehouse, seamlessly integrated with AI and robotics. Autonomous forklifts and AMRs navigate the facility, transporting goods between storage locations and packing stations. Robotic arms, equipped with advanced vision systems, efficiently pick and pack items, while AI algorithms optimize the entire process in real-time. The facility utilizes a sophisticated inventory management system, constantly monitoring stock levels and predicting future demand. AI-powered route optimization systems ensure that delivery vehicles follow the most efficient routes, minimizing transportation costs and delivery times. Data analytics provide real-time insights into the entire operation, allowing managers to identify bottlenecks and optimize performance. This advanced facility would boast significantly improved efficiency, reduced operational costs, and enhanced accuracy, leading to higher customer satisfaction and a competitive advantage in the market. Such facilities are not science fiction; elements of this are already being implemented by leading logistics companies, and the complete integration is a realistic expectation within the next decade.
Safety and Security Considerations
The integration of robots into logistics presents exciting possibilities, but also necessitates a robust approach to safety and security. Failing to prioritize these aspects could lead to accidents, data breaches, and significant operational disruptions. A proactive strategy, encompassing preventative measures and emergency protocols, is crucial for successful and responsible robotic implementation.
Implementing robotic systems in logistics requires a multi-faceted approach to safety, covering both the physical environment and the operational procedures. This includes careful consideration of potential hazards, the development of robust safety protocols, and ongoing employee training. Security measures must also be in place to protect against unauthorized access, data theft, and malicious manipulation of robotic systems.
Safety Protocols for Robotic Systems in Logistics
Effective safety protocols are paramount. These protocols should be designed to minimize the risk of accidents involving both human workers and the robotic systems themselves. This involves integrating safety features into the robots themselves, such as emergency stop mechanisms and sensors to detect obstacles, as well as establishing clear operating procedures for human workers. Regular maintenance and inspections are also critical to ensure the robots continue to function safely and reliably. For example, Amazon’s Kiva robots (now Amazon Robotics) utilize sophisticated sensor systems to avoid collisions with humans and other obstacles within their warehouse environment. This, coupled with clearly marked zones and employee training, minimizes the risk of accidents.
Security Measures for Robotic Systems
Protecting robotic systems from unauthorized access and manipulation is vital. This involves implementing robust cybersecurity measures, including strong passwords, encryption of data transmitted between robots and control systems, and regular software updates to patch security vulnerabilities. Access control systems, limiting physical access to robots and their control systems, are also crucial. Imagine a scenario where a malicious actor gains control of a fleet of autonomous delivery robots – the potential for disruption and damage is substantial. Therefore, measures such as multi-factor authentication and intrusion detection systems are essential components of a comprehensive security strategy.
Potential Risks and Mitigation Strategies
Several potential risks are associated with using robotics in logistics. Malfunctions in robotic systems, leading to accidents or operational downtime, are a significant concern. Mitigation strategies include redundancy in systems, regular maintenance, and fail-safe mechanisms that allow for safe shutdown in case of malfunctions. Another risk is data breaches, potentially compromising sensitive customer information or intellectual property. Robust cybersecurity measures, as mentioned earlier, are critical to mitigating this risk. Finally, the potential for job displacement due to automation needs careful consideration, requiring proactive measures such as retraining and upskilling programs for affected workers.
Safety Checklist for Robotic Systems in a Logistics Warehouse
A comprehensive safety checklist is crucial for the ongoing safe operation and maintenance of robotic systems. This checklist should include regular inspections of robots and their components for wear and tear, ensuring all safety features are functioning correctly, verifying the integrity of safety barriers and zones, and confirming that all employees are adequately trained and understand the safety procedures. The checklist should also include procedures for handling malfunctions and emergencies, ensuring clear communication channels between operators and maintenance personnel. This proactive approach to safety is paramount for minimizing risk and maintaining a safe working environment.
Final Summary
The integration of robotics into logistics and supply chains isn’t just a trend; it’s a fundamental shift that promises unprecedented efficiency, speed, and transparency. While challenges remain – particularly concerning workforce adaptation and safety protocols – the potential benefits are undeniable. The future of logistics is automated, intelligent, and increasingly reliant on robotic systems working seamlessly alongside human expertise. As technology continues to advance, expect even more innovative applications of robotics to redefine how we move goods globally and locally, paving the way for a more agile, responsive, and ultimately, more efficient world of commerce.