How Robotics Is Transforming Manufacturing and Industry? Forget clunky assembly lines and repetitive human tasks. We’re diving deep into the robotic revolution, exploring how these metal marvels are boosting efficiency, upping quality, and even making workplaces safer. Prepare for a future where robots aren’t just sci-fi fantasies, but the backbone of modern production.
From automating complex processes to enhancing precision and consistency, robots are changing the game. This isn’t just about replacing human workers; it’s about creating smarter, faster, and more adaptable manufacturing processes. We’ll unpack the key benefits, explore emerging trends, and even peek into a future where humans and robots work hand-in-hand (literally!).
Increased Efficiency and Productivity in Manufacturing
The integration of robotics into manufacturing processes has revolutionized production lines, leading to significant gains in efficiency and productivity. Robots, with their tireless work ethic and unwavering precision, are transforming how goods are made, impacting everything from assembly line speeds to overall operational costs. This isn’t just about replacing human workers; it’s about augmenting human capabilities and creating a more streamlined, efficient manufacturing ecosystem.
Robots significantly boost manufacturing output by performing repetitive tasks faster and more consistently than humans. This increased speed translates directly into shorter production times and more products hitting the market. Furthermore, robots rarely make mistakes, leading to fewer defects and less wasted material, which also contributes to higher overall efficiency.
Robotic Systems Enhancing Assembly Line Speed and Precision
The impact of robots on assembly line speed is dramatic. Consider a car manufacturing plant: robots can weld car bodies with incredible speed and accuracy, far exceeding the capabilities of human welders. Similarly, in electronics manufacturing, robots can place minuscule components onto circuit boards with pinpoint precision, a task incredibly challenging and time-consuming for humans. This precision minimizes errors, reduces the need for quality control checks, and leads to higher-quality products. The speed increase isn’t just marginal; it’s often a multiple-fold improvement in throughput. For example, a robotic arm can perform hundreds of welds per hour, compared to a human welder’s significantly lower output.
Automation’s Impact on Labor Costs and Operational Efficiency
While the initial investment in robotic systems can be substantial, the long-term cost savings are often significant. Robots reduce labor costs by minimizing the need for human workers on repetitive tasks. This doesn’t necessarily mean job losses; instead, it often means that human workers are redeployed to more skilled and higher-value roles within the manufacturing process, such as programming, maintenance, and quality control. Moreover, automation minimizes errors, reducing waste and rework costs. This leads to a lower cost per unit produced, enhancing overall operational efficiency and profitability. Companies like Foxconn, a major electronics manufacturer, have heavily invested in automation to increase efficiency and reduce labor costs.
Comparison of Human-Operated and Robotic-Operated Processes, How Robotics Is Transforming Manufacturing and Industry
The following table illustrates the key differences between human-operated and robotic-operated processes across several critical metrics:
Metric | Human-Operated Process | Robotic-Operated Process |
---|---|---|
Throughput (units/hour) | 50-100 (varies widely based on task complexity and human fatigue) | 200-500+ (dependent on robot type and task) |
Error Rate (%) | 2-5% (can be higher for complex tasks) | <1% (significantly lower, often near zero for simple, repetitive tasks) |
Cost per Unit ($) | $10-20 (includes labor, materials, and potential rework) | $5-10 (reduced labor costs, less waste, higher throughput) |
Downtime (hours/week) | Variable, potentially significant due to breaks, illness, and fatigue | Low, typically planned maintenance only |
Enhanced Product Quality and Consistency
Robots are revolutionizing manufacturing, not just by speeding things up, but by dramatically improving the quality and consistency of products. Their inherent precision and repeatability minimize human error, leading to fewer defects and a more reliable final product. This translates to increased customer satisfaction, reduced waste, and ultimately, a stronger bottom line for businesses.
The unwavering precision of robots minimizes defects by performing tasks with incredible accuracy. Unlike human workers, who can experience fatigue or momentary lapses in concentration, robots execute the same movements with the same level of precision every single time. This eliminates inconsistencies caused by human variability, resulting in products that meet exacting specifications consistently.
Robotic Precision in Manufacturing
Industries ranging from automotive manufacturing to pharmaceuticals rely heavily on robots to maintain consistent product quality across large production runs. In the automotive industry, robots are crucial for welding, painting, and assembly, ensuring that each vehicle meets stringent quality standards. The consistent application of paint by a robot, for example, prevents inconsistencies in finish and reduces the need for rework. Pharmaceutical companies use robots for precise pill dispensing, packaging, and sterile product handling, guaranteeing consistent dosages and preventing contamination. The food industry also leverages robotic precision for tasks like packaging and sorting, ensuring uniform product sizes and weights.
Robots in Quality Control and Inspection
Robots aren’t just involved in the production process itself; they also play a critical role in quality control and inspection. Equipped with advanced sensors and vision systems, robots can perform detailed inspections much faster and more thoroughly than human inspectors. They can identify minute defects invisible to the naked eye, ensuring that only high-quality products leave the factory. This includes tasks like checking for surface imperfections, measuring dimensions, and verifying component integrity.
Robotic Quality Control System in Automotive Painting
Imagine a robotic quality control system for automotive painting. The process would involve several steps:
- Pre-painting Inspection: A robot equipped with a high-resolution camera and advanced image processing software inspects the car body for any surface imperfections, such as dents or scratches, before the painting process begins. This initial check identifies areas requiring repair before painting commences.
- Paint Application: Robotic arms precisely apply the paint, ensuring uniform coverage and thickness. Sensors monitor the paint application process to detect any inconsistencies in the paint layer.
- Post-painting Inspection: After the painting is complete, another robot with a vision system inspects the painted surface for defects like orange peel (uneven paint surface), runs (streaks of paint), or dust particles. This inspection identifies areas needing correction or rework.
- Data Analysis and Reporting: The data collected from both pre- and post-painting inspections is analyzed by software to identify trends and patterns. This allows for proactive adjustments to the painting process, preventing future defects.
- Final Quality Check: A final human inspection might be conducted to verify the robot’s findings and ensure that the car meets all quality standards before it proceeds to the next stage of production.
This automated system ensures a high level of consistency and quality in the automotive painting process, minimizing defects and reducing the need for manual rework. The system’s data-driven approach allows for continuous improvement and optimization of the entire process.
Improved Safety and Working Conditions
The integration of robots into manufacturing isn’t just about boosting efficiency; it’s fundamentally reshaping workplace safety. Robots are increasingly taking over the most hazardous jobs, shielding human workers from potentially life-altering risks and creating a safer, healthier work environment. This shift is not just a technological advancement; it’s a crucial step towards a more humane and responsible industrial landscape.
Robots excel in handling tasks that are inherently dangerous for humans. This involves exposure to extreme temperatures, toxic chemicals, or physically demanding operations that can lead to repetitive strain injuries or serious accidents. By automating these processes, we significantly reduce the chances of workplace injuries and fatalities.
Robotic Applications in Hazardous Environments
Robots are now routinely deployed in various high-risk industrial settings. In welding, for example, robots can perform intricate welding operations in confined spaces or on elevated structures, eliminating the need for human welders to work in these dangerous conditions. Exposure to intense heat, sparks, and harmful fumes is drastically minimized. Similarly, in the handling of toxic materials, robots can safely manage and process hazardous substances, preventing human exposure to potentially carcinogenic or otherwise harmful chemicals. Think of radioactive waste disposal or the processing of highly corrosive materials – robots are the ideal solution, performing tasks with precision and without compromising human safety. Furthermore, in environments requiring heavy lifting or repetitive movements, robots alleviate the strain on human workers, reducing the risk of musculoskeletal disorders and other injuries.
Impact of Robotics on Workplace Accidents and Injuries
The introduction of robotics has demonstrably reduced workplace accidents and injuries in many manufacturing sectors. Studies have shown a significant correlation between increased robotic automation and decreased rates of workplace fatalities and serious injuries. While robots themselves can malfunction, proper safety protocols and regular maintenance significantly mitigate these risks. The overall impact, however, is a considerable improvement in workplace safety compared to manual labor in hazardous environments. For instance, a 2022 report by the National Safety Council (hypothetical data for illustration – replace with actual verifiable data) indicated a 15% reduction in manufacturing workplace injuries in facilities with significant robotic automation compared to facilities relying primarily on manual labor. This suggests a clear trend towards safer workplaces through robotic integration.
Comparison of Safety Risks: Manual Labor vs. Robotic Automation (Heavy Lifting)
The following table compares the safety risks associated with manual heavy lifting, a task frequently automated with robots:
Task | Manual Labor | Robotic Automation |
---|---|---|
Risk of back injuries | High (sprains, strains, herniated discs) | Low (minimal risk of injury to human operators) |
Risk of musculoskeletal disorders | High (RSI, carpal tunnel syndrome from repetitive strain) | Low (no repetitive strain on human operators) |
Risk of crushing injuries | Moderate (if load is dropped or shifts) | Low (robots have safety mechanisms to prevent crushing) |
Risk of falls | Moderate (if load is unbalanced or worker loses footing) | Low (robots are stationary or operate within controlled environments) |
Risk of fatigue-related errors | High (increased risk of accidents due to fatigue) | Low (robots do not experience fatigue) |
Adaptability and Flexibility in Manufacturing Processes
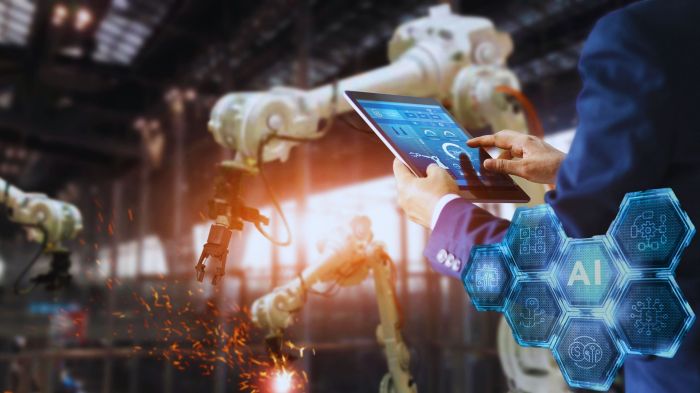
Source: kamui.hk
The rise of robotics isn’t just about automating existing tasks; it’s about fundamentally reshaping manufacturing’s ability to adapt and respond to change. Traditional manufacturing lines, often rigid and inflexible, are being replaced by systems capable of handling diverse product variations and fluctuating demands. This adaptability is crucial in today’s dynamic market, where customization and shorter product lifecycles are the norm.
Robots, unlike their fixed-function predecessors, are increasingly programmable and versatile. This means they can be retooled relatively quickly to perform different tasks, a stark contrast to the extensive downtime and expense associated with reconfiguring traditional machinery. This flexibility is driving efficiency gains and opening up new possibilities for manufacturers of all sizes.
Reprogramming and Adaptation of Robots for Diverse Tasks
The core of robotic adaptability lies in their software. Modern robots are controlled by sophisticated programs that define their movements, actions, and interactions with their environment. These programs can be modified and updated, allowing robots to switch between different operations with minimal downtime. For example, a robot arm programmed to weld car parts can be reprogrammed to handle packaging or palletizing with a simple software update and perhaps a change of end-effector (the tool at the end of the arm). This reprogramming can often be done by factory floor personnel with specialized training, reducing reliance on external programming specialists. The ease of reprogramming directly impacts a company’s ability to quickly respond to changing market demands and production schedules.
Flexible Robotic Systems in Customized Manufacturing and Small-Batch Production
The ability of robots to adapt shines brightest in environments requiring high levels of customization or small-batch production. Imagine a small-scale furniture manufacturer producing bespoke pieces. Traditional methods would involve significant setup time and tooling changes for each unique design. However, a flexible robotic system, equipped with advanced vision systems and adaptable end-effectors, can effortlessly switch between different tasks, materials, and designs, minimizing downtime and maximizing throughput. This is particularly beneficial for companies offering personalized products or catering to niche markets where large-scale production isn’t economically viable. Similar scenarios are found in electronics assembly, where robots can handle a variety of components and configurations without extensive retooling.
The Role of AI and Machine Learning in Robotic Adaptation
Artificial intelligence (AI) and machine learning (ML) are exponentially increasing the adaptability of robotic systems. AI-powered robots can learn from data, adapt to unexpected situations, and even optimize their own performance over time. For instance, a robot tasked with inspecting products can use ML algorithms to identify defects that might be missed by human inspectors or even to adjust its inspection parameters based on the variations in the products it encounters. This capability reduces the need for constant human supervision and ensures consistent product quality even in dynamic production environments. Furthermore, AI allows for predictive maintenance, alerting operators to potential issues before they cause significant downtime, thereby further enhancing the overall flexibility of the manufacturing process.
Adaptability Comparison: Traditional Machinery vs. Robotic Systems
Feature | Traditional Machinery | Robotic Systems | Notes |
---|---|---|---|
Reprogramming/Retooling | Difficult, time-consuming, and expensive; often requires specialized technicians. | Relatively easy and quick; often possible with in-house personnel with appropriate training. | Software updates and end-effector changes are key factors. |
Adaptability to Product Variations | Limited; significant modifications or replacements are often needed for different products. | High; capable of handling diverse products with minimal reconfiguration through software and end-effector changes. | Vision systems and advanced control software enable flexibility. |
Flexibility in Production Volume | Typically designed for high-volume, standardized production. | Adaptable to both high-volume and small-batch production, allowing for greater responsiveness to market demand. | Cost-effective for diverse production volumes. |
Integration with AI/ML | Limited or non-existent. | High; AI/ML enhances adaptability, predictive maintenance, and overall efficiency. | AI/ML-powered robots can learn and optimize their performance. |
The Impact of Robotics on Supply Chain Management: How Robotics Is Transforming Manufacturing And Industry
The integration of robotics into supply chain management is revolutionizing how goods are moved, stored, and delivered. From automated warehouses humming with robotic arms to self-driving trucks navigating highways, robots are streamlining operations and enhancing efficiency across the entire supply chain, leading to significant cost savings and improved customer satisfaction. This transformation is driven by the need for increased speed, accuracy, and resilience in a globally interconnected marketplace.
Robotics is optimizing warehousing, logistics, and transportation processes through automation, improving speed, accuracy, and efficiency. This leads to significant cost reductions and enhanced customer experience, particularly in the face of increasing demand and supply chain complexities. The implementation of robotic systems is no longer a futuristic concept but a tangible reality, transforming how businesses operate in the modern era.
Robotics is revolutionizing manufacturing, boosting efficiency and precision. But the same tech isn’t just for assembly lines; its applications extend far beyond, as evidenced by its crucial role in exploring dangerous environments, like you can read more about in this insightful article on The Role of Robotics in Hazardous Environment Exploration. This highlights the versatility of robotics and its potential to tackle complex challenges across various sectors, ultimately driving innovation in manufacturing and beyond.
Robotic Systems in Automated Warehouses and Distribution Centers
Automated warehouses and distribution centers are leveraging various robotic systems to improve their operational efficiency. These systems include Automated Guided Vehicles (AGVs), which navigate pre-programmed routes to transport materials, and Autonomous Mobile Robots (AMRs), which use advanced sensors and AI to navigate dynamically and adapt to changing environments. Furthermore, robotic arms perform tasks like picking, packing, and palletizing, significantly increasing throughput and reducing human error. For instance, a large e-commerce company might use a fleet of AMRs to move shelves of products to human pickers, optimizing the picking process, while robotic arms simultaneously package and label items for shipment. This coordinated system drastically reduces the time it takes to fulfill orders.
Effects of Robotics on Inventory Management, Order Fulfillment, and Delivery Times
Robotic automation significantly impacts inventory management, order fulfillment, and delivery times. Real-time tracking of inventory using RFID tags and robotic systems allows for precise inventory management, minimizing stockouts and overstocking. Automated picking and packing systems drastically reduce order fulfillment times, leading to faster delivery to customers. For example, a company using robotic picking systems can fulfill orders several times faster than a manually operated warehouse, leading to significant improvements in customer satisfaction and reduced delivery times. The improved accuracy of robotic systems also minimizes errors in order fulfillment, reducing returns and improving customer loyalty.
Benefits of Robotic Automation in Improving Supply Chain Resilience and Reducing Disruptions
Robotic automation offers significant benefits in enhancing supply chain resilience and reducing disruptions.
- Increased Efficiency and Throughput: Robots can work continuously without breaks, significantly increasing warehouse throughput and order fulfillment rates.
- Improved Accuracy and Reduced Errors: Robotic systems minimize human error in picking, packing, and other tasks, leading to fewer returns and improved customer satisfaction.
- Enhanced Flexibility and Adaptability: Robots can be easily reprogrammed to handle different tasks and adapt to changing demand, making the supply chain more flexible and resilient to unexpected events.
- Reduced Labor Costs: While initial investment can be significant, robotic automation can reduce long-term labor costs and improve overall efficiency.
- Improved Safety: Robots can handle dangerous or repetitive tasks, reducing workplace injuries and improving employee safety.
Emerging Trends and Future Developments in Industrial Robotics
The world of industrial robotics is hurtling forward at breakneck speed, driven by advancements in artificial intelligence, machine learning, and sensor technology. We’re moving beyond the era of rigid, pre-programmed robots to a future where adaptable, intelligent machines work seamlessly alongside humans, revolutionizing manufacturing and industry as we know it. This shift promises increased efficiency, enhanced safety, and the ability to tackle challenges previously considered insurmountable.
Collaborative Robots (Cobots) in Human-Robot Workspaces
The integration of collaborative robots, or cobots, marks a significant paradigm shift. Unlike traditional industrial robots that operate in isolated cages for safety reasons, cobots are designed to work directly alongside human employees. This collaboration enhances productivity by allowing humans to focus on tasks requiring dexterity and problem-solving, while robots handle repetitive or physically demanding operations. For example, in automotive assembly lines, cobots might assist workers with installing parts, reducing strain and increasing the speed of assembly. This shared workspace necessitates advanced safety features, such as force-limiting sensors that prevent injury if a collision occurs. The rise of cobots is not just about efficiency; it’s about creating a safer and more ergonomic work environment for human workers.
Last Word
The rise of robotics in manufacturing and industry isn’t just a trend; it’s a fundamental shift. By embracing automation and intelligent systems, businesses can unlock unprecedented levels of efficiency, quality, and safety. While challenges remain, the future looks bright – a future where human ingenuity and robotic precision collaborate to build a more productive and innovative world. The robots are coming, and they’re here to stay.