How Robotics is Transforming Logistics and Shipping Operations: Forget slow boats and manual labor – the future of getting your stuff from A to B is seriously automated. We’re talking robots zipping packages across warehouses, autonomous trucks cruising down highways, and drones delivering your online order straight to your doorstep. This isn’t science fiction; it’s the rapidly evolving reality of modern logistics, and it’s changing everything.
From automating mundane tasks to optimizing entire supply chains, robotics is injecting a massive dose of efficiency and resilience into the industry. This means faster deliveries, lower costs, and a supply chain that’s better equipped to handle unexpected disruptions. Get ready to dive into the world of automated warehouses, self-driving delivery vehicles, and the incredible impact of robots on how we move goods around the globe.
Automation in Warehousing
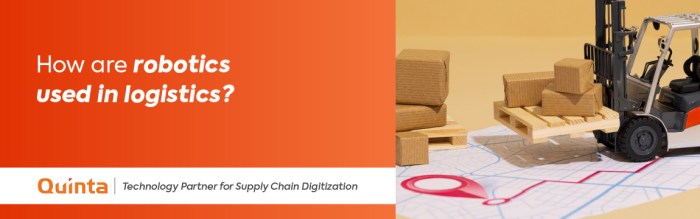
Source: co.in
Robotics are revolutionizing logistics, streamlining warehouses and optimizing delivery routes. But with this increased automation comes a surge in data, raising crucial questions about security and transparency. This is where the game-changing potential of blockchain comes in; learn more about how it’s tackling these issues in data privacy and ownership by checking out this article: How Blockchain is Redefining Online Privacy and Data Ownership.
Ultimately, secure data management via blockchain could unlock even greater efficiencies in robotic logistics systems.
The modern warehouse is undergoing a radical transformation, driven by the relentless pursuit of efficiency and speed. E-commerce’s explosive growth has created an unprecedented demand for faster order fulfillment, pushing logistics companies to adopt advanced automation technologies. This shift is significantly impacting warehouse operations, leading to streamlined processes and reduced operational costs.
The integration of robotics and automation into warehousing is no longer a futuristic concept; it’s a current reality reshaping the industry. From the moment goods arrive until they’re shipped, robots are increasingly handling tasks previously performed by humans, boosting productivity and accuracy while minimizing human error.
Automated Guided Vehicles (AGVs) and Autonomous Mobile Robots (AMRs)
AGVs and AMRs are revolutionizing material handling within warehouses. AGVs follow pre-programmed paths, typically guided by wires or magnetic strips embedded in the floor. They are highly reliable for repetitive tasks along fixed routes. In contrast, AMRs utilize advanced sensors and AI to navigate dynamically, adapting to changing warehouse layouts and obstacles. This adaptability makes AMRs more flexible and efficient in dynamic environments. The impact on warehouse efficiency is significant: AMRs and AGVs reduce labor costs associated with transporting goods, minimize the risk of human error in material handling, and optimize warehouse space utilization by streamlining material flow. For example, a large e-commerce fulfillment center might use a fleet of AMRs to transport totes of picked items from picking stations to packing areas, significantly reducing transit time compared to manual handling.
Robotic Arms in Picking, Packing, and Palletizing
Robotic arms, often equipped with advanced vision systems and grippers, are transforming picking, packing, and palletizing operations. These robotic systems can handle a wide range of items with varying shapes and sizes, accurately picking items from shelves or conveyor belts and placing them into boxes. In packing, robotic arms can seal boxes, apply labels, and even customize packaging based on order specifications. Palletizing robots efficiently stack boxes onto pallets, ensuring stability and optimizing pallet space. This automation significantly increases throughput, reduces labor costs, and improves the consistency and accuracy of these tasks. A prime example is the use of robotic arms in a grocery distribution center, where they can quickly and accurately pick and pack individual items for grocery delivery orders, significantly increasing order fulfillment speed.
Robotic Systems in Different Warehouse Sizes and Configurations
The implementation of robotic systems varies depending on the size and configuration of the warehouse. Smaller warehouses might benefit from individual robotic arms integrated into existing workflows, while larger facilities can leverage more comprehensive automated systems. The choice of technology depends on factors like budget, throughput requirements, and the types of goods handled. A small warehouse might implement a single robotic arm for palletizing, while a large distribution center might use a fully automated system incorporating AGVs, robotic arms, and automated storage and retrieval systems (AS/RS).
System | Cost | Throughput | Maintenance Requirements |
---|---|---|---|
Automated Storage and Retrieval System (AS/RS) | High | Very High | High |
Automated Conveyor Systems | Medium | High | Medium |
Robotic Picking Systems | Medium to High | High to Very High | Medium to High |
Robotics in Transportation
The logistics and shipping industry is undergoing a massive transformation, driven largely by the integration of robotics. While warehouse automation has grabbed headlines, the impact of robotics on transportation itself is equally profound, promising to revolutionize how goods move across the globe. This shift is being spearheaded by autonomous trucks and delivery drones, technologies that are rapidly reshaping the landscape of goods transportation.
Autonomous trucks and delivery drones are changing the landscape of goods transportation by offering increased efficiency, reduced labor costs, and the potential for 24/7 operation. Autonomous trucks, for instance, can operate continuously without needing rest stops, significantly reducing transit times. Delivery drones, meanwhile, offer a faster and more flexible solution for last-mile delivery, bypassing traffic congestion and reaching remote locations more easily. These advancements are not just incremental improvements; they represent a fundamental shift in how we think about logistics and the movement of goods.
Autonomous Vehicle Integration into Logistics Networks, How Robotics is Transforming Logistics and Shipping Operations
Integrating autonomous vehicles into existing logistics networks presents both significant challenges and exciting opportunities. One major hurdle is the need for robust infrastructure, including reliable communication networks and precise mapping systems. Existing road networks may need upgrades to accommodate autonomous vehicles safely. Furthermore, the legal framework surrounding autonomous vehicles is still evolving, requiring careful consideration of liability and regulatory compliance. However, the potential benefits are immense. Improved efficiency, reduced fuel consumption, and enhanced safety could significantly reduce the overall cost of transportation, making goods more accessible and affordable. The seamless integration of autonomous vehicles with existing warehouse automation systems further promises a more streamlined and efficient end-to-end logistics process. Successful integration will require collaborative efforts between technology developers, logistics providers, and policymakers.
Safety and Regulatory Aspects of Autonomous Delivery Systems
The deployment of autonomous delivery systems raises crucial safety and regulatory concerns. Ensuring the safety of both the public and the cargo being transported is paramount. This requires rigorous testing and validation of autonomous vehicle systems, as well as the development of robust safety protocols and emergency procedures. Regulatory frameworks need to address issues such as airspace management for drones, liability in case of accidents, and data privacy. International collaboration is crucial to establish consistent standards and regulations for autonomous vehicles operating across borders. The successful integration of these systems will depend on a balance between technological innovation and responsible regulation.
Autonomous Delivery Drone Benefits and Risks
The use of autonomous delivery drones presents a unique set of benefits and risks. Careful consideration of these factors, coupled with appropriate mitigation strategies, is essential for responsible deployment.
Benefit | Risk | Mitigation Strategy | Estimated Cost |
---|---|---|---|
Faster delivery times, especially for last-mile delivery | Accidents due to technical malfunctions or unforeseen circumstances | Redundant systems, rigorous testing, and emergency protocols | High initial investment in technology and infrastructure; ongoing maintenance costs |
Reduced labor costs | Security risks, such as theft or unauthorized access to cargo | Secure packaging, GPS tracking, and encrypted communication | Implementation of security measures, insurance premiums |
Increased accessibility to remote areas | Regulatory hurdles and airspace limitations | Collaboration with regulatory bodies, development of standardized operating procedures | Legal fees, compliance costs |
Reduced traffic congestion | Public acceptance and concerns about noise pollution | Public awareness campaigns, noise reduction technologies | Marketing and public relations expenses |
Enhanced Efficiency and Productivity
The integration of robotics into logistics and shipping is no longer a futuristic fantasy; it’s a present-day reality dramatically reshaping efficiency and productivity. Companies are leveraging robotic systems to streamline operations, reduce costs, and deliver goods faster than ever before. This shift isn’t just about replacing human workers; it’s about augmenting capabilities and optimizing processes for unprecedented levels of performance.
The impact of robotics on logistics and shipping is quantifiable through several key performance indicators (KPIs). These metrics offer a clear picture of the improvements achieved and allow for ongoing optimization.
Key Metrics for Measuring Robotic Impact
Analyzing the impact of robotics requires a focused approach using specific metrics. Improved throughput, reduced error rates, and faster order fulfillment times are all crucial indicators. For example, measuring the number of packages processed per hour before and after robotic implementation provides a clear picture of increased throughput. Similarly, tracking the decrease in order fulfillment errors demonstrates the enhanced accuracy robotic systems offer. The reduction in processing time from order placement to delivery showcases the overall speed improvements. Furthermore, the return on investment (ROI) calculation, considering initial investment costs against the savings from reduced labor and increased efficiency, provides a vital long-term perspective. Finally, safety metrics, such as the reduction in workplace accidents, highlight the added benefit of robotic automation in minimizing workplace hazards.
Examples of Successful Robotic Implementations
Several companies have successfully implemented robotic systems to boost their efficiency. Amazon, for example, heavily relies on robots in its fulfillment centers, using them for tasks like moving shelves and picking items. This has significantly increased the speed and accuracy of order fulfillment. Similarly, DHL utilizes automated guided vehicles (AGVs) in its warehouses, optimizing material handling and reducing manual labor. These AGVs navigate autonomously, transporting goods efficiently across large warehouse spaces, minimizing transit times and improving overall throughput. Furthermore, companies like Ocado, a UK-based online grocery retailer, have built fully automated warehouses that leverage a complex network of robots to pick, pack, and sort groceries with remarkable speed and precision. These examples showcase the diverse applications of robotics across different segments of the logistics and shipping industry, demonstrating significant improvements in productivity and efficiency.
Robotics, Labor Costs, and Order Fulfillment Speed
- Reduced Labor Costs: Robotics automates repetitive, labor-intensive tasks, reducing the need for a large human workforce in warehousing and transportation. This directly translates to lower labor costs, including wages, benefits, and training expenses. The extent of cost reduction varies depending on the scale of automation and the specific tasks automated. However, even partial automation can result in substantial savings over time.
- Improved Order Fulfillment Speed: Robotic systems can operate 24/7 without breaks, significantly increasing the speed of order processing and delivery. Automated picking, packing, and sorting processes eliminate human bottlenecks and ensure faster turnaround times. This accelerated order fulfillment leads to improved customer satisfaction and a competitive advantage in the market.
Improved Accuracy and Reduced Errors
Robotic systems are revolutionizing logistics and shipping by significantly reducing human error, a persistent problem that leads to delays, financial losses, and damaged reputations. The precision and repeatability of robots offer a level of accuracy simply unattainable through manual processes, leading to substantial improvements across the entire supply chain.
Robotic systems minimize human error in various tasks by automating processes that are prone to mistakes. Picking, packing, and sorting, for instance, are tasks that require meticulous attention to detail and are easily susceptible to human fatigue and oversight. Robots, however, can perform these tasks tirelessly and consistently, adhering to pre-programmed instructions and minimizing the chance of mispicks, incorrect packing, or items being sorted into the wrong locations. This increased accuracy translates directly into fewer returns, reduced customer complaints, and a more efficient overall operation.
Inventory Management and Stock Discrepancies
The precise tracking capabilities of robotic systems significantly enhance inventory management. Robots equipped with barcode scanners and other identification technologies can accurately track the movement of goods throughout the warehouse, providing real-time data on stock levels. This precise data minimizes discrepancies between physical inventory and recorded inventory, a common issue in manual systems that can lead to stockouts, overstocking, and lost revenue. The automation eliminates the human element in counting and recording, reducing the chances of human error leading to inaccurate inventory data.
Preventing Costly Shipping and Delivery Mistakes
The potential for costly mistakes during shipping and delivery is significantly reduced with robotic automation. For example, robots can verify the contents of packages against shipping manifests, ensuring that the correct items are shipped to the correct destinations. This eliminates errors that might otherwise lead to delays, returns, and customer dissatisfaction. The integration of robotics with warehouse management systems (WMS) further enhances accuracy by providing a seamless flow of information, ensuring that all steps in the process are coordinated and monitored effectively.
Imagine a scenario where a high-value electronic component is mistakenly shipped to the wrong customer due to a manual packing error. This mistake could lead to significant financial losses for the company, including the cost of the component, shipping, and potential legal ramifications. With robotic automation, this type of error would be far less likely to occur, due to the precise and consistent nature of the robotic picking and packing process. The system would cross-reference the order with the item and package contents before shipping, preventing the mistake altogether.
Impact on Supply Chain Resilience
The integration of robotics into logistics and shipping is fundamentally reshaping supply chain resilience. No longer are businesses tethered to the limitations of human labor and its inherent vulnerabilities. Instead, robotic systems offer a dynamic, adaptable approach to navigating the unpredictable nature of global commerce. This shift towards automation allows companies to better withstand disruptions, optimize operations during crises, and ultimately, enhance their overall competitive edge.
Robotics significantly bolster supply chain resilience by creating a more flexible and adaptable system. Traditional, manual systems are often rigid and struggle to respond quickly to unexpected changes. A sudden surge in demand, a natural disaster, or a geopolitical event can easily overwhelm these systems, leading to delays, shortages, and significant financial losses. Robotic systems, however, can be reprogrammed and redeployed relatively quickly to adapt to these shifts, minimizing downtime and maintaining operational continuity. This adaptability is a game-changer in an increasingly volatile global landscape.
Mitigation of Disruption Risks
Robotic systems offer a powerful toolkit for mitigating risks associated with supply chain disruptions. For example, autonomous mobile robots (AMRs) in warehouses can continue operating even during power outages, utilizing backup power sources to maintain essential functions. Similarly, robotic arms can seamlessly switch between tasks, ensuring that operations continue even if certain processes are temporarily impacted. Advanced analytics integrated with robotic systems can predict potential disruptions based on real-time data, allowing for proactive adjustments to mitigate the impact before it escalates. Consider a scenario where a port strike is anticipated. A robotic-enabled logistics network can reroute shipments proactively, leveraging alternative transportation modes and storage facilities to minimize delays. This proactive approach stands in stark contrast to traditional systems, which often react to disruptions after they occur.
Comparison of Robotic and Traditional Systems
The resilience of robotic-based logistics systems compared to traditional manual systems is demonstrably superior. The following table illustrates the response time difference during a simulated natural disaster:
Event | Traditional Warehouse Response Time | Robotic Warehouse Response Time | Cost Difference |
---|---|---|---|
Hurricane impacting warehouse access | 72 hours to assess damage and resume partial operations; full restoration taking weeks. | 24 hours to assess damage and resume partial operations using backup power and alternative routes; full restoration within 72 hours. | Significant cost savings due to reduced downtime, lower labor costs, and minimized inventory loss. |
Earthquake causing structural damage | Extensive delays and potential complete shutdown, requiring rebuilding and substantial time for recovery. | Damage assessment and operational restart within 48 hours, with prioritized processing of essential goods; recovery time significantly reduced. | Substantial cost savings through faster recovery and reduced need for extensive rebuilding. Potential for insurance claims reduction. |
Flood affecting transportation routes | Significant delays and potential for significant product damage and loss. | Reprogramming of routes and transportation methods using real-time data to avoid affected areas, minimizing delays and losses. | Cost savings through reduced product loss and quicker delivery times, potentially offsetting initial investment in robotics. |
The data above highlights the clear advantage of robotic systems in maintaining operational continuity during unforeseen events. While the initial investment in robotics is substantial, the long-term cost savings stemming from reduced downtime, minimized losses, and enhanced efficiency far outweigh the initial expense. The resilience offered by these systems is a crucial factor in a competitive landscape increasingly characterized by uncertainty and volatility.
The Future of Robotics in Logistics: How Robotics Is Transforming Logistics And Shipping Operations
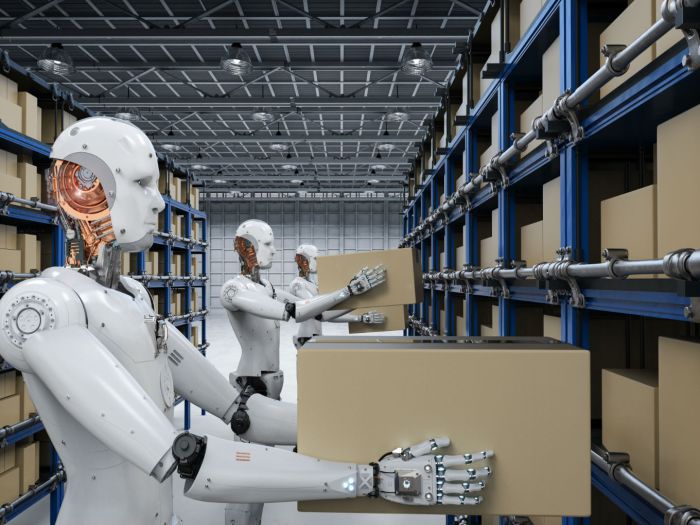
Source: inc42.com
The integration of robotics in logistics is rapidly evolving, moving beyond simple automation to encompass sophisticated AI-powered systems capable of complex decision-making and adaptive responses. This next generation of robotic technologies promises to redefine efficiency, resilience, and the overall landscape of the global supply chain. We’re on the cusp of a truly transformative era.
Emerging Robotic Technologies and Their Impact
Autonomous Mobile Robots (AMRs) and Advanced Navigation
Autonomous Mobile Robots (AMRs) are already prevalent in warehouses, but future iterations will boast significantly enhanced navigation capabilities. Expect to see AMRs equipped with advanced sensors (LiDAR, computer vision, and RFID) allowing for seamless operation in dynamic environments, navigating obstacles and adapting to changing layouts without human intervention. This includes the ability to learn and optimize routes based on real-time data, maximizing efficiency and minimizing congestion. For example, Amazon’s Kiva robots represent a foundational step, but future AMRs will go far beyond simple item retrieval, handling more complex tasks and integrating seamlessly with other robotic systems.
AI-Powered Sorting and Handling Systems
The integration of artificial intelligence will dramatically improve the speed and accuracy of sorting and handling processes. Advanced machine learning algorithms will enable robots to identify and classify items with unprecedented precision, even in cluttered or poorly lit conditions. This includes the ability to handle delicate or irregularly shaped objects, a significant challenge for current robotic systems. Imagine a system that can automatically sort and pack a diverse range of products – from fragile glassware to bulky electronics – with minimal human oversight. Companies like Boston Dynamics are already developing robots with impressive dexterity, pointing towards this future.
Drone Delivery and Autonomous Vehicles
Drone delivery is no longer a futuristic fantasy; it’s rapidly becoming a reality. However, the future will see larger, more capable drones capable of carrying heavier payloads over longer distances. Similarly, the development of fully autonomous trucks and ships promises to revolutionize long-haul transportation, reducing costs and improving delivery times. Companies like Starship Technologies are already testing autonomous delivery robots on a smaller scale, showcasing the potential for wider adoption. These technologies will need to address safety and regulatory challenges, but their potential impact is undeniable.
Challenges in Widespread Adoption
High Initial Investment Costs and ROI
The implementation of advanced robotic systems requires significant upfront investment. The cost of purchasing, installing, and maintaining sophisticated robots, along with the necessary infrastructure upgrades, can be a major barrier for smaller businesses. A clear return on investment (ROI) calculation, factoring in long-term operational efficiency gains, is crucial for successful adoption.
Integration Complexity and Data Management
Integrating different robotic systems and legacy systems within existing logistics networks can be incredibly complex. Ensuring seamless data flow and communication between various components is critical. This requires robust data management systems and skilled personnel capable of managing and interpreting the large volumes of data generated by these systems.
Workforce Reskilling and Adaptation
The widespread adoption of robotics will inevitably lead to changes in the workforce. Retraining and upskilling programs are essential to equip workers with the skills needed to manage and maintain these advanced systems. A focus on collaborative robots (cobots) that work alongside human employees can help mitigate job displacement concerns and foster a more efficient and productive work environment.
A Futuristic Logistics Center: A Visual Description
A futuristic logistics center is a hive of coordinated activity, yet remarkably silent. The vast warehouse is a brightly lit, highly organized space with automated guided vehicles (AGVs) silently gliding along designated pathways, transporting pallets and containers. Articulated robotic arms, equipped with advanced sensors and grippers, deftly sort and package items with incredible speed and precision. Overhead, autonomous drones zip between shelves, retrieving items and transporting them to designated packing stations. A central control system, powered by artificial intelligence, monitors and manages the entire operation, optimizing workflows and adapting to real-time demands. Human workers are present, but their roles are primarily supervisory, focused on system monitoring, maintenance, and higher-level decision-making. The overall environment is clean, efficient, and remarkably quiet, a stark contrast to the bustling, noisy warehouses of today. This is a glimpse into a future where robotics and AI are seamlessly integrated, driving unprecedented efficiency and productivity in the logistics industry.
Final Conclusion
The integration of robotics into logistics and shipping isn’t just a trend; it’s a fundamental shift in how we operate. As technology continues to advance, we can expect even greater automation, increased efficiency, and a more resilient global supply chain. While challenges remain, the potential benefits – from reduced costs and improved accuracy to enhanced sustainability – are undeniable. The future of logistics is robotic, and it’s arriving faster than you might think. So, buckle up, because this ride is going to be automated, efficient, and undeniably cool.