How Robotics is Shaping the Future of Autonomous Factories? It’s not just sci-fi anymore. We’re diving headfirst into a manufacturing revolution, where robots aren’t just tools, but collaborators, reshaping everything from production lines to workplace safety. This isn’t your grandpappy’s factory; we’re talking about autonomous systems, intelligent machines working tirelessly, and a future where efficiency meets innovation in ways we’re only beginning to understand. Get ready for a deep dive into the robotic heart of tomorrow’s industry.
From collaborative robots assisting human workers to autonomous guided vehicles (AGVs) zipping around warehouses, the range of robotic applications is staggering. This transformation is driven by the need for increased productivity, reduced costs, and enhanced safety – a trifecta that’s reshaping the competitive landscape. Industries like automotive, electronics, and logistics are already seeing major gains, and the ripple effects are spreading far and wide.
The Rise of Autonomous Factories
The manufacturing landscape is undergoing a dramatic transformation, driven by the relentless march of automation. Autonomous factories, once a futuristic fantasy, are rapidly becoming a reality, relying heavily on robotics to streamline operations and boost efficiency. This shift isn’t just about replacing human workers; it’s about creating more resilient, adaptable, and productive manufacturing environments capable of meeting the demands of a rapidly changing global economy.
The increasing adoption of robotics in manufacturing stems from several key factors. Firstly, the need for enhanced productivity and reduced operational costs is a major driver. Robots can work tirelessly, consistently producing high-quality outputs without breaks or fatigue, leading to significant cost savings in the long run. Secondly, the pursuit of improved product quality and consistency is another crucial element. Robots perform tasks with precision and accuracy far exceeding human capabilities, minimizing errors and ensuring uniformity in the final product. Finally, the growing demand for customization and shorter product lifecycles necessitates flexible and adaptable manufacturing processes, which robotics excels at providing.
Industries Leveraging Robotic Automation
The automotive industry has been at the forefront of robotic automation for decades, utilizing robots for tasks such as welding, painting, and assembly. The precision and speed offered by robotic systems are crucial in maintaining high production volumes while adhering to stringent quality standards. Beyond automobiles, the electronics industry relies heavily on robotic automation for the assembly of intricate components, particularly in the manufacturing of smartphones and other consumer electronics. The delicate nature of these components makes robotic precision essential. Furthermore, the food and beverage industry is increasingly incorporating robotics for tasks like packaging, palletizing, and material handling, ensuring consistency and hygiene in food production. The pharmaceutical industry also utilizes robotics extensively for precise drug dispensing, quality control, and sterile packaging. These examples illustrate the broad applicability of robotic automation across diverse sectors.
Types of Robots in Autonomous Factories
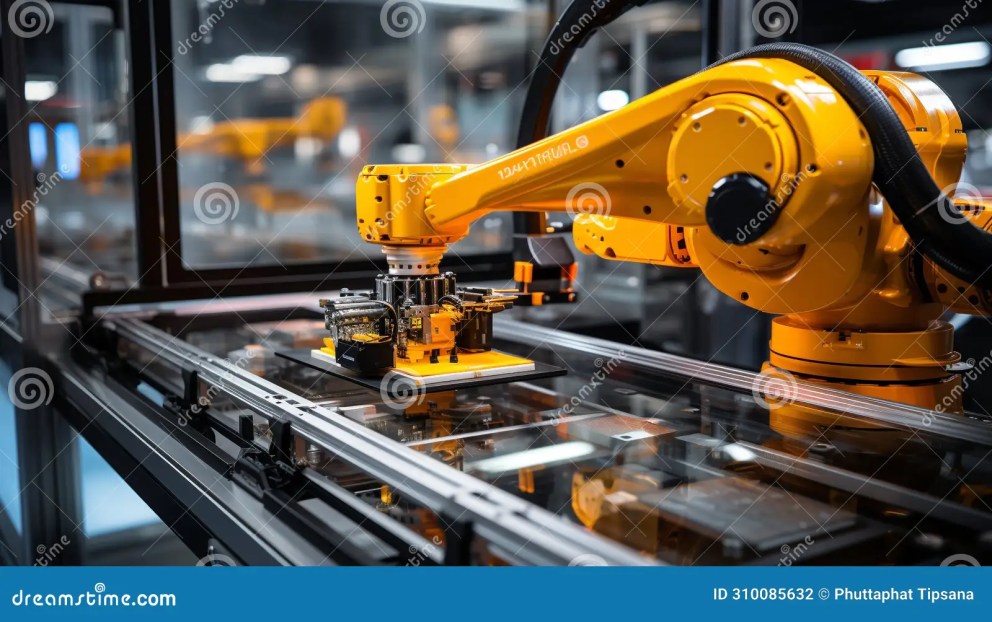
Source: dreamstime.com
The rise of autonomous factories hinges on the diverse array of robots performing specialized tasks. These aren’t your grandpa’s assembly line automatons; today’s robots are sophisticated, adaptable, and crucial to efficient, high-output production. Understanding the different types and their capabilities is key to appreciating the transformative power of robotic automation.
Autonomous factories utilize a range of robots, each designed for specific tasks and environments. Their capabilities and limitations directly impact the efficiency and flexibility of the factory floor. Choosing the right robot for a given application requires careful consideration of factors like payload capacity, precision, workspace size, and safety requirements. Let’s delve into the main categories.
Autonomous factories, driven by robotics, are the future of manufacturing, boosting efficiency and precision. This same drive for seamless, intuitive experiences is mirrored in the retail world, where tech is revolutionizing how we shop; check out how How Augmented Reality is Enhancing Online Shopping Experiences is changing the game. Ultimately, both robotics and AR are about creating more user-friendly, effective systems, whether in a factory or online store.
Industrial Robots
Industrial robots are the workhorses of automated manufacturing. These are typically large, powerful robots designed for high-speed, repetitive tasks in structured environments. They are often found performing welding, painting, material handling, and assembly operations. Their strength lies in their speed, precision, and ability to handle heavy loads. However, their size and lack of adaptability often restrict their use to dedicated, caged-off areas for worker safety. Examples include six-axis articulated robots used in car manufacturing plants for welding car bodies.
Collaborative Robots (Cobots)
Cobots are designed to work alongside human workers, sharing a workspace without the need for safety cages. These robots are smaller, lighter, and often equipped with sensors and safety features to prevent collisions. They are particularly well-suited for tasks requiring human-robot interaction, such as assembly, inspection, and packaging. While their payload capacity is generally lower than industrial robots, their flexibility and ease of programming make them ideal for smaller-scale operations and adaptable manufacturing processes. Think of a cobot assisting a technician with assembling delicate electronic components.
Automated Guided Vehicles (AGVs)
AGVs are mobile robots used for material handling and transportation within a factory. These vehicles can follow pre-programmed routes, navigate using sensors, or utilize advanced navigation systems like SLAM (Simultaneous Localization and Mapping) for dynamic environments. They are used to move raw materials, work-in-progress, and finished goods efficiently throughout the facility, freeing up human workers from these often laborious tasks. AGVs are particularly useful in large warehouses or factories with extensive material flow requirements, improving overall logistics and efficiency. Imagine a fleet of AGVs autonomously transporting parts between different production stations.
A Comparison of Robot Types
To better understand the differences, let’s summarize the key characteristics of each robot type in a table:
Robot Type | Application | Advantages | Disadvantages |
---|---|---|---|
Industrial Robots | Welding, painting, material handling, assembly (high-speed, repetitive tasks) | High speed, high precision, high payload capacity | Requires safety cages, less flexible, complex programming |
Collaborative Robots (Cobots) | Assembly, inspection, packaging (tasks requiring human-robot interaction) | Safe for human collaboration, flexible, easy programming | Lower payload capacity, slower speed compared to industrial robots |
Automated Guided Vehicles (AGVs) | Material handling, transportation of goods within a factory | Improved logistics, increased efficiency, reduced labor costs | Higher initial investment, potential for traffic congestion in busy environments |
Robotics’ Impact on Production Efficiency and Productivity: How Robotics Is Shaping The Future Of Autonomous Factories
The integration of robots into manufacturing processes is revolutionizing production efficiency and productivity, ushering in an era of unprecedented speed, accuracy, and cost-effectiveness. This isn’t just about replacing human workers; it’s about augmenting capabilities and creating a smarter, more responsive manufacturing ecosystem. The benefits are multifaceted, impacting everything from output volume to product quality.
Robotic automation significantly enhances production speed and output by performing tasks far faster and more consistently than human workers. Robots don’t require breaks, don’t get tired, and maintain a consistent pace throughout their operational cycle. This leads to increased throughput and shorter lead times, allowing companies to meet higher demands and deliver products faster to market. Furthermore, robots can operate continuously, maximizing production uptime and minimizing downtime associated with human limitations.
Increased Production Speed and Output
Robots excel at repetitive tasks, executing them with speed and precision that far surpasses human capabilities. Consider a car assembly line: robots can weld, paint, and install parts with unmatched speed and accuracy, significantly increasing the number of cars produced per day. This speed advantage translates directly to higher production volume and quicker fulfillment of orders. The consistency of robotic performance also minimizes errors, leading to fewer production delays caused by human error. The cumulative effect is a substantial boost in overall production output.
Reduced Manufacturing Costs and Improved Product Quality
While the initial investment in robotic systems can be substantial, the long-term cost savings are considerable. Robots reduce labor costs, minimize material waste through precise operations, and decrease the frequency of production errors. This translates to lower overall manufacturing costs per unit. Moreover, the precision and consistency of robots lead to a significant improvement in product quality. Uniformity in manufacturing processes results in fewer defects, less rework, and ultimately, higher customer satisfaction. This improved quality can also translate to a stronger brand reputation and increased market share.
Hypothetical Scenario: Robotic Integration in a Semiconductor Manufacturing Plant, How Robotics is Shaping the Future of Autonomous Factories
Imagine a semiconductor manufacturing plant that previously relied heavily on manual labor for chip packaging. The process was slow, prone to errors, and resulted in significant material waste. By integrating robotic arms equipped with advanced vision systems, the plant automated the chip packaging process. The robots could precisely place chips onto circuit boards, ensuring perfect alignment and minimizing waste. The result? A 30% increase in packaging speed, a 15% reduction in material waste, and a 20% decrease in defects. This translates to significantly higher profits and a stronger competitive edge. The improved precision and consistency also led to a noticeable improvement in the quality of the finished products, enhancing the company’s reputation and boosting customer confidence.
Robotics and the Enhancement of Workplace Safety
The rise of autonomous factories isn’t just about increased efficiency; it’s fundamentally changing workplace safety. By automating dangerous and repetitive tasks, robots are significantly reducing the risk of human injury and creating a safer work environment for everyone. This shift towards robotic automation represents a major leap forward in occupational health and safety, impacting everything from manufacturing plants to logistics centers.
Robots are increasingly taking over hazardous jobs, shielding human workers from potential harm. This isn’t just about reducing the number of accidents; it’s about preventing them altogether. The inherent precision and consistency of robotic systems minimize the chances of human error, a leading cause of workplace incidents.
Hazardous Task Automation
Robots excel at handling tasks that are inherently dangerous for humans. This includes working with heavy machinery, handling toxic chemicals, operating in extreme temperatures, or performing tasks in confined spaces. For example, in the automotive industry, robots are frequently used for welding and painting car bodies, tasks that expose workers to harmful fumes and sparks. Similarly, in the nuclear industry, robots are employed for tasks involving radioactive materials, minimizing human exposure to radiation. The consistent and precise nature of robotic work also reduces the risk of accidental exposure to hazardous materials or equipment malfunctions.
Minimizing Human Error and Workplace Accidents
Human error is a major contributor to workplace accidents. Fatigue, distraction, and lack of training can all lead to mistakes with potentially serious consequences. Robotic systems, however, operate with consistent precision, reducing the likelihood of these errors. Their programmed routines ensure tasks are performed accurately and repeatedly, minimizing the risk of accidents caused by human fallibility. Consider the example of a robotic arm precisely placing components on an assembly line; the consistent accuracy reduces the risk of dropped components or misalignments, which could lead to injuries or equipment damage. This consistent performance, unburdened by human limitations, creates a safer environment.
Safety Features in Industrial Robots
Modern industrial robots are equipped with a range of safety features designed to prevent accidents. These features often include emergency stop buttons, sensors to detect obstacles, and safety light curtains that halt robot operation if a human enters a designated zone. Many robots also incorporate force-limiting technology, which prevents them from applying excessive force if they come into contact with a person. For instance, collaborative robots (cobots) are specifically designed to work safely alongside humans, using sensors and software to ensure they stop or adjust their movements if they encounter an unexpected obstacle or human interaction. These sophisticated safety mechanisms significantly reduce the risk of human injury in the increasingly automated factory environment.
Challenges and Considerations in Implementing Robotic Systems
The transition to autonomous factories, while promising increased efficiency and safety, isn’t without its hurdles. Implementing robotic systems requires careful planning and consideration of significant financial, technical, and ethical factors. Ignoring these challenges can lead to costly delays, operational inefficiencies, and even reputational damage. Let’s delve into the key obstacles and strategies for navigating them successfully.
The shift to automation presents a complex interplay of technological advancements, economic realities, and societal implications. A successful integration requires a holistic approach that addresses not only the technical aspects but also the human element, ensuring a smooth transition for the workforce and the wider community.
High Initial Investment Costs
The upfront costs associated with purchasing, installing, and configuring robotic systems can be substantial. This includes the robots themselves, the necessary infrastructure (such as power supplies, safety systems, and specialized tooling), and the integration with existing factory systems. For smaller businesses or those with limited capital, this can represent a significant barrier to entry. Larger corporations, while better equipped to handle these costs, still need to carefully weigh the return on investment against potential risks. For example, a small manufacturing company might find the cost of a single advanced robotic arm prohibitive compared to its current manual labor costs, while a large automotive manufacturer might justify the expense based on projected increases in production and quality.
Integration Complexities
Integrating robots into existing factory workflows isn’t a simple plug-and-play process. It often requires significant modifications to existing infrastructure, software, and production lines. Ensuring seamless communication and data exchange between robots, other machines, and human workers can be technically challenging and time-consuming. This complexity necessitates specialized expertise in robotics, automation engineering, and IT, leading to higher labor costs during the integration phase. Consider the scenario of a company trying to integrate a new robotic welding system into an older assembly line – this might require reconfiguring the line layout, updating control systems, and retraining workers to operate the new equipment.
Workforce Retraining and Job Displacement
The introduction of robots inevitably raises concerns about job displacement. While robots are often deployed to handle repetitive, dangerous, or physically demanding tasks, the transition can lead to anxiety among workers who fear losing their jobs. Proactive workforce retraining programs are crucial to mitigate this risk. These programs should focus on upskilling workers to manage and maintain robotic systems, as well as developing new skills relevant to the evolving factory environment. For instance, a factory might offer training programs for its employees to become robotics technicians or programmers, ensuring that they remain valuable assets in the automated workplace. Furthermore, the implementation of robots may also create new job roles in areas such as robotics maintenance, programming, and system integration.
Ethical Considerations
The increasing reliance on robots in manufacturing raises important ethical considerations. Concerns around data privacy, algorithmic bias, and the potential for increased inequality need careful attention. Transparent and responsible implementation of robotic systems is essential to build trust and ensure equitable outcomes for all stakeholders. For example, the use of AI-powered robots in decision-making processes requires careful consideration of potential biases in the algorithms, to avoid unfair or discriminatory outcomes. Similarly, robust data security measures are essential to protect sensitive information related to production processes and employee data.
Strategies for Overcoming Challenges
Successfully integrating robotic systems requires a multi-pronged approach. A well-defined strategy is essential to mitigate the risks and maximize the benefits of automation.
- Phased Implementation: Instead of a complete overhaul, adopt a phased approach, starting with smaller, less complex projects to gain experience and refine processes before scaling up.
- Invest in Training and Retraining: Proactively invest in training programs to upskill the workforce and prepare them for the changing demands of an automated factory.
- Collaborate with Technology Providers: Partner with reputable robotics vendors and integration specialists to leverage their expertise and minimize implementation risks.
- Develop a Robust Risk Management Plan: Identify and assess potential risks associated with robotic integration and develop mitigation strategies to address them.
- Prioritize Ethical Considerations: Establish clear ethical guidelines for the development and deployment of robotic systems, ensuring fairness, transparency, and accountability.
The Future of Robotics in Autonomous Factories
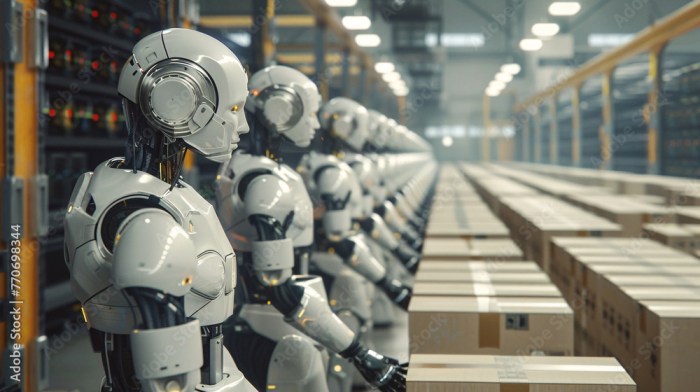
Source: ftcdn.net
The relentless march of technology promises a future where autonomous factories are not a futuristic fantasy, but a commonplace reality. The next decade will witness a dramatic acceleration in robotic capabilities, driven by advancements in artificial intelligence and machine learning, leading to unprecedented levels of automation and efficiency in manufacturing. This evolution will redefine the relationship between humans and machines in the production environment, fostering a collaborative ecosystem where both contribute to optimal output.
The convergence of several technological advancements will shape the future of robotics in autonomous factories. This includes advancements in sensor technology, allowing robots to perceive their environment with greater precision and nuance; improvements in AI-powered path planning and obstacle avoidance, enabling robots to navigate complex and dynamic factory floors with increased agility; and the development of more sophisticated robotic manipulators capable of handling delicate or intricate tasks previously beyond the reach of automation.
The Expanding Role of AI and Machine Learning
AI and ML are poised to revolutionize robotic capabilities within autonomous factories. AI will empower robots with cognitive functions, enabling them to learn from experience, adapt to changing conditions, and make independent decisions. This includes predictive maintenance, where AI algorithms analyze sensor data from robots and machinery to anticipate potential failures and schedule preventative maintenance, minimizing downtime and maximizing productivity. Machine learning will further enhance robotic dexterity and precision, allowing for more complex tasks, such as assembly of intricate components or quality control inspections, to be automated efficiently. For instance, a factory producing smartphones could utilize ML-trained robots to perform micro-soldering, a task previously requiring highly skilled human labor.
A Vision of the Fully Autonomous Factory
Imagine a factory in 2040: Robots, guided by sophisticated AI systems, seamlessly orchestrate every aspect of the production process. From raw material handling and processing to assembly, quality control, and packaging, robots work collaboratively, optimizing resource allocation and minimizing waste. Human workers, rather than performing repetitive tasks, focus on higher-level functions like system monitoring, programming, and strategic decision-making. Data analytics, powered by AI, provides real-time insights into production efficiency, allowing for immediate adjustments and improvements. This integrated system, driven by robotic automation and AI-powered intelligence, represents a significant leap forward in manufacturing productivity and efficiency. Companies like Tesla are already paving the way, incorporating advanced robotics and AI into their manufacturing processes, demonstrating the feasibility of this vision. Their advancements in automated assembly lines and quality control systems serve as a tangible example of the future of autonomous factories.
Predictive Maintenance and Optimization
Predictive maintenance, enabled by AI and machine learning, will become integral to the functioning of autonomous factories. By analyzing sensor data from robots and machinery, AI algorithms can identify patterns indicating potential failures before they occur. This allows for proactive maintenance, minimizing downtime and maximizing the lifespan of equipment. Furthermore, AI-powered optimization algorithms will continuously analyze production data to identify bottlenecks and inefficiencies, automatically adjusting parameters to optimize throughput and resource utilization. This level of automation and optimization would lead to significant cost savings and increased production efficiency. Imagine a scenario where a robotic arm detects an anomaly in its own operation, predicting a potential failure within 24 hours. The AI system then automatically schedules maintenance, preventing costly downtime and ensuring uninterrupted production.
Illustrative Example: A Robotic Assembly Line
Imagine a streamlined, futuristic assembly line, humming with controlled efficiency. This isn’t your grandfather’s factory floor; this is the epitome of autonomous manufacturing, where robots work in perfect harmony to assemble a complex product, let’s say, a smartphone. The process is a seamless ballet of precision and speed, orchestrated by sophisticated software and advanced sensory systems.
This particular assembly line utilizes a variety of robotic arms, each specialized for a specific task. Heavy-duty articulated robots, with their multiple joints and high payload capacity, handle the larger components like the chassis and battery. Smaller, more dexterous robots, perhaps collaborative robots (cobots), work alongside human technicians on delicate tasks such as installing the micro-circuitry and connecting tiny wires. Finally, mobile robots, resembling automated guided vehicles (AGVs), transport components between different stations along the line, ensuring a continuous flow of materials.
Robotic Task Coordination and Seamless Assembly
The robots don’t operate in isolation. A central control system, often powered by advanced AI algorithms, orchestrates their actions. This system uses a digital twin of the assembly line, a virtual representation mirroring the real-world setup, to predict and manage the workflow. The system receives real-time data from sensors located throughout the line, tracking the position and status of each robot and component. Based on this data, the control system dynamically adjusts the sequence of operations to optimize efficiency and minimize downtime. For instance, if one robot experiences a minor delay, the system might temporarily reroute components to other stations to prevent bottlenecks. The result is a highly adaptable system that can adjust to changing demands and unforeseen circumstances.
Sensory and Control Systems for Precise Movements
Precision is paramount in robotic assembly. Each robot is equipped with a suite of sensors that allow it to perceive its environment and interact with components accurately. These sensors include vision systems (cameras), force sensors (detecting contact pressure), and proximity sensors (detecting the presence of objects). Vision systems, for example, guide robots in precisely picking up and placing components, even identifying and correcting for minor variations in their position or orientation. Force sensors ensure that components are handled gently, preventing damage. The control system processes the sensory data in real-time, providing feedback to the robot controllers to fine-tune their movements and maintain accuracy.
Visual Representation of the Assembly Line
Imagine a long, modular assembly line, brightly lit and remarkably clean. At one end, AGVs bring in raw materials and components, neatly organizing them into designated staging areas. Heavy-duty articulated robots at various stations pick up the chassis, carefully placing them onto conveyors. Smaller, more agile robots, some working in collaboration with human operators, meticulously install the motherboard, processor, and other internal components. Along the line, quality control robots conduct inspections, ensuring that each smartphone meets the required specifications. Finally, at the end of the line, finished smartphones are packaged and ready for shipment. The entire process is orchestrated by a central control room, where technicians monitor the performance of the system, providing support and addressing any issues that might arise. This visualization emphasizes the coordinated movements and seamless flow of materials and components throughout the process.
Wrap-Up
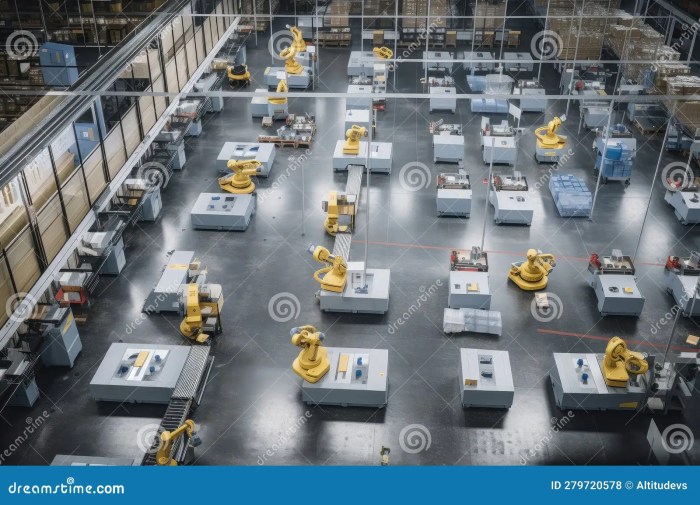
Source: dreamstime.com
The future of autonomous factories is undeniably robotic. The integration of AI and machine learning promises even more sophisticated and adaptable robotic systems, leading to hyper-efficient, safer, and more responsive production processes. While challenges remain – like initial investment costs and workforce retraining – the potential benefits are too significant to ignore. The factory floor of tomorrow isn’t just automated; it’s intelligent, collaborative, and ready to meet the demands of a rapidly changing world. The rise of the robots is here, and it’s changing everything.