How Robotics is Revolutionizing the Future of Consumer Goods Production? Forget clunky assembly lines – robots are rewriting the rules of manufacturing. From lightning-fast precision to hyper-personalized products, the impact is massive, touching everything from the factory floor to your shopping cart. Get ready for a deep dive into a future where robots aren’t just machines, but partners in creating the goods we all consume.
This isn’t just about automation; it’s about a complete transformation. We’ll explore how robots are boosting efficiency, creating safer workplaces, and even allowing for customized products on a mass scale. We’ll also tackle the challenges – the job displacement worries, the economic shifts – and how we can navigate this robotic revolution responsibly. Buckle up, because this is one ride you won’t want to miss.
Increased Efficiency and Productivity in Manufacturing

Source: shopnoecommerce.com
Robots are streamlining consumer goods production, boosting efficiency and slashing costs. This same automation revolution is impacting other sectors too, like healthcare, where advancements are seriously impressive – check out this article on How Robotics and Automation Are Transforming Healthcare for a glimpse into the future. Ultimately, the impact of robotics promises a more efficient and innovative future for both consumer goods and beyond.
Robotic automation is rapidly transforming consumer goods production, ushering in an era of unprecedented efficiency and productivity gains. This revolution is driven by robots’ ability to perform tasks faster, more precisely, and with greater consistency than human workers, leading to significant improvements across the entire manufacturing process.
The integration of robotic systems dramatically accelerates production speed. Robots can operate continuously, without breaks or fatigue, significantly increasing output compared to human-operated assembly lines. Their precision is also unmatched; robots can perform intricate tasks with microscopic accuracy, minimizing waste and improving product quality. This precision is particularly crucial in industries like electronics manufacturing, where even minor errors can have significant consequences.
Reduced Human Error and Improved Product Quality
Human error is an inevitable part of manual labor. Fatigue, distraction, and individual skill variations can all lead to inconsistencies in product quality and even safety hazards. Robotic systems, however, eliminate these variables. Their programmed actions are consistent and repeatable, resulting in a higher degree of accuracy and a significant reduction in defects. This translates directly into improved product quality, enhanced brand reputation, and reduced costs associated with rework or product recalls. For example, in the pharmaceutical industry, robotic precision in pill dispensing ensures accurate dosage and eliminates the risk of human error, a critical factor for patient safety.
Cost-Effectiveness of Robotic Systems
While the initial investment in robotic systems can be substantial, the long-term cost-effectiveness is often demonstrably superior to traditional manufacturing methods. While upfront costs are higher, the return on investment (ROI) is typically realized through increased productivity, reduced labor costs, and minimized waste. The following table summarizes key factors:
Cost | Speed | Quality | Human Labor |
---|---|---|---|
Higher initial investment, lower long-term operational costs | Significantly faster production cycles | Higher consistency and accuracy, reduced defects | Reduced need for manual labor, potential for retraining existing workforce |
Increased Productivity in a Hypothetical Scenario
Imagine a smartphone assembly factory currently employing 100 workers on an assembly line, producing 500 phones per day. Introducing a robotic system for specific tasks, such as screen installation and circuit board placement, could potentially automate 60% of the assembly process. This would result in a significant increase in production capacity. With robots handling the most precise and time-consuming tasks, the remaining human workforce could focus on quality control and more complex assembly steps. The factory could potentially increase its daily output to 800 phones, a 60% increase in productivity, with fewer human workers and significantly reduced error rates. This scenario highlights how targeted robotic automation can dramatically boost efficiency without necessarily displacing all human workers. Instead, it reshapes the workforce, requiring retraining and upskilling for higher-value roles.
Enhanced Flexibility and Customization
The rise of robotics isn’t just about faster production; it’s about a fundamental shift in how we manufacture consumer goods. We’re moving beyond mass production towards mass customization, a world where products are tailored to individual preferences, all while maintaining efficiency. This flexibility is driven by the adaptability and precision of robotic systems, allowing manufacturers to respond quickly to changing market demands and consumer tastes.
Robotic systems are at the forefront of this revolution, enabling manufacturers to produce a wider variety of products with shorter lead times and reduced waste. Their ability to quickly reconfigure themselves for different tasks allows for agile production lines that can adapt to fluctuating consumer preferences and seasonal trends. This agility is crucial in today’s dynamic marketplace where consumer expectations are constantly evolving.
Mass Customization Enabled by Robotics
Robotics plays a pivotal role in making mass customization a reality. Traditional assembly lines, designed for high-volume production of a single product, struggle to handle the diversity required for customized goods. Robotic systems, however, can be programmed to perform a wide range of tasks with high precision, making them ideal for producing personalized items at scale. This involves sophisticated programming and often incorporates advanced technologies like AI and machine learning to optimize the production process for each specific customization. Imagine a robotic arm delicately placing a personalized monogram on a leather handbag, or another precisely adjusting the settings on a custom-built bicycle – this level of precision and adaptability is what sets robotic systems apart.
Adaptability to Changing Production Demands and Consumer Preferences, How Robotics is Revolutionizing the Future of Consumer Goods Production
Robotic systems excel at adapting to changes in production demands. Unlike fixed assembly lines, which are costly and time-consuming to reconfigure, robotic systems can be reprogrammed and redeployed relatively quickly. This means manufacturers can respond rapidly to changes in consumer preferences, seasonal demands, or even unexpected events like supply chain disruptions. This adaptability is achieved through modular designs and sophisticated software that allows for easy reprogramming and retooling. For example, a factory producing smartphones might use robotics to easily switch between assembling different phone models or even incorporate new features based on consumer feedback, all with minimal downtime. This dynamic flexibility ensures that manufacturers can stay ahead of the curve and meet the ever-changing needs of the market.
Examples of Consumer Goods Industries Benefiting from Robotic Flexibility
The increased flexibility offered by robotics is particularly beneficial across several consumer goods industries:
- Apparel and Footwear: Robots can handle the intricate tasks involved in customizing clothing and shoes, from embroidery and stitching to precise cutting and assembly. This allows for personalized designs and sizes to be produced efficiently.
- Electronics: The electronics industry, with its vast array of models and configurations, benefits significantly from robotic flexibility. Robots can easily adapt to assembling various components and configurations for smartphones, laptops, and other devices.
- Automotive: While automation has been present in the automotive industry for some time, robotics enhances flexibility by enabling faster changeovers between different vehicle models and customization options, such as interior trims and special features.
- Food and Beverage: Robotics are increasingly used for customized food packaging and personalized food preparation, enabling efficient production of customized orders, such as personalized meal kits or customized snacks.
Adaptability Comparison: Robotic Systems vs. Traditional Assembly Lines
Feature | Robotic Systems | Traditional Assembly Lines |
---|---|---|
Product Variation Handling | High; easily reprogrammed for diverse products | Low; significant retooling required for new products |
Production Speed Adjustment | Quick; easily adjusted based on demand | Slow; requires manual adjustments and often downtime |
Customization Capabilities | High; enables mass customization | Limited; mostly mass production |
Cost of Changeover | Relatively low; primarily software reprogramming | High; involves significant physical retooling and downtime |
Improved Safety and Working Conditions
The integration of robotics into consumer goods manufacturing isn’t just about boosting efficiency; it’s fundamentally reshaping workplace safety. Robots are increasingly taking over dangerous, repetitive, or physically demanding tasks, leading to a significant reduction in workplace accidents and a marked improvement in the overall well-being of human workers. This shift towards automation represents a crucial step towards creating safer and more humane manufacturing environments.
Robots are effectively mitigating numerous workplace hazards prevalent in consumer goods production. They can handle heavy lifting, reducing the risk of back injuries and musculoskeletal disorders. They can perform tasks in hazardous environments, such as working with chemicals or operating machinery in confined spaces, thus protecting human workers from exposure to harmful substances and potential accidents. Furthermore, robotic precision minimizes the chances of human error leading to injuries.
Robotic Automation for Enhanced Worker Safety
Robotic automation is particularly beneficial in tasks involving high-risk elements. For instance, in the automotive industry, robots are extensively used for welding, painting, and assembly line operations, shielding workers from burns, toxic fumes, and repetitive strain injuries. In the food and beverage sector, robots handle tasks such as packaging and palletizing, minimizing the risk of repetitive strain injuries and workplace accidents associated with heavy lifting. Similarly, in electronics manufacturing, robots perform delicate assembly tasks, reducing the risk of eye strain and repetitive motion injuries. The consistent precision of robots ensures a safer working environment compared to manual labor, significantly reducing the possibility of human error-induced accidents.
Impact of Robotics on Workplace Injuries and Employee Well-being
The implementation of robotics has demonstrably reduced workplace injuries in various industries. Studies have shown a significant decrease in the incidence of musculoskeletal disorders, lacerations, and burns in factories that have incorporated robotic systems. This reduction in workplace injuries translates directly to improved employee well-being. Workers feel safer and more secure in their jobs, leading to increased job satisfaction, reduced stress levels, and a better overall work-life balance. The decreased risk of injury also translates into lower healthcare costs for both employees and companies. For example, a study by the National Institute for Occupational Safety and Health (NIOSH) showed a 40% reduction in workplace injuries in a manufacturing plant after the implementation of robotic systems. While this is a specific example, the general trend towards injury reduction through automation is widely observed across various industries.
Safety Features in Modern Industrial Robots
Modern industrial robots incorporate several safety features to ensure a safe working environment. These features are crucial in minimizing the risk of accidents and maximizing worker protection.
- Emergency Stop Buttons: Strategically placed emergency stop buttons allow workers to immediately halt robot operation in case of an emergency.
- Light Curtains and Safety Scanners: These sensors detect the presence of humans within the robot’s operational area, triggering an automatic stop to prevent collisions.
- Speed and Force Limiting: Robots are programmed with speed and force limits to minimize the impact of potential collisions.
- Interlocking Safety Guards: These physical barriers prevent access to hazardous areas while the robot is operating.
- Redundant Safety Systems: Multiple safety systems are often implemented to ensure that even if one system fails, others will still provide protection.
The Rise of Collaborative Robots (Cobots): How Robotics Is Revolutionizing The Future Of Consumer Goods Production
The integration of robots into consumer goods production has dramatically shifted, moving beyond the traditional image of isolated, caged industrial behemoths. The rise of collaborative robots, or cobots, signifies a new era of human-robot interaction, fostering a synergistic relationship on the factory floor that boosts efficiency and enhances worker well-being. Cobots are designed to work alongside humans, sharing tasks and responsibilities in a safe and productive manner, unlike their industrial robot counterparts.
Cobots are revolutionizing how we think about automation in manufacturing. Unlike traditional industrial robots, which are typically large, fast, and operate in isolated environments for safety reasons, cobots are smaller, slower, and designed with safety features that allow them to operate directly alongside human workers. This collaborative approach fosters a more efficient and flexible production process, allowing for greater customization and responsiveness to market demands. The key difference lies in their intended purpose: industrial robots excel at high-speed, repetitive tasks, while cobots are best suited for tasks requiring human-like dexterity, adaptability, and problem-solving skills.
Cobot Advantages in Human-Robot Interaction
Cobots offer several key advantages in human-robot collaboration. Their inherent safety features, such as force limiting sensors and collaborative speed controls, minimize the risk of injury to human workers. This allows for a more fluid and integrated workflow, where humans and robots seamlessly share tasks based on their respective strengths. The increased flexibility provided by cobots also enables faster adaptation to changing production needs and facilitates greater product customization. This flexibility translates to quicker response times to market trends and consumer demands, providing a significant competitive edge. Furthermore, cobots can handle repetitive or ergonomically challenging tasks, freeing up human workers to focus on more complex and value-added activities. This leads to increased job satisfaction and reduced worker fatigue, contributing to a safer and more productive work environment.
Comparison of Traditional Industrial Robots and Cobots
Traditional industrial robots are typically large, powerful, and designed for high-speed, repetitive tasks. They operate in caged environments to ensure worker safety. Their programming is often complex and requires specialized expertise. Applications include welding, painting, and material handling in high-volume manufacturing settings. Conversely, cobots are smaller, lighter, and designed for collaborative work with humans. They incorporate safety features that allow them to operate alongside workers without the need for safety cages. Their programming is often simpler and more intuitive, requiring less specialized training. Applications include assembly, packaging, and quality inspection, where human-like dexterity and adaptability are required.
Examples of Cobots Enhancing Human Worker Capabilities
The following table illustrates how cobots enhance human worker capabilities and improve teamwork in various consumer goods production scenarios:
Task Type | Robot Model | Benefits | Specific Example |
---|---|---|---|
Assembly | Universal Robots UR5 | Increased speed and precision, reduced worker strain | Assisting in the assembly of small electronic components in a smartphone factory. |
Packaging | Fanuc CRX-10iA | Improved efficiency, reduced risk of repetitive strain injuries | Packing delicate consumer goods like cosmetics or glassware. |
Quality Inspection | ABB YuMi | Enhanced accuracy, consistency, and speed of inspection | Checking for defects in clothing or footwear production. |
Material Handling | Kuka LBR iiwa | Reduced worker fatigue, improved safety | Moving heavy or bulky materials in a furniture factory. |
Collaborative Workflow in Consumer Goods Production
Consider a scenario in a cosmetics factory where a new lipstick line is being produced. Humans are responsible for the complex task of filling the lipstick tubes with precise amounts of product and attaching the caps. A cobot, like the Universal Robots UR10, is programmed to feed the empty tubes to the human workers at a consistent pace, ensuring a smooth workflow. The human workers then fill and cap the tubes, while the cobot removes the finished lipsticks and places them on a conveyor belt for packaging. This collaboration leverages the human’s dexterity and judgment for the filling and capping process while utilizing the cobot’s precision and consistent pace for material handling. This setup minimizes human fatigue from repetitive actions, enhances overall production speed, and ensures consistent product quality.
Impact on Supply Chains and Global Manufacturing
Robotics is fundamentally reshaping global supply chains for consumer goods, impacting everything from production efficiency to geographical distribution. The increased speed, precision, and flexibility offered by robotic systems are leading to significant changes in how companies source materials, manufacture products, and deliver them to consumers. This transformation is not just about increased efficiency; it’s about building more resilient and adaptable supply chains capable of weathering global disruptions.
The integration of robotics into manufacturing processes directly enhances the efficiency and resilience of global supply chains. Faster production cycles mean quicker response times to changing consumer demands. Automated quality control reduces waste and rework, minimizing delays. Furthermore, robots can operate continuously, increasing overall output and reducing reliance on human labor in potentially unreliable or geographically challenging locations. This increased efficiency translates to shorter lead times, reduced inventory costs, and a more agile response to market fluctuations. For example, companies using robotic automation in their factories have reported significant reductions in production time and a considerable increase in output, allowing them to better meet fluctuating orders and seasonal demands.
Nearshoring and Reshoring Enabled by Robotics
Robotics plays a crucial role in making near-shoring and reshoring of manufacturing operations economically viable. The higher labor costs associated with developed nations have traditionally driven manufacturing to lower-cost regions. However, the increasing sophistication and affordability of robots are mitigating this cost differential. Automation reduces the reliance on low-cost labor, making it more attractive to bring manufacturing closer to consumer markets. This reduces transportation costs, lead times, and carbon emissions, while also improving responsiveness to customer needs and facilitating better quality control. A prime example is the automotive industry, where several manufacturers are investing heavily in robotic automation to bring production closer to their key markets in North America and Europe.
Impact of Automation on Geographical Distribution
The automation of manufacturing processes is altering the geographical distribution of consumer goods production. While low-cost labor remains a factor, the strategic advantages of automation – such as reduced transportation costs, quicker response times, and improved supply chain resilience – are prompting a shift. Companies are considering factors beyond just labor costs, including proximity to markets, access to skilled labor for robot maintenance and programming, and overall supply chain infrastructure. This leads to a more decentralized and regionalized manufacturing landscape, with production facilities potentially located closer to consumers in developed nations. The result is a more dynamic and geographically diverse manufacturing ecosystem.
Visual Representation of Changing Global Supply Chains
Imagine a world map. Before the widespread adoption of robotics, the map would show a concentration of manufacturing hubs in specific regions known for low labor costs, typically in Asia. Thick lines would represent long, complex supply chains stretching across continents, highlighting the reliance on global shipping and potentially lengthy lead times. Now, imagine a revised map. While some manufacturing remains in low-cost regions, the map shows a more distributed pattern of production facilities. The lines representing supply chains are shorter and more localized, connecting factories to regional distribution centers and ultimately, to consumers. These shorter, more resilient supply chains are facilitated by the increased automation and flexibility offered by robotics. The visual contrast highlights the shift from a highly centralized, globally extended model to a more decentralized, regionally focused approach, made possible by robotic automation.
Challenges and Considerations in Robotic Adoption
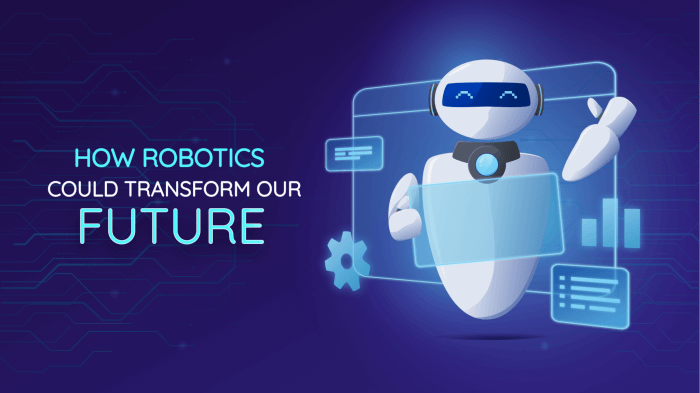
Source: mobcoder.com
Integrating robotics into consumer goods production isn’t a simple plug-and-play operation. Businesses face a complex web of challenges, ranging from hefty upfront investments to the potential disruption of existing workflows and the need for significant workforce adaptation. Successfully navigating these hurdles is crucial for reaping the rewards of robotic automation.
The economic and social implications of widespread robotic automation are profound and multifaceted. While increased efficiency and productivity lead to cost savings and potentially lower prices for consumers, there’s also the very real concern of job displacement in certain sectors. This necessitates a proactive approach to mitigating negative social consequences and ensuring a smooth transition for the workforce.
High Initial Investment Costs
Implementing robotic systems requires significant upfront capital expenditure. Robots themselves are expensive, and the cost extends to integration, programming, maintenance, and the necessary infrastructure upgrades. Smaller businesses, in particular, may struggle to justify such investments, potentially hindering their ability to compete with larger corporations that can absorb these costs more easily. This creates an uneven playing field and underscores the need for government incentives or financing options to support smaller businesses in their adoption of robotic technologies. For example, a small clothing manufacturer might find the cost of a robotic sewing machine prohibitive compared to the ongoing labor costs, even if the long-term ROI is significantly better.
Integration Challenges and Complexity
Integrating robots into existing production lines can be complex and disruptive. This involves not only the physical installation of the robots but also the need to reconfigure workflows, train personnel, and potentially modify existing equipment. Furthermore, ensuring seamless communication and data exchange between robots and other systems within the factory requires careful planning and specialized expertise. A poorly integrated system can lead to inefficiencies, downtime, and even safety hazards. Imagine trying to integrate a highly automated robotic arm into a legacy production line that was designed for manual processes—the challenges in synchronization and data flow would be substantial.
Workforce Retraining and Upskilling
The introduction of robots inevitably leads to shifts in job roles and responsibilities. While some jobs may be eliminated, new opportunities will emerge in areas such as robot maintenance, programming, and system integration. Addressing this requires a proactive approach to workforce retraining and upskilling. This involves providing existing employees with the necessary skills to transition into these new roles, potentially through partnerships with educational institutions or vocational training programs. For instance, a factory worker specializing in manual assembly might be retrained to become a robot technician, requiring specialized courses on robotics and maintenance.
Strategies for Overcoming Robotic Implementation Challenges
The successful implementation of robotics requires a well-defined strategy. Here are some key steps:
- Conduct a thorough needs assessment: Identify specific areas where robots can provide the greatest benefits and address existing limitations.
- Develop a phased implementation plan: Start with smaller-scale projects to test and refine the process before large-scale deployment.
- Invest in robust training and support: Provide employees with the necessary training and technical support to operate and maintain robotic systems.
- Establish strong partnerships with robotics vendors: Leverage their expertise in integration, maintenance, and ongoing support.
- Explore government incentives and funding opportunities: Take advantage of financial support to offset the high initial investment costs.
Final Review
The rise of robotics in consumer goods production isn’t just a technological advancement; it’s a societal shift. While challenges exist, the potential benefits – increased efficiency, safer workplaces, and greater product customization – are undeniable. The future of manufacturing is collaborative, precise, and undeniably robotic. Embracing this change, with thoughtful planning and adaptation, will pave the way for a more innovative and efficient future for all.