How Robotics is Revolutionizing the Construction Industry? Forget slow, expensive, and dangerous construction – robots are changing the game. From bricklaying bots to AI-powered project management, the construction site is getting a serious tech upgrade. This isn’t just about speed; it’s about precision, safety, and solving the industry’s biggest headaches: labor shortages and skyrocketing costs. Get ready to see how automation is building a better future, one brick (or beam) at a time.
This revolution isn’t just about replacing human workers; it’s about augmenting their skills and creating safer, more efficient work environments. We’ll explore how robots handle hazardous tasks, improve accuracy in complex projects, and even help train the next generation of construction professionals. The impact is huge, affecting everything from high-rise buildings to sprawling infrastructure projects, and the changes are only just beginning.
Increased Efficiency and Productivity in Construction
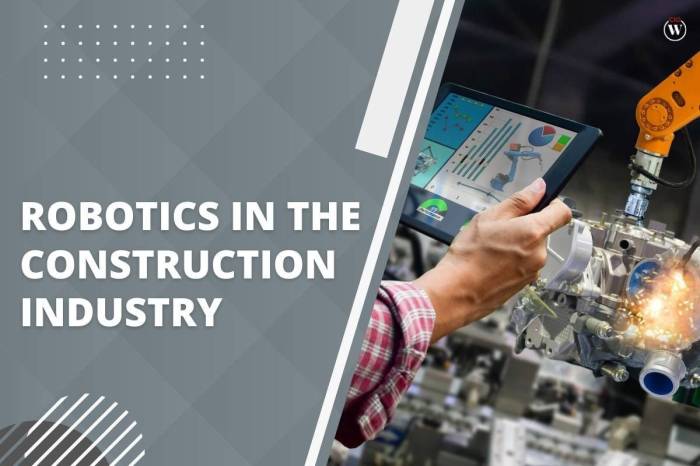
Source: medium.com
Robotic automation is dramatically reshaping the construction industry, injecting a much-needed dose of efficiency and productivity into a sector traditionally known for its slow pace and high variability. By automating repetitive and dangerous tasks, robotics allows construction companies to complete projects faster, reduce costs, and significantly improve worker safety. This shift promises to revolutionize not just how buildings are built, but also the overall profitability and sustainability of the industry.
Improved Construction Timelines Through Robotic Automation
Robotic systems are significantly accelerating construction timelines. Repetitive tasks like bricklaying, welding, and demolition, which once consumed considerable time and manpower, are now handled by robots with remarkable speed and precision. For instance, a bricklaying robot can lay bricks at a rate far exceeding that of a human worker, consistently maintaining high quality and reducing the time spent on this labor-intensive process. This increased speed translates directly to faster project completion, allowing construction companies to meet deadlines more effectively and potentially undertake more projects within a given timeframe. Furthermore, the precise nature of robotic work minimizes errors, reducing the need for rework and further shortening project duration.
The Impact of Robotics on Construction Labor Costs
While the initial investment in robotic systems can be substantial, the long-term impact on labor costs is generally positive. By automating tasks previously performed by human workers, companies can reduce their reliance on expensive labor, especially in areas where skilled labor is scarce or costly. This reduction in labor costs doesn’t necessarily translate to job losses, but rather a shift towards more skilled roles focused on programming, operating, and maintaining the robotic systems. The overall cost savings, resulting from faster project completion and reduced labor needs, can significantly improve project profitability. The exact cost savings vary depending on the project scale and type of robotic systems employed, but numerous case studies demonstrate significant returns on investment.
Robotic Systems Enhancing Worker Safety on Construction Sites
Construction sites are inherently dangerous environments, with risks ranging from falls and electrocution to heavy machinery accidents. Robotics plays a vital role in mitigating these risks. Robots can perform hazardous tasks, such as demolition in unstable structures or working at heights, minimizing the exposure of human workers to danger. Furthermore, robotic systems equipped with sensors and advanced safety features can help prevent accidents. For example, robots used for material handling can avoid collisions with workers or obstacles, reducing the likelihood of injuries. The increased safety provided by robots not only saves lives and reduces healthcare costs but also enhances worker morale and productivity by creating a safer working environment.
Comparison of Traditional and Robotic-Assisted Construction Methods
Method | Speed | Cost-Effectiveness | Safety |
---|---|---|---|
Traditional Construction | Slower, susceptible to delays | Higher labor costs, potential for rework | Higher risk of accidents and injuries |
Robotic-Assisted Construction | Faster, more consistent pace | Lower labor costs, reduced rework | Improved worker safety, reduced accident risk |
Enhanced Precision and Accuracy in Construction Tasks
Forget wonky walls and misaligned beams – robots are bringing a new level of precision to the construction game. Human error, a constant headache in construction, is significantly reduced thanks to the unwavering accuracy of robotic systems. This means safer, more structurally sound buildings, and ultimately, happier clients.
Robots minimize human error in tasks like bricklaying and welding through consistent, programmed movements. Unlike humans, who can tire, get distracted, or make mistakes due to varying skill levels, robots perform repetitive tasks with unwavering accuracy. This precision translates directly into reduced material waste, faster completion times, and a final product that meets exacting specifications.
Robotic Systems Ensuring Precise Measurements and Structural Integrity
Robotics plays a crucial role in ensuring precise measurements and structural integrity throughout the construction process. From initial site surveying using drones equipped with laser scanners to the precise placement of structural components, robots minimize discrepancies and ensure everything aligns perfectly. This is particularly important in complex projects requiring intricate designs and high tolerances. For instance, robotic arms can precisely position reinforcing steel within concrete structures, ensuring optimal strength and minimizing the risk of structural failure. Laser-guided systems can check for deviations from the blueprint in real-time, allowing for immediate corrections and preventing costly rework.
Robots are changing the construction game, boosting efficiency and safety on building sites. This transformation is further accelerated by the lightning-fast data speeds offered by The Rise of 5G and Its Impact on Global Connectivity , enabling real-time control and seamless communication between robotic systems and human operators. The result? Faster builds, reduced costs, and a safer future for construction workers.
Examples of Robotic Systems for High-Precision Construction Tasks
Several robotic systems are revolutionizing precision in construction. Bricklaying robots, for example, can lay bricks faster and more accurately than human bricklayers, resulting in perfectly straight walls and consistent mortar application. Welding robots ensure consistent weld quality, reducing defects and enhancing structural integrity. Automated concrete pouring systems ensure uniform concrete placement, minimizing voids and ensuring consistent strength throughout the structure. Furthermore, 3D printing technology is creating complex architectural features with unparalleled precision, allowing for designs previously deemed impossible.
Accuracy Improvements Achieved Through Robotic Implementation
Construction Task | Accuracy Improvement (Percentage) | Before Robotic Implementation | After Robotic Implementation |
---|---|---|---|
Bricklaying | 15-20% | +/- 5mm | +/- 1mm |
Welding | 10-15% | Variable weld penetration and consistency | Consistent weld penetration and minimal defects |
Concrete Pouring | 5-10% | Potential for voids and inconsistencies | Uniform concrete placement and minimal voids |
Steel Beam Placement | 20-25% | +/- 10mm | +/- 2mm |
Addressing Labor Shortages and Skill Gaps
The construction industry is facing a significant challenge: a dwindling workforce coupled with a shortage of skilled tradespeople. This labor gap threatens to stall crucial infrastructure projects and housing developments, impacting economic growth and societal progress. Robotics offers a powerful solution, not only by directly performing tasks but also by reshaping the training landscape and making construction work more attractive to a new generation.
Robotic systems are emerging as a key player in bridging the labor gap, offering a practical way to increase productivity and overcome the limitations imposed by a shrinking workforce. Their implementation not only fills immediate labor needs but also contributes to a more efficient and safer working environment, ultimately boosting the industry’s appeal to potential recruits.
Types of Robotic Systems Addressing Labor Shortages, How Robotics is Revolutionizing the Construction Industry
Several types of robotic systems are particularly well-suited to addressing specific labor shortages in construction. Autonomous excavators, for instance, can handle earthmoving tasks with greater speed and precision than human operators, reducing reliance on skilled excavator drivers who are in short supply. Bricklaying robots, capable of laying bricks with remarkable speed and accuracy, alleviate the shortage of experienced masons. Similarly, robotic welding systems automate a crucial aspect of structural construction, compensating for a lack of qualified welders. Drone-based surveying and inspection systems minimize the need for manual site surveys, which are often time-consuming and require specialized expertise. These examples illustrate the versatility of robotics in addressing a wide range of labor shortages across different construction disciplines.
Robotic Systems in Construction Worker Training and Upskilling
Robotics is not just about replacing human workers; it’s also about enhancing their capabilities. Robotic systems can serve as valuable training tools, providing simulated environments for workers to practice complex tasks before tackling them on real-world projects. This approach reduces on-site errors and promotes a safer learning curve. Furthermore, robotic assistants can guide workers through intricate processes, offering real-time feedback and improving their skill sets. For example, a robotic arm could assist a welder by precisely positioning materials, allowing the welder to focus on the welding technique and improve their proficiency. This upskilling initiative enhances the workforce’s overall productivity and makes the industry more competitive.
Benefits of Robotic Implementation in Addressing Labor Shortages
The integration of robotic systems in construction offers numerous advantages in addressing labor shortages and skill gaps:
- Increased productivity: Robots can work around the clock, significantly boosting output compared to human workers.
- Improved safety: Robots handle dangerous and repetitive tasks, reducing workplace accidents and injuries.
- Enhanced precision and accuracy: Robotic systems minimize errors, leading to higher-quality construction.
- Attracting younger workers: The use of advanced technology can make construction more appealing to a tech-savvy generation.
- Reduced labor costs: While initial investment is high, long-term labor costs can be significantly reduced.
- Addressing skill gaps: Robots can augment human capabilities, making less experienced workers more productive.
The Use of Robotics in Specific Construction Applications
Robotics is rapidly transforming various aspects of the construction industry, moving beyond simple automation to sophisticated applications that boost efficiency, precision, and safety. The integration of robots isn’t just about replacing human workers; it’s about augmenting their capabilities and tackling tasks previously deemed too dangerous, complex, or time-consuming. This leads to significant improvements across the entire construction lifecycle.
Robotic Applications in High-Rise Building Construction
High-rise construction presents unique challenges, including working at great heights and maintaining precision in complex structural assemblies. Robots are proving invaluable in overcoming these obstacles. For instance, robotic arms equipped with welding tools can precisely join steel beams at considerable heights, minimizing human risk and ensuring consistent weld quality. Similarly, robots can be used for tasks like bricklaying, window installation, and façade cleaning, all while enhancing speed and accuracy. Imagine a robotic system autonomously placing prefabricated concrete panels, layer upon layer, with millimeter-perfect accuracy, drastically accelerating the construction process and reducing the potential for human error. This represents a significant leap forward in high-rise construction efficiency and safety.
Robotics in Infrastructure Projects
The construction of bridges and roads often involves repetitive, labor-intensive tasks in challenging environments. Robots are deployed to automate tasks such as drilling, cutting, and welding in bridge construction, ensuring consistent quality and reducing the risks associated with working at heights or in confined spaces. Autonomous vehicles equipped with sensors and robotic arms can be used for road paving, laying down asphalt with precise thickness and smoothness. This minimizes material waste and ensures a consistently high-quality road surface. Moreover, robots can be deployed for inspections of existing infrastructure, identifying potential structural weaknesses or damage before they escalate into major problems. For example, drone-based inspections with high-resolution cameras and sensors can provide detailed 3D models of bridges, allowing for efficient and early detection of cracks or corrosion.
Robotics in Prefabrication and Modular Construction
Prefabrication and modular construction rely heavily on precision and repeatability. Robots excel in this environment. In prefabrication factories, robots can automate tasks such as cutting, assembling, and welding components for buildings. This leads to faster production, reduced waste, and improved quality control. Robots can also handle the precise placement of components during the assembly of modular units, ensuring a perfect fit and minimizing errors. Consider a robotic arm precisely installing electrical wiring and plumbing within a prefabricated bathroom unit – a task that is both time-consuming and prone to errors when done manually. The consistent quality and speed offered by robotics significantly impact the efficiency of the entire modular construction process.
Robots in Residential versus Commercial Construction
Feature | Residential Construction | Commercial Construction |
---|---|---|
Robot Applications | Primarily focused on smaller-scale tasks like bricklaying, drywall installation, and interior finishing. Increasing use of prefabrication for specific components. | Wider range of applications, including high-rise construction, large-scale prefabrication, and infrastructure work. More extensive use of autonomous systems. |
Scale of Deployment | Generally smaller-scale deployments, often focusing on specific tasks rather than complete automation of the entire process. | Larger-scale deployments, with potential for complete automation of certain processes in large projects. |
Economic Viability | Cost-effectiveness is a key consideration, with the focus on tasks where robotic automation offers significant ROI. | Larger project budgets often make the investment in advanced robotics more feasible. |
Level of Automation | More likely to involve human-robot collaboration, with robots assisting human workers. | Greater potential for autonomous operation, particularly in controlled environments like prefabrication plants. |
Safety Improvements on Construction Sites
Construction sites are notoriously dangerous environments, with high rates of workplace accidents. The introduction of robotics offers a significant opportunity to mitigate these risks and create safer working conditions for human construction workers. By automating hazardous tasks and enhancing site monitoring, robots are transforming the safety landscape of the construction industry.
Robots reduce workplace accidents primarily through hazard mitigation. They can perform tasks that are inherently dangerous for humans, such as working at heights, operating heavy machinery in confined spaces, or handling hazardous materials. This minimizes human exposure to risky situations, directly leading to a reduction in accidents and injuries.
Robotics in Hazardous Material Handling
Robots are ideally suited for handling hazardous materials. They can be equipped with specialized sensors and manipulators to safely manage materials like asbestos, lead paint, or chemicals without putting human workers at risk. For instance, a robotic arm with a vacuum system can safely remove asbestos from a building, containing the hazardous fibers and preventing worker exposure. Similarly, robots can be used to decontaminate areas exposed to dangerous chemicals, minimizing the risk of human exposure and contamination. This automation reduces the chance of inhalation, ingestion, or skin contact with hazardous substances, leading to fewer health problems and fatalities.
Robotic Systems for Challenging Environments
Several robotic systems are specifically designed to improve worker safety in challenging environments. One example is the use of drones for site inspections. Drones equipped with high-resolution cameras can assess structural integrity, identify potential hazards, and monitor worker activity from a safe distance, eliminating the need for workers to perform these potentially dangerous tasks manually at heights. Another example involves the use of robotic excavators or demolition robots that can operate in unstable or collapsed structures, removing the need for human workers to enter these dangerous zones. These robots can perform demolition work more precisely and safely, reducing the risk of collapse and injury.
Safety Improvements Achieved Through Robotics in Construction
The implementation of robotics in construction has led to a multitude of safety improvements. These improvements can be summarized as follows:
- Reduced risk of falls from heights through the use of robots for high-altitude tasks.
- Minimized exposure to hazardous materials, such as asbestos and chemicals.
- Decreased risk of injuries from heavy machinery operation through robotic automation.
- Improved site safety through remote monitoring and inspection using drones and other robotic systems.
- Enhanced worker safety in confined spaces by using robots to perform tasks in dangerous areas.
- Reduction in repetitive strain injuries by automating repetitive tasks.
The Economic Impact of Robotics in Construction
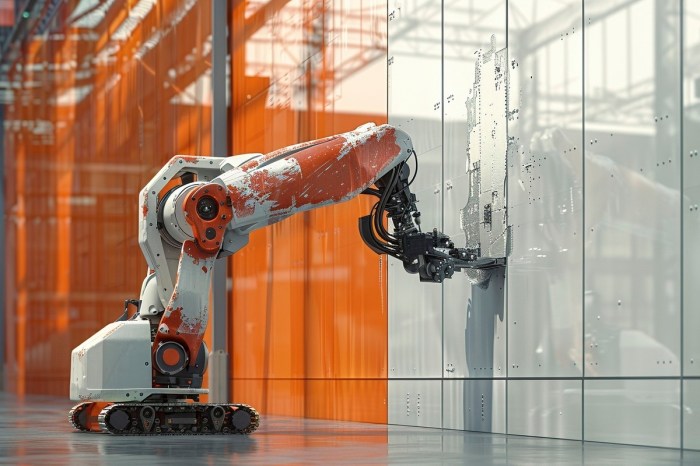
Source: neuroject.com
The construction industry, traditionally slow to adopt technological advancements, is experiencing a seismic shift with the integration of robotics. This isn’t just about shiny new gadgets; it’s about fundamentally altering the economic landscape of the sector, promising increased profitability, reduced project costs, and a more sustainable future. The long-term economic benefits are substantial and far-reaching, impacting everything from individual firms to national economies.
Increased Profitability for Construction Firms
Robotic adoption translates directly into increased profitability for construction firms. Automation reduces labor costs, minimizes material waste, and speeds up project completion times. For example, a bricklaying robot can lay bricks significantly faster and more consistently than a human crew, leading to substantial savings in labor hours and reduced project timelines. This efficiency translates into higher profit margins and the ability to take on more projects, fueling further growth. Moreover, the improved quality and precision of robotic work reduces costly rework and delays, further boosting profitability. Early adopters are already seeing a significant return on their investment, demonstrating the compelling financial case for robotics in the construction sector.
Impact on the Overall Cost of Construction Projects
While the initial investment in robotic systems can be substantial, the long-term impact on the overall cost of construction projects is generally positive. The reduced labor costs, material waste, and project delays outweigh the initial investment, leading to cost savings across the board. Consider the example of a high-rise building project: using robotic systems for tasks like welding, concrete pouring, and façade installation can drastically reduce the time and labor required, ultimately resulting in a lower overall project cost. Furthermore, the enhanced precision of robotic systems minimizes errors and rework, further reducing costs. The data shows that projects incorporating robotics often come in under budget and ahead of schedule.
Return on Investment (ROI) for Different Robotic Systems
The return on investment (ROI) for robotic systems varies depending on the specific application, the scale of the project, and the initial cost of the equipment. However, numerous studies and case studies demonstrate a strong positive ROI for many robotic systems in construction. Below is a table illustrating potential ROI for different robotic applications:
Robotic System | Estimated Initial Investment | Estimated Annual Savings | Estimated ROI (Years) |
---|---|---|---|
Bricklaying Robot | $150,000 | $50,000 | 3 |
Concrete Pouring Robot | $250,000 | $75,000 | 3.3 |
Welding Robot | $100,000 | $30,000 | 3.3 |
Demolition Robot | $300,000 | $100,000 | 3 |
*Note: These figures are estimates and may vary based on specific project parameters and operational efficiency.* The actual ROI will depend on factors such as project size, labor costs, and the specific capabilities of the robotic system employed. However, the trend clearly indicates a significant potential for cost savings and increased profitability through the adoption of robotics.
Challenges and Future Trends in Construction Robotics
The construction industry, while embracing robotics with enthusiasm, faces significant hurdles in its widespread adoption. From high initial investment costs to the complexities of integrating robots into existing workflows, the path to a fully automated construction site is paved with challenges. However, ongoing technological advancements and a growing understanding of the industry’s unique needs are paving the way for a future where robots are commonplace, significantly transforming how we build.
Current Challenges Hindering Widespread Adoption
Several factors currently limit the broader implementation of robotics in construction. High upfront costs for purchasing and maintaining robots are a major deterrent, particularly for smaller construction firms. The lack of standardized interfaces and protocols between different robotic systems creates integration difficulties, hindering efficient collaboration between various robots and existing equipment. Furthermore, the unpredictable and dynamic nature of construction sites presents a significant challenge for robot navigation and task execution. Robots need to adapt to changing environments, unexpected obstacles, and variations in materials, a task that currently requires significant programming and oversight. Finally, a shortage of skilled labor capable of programming, operating, and maintaining these advanced robotic systems also presents a barrier to widespread adoption.
Future Trends and Advancements in Construction Robotics Technology
The future of construction robotics is bright, with several key trends poised to drive significant advancements. We can expect to see increased use of AI and machine learning to enhance robot autonomy and adaptability. Robots will become more capable of handling unstructured environments and complex tasks with minimal human intervention. Improved sensor technologies, such as advanced vision systems and 3D laser scanners, will provide robots with a more comprehensive understanding of their surroundings, enabling more precise and efficient work. Furthermore, the development of more robust and durable robots designed to withstand the harsh conditions of construction sites will be crucial. Collaborative robots (cobots) designed to work safely alongside human workers will also play an increasingly important role, maximizing efficiency and safety. Finally, modular and adaptable robotic systems will become more prevalent, allowing for easier integration and customization to suit various construction tasks and site conditions.
The Impact of Artificial Intelligence on Construction Robotics
AI is set to revolutionize construction robotics, enabling robots to perform tasks that were previously impossible. AI-powered robots will be capable of learning from experience, adapting to changing conditions, and making autonomous decisions. For example, AI can optimize robot movements for maximum efficiency, predict potential problems, and even adjust construction plans in real-time based on environmental factors. This level of autonomy will significantly increase productivity and reduce the risk of human error. AI-powered vision systems will allow robots to accurately identify and classify objects, materials, and even potential hazards on the construction site, improving safety and precision. Moreover, AI can be used to analyze large datasets of construction information to predict potential delays, optimize resource allocation, and improve overall project management. Imagine AI predicting potential material shortages days in advance, allowing for proactive ordering and preventing costly delays. This predictive capability, powered by AI, will be transformative.
Potential Future Applications of Robotics in Construction
The potential applications of robotics in construction are vast and constantly expanding. As technology advances, we can anticipate the following:
- Automated bricklaying: Robots capable of laying bricks at significantly higher speeds and with greater precision than human workers.
- Autonomous concrete pouring and finishing: Robots that can pour and finish concrete with consistent quality and efficiency, minimizing waste and labor costs.
- Automated welding and cutting: Robots performing precise welding and cutting tasks, enhancing structural integrity and reducing human error.
- Drone-based site surveying and inspection: Drones equipped with high-resolution cameras and sensors providing detailed site surveys and identifying potential safety hazards.
- Robotic demolition and dismantling: Robots capable of safely and efficiently demolishing structures, minimizing risks to human workers.
- Automated drywall installation: Robots that can quickly and accurately install drywall, reducing labor costs and improving consistency.
- AI-powered project management and planning: AI systems analyzing project data to optimize schedules, resource allocation, and risk management.
Illustrative Examples of Robotic Systems in Construction
The construction industry, traditionally reliant on manual labor, is undergoing a dramatic transformation thanks to the integration of robotic systems. These machines are not just automating tasks; they’re improving safety, precision, and overall efficiency, leading to significant cost savings and project completion acceleration. Let’s delve into some specific examples of robots revolutionizing different aspects of construction.
Robotic Bricklaying System: The SAM100
The SAM100, developed by Construction Robotics, is a prime example of a robotic bricklaying system. This impressive machine uses a robotic arm equipped with a sophisticated gripper to pick up and place bricks with remarkable speed and accuracy. The SAM100 is programmed with the building’s blueprint, allowing it to autonomously lay bricks according to the design. Its capabilities extend beyond simply placing bricks; it can also handle various brick sizes and types, adjust mortar application, and maintain consistent spacing. This automation drastically reduces labor costs and significantly accelerates the bricklaying process, leading to faster project completion times and improved productivity. The SAM100’s precision minimizes material waste and ensures consistent quality, resulting in a more structurally sound and aesthetically pleasing final product. Unlike human bricklayers, it can operate continuously without fatigue, significantly increasing the overall efficiency of the construction process.
Robotic Demolition System: Brokk Demolition Robots
Brokk offers a range of robotic demolition systems designed for various applications, from small-scale demolition work to large-scale building dismantling. These robots are remotely controlled, allowing operators to work from a safe distance, minimizing risks associated with hazardous demolition tasks. The robots utilize powerful hydraulic arms equipped with various attachments, such as breakers, shears, and grapples, to efficiently dismantle structures. Their compact size allows them to access confined spaces, making them suitable for demolition work in complex environments. The ability to remotely operate these robots significantly enhances worker safety by removing them from potentially dangerous situations. Furthermore, Brokk robots are known for their robustness and durability, capable of handling challenging demolition tasks in harsh conditions. Their precise control allows for selective demolition, minimizing collateral damage and reducing waste. For instance, in the demolition of a multi-story building, a Brokk robot could be used to selectively remove sections of a wall without damaging adjacent structures.
Robotic Welding System: Yaskawa Motoman
Yaskawa Motoman produces a variety of robotic welding systems specifically designed for the construction industry. These robots offer high precision and speed, capable of performing complex welds with exceptional accuracy. The robotic arms are equipped with advanced sensors and control systems that ensure consistent weld quality and minimize defects. The robots can be programmed to perform a wide range of welding tasks, including fillet welds, groove welds, and spot welds, on various materials commonly used in construction, such as steel and aluminum. Safety is a paramount concern in welding, and these robotic systems incorporate features such as safety light curtains and emergency stop mechanisms to prevent accidents. By automating the welding process, these robots improve worker safety by eliminating the need for human welders to perform potentially hazardous tasks in confined spaces or high-risk environments. The increased precision of robotic welding also translates into reduced material waste and improved structural integrity of the welded joints, leading to stronger and more durable structures.
Final Review: How Robotics Is Revolutionizing The Construction Industry
The construction industry’s embrace of robotics isn’t just a trend; it’s a necessary evolution. By tackling labor shortages, boosting productivity, and enhancing safety, robots are paving the way for a more sustainable and efficient future. While challenges remain, the potential benefits are undeniable, promising faster project completion, reduced costs, and a safer workplace for everyone. The future of construction is being built, one robotic arm at a time, and it’s looking pretty impressive.