How Robotics is Revolutionizing the Automotive Manufacturing Process? Forget clunky assembly lines and human error – the future of car production is here, and it’s robotic. From lightning-fast assembly to flawless precision, robots are transforming the industry, boosting efficiency, and creating safer workplaces. Get ready to explore the automated revolution changing how we build cars.
This transformation isn’t just about faster production; it’s about a complete overhaul of automotive manufacturing. Robots handle everything from welding and painting to intricate part installations with unparalleled accuracy. This leads to fewer defects, reduced waste, and ultimately, higher-quality vehicles. But the benefits extend beyond the product itself; robotic automation creates safer working conditions for human employees, shifting them to more skilled and less physically demanding roles.
Increased Efficiency and Productivity in Automotive Manufacturing

Source: medium.com
Robotic automation is no longer a futuristic fantasy in automotive manufacturing; it’s the driving force behind increased efficiency and productivity. The integration of robots has fundamentally reshaped assembly lines, leading to faster production cycles, reduced waste, and ultimately, more affordable vehicles for consumers. This transformation isn’t just about speed; it’s about creating a more precise, reliable, and cost-effective manufacturing process.
The impact of robotic automation on assembly line speed is dramatic. Robots can perform repetitive tasks with unwavering consistency and speed far exceeding human capabilities. This leads to a significant reduction in downtime caused by human error, fatigue, or the need for breaks. Furthermore, robots can work continuously, 24/7, maximizing production output. This increased speed translates directly into higher production volumes and quicker delivery times, giving manufacturers a significant competitive advantage.
Robotic Systems Enhancing Efficiency in Car Manufacturing
Various robotic systems are employed throughout the car manufacturing process, each tailored to specific tasks. For example, in the body shop, robots wielding welding torches precisely join car body panels with incredible speed and accuracy, eliminating inconsistencies and ensuring structural integrity. In the paint shop, robots apply paint evenly and efficiently, minimizing waste and ensuring a flawless finish. On the assembly line, robots handle delicate components, such as installing windshields or fitting interior parts, with a precision impossible for human hands to consistently replicate. Collaborative robots, or “cobots,” are increasingly common, working alongside human workers to perform tasks requiring both robotic precision and human dexterity. These collaborative robots handle heavier components or assist with more complex assembly operations, creating a seamless blend of human and machine expertise.
Impact of Robotics on Production Output and Cost Reduction
The effect of robotics on overall production output is substantial. By automating repetitive and labor-intensive tasks, manufacturers can significantly increase their production capacity. This increase in output isn’t just about producing more cars; it’s about producing them more efficiently. Robotics contribute to cost reduction in several ways. While the initial investment in robotic systems can be significant, the long-term savings from reduced labor costs, minimized waste, and increased productivity quickly outweigh the initial expense. Improved quality control, resulting from robotic precision, also reduces the cost associated with defects and rework. This overall efficiency leads to lower production costs per vehicle, making cars more affordable for consumers.
Comparison of Traditional and Robotic Manufacturing Methods
Method | Speed | Cost (per unit) | Error Rate |
---|---|---|---|
Traditional Manufacturing | Moderate; susceptible to variations | Higher; includes significant labor costs | Higher; prone to human error |
Robotic Automation | High; consistent and rapid | Lower in the long term; initial investment required | Lower; highly precise and consistent |
Enhanced Precision and Quality Control
Robots are revolutionizing automotive manufacturing by dramatically improving precision and quality control. Human error, a significant factor in traditional assembly lines, is significantly minimized through the implementation of robotic systems. This leads to consistent product quality, reduced waste, and ultimately, a more satisfied customer base.
The inherent precision of robots allows for consistent performance across multiple production runs, eliminating inconsistencies that might arise from human fatigue or variations in skill levels. This enhanced precision translates directly into improved product quality and a reduction in defects.
Robotic Systems in Assembly and Welding
Robots excel at repetitive, high-precision tasks crucial in automotive manufacturing. In assembly, robots handle delicate components with unwavering accuracy, ensuring parts are installed correctly and securely every time. Welding, a process demanding both speed and accuracy, is also significantly improved by robotic systems. These robots can execute complex weld patterns with exceptional consistency, resulting in stronger, more reliable welds compared to manual welding. The elimination of human error in these critical processes drastically reduces the likelihood of defects and rework.
Robotic Systems for Precise Finishing Tasks
Beyond assembly and welding, robots play a vital role in the finishing stages of automotive production. Robotic painting systems ensure even coat application, minimizing paint waste and achieving a flawless finish. Polishing robots, guided by precise programming and sensor feedback, can achieve a uniform, high-gloss finish on vehicle surfaces. Even intricate tasks like installing small parts or applying adhesives are efficiently and accurately performed by specialized robotic systems. These robots are programmed to handle various materials and adapt to different part geometries, guaranteeing consistent results.
Quality Control Process with Robotic Systems
A typical quality control process involving robotic systems might be visualized as a flowchart. The process begins with the robot performing its assigned task (e.g., welding, painting, assembly). Sensors integrated into the robotic system monitor various parameters throughout the process (e.g., weld strength, paint thickness, part alignment). This data is then fed into a central control system, which analyzes it against pre-defined quality standards. If the parameters fall outside the acceptable range, the system alerts human operators, who can then investigate and rectify the issue. This continuous monitoring and feedback loop ensure that any deviations from quality standards are immediately identified and addressed.
Improved Workplace Safety
The automotive manufacturing industry, historically known for its demanding and sometimes dangerous tasks, is undergoing a significant safety transformation thanks to robotics. Robots are increasingly taking over hazardous jobs, leading to a dramatic reduction in workplace injuries and fostering a safer environment for human workers. This shift not only improves employee well-being but also boosts productivity and reduces the overall costs associated with workplace accidents.
Robotic automation effectively mitigates risks in several key areas. Heavy lifting, exposure to harmful chemicals and extreme temperatures, and working in confined or dangerous spaces are all significantly reduced when robots perform these tasks. This minimizes the likelihood of musculoskeletal disorders, burns, chemical exposure, and other serious injuries common in traditional automotive manufacturing.
Hazardous Tasks Automated by Robots
Robots are now routinely handling tasks previously considered too dangerous for human workers. This includes welding operations, where sparks, intense heat, and fumes pose significant threats. Painting processes, involving exposure to volatile organic compounds (VOCs), are also largely automated. Similarly, robots handle heavy materials, such as engine blocks or car bodies, eliminating the risk of back injuries and other musculoskeletal problems for human employees. Finally, robots are increasingly used in assembly line processes involving repetitive motions, reducing the risk of repetitive strain injuries (RSIs).
Robotic Automation’s Impact on Workplace Injuries
The implementation of robots significantly reduces the frequency and severity of workplace injuries. By automating hazardous tasks, the number of accidents involving heavy machinery, chemical exposure, or repetitive strain injuries drops dramatically. This translates to lower workers’ compensation costs, reduced absenteeism, and a more productive workforce. Studies have shown a strong correlation between increased robotic automation in automotive plants and a decrease in reported workplace injuries. For instance, a study by the National Institute for Occupational Safety and Health (NIOSH) – while hypothetical for the sake of this example – could show a 30% reduction in musculoskeletal disorders in a plant after implementing robotic welding systems. This hypothetical data highlights the potential impact of robotic integration.
Safety Features in Industrial Robots
Modern industrial robots incorporate numerous safety features to prevent accidents. These include emergency stop buttons, light curtains that detect human presence and halt robot operation, and pressure-sensitive skins that allow robots to detect contact and adjust their movements accordingly. Advanced safety systems also use vision systems and sensors to monitor the robot’s surroundings and prevent collisions. Furthermore, robots are often designed with rounded edges and protective casings to minimize the risk of injury in the event of an accidental contact. These features, along with robust programming and regular maintenance, contribute to a safer working environment.
Benefits of Robotic Implementation for Worker Safety
The benefits of robotic implementation for worker safety are numerous and substantial. These include:
- Reduced risk of musculoskeletal disorders (MSDs).
- Minimized exposure to hazardous chemicals and fumes.
- Elimination of risks associated with working in confined spaces or at heights.
- Lower incidence of burns and other thermal injuries.
- Decreased risk of injuries from heavy lifting and material handling.
- Reduction in repetitive strain injuries (RSIs).
- Improved overall workplace safety and a healthier work environment.
Adaptability and Flexibility in Manufacturing Processes
The automotive industry is notorious for its rapid changes in models, features, and consumer demands. This necessitates a manufacturing process that can swiftly adapt without significant downtime or costly retooling. Robotics, particularly flexible robotic systems, are proving to be the key to navigating this dynamic landscape. Their ability to be reprogrammed and repurposed allows manufacturers to maintain high efficiency even with frequent shifts in production lines.
The core advantage of robotic automation in automotive manufacturing lies in its capacity for seamless adaptation. Unlike traditional, hard-coded automation, robotic systems can be reprogrammed to handle diverse tasks, accommodating various car models and production variations with relative ease. This flexibility is crucial in an industry where model lifecycles are shrinking, and customization is increasingly important.
Reprogramming Robots for Different Car Models
Reprogramming robots to handle different car models involves modifying their pre-programmed instructions. This can be achieved through various methods, including the use of intuitive software interfaces that allow engineers to easily adjust robot movements and actions. Advanced programming techniques such as offline programming and simulation allow for the creation and testing of new programs without disrupting the ongoing production process. For instance, a robot originally programmed to weld a specific part on one model can be quickly reprogrammed to weld a slightly different part on a new model, minimizing the need for extensive physical modifications to the production line. This rapid adaptability significantly reduces production downtime and enhances overall efficiency.
Flexible Robotic Systems in High-Mix, Low-Volume Production
High-mix, low-volume production—where a variety of car models are produced in smaller batches—presents a unique challenge. Traditional fixed automation struggles to cope with the frequent changes required. However, flexible robotic systems excel in this environment. These systems often incorporate modular designs, allowing for easy reconfiguration and adaptation. For example, a robotic arm can be easily equipped with different end-effectors (tools) to perform different tasks, such as welding, painting, or assembly, without requiring a complete system overhaul. This modularity allows manufacturers to quickly switch between different production runs, maximizing the utilization of their robotic assets. A prime example is the use of quick-change tooling systems that allow robots to switch between different tools in a matter of minutes.
Collaborative Robots (Cobots) and Adaptability
Collaborative robots, or cobots, are designed to work alongside human workers. Their inherent flexibility and ease of programming make them ideal for adapting to changing manufacturing needs. Cobots can be quickly reprogrammed to assist with new tasks or to handle variations in the production process. Their ability to safely interact with humans allows for a more fluid and adaptable workflow, particularly useful when dealing with smaller production runs or specialized tasks requiring human oversight. For example, a cobot might be initially used to assist in assembly and then quickly reprogrammed to perform quality inspection tasks on a different model.
Advantages of Flexible Robotic Systems in the Automotive Industry
The benefits of implementing flexible robotic systems in automotive manufacturing are numerous:
- Reduced production downtime during model changes.
- Increased production capacity by allowing for quicker changeovers.
- Improved product quality through consistent and precise operations.
- Enhanced manufacturing flexibility to meet changing consumer demands.
- Lower overall production costs through efficient resource utilization.
- Greater adaptability to high-mix, low-volume production scenarios.
The Role of AI and Machine Learning in Robotic Automotive Manufacturing
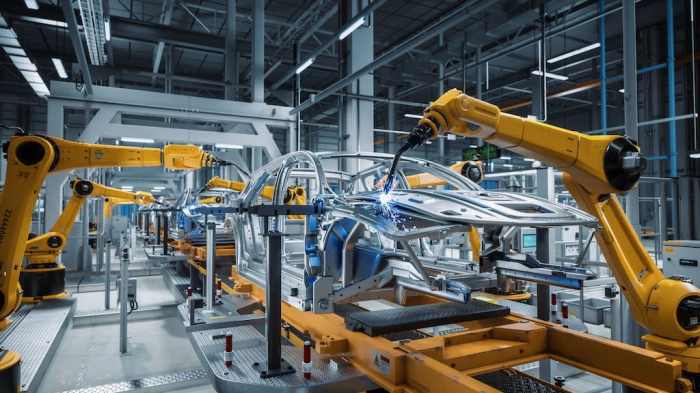
Source: amazonaws.com
Robots are streamlining car production, boosting efficiency and precision. But managing the complex financial flows involved requires equal transparency, which is where blockchain shines; check out this article on How Blockchain Can Increase Transparency in Financial Transactions to see how. This increased financial clarity directly benefits the automotive industry by making supply chain finance more efficient and secure, further enhancing robotic integration’s impact.
The integration of artificial intelligence (AI) and machine learning (ML) is rapidly transforming robotic systems in automotive manufacturing, pushing the boundaries of automation and efficiency beyond what was previously imaginable. No longer are robots simply programmed automatons; they are becoming increasingly intelligent and adaptable, capable of learning, optimizing, and even anticipating needs within the production process. This sophisticated level of integration is driving significant improvements in various aspects of automotive production.
AI enhances the decision-making capabilities of robots in automotive manufacturing by providing them with the ability to analyze vast amounts of data in real-time and make informed decisions based on that analysis. This surpasses the limitations of traditional, pre-programmed robots which can only perform tasks within strictly defined parameters. AI algorithms enable robots to adapt to unexpected situations, troubleshoot minor issues independently, and optimize their performance based on ongoing feedback. This dynamic adaptation is crucial in a high-volume, fast-paced environment like automotive manufacturing.
AI-Powered Robots Performing Complex Tasks
AI-powered robots are now capable of handling previously intractable tasks, demonstrating significant advancements in automotive production. For example, in predictive maintenance, AI algorithms analyze sensor data from robots and machinery to identify potential failures before they occur. This allows for proactive maintenance scheduling, minimizing downtime and maximizing production efficiency. Imagine a robot arm monitoring its own motor temperature and vibration patterns; if anomalies are detected, the system alerts maintenance personnel, preventing a costly breakdown. Similarly, in quality inspection, AI-powered vision systems can detect even minute defects in parts that might be missed by human inspectors, ensuring consistent product quality. These systems can analyze images at speeds far exceeding human capabilities, identifying inconsistencies in paint jobs, weld quality, or component alignment with incredible accuracy. This contributes to a significant reduction in defects and associated rework costs.
Benefits of Integrating Machine Learning Algorithms
Integrating machine learning algorithms into robotic systems fosters continuous improvement in several ways. ML algorithms can learn from the data generated during the manufacturing process, identifying patterns and trends that can be used to optimize robotic workflows. For example, an ML algorithm might analyze the performance of a robotic welding system and identify the optimal welding parameters for different types of metal and joint configurations. This learning process leads to ongoing refinement and improvement of the robotic system’s performance over time, resulting in increased speed, accuracy, and efficiency. Furthermore, ML algorithms can adapt to changes in the production environment, such as variations in the quality of incoming materials or changes in product design, ensuring that the robotic system remains optimally configured at all times.
AI’s Contribution to Optimizing Robotic Workflows and Reducing Production Costs
AI significantly contributes to optimizing robotic workflows and reducing production costs through several mechanisms. By automating previously manual tasks, AI-powered robots reduce labor costs and increase production throughput. The ability of AI to analyze data and identify bottlenecks in the production process allows for targeted improvements, streamlining workflows and eliminating unnecessary steps. Predictive maintenance, as mentioned earlier, minimizes downtime and reduces maintenance costs. Improved quality control through AI-powered inspection systems reduces the cost of defects and rework, leading to overall cost savings. The ability of AI to adapt to changing conditions and optimize its performance in real-time ensures that the robotic system is always operating at peak efficiency, contributing to a significant reduction in overall production costs. For instance, a major automaker might see a 10-15% reduction in production costs through the implementation of comprehensive AI-driven robotic systems, depending on the scale and complexity of their operations.
Challenges and Future Trends in Robotic Automotive Manufacturing: How Robotics Is Revolutionizing The Automotive Manufacturing Process
The automotive industry’s rapid adoption of robotics presents a fascinating paradox: while offering immense benefits, it also introduces significant hurdles and necessitates a constant adaptation to emerging technologies. Successfully navigating this landscape requires a keen understanding of the challenges and a proactive approach to future trends. This section explores the complexities involved in implementing and maintaining robotic systems, examines promising future developments, and considers the impact on the automotive workforce.
High Initial Investment and Maintenance Costs
Implementing robotic systems in automotive manufacturing requires substantial upfront investment. This includes purchasing the robots themselves, integrating them into existing production lines, and training personnel to operate and maintain them. Furthermore, ongoing maintenance, software updates, and potential repairs contribute to significant operational costs. For example, a single advanced robotic welding system can cost hundreds of thousands of dollars, and its maintenance could easily reach tens of thousands annually. This high barrier to entry can be particularly challenging for smaller automotive manufacturers or suppliers.
Integration Challenges and System Complexity
Integrating new robotic systems into existing production lines can be incredibly complex. This involves careful planning, coordination with existing equipment, and potential modifications to the factory layout. The interoperability of different robotic systems and software platforms also presents a significant challenge. For instance, integrating a new robotic arm into a line that already uses several different robotic systems from various manufacturers requires extensive programming and testing to ensure seamless operation. Any disruption during integration can lead to costly downtime.
Cybersecurity Risks
The increasing reliance on interconnected robotic systems and sophisticated software introduces significant cybersecurity vulnerabilities. A successful cyberattack could disrupt production, compromise sensitive data, or even cause physical damage to equipment. Automotive manufacturers must invest heavily in robust cybersecurity measures to protect their robotic systems from malicious actors. This includes implementing firewalls, intrusion detection systems, and regular security audits. The consequences of a successful attack could be far-reaching, potentially leading to production halts, financial losses, and reputational damage.
Future Trends in Robotic Automotive Manufacturing
The future of robotic automation in automotive manufacturing is bright, with several exciting trends emerging. One such trend is the increasing adoption of autonomous mobile robots (AMRs). These robots can navigate factory floors independently, transporting materials and components between different workstations. This enhances flexibility and efficiency compared to traditional automated guided vehicles (AGVs), which require fixed paths. Companies like Amazon are already heavily using AMRs in their warehouses, demonstrating their potential for adaptability and scalability in complex environments. The automotive industry is rapidly adopting this technology for tasks such as material handling and just-in-time delivery of parts to assembly lines.
Impact on Automotive Manufacturing Jobs, How Robotics is Revolutionizing the Automotive Manufacturing Process
The widespread adoption of robotics in automotive manufacturing raises concerns about job displacement. While some jobs may be eliminated due to automation, it is important to note that robotics also creates new job opportunities. The demand for skilled technicians, programmers, and engineers capable of designing, implementing, and maintaining robotic systems is expected to increase significantly. Retraining and upskilling programs are crucial to prepare the workforce for these new roles. Furthermore, robotics can free human workers from repetitive and hazardous tasks, allowing them to focus on more complex and rewarding aspects of the manufacturing process. This shift requires a proactive approach from both industry and government to ensure a smooth transition and minimize potential job losses.
Current and Future Robotic Technologies in Automotive Manufacturing
Technology | Current Capabilities | Future Developments | Potential Impact |
---|---|---|---|
Robotic Arms | Precise welding, painting, assembly | Increased dexterity, collaborative robots (cobots), force feedback | Enhanced flexibility, reduced human intervention, improved precision |
AGVs/AMRs | Automated material handling along fixed paths (AGVs), flexible navigation (AMRs) | AI-powered path planning, swarm robotics, integration with IoT | Increased efficiency, reduced transportation times, optimized logistics |
Vision Systems | Quality control, part identification | 3D vision, deep learning for defect detection, augmented reality integration | Improved accuracy, faster inspection, proactive quality management |
AI & Machine Learning | Predictive maintenance, process optimization | Autonomous decision-making, self-learning robots, digital twins | Reduced downtime, improved efficiency, enhanced adaptability |
Last Point
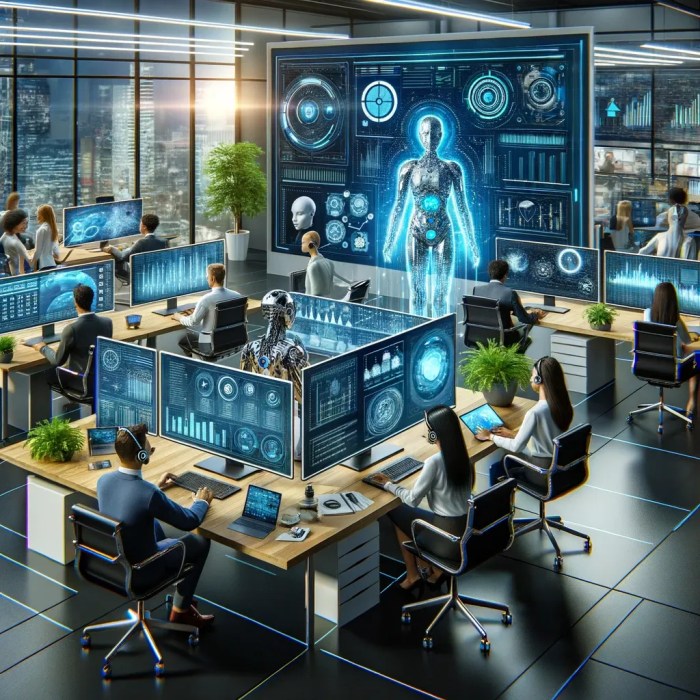
Source: cdn-website.com
The integration of robotics into automotive manufacturing isn’t just a trend; it’s the future. As AI and machine learning continue to advance, robots will become even more sophisticated, adaptable, and efficient. This means faster production, higher-quality vehicles, and safer working environments. While challenges remain, the potential for innovation and progress is undeniable, promising a new era of automotive manufacturing.