How Robotics is Improving the Future of Food Production Systems: Forget rusty farm tools and back-breaking labor. The future of food is automated, efficient, and surprisingly delicious. We’re diving deep into the robotic revolution transforming how we grow, process, and deliver our food, from autonomous tractors to AI-powered sorting systems. Get ready to feast your eyes on the tech that’s feeding the world, one perfectly-picked tomato at a time.
This isn’t just about faster harvesting; it’s about creating a more sustainable, safer, and ultimately more delicious food system. We’ll explore how robots are tackling labor shortages, boosting yields, and minimizing waste – all while ensuring the food on your plate is top-notch. Think of it as a delicious blend of tech and agriculture, a recipe for a better tomorrow.
Increased Efficiency and Productivity in Farming
Robotic automation is revolutionizing food production, significantly boosting efficiency and productivity across the agricultural landscape. Traditional farming methods, heavily reliant on manual labor, are increasingly proving inadequate to meet the growing global demand for food. Robotics offers a solution, promising faster harvesting, higher yields, and reduced waste, ultimately making food production more sustainable and economically viable.
The integration of robots into farming practices is dramatically altering harvesting speed and yield. Robots can operate continuously, unaffected by fatigue or weather conditions, unlike human workers. This leads to quicker harvest times and minimizes post-harvest losses due to spoilage or damage. The precision and consistency of robotic systems also contribute to higher yields by ensuring that only ripe or mature produce is harvested, leaving immature fruits or vegetables to continue growing.
Robotics is revolutionizing food production, boosting efficiency and yield. But imagine a system where farmers get paid instantly and transparently for their produce – that’s where finance meets farming. Learn more about how this transparent payment system works by checking out this article on How Blockchain is Enabling Decentralized Finance Solutions. This blockchain-based approach ensures fair compensation, directly impacting the economic viability of robotic farming initiatives and fostering a more sustainable food system.
Robotic Harvesting: Speed and Yield Comparison
Let’s consider the example of tomato harvesting. The following table compares the time and labor required for harvesting a hectare of tomatoes using both robotic and manual methods. These figures are estimates based on industry reports and field trials, and may vary depending on specific robotic systems, crop density, and other factors.
Method | Harvest Time (hours) | Labor Required (workers) | Yield (tons/hectare) |
---|---|---|---|
Manual Harvesting | 200-300 | 10-15 | 50-60 |
Robotic Harvesting | 50-100 | 2-3 (for supervision and maintenance) | 60-70 |
Precision Agriculture with Robots
Beyond harvesting, robots are playing a crucial role in precision agriculture, optimizing various farming tasks for maximum efficiency and resource utilization. This involves employing robots for targeted actions, minimizing waste and maximizing yields.
For example, robotic planting systems ensure uniform seed spacing and depth, leading to improved germination rates and healthier plant growth. Companies like Abundant Robotics and Bosch are developing sophisticated robotic systems capable of autonomous planting. Similarly, robots equipped with sensors can precisely apply fertilizers and pesticides, reducing the amount of chemicals needed and minimizing environmental impact. This targeted application is often called “variable rate technology.” Irrigation is also being revolutionized by robotic systems that monitor soil moisture levels and adjust watering schedules accordingly, preventing water waste and optimizing crop hydration.
Reducing Crop Damage and Waste
Robotic systems contribute significantly to minimizing crop damage and waste throughout the production process. Gentle harvesting mechanisms used in robotic systems reduce bruising and other physical damage during harvesting, extending shelf life and improving product quality. Furthermore, robots can efficiently sort and grade produce based on size, shape, and quality, minimizing post-harvest losses due to spoilage or rejection of sub-standard produce. Automated packaging and handling systems further reduce waste and ensure efficient transport to markets, contributing to improved overall productivity.
Improved Food Quality and Safety
Robotic systems are revolutionizing food production, not only by boosting efficiency but also by significantly enhancing food quality and safety. Minimizing human intervention throughout the process leads to a cleaner, more consistent, and ultimately safer product reaching consumers. This is achieved through automation of tasks previously reliant on manual labor, reducing the risk of contamination and ensuring consistent adherence to quality standards.
Robotic systems offer a powerful solution to maintaining and improving food quality and safety across the entire supply chain. By automating processes and enhancing precision, they minimize the chances of human error and contamination, leading to a higher-quality and safer food product for consumers.
Minimizing Human Contact and Ensuring Consistent Processing
Automated harvesting, sorting, and processing systems reduce the risk of contamination from human handling. Imagine a robotic arm gently picking ripe strawberries from a field, meticulously sorting them by size and ripeness, and then placing them into containers without any human touch. This precision not only minimizes bruising but also eliminates the introduction of bacteria or other contaminants that might occur with human handling. Consistent processing parameters, such as temperature and pressure, are maintained by robotic systems, leading to more uniform and predictable final products. This consistency is crucial for maintaining quality and meeting specific consumer expectations. For example, robotic systems can ensure that every can of peaches is filled to the exact same level, maintaining a consistent product across batches.
Robotics in Contaminant Detection and Removal
Robotic vision systems, equipped with advanced image recognition software, can identify and remove contaminants such as foreign objects, damaged produce, or insect infestations with remarkable accuracy. These systems can inspect food products at incredibly high speeds, far exceeding human capabilities. For example, a robotic system could scan a conveyor belt of potatoes, identifying and removing any that are bruised or show signs of disease, ensuring only high-quality produce is processed further. Furthermore, sophisticated sensor technology integrated into robotic systems can detect subtle indicators of contamination that might be missed by the human eye, such as microbial growth or chemical residues. This proactive approach to contamination control significantly improves food safety.
Robotic Applications in Food Packaging and Labeling
Robotic systems play a crucial role in enhancing food safety and traceability through automated packaging and labeling. Precise and consistent packaging ensures product integrity and prevents contamination. Automated labeling allows for accurate and efficient tracking of products throughout the supply chain, facilitating quick and effective recall procedures if necessary.
- High-speed, automated packaging: Robots can rapidly package food products in various containers, maintaining consistent seals and preventing contamination.
- Precise label application: Robotic arms can accurately apply labels with all necessary information, including batch numbers, expiration dates, and nutritional details, enabling efficient traceability.
- Integrated quality control checks: Robotic systems can verify label accuracy and package integrity before the product leaves the facility.
- Sterile packaging environments: Robots can operate in sterile environments, minimizing the risk of contamination during packaging.
Addressing Labor Shortages and Reducing Labor Costs: How Robotics Is Improving The Future Of Food Production Systems
The agricultural and food processing sectors are facing a significant challenge: a dwindling workforce. Aging populations, changing career aspirations, and the physically demanding nature of the work are contributing to a critical labor shortage. Robotic automation offers a potential solution, promising increased efficiency and reduced reliance on human labor in various stages of food production.
Robotic automation’s impact on labor shortages is multifaceted. In the fields, robots can perform tasks like planting, harvesting, and weeding, alleviating the strain on human workers. In processing plants, robots can handle repetitive tasks such as sorting, packing, and quality control, freeing up human workers for more complex and strategic roles. This shift not only addresses the immediate labor shortage but also improves working conditions, making the industry more attractive to a younger generation.
Cost-Effectiveness of Robotic Solutions vs. Human Labor
The cost-effectiveness of robotic solutions versus human labor varies significantly depending on the specific application and scale of operation. While the initial investment in robots can be substantial, the long-term benefits often outweigh the costs. Consider the following comparison:
Task | Robotic Solution Cost (Estimated Annual) | Human Labor Cost (Estimated Annual) | Notes |
---|---|---|---|
Harvesting (e.g., lettuce) | $50,000 – $100,000 (including maintenance and energy) | $75,000 – $150,000 (depending on labor rates and hours) | Robots offer potential cost savings at scale, especially during peak seasons. However, initial investment is high. |
Packing and Sorting | $30,000 – $60,000 | $40,000 – $80,000 | Robots excel in consistent speed and accuracy, reducing waste and improving efficiency. |
Weeding | $20,000 – $40,000 | $30,000 – $60,000 (highly dependent on labor availability and crop density) | Autonomous weeding robots can significantly reduce labor costs, particularly in large-scale operations. |
Dairy Farming (Milking) | $40,000 – $80,000 (per robotic milking system) | $60,000 – $120,000 (depending on herd size and labor requirements) | Robotic milking systems can increase efficiency and improve animal welfare, potentially leading to cost savings. |
*Note: These cost estimates are broad generalizations and can vary based on factors such as robot type, farm size, labor rates, and maintenance costs. Actual costs should be determined through detailed cost-benefit analyses.*
New Job Opportunities Created by Robotics
The adoption of robotics in food production isn’t just about replacing human workers; it also creates new job opportunities. The increasing complexity of robotic systems necessitates skilled professionals in areas such as robotics maintenance, programming, and system integration. These roles require specialized knowledge and training, offering attractive career paths for individuals with technical skills. Furthermore, data analysis related to robot performance and optimization is creating a demand for skilled data scientists within the agricultural technology sector. The transition to a more automated food production system thus involves a shift in the type of labor required, not necessarily a reduction in overall employment opportunities.
Sustainable Food Production Practices
Robotics is revolutionizing agriculture, pushing beyond increased efficiency to address a critical global challenge: sustainable food production. By optimizing resource use and minimizing environmental impact, robotic systems are paving the way for a greener, more responsible food future. This isn’t just about higher yields; it’s about ensuring the long-term health of our planet and the viability of our food systems.
Robotic systems contribute significantly to sustainable farming by optimizing the use of vital resources like water, fertilizer, and pesticides. Precision agriculture, powered by robotics, allows for targeted application of these inputs, minimizing waste and reducing the environmental footprint. For example, robotic sprayers can identify individual weeds and apply herbicide only where needed, reducing overall pesticide use and preventing runoff into waterways. Similarly, robotic irrigation systems use sensors and data analysis to deliver water precisely where and when crops need it most, conserving water resources and reducing water stress on plants. This targeted approach contrasts sharply with traditional methods, which often lead to overuse and subsequent environmental damage.
Optimized Resource Utilization in Farming
Precision application of resources is key to sustainable agriculture. Robotic systems equipped with sensors and GPS technology can map fields, analyze soil conditions, and identify areas requiring specific treatments. This allows for variable rate application of fertilizers and pesticides, ensuring that crops receive the exact amount needed, reducing waste and minimizing environmental impact. Imagine a robotic tractor autonomously navigating a field, applying fertilizer only to areas identified as nutrient-deficient by soil sensors. This targeted approach minimizes fertilizer runoff, protecting water quality and reducing the environmental cost of nitrogen pollution. Furthermore, drones equipped with multispectral cameras can monitor crop health, providing early warnings of disease or nutrient deficiencies, enabling timely interventions and reducing the need for extensive pesticide applications later on.
Minimizing Environmental Impact through Robotics, How Robotics is Improving the Future of Food Production Systems
Beyond resource optimization, robotics plays a crucial role in minimizing waste and improving energy efficiency throughout the food production chain. Automated harvesting systems, for instance, can reduce post-harvest losses by gently collecting ripe produce, minimizing damage and extending shelf life. This reduces food waste, a significant environmental concern. Additionally, robotic sorting and packing systems can increase efficiency and accuracy, minimizing the amount of produce that is rejected due to imperfections. These systems also often operate on less energy than their human counterparts, further reducing the environmental footprint of food production. The overall impact is a reduction in greenhouse gas emissions and a more sustainable approach to food production.
Robotics in Sustainable Hydroponic Farming
Consider a large-scale hydroponic farm utilizing robotic systems. Automated systems manage nutrient delivery, precisely controlling the concentration and timing of nutrient solutions to optimize plant growth and minimize waste. Robotic arms can precisely plant seedlings, ensuring uniform spacing and maximizing yield. Furthermore, sensors monitor environmental parameters such as temperature, humidity, and light levels, allowing for automated adjustments to optimize plant growth and energy efficiency. Automated harvesting robots gently collect mature produce, minimizing damage and maximizing shelf life. This integrated robotic system results in significantly reduced water consumption compared to traditional agriculture, minimizing fertilizer runoff, and optimizing energy usage, showcasing the potential of robotics for sustainable intensive food production.
Robotics in Specific Food Production Areas
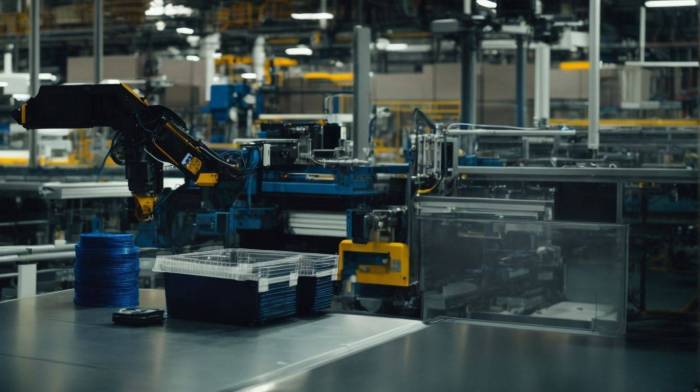
Source: dig8italx.com
The application of robotics varies significantly across different sectors of food production, driven by unique challenges and opportunities within each. While some areas see rapid adoption, others face hurdles related to cost, infrastructure, and the inherent complexities of working with living organisms. Examining these differences provides a clearer picture of robotics’ evolving role in our food systems.
The integration of robotics into food production is not a uniform process. Each area—dairy farming, livestock management, and poultry farming—presents its own set of obstacles and advantages when it comes to automating tasks. Understanding these nuances is crucial for optimizing the implementation of robotic technologies and maximizing their potential benefits.
Robotic Applications in Dairy, Livestock, and Poultry Farming
The following points highlight the diverse ways robotics are impacting different agricultural sectors, along with their respective challenges and opportunities.
- Dairy Farming: Robotics are increasingly used for automated milking, feeding, and monitoring cow health. Opportunities include increased milk yield, improved animal welfare through early disease detection, and reduced labor costs. Challenges include the high initial investment cost of robotic milking systems and the need for specialized infrastructure and skilled personnel for maintenance and operation. For example, some farms have seen a significant increase in milk production per cow with the implementation of robotic milking systems, but this is only cost-effective on larger farms with sufficient herd size.
- Livestock Management (Beef Cattle): Robotic systems are being developed for tasks such as automated feeding, monitoring animal health and behavior, and even selective breeding. Opportunities include improved feed efficiency, reduced labor needs, and enhanced animal welfare through precision monitoring. Challenges include the larger scale and more variable environment of beef cattle operations compared to dairy farms, making the implementation of robotics more complex and potentially costly. Moreover, the robustness of robotic systems needs to be significantly enhanced to withstand the harsh conditions of outdoor livestock management.
- Poultry Farming: Robotics in poultry farming are mainly focused on automated feeding, egg collection, and cleaning. Opportunities include increased efficiency in egg production, improved hygiene, and reduced labor costs. Challenges involve the delicate nature of poultry and the need for robots to navigate densely populated environments without causing harm to the birds. The relatively low cost of manual labor in some regions also makes the economic case for robotic systems less compelling in poultry farming compared to other areas.
Automated Milking System: A Case Study
One example of a successful robotic system is the automated milking system (AMS). These systems typically consist of a robotic arm equipped with sensors that identify and attach milking cups to individual cows. The system then monitors milk flow, detects mastitis (udder infection), and automatically detaches the cups once milking is complete. Data collected by the AMS provides valuable insights into individual cow health and productivity, allowing farmers to make informed management decisions.
Imagine a clean, modern dairy barn. A sleek, robotic arm extends gracefully from a stainless-steel unit, gently approaching a cow. Sensors precisely identify the cow’s udder, and the robotic arm deftly attaches the milking cups. The process is quiet and efficient, minimizing stress on the animal. A large display screen shows real-time data on milk yield, somatic cell count (indicating udder health), and other vital information. This system, while expensive, allows farmers to increase milk production, improve animal welfare, and reduce labor demands. However, the initial investment cost, coupled with the need for specialized training and maintenance, remains a significant limitation for many smaller farms.
Wrap-Up
The robotic revolution in food production isn’t just a futuristic fantasy; it’s happening now. From field to fork, robots are streamlining processes, boosting efficiency, and paving the way for a more sustainable food future. While challenges remain, the potential benefits are undeniable – a more abundant, safer, and tastier food supply for everyone. So, next time you enjoy a perfectly ripe piece of fruit or a juicy burger, remember the robots working behind the scenes to make it happen.