How Robotics is Improving the Efficiency of the Food Supply Chain? It’s a question that’s shaking up the entire industry. From farm to fork, robots are streamlining operations, boosting output, and making our food safer and more sustainable. Forget clunky, slow processes – think lightning-fast harvesting, precise sorting, and automated delivery. This isn’t science fiction; it’s the future of food, and it’s happening now.
This revolution spans the entire food supply chain. Imagine robots delicately picking strawberries, AI-powered systems sorting produce with laser precision, and automated guided vehicles zipping through warehouses delivering goods. This isn’t just about efficiency; it’s about minimizing waste, ensuring food safety, and ultimately, getting fresher, better food to your table faster.
Automation in Harvesting and Processing
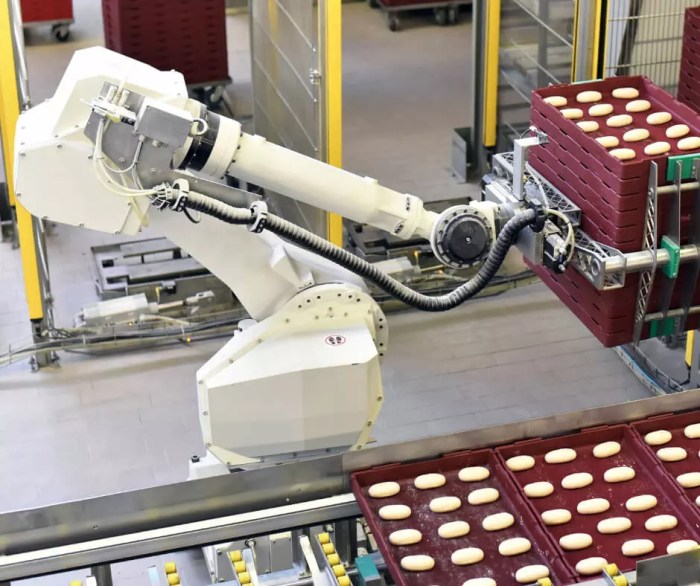
Source: tera-automation.com
Robotics is revolutionizing food production, from automated harvesting to precise packaging. This efficiency boost extends beyond the farm; imagine the impact on delivery with fewer delays caused by human error. The same technological advancements driving this change are also shaping the future of transportation, as explored in this insightful article on The Future of Autonomous Vehicles in Reducing Traffic Accidents , meaning faster, more reliable food transport and less spoilage.
Ultimately, this interconnectedness of tech promises a smoother, more efficient food supply chain.
The food supply chain, from farm to table, is a complex network demanding efficiency and resilience. Automation, driven by robotics, is revolutionizing this process, addressing labor shortages, minimizing waste, and improving overall productivity. This section explores the specific applications of robotics in harvesting and processing, highlighting the significant improvements they bring to the industry.
Robotic Harvesting Across Diverse Crops
The deployment of robots in harvesting varies greatly depending on the crop’s characteristics. While fully autonomous harvesting remains a challenge for many delicate fruits and vegetables, significant progress is being made. The following table illustrates the current state of robotic harvesting across different crop types:
Crop Type | Robot Type | Task Performed | Efficiency Improvement |
---|---|---|---|
Strawberries | Vision-guided robotic arm with soft grippers | Picking ripe strawberries, avoiding unripe or damaged ones | Increased picking speed by 30-50%, reduced labor costs, improved fruit quality |
Lettuce | Autonomous harvesting vehicle with cutting and conveying systems | Cutting and harvesting heads of lettuce | Higher harvesting rates compared to manual labor, reduced labor costs, consistent harvesting height |
Grains (wheat, barley) | Self-propelled combine harvesters with automated header control | Harvesting grains, threshing, and separating grain from straw | Increased harvesting speed, reduced fuel consumption, improved grain quality through precise cutting |
Apples | Robotic arm with advanced sensors and grasping mechanisms | Identifying and picking ripe apples | Reduced labor costs, minimized fruit damage during harvesting, potential for selective harvesting based on quality |
Automated Sorting and Grading Systems
Automated sorting and grading systems utilize computer vision, sensors, and robotic manipulators to categorize and classify harvested produce based on size, shape, color, and other quality parameters. This significantly reduces waste by identifying and separating damaged or substandard products from those meeting market standards. For example, systems employing near-infrared spectroscopy can detect internal defects in fruits and vegetables invisible to the naked eye, ensuring only high-quality products are packaged and shipped. The result is reduced waste, improved product consistency, and enhanced consumer satisfaction. One example is a robotic system used in potato processing plants that sorts potatoes by size and shape with high accuracy, reducing manual labor and improving efficiency.
Robotics in Post-Harvest Handling
Robotics plays a crucial role in minimizing human labor in post-harvest handling, encompassing washing, packaging, and palletizing. These processes are often repetitive, labor-intensive, and prone to human error. Robotic systems offer a solution, improving efficiency and consistency while enhancing hygiene and safety.
This simplified flowchart illustrates the process improvements achieved through robotic automation in post-harvest handling:
(Imagine a flowchart here. It would begin with “Harvested Produce,” then branch to “Washing (Robotic Wash System),” then to “Sorting/Grading (Automated System),” then to “Packaging (Robotic Arm & Packaging Machine),” finally to “Palletizing (Robotic Palletizer)” and ending with “Ready for Distribution.”) The robotic systems at each stage significantly increase throughput, reduce labor costs, and maintain consistent quality and hygiene.
Robotics in Warehousing and Logistics
The food supply chain, a complex network of farms, processing plants, and distribution centers, relies heavily on efficient warehousing and logistics. Robotics is revolutionizing this sector, streamlining operations and minimizing waste. From automated guided vehicles navigating vast warehouse spaces to robotic arms meticulously picking and packing orders, the impact is significant and far-reaching. This section delves into the specific roles of various robotic systems in enhancing warehouse efficiency within the food industry.
Automated Guided Vehicles (AGVs) versus Autonomous Mobile Robots (AMRs)
The choice between AGVs and AMRs depends heavily on the specific needs of a food warehouse. Both are crucial in automating material handling, but they differ significantly in their operational flexibility and capabilities. The following comparison highlights their key distinctions:
- Automated Guided Vehicles (AGVs): These robots follow pre-programmed paths, often relying on wires, magnetic tapes, or laser guidance systems. They are highly efficient in structured environments with predictable routes, making them ideal for repetitive tasks like transporting pallets along fixed pathways within a warehouse. However, their inflexibility makes them less adaptable to changing warehouse layouts or unexpected obstacles.
- Autonomous Mobile Robots (AMRs): AMRs utilize advanced sensors and artificial intelligence to navigate dynamically. They can adjust their routes in real-time to avoid obstacles, respond to changing conditions, and even learn from their experiences. This adaptability makes them more versatile than AGVs, especially in dynamic environments where warehouse layouts might frequently change or where unexpected obstacles are common. However, their sophisticated technology often translates to higher initial investment costs.
Enhancing Food Safety and Quality Control
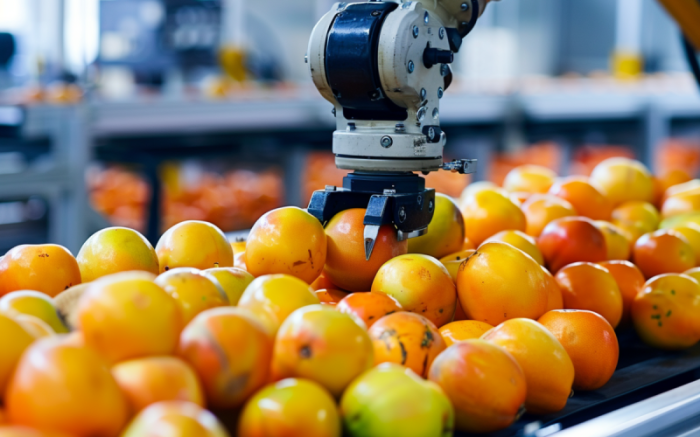
Source: frozenet.com
Robotics is revolutionizing food safety and quality control, moving beyond simple automation to deliver unprecedented levels of precision and hygiene. The integration of robotic systems across the food supply chain minimizes human error, enhances traceability, and ultimately protects consumers from foodborne illnesses. This results in a more efficient and safer food production process, benefiting both producers and consumers.
Robotic Vision Systems in Food Inspection
Robotic vision systems are playing a crucial role in detecting defects, contaminants, and foreign objects in food products. These systems utilize advanced image processing techniques and machine learning algorithms to analyze images captured by cameras, identifying even subtle imperfections that might be missed by human inspectors. This leads to improved product quality and reduced waste. The speed and accuracy of these systems far surpasses human capabilities, enabling faster processing speeds and higher throughput.
Robotic Vision Technologies and Applications
The following table compares different robotic vision technologies used in food inspection:
Technology | Application | Advantages | Limitations |
---|---|---|---|
2D Machine Vision | Defect detection (bruises, discoloration), foreign object detection (metal, glass, plastic) in fruits, vegetables, and packaged goods. | Cost-effective, relatively easy to implement. | Limited to surface inspection, struggles with complex 3D objects. |
3D Machine Vision (Structured Light, Time-of-Flight) | Shape analysis, accurate dimensional measurements, detection of internal defects in produce. | Provides complete 3D information, better for complex objects. | Higher cost, more complex implementation. |
Hyper-spectral Imaging | Detection of contaminants (bacteria, pesticides), internal bruising in produce, identification of food spoilage. | Detects subtle variations in chemical composition. | High cost, complex data analysis. |
Robotic Systems for Hygiene and Sanitation
Maintaining stringent hygiene and sanitation standards is paramount in food processing. Robotic systems are increasingly used for cleaning and disinfection tasks, ensuring consistent and thorough cleaning that minimizes the risk of contamination. These robots can access hard-to-reach areas, operate continuously, and maintain consistent cleaning parameters, leading to a safer and more efficient cleaning process.
Specific robotic cleaning methods include automated floor scrubbers, robotic arms for high-pressure washing of equipment, and UV-C disinfection robots that eliminate bacteria and viruses on surfaces. For example, companies like Xenex Disinfection Services utilize UV-C robots to disinfect hospital rooms and are expanding into food processing facilities.
Robotics in Ensuring Traceability and Reducing Foodborne Illness Risk
Robotic systems contribute significantly to product traceability, a key element in preventing and managing foodborne illnesses. By tracking products throughout their journey, from farm to table, companies can quickly identify the source of contamination in case of an outbreak. This involves integrating robotic systems with tracking technologies like RFID tags and barcodes. Robots can efficiently apply these tags, scan them for verification, and record data throughout the process.
Product Traceability System Diagram
Imagine a system where robotic arms place RFID tags on individual produce items at the harvesting stage. These items are then transported on conveyor belts monitored by robotic vision systems, which verify the tags and record location data. At processing facilities, robots sort and package the products, updating the traceability database with each step. Finally, this data is accessible to consumers through a QR code on the packaging, providing complete transparency regarding the product’s journey. This detailed tracking allows for swift identification and removal of contaminated batches, minimizing the impact of potential outbreaks. A simplified representation of this would be a flowchart showing the movement of products through the system, with each stage showing the role of robotics in data acquisition and tracking.
Impact on Sustainability and Resource Management: How Robotics Is Improving The Efficiency Of The Food Supply Chain
The integration of robotics into the food supply chain isn’t just about boosting efficiency; it’s also a powerful tool for fostering sustainability and responsible resource management. By automating tasks and optimizing processes, robotics significantly reduces environmental impact across the entire food production and distribution network, from farm to table. This translates to lower energy consumption, minimized waste, and more efficient use of precious resources like water.
Robotic systems are proving to be crucial in minimizing environmental footprints throughout the food supply chain. Their precision and efficiency lead to demonstrable improvements in energy and resource usage, contributing significantly to a more sustainable food future.
Energy Efficiency and Waste Reduction, How Robotics is Improving the Efficiency of the Food Supply Chain
Energy-efficient robotic systems play a vital role in reducing the overall energy consumption of the food industry. For example, automated harvesting robots, equipped with sensors and AI, can selectively pick ripe produce, minimizing energy waste associated with harvesting entire fields regardless of ripeness. Similarly, robotic sorting systems use less energy than manual sorting, as they operate with precision and require less labor-intensive processes. Furthermore, the use of autonomous vehicles in transportation reduces idling time and optimizes routes, leading to significant fuel savings. Consider a scenario where a fleet of traditional delivery trucks covers a route with unnecessary detours and stops, consuming more fuel. In contrast, a fleet of autonomous vehicles, guided by sophisticated route optimization algorithms, will cover the same distance with significantly fewer fuel requirements. This translates to a substantial reduction in greenhouse gas emissions.
Water Conservation in Agriculture
Robotics is making significant contributions to sustainable agricultural practices, particularly in water conservation. Robotic irrigation systems, equipped with sensors and data analytics, monitor soil moisture levels in real-time and deliver water only where and when it’s needed. This precision irrigation significantly reduces water waste compared to traditional flood irrigation methods. Studies have shown that robotic irrigation systems can achieve water savings of up to 40% in certain crops, depending on the climate and soil conditions. For instance, in arid regions where water scarcity is a major concern, these systems are transforming farming practices, ensuring efficient water use without compromising crop yields. This data highlights the potential for substantial water savings on a larger scale through widespread adoption of robotic irrigation.
Optimized Transportation and Reduced Fuel Consumption
Robotics is revolutionizing food transportation, leading to optimized routes and reduced fuel consumption. Traditional delivery routes often involve multiple stops, detours, and inefficient scheduling. Imagine a map showing a complex, meandering route with numerous stops and backtracks representing a traditional delivery system. Now, contrast that with a streamlined, direct route with minimal stops, representing a robotics-optimized delivery system. This optimized route, planned by sophisticated algorithms using real-time traffic data and route optimization software, is a clear representation of the efficiency gains achieved through robotics. Autonomous delivery vehicles, guided by GPS and AI, can navigate efficiently, minimizing fuel consumption and reducing delivery times. The reduction in fuel consumption directly translates to lower carbon emissions and a smaller environmental footprint. This efficiency not only benefits the environment but also reduces transportation costs for businesses.
Last Recap
The integration of robotics into the food supply chain isn’t just a trend; it’s a necessity. As global populations grow and demand for food increases, the need for efficient, sustainable, and safe food production becomes paramount. Robotics offers a powerful solution, addressing challenges from labor shortages to waste reduction. While challenges remain, the future of food is undeniably robotic, promising a more efficient, sustainable, and ultimately, delicious food system for all.