How Robotics is Improving the Efficiency of Industrial Supply Chains? Forget slow, clunky processes – robots are revolutionizing everything from warehousing to manufacturing. We’re talking automated guided vehicles zipping through warehouses, robotic arms assembling products with lightning speed, and AI-powered predictive maintenance slashing downtime. This isn’t science fiction; it’s the future of efficiency, and it’s happening now.
This deep dive explores how robots are streamlining industrial supply chains, boosting productivity, and reducing costs. We’ll cover everything from the nitty-gritty of warehouse automation to the broader implications for supply chain management, and even peek into a future where human-robot collaboration is the norm. Get ready to witness the robotic takeover – in the best way possible.
Introduction
Industrial supply chains, the intricate networks responsible for getting goods from raw materials to end consumers, are the lifeblood of modern economies. Traditionally, these chains involve a complex interplay of sourcing, manufacturing, warehousing, transportation, and distribution, often spanning continents and involving numerous suppliers, manufacturers, and retailers. Each stage presents its own set of challenges, from managing inventory and ensuring timely delivery to navigating geopolitical complexities and fluctuating demand. The integration of robotics is revolutionizing how these chains operate, offering the potential for unprecedented efficiency and resilience.
Robotics are being incorporated into various stages of the industrial supply chain, streamlining operations and enhancing productivity. This integration isn’t just about replacing human workers; it’s about augmenting human capabilities and tackling tasks that are dangerous, repetitive, or require high precision. This leads to significant improvements in speed, accuracy, and overall efficiency, ultimately reducing costs and improving customer satisfaction.
Types of Robots in Industrial Supply Chains
Several types of robots are transforming industrial supply chains. Articulated robots, with their multiple joints and axes of movement, are widely used in manufacturing for tasks like welding, painting, and assembly. SCARA robots, known for their speed and precision, excel in pick-and-place operations, frequently seen in electronics assembly and packaging. Collaborative robots, or “cobots,” are designed to work safely alongside human workers, assisting with tasks that require both human dexterity and robotic strength and consistency. Automated guided vehicles (AGVs) and autonomous mobile robots (AMRs) are revolutionizing material handling within warehouses and factories, autonomously transporting goods between different stages of the production process. Finally, drone technology is increasingly used for inventory management, inspection, and even delivery in certain contexts.
Challenges Faced by Industrial Supply Chains
Industrial supply chains currently face a multitude of challenges. These include unpredictable global events (like pandemics or natural disasters) that disrupt supply and demand, increasing labor costs and shortages, growing consumer expectations for faster and more personalized delivery, and the need for increased sustainability and reduced environmental impact. Furthermore, managing complex inventory across multiple locations, ensuring product quality and traceability, and optimizing logistics to minimize costs and delivery times remain persistent hurdles. Robotics offer a powerful tool to address many of these challenges, but their successful implementation requires careful planning, investment, and integration with existing systems. For example, the initial investment in robotic systems can be substantial, and there’s a need for skilled personnel to operate and maintain them. Furthermore, the integration of robots into existing workflows requires careful consideration to avoid disruptions and ensure seamless operation.
Robotics Enhancing Warehouse and Logistics Operations
The integration of robotics into warehouse and logistics operations is revolutionizing efficiency and productivity, allowing businesses to streamline processes, reduce costs, and meet the ever-increasing demands of e-commerce and global supply chains. This transformation is driven by advancements in automation technology, making sophisticated robotic systems more accessible and cost-effective than ever before.
Automated Guided Vehicles (AGVs) in Warehouse Efficiency
Automated Guided Vehicles (AGVs) are transforming warehouse operations by autonomously transporting materials throughout the facility. These vehicles, guided by various technologies like magnetic strips, laser scanners, or vision systems, navigate pre-programmed routes, eliminating the need for manual forklift operation and significantly reducing transportation times. AGVs can operate 24/7, increasing throughput and optimizing warehouse space utilization. Their precise movements minimize the risk of collisions and damage, leading to a safer working environment. Furthermore, real-time tracking capabilities provided by AGV systems allow for efficient inventory management and improved order fulfillment. For instance, a large distribution center using a fleet of AGVs could see a 30% reduction in transportation time compared to manual methods, directly impacting order processing speed.
Robotic Arms in Picking, Packing, and Palletizing
Robotic arms, equipped with advanced sensors and grippers, are increasingly prevalent in warehouse automation. These robotic systems perform repetitive tasks such as picking individual items from shelves, packing them into boxes, and palletizing finished goods for shipment. Their precision and speed far surpass human capabilities, especially in handling delicate or irregularly shaped items. The use of robotic arms reduces errors associated with manual handling, minimizes product damage, and enhances overall order accuracy. For example, a robotic arm in a fulfillment center can pick and pack hundreds of items per hour with consistent accuracy, significantly outperforming human workers in terms of speed and precision, especially during peak seasons.
Robotic Systems vs. Manual Labor in Warehouse Tasks: A Comparison
The efficiency gains from robotic systems are substantial when compared to manual labor. While initial investment costs are higher, the long-term return on investment (ROI) is often significant due to increased throughput, reduced labor costs, and minimized errors.
Metric | Human Performance | Robotic Performance |
---|---|---|
Speed (items/hour) | 50-100 (variable based on task complexity and fatigue) | 150-300+ (consistent speed) |
Accuracy (%) | 95-98% (prone to error due to fatigue and human variability) | 99.5%+ (high consistency and precision) |
Cost (per item processed) | Variable, influenced by wages, benefits, and training | Initially high, but decreases over time due to reduced labor costs and increased throughput |
Error Rate | Higher, leading to potential returns and customer dissatisfaction | Significantly lower, resulting in improved customer satisfaction |
Hypothetical Warehouse Layout and Workflow Incorporating Robotic Systems
Imagine a large warehouse divided into zones. The receiving zone utilizes AGVs to transport incoming pallets to designated storage areas. Robotic arms in the picking zone retrieve items from shelves based on order specifications. Conveyor belts transport the picked items to the packing zone, where other robotic arms package them into boxes. Finally, AGVs move the packaged goods to the shipping zone for dispatch. This automated workflow minimizes human intervention in repetitive tasks, maximizing efficiency and throughput. Real-time inventory management systems track the location and status of every item throughout the process, providing complete visibility and control. The warehouse layout would be optimized to minimize travel distances for AGVs and robotic arms, further improving efficiency.
Improving Manufacturing Processes with Robotics
The integration of robotics into manufacturing has revolutionized production lines, boosting efficiency and precision across various industries. From the automotive sector to the delicate world of electronics assembly, robots are no longer futuristic fantasies but essential tools driving progress and profitability. Their impact spans increased speed, reduced errors, and the ability to handle tasks previously deemed too dangerous or complex for human workers.
Robotic systems are transforming manufacturing processes, enhancing productivity, and improving product quality. This is achieved through automation of repetitive tasks, increased precision, and the ability to work continuously without fatigue, leading to significant cost savings and competitive advantages.
Robotic Welding and Painting in Automotive Manufacturing
The automotive industry has been a pioneer in adopting robotics, particularly for welding and painting. Robotic welding arms offer unparalleled precision and consistency, resulting in stronger, more reliable welds compared to manual welding. They can execute complex welds with speed and accuracy, reducing the risk of human error and ensuring consistent quality across a large production volume. Similarly, robotic painting systems deliver a uniform coat of paint, minimizing waste and improving the final aesthetic appeal of vehicles. These systems are programmable to handle various paint types and application techniques, adapting to different vehicle models and designs. The consistent application also reduces the need for touch-ups, further enhancing efficiency.
Robotic Assembly Lines Increase Production Speed and Reduce Defects, How Robotics is Improving the Efficiency of Industrial Supply Chains
Robotic assembly lines are the backbone of modern high-volume manufacturing. These lines consist of a coordinated network of robots performing specific tasks in a sequential manner, from picking and placing components to tightening screws and performing quality checks. The speed and precision of robotic systems significantly increase production rates, allowing manufacturers to meet higher demands and reduce lead times. Moreover, the consistency of robotic actions minimizes defects and ensures higher product quality. The elimination of human error in repetitive tasks translates directly to improved yield and reduced waste. For example, in the assembly of consumer electronics, robots can handle delicate components with precision, reducing the likelihood of damage during assembly.
Robots in Precision Manufacturing: Electronics Assembly
The electronics industry, with its demand for intricate and delicate assembly, heavily relies on robots for precision manufacturing. Robots are adept at handling minuscule components and performing complex assembly tasks with a level of accuracy far exceeding human capabilities. This is crucial in the production of smartphones, computers, and other electronic devices, where even minor errors can have significant consequences. Robots can perform tasks such as soldering, component placement, and testing with exceptional precision, ensuring the quality and reliability of the final product. The use of vision systems integrated with robots further enhances accuracy, allowing for real-time adjustments and quality control.
The implementation of robots in manufacturing presents a multitude of advantages and disadvantages. Careful consideration of both aspects is crucial for successful integration.
Robotics are revolutionizing industrial supply chains, optimizing warehousing and streamlining logistics. This efficiency boost mirrors advancements in other sectors; for instance, the application of AI in healthcare is similarly transformative, as seen in The Role of AI in Streamlining Administrative Processes in Healthcare , which tackles administrative bottlenecks. Ultimately, both fields show how automation is key to boosting productivity and reducing operational costs.
- Advantages: Increased production speed, improved product quality and consistency, reduced defects, enhanced safety for workers (handling dangerous tasks), reduced labor costs (in the long term), increased flexibility and adaptability to changing production needs, improved efficiency in material handling and logistics.
- Disadvantages: High initial investment costs, need for skilled technicians for maintenance and programming, potential job displacement for human workers, dependency on power and reliable infrastructure, limited adaptability to certain tasks requiring high levels of dexterity or problem-solving abilities.
Supply Chain Optimization through Predictive Maintenance
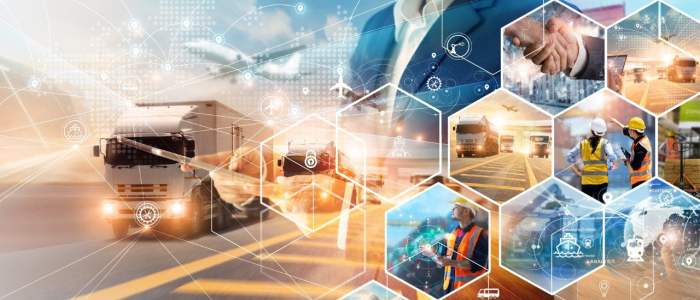
Source: primerobotics.com
Predictive maintenance, powered by the synergy of robotics, sensors, and data analytics, is revolutionizing industrial supply chains. It moves beyond reactive repairs triggered by breakdowns, offering a proactive approach that minimizes downtime and maximizes operational efficiency. This shift towards anticipating and preventing equipment failures translates to significant cost savings and enhanced overall supply chain resilience.
By integrating smart sensors into robotic systems and leveraging advanced data analytics, businesses gain unprecedented insights into the health and performance of their equipment. This allows for the precise prediction of potential failures, enabling timely interventions before they disrupt operations.
Robotic Systems in Predictive Maintenance
Robotic systems are becoming indispensable tools in predictive maintenance. Their ability to access hard-to-reach areas, perform repetitive tasks with precision, and operate continuously makes them ideal for routine inspections and minor repairs. For instance, a robotic arm equipped with advanced vision systems can inspect conveyor belts for wear and tear, identifying potential issues before they escalate into major breakdowns. Similarly, robots can perform automated lubrication, tightening of bolts, and other preventative maintenance tasks, reducing the need for human intervention in hazardous or physically demanding environments. This ensures consistent maintenance standards and minimizes human error.
Downtime Reduction and Efficiency Gains
The implementation of predictive maintenance using robotics directly impacts a company’s bottom line. By anticipating and preventing equipment failures, businesses drastically reduce unplanned downtime. This translates to significant cost savings, as lost production time and emergency repairs are minimized. Consider a large manufacturing facility: A single hour of unplanned downtime on a critical production line can cost thousands of dollars in lost output. Predictive maintenance, leveraging robotics, can reduce such downtime by as much as 40%, leading to substantial improvements in operational efficiency and profitability. For example, a company using predictive maintenance with robotic systems might see a reduction in machine downtime from an average of 10 hours per month to 6 hours, resulting in a 40% improvement in productivity.
Predictive Maintenance Process Flowchart
The process of predictive maintenance using robotics can be visualized through a simple flowchart:
1. Data Acquisition: Sensors embedded in equipment collect real-time data on vibration, temperature, pressure, and other relevant parameters.
2. Data Transmission: This data is transmitted wirelessly to a central data processing system.
3. Data Analysis: Advanced algorithms and machine learning models analyze the data to identify patterns and predict potential failures.
4. Maintenance Scheduling: Based on the predictions, a maintenance schedule is automatically generated.
5. Robotic Intervention: Robotic systems are dispatched to perform the necessary inspections or repairs as per the schedule.
6. Performance Monitoring: Post-maintenance, the system monitors the equipment’s performance to verify the effectiveness of the intervention. The entire cycle then repeats, continuously refining predictions and improving maintenance efficiency.
The Impact of Robotics on Inventory Management and Tracking: How Robotics Is Improving The Efficiency Of Industrial Supply Chains
Forget the days of endless manual stock checks and inaccurate inventory counts. Robotics is revolutionizing inventory management, bringing unprecedented levels of efficiency and accuracy to warehouses and distribution centers worldwide. Automated systems are transforming how businesses track, manage, and optimize their inventory, leading to significant cost savings and improved operational efficiency. This section explores how robots are reshaping inventory management and its impact on the modern supply chain.
Robots are no longer just futuristic fantasies; they’re actively streamlining inventory processes, from receiving shipments to fulfilling orders. This increased automation minimizes human error, optimizes storage space, and provides real-time visibility into inventory levels, allowing businesses to make data-driven decisions about procurement and production.
Automated Inventory Tracking and Management
Automated Guided Vehicles (AGVs) and Autonomous Mobile Robots (AMRs) are transforming warehouse operations. AGVs follow pre-programmed routes, efficiently moving goods between storage locations and picking stations. AMRs, on the other hand, use advanced sensors and AI to navigate dynamically, adapting to changing warehouse layouts and avoiding obstacles. These robots significantly reduce the time and labor required for inventory movement, leading to faster order fulfillment and improved overall efficiency. For example, a large e-commerce company might use a fleet of AMRs to transport picked items from storage to packing stations, significantly speeding up the shipping process and reducing order fulfillment times.
Reducing Storage Costs and Waste through Automated Systems
Automated storage and retrieval systems (AS/RS) optimize warehouse space utilization. These systems use robots to automatically retrieve and store items in high-density storage racks, maximizing storage capacity and minimizing wasted space. This efficient use of space directly translates to lower storage costs. Furthermore, automated inventory management systems minimize the risk of stockouts and overstocking, reducing waste from obsolete or expired goods. Imagine a pharmaceutical company using an AS/RS to manage temperature-sensitive medications; the precise control and efficient storage offered by the system prevents spoilage and ensures product quality.
Improved Accuracy in Inventory Counts and Order Fulfillment
Robotics drastically improves the accuracy of inventory counts. Traditional manual counting is prone to errors, leading to inaccurate stock levels and potential stockouts or overstocking. Robotic systems, equipped with barcode scanners or RFID readers, accurately track each item’s location and quantity in real-time. This ensures that inventory records are always up-to-date and accurate, minimizing discrepancies and improving order fulfillment accuracy. A clothing retailer, for instance, could utilize robotic systems to conduct regular inventory scans, ensuring accurate stock levels for online and in-store sales, thereby preventing customer dissatisfaction due to out-of-stock items.
Real-Time Data for Inventory Level Optimization
The real-time data generated by robotic inventory systems provides valuable insights into inventory levels and demand patterns. This data allows businesses to optimize inventory levels, minimizing storage costs while ensuring sufficient stock to meet customer demand. Predictive analytics, combined with robotic data, can forecast future demand, enabling proactive inventory management and preventing stockouts. For example, a food distributor could use real-time data from robotic inventory systems to anticipate spikes in demand during holidays, ensuring sufficient stock to meet customer orders without overstocking and incurring unnecessary storage costs.
Addressing the Challenges of Robotics Implementation
Integrating robots into supply chains offers immense potential, but it’s not a seamless transition. The journey involves navigating significant hurdles, from substantial upfront investments to the need for a skilled workforce and ethical considerations surrounding automation’s impact on employment. Understanding these challenges is crucial for successful implementation and reaping the rewards of robotic automation.
The introduction of robotics into existing supply chain infrastructure presents a multifaceted challenge. It’s not simply a matter of purchasing robots and plugging them in; successful implementation requires careful planning, significant investment, and a comprehensive understanding of the potential disruptions and adjustments needed across the entire operation. This includes not only the technical aspects of integration but also the human element, encompassing workforce training and addressing potential job displacement concerns.
High Initial Investment Costs
Implementing robotic systems demands considerable upfront capital expenditure. Robots themselves are expensive, and the costs extend beyond the purchase price. Integration necessitates specialized software, infrastructure modifications (like reinforced flooring or power upgrades), and ongoing maintenance. For smaller businesses or those with limited budgets, this can be a significant barrier to entry. For example, a single advanced robotic arm capable of complex tasks can cost tens of thousands of dollars, and the associated infrastructure upgrades can easily add another substantial amount. This high initial cost requires careful financial planning and a thorough return on investment (ROI) analysis to justify the expense.
The Need for Skilled Labor
While robots automate many tasks, they don’t eliminate the need for human expertise. Instead, they shift the demand towards specialized skills. Operating, maintaining, and programming robots requires a workforce trained in robotics engineering, programming, and maintenance. Finding and retaining this skilled labor can be difficult, particularly in regions with limited access to relevant educational programs. The lack of a skilled workforce can lead to downtime, increased maintenance costs, and reduced efficiency, undermining the very benefits robots are intended to provide. Companies often need to invest in comprehensive training programs for existing employees or recruit specialized talent from outside their region.
Ethical Considerations of Job Displacement
Automation, while boosting efficiency, inevitably raises concerns about job displacement. As robots take over repetitive or dangerous tasks, some jobs may become redundant. This necessitates proactive measures to mitigate the negative impacts on workers. Retraining programs, offering opportunities for employees to acquire new skills suitable for roles supporting robotic systems, are essential. Open communication and transparent strategies to manage workforce transitions are crucial to maintain employee morale and avoid social unrest. Companies should consider a phased approach to automation, allowing for gradual integration and retraining, minimizing the immediate impact on employment. For example, a company might first implement robots for specific tasks before gradually expanding their use, giving employees time to adapt and acquire new skills.
Cost-Benefit Analysis of Robotic Implementation
The following table provides a simplified overview of the costs and benefits of robotic implementation across different supply chain segments. Note that these figures are highly variable and depend on factors like the specific robot used, the scale of implementation, and the existing infrastructure.
Supply Chain Segment | Costs | Benefits |
---|---|---|
Warehousing | Robot purchase, integration, software, training, maintenance | Increased throughput, reduced labor costs, improved accuracy, less damage to goods |
Manufacturing | Robot purchase, integration, programming, specialized tooling, safety measures | Higher production rates, improved product quality, reduced waste, enhanced worker safety |
Transportation & Logistics | Autonomous vehicle purchase, infrastructure adaptation (e.g., charging stations), software development, safety systems | Reduced transportation costs, improved delivery times, increased efficiency, enhanced tracking capabilities |
The Future of Robotics in Industrial Supply Chains
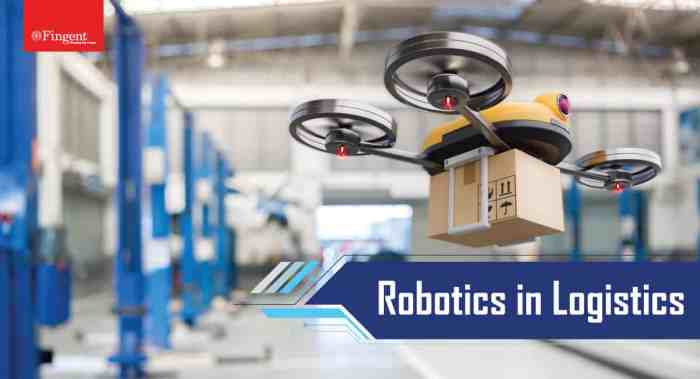
Source: fingent.com
The integration of robotics into industrial supply chains is still in its relatively early stages, but the potential for future advancements is staggering. We’re on the cusp of a revolution where increasingly sophisticated robots, guided by powerful AI and machine learning algorithms, will reshape every aspect of how goods are moved, stored, and delivered. This transformation will not only enhance efficiency but also redefine the very nature of work within the supply chain ecosystem.
Emerging technologies are poised to dramatically accelerate this evolution. The convergence of robotics with artificial intelligence and machine learning will create autonomous systems capable of far greater adaptability and problem-solving capabilities than currently exist. This means robots that can learn from their experiences, optimize their own processes, and even anticipate potential disruptions in the supply chain before they occur. Furthermore, the rise of collaborative robots, or “cobots,” designed to work safely alongside human employees, will lead to more efficient and flexible workflows.
Increased Human-Robot Collaboration
The future of robotics in industrial supply chains is not about replacing humans, but rather augmenting their capabilities. Cobots, equipped with advanced sensors and AI-powered decision-making systems, will handle repetitive or physically demanding tasks, freeing up human workers to focus on more complex and strategic roles. Imagine warehouse workers collaborating with robots to quickly and accurately pick, pack, and ship orders, with the robots handling the heavy lifting and repetitive movements while humans oversee quality control and manage exceptions. This collaborative approach will leverage the strengths of both humans and machines, resulting in a more productive and safer working environment. For example, companies like Amazon are already heavily investing in robotic systems that work alongside human employees in their fulfillment centers.
Future Impact on Supply Chain Design and Management
The widespread adoption of robotics will fundamentally alter how supply chains are designed and managed. Real-time data analytics, powered by AI and machine learning, will allow for predictive modeling of demand, optimizing inventory levels, and proactively addressing potential disruptions. This will lead to leaner, more agile, and resilient supply chains capable of responding quickly to changes in market demand and unforeseen events. Supply chain networks may become more decentralized, with smaller, more localized fulfillment centers supported by automated systems. The design of warehouses and manufacturing facilities will also change, optimized for seamless human-robot interaction and efficient material flow.
A Vision of a Fully Automated Supply Chain
Imagine a future where a self-driving truck autonomously transports goods from a factory equipped with robotic assembly lines. Along the way, AI-powered systems monitor the cargo’s condition and predict potential delays, automatically adjusting the route and delivery schedule. Upon arrival at a fully automated warehouse, robotic arms unload the goods and place them into designated storage locations using advanced vision systems. Orders are processed instantly by AI-powered algorithms, and robots pick, pack, and label items with flawless precision. Finally, another self-driving vehicle delivers the package directly to the customer, all with minimal human intervention. This highly efficient and optimized system minimizes waste, reduces lead times, and ensures unparalleled reliability. While a fully automated system is still some years away, elements of this vision are already being implemented in various sectors, paving the way for a future of seamless, automated supply chains.
Final Summary
The integration of robotics into industrial supply chains isn’t just about faster production; it’s a fundamental shift towards smarter, more resilient, and cost-effective operations. From optimized inventory management to predictive maintenance, robots are tackling some of the biggest challenges facing modern businesses. While challenges remain – like the need for skilled labor and ethical considerations around automation – the potential benefits are undeniable. The future of industrial supply chains is robotic, and it’s looking incredibly efficient.