How Robotics is Improving Industrial Efficiency and Safety? Forget clunky assembly lines and repetitive strain injuries – robots are revolutionizing industry, boosting productivity, and making workplaces safer. From precision welding to automated quality checks, the impact of robotic automation is undeniable. This isn’t just about replacing humans; it’s about enhancing capabilities and creating a smarter, more efficient future for manufacturing and beyond.
We’re diving deep into how robots are tackling hazardous tasks, minimizing human error, and optimizing resource management. Get ready to explore the exciting world of industrial robotics and its transformative power – because the future of work is automated, and it’s looking pretty bright.
Increased Productivity through Automation
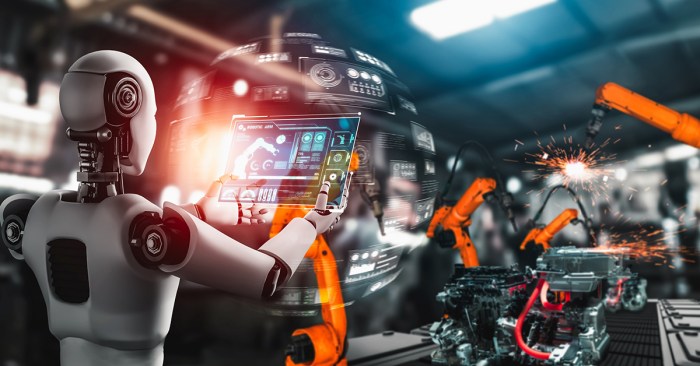
Source: edu.in
Robotic automation is revolutionizing industrial efficiency, significantly boosting productivity and reshaping the manufacturing landscape. By taking over repetitive, strenuous, and often dangerous tasks, robots free up human workers to focus on more complex and strategic roles, ultimately leading to a more productive and safer work environment. This increased efficiency translates directly into higher output and improved profitability for businesses.
The core benefit lies in robotic automation’s ability to streamline repetitive tasks. These tasks, while crucial to production, often lead to worker fatigue, errors, and even injuries. Robots, however, perform these tasks consistently, tirelessly, and with exceptional precision, dramatically reducing errors and increasing output. This is particularly true in high-volume manufacturing where the same operation is repeated thousands of times a day.
Examples of Robotic Automation Improving Industrial Processes
Several industrial processes have witnessed remarkable improvements thanks to robotic automation. The following table highlights some key examples, comparing the “before” and “after” scenarios and quantifying the percentage improvement achieved.
Process | Before Automation | After Automation | Percentage Improvement |
---|---|---|---|
Welding Car Bodies | Manual welding, prone to inconsistencies and worker fatigue, resulting in slower production and higher defect rates. Average production: 50 car bodies per day. | Robotic welding, providing consistent welds, higher speed, and reduced defect rate. Average production: 150 car bodies per day. | 200% |
Packaging and Palletizing | Manual handling, leading to injuries, slower processing, and higher error rates. Average processing speed: 100 units per hour. | Automated robotic systems handling, packing, and palletizing goods quickly and accurately. Average processing speed: 300 units per hour. | 200% |
Painting and Finishing | Manual painting, resulting in inconsistent coatings, higher material waste, and exposure to harmful chemicals. Average production: 200 units per day. | Robotic painting systems, delivering precise and consistent coatings, reduced material waste, and improved worker safety. Average production: 600 units per day. | 200% |
Machine Tending | Manual loading and unloading of machines, causing delays, potential for injuries, and reduced machine uptime. Average production: 1000 parts per day. | Robots seamlessly loading and unloading machines, maximizing machine uptime and significantly increasing output. Average production: 3000 parts per day. | 200% |
Impact on Production Throughput and Overall Output
The integration of robotic automation directly translates to a substantial increase in production throughput. By eliminating bottlenecks caused by manual processes and reducing error rates, robots ensure a consistent flow of work, leading to higher overall output. This increased efficiency isn’t just about producing more units; it also means improved quality, reduced waste, and ultimately, greater profitability. For example, a factory producing electronic components might see a 50% increase in daily output after implementing robotic assembly lines, directly impacting their market share and bottom line. Similarly, a manufacturing plant producing automotive parts could experience a 30% reduction in production time due to robotic welding and painting, allowing them to meet increased demand more effectively.
Enhanced Precision and Quality Control
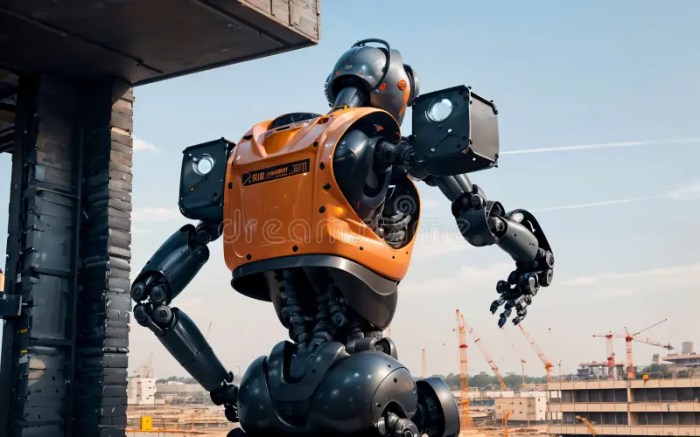
Source: dreamstime.com
Robots are revolutionizing industrial processes, not just by increasing speed and output, but also by dramatically improving the precision and consistency of manufacturing and assembly. Human error, a persistent factor in traditional production lines, is significantly minimized through the implementation of robotic systems, leading to a substantial leap in product quality and a reduction in waste.
The unwavering accuracy of robots allows for intricate tasks to be performed with a level of consistency unattainable by human workers, even the most skilled. This heightened precision translates directly into improved product quality, reduced defects, and ultimately, increased customer satisfaction.
Robotic Precision in Manufacturing and Assembly
The automotive industry provides a prime example of robotic precision’s impact. Robots are responsible for welding, painting, and assembling car bodies with incredibly tight tolerances. The consistent application of weld points, the even distribution of paint, and the precise placement of components ensure that vehicles meet stringent quality standards. Inconsistencies that might arise from human fatigue or variations in skill are eliminated, resulting in a more uniform and reliable final product. Similarly, in electronics manufacturing, robots handle the delicate placement of tiny components on circuit boards with micron-level accuracy, preventing short circuits and malfunctions. The reduction in defects translates to significant cost savings, as rework and scrap rates plummet.
Robots in Quality Inspection
Robots play a crucial role in quality inspection, going beyond simply performing tasks to actively monitoring and ensuring product quality. Traditional methods of quality control often rely on human inspectors, a process that can be time-consuming, prone to error, and inconsistent. Robotic inspection systems, however, offer speed, accuracy, and objectivity.
The implementation of robotic inspection involves several methods:
- Vision Systems: Equipped with high-resolution cameras and sophisticated image processing software, robotic vision systems can identify even minute defects, such as scratches, cracks, or inconsistencies in color or texture. These systems are used extensively in industries like food processing to inspect products for imperfections before packaging.
- Dimensional Measurement: Robots can use laser scanners, coordinate measuring machines (CMMs), and other sensors to precisely measure the dimensions of components and ensure they conform to specifications. This is particularly crucial in aerospace and automotive manufacturing, where tolerances are extremely tight.
- Non-Destructive Testing (NDT): Robots can perform NDT techniques such as ultrasonic testing or X-ray inspection to detect internal flaws in materials without damaging the product. This is essential in industries like construction and manufacturing where the integrity of materials is paramount.
For instance, in the pharmaceutical industry, robotic vision systems inspect pills for defects in shape, size, and color, ensuring that only high-quality medication reaches the market. The speed and accuracy of these systems far exceed the capabilities of human inspectors, leading to improved product quality and increased throughput. In the semiconductor industry, robotic inspection plays a critical role in identifying defects on microchips, ensuring that only functional chips are shipped to customers. The precision and speed of these systems are essential for maintaining the high quality standards required in this demanding industry.
Improved Worker Safety
Robots are revolutionizing industrial safety, stepping in to handle tasks too dangerous or strenuous for human workers. This shift not only boosts productivity but also creates a significantly safer working environment, reducing workplace accidents and fostering a healthier workforce. The benefits extend beyond simply avoiding immediate injuries; long-term health problems associated with repetitive tasks and exposure to hazardous materials are also mitigated.
Robots excel at handling hazardous industrial tasks, effectively eliminating many safety risks. Their tireless precision and unwavering adherence to safety protocols drastically reduce the likelihood of human error, a major contributor to workplace accidents.
Hazardous Task Automation and Risk Mitigation, How Robotics is Improving Industrial Efficiency and Safety
Many inherently dangerous jobs are now successfully automated. Welding, for instance, exposes workers to intense heat, bright light, and potentially harmful fumes. Robots perform these tasks with consistent precision, eliminating the risk of burns, eye damage, and respiratory problems. Similarly, tasks involving handling heavy materials, like lifting and transporting large metal components in a foundry, are prone to back injuries and musculoskeletal disorders. Robots easily manage these loads, preventing human strain and potential injury. Working in confined spaces, such as pipelines or tanks requiring inspection and maintenance, poses risks of asphyxiation or exposure to toxic substances. Robots can be deployed to these areas remotely, eliminating the direct human risk. Finally, working with explosives or highly flammable materials is another area where robots offer significant safety improvements, performing tasks with precise control and minimizing the risk of accidental detonation or fire.
Reduction of Workplace Accidents and Injuries
Robots significantly reduce workplace accidents and injuries linked to repetitive strain, heavy lifting, and exposure to harmful substances. Repetitive tasks, like assembly line work, often lead to carpal tunnel syndrome and other repetitive strain injuries (RSIs). Robots can perform these repetitive motions tirelessly without fatigue, eliminating the risk of RSIs for human workers. Heavy lifting, a major cause of back injuries and other musculoskeletal problems, is easily handled by robots capable of lifting far heavier loads than humans. Exposure to harmful substances, such as chemicals, solvents, and dust, can lead to a range of health problems, including respiratory illnesses and cancers. Robots can handle these materials, minimizing or eliminating human exposure. In the automotive industry, for example, the use of robots in painting and welding has drastically reduced the incidence of respiratory problems among workers.
Scenario: Safe Robot-Assisted Demolition
Consider a scenario involving the demolition of a dilapidated building containing asbestos. Human workers face significant risks of asbestos exposure, leading to serious lung diseases. A robot equipped with specialized tools and sensors can safely perform the demolition. The robot is remotely controlled from a safe distance, allowing for precise dismantling of the structure. Safety mechanisms include multiple redundant systems, ensuring that if one component fails, the others maintain control and prevent accidents. The robot is also equipped with sensors to monitor asbestos levels in the air, providing real-time feedback to the operator and automatically shutting down if levels exceed safe limits. Furthermore, the robot is designed to contain any asbestos dust generated during demolition, preventing its release into the environment. This robotic solution minimizes human exposure to asbestos, protecting workers from potentially fatal health consequences.
Optimized Resource Management
Robotics is revolutionizing industrial resource management, pushing beyond mere automation to achieve significant improvements in efficiency and sustainability. By precisely controlling processes and minimizing waste, robots contribute to a leaner, greener, and ultimately more profitable industrial landscape. This optimized resource management translates directly to reduced operational costs and a smaller environmental footprint.
Robots contribute to reduced material waste and improved resource utilization through precise material handling and process control. Unlike human workers, robots can consistently maintain accuracy and speed, minimizing errors that lead to scrap or rework. This precision extends to various processes, from cutting and welding to painting and assembly, leading to less material waste and improved yield. Furthermore, advanced robotic systems utilize sensors and data analytics to monitor material consumption in real-time, allowing for proactive adjustments and further optimization.
Reduced Material Waste in Manufacturing
In manufacturing, robotic systems significantly reduce material waste by improving precision in cutting, shaping, and assembling components. For example, in the automotive industry, robots perform precise welding, minimizing the amount of filler material needed and reducing the risk of defects. Similarly, in the electronics industry, robots are used for delicate tasks like placing components on circuit boards, minimizing the risk of damage and waste. This level of precision leads to higher yields and reduced production costs.
Energy Optimization in Industrial Processes
Robots contribute to energy optimization by streamlining processes and reducing energy-intensive tasks. For example, in the packaging industry, robots can optimize the arrangement of items in boxes, minimizing wasted space and reducing the need for excessive packaging materials. This translates to less fuel consumption during transportation and a reduced carbon footprint. In addition, many modern robotic systems are designed with energy efficiency in mind, incorporating features like regenerative braking and optimized motor control.
Resource Consumption Comparison: Robotic vs. Human-Operated System
Let’s compare the resource consumption of a robotic system versus a human-operated system for a simple, yet illustrative, task: pallet stacking in a warehouse.
Resource | Human-Operated System | Robotic System | Percentage Difference |
---|---|---|---|
Energy Consumption (kWh per hour) | 1.5 (estimated human metabolic energy equivalent) | 0.5 | -66.7% |
Material Waste (percentage of total materials handled) | 5% (due to errors and inefficiencies) | 1% | -80% |
Labor Costs ($ per hour) | 25 | 5 (including maintenance and depreciation) | -80% |
Time per Pallet (minutes) | 10 | 5 | -50% |
Note: These figures are estimates and can vary based on specific factors like the size and weight of the pallets, the efficiency of the human worker, and the specific robotic system used. However, they demonstrate the potential for significant resource savings through robotic automation.
Adaptability and Flexibility in Manufacturing
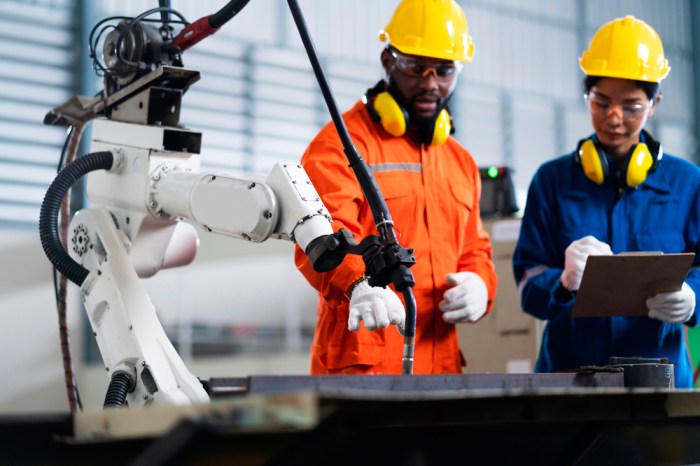
Source: blr.com
The rise of robotics isn’t just about automating repetitive tasks; it’s about creating manufacturing systems that can dance to the ever-changing tune of market demands. Robots are no longer lumbering, inflexible machines; they’re becoming incredibly adaptable partners, allowing businesses to respond swiftly to fluctuating orders and evolving product designs. This flexibility translates directly into increased efficiency, reduced waste, and a significant competitive edge.
Robots equipped with advanced software and sensor technologies are transforming the landscape of flexible manufacturing systems (FMS). These systems are designed to handle a variety of products and production volumes with minimal downtime for reconfiguration. The key is their ability to seamlessly switch between different tasks, adapting to shifting priorities without the need for extensive manual intervention. This contrasts sharply with traditional, rigid production lines which are often ill-equipped to handle sudden changes in demand or product variations.
Reprogrammable and Reconfigurable Robotic Systems
Several robotic systems exemplify this adaptability. Collaborative robots, or “cobots,” are designed to work alongside human workers, easily reprogrammed for different tasks through intuitive interfaces. Their compact size and safety features make them ideal for integrating into existing production lines without major disruptions. Similarly, modular robotic systems allow for easy reconfiguration by simply swapping out components or adding new ones. This plug-and-play approach minimizes downtime and allows manufacturers to quickly adapt to changing production needs. For instance, a system designed for assembling one type of electronic device can be quickly reconfigured to assemble another by swapping out end-effectors (the robot’s “hands”) and modifying the programming. This flexibility allows manufacturers to handle multiple product lines efficiently without needing separate, dedicated production lines for each.
Rapid Adaptation to Shifting Demand: A Hypothetical Scenario
Imagine a manufacturer producing smartwatches. Suddenly, a new, trendy color variant becomes unexpectedly popular, leading to a surge in demand. With a traditional production line, this would likely result in significant delays and lost revenue while the line is retooled. However, with a flexible robotic system, the change is seamless. The system’s central control software detects the increased demand for the new color. The robots are then reprogrammed to prioritize the production of the new variant, automatically adjusting the supply chain and material flow. This might involve changing the end-effectors to handle the new color components and updating the assembly sequence in the robot’s programming – a process that can be completed in a matter of hours, not days or weeks. The system may also automatically order additional supplies of the needed components, demonstrating the integration of the robotic system with wider supply chain management. This swift response allows the manufacturer to capitalize on the increased demand and maintain its competitive position.
Data Acquisition and Analysis for Process Improvement
Robots aren’t just tireless workers; they’re sophisticated data collectors, constantly monitoring their operations and providing insights that human workers simply can’t match. This data revolutionizes industrial processes, driving efficiency and safety to unprecedented levels. By analyzing this information, manufacturers can fine-tune their operations, predict potential problems, and ultimately, boost their bottom line.
The integration of sensors and sophisticated software allows robots to gather a wealth of information during their tasks. This data is then processed and analyzed to identify areas for improvement, leading to optimized workflows and reduced waste. Imagine a robot welding car parts; it’s not just performing the weld, it’s simultaneously recording the exact pressure, temperature, and speed used, allowing engineers to refine the process for optimal strength and consistency. This level of detail is impossible to achieve with manual labor alone.
Data-Driven Insights Leading to Efficiency Improvements
Data collected by robots reveals hidden inefficiencies and bottlenecks in industrial processes. For instance, a robotic arm in a packaging facility might record data showing that a particular type of box is consistently causing jams in the conveyor belt. This insight, derived from thousands of data points, allows for targeted improvements – perhaps a change in box design or a modification to the conveyor system – leading to significant improvements in throughput and reduced downtime. Similarly, analyzing data on robot cycle times can pinpoint slowdowns, revealing areas needing optimization, such as adjusting robot movements or improving material handling. In a large-scale manufacturing environment, even small improvements in efficiency, when multiplied across numerous cycles, can result in substantial cost savings and increased productivity. One example is a car manufacturer who, using robotic data analysis, identified a slight variation in the application of paint, leading to a reduction in material waste and an increase in the quality of the final product.
Key Data Points Collected by Industrial Robots and Their Significance
The sheer volume and variety of data collected by industrial robots is impressive. Understanding the significance of these data points is crucial for effective process improvement and safety enhancements.
Here’s a look at some key data points:
- Cycle Time: The time taken to complete a single operation. Analyzing this data helps identify bottlenecks and optimize robot movements for faster production.
- Throughput: The rate at which a robot completes tasks. This metric directly reflects overall productivity and helps identify areas for improvement.
- Error Rates: The frequency of errors or defects in the robot’s work. This data is crucial for identifying and correcting issues in the robot’s programming or the process itself, improving quality and reducing waste.
- Energy Consumption: Monitoring energy usage helps optimize robot operations for maximum efficiency and reduced environmental impact. This data can also help identify potential mechanical issues before they become major problems.
- Sensor Readings (Temperature, Pressure, Force): These readings are essential for quality control and process optimization. For example, in welding, consistent pressure and temperature readings ensure the quality of the weld.
- Maintenance Data: Data on robot maintenance, including hours of operation, error codes, and maintenance schedules, helps predict potential failures and schedule preventive maintenance, minimizing downtime.
The Future of Robotics in Industrial Settings: How Robotics Is Improving Industrial Efficiency And Safety
The integration of robotics in industrial settings is rapidly evolving, driven by advancements in artificial intelligence, machine learning, and sensor technologies. This isn’t just about faster production lines; it’s about creating smarter, safer, and more adaptable factories capable of responding to the ever-changing demands of the global market. The future promises a collaborative partnership between humans and robots, where each leverages their unique strengths to achieve unprecedented levels of efficiency and innovation.
The next generation of industrial robots will be far more sophisticated than their predecessors. We’re moving beyond pre-programmed, repetitive tasks to robots capable of learning, adapting, and making decisions in real-time. This level of autonomy will be crucial for handling increasingly complex manufacturing processes and navigating unpredictable environments.
AI and Machine Learning’s Impact on Industrial Robotics
Artificial intelligence and machine learning are revolutionizing industrial robotics, enabling robots to perform tasks previously considered impossible for automation. AI empowers robots with cognitive abilities, allowing them to analyze data, learn from experience, and improve their performance over time. Machine learning algorithms enable robots to recognize patterns, predict failures, and optimize their actions based on real-time feedback. For example, AI-powered robots can now inspect products with a level of precision far surpassing human capabilities, identifying even minute defects that could lead to product recalls. Similarly, machine learning algorithms are used to predict equipment maintenance needs, minimizing downtime and maximizing productivity. Companies like Tesla are already utilizing AI-powered robots extensively in their manufacturing processes, showcasing the transformative potential of this technology.
Future Applications of Robotics in Industry
The possibilities are vast. Imagine robots capable of collaborating seamlessly with human workers, performing complex assembly tasks that require dexterity and precision. Picture autonomous mobile robots navigating factory floors, delivering materials and components exactly where and when they’re needed. Envision robots equipped with advanced sensors and AI that can perform predictive maintenance, identifying potential equipment failures before they occur, preventing costly downtime and ensuring smooth production flow. The development of collaborative robots, or “cobots,” designed to work safely alongside humans, is also rapidly accelerating. These robots can handle repetitive or dangerous tasks, freeing up human workers to focus on more creative and strategic aspects of the job.
A Glimpse into a Futuristic Factory
The year is 2040. A sprawling, brightly lit factory hums with activity. Sleek, agile robots move effortlessly alongside human workers, each performing their specialized tasks with precision and efficiency. AI-powered systems monitor the entire production process in real-time, optimizing resource allocation and identifying potential bottlenecks. Human workers collaborate with robots on complex assembly tasks, using augmented reality headsets to receive real-time instructions and data. Robots perform routine maintenance and inspections, ensuring the smooth operation of the factory. The air is clean and quiet, a testament to the efficiency and safety of this advanced manufacturing environment. The overall atmosphere is one of seamless collaboration between humans and machines, where technology empowers human ingenuity and creativity, leading to unprecedented levels of productivity and innovation. This futuristic factory isn’t science fiction; it’s a vision rapidly becoming reality.
Ultimate Conclusion
The integration of robotics in industrial settings isn’t just a trend; it’s a fundamental shift towards a more efficient, safer, and ultimately, more productive future. As technology continues to evolve, we can expect even more innovative applications of robotics, further blurring the lines between human and machine collaboration. The possibilities are endless, promising a future where industrial processes are optimized to unprecedented levels, paving the way for a more sustainable and technologically advanced world.