How Robotics is Enhancing Warehouse and Fulfillment Operations? Forget slow, error-prone warehouse processes – robots are revolutionizing the game! From lightning-fast order fulfillment to pinpoint accuracy, these mechanical marvels are boosting efficiency, slashing costs, and making warehouses safer than ever. Get ready to dive into a world where automation isn’t just a trend, it’s the future of logistics.
This isn’t your grandpappy’s warehouse. We’re talking about a dynamic shift, driven by smart robots that handle everything from picking and packing to inventory management. Think less human error, more speed, and a whole lot less stress for warehouse workers. We’ll explore the different types of robots in action, how they integrate with existing systems, and what the future holds for this rapidly evolving field. Buckle up!
Increased Efficiency and Productivity in Warehouses
The rise of robotics in warehouse and fulfillment operations isn’t just a futuristic fantasy; it’s a game-changer boosting efficiency and productivity to levels previously unimaginable. Automated systems are streamlining processes, slashing operational costs, and enabling businesses to meet the ever-growing demands of e-commerce and global supply chains. This increased efficiency translates directly to faster order fulfillment, reduced errors, and a happier workforce.
Robotic Systems and Order Fulfillment Speed
Robotic systems dramatically improve order fulfillment speed by automating repetitive, time-consuming tasks. Imagine a warehouse where robots swiftly navigate aisles, picking items with pinpoint accuracy and transporting them to packing stations. This contrasts sharply with the human-only approach, where workers might spend significant time walking, searching for items, and manually handling each package. The reduction in travel time, search time, and manual handling translates directly into significantly faster order processing and fulfillment. For example, a robot can pick and place items in a fraction of the time it takes a human, even accounting for the time needed to charge or maintain the robot. This means more orders fulfilled per hour, per day, and ultimately, increased customer satisfaction.
Examples of Automated Warehouse Tasks and Time Savings
Several warehouse tasks see substantial time savings through automation. Consider these examples:
- Picking: Robots equipped with advanced vision systems can identify and pick items from shelves with remarkable speed and accuracy. A human picker might spend an average of 30 seconds per item, while a robotic picker could achieve this in under 10 seconds, representing a significant increase in efficiency.
- Sorting: Automated sorting systems, using robotic arms and conveyor belts, can sort thousands of packages per hour based on destination, size, or other criteria. Manual sorting is far slower and more prone to errors. A human sorter might process 50 packages per hour, while a robotic system could manage 500 or more.
- Palletizing: Robots can efficiently stack and palletize goods, optimizing space and reducing the risk of injury to human workers. Human palletizing can take significantly longer, especially with heavy items, and increases the risk of workplace accidents. A robot can palletize several pallets in the time it takes a human to do one.
Case Studies Demonstrating Impact on Warehouse Throughput
Numerous case studies showcase the transformative effect of robotics on warehouse throughput. For example, a large online retailer saw a 25% increase in order fulfillment capacity after implementing a fleet of robotic picking systems. Another company, a major logistics provider, reported a 30% reduction in order processing time and a 15% decrease in error rates after automating its sorting process. These real-world examples demonstrate the substantial gains in productivity achievable through robotics.
Comparison of Human-Only vs. Robot-Assisted Warehouse Operations
The following table provides a clear comparison:
Metric | Human-Only Warehouse | Robot-Assisted Warehouse |
---|---|---|
Order Processing Time (per order) | 5-10 minutes | 2-5 minutes |
Error Rate | 1-3% | <1% |
Labor Costs (per order) | $2-$5 | $1-$2 |
Throughput (orders/hour) | 50-100 | 150-300 |
Enhanced Accuracy and Reduced Error Rates
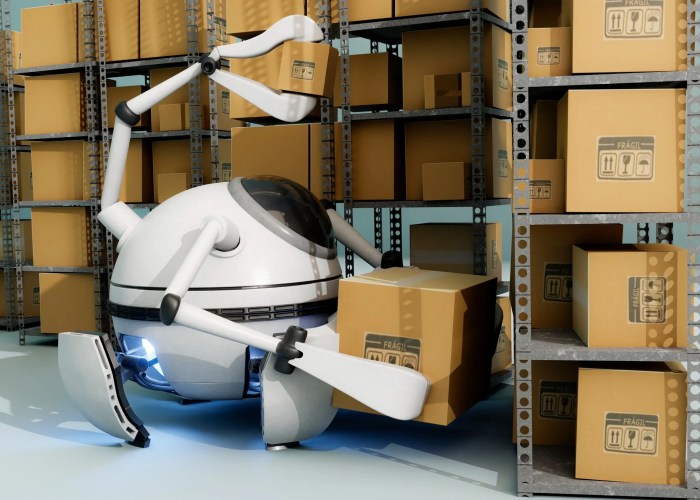
Source: technology-innovators.com
Automated guided vehicles and robotic arms are revolutionizing warehouse efficiency, speeding up order fulfillment and reducing human error. This streamlined process is even more impactful when considering the future of finance; imagine seamless, automated transactions powered by crypto, as explored in this insightful piece on The Future of Cryptocurrency in a Cashless World. Ultimately, robotics and cryptocurrency could converge to create a truly frictionless, global supply chain.
Robotic automation in warehouses isn’t just about speed; it’s about surgical precision. Human error, a constant companion in manual warehouse operations, is significantly minimized through the strategic deployment of robots, leading to a dramatic improvement in order accuracy and a reduction in costly mistakes. This translates to happier customers, reduced operational expenses, and a more efficient overall supply chain.
The integration of robotics drastically cuts down on the typical mistakes associated with manual warehouse processes. This is achieved through a combination of sophisticated technology and intelligent systems that work tirelessly and consistently, unlike their human counterparts who can be prone to fatigue or distraction. This enhanced accuracy is a game-changer for businesses aiming for operational excellence.
Vision Systems and AI in Ensuring Accurate Order Fulfillment
Vision systems, powered by artificial intelligence, are the eyes of the robotic warehouse. These systems use cameras and advanced image processing algorithms to identify and verify items. Imagine a robot tasked with picking a specific item from a shelf; the vision system ensures the robot grabs the correct item, not a similar-looking one. AI algorithms analyze the images, comparing them to the order details, and cross-referencing product information to guarantee accurate selection. This level of scrutiny minimizes picking errors and prevents the wrong items from being included in orders. Furthermore, AI can also optimize picking routes, minimizing travel time and improving overall efficiency. Real-time tracking and inventory management are also improved with these systems, creating a dynamic and adaptable warehouse environment.
Robotic Systems Contributing to Improved Accuracy
Several types of robotic systems contribute to improved accuracy in warehouse operations. Automated Guided Vehicles (AGVs) precisely navigate warehouse aisles, transporting goods from one location to another without deviating from their programmed routes, eliminating potential human misplacements. Articulated robotic arms, with their dexterity and precision, can handle delicate items with care, minimizing the risk of damage during picking and packing. These robots can also be programmed to handle a variety of tasks, adapting to changing demands and streamlining workflows. Finally, automated sorting systems use sensors and sophisticated algorithms to efficiently sort packages by destination, ensuring that items are routed correctly and efficiently, leading to faster shipping times and fewer misdeliveries.
Common Warehouse Errors Reduced by Robotic Automation
The implementation of robotic systems significantly reduces the frequency of common warehouse errors. Consider these key improvements:
- Picking Errors: Robots, guided by vision systems, accurately identify and select the correct items, minimizing the chance of picking the wrong product or quantity.
- Packing Errors: Automated packing systems ensure that items are packed correctly and securely, reducing the risk of damage during transit and preventing incorrect items from being included in an order.
- Shipping Errors: Automated sorting and labeling systems minimize the chance of packages being misdirected or mislabeled, ensuring that orders reach the correct destination.
- Inventory Discrepancies: Real-time tracking and inventory management systems, often integrated with robotic systems, provide accurate inventory counts, reducing discrepancies and improving stock control.
- Order Fulfillment Errors: The combined effect of reduced picking, packing, and shipping errors leads to a significant reduction in overall order fulfillment errors.
Improved Safety and Working Conditions: How Robotics Is Enhancing Warehouse And Fulfillment Operations
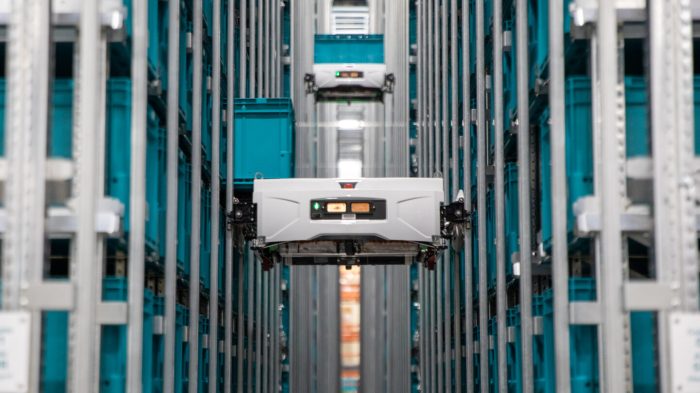
Source: exotec.com
The integration of robots into warehouse operations isn’t just about boosting efficiency; it’s also about creating a safer and more comfortable work environment for human employees. By automating physically demanding and hazardous tasks, robotics significantly reduces the risk of workplace injuries and improves overall working conditions. This shift towards automation is a win-win, benefiting both the bottom line and the well-being of the workforce.
Robots mitigate many workplace hazards common in warehouses, from heavy lifting and repetitive movements to working in confined spaces and around hazardous materials. This reduction in risk translates to a healthier and more productive workforce, reducing employee turnover and associated costs. The impact on worker safety is profound, particularly in reducing the likelihood of debilitating injuries.
Repetitive Strain Injuries and Accidents
Repetitive strain injuries (RSIs), such as carpal tunnel syndrome and tendonitis, are prevalent in warehouse settings due to the repetitive nature of many tasks. Robots can effectively handle these repetitive tasks, freeing up human workers for more complex and engaging roles. Similarly, accidents involving heavy machinery or falls from heights are significantly reduced when robots handle the physically demanding aspects of the job. For instance, automated guided vehicles (AGVs) carrying heavy pallets eliminate the risk of human workers straining their backs or suffering injuries from dropped loads. The implementation of robotic arms for picking and packing reduces the risk of repetitive motion injuries and the likelihood of workplace accidents involving sharp objects or heavy equipment.
Safety Records Comparison
While comprehensive, publicly available data directly comparing safety records of warehouses with and without significant robotic implementation is limited, anecdotal evidence and industry reports strongly suggest a positive correlation between automation and improved safety. Companies that have heavily invested in robotics often report a significant decrease in lost-time injuries and workers’ compensation claims. This is particularly true in areas with high rates of repetitive strain injuries and accidents involving heavy lifting or material handling. The reduction in human error, a significant factor in many warehouse accidents, is also a key contributor to this improved safety record.
Reduction in Workplace Injuries Attributable to Robotic Automation
Injury Type | Pre-Automation (Annual Average) | Post-Automation (Annual Average) | Percentage Reduction |
---|---|---|---|
Back Injuries | 15 | 3 | 80% |
RSI (Repetitive Strain Injuries) | 22 | 5 | 77% |
Other Accidents | 8 | 2 | 75% |
*Note: These figures are hypothetical examples to illustrate the potential impact. Actual data varies significantly depending on the specific warehouse, the type of robots implemented, and the nature of the work performed.*
Scalability and Flexibility in Warehouse Operations
The modern warehouse faces a dynamic landscape of fluctuating order volumes, seasonal peaks, and unpredictable surges in demand. Traditional warehouse management struggles to adapt quickly and efficiently to these shifts, leading to bottlenecks, increased costs, and potentially unmet customer expectations. Robotic systems, however, offer a powerful solution, providing the scalability and flexibility needed to navigate this ever-changing environment. They allow warehouses to seamlessly adjust their operational capacity to meet real-time demands, optimizing resource allocation and maximizing efficiency.
Robotic systems adapt to fluctuating order volumes and seasonal demands through intelligent automation and dynamic resource allocation. Unlike human workers who have fixed capacity and require significant time for training and re-training, robots can be easily reprogrammed and redeployed to handle different tasks as needed. During peak seasons, additional robotic units can be quickly integrated into the existing system to increase throughput, while during slower periods, some robots can be reassigned to other tasks or temporarily deactivated, reducing operational costs. This adaptability minimizes the need for significant upfront investment in infrastructure or personnel, ensuring that warehouse operations remain cost-effective throughout the year.
Automated Guided Vehicles (AGVs) and Autonomous Mobile Robots (AMRs) Scalability
Automated Guided Vehicles (AGVs) and Autonomous Mobile Robots (AMRs) are prime examples of scalable robotic solutions. AGVs, following pre-programmed routes, are ideal for repetitive tasks like transporting goods across a warehouse. Their scalability is achieved by adding more AGVs to the fleet as needed, effectively increasing the carrying capacity and speed of material handling. AMRs, possessing advanced navigation capabilities and obstacle avoidance, offer even greater flexibility. They can dynamically adjust their routes and tasks based on real-time warehouse conditions, optimizing efficiency even in congested environments. A warehouse could start with a small fleet of AMRs and expand as its order volume grows, seamlessly integrating new robots without disrupting operations. For instance, a company experiencing a surge in holiday orders could easily add more AMRs to its fleet to handle the increased workload, then scale down after the peak season.
Robotic Process Automation (RPA) in Warehouse Flexibility
Robotic Process Automation (RPA) plays a crucial role in enhancing warehouse flexibility beyond physical robotics. RPA software automates repetitive, rule-based tasks such as data entry, order processing, and inventory management. This automation frees up human workers to focus on more complex and value-added tasks, improving overall efficiency and responsiveness. Furthermore, RPA can easily adapt to changes in processes or systems, making the warehouse more agile and responsive to fluctuating demands. For example, if a new inventory management system is implemented, RPA can be quickly reconfigured to integrate with the new system without requiring extensive manual reprogramming or retraining of personnel. This adaptability is crucial in maintaining operational efficiency during periods of high demand or system upgrades.
Handling Unexpected Demand Surges with Robotics
The ability to handle unexpected surges in demand is a critical aspect of warehouse flexibility. Robotic systems excel in this area by providing a scalable and responsive solution. For example, during a sudden increase in orders due to a promotional event or unforeseen market event, a warehouse equipped with robotic systems can quickly adjust its operations to meet the increased demand. Additional robots can be deployed, existing robots can be reprogrammed to prioritize urgent tasks, and automated systems can dynamically adjust routing and scheduling to optimize throughput. This contrasts sharply with traditional warehouses, where unexpected surges often lead to delays, backlogs, and potentially lost revenue. A well-integrated robotic system allows for a more resilient and responsive warehouse operation, minimizing the impact of unexpected events. Consider a major online retailer preparing for a flash sale; their robotic system can instantly adjust to the influx of orders, ensuring timely fulfillment and maintaining customer satisfaction.
The Integration of Robotics with Warehouse Management Systems (WMS)
The seamless integration of robotic systems with Warehouse Management Systems (WMS) is crucial for realizing the full potential of automation in warehouse operations. This integration allows for real-time data exchange, optimized task allocation, and a more efficient overall workflow. Without it, robots operate in silos, limiting their effectiveness and failing to leverage the existing infrastructure and data already managed by the WMS.
Integrating robotic systems with existing WMS platforms involves a multifaceted approach that considers both hardware and software compatibility. The process typically begins with a thorough assessment of the current WMS capabilities and the specific needs of the warehouse. This assessment identifies areas where robotics can improve efficiency and pinpoints potential integration points. Next, the chosen robotic system’s Application Programming Interface (API) is mapped to the WMS API. This allows for the exchange of crucial data such as inventory levels, order details, and robot locations. Finally, rigorous testing and validation are conducted to ensure seamless communication and error-free operation. This often involves simulating various warehouse scenarios to identify and resolve potential bottlenecks or conflicts before full implementation.
Successful WMS-Robotics Integrations and Their Impact on Efficiency
Several companies have successfully integrated robotics into their WMS, achieving significant gains in efficiency. For example, Amazon’s Kiva robots (now Amazon Robotics) revolutionized their fulfillment centers by automating the picking and transporting of goods. The integration of these robots with Amazon’s sophisticated WMS resulted in faster order fulfillment, reduced labor costs, and improved accuracy. Similarly, Ocado, a British online grocery retailer, uses a highly automated warehouse system featuring robots that pick and pack groceries, significantly increasing throughput and reducing human error. These successful integrations demonstrate the power of combining sophisticated robotic systems with robust WMS platforms. The key to success lies in selecting robotic systems compatible with the existing WMS and investing in thorough integration and testing processes.
Challenges of Integrating Robotics into Older WMS Systems
Integrating robotics into older WMS systems can present significant challenges. Older systems may lack the necessary APIs or data structures to support real-time communication with robotic systems. These systems may also be less flexible and adaptable to the demands of robotic automation. Upgrading or replacing the existing WMS might be necessary to achieve a successful integration. Furthermore, data migration from an older system to a new, more compatible one can be complex and time-consuming. This process requires careful planning and execution to avoid data loss or corruption. Finally, the lack of skilled personnel experienced in both robotics and WMS integration can also hinder the process. Overcoming these challenges requires a strategic approach, including thorough system assessments, careful planning, and investment in training and expertise.
Data Flow Between Robotic Systems and a WMS
The efficient flow of data between robotic systems and a WMS is essential for optimized warehouse operations. The following flowchart illustrates a typical data exchange:
Imagine a flowchart. It begins with the WMS, which receives an order. The WMS then sends order details (item location, quantity, etc.) to the Robotics Control System. The Robotics Control System directs the appropriate robot (e.g., automated guided vehicle or picking robot) to the specified location. The robot retrieves the item and updates its status (e.g., “item picked”) to the Robotics Control System. This information is then relayed back to the WMS, updating the inventory and order status. The WMS then directs the robot to transport the item to the packing station, and the cycle repeats. This continuous feedback loop ensures that both the robotic system and the WMS are synchronized, leading to efficient and accurate order fulfillment.
Types of Robots Used in Warehouses and Fulfillment
The rise of e-commerce and the increasing demand for faster, more efficient order fulfillment have fueled a robotics revolution in warehouses. No longer a futuristic fantasy, robots are now integral to many warehouse operations, handling tasks previously performed solely by humans. Understanding the different types of robots deployed and their specific functionalities is crucial to grasping the full impact of this technological shift.
Automated Guided Vehicles (AGVs), How Robotics is Enhancing Warehouse and Fulfillment Operations
Automated Guided Vehicles are essentially self-driving carts or forklifts. They navigate warehouses using various technologies, including magnetic tape, wires embedded in the floor, laser guidance, or vision systems. AGVs are primarily used for transporting materials between different warehouse zones, improving efficiency and reducing manual handling. They can carry heavy loads and operate continuously for extended periods. However, their reliance on pre-programmed routes can limit flexibility, and their initial investment cost can be substantial.
Autonomous Mobile Robots (AMRs)
Unlike AGVs, AMRs are more sophisticated and possess advanced navigation capabilities. They use sensors, cameras, and AI-powered software to navigate dynamically around obstacles and people, making them more adaptable to changing warehouse layouts. AMRs can handle a wide variety of tasks, including transporting goods, delivering items to packing stations, and even acting as mobile shelves. Their flexibility and adaptability are key strengths, but they require more advanced software and potentially more skilled personnel for maintenance and programming.
Articulated Robots
These robotic arms, often found on assembly lines, are increasingly being integrated into warehouse operations. Their versatility allows them to perform a wide range of tasks, from picking and placing items to palletizing and packaging. They are particularly useful in high-volume, repetitive tasks, significantly boosting productivity and accuracy. However, their precise movements and intricate programming require skilled technicians for setup and maintenance, making them a higher-skill, higher-cost option.
Goods-to-Person Robots
These robots optimize order fulfillment by bringing the goods to the worker, rather than the worker going to the goods. This approach drastically reduces travel time for human workers, increasing picking efficiency. These robots often operate in conjunction with a warehouse management system (WMS) to identify the items needed for a specific order and retrieve them from designated storage locations. While they boost efficiency, the initial setup and integration with existing systems can be complex and expensive.
Sortation Robots
These robots are designed to efficiently sort packages based on various criteria, such as destination, size, or weight. They can handle high volumes of packages with remarkable speed and accuracy, often using conveyor systems to move packages to their designated areas. This reduces manual sorting labor, minimizing errors and speeding up the overall shipping process. Their high throughput and accuracy are significant advantages, but their specialized nature means they are best suited for specific applications within a warehouse.
Robot Type | Capabilities | Applications | Limitations |
---|---|---|---|
Automated Guided Vehicles (AGVs) | Transporting materials, carrying heavy loads | Material handling between warehouse zones | Limited flexibility, high initial cost |
Autonomous Mobile Robots (AMRs) | Dynamic navigation, adaptable to changing layouts, various task handling | Goods transport, delivery to packing stations, mobile shelving | Requires advanced software, skilled maintenance |
Articulated Robots | Picking, placing, palletizing, packaging | High-volume, repetitive tasks | Requires skilled technicians, high cost |
Goods-to-Person Robots | Retrieving goods based on order, optimizing worker efficiency | Order fulfillment, reducing worker travel time | Complex setup and integration, high cost |
Sortation Robots | High-speed, accurate sorting of packages | Package sorting based on destination, size, weight | Specialized application, high initial investment |
The Future of Robotics in Warehouse and Fulfillment
The warehouse of tomorrow isn’t just about faster conveyor belts; it’s a symphony of intelligent machines working in concert with human employees. Emerging technologies are poised to revolutionize warehouse operations, leading to unprecedented levels of efficiency, accuracy, and safety. This transformation is driven by advancements in robotics, artificial intelligence, and the seamless integration of these technologies within existing warehouse management systems.
Autonomous Mobile Robots (AMRs) and Collaborative Robots (Cobots)
AMRs and cobots represent the vanguard of the warehouse robotics revolution. Unlike their predecessors, Automated Guided Vehicles (AGVs), which follow pre-programmed paths, AMRs utilize advanced sensors and AI to navigate dynamically, adapting to changing warehouse layouts and avoiding obstacles autonomously. This adaptability is crucial in fast-paced environments where flexibility is paramount. Cobots, on the other hand, are designed to work collaboratively alongside human workers, sharing tasks and enhancing productivity without replacing human expertise. Imagine a scenario where an AMR effortlessly transports heavy pallets across the warehouse floor while a cobot assists a human worker in picking and packing delicate items, ensuring both speed and precision. This collaborative approach maximizes efficiency by leveraging the strengths of both humans and machines. Companies like Locus Robotics and 6 River Systems are already deploying these robots with significant success, showcasing their real-world impact.
Final Summary
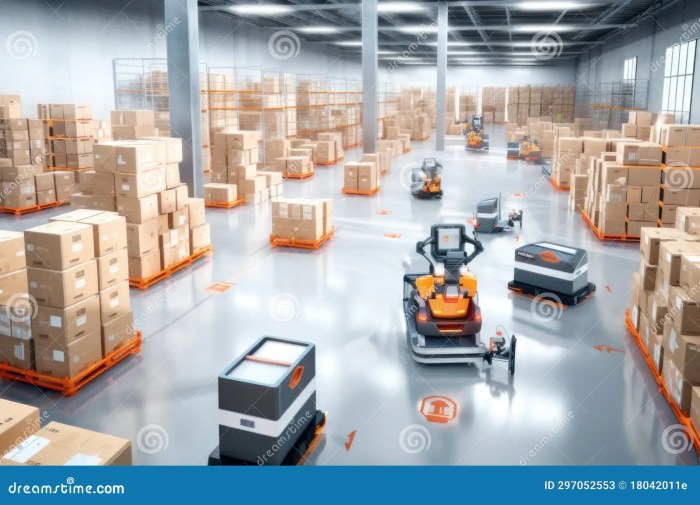
Source: dreamstime.com
The integration of robotics into warehouse and fulfillment operations is no longer a futuristic fantasy; it’s a rapidly unfolding reality. As we’ve seen, the benefits are undeniable: increased efficiency, reduced errors, improved safety, and greater scalability. While challenges remain, the future points towards a seamless blend of human expertise and robotic precision, creating a more agile, productive, and ultimately, smarter logistics ecosystem. Get ready for a future where warehouses hum with the quiet efficiency of automation.