How Robotics is Changing the Way We Manufacture Products? Forget clunky assembly lines and repetitive human tasks. We’re diving headfirst into a manufacturing revolution, where robots aren’t just replacing humans, but empowering them. Think faster production, higher quality goods, and a whole lot less workplace injuries. This isn’t science fiction; it’s the future of making stuff, and it’s happening now.
From precision welding to intricate microchip assembly, robots are handling jobs once deemed impossible for machines. This shift isn’t just about efficiency; it’s about adapting to a changing world, overcoming labor shortages, and creating safer work environments. We’ll explore how this robotic boom impacts everything from your morning coffee to the smartphone in your pocket.
Increased Efficiency and Productivity in Manufacturing
Robotic automation is revolutionizing manufacturing, dramatically boosting efficiency and productivity. It’s not just about faster production lines; it’s about a fundamental shift in how we approach manufacturing, leading to higher quality, lower costs, and a safer work environment. The integration of robots allows for a more streamlined, precise, and ultimately, more profitable manufacturing process.
Improved Manufacturing Speed and Output
Robotic automation significantly accelerates manufacturing processes. Unlike human workers who need breaks and are susceptible to fatigue, robots can operate continuously, at a consistent pace, for extended periods. This uninterrupted operation translates directly into increased production volume and shorter lead times. For example, in automotive manufacturing, robots weld car bodies at speeds far exceeding human capabilities, completing thousands of welds per day with unwavering precision. This increased speed directly impacts the company’s ability to meet market demands and stay competitive.
Reduced Human Error in Manufacturing
Human error is an inevitable part of manual manufacturing processes. Fatigue, distraction, or even simple miscalculations can lead to defects, wasted materials, and costly delays. Robots, however, operate with pre-programmed precision, minimizing the likelihood of errors. Their consistent performance leads to higher quality products and reduced waste. Consider the pharmaceutical industry, where even minor inaccuracies can have significant consequences. Robots are now commonly used in pharmaceutical manufacturing for tasks requiring high precision, such as pill counting and packaging, ensuring consistency and minimizing the risk of errors.
Examples of Manufacturing Processes Significantly Speeded Up by Robots, How Robotics is Changing the Way We Manufacture Products
Several manufacturing processes have experienced dramatic speed improvements thanks to robotic integration. Welding, painting, and assembly lines in automotive manufacturing are prime examples. Robots can perform these tasks much faster and more consistently than human workers, leading to a significant increase in production output. Similarly, in electronics manufacturing, robots are used for tasks such as component placement and soldering, enabling high-speed, high-volume production of electronic devices. The food processing industry also benefits, with robots handling tasks like packaging and palletizing at rates far exceeding human capabilities.
Cost-Effectiveness of Robotic Automation
While the initial investment in robotic automation can be substantial, the long-term cost-effectiveness is often undeniable. The increased speed and precision of robots lead to reduced labor costs, lower material waste, and fewer defects. This results in significant savings over time, offsetting the initial investment. A comparison between the cost of employing human workers and maintaining robots reveals that, while robots require upfront investment and maintenance, the overall cost per unit produced often falls below that of human labor, especially in high-volume production environments. Furthermore, robots can work in hazardous environments, reducing the risk of workplace accidents and associated costs.
Comparison of Human Labor vs. Robotic Labor
Metric | Human Labor | Robotic Labor |
---|---|---|
Speed | Variable, susceptible to fatigue | Consistent, high speed |
Accuracy | Prone to error | High precision, minimal error |
Cost (per unit) | Higher in high-volume production | Lower in high-volume production (considering initial investment) |
Enhanced Product Quality and Consistency
Robots are revolutionizing manufacturing, not just by speeding things up, but by dramatically improving the quality and consistency of the final product. Human error, a significant contributor to defects, is minimized, leading to more reliable and higher-quality goods. This translates to increased customer satisfaction, reduced waste, and ultimately, a stronger bottom line for manufacturers.
The unwavering precision and repeatability of robots allow them to maintain consistent quality standards across even the largest production runs. Unlike human workers who can experience fatigue or variations in performance, robots perform the same task with the same level of accuracy every time. This consistency is particularly crucial in industries where even minor deviations can have significant consequences.
Robotic Precision and Accuracy in Assembly and Manipulation
Robotic systems boast unparalleled precision in assembly and manipulation tasks. Equipped with advanced sensors and control systems, they can handle intricate components with a level of accuracy far surpassing human capabilities. This allows for tighter tolerances, more complex assemblies, and a significant reduction in defects caused by misalignment, incorrect placement, or damage during handling. For example, in the electronics industry, robots are used to place tiny components onto circuit boards with micron-level accuracy, ensuring optimal functionality and preventing short circuits. The automotive industry also leverages this precision for tasks like welding and painting, leading to consistently high-quality finishes and structurally sound vehicles.
Examples of Improved Product Quality Across Industries
The impact of robots on product quality is evident across numerous sectors. In the pharmaceutical industry, robots ensure the precise dispensing and packaging of medications, minimizing contamination risks and guaranteeing dosage accuracy. This is crucial for maintaining the safety and efficacy of pharmaceuticals. The food processing industry benefits from robotic systems that handle delicate products with care, reducing damage and spoilage while maintaining consistent portion sizes and packaging. In aerospace manufacturing, robots play a vital role in assembling complex components with extreme precision, contributing to the reliability and safety of aircraft and spacecraft.
Types of Defects Robots Help Prevent
Robots effectively prevent a wide array of defects. These include dimensional inaccuracies, misalignments, surface imperfections (scratches, dents), incorrect component placement, and inconsistencies in assembly. Furthermore, they minimize contamination risks, particularly crucial in industries like pharmaceuticals and food processing. The reduction in human error directly translates to fewer recalls, reduced warranty claims, and a significant boost to the manufacturer’s reputation.
Quality Control Process with Robotic Integration
The flowchart above illustrates a typical quality control process with robotic integration. Robots perform inspections at various stages, identifying defects early and preventing them from propagating through the production line. Human oversight remains crucial for complex decision-making and advanced quality assurance.
Adaptability and Flexibility in Manufacturing Processes
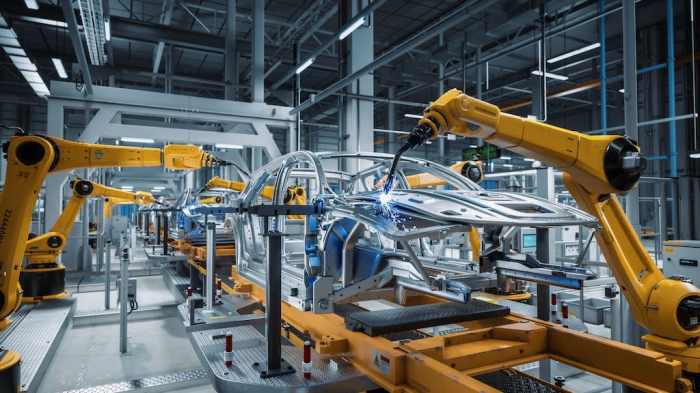
Source: amazonaws.com
Robotics is revolutionizing manufacturing, boosting efficiency and precision. This automation push mirrors similar advancements in other sectors; for example, the agricultural industry is also undergoing a massive tech upgrade, as detailed in this insightful article: How Technology is Shaping the Future of Sustainable Agriculture. Ultimately, both fields demonstrate how smart tech is driving productivity and reshaping our world, leading to more sustainable and efficient processes in manufacturing and beyond.
The rise of robotics in manufacturing isn’t just about increased speed and precision; it’s about creating a production environment that can seamlessly adapt to the ever-changing demands of the modern market. This adaptability, driven by the inherent flexibility of robotic systems, is revolutionizing how companies design, produce, and deliver their goods. Forget rigid, inflexible assembly lines – the future of manufacturing is agile and responsive.
Robots’ ability to adjust to changes in product design or manufacturing requirements is a game-changer. This isn’t about simply replacing human workers; it’s about creating a system that can handle variations in product specifications, production volumes, and even entire product lines with minimal downtime. This adaptability translates directly to cost savings and increased competitiveness.
Reprogrammability and Production Flexibility
The core of robotic adaptability lies in their reprogrammability. Unlike traditional hard-automation systems, which are essentially fixed in their operations, robots can be reprogrammed to perform different tasks with relative ease. This means that a single robot can be repurposed for various stages of production or even different product lines. Imagine a robot initially programmed for welding car frames being reprogrammed to handle the assembly of electronic components – a testament to the versatility offered by modern robotic systems. This reprogrammability significantly reduces the time and cost associated with switching between production runs, leading to increased production flexibility and shorter lead times. This is particularly valuable in industries with high product variability, such as consumer electronics or customized manufacturing.
Robots in Diverse Manufacturing Environments
Robots are no longer confined to large-scale automotive factories. Their adaptability allows them to thrive in diverse environments, from small-batch production in specialized workshops to high-volume operations in global manufacturing hubs. For instance, collaborative robots (cobots) are increasingly used in smaller manufacturing facilities to assist human workers with repetitive or physically demanding tasks, enhancing productivity without requiring significant retooling or workspace redesign. In contrast, larger industrial robots are used in automotive plants for tasks such as welding, painting, and assembly, handling heavy loads and performing complex movements with high precision. In the food processing industry, robots handle delicate tasks like packaging and sorting, ensuring hygiene and consistency. The adaptability of these systems extends to various materials and processes, making them truly versatile tools for modern manufacturers.
Adaptability of Robotic Systems Compared to Traditional Hard-Automation
Traditional hard-automation systems, such as fixed assembly lines, are designed for a specific product and process. Any changes to the product design or manufacturing requirements necessitate costly and time-consuming modifications to the entire system. This lack of flexibility often leads to production bottlenecks and reduced efficiency. Robotic systems, on the other hand, offer significantly greater flexibility. Their modular design and reprogrammability allow for easy adaptation to changing needs, minimizing downtime and maximizing resource utilization. This difference in adaptability is a key factor in the increasing adoption of robots across various industries.
Advantages and Disadvantages of Flexible Robotic Systems
The implementation of flexible robotic systems offers several advantages, but it’s crucial to acknowledge potential drawbacks.
Before listing the advantages and disadvantages, it’s important to understand that the overall impact of implementing flexible robotic systems depends on several factors, including the specific application, the scale of the operation, and the level of integration with existing systems. Careful planning and a thorough cost-benefit analysis are crucial for successful implementation.
- Advantages: Increased production flexibility, reduced lead times, improved product quality, higher efficiency, reduced labor costs (in some cases), enhanced safety, improved scalability, and better adaptability to changing market demands.
- Disadvantages: High initial investment costs, the need for skilled personnel for programming and maintenance, potential for job displacement in some roles, and the requirement for robust safety protocols to ensure safe human-robot collaboration.
The Role of Robotics in Addressing Labor Shortages
The manufacturing industry is facing a significant challenge: a growing shortage of skilled labor. This shortage impacts productivity, delivery timelines, and overall competitiveness. Robotics offers a powerful solution, automating tasks that are difficult to fill with human workers, and boosting overall efficiency. This isn’t about robots replacing humans entirely, but rather about robots augmenting the workforce and allowing human employees to focus on more complex and creative tasks.
Robots mitigate labor shortages by taking on repetitive, physically demanding, or hazardous jobs that are often difficult to fill. This allows companies to maintain production levels even when facing a limited pool of available workers. The strategic deployment of robots can bridge the gap between labor demand and supply, ensuring consistent output and preventing production delays.
Types of Tasks Best Suited for Robots
Robots excel in tasks requiring high precision, speed, and consistency. They are ideal for repetitive assembly line work, material handling (including heavy lifting and palletizing), welding, painting, and quality control inspections. These are often physically demanding or monotonous tasks that can lead to worker fatigue and injuries, resulting in decreased productivity and increased absenteeism. By automating these processes, manufacturers can maintain a steady workflow and improve overall safety.
Examples of Successful Robot Deployments
Companies like Tesla have extensively integrated robots into their manufacturing processes, automating many aspects of vehicle assembly. This has allowed them to increase production volume while maintaining quality, even in the face of labor shortages. Similarly, in the electronics industry, Foxconn, a major Apple supplier, has utilized robots to automate various assembly tasks, enhancing efficiency and reducing reliance on manual labor. These are just two examples of how large-scale adoption of robotics has addressed labor challenges. Smaller manufacturers are also finding success with collaborative robots (cobots) which can work alongside human workers, improving safety and efficiency on a smaller scale.
Potential Impact of Robots on Manufacturing Employment
The impact of robots on employment is a complex issue. While some jobs may be displaced by automation, new roles are created in areas like robotics programming, maintenance, and system integration. The overall effect is likely to be a shift in the types of jobs available, requiring a workforce with different skill sets. Reskilling and upskilling initiatives will be crucial to ensure a smooth transition and prevent widespread unemployment. The focus should be on leveraging robotics to enhance human capabilities rather than replacing them entirely.
Societal Impacts of Increased Automation in Manufacturing
The increasing automation of manufacturing has several potential societal impacts, both positive and negative:
- Increased productivity and economic growth: Automation can lead to higher output and economic growth, benefiting society as a whole.
- Changes in the job market: A shift in job types will require adaptation and reskilling initiatives to prevent unemployment.
- Improved working conditions: Robots can take over dangerous or repetitive tasks, improving worker safety and well-being.
- Potential for income inequality: The benefits of automation may not be evenly distributed, potentially exacerbating income inequality if not properly managed.
- Increased competitiveness for nations: Countries that embrace automation effectively will likely gain a competitive edge in global markets.
Safety Improvements in Manufacturing Environments
The integration of robots into manufacturing has dramatically reshaped workplace safety, shifting the burden of hazardous tasks from human workers to automated systems. This transition not only reduces the risk of injuries but also fosters a safer and more productive work environment. The benefits extend beyond simply avoiding accidents; robots contribute to a proactive safety culture, minimizing the potential for human error in high-risk situations.
Robots enhance workplace safety primarily by taking over hazardous tasks. This involves handling dangerous materials, working in extreme environments, and performing repetitive actions that can lead to injury. By automating these processes, manufacturers significantly reduce the exposure of human workers to harm. The resulting decrease in workplace injuries translates into lower insurance premiums, reduced lost productivity, and a more positive overall work environment.
Hazardous Task Automation
Robots are ideally suited for handling tasks that pose significant safety risks to human workers. Examples include working with heavy machinery, operating in confined spaces, handling toxic chemicals, and working at heights. Welding, for instance, exposes workers to intense heat, sparks, and harmful fumes. Robots can perform these welding tasks with precision and consistency, eliminating the risks associated with human error and exposure to hazardous materials. Similarly, painting operations often involve the use of volatile organic compounds (VOCs), which can be harmful to human health. Robots can automate the painting process, minimizing worker exposure to these harmful substances. In the automotive industry, robots are frequently used to handle heavy car parts, reducing the risk of back injuries and other musculoskeletal disorders among human workers.
Reduction in Workplace Injuries
Numerous studies have demonstrated a significant correlation between robotic automation and a reduction in workplace injuries. Factories with high levels of robotic integration often exhibit substantially lower rates of workplace accidents compared to those with limited or no robotic automation. While precise figures vary depending on the industry and the specific types of robots employed, the overall trend points towards a marked improvement in safety metrics. For example, a study by the National Institute for Occupational Safety and Health (NIOSH) might show a significant decrease in the number of lost-time injuries in factories that have implemented robotic automation. (Note: Specific data would require referencing actual NIOSH or similar studies). The reduction in injuries is not just a matter of statistics; it translates into a healthier and more satisfied workforce.
Repetitive Strain Injury Prevention
Robots are particularly effective in mitigating the risk of repetitive strain injuries (RSIs). Many manufacturing jobs involve repetitive movements, such as assembling components or operating machinery, which can lead to carpal tunnel syndrome, tendonitis, and other RSIs. By automating these repetitive tasks, robots significantly reduce the strain on human workers’ bodies. Imagine a worker repeatedly assembling small electronic components for eight hours a day. The constant hand and wrist movements can cause significant fatigue and lead to long-term health problems. With a robot handling the repetitive assembly process, the worker can focus on tasks requiring higher-level skills, reducing the risk of RSI and improving their overall well-being. This shift allows for a more ergonomic and sustainable work environment, contributing to a healthier and more engaged workforce.
The Future of Robotics in Manufacturing: How Robotics Is Changing The Way We Manufacture Products
The manufacturing landscape is poised for a dramatic transformation, driven by relentless advancements in robotics. We’re moving beyond simple automation towards a future where robots and humans collaborate seamlessly, leading to unprecedented levels of efficiency, innovation, and productivity. This section explores the key trends shaping this exciting evolution.
Emerging Trends in Robotics Technology and Their Impact on Manufacturing
Several key technological advancements are reshaping the robotics industry, significantly impacting manufacturing processes. Artificial intelligence (AI) is increasingly integrated into robots, enabling them to learn, adapt, and make decisions autonomously. This leads to more flexible and responsive manufacturing systems capable of handling complex tasks and variations in production. Machine learning algorithms allow robots to improve their performance over time, reducing errors and optimizing efficiency. Simultaneously, advancements in sensor technology provide robots with a richer understanding of their environment, improving precision and safety. For example, advanced vision systems allow robots to identify and handle a wider variety of objects, while force sensors enable delicate and precise manipulation. The convergence of these technologies is creating a new generation of robots capable of performing tasks previously considered impossible for automation.
Collaborative Robots (Cobots) in Human-Robot Collaboration
Collaborative robots, or cobots, represent a paradigm shift in manufacturing. Unlike traditional industrial robots, which operate in isolated cages for safety reasons, cobots are designed to work safely alongside humans. This collaborative approach leverages the strengths of both humans and robots, combining human dexterity and problem-solving skills with the robot’s speed, precision, and endurance. Cobots are particularly useful in tasks requiring both physical strength and human judgment, such as assembly, packaging, and quality control. For instance, a cobot might assist a human worker by providing parts or tools, reducing physical strain and increasing productivity. This synergy between human and machine not only increases efficiency but also creates a more engaging and less physically demanding work environment. Companies like Universal Robots and ABB are leading the charge in cobot development and deployment, showcasing their applications in diverse manufacturing settings.
Innovative Robotic Applications in Manufacturing
The applications of robotics in manufacturing are expanding rapidly, extending beyond traditional assembly line tasks. One notable example is the use of autonomous mobile robots (AMRs) for material handling and logistics within factories. These robots navigate autonomously, transporting materials and goods between different workstations, optimizing warehouse efficiency and reducing labor costs. Another exciting development is the integration of robotics in 3D printing, enabling the creation of complex and customized parts with high precision. This technology allows manufacturers to respond to individual customer needs and produce highly specialized products, increasing flexibility and responsiveness. Furthermore, the use of robotics in quality control is becoming increasingly sophisticated, with robots employing advanced vision systems and machine learning algorithms to detect even subtle defects in products. This ensures higher product quality and reduces waste.
Challenges and Limitations of Widespread Robotic Adoption in Manufacturing
Despite the numerous advantages, widespread robotic adoption in manufacturing faces several challenges. The initial investment cost of robotic systems can be substantial, posing a barrier for smaller businesses. The need for skilled technicians to program, maintain, and repair these systems also presents a challenge. Furthermore, concerns about job displacement due to automation remain a significant social and economic issue. Addressing these challenges requires strategic investments in workforce training and education, as well as the development of affordable and user-friendly robotic solutions. Careful planning and consideration of the social and economic impacts are crucial for successful and responsible implementation of robotics in manufacturing.
Predicted Evolution of Robotics in Manufacturing Over the Next Decade
Year | Predicted Development | Example/Real-life Case |
---|---|---|
2024-2026 | Increased adoption of AI-powered robots and cobots in small and medium-sized enterprises (SMEs). | Increased availability of user-friendly programming interfaces and leasing options for robots. |
2027-2029 | Widespread implementation of autonomous mobile robots (AMRs) for material handling and logistics. | Major logistics companies integrating AMRs into their warehouse operations. |
2030-2032 | Emergence of more sophisticated human-robot collaboration (HRC) systems with advanced safety features. | Development of robots with improved haptic feedback and more intuitive human-machine interfaces. |
2033-2035 | Significant advancements in robotic vision and machine learning, enabling robots to handle increasingly complex tasks. | Robots capable of performing intricate assembly tasks requiring high precision and adaptability. |
Final Conclusion
The rise of robotics in manufacturing isn’t just a technological advancement; it’s a fundamental shift in how we produce goods. While questions about job displacement remain, the benefits – increased efficiency, improved quality, and enhanced safety – are undeniable. The future of manufacturing is collaborative, smart, and undeniably robotic. Get ready for a world where humans and robots work side-by-side, creating a more productive and innovative manufacturing landscape.