How Robotics is Changing the Manufacturing of Consumer Products? It’s not just about faster assembly lines anymore. We’re talking a total revolution, a seismic shift in how everything from your phone to your toothbrush gets made. Forget clunky, repetitive tasks – robots are now wielding laser precision, adapting to changing demands, and even collaborating with humans for peak efficiency. Get ready to dive into a world where automation isn’t just improving production, it’s reinventing it.
This deep dive explores the multifaceted impact of robotics on consumer product manufacturing, from increased automation and enhanced precision to improved efficiency and a transformed workforce. We’ll dissect the cost-benefits, address the evolving job market, and showcase how robotics is paving the way for a safer, more adaptable, and ultimately, more innovative future for the industry.
Increased Automation in Manufacturing
The rise of robotics is fundamentally reshaping the manufacturing landscape for consumer products, ushering in an era of unprecedented efficiency and precision. From the initial stages of raw material handling to the final packaging and distribution, robots are increasingly taking on tasks previously performed by humans, leading to significant changes in production processes and overall business strategies.
Robotic automation’s impact spans the entire manufacturing lifecycle. Consider the journey of a simple smartphone: robots might initially handle and sort the raw materials like precious metals and plastics. Then, in assembly, robots with incredibly fine motor skills meticulously place and solder minuscule components onto circuit boards, a task impossible for human hands to perform with such speed and accuracy. Painting and welding processes, traditionally dangerous and laborious for human workers, are now efficiently handled by robotic arms, ensuring consistent quality and minimizing workplace hazards. Finally, robots are used in packaging and palletizing, speeding up the process and reducing errors in order fulfillment.
Robotic Systems in Manufacturing Processes
A variety of sophisticated robotic systems are employed across various stages of consumer product manufacturing. For example, in welding, robots utilize arc welding techniques, precisely controlling the heat and positioning to create strong and consistent welds on metal components. Painting robots use spray guns guided by advanced software to apply even coats of paint to car bodies or appliances, reducing waste and ensuring a uniform finish. In assembly, collaborative robots, or “cobots,” work alongside human workers, assisting with repetitive tasks like screwing, fastening, and inserting small parts. These cobots are designed with safety features to prevent accidents and enhance human-robot collaboration.
Cost-Benefit Analysis of Robotic Automation
Implementing robotic automation involves a significant upfront investment in purchasing and installing the robotic systems, programming, and worker training. However, the long-term benefits often outweigh these initial costs. Operational costs, including maintenance and energy consumption, need to be considered. However, the increase in productivity, reduced labor costs (though requiring investment in training for different roles), and improved product quality can lead to a substantial return on investment (ROI) over time. For instance, a factory automating its painting process might see a reduction in paint waste, fewer defects, and increased production output, all contributing to a faster ROI.
Efficiency and Productivity Gains
The efficiency and productivity improvements achieved through robotic automation are substantial compared to traditional methods. The following table illustrates this:
Process | Traditional Method | Robotic Method | Efficiency Gain |
---|---|---|---|
Welding | Manual welding, prone to inconsistencies and human error. | Robotic arc welding, precise and consistent welds. | 30-50% increase in speed and quality. |
Painting | Manual spraying, leading to uneven coats and potential waste. | Robotic spraying, consistent coating with reduced material usage. | 20-40% increase in speed and reduced material waste. |
Assembly | Manual assembly, slow and susceptible to human error. | Robotic assembly, high-speed and precise placement of components. | 40-70% increase in speed and reduced error rate. |
Packaging | Manual packaging, potentially slow and prone to errors. | Automated packaging systems with robots, high speed and accuracy. | 50-80% increase in speed and reduced error rate. |
Enhanced Precision and Quality Control
Robots are revolutionizing manufacturing, not just by increasing automation, but by dramatically improving the precision and consistency of production processes. This leads to higher quality consumer goods, reduced waste, and increased efficiency across a range of industries. The enhanced accuracy offered by robotic systems allows for the creation of products with tighter tolerances and fewer defects, ultimately benefiting both manufacturers and consumers.
Robots contribute to improved accuracy and consistency by performing repetitive tasks with unwavering precision. Unlike human workers, robots don’t experience fatigue or make mistakes due to distraction. Their movements are programmed to exacting standards, resulting in consistently high-quality output. This is particularly crucial in industries where even minor imperfections can have significant consequences.
Robotic Precision in Diverse Industries
The impact of robotic precision is clearly visible across various sectors. In the electronics industry, robots are essential for assembling intricate components with micron-level accuracy. The assembly of smartphones, for instance, relies heavily on robotic systems to place minuscule parts with pinpoint accuracy, ensuring the functionality and reliability of the final product. Similarly, the pharmaceutical industry uses robots for tasks such as pill counting, packaging, and precise dispensing of medications, guaranteeing consistent dosage and preventing errors that could have serious health implications. The automotive industry also benefits from robotic precision in welding, painting, and assembly, leading to vehicles with improved structural integrity and superior finishes.
Vision Systems and Sensor Technologies in Robotic Precision
Robotic precision is not simply about programmed movements; it’s also about sophisticated feedback mechanisms. Vision systems and sensor technologies play a critical role in enabling robots to perform complex tasks accurately and detect defects. Vision systems, essentially robotic “eyes,” use cameras and advanced image processing algorithms to guide robotic movements and inspect finished products. They can identify even minute flaws that might be invisible to the human eye, ensuring only perfect products proceed to the next stage. Sensor technologies, including force sensors, proximity sensors, and laser scanners, provide robots with real-time information about their environment, allowing for adjustments to movements and preventing collisions or damage. For example, a robot performing a delicate welding operation can use force sensors to ensure consistent pressure, preventing weak welds.
Quality Control Process Enhanced by Robotic Systems
The following flowchart illustrates how robotic systems enhance the quality control process:
[Imagine a flowchart here. The flowchart would begin with “Raw Material Input,” followed by a box labeled “Robotic Inspection (Vision System & Sensors)” where robots check for defects in the raw materials. The next box would be “Robotic Assembly/Manufacturing,” showing robots performing precise assembly or manufacturing tasks. Following this is another box, “Robotic Quality Control Checks (Dimensional Accuracy, Functional Testing)”, showing robots conducting various quality control tests. This leads to a “Pass/Fail” decision box. Products passing the tests go to “Packaging and Shipping,” while those failing go to “Defect Analysis and Rectification.” The flowchart ends with “Finished Goods.”]
The flowchart highlights how robots are integrated at multiple stages, ensuring quality from raw material inspection to final product verification. This minimizes human error and significantly increases the overall quality of the manufactured goods.
Improved Efficiency and Productivity
Robotics is revolutionizing manufacturing, significantly boosting efficiency and productivity. The tireless, precise, and consistent nature of robots allows for unparalleled output compared to human workers, leading to faster production cycles and increased profitability. This efficiency isn’t just about speed; it’s about optimizing the entire manufacturing process, minimizing downtime, and reducing waste.
Robots excel at repetitive tasks, operating continuously without breaks or fatigue. This consistent performance translates directly into increased output and reduced production time. Moreover, robotic systems often integrate seamlessly with other automated systems, creating a highly efficient, interconnected production line. This integrated approach minimizes bottlenecks and maximizes overall throughput.
Robotic Speed and Throughput Compared to Human Workers
The speed and throughput advantages of robotic systems are substantial across various manufacturing tasks. For example, in automotive assembly, robots can weld car bodies at a rate far exceeding that of human welders, resulting in a significantly higher number of vehicles produced per day. Similarly, in electronics manufacturing, robots can place components on circuit boards with incredible speed and accuracy, dramatically increasing production volume. While human workers bring invaluable skills like problem-solving and adaptability, robots excel at consistent, high-speed execution of repetitive tasks. A single robotic arm, for instance, might perform hundreds of spot welds per hour, while a human welder would likely complete far fewer. The difference in throughput becomes even more pronounced when considering multiple robotic arms working simultaneously on a production line.
Reduced Production Time and Increased Output Volume
Robotic automation directly contributes to shorter production cycles and increased output. By automating repetitive tasks, manufacturers can eliminate bottlenecks and optimize workflows. This leads to a significant reduction in lead times, allowing companies to fulfill orders faster and respond more effectively to market demands. Consider a factory producing smartphones: the integration of robots in tasks like component placement, testing, and packaging can drastically shorten the time it takes to manufacture a single phone, leading to a substantial increase in the total number of phones produced per day or week. This heightened efficiency is crucial in today’s fast-paced consumer market.
Productivity Improvements Across Manufacturing Sectors
The implementation of robotic systems has yielded impressive productivity gains across various manufacturing sectors. The following examples highlight the transformative impact of robotics:
- Automotive Manufacturing: Studies show a 20-30% increase in productivity after implementing robotic welding and assembly systems. This translates to thousands of additional vehicles produced annually per factory.
- Electronics Manufacturing: Robotic automation has led to a 15-25% increase in production volume in electronics assembly, primarily due to faster component placement and reduced error rates.
- Food and Beverage Processing: Robotic systems have boosted packaging and palletizing efficiency by 20-30%, reducing labor costs and improving output.
- Pharmaceutical Manufacturing: Robots are crucial for precise and sterile handling of medications, leading to a 10-15% increase in output and reduced risk of contamination.
These examples illustrate the widespread impact of robotics on manufacturing productivity, showcasing its ability to drive significant improvements across diverse sectors.
Adaptability and Flexibility in Manufacturing: How Robotics Is Changing The Manufacturing Of Consumer Products
The rise of robotics in manufacturing isn’t just about increased speed and precision; it’s fundamentally reshaping the industry’s ability to adapt. Traditional assembly lines, while efficient for mass production of a single product, struggle to keep pace with the ever-changing demands of modern consumers. Robotic systems, however, offer a level of flexibility previously unimaginable, allowing manufacturers to respond quickly to market shifts and customize products with ease.
Robotic systems are proving invaluable in navigating the complexities of modern manufacturing, particularly in their capacity to handle fluctuating demands and product diversification. This adaptability stems from their inherent reprogrammability and the integration of advanced software and sensors. This allows manufacturers to quickly adjust production lines to meet shifting consumer preferences and market demands.
Reprogrammable Robots and Flexible Production Lines
Reprogrammable robots are the backbone of flexible manufacturing. Unlike fixed automation, which is designed for a specific task and product, these robots can be easily reprogrammed to perform different tasks. This means a single robot, or a network of robots, can be deployed to manufacture a variety of products on the same production line. For instance, a robot arm initially programmed to assemble smartphones could be reprogrammed to assemble tablets or even smaller electronic devices with minimal downtime. This versatility reduces the need for multiple, specialized assembly lines, saving significant capital expenditure and floor space. Advanced software allows for seamless transitions between different product configurations, minimizing disruption and maximizing efficiency.
Managing Fluctuating Order Volumes and Product Customization
Flexible automation solutions, powered by robotic systems, are ideally suited for managing fluctuating order volumes and the increasing demand for product customization. Manufacturers can easily scale up or down their production based on real-time demand forecasts, adjusting the number of robots operating on a given task. This responsiveness is crucial in today’s market, where demand can fluctuate dramatically due to seasonal trends, marketing campaigns, or unexpected events. Furthermore, the ability to reprogram robots allows manufacturers to easily accommodate customer requests for customized products. A robotic system can be programmed to incorporate different components or perform unique assembly steps, catering to individual customer preferences without significantly impacting production speed or efficiency. This level of customization enhances customer satisfaction and strengthens brand loyalty.
Comparison of Robotic Systems and Fixed Automation, How Robotics is Changing the Manufacturing of Consumer Products
The flexibility offered by robotic systems is a significant advantage over traditional fixed automation lines. The following table highlights the key differences:
Feature | Robotic System | Fixed Automation | Advantage of Robotic System |
---|---|---|---|
Adaptability to Product Changes | High; easily reprogrammable | Low; requires significant re-engineering | Reduced downtime and capital expenditure when product lines change. |
Handling Fluctuating Demand | High; easily scalable | Low; inflexible capacity | Optimized resource utilization and responsiveness to market changes. |
Customization Capabilities | High; allows for diverse product variations | Low; limited to pre-defined configurations | Enhanced customer satisfaction and market competitiveness through personalized products. |
Return on Investment (ROI) | Faster ROI due to flexibility and adaptability | Slower ROI due to rigidity and limited adaptability | Faster return on investment due to adaptability and broader application potential. |
The Impact on the Workforce
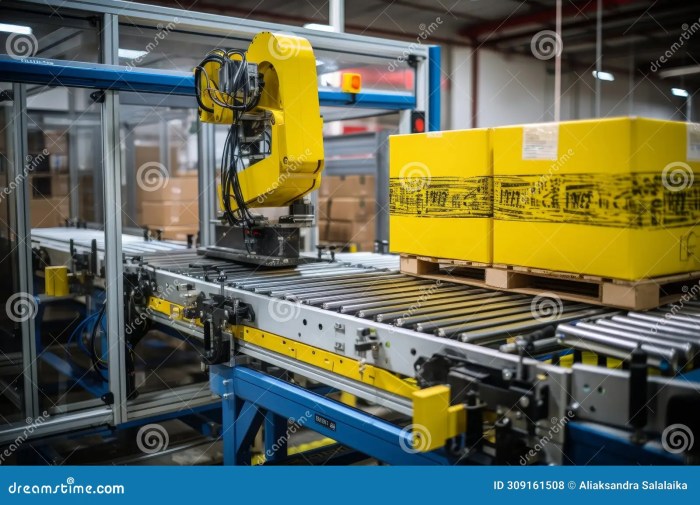
Source: dreamstime.com
Robots are revolutionizing consumer product manufacturing, boosting efficiency and precision. This same robotic revolution is impacting other sectors too, like healthcare; check out this insightful article on The Role of Robotics in Supporting the Healthcare Industry to see how. Ultimately, the rise of robotics promises a future of streamlined processes and improved quality across numerous industries, including, of course, consumer goods production.
The rise of robotics in manufacturing is undeniably reshaping the job landscape. While fears of widespread job displacement are understandable, the reality is more nuanced. Automation is changing the types of jobs available, demanding new skills and creating opportunities for upskilling and reskilling. This shift necessitates a proactive approach from both employers and employees to navigate this evolving environment successfully.
The integration of robots into manufacturing processes necessitates a shift in the required skillset for workers. Traditional manual labor roles are being augmented or replaced by roles requiring expertise in programming, maintenance, and data analysis related to robotic systems. This transition requires a significant investment in training and development programs to bridge the gap between existing worker skills and the demands of the automated factory floor.
Changes in Job Roles and Skills
Increased automation leads to a decrease in demand for repetitive, manual labor tasks. Jobs involving operating simple machinery are becoming less prevalent, replaced by roles focused on overseeing and maintaining sophisticated robotic systems. The need for skilled technicians capable of programming, troubleshooting, and repairing robots is increasing significantly. Data analysts are also becoming crucial, interpreting the vast amounts of data generated by automated systems to optimize production processes and predict potential issues. Furthermore, roles focused on integrating robots into existing workflows and managing human-robot collaboration are emerging. These roles require a blend of technical expertise and strong interpersonal skills.
Upskilling and Reskilling Initiatives
Addressing the evolving workforce needs requires a concerted effort in upskilling and reskilling initiatives. Governments, educational institutions, and manufacturers themselves must collaborate to provide accessible and relevant training programs. These programs should focus on developing skills in areas like robotics programming, automation maintenance, data analytics, and human-robot collaboration. Companies can invest in on-the-job training, apprenticeships, and partnerships with vocational schools to equip their workforce with the necessary skills. Furthermore, government-sponsored initiatives can provide funding and resources to support these upskilling and reskilling efforts, ensuring a smoother transition for workers affected by automation. For example, Germany’s “Industry 4.0” initiative focuses heavily on reskilling programs to support the integration of automation in manufacturing.
Collaborative Robots (Cobots) and Human-Robot Collaboration
The increasing prevalence of collaborative robots, or cobots, is transforming the manufacturing landscape. Cobots are designed to work safely alongside human workers, performing tasks that are either too dangerous, repetitive, or physically demanding for humans. They handle heavy lifting, precise assembly tasks, and other physically strenuous operations, freeing up human workers to focus on tasks requiring higher-level cognitive skills, such as quality control, problem-solving, and process optimization. This collaborative approach enhances efficiency, improves safety, and creates a more productive and fulfilling work environment. For instance, in automotive manufacturing, cobots assist human workers with assembly tasks, reducing the risk of workplace injuries and improving overall production speed.
Potential Effects on Employment Levels
The impact of robotic automation on employment levels varies across different manufacturing sectors. While some sectors might experience job displacement in the short term, others may see an overall increase in employment due to increased productivity and the creation of new, higher-skilled jobs.
- Automotive Manufacturing: Significant automation, potentially leading to job displacement in some assembly roles, but also creating demand for skilled technicians and engineers.
- Electronics Manufacturing: High level of automation already in place, with potential for further automation and job displacement in low-skill roles, but also increasing demand for specialized technicians.
- Food and Beverage Manufacturing: Increasing use of robots for packaging and handling, potentially affecting some low-skill jobs, but also creating demand for maintenance and programming specialists.
- Pharmaceutical Manufacturing: Automation is crucial for maintaining high levels of precision and hygiene, potentially increasing overall employment due to higher demand for skilled workers.
It’s important to note that these are potential effects, and the actual impact will depend on various factors, including the pace of technological advancements, government policies, and the adaptability of the workforce.
Safety and Ergonomics in Manufacturing
The integration of robots into manufacturing isn’t just about boosting productivity; it’s fundamentally reshaping workplace safety and ergonomics. By taking on dangerous and physically demanding tasks, robots are creating a healthier and more secure environment for human workers, leading to fewer injuries and improved overall well-being. This shift towards automation is not just a technological advancement, but a crucial step towards a more humane and efficient manufacturing process.
Robots contribute significantly to a safer working environment by handling tasks that pose risks to human workers. These include working with hazardous materials, operating heavy machinery, and performing repetitive movements that can lead to musculoskeletal disorders. The elimination of these risks directly translates into a reduction in workplace accidents and injuries, improving the overall health and safety of the workforce.
Robotic Applications Reducing Workplace Injuries and Improving Worker Ergonomics
Several robotic applications directly address workplace safety and ergonomic concerns. For instance, robots are used extensively in welding, a process that exposes workers to harmful fumes and intense heat. Similarly, robots are employed in tasks involving heavy lifting and material handling, significantly reducing the risk of back injuries and other musculoskeletal problems. In the automotive industry, robots perform repetitive tasks like painting and assembling car parts, eliminating the strain and potential for repetitive strain injuries (RSIs) on human workers. These applications not only increase safety but also improve the quality of life for employees by reducing physical strain and the risk of long-term health issues.
Safety Features and Protocols for Safe Human-Robot Collaboration
Safe human-robot collaboration requires careful planning and implementation of safety features and protocols. Robots are equipped with various safety mechanisms, such as emergency stop buttons, sensors that detect human presence, and speed and force limiting systems. These features ensure that robots operate safely alongside human workers, minimizing the risk of accidents. Furthermore, comprehensive safety training for human workers is crucial to ensure they understand how to interact with robots safely and effectively. This training covers safe operating procedures, emergency response protocols, and awareness of potential hazards. Regular maintenance and inspection of robotic systems are also vital in preventing malfunctions and ensuring continued safe operation.
A Collaborative Manufacturing Environment
Imagine a brightly lit, spacious factory floor. A team of human workers is collaborating seamlessly with a fleet of collaborative robots (cobots). These cobots, with their rounded edges and bright yellow exteriors, are performing tasks like assembling small electronic components, their movements precise and controlled. The human workers are focused on higher-level tasks such as quality control and troubleshooting, leveraging their cognitive abilities and problem-solving skills. Safety sensors on the cobots ensure that they automatically slow down or stop if a human worker enters their workspace. Emergency stop buttons are strategically placed throughout the area, and clear visual indicators display the operational status of each robot. The overall atmosphere is one of efficiency, collaboration, and safety, with both human workers and robots contributing to a streamlined and productive manufacturing process. The environment is clean, well-lit, and organized, reflecting a commitment to both productivity and worker well-being.
Concluding Remarks
The integration of robotics in consumer product manufacturing isn’t just a trend; it’s the future. While challenges remain, particularly concerning workforce adaptation, the benefits—increased efficiency, superior quality, and enhanced safety—are undeniable. The manufacturing landscape is evolving at breakneck speed, and those who embrace robotic automation will be best positioned to thrive in this new era of hyper-efficient, highly customized production. The question isn’t *if* robotics will dominate, but *how* we’ll harness its power to create a more innovative and sustainable future for all.