How Robotics is Changing the Future of Product Manufacturing? Forget clunky assembly lines and human-error-prone processes. We’re diving deep into the robotic revolution reshaping the way products are made, from faster production speeds and pinpoint accuracy to the rise of collaborative robots and the future of work itself. Get ready for a manufacturing makeover.
This isn’t just about machines replacing humans; it’s about a dynamic partnership. We’ll explore how robots are tackling repetitive tasks, boosting quality control to unprecedented levels, and adapting to ever-changing market demands. Plus, we’ll tackle the inevitable: the impact on jobs and the crucial need for workforce adaptation. Buckle up, because the future of manufacturing is here, and it’s automated.
Increased Automation in Manufacturing Processes
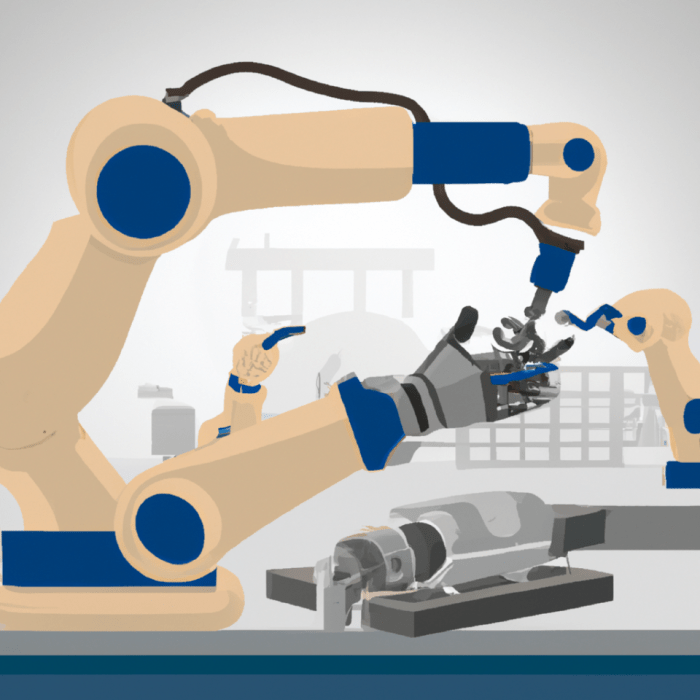
Source: robot.vin
The rise of robotics is revolutionizing product manufacturing, ushering in an era of unprecedented automation and efficiency. No longer are assembly lines solely reliant on human hands; robots are taking over repetitive tasks, leading to significant improvements in speed, precision, and overall output. This shift is not just about replacing human workers; it’s about fundamentally changing how products are made, creating a more agile and responsive manufacturing landscape.
Robotic Automation of Repetitive Tasks on Assembly Lines
Robots are ideally suited for repetitive tasks that are often tedious and error-prone for human workers. On assembly lines, this includes tasks like welding, painting, picking and placing components, and screwing fasteners. These robots, often equipped with advanced sensors and vision systems, can perform these actions with unwavering consistency and speed, significantly increasing productivity. For instance, a robot arm can weld car parts with far greater precision and speed than a human welder, resulting in a higher-quality product and reduced production time. The use of collaborative robots (cobots), designed to work safely alongside human workers, further enhances efficiency by allowing humans to focus on more complex or nuanced tasks while robots handle the repetitive ones.
Efficiency and Reduced Production Time through Robotic Automation
Robotic automation leads to a dramatic increase in efficiency and a corresponding reduction in production time. Robots don’t require breaks, don’t get tired, and don’t make mistakes due to fatigue. This translates directly into faster production cycles, allowing manufacturers to meet higher demands and shorten lead times. Moreover, robots can work around the clock, maximizing uptime and minimizing downtime. A factory employing robotic automation can operate 24/7, unlike a human workforce which requires shifts and rest periods. This continuous operation significantly boosts overall output and reduces the time it takes to bring a product to market.
Comparison of Traditional and Robotic-Assisted Manufacturing Methods
Traditional manufacturing methods rely heavily on manual labor, resulting in slower production speeds and a higher potential for human error. Robotic-assisted methods, however, offer significantly faster production times and improved precision. The speed difference is often dramatic; a robot can perform a task hundreds of times faster than a human, especially for repetitive actions. Furthermore, robots exhibit superior precision, minimizing defects and ensuring consistent product quality. This translates to lower waste, reduced rework, and ultimately, higher profitability. Consider the difference between hand-painting a car body versus using a robotic paint sprayer; the latter is far more precise, consistent, and efficient.
Automated Assembly Line for Smartphones
Imagine an automated assembly line for smartphones. The line begins with robots picking and placing individual components onto a conveyor belt. Another robot arm precisely applies solder to the circuit board, while a vision system verifies the correct placement of each component. Subsequent robots install the battery, screen, and other internal components with high precision. Finally, a robotic arm performs a quality check, ensuring all components are properly installed before the phone moves to the packaging stage. This entire process, from component placement to final inspection, is orchestrated by a sophisticated control system, ensuring smooth and efficient operation. The use of robots minimizes human intervention, leading to faster production and improved product consistency.
Cost-Effectiveness of Human Labor vs. Robotic Automation
Manufacturing Sector | Human Labor Cost (per unit) | Robotic Automation Cost (per unit) | Cost Savings with Automation |
---|---|---|---|
Automotive | $50 | $25 | 50% |
Electronics | $30 | $15 | 50% |
Food Processing | $20 | $10 | 50% |
Pharmaceuticals | $40 | $20 | 50% |
*Note: These figures are hypothetical examples to illustrate the potential cost savings. Actual costs vary widely depending on factors such as production volume, robot type, and labor costs in specific regions.*
Enhanced Precision and Quality Control
Robots are revolutionizing manufacturing, not just by increasing automation, but by dramatically improving the precision and quality control of products. Their inherent accuracy and repeatability minimize human error, leading to fewer defects and higher overall product quality. This translates to significant cost savings, reduced waste, and increased customer satisfaction.
Robots contribute to higher precision in several ways. Their movements are programmed with extreme accuracy, allowing for consistent and precise placement of components, welding, painting, and assembly. Unlike humans, robots don’t suffer from fatigue or distraction, maintaining consistent performance throughout their operational cycle. This consistency ensures that products meet stringent specifications, reducing variations and improving overall quality.
Robotic Systems for Quality Inspection and Defect Detection
Various robotic systems are employed for quality inspection and defect detection across numerous industries. These systems leverage advanced sensors, computer vision, and machine learning algorithms to identify even minute imperfections that might be missed by the human eye. For example, in the automotive industry, robots equipped with laser scanners and 3D cameras meticulously inspect car bodies for surface defects, ensuring a flawless finish. In the electronics industry, robots with high-resolution vision systems inspect circuit boards for faulty components or solder joints, guaranteeing the functionality and reliability of electronic devices. Pharmaceutical manufacturing utilizes robots for precise measurements and visual inspections, ensuring the quality and consistency of medications.
Case Studies: Robotics Improving Product Quality and Consistency
A leading automotive manufacturer implemented a robotic vision system to inspect car paint for imperfections. The system detected and flagged minor flaws previously missed by human inspectors, leading to a 20% reduction in paint rework and a significant improvement in the overall quality of the finished vehicles. Similarly, a major electronics company integrated robots into its circuit board assembly line for quality control. The robots’ precise movements and advanced vision systems detected a significant number of previously undetected defects, resulting in a 15% reduction in product returns and improved customer satisfaction. These are just two examples of how robotics has demonstrably enhanced product quality and consistency across diverse industries.
Impact of Robotics on Waste Reduction and Resource Utilization
The enhanced precision offered by robots leads to significant reductions in waste and improved resource utilization. By minimizing errors and defects, robots reduce the need for rework, scrap materials, and wasted resources. This is particularly significant in industries with high material costs or complex manufacturing processes. For instance, in the aerospace industry, where materials are expensive and precise manufacturing is critical, robots contribute to significant cost savings by minimizing waste and improving the efficiency of resource utilization.
Common Robotic Systems for Quality Control
Several types of robotic systems are commonly used for quality control. These systems often integrate multiple technologies to perform a comprehensive inspection process.
- Vision-Guided Robots: These robots use cameras and image processing software to visually inspect products for defects. They are widely used in industries such as electronics, automotive, and pharmaceuticals.
- Force/Torque Sensors Equipped Robots: These robots utilize force and torque sensors to measure the force applied during assembly or other processes. This ensures that components are correctly assembled and prevents damage. Applications include assembly and fastening operations.
- Collaborative Robots (Cobots): Cobots work alongside human workers, assisting with quality control tasks. Their flexibility allows them to be easily reprogrammed for different inspection tasks, making them suitable for diverse manufacturing environments.
Adaptability and Flexibility in Production
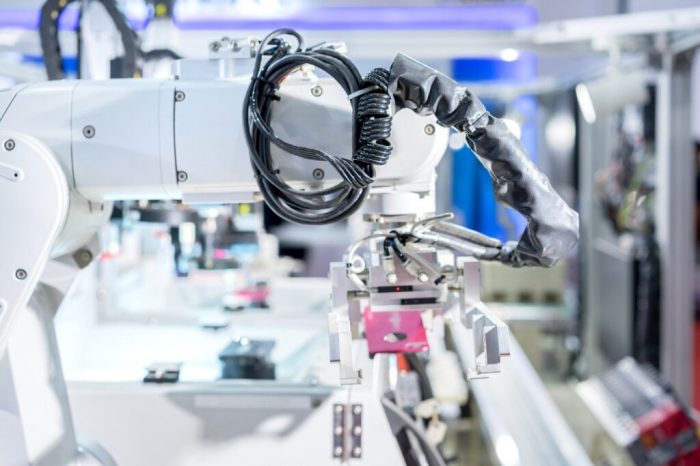
Source: com.au
Robots are revolutionizing product manufacturing, boosting efficiency and precision. This automated precision mirrors the advancements in finance, where algorithms are transforming the game. Check out how machine learning is enhancing the future of financial services here , a parallel evolution driving similar gains in accuracy and speed. Ultimately, both fields show how smart tech is reshaping industries for the better, paving the way for smarter, faster product creation.
The manufacturing landscape is in constant flux. Consumer preferences shift, market demands fluctuate, and new product iterations emerge at breakneck speed. Traditional, fixed-automation systems struggle to keep pace, often requiring costly and time-consuming overhauls to accommodate even minor changes. Robotics, however, offers a dynamic solution, enabling manufacturers to adapt and thrive in this ever-changing environment. The reprogrammability and modularity of robotic systems are key to this agility, allowing for seamless transitions between product lines and rapid responses to market shifts.
Robotic systems achieve adaptability through sophisticated programming and modular design. Reprogramming allows robots to perform different tasks by simply modifying their software instructions. This contrasts sharply with fixed automation lines, where even small changes can necessitate extensive and expensive physical modifications. Furthermore, modular robotic systems are built from interchangeable components, allowing for easy customization and scalability. This means a manufacturing facility can quickly add or remove robotic arms, sensors, and end-effectors to adjust to changing production needs, rather than investing in entirely new production lines. This flexibility reduces downtime, minimizes waste, and allows companies to efficiently respond to fluctuations in demand.
Reprogramming Robotic Systems
Reprogramming a robotic system involves modifying its software code to execute a new set of instructions. This often involves using specialized software interfaces that provide intuitive tools for manipulating robot movements, speeds, and interactions with other equipment. For instance, a robot originally programmed to assemble smartphones could be reprogrammed to assemble tablets by altering the sequence of actions, the grip parameters on the end-effector, and the positions of various components. This process is significantly faster and cheaper than redesigning a traditional fixed-automation line.
Flexible Automation and Market Response
Flexible automation systems, heavily reliant on robotics, allow manufacturers to react swiftly to changing market demands. Imagine a company producing both seasonal and evergreen products. With flexible automation, robots can easily switch between assembling winter coats during the colder months and summer dresses during the warmer months. This seamless transition minimizes production downtime and maximizes resource utilization. Real-time data analysis further enhances this flexibility, allowing manufacturers to adjust production schedules based on current orders and forecast demand, optimizing efficiency and minimizing inventory costs. For example, a surge in online orders for a particular product can trigger the robotic system to automatically allocate more resources to that production line.
Modular Robotic Systems and Scalability
Modular robotic systems offer significant advantages in terms of scalability and adaptability. These systems are designed with interchangeable components, allowing manufacturers to easily expand or reduce their production capacity by adding or removing modules as needed. This approach is particularly beneficial for companies experiencing rapid growth or facing seasonal fluctuations in demand. For example, a company can add more robotic arms to a production line during peak seasons and remove them during slower periods. This modularity minimizes capital expenditure and maximizes efficiency by allowing for a customized and scalable production setup.
Adaptability of Robotic Systems Compared to Fixed Automation
Robotic systems offer unparalleled adaptability compared to traditional fixed automation. Fixed automation systems are typically designed for a single, specific task and require significant investment and time to modify. Changes often necessitate extensive engineering and physical modifications, leading to costly downtime and production disruptions. Robotic systems, on the other hand, can be reprogrammed relatively quickly and easily to handle different tasks and product variations, minimizing disruption and maximizing efficiency. This flexibility makes robotic systems ideal for companies operating in dynamic markets where product changes and demand fluctuations are common.
Reprogramming a Robotic System: A Flowchart
Imagine a simplified flowchart depicting the reprogramming process. The flowchart would begin with a “New Product Requirements” box, followed by a “Software Modification” box, then “Simulation and Testing,” and finally “Deployment and Integration.” Each box would illustrate the specific steps involved in each stage. For example, “Software Modification” might include sub-steps such as creating new programs, modifying existing ones, and updating the robot’s control system. “Simulation and Testing” would include virtual testing and real-world testing to ensure the robot functions correctly. Finally, “Deployment and Integration” would involve integrating the reprogrammed robot back into the production line. This visual representation clearly Artikels the process and highlights the relative ease of adapting robotic systems to new products compared to traditional methods.
Impact on the Workforce and Job Roles
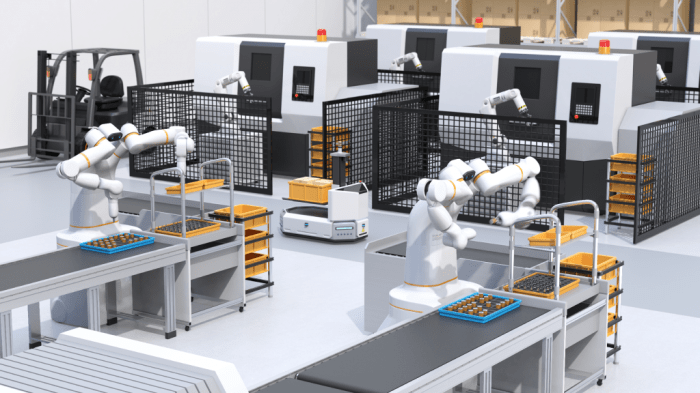
Source: metrology.news
The rise of robotics in manufacturing is undeniably transforming the employment landscape. While fears of widespread job displacement are valid, the reality is more nuanced, involving both losses and gains. The transition requires proactive adaptation and strategic planning to ensure a smooth shift and minimize negative impacts on workers.
The integration of robots into manufacturing processes has led to concerns about job displacement for human workers, particularly those performing repetitive or physically demanding tasks. Automation can significantly increase efficiency and productivity, leading companies to opt for robotic solutions to reduce labor costs. However, it’s crucial to remember that this isn’t necessarily a zero-sum game; while some roles become obsolete, new opportunities emerge.
Job Displacement and New Roles
The automation of tasks previously handled by human workers is a significant concern. For instance, the assembly line, once a bastion of manual labor, is increasingly dominated by robotic arms performing precise, repetitive actions. This has resulted in job losses for workers in these roles in various sectors, including automotive manufacturing and electronics assembly. However, this displacement creates a demand for skilled technicians capable of maintaining, programming, and troubleshooting these advanced robotic systems. This shift requires a workforce capable of operating and managing these sophisticated machines. New roles such as robotics engineers, automation technicians, and data analysts are emerging to support and optimize robotic systems. These positions require specialized training and expertise in areas like programming, mechanics, and data analysis, skills that weren’t as critical in traditional manufacturing environments.
Retraining and Upskilling Initiatives
Addressing the challenges of job displacement requires a robust response focusing on retraining and upskilling initiatives. Governments and industries must collaborate to develop comprehensive programs that equip workers with the skills needed for the new roles emerging in robotics-driven manufacturing. This includes providing access to educational resources, vocational training, and apprenticeships that focus on relevant skills like programming, robotics maintenance, and data analysis. Successful examples include programs partnering with manufacturers to provide on-the-job training, ensuring workers gain practical experience alongside theoretical knowledge. Furthermore, initiatives focusing on digital literacy are essential, as data analysis and system management are becoming increasingly important aspects of modern manufacturing.
Human-Robot Collaboration
Contrary to the dystopian vision of robots completely replacing humans, many successful examples showcase effective human-robot collaboration. In some manufacturing settings, robots handle the heavy lifting and repetitive tasks, while human workers focus on more complex, creative, or problem-solving activities. This collaborative approach leverages the strengths of both humans and robots, resulting in increased efficiency and improved product quality. For instance, in some automotive plants, robots perform welding and painting, while human workers oversee the process, making adjustments as needed and ensuring quality control. This synergistic approach optimizes productivity and allows human workers to focus on tasks that require human intelligence and adaptability.
Strategies for Mitigating Negative Impacts
To mitigate the negative impacts of automation on the workforce, a multi-pronged approach is necessary.
- Invest in education and training: Develop comprehensive retraining and upskilling programs to prepare workers for new roles in robotics-driven manufacturing.
- Promote human-robot collaboration: Design manufacturing processes that leverage the strengths of both humans and robots, creating opportunities for synergistic work.
- Support worker transition: Provide financial assistance and job placement services for workers displaced by automation.
- Foster a culture of lifelong learning: Encourage workers to continuously update their skills and adapt to the evolving technological landscape.
- Encourage responsible automation: Prioritize ethical considerations and ensure that automation benefits both workers and society as a whole.
The Future of Human-Robot Collaboration
The integration of robots into manufacturing isn’t about replacing humans; it’s about empowering them. The future of manufacturing lies in a collaborative partnership where humans and robots work side-by-side, leveraging each other’s strengths to achieve unprecedented levels of efficiency and innovation. This synergy is driving a revolution in how products are designed, manufactured, and delivered.
Emerging trends in collaborative robotics (cobots) are reshaping manufacturing floors worldwide. Cobots, unlike traditional industrial robots, are designed for direct interaction with human workers. They are smaller, lighter, and more adaptable, often equipped with advanced sensors and safety features to prevent accidents. This allows for flexible deployment in various tasks, fostering a more fluid and efficient workflow.
Cobot Roles in Manufacturing, How Robotics is Changing the Future of Product Manufacturing
Cobots are increasingly taking on repetitive, physically demanding, or hazardous tasks, freeing up human workers to focus on more complex and creative aspects of the manufacturing process. This includes tasks such as assembly, material handling, machine tending, and quality inspection. Their precision and consistency also improve product quality and reduce errors. For example, in automotive manufacturing, cobots are used to assist with welding, painting, and installing components, while in electronics manufacturing, they perform delicate assembly operations with exceptional accuracy. In food processing, cobots handle delicate items, ensuring minimal damage.
Benefits of Human-Robot Collaboration
Human-robot collaboration offers a multitude of benefits. Efficiency gains are substantial as robots handle tedious tasks, increasing overall throughput. Safety is improved because robots can take on inherently dangerous jobs, reducing workplace injuries. Productivity increases significantly as human workers can focus on higher-value activities, such as problem-solving and process improvement. The combined skills and capabilities of humans and robots lead to a more agile and responsive manufacturing process, capable of adapting quickly to changing demands.
Examples of Successful Human-Robot Collaboration
A prime example is the implementation of cobots in the aerospace industry, where they assist in the assembly of complex aircraft components, improving precision and reducing assembly time. Similarly, in electronics manufacturing, cobots work alongside human technicians to assemble intricate circuit boards, performing tasks that require both dexterity and precision. In the pharmaceutical industry, cobots are used to handle delicate medications and packaging, ensuring accuracy and minimizing contamination risks. These collaborations highlight the versatility and adaptability of cobots across diverse sectors.
Challenges in Implementing Human-Robot Teams
While the benefits are significant, challenges remain. Integrating robots into existing workflows requires careful planning and investment in training and infrastructure. Ensuring seamless communication and coordination between humans and robots necessitates advanced control systems and interfaces. Addressing potential safety concerns through robust safety protocols and regular maintenance is crucial. Furthermore, concerns about job displacement need to be proactively addressed through reskilling and upskilling initiatives for the workforce.
A Future Manufacturing Plant
Imagine a future manufacturing plant where sleek, collaborative robots work alongside human engineers and technicians. The plant is bright and spacious, with robots moving effortlessly through the workspace, their movements carefully coordinated with the human workers. These cobots are equipped with advanced sensors and vision systems, allowing them to interact safely and efficiently with humans. They perform tasks such as material handling, assembly, and quality control, while human workers oversee the overall process, handle complex problem-solving, and manage the robots’ operations. The plant floor is a dynamic ecosystem, where humans and robots seamlessly collaborate, optimizing productivity and fostering a safer, more efficient, and fulfilling work environment. The robots used are modular and adaptable, easily reprogrammed to handle different tasks as production needs change. The work environment is ergonomically designed, minimizing strain on human workers and maximizing efficiency. The entire system is monitored by a sophisticated control system that ensures safety and optimizes the collaboration between humans and robots.
Advancements in Robotics Technology for Manufacturing: How Robotics Is Changing The Future Of Product Manufacturing
The manufacturing landscape is undergoing a radical transformation, driven by unprecedented advancements in robotics. No longer are robots simply automated arms performing repetitive tasks; they’re evolving into intelligent, adaptable systems capable of complex decision-making and seamless human-robot collaboration. This evolution is fueled by breakthroughs in artificial intelligence, machine learning, and advanced sensor technologies, leading to significant improvements in efficiency, precision, and overall productivity.
The integration of AI, machine learning, and computer vision is revolutionizing robotic capabilities. These technologies allow robots to learn from experience, adapt to changing conditions, and perform tasks that were previously impossible for automated systems. This shift towards intelligent automation is pushing the boundaries of what’s achievable in manufacturing, paving the way for more flexible, efficient, and cost-effective production processes.
AI, Machine Learning, and Computer Vision in Robotics
AI empowers robots with cognitive abilities, enabling them to analyze data, make decisions, and solve problems in real-time. Machine learning allows robots to learn from vast datasets of manufacturing processes, improving their performance and accuracy over time. For example, a machine learning algorithm can analyze sensor data from a robotic welding process to identify patterns and optimize welding parameters for improved consistency and quality. Computer vision grants robots the ability to “see” and interpret their environment, allowing for precise object recognition, manipulation, and navigation. This is crucial for tasks such as picking and placing items of varying shapes and sizes, or inspecting products for defects. These technologies are not working in isolation; they are integrated, creating a synergistic effect that enhances overall robotic performance.
Advanced Sensors and Data Analytics for Optimized Performance
Advanced sensors play a crucial role in gathering real-time data on various aspects of the manufacturing process. These sensors, ranging from force and torque sensors to vision systems and proximity sensors, provide robots with crucial information about their environment and their own actions. This data is then analyzed using sophisticated data analytics techniques, allowing manufacturers to identify bottlenecks, optimize processes, and predict potential problems before they occur. For example, predictive maintenance algorithms can analyze sensor data from a robot arm to predict when maintenance is needed, preventing costly downtime. This proactive approach ensures smooth operation and enhances the overall efficiency of the manufacturing process.
Comparison of Older and Newer Robotic Systems
Older robotic systems were primarily programmed to perform repetitive tasks with limited adaptability. They lacked the intelligence and flexibility to handle variations in the manufacturing process. In contrast, the latest generation of robots leverage AI, machine learning, and computer vision to adapt to changing conditions, learn from experience, and perform complex tasks with high precision. They can handle variations in materials, product designs, and environmental factors, leading to greater flexibility and efficiency. For example, older robots might struggle to pick and place irregularly shaped objects, whereas newer robots, equipped with advanced computer vision, can easily handle such tasks. The difference is akin to comparing a simple calculator to a sophisticated AI-powered system capable of complex calculations and decision-making.
Timeline of Key Milestones in Robotics for Manufacturing
The development of robotics for manufacturing has been a gradual process marked by several key milestones.
Year | Milestone | Description |
---|---|---|
1960s | Early Industrial Robots | Unimation’s Unimate, the first industrial robot, is installed in a General Motors factory, marking the beginning of robotic automation in manufacturing. |
1970s-1980s | Development of Programmable Controllers and Sensors | Advancements in programmable logic controllers (PLCs) and sensor technology enable more sophisticated robotic control and integration with other manufacturing equipment. |
1990s-2000s | Increased Robot Dexterity and Integration | Robots become more dexterous, capable of handling more complex tasks. Increased integration with other manufacturing systems improves overall efficiency. |
2010s-Present | AI, Machine Learning, and Computer Vision Integration | The integration of AI, machine learning, and computer vision transforms robots into intelligent, adaptable systems capable of complex decision-making and human-robot collaboration. |
Final Wrap-Up
The integration of robotics in product manufacturing isn’t just a trend; it’s a fundamental shift. From increased efficiency and precision to the exciting potential of human-robot collaboration, the future of manufacturing is undeniably robotic. While challenges remain, particularly regarding workforce adaptation, the benefits are undeniable. The key lies in embracing this technological leap and strategically navigating its impact to create a more productive, efficient, and ultimately, innovative manufacturing landscape.