How Robotics is Changing the Future of Industrial Automation: Forget clunky assembly lines – the future of manufacturing is here, and it’s robotic. We’re diving deep into the automation revolution, exploring how robots are supercharging efficiency, precision, and safety across industries. From collaborative robots working hand-in-hand with humans to AI-powered systems learning on the fly, the changes are nothing short of mind-blowing. Get ready to witness how this tech is reshaping the very fabric of industrial production.
This isn’t just about replacing human workers; it’s about a powerful partnership. We’ll unpack the ways robots are tackling dangerous tasks, boosting productivity to unprecedented levels, and even creating entirely new job opportunities. We’ll also address the concerns surrounding job displacement and explore the solutions driving a smooth transition into this new era of manufacturing. Prepare for a fascinating journey into the heart of the industrial automation revolution.
Increased Efficiency and Productivity in Manufacturing
Robotic automation is revolutionizing industrial manufacturing, significantly boosting efficiency and productivity. The integration of robots into various processes allows for faster production cycles, higher output, and ultimately, lower costs. This shift towards automation is not just about replacing human workers; it’s about optimizing workflows and creating a more efficient and competitive manufacturing landscape.
Robots excel at performing repetitive tasks with high precision and speed, far exceeding human capabilities in many areas. This enhanced speed and accuracy translate directly into increased manufacturing output and a reduced error rate, minimizing waste and rework. Furthermore, robots can operate continuously, unlike human workers who require breaks and rest periods, leading to significantly higher production volume in a given timeframe.
Examples of Robotic Efficiency in Industrial Processes
The impact of robotic automation is evident across various manufacturing sectors. Consider the automotive industry, where robots are extensively used for welding, painting, and assembly. These robots perform tasks with incredible speed and precision, leading to a dramatic increase in vehicle production rates and a significant reduction in defects. Similarly, in electronics manufacturing, robots are crucial for tasks like component placement and soldering, ensuring consistent quality and speed in assembling intricate devices. The food processing industry also benefits, using robots for packaging, palletizing, and other repetitive actions, improving hygiene standards and output.
Cost Reduction Through Robotic Implementation
While the initial investment in robotic systems can be substantial, the long-term cost savings are considerable. Robots reduce labor costs by minimizing the need for human workers in repetitive, strenuous tasks. They also reduce material waste through improved accuracy, minimizing errors and the need for rework. Furthermore, robots can operate around the clock, increasing production volume without incurring overtime pay. The reduction in downtime due to fewer errors and consistent performance further contributes to significant cost savings. These factors combine to provide a compelling return on investment (ROI) for businesses adopting robotic automation.
Comparison of Human Labor and Robotic Automation
The following table illustrates the comparative advantages of robotic automation over human labor in various manufacturing processes:
Process | Human Labor (Time/Cost) | Robotic Automation (Time/Cost) | Efficiency Gain |
---|---|---|---|
Welding Car Bodies | High time, high cost per unit | Significantly reduced time, lower cost per unit | 50-75% increase in production speed and cost reduction |
Packaging Food Items | Moderate time, moderate cost per unit, potential for human error | Reduced time, lower cost per unit, minimal errors | 30-50% increase in production speed and cost reduction, significant improvement in consistency |
Circuit Board Assembly | Very high time, high cost per unit, high error rate | Substantially reduced time, significantly lower cost per unit, minimal errors | 70-90% increase in production speed and cost reduction, drastic improvement in quality |
Painting Automotive Parts | High time, high cost per unit, inconsistent finish | Significantly reduced time, lower cost per unit, consistent, high-quality finish | 60-80% increase in production speed and cost reduction, significant improvement in quality |
Enhanced Precision and Quality Control: How Robotics Is Changing The Future Of Industrial Automation
Robots are revolutionizing industrial automation, not just by increasing speed and output, but also by dramatically improving the precision and consistency of manufacturing processes. Human error, a constant factor in traditional manufacturing, is significantly minimized, leading to higher quality products and reduced waste. This enhanced precision translates to tangible benefits across numerous industries, ultimately boosting profitability and competitiveness.
Robots excel in tasks demanding extreme accuracy and repeatability, areas where human capabilities often fall short. This precision isn’t just about speed; it’s about ensuring each product meets exacting specifications, every time. The result? A consistent, high-quality output that satisfies even the most demanding customers.
Robotic Precision in Manufacturing Processes
The superior precision of robots is particularly evident in processes like welding, painting, and assembly. In welding, robots can execute precise welds with consistent penetration and heat input, reducing defects and ensuring structural integrity. Painting applications benefit from robots’ ability to apply even coats with consistent thickness and coverage, minimizing waste and improving the final finish. Complex assembly tasks, involving intricate parts and tight tolerances, are performed flawlessly by robots, reducing the risk of human error and ensuring product consistency. The automotive industry, for example, relies heavily on robots for these tasks, producing vehicles with consistently high-quality finishes and reliable performance.
Robotics and Stringent Quality Control
Robotics plays a crucial role in implementing stringent quality control measures. Robots can perform automated inspections, identifying defects with greater accuracy and speed than human inspectors. They can utilize advanced sensors and vision systems to detect even minute imperfections, ensuring that only products meeting the highest quality standards leave the production line. This proactive approach to quality control reduces the need for extensive post-production inspections, saving time and resources while improving overall product quality. Moreover, data collected by robotic inspection systems can be used to identify trends and patterns in defects, enabling manufacturers to proactively address potential issues in their production processes.
Impact of Robotic Precision on Defect Rates
The following table illustrates the significant impact of robotic precision on defect rates across various manufacturing sectors. These figures are based on industry reports and case studies showcasing the real-world benefits of robotic automation. Note that the specific numbers can vary based on the complexity of the manufacturing process and the specific robots and sensors used.
Industry | Human Error Rate (%) | Robotic Error Rate (%) | Quality Improvement Percentage (%) |
---|---|---|---|
Automotive Assembly | 5-10 | 1-2 | 70-80 |
Electronics Manufacturing | 3-7 | 0.5-1 | 60-85 |
Pharmaceutical Production | 2-5 | 0.2-0.8 | 75-90 |
Aerospace Manufacturing | 4-8 | 0.5-1.5 | 70-85 |
Improved Workplace Safety
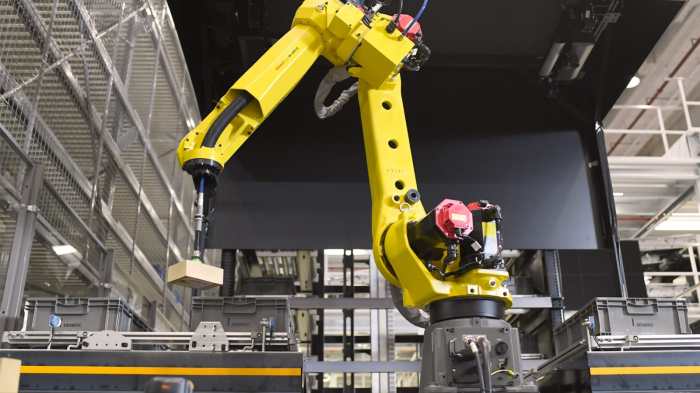
Source: dematic.com
Industrial automation’s getting a serious robotic upgrade, boosting efficiency and precision like never before. But the same tech isn’t just revolutionizing factories; it’s also transforming emergency response, as you can see in this fascinating article: How Robotics is Changing the Future of Emergency Response. These advancements in robotics, initially focused on industrial tasks, are now saving lives in hazardous situations, further highlighting the versatility and future potential of this rapidly evolving field.
Industrial robots aren’t just boosting efficiency; they’re revolutionizing workplace safety. By taking on dangerous and physically demanding tasks, robots are significantly reducing workplace accidents and creating a healthier environment for human workers. This shift towards automation is not just about increasing productivity; it’s about prioritizing the well-being of the workforce.
Robots are increasingly vital in minimizing human exposure to hazardous conditions, ultimately improving overall workplace safety. This is achieved through their ability to perform tasks that are too risky or strenuous for humans, leading to a substantial decrease in workplace injuries and fatalities. The implementation of robotic systems represents a proactive approach to risk mitigation, moving beyond reactive measures like safety training and protective equipment.
Hazardous Tasks Handled by Robots
Robots excel in handling hazardous materials, working in extreme environments, and performing repetitive, high-risk tasks. For instance, robots are routinely employed in the nuclear industry to handle radioactive materials, minimizing the risk of exposure to human workers. In the manufacturing of explosives, robots ensure precise handling and assembly, significantly reducing the potential for accidental detonation. Similarly, robots are used in deep-sea exploration and mining operations, performing tasks in environments that are impossible or incredibly dangerous for human divers or miners. These are just a few examples of how robots are paving the way for safer workplaces.
Examples of Robots Performing Dangerous Jobs
Consider the automotive industry, where robots are extensively used in welding and painting processes. These tasks often involve exposure to harmful fumes, intense heat, and repetitive motions that can lead to musculoskeletal disorders in humans. Robots perform these tasks with precision and consistency, eliminating the risk of human injury. In the chemical industry, robots handle the mixing and processing of hazardous chemicals, shielding workers from potential exposure to toxic substances. The deployment of robots in disaster relief scenarios, such as handling unstable structures or searching for survivors in hazardous environments, also showcases their life-saving capabilities.
Minimizing Risks to Human Workers
Robotic automation minimizes risks to human workers in several key ways. First, robots eliminate the need for humans to perform inherently dangerous tasks. Second, robots offer increased precision and consistency, reducing the likelihood of errors that could lead to accidents. Third, robots can work continuously without fatigue, maintaining consistent safety protocols. Finally, the implementation of robots allows for the redesign of workplaces to be more ergonomically friendly and less hazardous overall. The cumulative effect of these factors results in a significantly safer work environment for human employees.
Types of Industrial Accidents Prevented by Robotic Implementation
The implementation of robots has demonstrably reduced several types of industrial accidents.
- Burns and scalds: Robots can handle hot materials and processes, preventing burns to human workers.
- Crush injuries: Robots can operate heavy machinery and perform tasks in confined spaces, reducing the risk of crushing injuries.
- Exposure to hazardous materials: Robots can handle toxic chemicals and radioactive materials, preventing exposure and related health issues.
- Falls from heights: Robots can perform tasks at heights, eliminating the risk of falls for human workers.
- Electrocution: Robots can work with electricity, reducing the risk of electrocution to human workers.
- Repetitive strain injuries: Robots can perform repetitive tasks, reducing the risk of musculoskeletal disorders in human workers.
Adaptability and Flexibility in Production
The rise of robotics in industrial settings isn’t just about automating existing tasks; it’s about creating manufacturing processes that are agile, responsive, and capable of handling the ever-shifting demands of the modern market. Robots are no longer confined to repetitive, pre-programmed actions. Today’s advanced robotic systems offer a level of adaptability and flexibility that’s revolutionizing how businesses approach production.
Robotic systems are increasingly designed with modularity and reconfigurability in mind. This means that components can be easily swapped, reprogrammed, or rearranged to suit different production needs. This contrasts sharply with traditional, hard-automation methods which are often fixed and inflexible, making them expensive and difficult to adapt to changes in product design or market demand. The ability to quickly retool and redeploy robots offers significant advantages in terms of efficiency, cost-effectiveness, and overall competitiveness.
Reprogramming and Reconfiguration of Robotic Systems
Reprogramming robots for new tasks often involves using intuitive software interfaces and pre-built modules. For example, a robot arm initially programmed for welding car bodies might be reprogrammed to handle the assembly of electronics with minimal downtime. This is achieved through software updates and adjustments to the robot’s control algorithms, rather than requiring complete physical redesign. Reconfiguration, on the other hand, might involve physically changing the robot’s end-effector (the tool at the end of the arm) or adding new sensors. A robot used for painting might have its end-effector replaced with a gripper for picking and placing components. This flexibility allows manufacturers to handle multiple product variations on a single production line, maximizing resource utilization and minimizing waste.
Benefits of Flexible Automation in Scalability and Market Responsiveness
Flexible automation systems, driven by robotics, offer unparalleled scalability. Manufacturers can easily increase or decrease production capacity by adding or removing robots as needed. This contrasts with traditional hard automation, where scaling up requires significant investment in new, dedicated machinery. Furthermore, flexible automation allows businesses to respond rapidly to changes in market demand. If a particular product becomes unexpectedly popular, manufacturers can quickly reprogram or reconfigure robots to increase production of that item without extensive lead times or costly retooling. This responsiveness is crucial in today’s dynamic market environment.
Comparison of Flexible Robotic Systems and Traditional Hard Automation
The choice between flexible robotic systems and traditional hard automation depends heavily on the specific application and business needs. A comparison highlights the key advantages and disadvantages of each approach.
Let’s consider a simple comparison:
Feature | Flexible Robotic Systems | Traditional Hard Automation |
---|---|---|
Adaptability | High; easily reprogrammed and reconfigured for different tasks and products. | Low; significant investment and downtime required for changes. |
Cost | Initial investment can be higher, but long-term costs are often lower due to flexibility. | Lower initial investment, but higher long-term costs due to inflexibility and potential obsolescence. |
Scalability | Easy to scale production up or down by adding or removing robots. | Difficult and costly to scale; requires significant investment in new machinery. |
Responsiveness to Market Changes | High; quick adaptation to changing product demand. | Low; slow and costly to adapt to changes. |
The Rise of Collaborative Robots (Cobots)
Forget the clunky, cage-enclosed robots of yesteryear. The future of industrial automation is collaborative, and it’s powered by cobots. These aren’t your grandpappy’s robots; they’re designed to work *with* humans, not replace them, creating a synergistic partnership on the factory floor.
Cobots, or collaborative robots, are smaller, lighter, and more adaptable than traditional industrial robots. They’re equipped with advanced sensors and safety features that allow them to operate alongside human workers without posing a significant safety risk. This collaborative approach allows for a more efficient and flexible production process, enhancing both productivity and worker satisfaction. Their functionalities range from simple pick-and-place operations to complex assembly tasks, depending on their programming and design. They often incorporate force-sensing technology, allowing them to adjust their movements to avoid collisions with humans or unexpected obstacles.
Cobot Applications in Manufacturing
Imagine a car assembly line. A human worker expertly fits intricate wiring harnesses into place, a task requiring dexterity and precision. A cobot, positioned nearby, simultaneously installs smaller components, such as fasteners or clips, with consistent speed and accuracy. The human worker handles the complex, nuanced tasks, while the cobot takes on the repetitive, less demanding, but crucial, elements of the assembly process. This division of labor significantly speeds up the overall process, reducing production time and increasing output. Another example is in a packaging facility where a cobot might lift and place heavy boxes onto a conveyor belt, reducing the strain on human workers and minimizing the risk of workplace injuries. In electronics manufacturing, cobots are used to handle delicate components with great precision, reducing the risk of damage and improving product quality.
Benefits of Human-Robot Collaboration
Human-robot collaboration offers a multitude of advantages. Firstly, it boosts efficiency by optimizing the workflow. Humans handle tasks requiring judgment, creativity, and problem-solving, while robots perform repetitive, strenuous, or dangerous tasks. This division of labor leads to increased productivity and output. Secondly, the improved precision and consistency of cobots significantly reduces errors, leading to higher quality products. Thirdly, workplace safety is enhanced by automating hazardous tasks, reducing the risk of injuries from repetitive strain or exposure to harmful substances. Finally, the flexibility afforded by cobots allows for easier adaptation to changing production demands and quicker response to market fluctuations.
A Visual Example of Cobot-Human Collaboration in Manufacturing
Picture a worker assembling a complex piece of machinery. The worker, let’s call him Alex, is seated at a workstation with various components spread out before him. A cobot, sleek and compact with rounded edges, is positioned beside Alex.
Step 1: Alex carefully inserts a large, intricate part into the main chassis.
Step 2: The cobot, using its sensors, identifies the location of pre-drilled holes in the chassis.
Step 3: Alex positions a smaller component near the holes.
Step 4: The cobot, guided by its programming and sensors, precisely inserts screws into the pre-drilled holes, securing the smaller component in place.
Step 5: Alex then connects a wire harness to the newly secured component.
Step 6: The cobot applies a small amount of adhesive, further securing the connection. This entire process is repeated, with Alex and the cobot seamlessly coordinating their actions, resulting in a more efficient and safer assembly process than if either were working alone. Alex focuses on the complex tasks, while the cobot ensures consistent accuracy and speed for the simpler ones, creating a powerful synergy.
The Impact on the Industrial Workforce
The rise of robotics in industrial automation presents a complex picture for the industrial workforce. While fears of widespread job displacement are understandable, the reality is more nuanced, involving both challenges and opportunities. The transition requires proactive strategies to manage the impact on existing jobs and to create new ones in the burgeoning field of robotics and automation.
The introduction of robots into manufacturing processes undeniably leads to concerns about job losses. Certain repetitive, manual tasks are easily automated, potentially rendering some human roles obsolete. This displacement, however, isn’t necessarily a complete wipeout; it’s a shift in the required skillsets. The key lies in adapting and reskilling the workforce to meet the evolving demands of a technologically advanced industry.
Job Displacement and the Need for Reskilling and Upskilling
The automation of manufacturing processes inevitably leads to a decrease in demand for workers performing routine, repetitive tasks. This necessitates a significant investment in reskilling and upskilling programs to equip workers with the competencies required for the new roles created by the robotics revolution. For example, workers previously employed in simple assembly lines might require training in robotics maintenance, programming, or data analysis to transition into new, higher-skilled positions. Without such initiatives, the benefits of automation risk exacerbating existing inequalities. Successful transitions require collaboration between governments, industry, and educational institutions to provide accessible and relevant training opportunities.
New Job Opportunities in Robotics and Automation
The integration of robots into industrial settings creates a significant demand for skilled professionals in various areas. The expanding robotics sector necessitates experts in robotics maintenance, programming, system integration, and data analytics. These roles require specialized knowledge and technical skills, often involving advanced degrees or certifications. For instance, a technician specializing in robotic maintenance is crucial for ensuring the smooth operation of automated systems, requiring a deep understanding of mechanical, electrical, and software components. Similarly, robotics programmers are needed to develop and implement the complex algorithms that control robotic movements and actions, demanding proficiency in coding languages and robotic simulation software. The growing complexity of automated systems also fuels demand for system integrators who oversee the seamless integration of robots into existing production lines.
Examples of Successful Reskilling Programs
Several successful reskilling programs demonstrate the effectiveness of proactive approaches to workforce adaptation. For example, some automotive manufacturers have partnered with local community colleges to provide training programs for their employees affected by automation. These programs focus on developing skills in areas such as programming, data analytics, and robotic maintenance, preparing workers for new roles within the company. Another example includes programs that offer apprenticeships and on-the-job training, allowing workers to gain practical experience alongside theoretical knowledge. These initiatives demonstrate that targeted, industry-specific reskilling can successfully mitigate the negative impacts of automation while fostering a skilled workforce for the future.
Strategies for Mitigating Job Displacement
To effectively manage the transition and minimize the negative impacts of robotic automation on the workforce, a multi-pronged approach is crucial. This includes:
- Investing heavily in education and training programs focused on STEM fields and advanced manufacturing skills.
- Developing partnerships between educational institutions, industry, and government to create tailored reskilling and upskilling initiatives.
- Promoting lifelong learning and encouraging workers to continuously adapt their skills to meet evolving industry demands.
- Implementing policies that support workers during transitions, such as unemployment benefits and job placement services.
- Focusing on the creation of new, higher-skilled jobs in the robotics and automation sector through incentives and investments.
Future Trends in Industrial Robotics
The future of industrial automation is inextricably linked to advancements in robotics. We’re moving beyond simple, repetitive tasks towards a world where robots are intelligent, adaptable, and collaborative partners in the manufacturing process. This evolution is driven by several converging technological trends, promising a significant leap in efficiency, safety, and overall productivity.
Emerging technologies are rapidly transforming the landscape of industrial robotics, creating opportunities for unprecedented levels of automation and sophistication. The integration of artificial intelligence, machine learning, and the Internet of Things (IoT) is fundamentally reshaping how robots operate and interact within industrial settings. This convergence isn’t just about incremental improvements; it’s a paradigm shift that promises to redefine the very nature of industrial production.
The Impact of AI, Machine Learning, and IoT
The integration of AI, machine learning, and the IoT is revolutionizing industrial robotics. AI enables robots to learn from data, adapt to changing conditions, and make decisions autonomously. Machine learning algorithms allow robots to improve their performance over time without explicit programming, optimizing processes and reducing errors. The IoT connects robots to a network, enabling real-time data exchange and remote monitoring, facilitating predictive maintenance and optimizing overall system performance. For example, a smart factory using IoT sensors can detect anomalies in a robot’s operation, predicting potential failures before they occur, minimizing downtime and maximizing productivity. This proactive approach to maintenance is a significant departure from traditional reactive methods.
Advancements in Robot Dexterity, Intelligence, and Adaptability, How Robotics is Changing the Future of Industrial Automation
Robots are becoming increasingly dexterous, intelligent, and adaptable. Advancements in sensor technology, particularly vision systems and force feedback, allow robots to manipulate objects with greater precision and handle a wider range of tasks. Improved AI algorithms enable robots to learn complex manipulation skills through observation and practice, mimicking human dexterity. This enhanced adaptability allows robots to operate in dynamic and unpredictable environments, adapting to changes in the production line or handling unexpected variations in materials. Imagine robots capable of assembling intricate electronics components or performing delicate surgical procedures—this level of dexterity is becoming increasingly achievable.
Performing Increasingly Complex and Sophisticated Tasks
The convergence of these technologies allows robots to perform increasingly complex and sophisticated tasks. Tasks previously requiring human expertise, such as quality inspection, assembly of complex products, and even creative design processes, are now within the realm of robotic capabilities. For instance, robots equipped with advanced vision systems and AI algorithms can perform high-precision inspections, identifying defects that are invisible to the human eye. In the automotive industry, robots are now used not only for welding and painting but also for complex assembly tasks, significantly increasing production efficiency and reducing human error. The future will see robots taking on even more challenging roles, collaborating with humans to solve complex problems and optimize manufacturing processes. For example, we can envision robots working alongside human engineers to design and optimize new products, leveraging their speed and precision to accelerate the design cycle.
Summary
The rise of robotics in industrial automation isn’t just a trend; it’s a fundamental shift in how we manufacture and produce goods. While concerns about job displacement are valid, the potential benefits – increased efficiency, improved safety, and the creation of innovative new roles – are undeniable. The future of work is collaborative, intelligent, and undeniably robotic. Embracing this change, with thoughtful strategies for reskilling and upskilling, will be key to unlocking the full potential of this exciting technological revolution. The question isn’t *if* robots will transform industry, but *how* we’ll navigate this transformation to create a more efficient, safer, and ultimately, more prosperous future.