How Robotics is Changing the Future of Autonomous Manufacturing? Forget clunky assembly lines; the future of factories is here, and it’s surprisingly collaborative. We’re talking robots working *with* humans, not replacing them entirely. This isn’t just about faster production; it’s about smarter, safer, and more sustainable manufacturing processes. Think self-driving vehicles for your warehouse, robots that learn from their mistakes, and a whole new level of precision in quality control. Get ready for a deep dive into the exciting world of automated factories.
This shift towards autonomous manufacturing isn’t just about technological advancements; it’s a fundamental reshaping of how we produce goods. From collaborative robots (cobots) assisting human workers to AI-powered systems optimizing entire production lines, the integration of robotics is revolutionizing efficiency, safety, and even the very nature of jobs within the manufacturing sector. We’ll explore the impact on the workforce, the rise of new skills, and the ethical considerations that come with this rapid technological leap.
The Rise of Collaborative Robots (Cobots) in Manufacturing
The manufacturing landscape is undergoing a dramatic transformation, driven by the increasing adoption of automation technologies. While traditional industrial robots have played a significant role, a new breed of robots is rapidly gaining traction: collaborative robots, or cobots. These robots are designed to work alongside human workers, sharing tasks and improving overall efficiency and safety. This shift represents a significant leap forward in autonomous manufacturing, moving beyond isolated robotic cells to a more integrated and human-centered approach.
Cobot Features and Functionalities
Collaborative robots are characterized by their inherent safety features and ease of programming. Unlike their industrial counterparts, cobots are equipped with sensors and software that allow them to detect and react to human presence, preventing accidents. They often possess force-limiting capabilities, meaning they will stop operation if they encounter unexpected resistance. This makes them ideal for tasks requiring close human-robot interaction. Their user-friendly interfaces also simplify programming and deployment, reducing the need for specialized expertise. Many cobots utilize intuitive visual programming interfaces, enabling even non-programmers to quickly adapt and reprogram the robot for different tasks. This flexibility is crucial in dynamic manufacturing environments.
Cobots vs. Traditional Industrial Robots
Traditional industrial robots are typically large, powerful, and designed for high-speed, repetitive tasks within caged environments to ensure worker safety. They require extensive programming and specialized expertise to operate and maintain. Cobots, on the other hand, are smaller, lighter, and designed for collaborative tasks. Their safety features eliminate the need for protective cages, allowing them to work directly alongside humans. While traditional robots excel at high-speed, repetitive tasks, cobots are better suited for flexible, adaptable tasks requiring human-robot interaction. A key disadvantage of cobots is their generally lower payload capacity and slower speeds compared to industrial robots. However, their flexibility and ease of use often outweigh these limitations in many applications.
Cobot Applications in Manufacturing
Cobots are finding applications across various manufacturing sectors. In the automotive industry, cobots are used for assembly tasks, such as installing parts or tightening bolts, working alongside human technicians. The electronics industry leverages cobots for delicate tasks like circuit board assembly and testing, benefiting from their precision and collaborative nature. The food and beverage industry utilizes cobots for packaging and palletizing, improving efficiency and reducing the risk of workplace injuries. In the medical device industry, cobots assist in the assembly and testing of complex medical devices, ensuring high precision and consistency. The impact on productivity is significant, as cobots can handle repetitive tasks, freeing up human workers to focus on more complex and value-added activities. Furthermore, the improved safety features significantly reduce the risk of workplace accidents.
Comparison of Cobot Models, How Robotics is Changing the Future of Autonomous Manufacturing
The following table compares three popular cobot models, highlighting their key specifications:
Cobot Model | Payload Capacity (kg) | Reach (m) | Programming Interface |
---|---|---|---|
Universal Robots UR5e | 5 | 0.85 | Intuitive visual programming |
Fanuc CRX-10iA | 10 | 1.4 | TSR (Teach, Set, Run) and iHMI |
ABB YuMi | 0.5 (per arm) | 0.55 | Lead-through programming and FlexPendant |
Autonomous Guided Vehicles (AGVs) and Material Handling
Forget the image of factory workers frantically pushing carts – the future of material handling is autonomous. Autonomous Guided Vehicles (AGVs) are revolutionizing manufacturing, streamlining logistics, and boosting efficiency in ways previously unimaginable. These robotic workhorses are transforming how materials move within factories and warehouses, paving the way for a truly automated production environment.
AGV Transformation of Material Handling Processes
AGVs are significantly altering material handling processes by automating the transport of goods, raw materials, and finished products. This automation eliminates the need for manual handling, reducing labor costs, improving accuracy, and increasing overall throughput. Instead of relying on human operators, AGVs navigate pre-programmed routes, following guidance systems to deliver materials precisely where and when needed. This results in a more efficient workflow, minimizing delays and bottlenecks that often plague traditional material handling systems. For example, a car manufacturing plant might use AGVs to transport engine parts from the assembly line to the vehicle chassis stations, ensuring a consistent supply of components and minimizing production downtime.
Types of Autonomous Guided Vehicles
Several types of AGVs cater to different factory layouts and material handling needs. The choice depends on factors like floor conditions, the complexity of the routes, and the required payload capacity.
- Laser-Guided AGVs: These vehicles use laser scanners to create a map of their environment and navigate using this map. They are highly accurate and adaptable to changes in the factory layout, as they can dynamically adjust their routes based on detected obstacles. They’re ideal for complex environments with frequent changes.
- Magnetic-Guided AGVs: These AGVs follow magnetic tapes or wires embedded in the floor. While simpler and often less expensive than laser-guided systems, they are less flexible and require significant upfront investment in infrastructure. Changes to the route necessitate modifying the magnetic guide path.
- Vision-Guided AGVs: These advanced AGVs use cameras and computer vision to navigate. They can recognize landmarks, follow paths, and even avoid unexpected obstacles without relying on pre-programmed routes or physical guides. They offer the greatest flexibility but are generally more complex and expensive to implement.
Benefits of Implementing AGVs
The benefits of integrating AGVs into a manufacturing environment are substantial and far-reaching.
- Increased Efficiency: AGVs operate continuously, without breaks or fatigue, leading to significantly higher throughput and reduced cycle times. They can work around the clock, optimizing production schedules.
- Cost Reduction: While the initial investment can be significant, the long-term cost savings from reduced labor, improved efficiency, and minimized errors often outweigh the upfront expenses. This is especially true in environments with high material handling demands.
- Enhanced Safety: AGVs contribute to a safer working environment by reducing the risk of workplace accidents associated with manual material handling. Their automated operation minimizes human error and the potential for injuries from heavy lifting or collisions.
AGV System Operation in a Warehouse Environment
The following flowchart illustrates the basic operation of an AGV system within a warehouse:
[Imagine a flowchart here. The flowchart would start with a “Request for Material” box, leading to an “AGV Selection” box (choosing the appropriate AGV based on the task), then to a “Path Planning” box (AGV determines the optimal route using its navigation system), followed by a “Material Pickup” box, then a “Transport” box (AGV moves along the planned route), then a “Material Delivery” box, then a “Confirmation” box (confirmation of delivery), and finally a “Return to Base” box. The flowchart would use arrows to indicate the flow between each box.]
Artificial Intelligence (AI) and Machine Learning (ML) in Robotics for Manufacturing
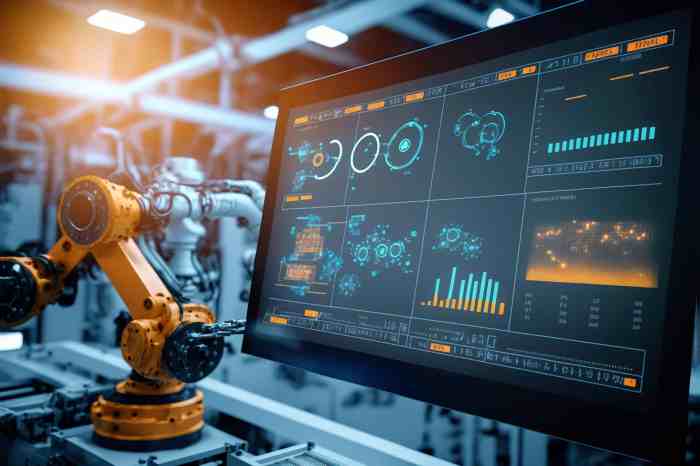
Source: amta.sg
The integration of artificial intelligence (AI) and machine learning (ML) is supercharging the capabilities of robots in manufacturing, pushing the boundaries of automation beyond pre-programmed tasks. This powerful combination allows robots to learn, adapt, and make decisions autonomously, leading to significant improvements in efficiency, quality, and overall productivity. Forget rigid, repetitive movements; AI-powered robots are ushering in a new era of flexible and intelligent automation.
AI and ML algorithms equip robots with the ability to analyze vast amounts of data, identify patterns, and make informed decisions in real-time. This enables autonomous decision-making, allowing robots to handle unexpected situations, optimize their actions, and even learn from their mistakes, constantly refining their performance. This is a far cry from the traditional robots of the past, which were limited to performing pre-programmed tasks.
AI-Enabled Quality Control
AI-powered vision systems are revolutionizing quality control in manufacturing. These systems can analyze images and videos with incredible speed and accuracy, identifying defects that might be missed by human inspectors. For example, a robot equipped with an AI-powered vision system can inspect thousands of parts per hour, identifying even minute imperfections like scratches, dents, or inconsistencies in color or texture. This leads to higher product quality and reduced waste, ultimately saving manufacturers time and money. The speed and accuracy surpass human capabilities, leading to consistent and reliable quality checks.
Predictive Maintenance through AI
Predictive maintenance, powered by AI, is another game-changer. By analyzing data from sensors on machinery, AI algorithms can predict potential equipment failures before they occur. This allows manufacturers to schedule maintenance proactively, minimizing downtime and preventing costly repairs. Imagine a robot monitoring the vibrations and temperature of a machine; using ML, it can detect subtle anomalies that indicate impending failure, alerting maintenance personnel well in advance. This proactive approach significantly reduces unexpected downtime and improves overall operational efficiency.
AI for Process Optimization
AI and ML algorithms can analyze manufacturing processes to identify bottlenecks and inefficiencies. By analyzing data from various sources, such as production rates, energy consumption, and material usage, AI can suggest improvements to optimize the entire process. This might involve adjusting parameters, such as speed or temperature, or even redesigning parts of the manufacturing process to improve efficiency and reduce costs. For instance, an AI system might identify a particular stage in the production line that is consistently slowing down the overall process and recommend adjustments to improve its throughput.
Challenges and Limitations of AI/ML in Manufacturing Robotics
Despite the numerous advantages, implementing AI and ML in manufacturing robotics also presents some challenges. The need for large datasets to train effective AI models can be a hurdle, especially for smaller manufacturers. Data security and privacy concerns are also paramount. Furthermore, integrating AI systems with existing manufacturing infrastructure can be complex and expensive, requiring significant investment in hardware and software. Finally, ensuring the reliability and robustness of AI-powered robots is crucial to prevent costly errors or production stoppages. Robust error handling and fail-safe mechanisms are essential.
Case Study: Fanuc’s AI-Powered Robot for Weld Quality Inspection
Fanuc, a leading robotics company, has developed an AI-powered robot for weld quality inspection. This robot uses a vision system and AI algorithms to automatically inspect welds for defects, such as porosity, cracks, or incomplete penetration. The system significantly reduces the time and cost associated with manual weld inspection, while also improving the accuracy and consistency of quality control. The system’s ability to learn and adapt over time, improving its accuracy with each inspection, makes it a valuable asset in high-volume manufacturing environments. The reduced inspection time and improved accuracy translate to direct cost savings and higher product quality.
Impact on the Workforce and Reskilling Initiatives: How Robotics Is Changing The Future Of Autonomous Manufacturing
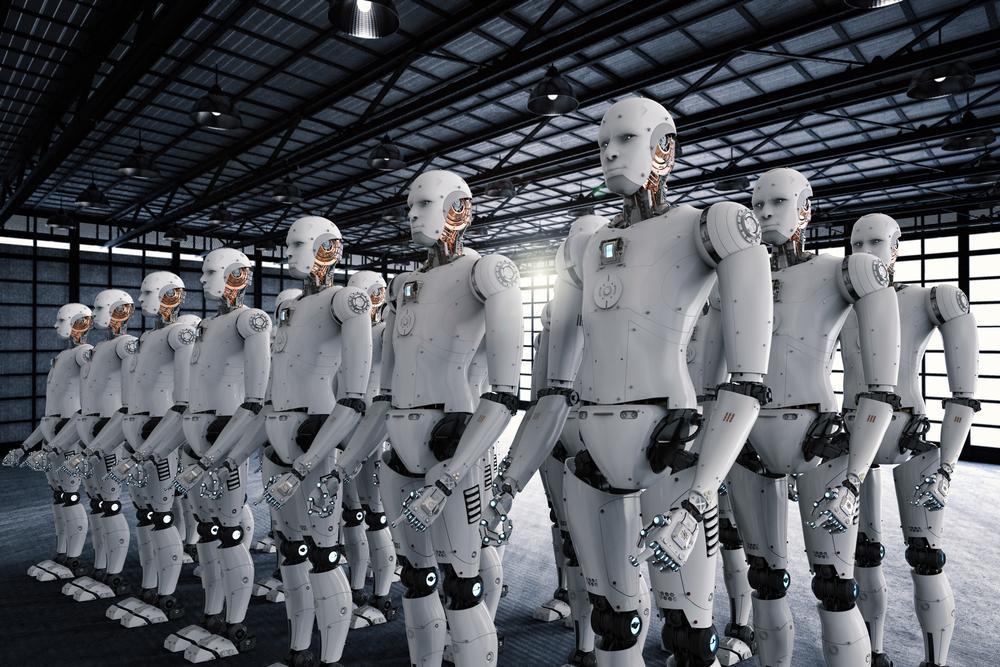
Source: progressiveautomations.com
The rise of autonomous manufacturing, while promising increased efficiency and productivity, presents a significant challenge: its impact on the human workforce. The automation of tasks previously performed by humans inevitably leads to concerns about job displacement and the need for substantial workforce adaptation. Understanding this impact and proactively addressing it through reskilling and upskilling initiatives is crucial for a smooth transition to a future dominated by robotic automation.
The integration of robots and AI in manufacturing plants could lead to a reduction in certain roles, particularly those involving repetitive or physically demanding tasks. This isn’t necessarily a complete job loss scenario; rather, it’s a shift in the demand for skills. While some jobs may disappear, new opportunities will emerge, requiring a different skill set from the workforce. The challenge lies in ensuring a seamless transition for workers, equipping them with the skills needed to thrive in this evolving landscape.
Job Displacement and New Opportunities
The automation of manufacturing processes will undoubtedly affect employment. Some roles, such as those involving simple assembly line work or repetitive material handling, are highly susceptible to automation. However, this doesn’t signal the end of human involvement. The demand for skilled technicians to maintain, program, and repair robotic systems will increase significantly. Furthermore, roles focusing on data analysis, AI integration, and process optimization will become increasingly crucial. Companies like Tesla, for example, have already demonstrated the need for highly skilled technicians capable of working alongside advanced robotic systems in their production facilities. This shift requires a proactive approach to reskilling and upskilling the existing workforce.
Reskilling and Upskilling Initiatives: Bridging the Skills Gap
Addressing the skills gap created by the rise of automation requires a multi-pronged approach involving government, educational institutions, and industry collaboration. Governments can play a vital role by investing in training programs and providing financial support for workers undergoing reskilling. Educational institutions need to adapt their curricula to include courses in robotics, AI, data analytics, and other relevant fields. Industry partnerships are crucial for providing practical training and apprenticeship opportunities, allowing workers to gain hands-on experience with the latest technologies. Successful programs often combine classroom learning with on-the-job training, ensuring that workers acquire both theoretical knowledge and practical skills. For instance, many vocational schools are now incorporating robotics and automation training into their programs, preparing students for the jobs of the future.
In-Demand Skills in Autonomous Manufacturing
The future of autonomous manufacturing will require a diverse skill set, blending traditional manufacturing expertise with advanced technological knowledge. These skills will fall broadly into three categories:
- Technical Skills: Robotics programming and maintenance, AI and machine learning integration, automation system design, sensor technology, data analytics, and cybersecurity.
- Analytical Skills: Data interpretation, process optimization, predictive maintenance, and problem-solving using advanced analytics tools.
- Soft Skills: Collaboration, critical thinking, adaptability, problem-solving, and continuous learning.
Resources for Workforce Development
Workers seeking to acquire new skills in robotics and automation have access to a variety of resources:
- Online Courses and Platforms: Platforms like Coursera, edX, Udacity, and FutureLearn offer a wide range of courses on robotics, AI, and related technologies.
- Vocational Schools and Community Colleges: Many vocational schools and community colleges offer training programs in robotics, automation, and related fields, often with industry partnerships.
- Industry-Specific Training Programs: Many manufacturers offer training programs for their employees to upskill and adapt to the changing technological landscape. These programs often focus on specific technologies used within the company.
- Government-Funded Training Programs: Several governments offer funding and support for workers seeking to reskill or upskill, often focusing on high-demand sectors like advanced manufacturing.
- Apprenticeships and On-the-Job Training: Apprenticeships provide a valuable opportunity to learn practical skills while working in a real-world setting. On-the-job training is often offered by employers to help their workforce adapt to new technologies.
The Future of Human-Robot Collaboration in Smart Factories
Smart factories represent the cutting edge of manufacturing, leveraging interconnected robotic systems and advanced data analytics to optimize production processes. This interconnectedness, however, necessitates a sophisticated approach to human-robot collaboration, moving beyond simple automation to a truly synergistic partnership. The future of manufacturing lies in seamlessly integrating human ingenuity and robotic precision.
The concept of a smart factory hinges on the interconnectedness of its various components. Imagine a network of robots, sensors, and machines communicating seamlessly through a sophisticated system, sharing data in real-time to optimize efficiency and predict potential issues. This network allows for dynamic adjustments to production schedules, proactive maintenance, and a significant reduction in downtime. This interconnectedness is crucial for enabling the next level of human-robot collaboration.
Autonomous manufacturing’s future is being radically reshaped by robotics, boosting efficiency and precision. But training the next generation of robotics engineers requires innovative methods, which is where the power of immersive tech comes in. Check out this article on The Role of Augmented Reality in Modernizing Education and Training to see how AR is revolutionizing learning.
Ultimately, this upskilling will be crucial for the continued advancement of robotic automation in factories worldwide.
Challenges and Opportunities in Human-Robot Collaboration
Creating a safe and efficient human-robot collaboration environment presents unique challenges. Safety protocols must be robust to prevent accidents, while simultaneously enabling flexible and responsive collaboration. The opportunity lies in leveraging human skills like adaptability and problem-solving alongside robotic precision and tireless work ethic. This synergistic approach can lead to higher quality products, increased productivity, and a more engaging work environment for human employees. For example, a recent study by the Fraunhofer Institute for Manufacturing Engineering and Automation IPA showed a 20% increase in productivity in a factory that implemented collaborative robots alongside human workers, compared to a traditional, fully automated line.
Design Considerations for Human-Robot Shared Workspaces
Integrating humans and robots effectively requires careful consideration of workspace design. Ergonomics play a crucial role, ensuring that both human workers and robots operate in a comfortable and safe manner. Clear visual cues, such as color-coded zones or safety lights, are essential to delineate areas of human and robotic operation, minimizing the risk of collisions. The robots themselves need to be designed with safety features like force-limiting sensors and emergency stop mechanisms. Furthermore, intuitive human-machine interfaces are crucial for effective communication and control, allowing humans to easily interact with and direct the robots. For instance, a well-designed workspace might include easily accessible control panels, clear visual indicators of robot status, and strategically placed safety barriers.
A Collaborative Assembly Line Scenario
Consider a car assembly line where humans and robots work side-by-side. The process begins with a human worker positioning a car chassis on the assembly line. A collaborative robot, equipped with advanced sensors, then precisely welds specific components onto the chassis, guided by the human worker who ensures the correct placement and orientation of parts. After the welding is complete, the robot safely moves away, allowing the human worker to install interior components. Another robot might then apply sealant, working in close proximity to the human worker but maintaining a safe distance. Finally, the human worker performs a quality check, ensuring that all components are correctly installed and the welds are sound. This scenario demonstrates how humans and robots can seamlessly share tasks, leveraging each other’s strengths to achieve optimal efficiency and product quality. The human worker retains control over complex tasks requiring judgment and dexterity, while the robot performs repetitive, high-precision tasks with unwavering consistency.
Safety and Security Considerations in Autonomous Manufacturing
The rise of autonomous systems in manufacturing promises increased efficiency and productivity, but it also introduces new safety and security challenges. Balancing the benefits of automation with the need for a safe and secure working environment is crucial for successful implementation. Failing to address these concerns could lead to accidents, production downtime, and reputational damage.
Potential Safety Hazards Associated with Robots
Industrial robots, even those designed for collaboration, possess significant potential for causing harm. Their powerful actuators, sharp edges, and high speeds pose risks of crushing, cutting, and impact injuries to human workers. Malfunctions in robotic systems, programming errors, or unexpected interactions with the environment can also lead to unpredictable behavior and hazardous situations. For example, a malfunctioning robotic arm might unexpectedly swing out of its designated workspace, causing injury to nearby personnel. Furthermore, the complex interactions between multiple autonomous systems within a smart factory increase the likelihood of unforeseen events.
Robust Safety Protocols and Emergency Shutdown Mechanisms
Implementing comprehensive safety protocols is paramount. These should include physical safeguards like safety cages, light curtains, and emergency stop buttons strategically placed throughout the work area. Regular safety inspections and maintenance are essential to ensure the continued effectiveness of these measures. Emergency shutdown mechanisms must be readily accessible and reliably function to quickly halt robotic operations in case of an accident or malfunction. These systems should be designed with redundancy to minimize the risk of failure. For instance, a factory might employ multiple independent emergency stop systems, each capable of shutting down the entire robotic system.
Cybersecurity Risks Associated with Connected Robotic Systems
The increasing connectivity of robotic systems introduces significant cybersecurity vulnerabilities. Hackers could potentially gain unauthorized access to control systems, manipulating robotic operations for malicious purposes, ranging from disrupting production to causing physical harm. Data breaches could also expose sensitive intellectual property and operational data. Consider the scenario of a factory’s robotic welding system being compromised, causing it to weld incorrectly and damage expensive equipment or even cause a fire. This highlights the importance of robust cybersecurity measures.
Best Practices for Robot Safety and Security in Manufacturing
Safety Aspect | Security Aspect | Best Practice | Example |
---|---|---|---|
Risk Assessment | Network Segmentation | Conduct thorough risk assessments to identify potential hazards and vulnerabilities. | Regularly assess the risks associated with each robot and its operational environment. |
Emergency Stop Systems | Firewall Implementation | Implement multiple, independent emergency stop systems with redundancy. | Utilize both physical emergency stop buttons and software-based emergency stop functions. |
Physical Barriers | Intrusion Detection System | Use safety cages, light curtains, and other physical barriers to separate robots from human workers. | Install safety cages around high-risk robotic operations and utilize light curtains to detect human intrusion. |
Regular Maintenance | Regular Security Audits | Conduct regular maintenance and inspections to ensure the proper functioning of safety mechanisms. | Implement a scheduled maintenance program for all robotic systems, including regular safety checks. |
Economic and Societal Implications of Autonomous Manufacturing
The rise of autonomous manufacturing presents a complex tapestry of economic and societal impacts, weaving together threads of potential prosperity and potential disruption. Understanding these implications is crucial for navigating the transition and ensuring a future where the benefits are widely shared and the challenges are effectively mitigated. This section explores the multifaceted effects of this technological revolution on our economies and societies.
Economic Benefits and Drawbacks of Autonomous Manufacturing
Widespread adoption of autonomous manufacturing systems promises significant economic benefits. Increased productivity and efficiency, driven by automation, lead to lower production costs and potentially lower prices for consumers. This can boost competitiveness in global markets and stimulate economic growth. However, the transition also presents challenges. The initial investment in advanced technologies can be substantial, potentially creating a barrier to entry for smaller businesses. Furthermore, job displacement in certain sectors is a legitimate concern, requiring proactive measures to address workforce retraining and adaptation. For example, the automotive industry’s increasing reliance on robots has led to a decrease in assembly line jobs, necessitating investment in training programs for workers to transition into roles requiring higher-level skills such as programming and maintenance of robotic systems. The long-term economic impact will depend on how effectively these challenges are managed.
Ethical Implications of Increasing Automation in Manufacturing
The ethical considerations surrounding increased automation in manufacturing are profound. Concerns about job displacement and the potential widening of the wealth gap are central to this discussion. The concentration of economic power in the hands of a few companies that can afford advanced automation technologies poses a risk to social equity. Furthermore, the reliance on algorithms and AI in decision-making processes within autonomous manufacturing systems raises questions about accountability and transparency. Who is responsible when a robotic system malfunctions, causing damage or injury? These are critical questions that need careful consideration and robust regulatory frameworks to address. For instance, the development of clear guidelines for algorithmic transparency and liability in autonomous systems is essential to mitigate potential ethical concerns.
Autonomous Manufacturing and Global Challenges
Autonomous manufacturing offers a powerful tool for addressing pressing global challenges. Its potential contribution to sustainability is significant. Optimized production processes, driven by AI and data analysis, can minimize waste and resource consumption. Precise control over manufacturing processes can lead to more efficient use of energy and materials, reducing the environmental footprint of industries. Furthermore, autonomous systems can play a role in addressing resource scarcity by enabling the efficient extraction and processing of resources, while simultaneously minimizing environmental damage. For example, the use of autonomous vehicles in mining operations can improve safety and efficiency while reducing the environmental impact of traditional mining practices. The precision of robotic systems also allows for the creation of more durable and long-lasting products, reducing the need for frequent replacements and minimizing waste.
Autonomous Manufacturing’s Contribution to Economic Growth and Improved Living Standards
The potential for autonomous manufacturing to contribute to economic growth and improve living standards is substantial. Increased productivity and efficiency translate into lower prices for goods and services, making them more accessible to a wider population. This can lead to improved living standards, particularly in developing countries where access to affordable goods is a significant factor in economic advancement. Moreover, the creation of new jobs in areas such as robotics engineering, AI development, and data analysis will offset job losses in other sectors. For instance, the development and implementation of autonomous manufacturing systems in the textile industry in Bangladesh could lead to increased efficiency and improved working conditions, resulting in higher wages and improved living standards for workers. However, ensuring that the benefits are equitably distributed requires thoughtful policy interventions and investment in education and reskilling initiatives.
Closing Notes
The future of manufacturing isn’t about robots taking over; it’s about humans and robots working together in smarter, more efficient factories. Autonomous systems, powered by AI and collaborative robots, are paving the way for a new era of productivity and innovation. While challenges remain, like reskilling the workforce and addressing ethical concerns, the potential benefits – from increased efficiency and safety to sustainable practices – are undeniable. The integration of robotics in manufacturing isn’t just a technological advancement; it’s a societal shift, promising a future where technology empowers human potential and addresses global challenges.