How Robotics is Advancing the Manufacturing of Consumer Goods: Forget clunky assembly lines – the future of consumer product creation is here, and it’s robotic. We’re talking hyper-efficient processes, flawless quality control, and a whole new level of safety. This isn’t just about replacing humans; it’s about a powerful collaboration, boosting productivity and reinventing the way we make everything from smartphones to your favorite snack food. Get ready to explore the robotic revolution reshaping the consumer goods landscape.
From automating repetitive tasks to handling hazardous materials, robots are streamlining production lines and pushing the boundaries of what’s possible. This means faster production times, fewer errors, and a significant boost in overall efficiency. But the impact extends beyond mere numbers; it’s about creating safer work environments, fostering innovation, and ultimately, delivering higher-quality products to consumers. We’ll delve into the specifics, examining the financial benefits, the evolving role of human workers, and the ethical considerations that come with this technological leap.
Increased Efficiency and Productivity in Manufacturing
The integration of robotics into consumer goods manufacturing has revolutionized production lines, significantly boosting efficiency and productivity. Robots, with their tireless work ethic and precision, are transforming how we make everything from smartphones to snacks. This increased efficiency translates directly into lower costs and faster delivery times for consumers.
Robots are enhancing speed and output in several key ways. Their tireless operation allows for continuous production, unlike human workers who require breaks and rest. This continuous operation minimizes downtime and maximizes output. Moreover, robots can perform tasks with incredible speed and accuracy, far surpassing human capabilities in repetitive actions. This precision also reduces errors and waste, further increasing overall efficiency.
Robots are revolutionizing consumer goods manufacturing, boosting efficiency and precision. This hyper-automation trend mirrors the changes happening in digital content consumption, where AI is personalizing our experiences, as detailed in this insightful article: How AI is Changing the Way We Consume Digital Content. Ultimately, both AI and robotics are shaping how we interact with products, from their creation to their consumption.
Robotic Systems vs. Manual Labor in Manufacturing Processes
A comparison of robotic systems and traditional manual labor reveals a clear advantage for automation in many consumer goods manufacturing processes. In assembly, for instance, robots can handle intricate tasks with consistent precision, significantly reducing the number of defective products and speeding up the assembly line. Packaging, another labor-intensive process, benefits immensely from robotic automation. Robots can quickly and accurately package items, apply labels, and prepare them for shipping, improving throughput and reducing the risk of human error. The difference in speed and accuracy is stark; a robot can perform hundreds of packaging operations per hour, whereas a human worker might manage only a fraction of that.
Reduced Downtime and Improved Production Flow
Robots contribute significantly to reduced downtime and improved production flow. Unlike human workers, robots don’t get sick, take breaks, or require vacations. This continuous operation eliminates bottlenecks in the production line, resulting in a smoother, more efficient workflow. Furthermore, robots can be programmed to work around the clock, enabling manufacturers to operate 24/7 and maximize production capacity. Predictive maintenance capabilities built into robotic systems also help identify potential issues before they cause significant downtime. This proactive approach minimizes disruption and keeps the production line running smoothly.
Key Performance Indicators (KPIs) Before and After Robotic Implementation
KPI | Before Robotic Implementation | After Robotic Implementation | Percentage Change |
---|---|---|---|
Units Produced Per Hour | 100 | 250 | +150% |
Defect Rate | 5% | 1% | -80% |
Production Downtime (Hours/Week) | 10 | 2 | -80% |
Labor Costs (per unit) | $2 | $1 | -50% |
Note: These figures are illustrative examples based on hypothetical data and may vary significantly depending on the specific industry, factory setup, and type of robots implemented.
Enhanced Product Quality and Consistency
Forget those wonky widgets and slightly-off-kilter gadgets. Robotics is revolutionizing manufacturing, bringing a level of precision and consistency that was previously unimaginable. This isn’t just about faster production; it’s about ensuring every single item rolling off the assembly line meets the highest quality standards, consistently.
Robots, with their unwavering accuracy and tireless repetition, minimize human error, a major source of defects in traditional manufacturing. This translates directly into higher-quality products, fewer returns, and increased customer satisfaction. The impact is particularly significant in industries demanding exceptional precision.
Robotic Precision Minimizes Errors and Defects, How Robotics is Advancing the Manufacturing of Consumer Goods
The inherent precision of robots drastically reduces manufacturing defects. Unlike human workers, who can experience fatigue or momentary lapses in concentration, robots perform tasks with unwavering accuracy, time after time. This is especially critical in processes requiring intricate assembly, delicate handling, or microscopic adjustments. For instance, in the assembly of microchips, a single misplaced component can render the entire chip useless. Robots, with their microscopic precision, significantly reduce the risk of such errors, resulting in higher yields and reduced waste. Furthermore, their consistent application of force prevents damage to delicate components during assembly. This precision extends beyond simple assembly; robots can also perform quality checks with far greater accuracy than human inspectors, identifying even minute flaws that might be missed by the human eye.
Maintaining Consistent Product Quality Across Large Production Runs
Maintaining consistent quality across large-scale production is a significant challenge in traditional manufacturing. Variations in human performance, tool wear, and environmental factors can all contribute to inconsistencies. Robotics eliminates many of these variables. Robots consistently apply the same force, speed, and precision to each unit produced, regardless of the production volume. This ensures uniformity across the entire production run, leading to a more consistent final product. This consistency is vital for brands seeking to maintain a strong reputation for quality and reliability. Consider the example of pharmaceutical manufacturing, where even minor inconsistencies can have significant consequences. Robots guarantee consistent dosage and formulation, crucial for patient safety and efficacy.
Examples of Consumer Goods Benefiting from Robotic Precision
Robotic precision is particularly crucial in several consumer goods sectors. In electronics manufacturing, robots assemble intricate components with micron-level accuracy, ensuring the functionality and reliability of smartphones, computers, and other electronic devices. The pharmaceutical industry relies heavily on robots for precise dosage control, sterile packaging, and quality inspection, guaranteeing the safety and efficacy of medications. The automotive industry uses robots for welding, painting, and assembly, producing vehicles with consistent quality and reducing the risk of defects. Even in food processing, robots ensure consistent packaging and portioning, contributing to food safety and reducing waste.
Quality Control Steps Enhanced by Robotics in Electronics Manufacturing
The following flowchart illustrates how robotics enhances quality control in the manufacturing of smartphones:
[Imagine a flowchart here. It would begin with “Raw Materials Inspection (Automated Vision System)”, followed by “Component Assembly (Robotic Arms)”, then “Automated Testing (Functional and Performance Tests)”, followed by “Visual Inspection (Automated Vision System)”, and finally “Packaging (Robotic Arm and Automated Labeling)”. Each step would have a small box with a brief description, connected by arrows showing the flow. The key here is the use of automated systems at each step, highlighting the robotic involvement in quality control.]
The consistent application of automated vision systems and robotic arms throughout the process ensures that every smartphone meets the required quality standards before it reaches the consumer. The precision of robots at each stage drastically reduces defects and ensures consistency across all units.
Improved Safety and Working Conditions
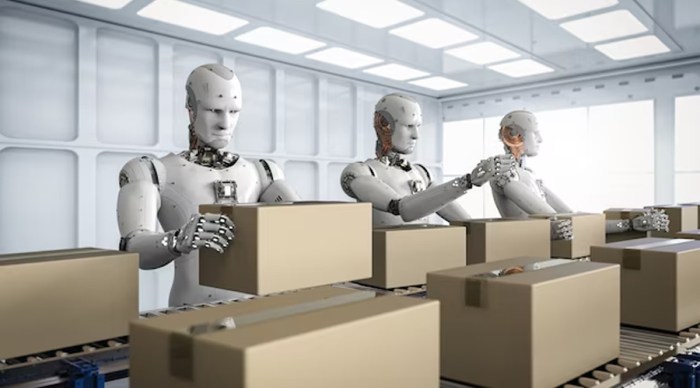
Source: indianachiever.com
Robots are revolutionizing manufacturing safety, stepping into roles previously deemed too dangerous for humans. This shift not only protects workers from injury but also boosts overall productivity by allowing continuous operation in hazardous environments. The integration of robotics significantly reduces the risk of workplace accidents, leading to a healthier and more secure work environment for everyone.
The implementation of robotic systems directly addresses many inherent dangers in consumer goods manufacturing. Repetitive strain injuries, exposure to harmful chemicals, and the risk of heavy machinery accidents are all mitigated through automation. Robots can tirelessly perform tasks requiring precision and strength in environments that would be dangerous or physically taxing for humans.
Hazardous Tasks Handled by Robots
Robots are increasingly taking over tasks involving high temperatures, toxic substances, or physically demanding operations. For instance, in the automotive industry (a sector closely related to consumer goods manufacturing), robots weld car bodies in extremely hot environments, a task previously associated with high burn risks for human workers. Similarly, robots handle paint spraying, reducing exposure to harmful solvents. In food processing, robots perform repetitive cutting and packaging tasks, reducing the risk of repetitive strain injuries. The use of robots in these scenarios significantly minimizes the chance of human error leading to accidents.
Examples of Automated Dangerous Jobs
Several dangerous jobs in consumer goods manufacturing have been successfully automated. One prime example is the handling of sharp objects in glass or ceramic manufacturing. Robots can efficiently and safely handle fragile and sharp materials, minimizing the risk of cuts and lacerations. Another example is the automated handling of heavy materials, such as in the construction of large appliances or furniture. Robots can lift and move heavy components without strain or risk of injury, unlike human workers. Furthermore, in the chemical industry, robots can safely handle and mix hazardous chemicals, protecting human workers from exposure to potentially harmful substances. This reduces the risk of chemical burns, inhalation injuries, and long-term health problems.
Workplace Accident Rate Comparison
While precise, universally applicable data comparing accident rates across all factories with and without significant robotic integration is difficult to obtain due to variations in reporting standards and industry specifics, numerous studies show a strong correlation between increased robotic automation and reduced workplace accidents. For example, a study by the National Institute for Occupational Safety and Health (NIOSH) – while not directly comparing accident rates – highlighted the effectiveness of robotic systems in mitigating risks associated with specific hazardous tasks, indirectly suggesting a reduction in overall accident rates. Numerous case studies from individual factories showcasing significant accident reductions following robotic integration further support this correlation. It’s important to note that the reduction in accidents isn’t solely attributed to robots; comprehensive safety protocols and worker training remain crucial.
Ergonomic Improvements in a Manufacturing Setting: Automotive Assembly
The introduction of robots into automotive assembly lines has significantly improved ergonomic conditions.
- Reduced Repetitive Motions: Robots handle repetitive tasks like welding and painting, preventing repetitive strain injuries in human workers.
- Elimination of Heavy Lifting: Robots lift and move heavy components, reducing the risk of back injuries and musculoskeletal disorders.
- Improved Workstation Design: Automation allows for better workstation design, optimizing human-robot interaction and reducing awkward postures.
- Reduced Exposure to Hazardous Materials: Robots handle tasks involving hazardous materials, reducing worker exposure and the associated health risks.
- Increased Work-Life Balance: By reducing the burden of physically demanding and hazardous tasks, robotic automation allows for a more balanced and less physically strenuous work environment, contributing to better employee health and well-being.
Adaptability and Flexibility in Manufacturing Processes: How Robotics Is Advancing The Manufacturing Of Consumer Goods
Robots are revolutionizing manufacturing, not just by increasing speed and precision, but also by offering unprecedented adaptability. This flexibility is crucial in today’s dynamic market, where consumer demands shift rapidly and product variations are increasingly common. The ability to quickly reconfigure robotic systems for different tasks represents a significant competitive advantage.
Reprogramming and adaptation of robots to handle diverse products or production variations is a core strength of modern robotic systems. This is achieved through sophisticated software and intuitive interfaces that allow manufacturers to easily modify robot programs. Instead of building separate production lines for each product, a single robotic cell can be reprogrammed to handle multiple items, reducing capital investment and maximizing resource utilization. This adaptability is particularly beneficial for managing fluctuating demand and order sizes. During peak seasons, robotic systems can be easily scaled up to meet increased production needs, while during slower periods, they can be reconfigured to handle other tasks or products, minimizing downtime and maximizing efficiency.
Robotic Flexibility in Customized Consumer Goods Production
Several industries are already reaping the benefits of robotic flexibility in producing customized consumer goods. The electronics industry, for example, uses robots to assemble a wide range of personalized smartphones and tablets. Different components, colors, and internal configurations are easily accommodated through reprogramming, allowing manufacturers to cater to individual consumer preferences. Similarly, the automotive industry utilizes flexible robotic systems to produce customized vehicle models, offering a vast array of options to consumers. These systems can seamlessly switch between assembling different vehicle components, adapting to changing order specifications with minimal disruption. The apparel industry also benefits from robotic flexibility, using robots for customized clothing production, allowing for on-demand creation of garments with personalized designs, sizes, and materials.
Reconfiguring a Robotic Cell for a Different Consumer Product
Let’s imagine a robotic cell initially configured to assemble smartphones. Reconfiguring this cell to assemble smartwatches would involve a series of steps. First, the end-of-arm tooling (EOAT), the specialized grippers and tools attached to the robot arm, would be replaced. The EOAT designed for handling smartphone components, such as delicate circuit boards, would be swapped for tooling suited to the smaller, more intricate parts of a smartwatch. This might involve changing grippers for finer manipulation and adding tools for precise assembly tasks like attaching tiny watch straps. Second, the robot’s program would be updated. This involves modifying the sequence of actions, the robot’s movements, and the force and speed parameters to match the requirements of smartwatch assembly. New instructions would be added for handling different components and for performing the specific assembly operations involved in smartwatch production. Third, the material handling system feeding components to the robot would be adjusted. Conveyors and feeders would be reconfigured to accommodate the different sizes and shapes of smartwatch components. Finally, quality control checkpoints within the robotic cell would be updated to reflect the specific quality standards for smartwatches. This entire process, while requiring expertise, is significantly faster and less disruptive than setting up an entirely new production line.
The Impact of Robotics on the Workforce
The integration of robotics into manufacturing has undeniably reshaped the landscape of employment in the consumer goods sector. While concerns about job displacement are valid, the reality is far more nuanced, involving a significant transformation of roles rather than a simple reduction in workforce size. This shift necessitates a focus on upskilling and reskilling initiatives to equip workers with the competencies required for thriving in this new era of automated production.
The evolving roles of human workers in robotic-integrated factories are characterized by a move away from repetitive, manual tasks towards more sophisticated and strategic functions. Human expertise remains crucial for oversight, problem-solving, and the integration of human ingenuity into the automated process.
New Skill Sets for Managing and Maintaining Robotic Systems
The introduction of robots demands a new breed of skilled workers. Maintaining and repairing complex robotic systems requires expertise in areas such as mechatronics, programming, and data analysis. Furthermore, the ability to troubleshoot malfunctions, interpret diagnostic data, and manage complex software interfaces is increasingly vital. These skills go beyond basic mechanical aptitude, demanding a deep understanding of computer systems, sensor technology, and robotic control algorithms. Training programs focused on these specialized skills are essential for bridging the gap between the existing workforce and the demands of the modern, robotic-integrated factory.
Job Displacement Concerns Versus New Job Creation
While some jobs involving repetitive manual labor may be automated, robotics simultaneously generates new roles. The demand for robotic technicians, programmers, data analysts, and systems engineers is rapidly expanding. Consider the example of a car manufacturing plant: while robotic arms may have replaced some assembly line workers, the plant now requires specialists to program, maintain, and repair those same robotic arms. Similarly, the need for data analysts to monitor and optimize robotic performance creates entirely new job categories. The net impact on employment depends heavily on the speed of workforce adaptation and the availability of reskilling programs. The fear of widespread job displacement is often overstated when not coupled with proactive workforce development strategies.
Transformation of Job Roles in a Consumer Goods Factory
Imagine a typical consumer goods factory producing electronics. Before robotic integration, the assembly line consisted primarily of workers performing repetitive tasks like soldering components or attaching screens. A visual representation of this would show a long line of workers, each performing a small, isolated part of the assembly process. After robotic integration, the same factory might employ fewer workers directly involved in manual assembly. Instead, the visual would show a more modular layout, with robotic arms handling the repetitive tasks. Human workers would be strategically positioned, overseeing the robots, programming them, troubleshooting malfunctions, and managing the overall production flow. Some workers might be involved in quality control, using advanced sensor data and AI-assisted systems to identify defects. Others would focus on advanced tasks like system maintenance, programming upgrades, and strategic planning. This shift represents a transition from repetitive manual labor to a more skilled and technology-driven workforce, requiring greater expertise and problem-solving capabilities.
Cost Considerations and Return on Investment (ROI)
Implementing robotic systems in manufacturing isn’t a small undertaking; it requires a significant upfront investment. However, the long-term benefits in terms of increased efficiency and reduced costs can lead to a substantial return on investment, making it a compelling proposition for many consumer goods manufacturers. Let’s delve into the financial aspects of robotic integration.
Initial Investment Costs
The initial cost of implementing robotics varies widely depending on several factors. These include the type of robots needed (e.g., collaborative robots or industrial robots), the number of robots required, the complexity of the integration process, and the need for additional infrastructure (such as specialized tooling or software). For example, a single industrial robot arm can cost anywhere from $25,000 to $250,000 or more, while simpler collaborative robots might start around $20,000. Beyond the robots themselves, consider the costs of installation, programming, training personnel, and ongoing maintenance. These additional expenses can significantly increase the total initial investment.
Long-Term Cost Savings
While the initial outlay is substantial, the long-term cost savings can be substantial as well. Increased efficiency, achieved through faster production rates and reduced downtime, is a major factor. Robots can work continuously without breaks, unlike human workers, leading to increased output and reduced labor costs. Furthermore, robots minimize waste by performing tasks with greater precision and consistency, reducing material spoilage and rework. Improved product quality translates into fewer defects and returns, further saving money. Finally, safer working conditions, resulting from robots handling hazardous or repetitive tasks, lead to reduced workplace injuries and associated costs.
Examples of Successful Robotic Implementations
Several consumer goods manufacturers have successfully implemented robotics and achieved a positive ROI. For instance, companies like Procter & Gamble have extensively used robots in their manufacturing facilities for tasks such as packaging and palletizing, resulting in significant efficiency gains and cost reductions. Similarly, many automotive parts suppliers have automated various aspects of their production lines, leading to improved quality and lower labor costs. These success stories highlight the potential for significant returns on investment when robotics are strategically implemented.
ROI Calculation for a Hypothetical Small Business
Let’s consider a small consumer goods manufacturer producing handcrafted candles. Suppose they currently employ five workers earning $30,000 annually each, with an annual production of 100,000 candles. They are considering investing in a robotic system costing $100,000, which can automate the candle-pouring process, increasing production to 150,000 candles annually. The robot requires minimal maintenance at $5,000 annually. The cost savings from reduced labor is $150,000 (5 workers x $30,000). The increased production could lead to higher revenue, but even ignoring that, the net annual savings are $150,000 – $5,000 = $145,000.
The simple ROI calculation would be: ($145,000 annual savings) / ($100,000 initial investment) = 1.45 or 145%. This indicates a significant return on investment within the first year. More sophisticated calculations would incorporate factors like the robot’s lifespan, potential revenue increases, and the discount rate.
Closure
The integration of robotics in consumer goods manufacturing isn’t just a trend; it’s a fundamental shift. It’s a testament to human ingenuity, blending advanced technology with our innate drive for progress. While concerns about job displacement are valid, the overall picture points to a future where humans and robots work side-by-side, leveraging each other’s strengths to achieve unprecedented levels of efficiency and innovation. The robotic revolution is here, and it’s shaping a more efficient, safer, and ultimately, better future for both manufacturers and consumers alike. So buckle up, because this is just the beginning.