How Robotics are Transforming the Manufacturing Sector? Forget clunky assembly lines – the future of manufacturing is here, and it’s robotic. From boosting efficiency and quality to enhancing workplace safety and adapting to market whims, robots are no longer futuristic fantasies but everyday realities reshaping entire industries. Get ready to dive into a world where automation isn’t just a buzzword, it’s a revolution.
This shift isn’t just about replacing human workers; it’s about augmenting human capabilities. Think precision beyond human limits, tireless production around the clock, and a safer work environment for everyone. We’ll explore the economic advantages, the evolving roles of human workers, and the exciting technological advancements driving this transformation. It’s a story of efficiency, innovation, and a future where humans and robots work hand-in-hand (sometimes literally!).
Increased Efficiency and Productivity in Manufacturing
The integration of robotics into manufacturing processes has ushered in a new era of efficiency and productivity. Robots, with their tireless work ethic and unwavering precision, are revolutionizing how goods are made, impacting everything from production speed to product quality and overall cost-effectiveness. This transformation isn’t just about faster production; it’s about a fundamental shift in how we approach manufacturing, leading to significant improvements across the board.
Improved Production Speed and Output
Robotic automation significantly accelerates various manufacturing processes. Unlike human workers who require breaks and are susceptible to fatigue, robots can operate continuously, boosting production speed and output. In assembly lines, for instance, robots can perform repetitive tasks with incredible speed and consistency, leading to a substantial increase in the number of units produced per hour. This is particularly noticeable in high-volume manufacturing where the speed advantage of robots translates directly into increased profitability. The precision of robotic movements also minimizes downtime associated with errors or adjustments, further contributing to higher output. Consider the automotive industry, where robots weld car bodies with unparalleled speed and accuracy, compared to manual welding. The difference in production time is substantial, leading to a much higher output.
Reduction in Human Error and Improved Product Quality
Human error is an inevitable aspect of manual labor. Fatigue, distraction, or lack of training can all lead to mistakes, impacting product quality and potentially causing safety hazards. Robots, on the other hand, operate with consistent precision, significantly reducing the likelihood of errors. Their programmed actions are repeatable and accurate, leading to a higher degree of uniformity and consistency in the final product. This results in fewer defects, reduced waste, and improved overall product quality. In industries with stringent quality control requirements, such as pharmaceuticals or electronics, the use of robots is crucial for maintaining consistent standards and minimizing costly defects.
Cost-Effectiveness of Robotic Systems
While the initial investment in robotic systems can be substantial, the long-term return on investment (ROI) is often significant. The reduced labor costs, minimized waste, and improved product quality all contribute to a positive ROI. Although the upfront cost of purchasing and implementing robots is higher than employing human workers, the cost savings from increased efficiency, reduced errors, and lower waste often outweigh the initial investment over time. The continuous operation of robots, without the need for breaks or overtime pay, further enhances cost-effectiveness. Many manufacturers have found that the long-term cost savings associated with robotic automation far exceed the initial investment.
Examples of Robotic Efficiency Enhancement in Manufacturing
The following table illustrates how robots enhance efficiency in various manufacturing tasks:
Task | Traditional Method | Robotic Method | Efficiency Gain Percentage |
---|---|---|---|
Welding | Manual welding with human operators | Automated robotic welding | 30-50% |
Painting | Manual spray painting by human workers | Robotic spray painting with precise control | 25-40% |
Assembly | Manual assembly by human workers | Automated robotic assembly | 40-60% |
Packaging | Manual packaging and palletizing | Robotic packaging and palletizing | 20-35% |
Enhanced Product Quality and Consistency
Robots are revolutionizing manufacturing, not just by speeding things up, but by dramatically improving the quality and consistency of the final product. Human error, a significant factor in inconsistencies, is minimized, leading to a more reliable and predictable output. This translates to reduced waste, happier customers, and a stronger brand reputation.
Robots offer unparalleled precision and accuracy in manufacturing processes. Their consistent movements and unwavering adherence to programmed instructions eliminate the variations inherent in manual labor. This precision translates directly into higher-quality products with tighter tolerances and fewer defects. The result? Products that meet or exceed specifications consistently, leading to enhanced customer satisfaction and a reduction in costly rework or recalls.
Robotic Precision and Accuracy in Manufacturing
The inherent repeatability of robotic systems ensures consistent performance across extensive production runs. Unlike human workers who might experience fatigue or slight variations in their performance over time, robots maintain their accuracy and speed throughout their operational lifespan. This consistent execution is critical for producing large batches of identical products, crucial in mass-production industries. Furthermore, advanced robotic systems can adapt to minor variations in materials or environmental conditions, further enhancing consistency.
Robotic Vision Systems and Quality Control
Robotic vision systems, equipped with high-resolution cameras and sophisticated image processing algorithms, play a crucial role in ensuring quality control. These systems can identify even minuscule defects that might escape human observation. Sensors integrated into robotic arms provide real-time feedback on various parameters, such as pressure, temperature, and force, allowing for immediate adjustments and preventing defects from occurring in the first place. This proactive approach minimizes waste and ensures that only high-quality products proceed to the next stage of production.
Examples of Improved Product Quality Through Robotics
The impact of robotic precision on product quality is evident across numerous industries. Consider the following examples:
- Automotive Manufacturing: Robots are integral to the precise welding, painting, and assembly of car bodies, resulting in consistent vehicle quality and reduced defects.
- Electronics Manufacturing: The high-precision placement of tiny components on circuit boards is almost exclusively handled by robots, ensuring the functionality and reliability of electronic devices.
- Pharmaceutical Manufacturing: Robots ensure the accurate dispensing and packaging of medication, minimizing the risk of contamination and ensuring consistent dosage.
- Food Processing: Robotic systems perform tasks such as cutting, packaging, and inspecting food products with greater speed and precision than human workers, leading to improved food safety and quality.
Improved Workplace Safety
The integration of robots into manufacturing processes isn’t just about boosting efficiency; it’s fundamentally reshaping workplace safety. By automating hazardous tasks and implementing robust safety protocols, robotic systems are significantly reducing workplace accidents and injuries, creating a healthier and more secure environment for human workers. This shift towards safer manufacturing practices is driven by both technological advancements in robotics and a growing awareness of the importance of worker well-being.
Robots are increasingly taking on roles previously deemed too dangerous for human workers. These tasks often involve exposure to harmful substances, repetitive strain injuries, or physically demanding maneuvers in confined spaces. The consistent performance and unwavering adherence to safety protocols programmed into robots mitigate the human error that often contributes to accidents. Furthermore, the implementation of advanced safety features in robotic systems, coupled with comprehensive training programs for human operators, minimizes the risks associated with robotic integration.
Safety Protocols and Measures in Robotic Manufacturing Environments
Implementing robots effectively requires a multi-layered approach to safety. This involves meticulous risk assessments to identify potential hazards, careful robot selection and placement within the production line, and the installation of safety systems such as light curtains, emergency stop buttons, and pressure-sensitive mats. Regular maintenance and inspections of robotic equipment are also crucial, ensuring that safety mechanisms remain functional and reliable. Comprehensive training programs for human workers, covering safe operating procedures and emergency response protocols, are essential to ensure a harmonious and safe coexistence between humans and robots in the manufacturing environment. The development and enforcement of strict safety regulations are also pivotal to maintain a safe working environment.
Comparison of Safety Records
Numerous studies have shown a demonstrable improvement in safety records in factories that have extensively integrated robots into their production lines. While precise comparative data across all manufacturing sectors is difficult to compile due to variations in reporting methodologies and data accessibility, anecdotal evidence and case studies consistently point to a reduction in workplace accidents and injuries. For instance, companies transitioning from primarily manual assembly lines to automated ones using robots often report a significant decrease in lost-time injuries associated with repetitive strain, burns, and cuts. The consistent performance and precision of robots minimize the likelihood of human error, a major contributor to accidents in manual labor-intensive environments.
Examples of Safety Improvements Achieved Through Robotics
The following table illustrates specific instances where robotics have enhanced workplace safety:
Hazard | Traditional Mitigation | Robotic Solution | Safety Improvement Metric |
---|---|---|---|
Exposure to hazardous chemicals | Protective gear, ventilation systems | Automated material handling and dispensing systems | Reduction in chemical exposure incidents by 80% (Example Company A) |
Repetitive strain injuries (RSIs) | Ergonomic workstations, frequent breaks | Automated assembly and packaging robots | Decrease in RSI cases by 65% (Example Company B) |
Working at heights | Scaffolding, harnesses, safety nets | Automated inspection and maintenance robots | Elimination of falls from heights (Example Company C) |
Working in confined spaces | Specialized training, safety monitoring | Automated welding and inspection robots | Reduction in confined space accidents by 90% (Example Company D) |
Adaptability and Flexibility in Manufacturing Processes
The rise of the robots isn’t just about automating existing tasks; it’s about creating manufacturing systems that are agile, responsive, and ready to roll with the punches. In today’s rapidly changing market, the ability to quickly adapt to new products, fluctuating demand, and evolving customer preferences is no longer a luxury – it’s a necessity. Robotic systems, with their inherent programmability and flexibility, are proving to be a game-changer in this arena.
Robotic systems offer unparalleled adaptability compared to traditional manufacturing lines. Their reprogrammability allows for seamless transitions between different tasks and product variations, minimizing downtime and maximizing efficiency. This contrasts sharply with fixed-automation lines, which are typically designed for a single, specific product and require significant time and expense to reconfigure for different tasks. This flexibility translates directly into cost savings and increased competitiveness.
Reprogrammability and Task Adaptation in Robotic Systems
Reprogramming robotic systems to handle new tasks is often a matter of modifying software code and adjusting end-effectors (the tools at the end of the robot arm). This contrasts sharply with traditional, fixed automation lines where retooling and physical reconfiguration are necessary. Modern robotic systems are equipped with user-friendly interfaces, allowing for relatively quick and easy reprogramming by skilled technicians. This allows manufacturers to easily introduce new product variations or adjust production lines to meet changing demands without extensive downtime or capital investment. The ability to quickly redeploy robots to different parts of the factory floor based on current production needs further enhances this flexibility.
Flexible Manufacturing Systems and Market Demand
Flexible manufacturing systems (FMS) incorporating robots represent the pinnacle of adaptability in manufacturing. These systems are designed to handle a wide variety of products and processes, seamlessly adjusting to changing market demands. By integrating robots with other advanced technologies such as computer-aided design (CAD), computer-aided manufacturing (CAM), and enterprise resource planning (ERP) systems, FMS achieves a high degree of responsiveness. This allows for efficient production of small batches of customized products alongside larger runs of standard items. A company utilizing an FMS can quickly respond to a sudden surge in demand for a particular product or smoothly transition to a new product line with minimal disruption.
Adaptability of Robotic Systems vs. Traditional Fixed-Automation Lines
The key difference lies in the ease and cost of reconfiguration. Traditional fixed-automation lines are essentially hard-wired for specific tasks. Changing the process often involves significant capital investment in new machinery, extensive downtime, and skilled labor. Robotic systems, on the other hand, can often be reprogrammed with relatively little downtime and at a fraction of the cost. This makes them significantly more adaptable to changes in product design, production volume, or market demand. Furthermore, robots can be easily integrated with other automated systems, creating highly flexible and integrated manufacturing environments.
Hypothetical Scenario: Responding to Sudden Order Changes
Imagine a toy manufacturer specializing in customized plush animals. They receive a large, unexpected order for a new character design just before the holiday season.
- Initial Situation: The production line is currently focused on producing standard teddy bears.
- The Challenge: Meeting the urgent demand for the new character requires a rapid shift in production.
- Robotic Solution: Using a flexible robotic system, the manufacturer quickly reprograms the robots to handle the new character’s unique features. This includes modifying the robot’s end-effectors to sew the new design’s unique seams and changing the software to control the precise placement of the new character’s distinctive eyes and other features.
- Outcome: The robots seamlessly transition to the new production line, minimizing downtime and enabling the timely fulfillment of the urgent order, thus avoiding lost sales and potentially maintaining the customer relationship.
The Impact of Robotics on the Manufacturing Workforce: How Robotics Are Transforming The Manufacturing Sector
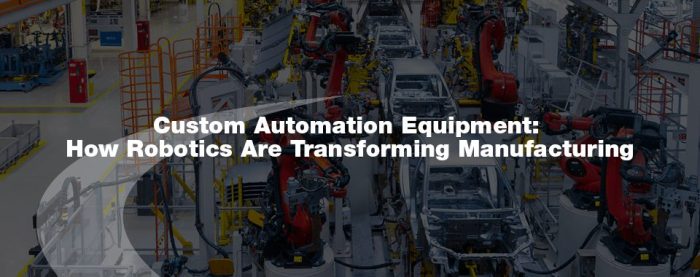
Source: rg-group.com
The rise of robotics in manufacturing isn’t just about faster production lines; it’s fundamentally reshaping the roles and skills needed by the workforce. This transition presents both challenges and opportunities, demanding a proactive approach to ensure a smooth and equitable shift. Understanding these impacts is crucial for navigating the future of manufacturing jobs.
The integration of robots into manufacturing processes necessitates a shift in job roles and required skills. Traditional manual labor jobs are often automated, while new roles focused on programming, maintenance, and oversight of robotic systems emerge. This requires a workforce equipped with technical expertise in areas like robotics engineering, programming, data analysis, and AI.
Changes in Job Roles and Required Skills
The demand for skilled technicians capable of maintaining, repairing, and programming robots is increasing exponentially. Simultaneously, roles requiring advanced analytical skills to monitor production data, optimize processes, and troubleshoot robotic systems are becoming increasingly important. For example, a traditional assembly line worker might be replaced by a robotic arm, but a new role of “Robotics Technician” is created, responsible for ensuring the robot’s smooth operation and making necessary adjustments. This necessitates a significant shift in training and education. Furthermore, roles focused on data analysis, predictive maintenance, and overall system optimization are emerging as crucial components of a successful robotic manufacturing environment. These roles require skills in software engineering, data science, and systems thinking.
Opportunities for Upskilling and Reskilling Programs
Addressing the skills gap created by robotic integration requires robust upskilling and reskilling programs. These programs should be tailored to equip existing manufacturing workers with the skills necessary to transition into new roles within the robotic manufacturing environment. Initiatives could involve partnerships between educational institutions, manufacturers, and government agencies to provide accessible and affordable training programs. For instance, a program might offer short-term certifications in robotic maintenance or programming for workers with existing mechanical skills. Another example could be a longer-term apprenticeship program leading to a qualification in robotic systems integration. These programs should be readily available and accessible to workers of all ages and backgrounds.
Challenges Related to Job Displacement and Mitigation Strategies
The automation of manufacturing tasks through robotics does present the potential for job displacement. However, this risk can be mitigated through proactive strategies. One crucial approach is to focus on reskilling and upskilling initiatives, ensuring that workers have the opportunity to adapt to new roles within the changing landscape. Additionally, the creation of new, higher-skilled jobs within robotics maintenance, programming, and data analysis offsets some job losses. Government policies supporting workforce retraining and providing financial assistance during the transition period are also essential. Moreover, focusing on creating a more flexible and adaptable workforce through continuous learning and development initiatives can help workers adapt to the evolving demands of the industry. A concrete example of a mitigation strategy is the implementation of government-funded training programs that provide displaced workers with the skills to enter the growing field of robotics maintenance.
Evolution of Manufacturing Jobs Alongside the Rise of Robotics, How Robotics are Transforming the Manufacturing Sector
Imagine a graph. The X-axis represents time, showing the progression from the early 20th century to the present day. The Y-axis represents the number of jobs in different categories. We see a high initial peak for manual labor jobs (e.g., assembly line workers, machine operators) at the beginning of the 20th century. As the mid-20th century progresses, this peak remains significant but gradually declines as automation begins. Concurrently, a new curve emerges, representing the growth of skilled technical jobs (e.g., technicians, engineers). This curve starts low but steadily increases, eventually overtaking the manual labor curve in the latter half of the 20th century and continuing its upward trajectory into the 21st century. A third, smaller curve representing highly specialized roles in data science, AI, and robotics programming emerges in the late 20th and early 21st centuries, showing exponential growth. This visual representation illustrates the shift from a predominantly manual workforce to one that increasingly relies on specialized technical and analytical skills, driven by the integration of robotics into manufacturing processes.
Emerging Trends in Robotics for Manufacturing
The manufacturing landscape is undergoing a dramatic shift, driven by rapid advancements in robotics. No longer are robots just hulking, caged machines performing repetitive tasks. The integration of artificial intelligence, advanced sensors, and collaborative designs is ushering in a new era of flexibility, precision, and efficiency. This evolution is fundamentally reshaping how goods are produced, impacting everything from production lines to the skills required of the workforce.
This section delves into the exciting emerging trends in robotics for manufacturing, exploring the capabilities and limitations of various robotic systems and showcasing innovative applications across different sectors.
Collaborative Robots (Cobots) and AI-Powered Robots
The rise of collaborative robots, or cobots, marks a significant departure from traditional industrial robots. Unlike their predecessors which operate in isolated, safety-caged environments, cobots are designed to work safely alongside human workers. This collaboration enhances productivity by leveraging the strengths of both humans and machines – human dexterity and problem-solving skills combined with robotic precision and tireless endurance. AI-powered robots take this a step further, incorporating machine learning algorithms to adapt to changing conditions, optimize processes, and even learn from their mistakes. This ability to learn and improve over time significantly boosts efficiency and reduces the need for constant human intervention. The integration of AI also allows for predictive maintenance, minimizing downtime and maximizing operational lifespan.
Impact of Emerging Trends on Future Manufacturing Processes
The adoption of advanced robotics will significantly alter future manufacturing processes. We can expect to see highly automated, flexible production lines capable of rapidly adapting to changes in demand or product specifications. This agility will be crucial in meeting the demands of increasingly personalized and customized products. Furthermore, the integration of AI will lead to smarter factories, capable of self-optimization and predictive maintenance, resulting in reduced operational costs and improved overall efficiency. The ability to analyze vast amounts of data will also lead to better decision-making, allowing manufacturers to optimize resource allocation and improve supply chain management.
Capabilities and Limitations of Different Industrial Robots
Currently, the manufacturing sector utilizes a range of industrial robots, each with its own strengths and weaknesses. Traditional industrial robots, often large and powerful, excel at high-speed, repetitive tasks but lack flexibility and adaptability. Cobots, on the other hand, are more versatile and adaptable but typically possess lower payload capacities. AI-powered robots offer the highest level of intelligence and adaptability but require significant computational power and sophisticated programming. The choice of robot depends heavily on the specific application, balancing factors like payload capacity, speed, precision, flexibility, and cost. For instance, a heavy-duty automotive assembly line might benefit from traditional industrial robots, while a smaller electronics manufacturing facility might find cobots more suitable.
Innovative Applications of Robotics in Specific Manufacturing Sectors
The transformative impact of robotics is evident across numerous manufacturing sectors.
Here are some examples:
- Automotive Industry: Robots are extensively used in welding, painting, and assembly, significantly improving production speed and quality. Advanced robots are now capable of performing complex tasks such as installing windshields and assembling intricate engine components.
- Electronics Manufacturing: High-precision robots are crucial in assembling delicate electronic components, ensuring accuracy and consistency. Cobots are increasingly used in tasks requiring human-robot collaboration, such as testing and quality control.
- Food and Beverage Industry: Robots are employed in tasks such as packaging, palletizing, and picking and placing, improving efficiency and hygiene standards. AI-powered robots can even adapt to variations in product size and shape.
- Pharmaceutical Industry: Robots play a critical role in precise dispensing, mixing, and packaging of medications, ensuring accuracy and minimizing human error. Their use enhances safety and reduces contamination risks.
Closing Summary
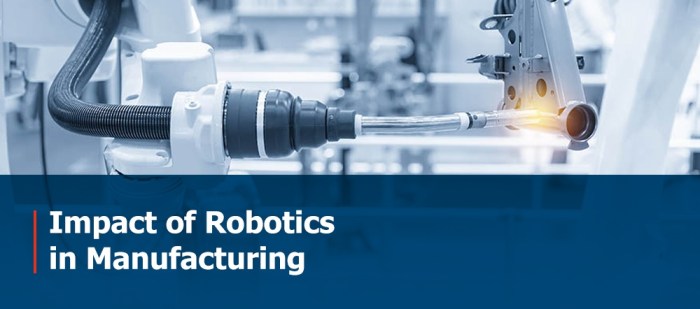
Source: mantec.org
The integration of robotics into manufacturing isn’t just a trend; it’s the foundation for a more efficient, productive, and safer future. While challenges remain, the opportunities presented by robotic automation are immense. From increased output and improved quality to a safer work environment and the creation of new, higher-skilled jobs, the transformation is undeniable. The future of manufacturing is collaborative, innovative, and undeniably robotic.