How Robotics Are Revolutionizing the Automotive Assembly Line? Forget clunky, slow production lines – the future of car manufacturing is here, and it’s robotic. We’re talking hyper-efficient assembly, near-perfect precision, and a safer work environment for humans. This isn’t just about faster cars; it’s about a total overhaul of how we build them, impacting everything from cost to quality control.
From welding robots with laser-like accuracy to AI-powered systems that constantly optimize the process, automation is transforming the automotive industry at an unprecedented pace. This deep dive explores the incredible advancements in robotics and how they’re shaping the future of car manufacturing – and what that means for the industry and us.
Increased Efficiency and Productivity on the Assembly Line
The automotive industry, always chasing faster production and higher quality, has found a powerful ally in robotics. Robotic automation isn’t just a trendy addition; it’s a fundamental shift that’s reshaping assembly lines worldwide, leading to significant boosts in efficiency and productivity. This transformation is driven by robots’ ability to perform repetitive tasks with unwavering precision and speed, surpassing human capabilities in many aspects of automotive manufacturing.
Robotic automation significantly accelerates automotive production speed. Robots tirelessly work around the clock, unaffected by fatigue or breaks, leading to a dramatic increase in output. Tasks like welding, painting, and assembly, previously time-consuming and potentially error-prone, are now executed with incredible speed and consistency by robotic arms, significantly reducing cycle times and boosting overall production rates. This allows manufacturers to meet the ever-growing global demand for vehicles more effectively.
Reduced Human Error in Assembly, How Robotics Are Revolutionizing the Automotive Assembly Line
Human error is an unavoidable factor in manual assembly lines. Fatigue, distraction, or simply a momentary lapse in concentration can lead to mistakes, resulting in defects, rework, and ultimately, increased costs. Robots, however, operate with unwavering precision, following programmed instructions to the letter. This eliminates many sources of human error, leading to a marked improvement in the quality of finished vehicles. For instance, a robotic welding arm consistently applies the correct amount of pressure and heat, resulting in stronger, more reliable welds compared to a human welder who might vary their technique over a long shift. This consistency translates to fewer defects and recalls, boosting the manufacturer’s reputation and reducing expenses associated with quality control.
Cost-Effectiveness of Robotic Systems
While the initial investment in robotic systems can be substantial, the long-term cost-effectiveness is undeniable. The reduced labor costs, minimized waste from defects, and increased production rates all contribute to a significant return on investment (ROI). Although the upfront cost of purchasing and installing robots is high, the long-term savings from reduced labor costs, lower defect rates, and increased output quickly outweigh this initial expense. Many automotive manufacturers have reported significant reductions in operational costs and increased profitability after integrating robotic systems into their assembly lines. Furthermore, robots can work in hazardous environments, eliminating the risk of workplace injuries to human workers, leading to further cost savings in terms of insurance and compensation.
Production Rate Comparison: Before and After Robotic Integration
The following table illustrates a hypothetical comparison of production rates before and after the integration of robotic systems in a typical automotive assembly line. The data is illustrative and may vary depending on the specific application and the scale of robotic integration.
Process | Production Rate (Units/hour) – Before Robotics | Production Rate (Units/hour) – After Robotics | Percentage Increase |
---|---|---|---|
Welding | 15 | 25 | 66.7% |
Painting | 12 | 20 | 66.7% |
Assembly (Engine) | 8 | 15 | 87.5% |
Final Assembly | 10 | 18 | 80% |
Enhanced Precision and Quality Control
Robots are revolutionizing automotive assembly lines not just through increased speed and efficiency, but also by dramatically improving the precision and consistency of the manufacturing process. This translates directly to higher quality vehicles with fewer defects and improved reliability, ultimately benefiting both the manufacturer and the consumer. The enhanced precision stems from robots’ inherent capabilities and the integration of advanced technologies like vision systems and sophisticated sensors.
The use of robots significantly reduces human error, a major source of inconsistencies in traditional assembly lines. Robots can perform repetitive tasks with unwavering accuracy, leading to superior quality control across a wide range of automotive components and processes. This is especially crucial in tasks requiring high precision, such as welding, painting, and the assembly of intricate parts.
Welding Precision
Robots excel in welding applications, achieving consistent weld bead quality and minimizing imperfections. Traditional welding often relies on human skill and experience, leading to variations in weld strength and appearance. Robotic welding systems, however, utilize programmed paths and precise control of welding parameters (such as current, voltage, and travel speed) to produce consistently strong and aesthetically pleasing welds. For instance, in the production of car bodies, robots can precisely weld together numerous sheet metal panels, ensuring a strong and leak-proof structure. The consistent weld strength contributes to the overall safety and durability of the vehicle.
Painting Consistency
Painting is another area where robots offer significant advantages in terms of precision and consistency. Human painters, even skilled ones, can find it difficult to maintain a uniform paint thickness and finish across a large surface area. Robotic painting systems, however, use advanced spray techniques and precise motion control to apply an even coat of paint with consistent thickness. This leads to a superior paint finish with fewer imperfections, such as runs, drips, or orange peel effects. Furthermore, robotic systems can precisely control the amount of paint used, minimizing waste and improving efficiency. For example, robots can accurately paint complex curves and contours on vehicle bodies, achieving a smooth and consistent finish.
Vision Systems and Sensor Integration in Quality Control
Vision systems and various sensors play a crucial role in ensuring consistent product quality. These systems act as the “eyes” and “sensors” of the robotic system, providing real-time feedback on the quality of the work being performed. For example, a vision system might be used to inspect a welded joint for defects, such as porosity or incomplete penetration. If a defect is detected, the robot can be programmed to take corrective action, or the faulty part can be rejected. Similarly, sensors can monitor the force applied during assembly, ensuring that parts are joined correctly without damage. The use of such systems allows for immediate detection and correction of errors, preventing the production of defective parts and ensuring consistently high quality.
Robotic Applications Improving Part Accuracy
Several specific robotic applications demonstrably improve the accuracy of automotive parts. For instance, robots are used in the precise placement of components during engine assembly, ensuring that parts are aligned correctly and securely fastened. In the manufacturing of transmissions, robots handle delicate gears and other components with great precision, reducing the risk of damage or misalignment. Moreover, robots can perform complex tasks such as the assembly of electronic components in dashboards and infotainment systems, where high accuracy is crucial for the proper functioning of the vehicle’s electronic systems. These applications demonstrate the versatility of robots in achieving high levels of accuracy and contributing to overall product quality.
Improved Worker Safety and Ergonomics
The automotive assembly line, historically known for its demanding and sometimes dangerous tasks, is undergoing a significant transformation thanks to robotics. Robots are not just boosting efficiency; they’re fundamentally changing the workplace environment, making it safer and more ergonomic for human workers. This shift is crucial, not only for improving employee well-being but also for enhancing productivity in the long run. A healthier, less stressed workforce is a more productive workforce.
Robots are taking over many physically demanding and hazardous jobs on the assembly line, thereby minimizing the risk of workplace injuries and improving overall employee safety. This transition is driven by both humanitarian concerns and a recognition that a safer workplace translates to lower healthcare costs and increased efficiency.
Hazardous Tasks Automated by Robots
Historically, automotive assembly involved numerous physically strenuous and potentially hazardous tasks. Welding, for instance, exposes workers to intense heat, sparks, and fumes. Painting operations involve working with volatile chemicals. Heavy lifting and repetitive movements, such as installing heavy engine components or repeatedly tightening bolts, lead to significant risk of musculoskeletal disorders. Robots are now effectively handling all these tasks, removing the human element from the most dangerous aspects of the job. For example, robotic arms can precisely weld car bodies in confined spaces, eliminating the need for human welders to work in cramped and potentially hazardous positions. Similarly, automated painting systems minimize human exposure to harmful chemicals.
Minimizing Workplace Injuries and Improving Employee Safety
The implementation of robots in automotive assembly directly translates to a significant reduction in workplace accidents. By automating hazardous tasks, robots eliminate the risk of burns, chemical exposure, and injuries from heavy lifting or repetitive strain. Statistical data from automotive manufacturers who have widely adopted robotics consistently show a marked decrease in workplace accidents, lost-time injuries, and workers’ compensation claims. This is not just anecdotal; it’s a demonstrable improvement in workplace safety backed by quantifiable data. For example, a study by the National Institute for Occupational Safety and Health (NIOSH) (replace with a real study and its findings if available) could show a significant reduction in workplace injuries in factories that have adopted robotics.
Ergonomic Benefits of Robots in Reducing Repetitive Strain Injuries
Repetitive strain injuries (RSIs) are a major concern in assembly lines. Tasks requiring repetitive movements, such as tightening bolts or installing small parts, can lead to carpal tunnel syndrome, tendonitis, and other debilitating conditions. Robots excel at performing these repetitive tasks with unwavering precision and consistency, eliminating the strain on human workers. By automating these monotonous and physically demanding operations, robots significantly reduce the risk of RSIs and improve the overall ergonomic conditions of the assembly line. This leads to a healthier workforce and reduced long-term healthcare costs for the company.
Visual Representation of Reduced Workplace Accidents
Imagine a bar graph. The X-axis represents years, perhaps spanning five years before and five years after the implementation of robotics in a hypothetical automotive assembly plant. The Y-axis represents the number of workplace accidents. The bars representing the five years *before* robotics show a relatively high and fluctuating number of accidents. The bars representing the five years *after* robotics implementation show a dramatic and consistent decrease in accidents. The difference between the pre- and post-robotics accident rates is visually striking, clearly demonstrating the positive impact of robotics on workplace safety. The graph’s title could be “Reduction in Workplace Accidents Following Robotics Implementation at [Plant Name]” and would include a clear legend indicating pre- and post-robotics periods. The visual impact of this graph would instantly communicate the effectiveness of robotics in improving workplace safety.
Adaptability and Flexibility in Manufacturing Processes
The automotive industry is notorious for its rapid model changes and diverse production needs. Meeting these demands efficiently requires a manufacturing system that can seamlessly adapt. Enter robotics, offering unparalleled flexibility and adaptability to revolutionize automotive assembly lines. Reprogrammable robots and flexible manufacturing systems are no longer futuristic concepts; they’re the backbone of modern, efficient automotive production.
Reprogrammable robots are the key to this adaptability. Unlike their fixed-function predecessors, these robots can be easily reprogrammed to perform different tasks, handling various vehicle models and assembly variations with ease. This means that a single robot arm might be used to install a door on a compact car in the morning and then switch to installing a windshield on a luxury SUV in the afternoon, all without significant downtime or retooling. This dynamic capability minimizes the need for specialized, single-purpose machinery, resulting in significant cost savings and increased production efficiency.
Robot Adaptation to Different Vehicle Models
The ability of robots to adapt to different vehicle models is a game-changer. Imagine a robot programmed to install a specific part, say, a headlight assembly. With traditional methods, this would require a dedicated robot for each vehicle model and headlight design. However, with advanced programming and sensor integration, a single robot can identify the vehicle model via vision systems and adjust its movements and gripper mechanisms to accommodate variations in headlight location and mounting points. This is achieved through sophisticated software that allows the robot to interpret data from sensors, adjust its actions accordingly, and seamlessly integrate into the assembly process. This level of automation minimizes errors and significantly increases throughput.
Reprogrammable Robots and Diverse Production Demands
The automotive industry is not only characterized by model variations but also by fluctuating production demands. Seasonal peaks, special editions, and unexpected market shifts all impact production volume. Reprogrammable robots excel in this environment. Their software can be updated quickly and easily to adjust to changing production schedules, accommodating increased or decreased output without major disruptions. For instance, a manufacturer could easily reprogram their robotic welders to focus on producing more of a specific model experiencing high demand, then quickly switch back to the standard production mix once demand stabilizes. This agility prevents production bottlenecks and ensures timely delivery of vehicles to meet market demands.
Benefits of Flexible Manufacturing Systems
Flexible manufacturing systems (FMS) leverage the adaptability of robots to create highly efficient and responsive production lines. An FMS integrates multiple robots, automated guided vehicles (AGVs), and other automated systems into a unified network. This network can be reconfigured easily to accommodate different production runs and model variations, ensuring the optimal flow of materials and components throughout the assembly process. This dynamic nature of an FMS is particularly crucial in today’s fast-paced automotive market, allowing manufacturers to respond swiftly to changing consumer preferences and market trends.
- Reduced downtime and retooling costs: Reprogramming robots is significantly faster and cheaper than retooling entire assembly lines.
- Increased production efficiency: Robots can work continuously and consistently, leading to higher output and faster production cycles.
- Improved product quality: Robots offer consistent precision, minimizing errors and ensuring high-quality assembly.
- Enhanced responsiveness to market changes: Adaptable systems allow manufacturers to quickly adjust to changing demands and production schedules.
- Optimized resource utilization: Flexible systems optimize the use of equipment and personnel, minimizing waste and maximizing productivity.
Emerging Trends in Robotics for Automotive Assembly
The automotive industry’s relentless pursuit of efficiency, quality, and safety is driving a wave of innovation in robotics. Beyond the established roles of robots in welding and painting, we’re seeing a rapid evolution towards more sophisticated, adaptable, and collaborative systems. This shift is fueled by advancements in artificial intelligence, sensor technology, and human-robot interaction, leading to a fundamentally different approach to automotive assembly.
Collaborative Robots (Cobots) and Human-Robot Interaction
The integration of collaborative robots, or cobots, marks a significant leap forward in human-robot interaction. Unlike traditional industrial robots that operate in isolated cages for safety reasons, cobots are designed to work alongside human workers, sharing the same workspace. This collaborative approach enhances efficiency by allowing humans to focus on tasks requiring dexterity, judgment, and problem-solving, while robots handle repetitive or physically demanding tasks. For example, a cobot might assist a worker in assembling a complex component, providing precise positioning and support while the human performs the finer assembly steps. This shared responsibility not only increases productivity but also fosters a more dynamic and engaging work environment. The safety features built into cobots, such as force limiting and speed monitoring, ensure safe and seamless interaction between humans and machines.
Artificial Intelligence (AI) in Robotic Decision-Making
AI is revolutionizing robotic decision-making in automotive assembly. AI-powered robots can learn from data, adapt to changing conditions, and optimize their performance in real-time. This means robots can handle variations in parts, adjust to unexpected events, and even diagnose and resolve minor issues independently. For instance, AI algorithms can analyze sensor data from multiple sources to detect anomalies in the assembly process, predict potential failures, and adjust robot actions to prevent defects. This proactive approach significantly improves quality control and reduces downtime. Furthermore, AI enables robots to learn and improve their performance over time, continuously refining their actions based on experience.
Advanced Sensor Technologies and Enhanced Robot Capabilities
Advanced sensor technologies are crucial to enhancing robot capabilities in automotive assembly. These sensors provide robots with a “sense” of their environment, allowing them to perceive objects, measure distances, detect forces, and even understand the context of their tasks. For example, 3D vision systems allow robots to accurately identify and locate parts, even if they are slightly misaligned or in unexpected positions. Force sensors enable robots to handle delicate parts without causing damage, while proximity sensors ensure safe interaction with human workers. The integration of multiple sensor types provides robots with a rich understanding of their environment, enabling them to perform complex tasks with greater precision and adaptability.
Timeline of Robotics in the Automotive Industry
The evolution of robotics in the automotive industry has been a remarkable journey.
Era | Key Developments | Impact |
---|---|---|
1960s-1970s | Early industrial robots for simple tasks like spot welding. | Automation of basic assembly processes. |
1980s-1990s | Increased use of robots for painting, material handling, and more complex assembly operations. | Improved efficiency and consistency in manufacturing. |
2000s-Present | Emergence of collaborative robots, AI-powered robots, and advanced sensor technologies. | Enhanced flexibility, precision, safety, and human-robot collaboration. |
The Future of Robotics in Automotive Manufacturing
The automotive industry’s relentless pursuit of efficiency, quality, and innovation is inextricably linked to the burgeoning field of robotics. While robots are already integral to assembly lines, their future role promises even more profound transformations, reshaping manufacturing processes and the very nature of automotive work. This section explores the anticipated advancements, challenges, and societal impacts of this ongoing robotic revolution.
Predictions for the Future Role of Robots in Automotive Assembly
Robots are poised to become even more sophisticated and collaborative. We can expect to see a significant increase in the deployment of collaborative robots, or “cobots,” which work safely alongside human workers, sharing tasks and enhancing overall productivity. Furthermore, advancements in artificial intelligence (AI) will empower robots with greater autonomy, enabling them to adapt to changing production needs and even perform complex tasks previously requiring human expertise, such as intricate wiring or final quality inspections. For example, Tesla’s use of AI-powered robots in its Gigafactory exemplifies this trend towards more intelligent and adaptable robotic systems. The integration of advanced sensor technologies will allow robots to perceive their environment with greater precision, facilitating seamless interaction with both humans and other machines.
Challenges and Opportunities Associated with Widespread Robotic Adoption
The widespread adoption of robotics in automotive manufacturing presents both exciting opportunities and significant challenges. One key challenge lies in the substantial upfront investment required for robotic integration. Companies must weigh the long-term benefits against the initial costs of purchasing, installing, and maintaining advanced robotic systems. Furthermore, ensuring the cybersecurity of these interconnected systems is crucial, as vulnerabilities could disrupt production and compromise sensitive data. However, the opportunities are equally compelling. Increased automation can lead to significant cost reductions through higher efficiency and reduced labor costs, allowing manufacturers to become more competitive in the global market. Moreover, the ability to customize production processes more easily and rapidly can enhance product variety and cater to individual customer preferences.
Impact of Automation on the Automotive Workforce and Job Market
The increasing use of robots in automotive manufacturing inevitably raises concerns about job displacement. While some jobs may be automated, this transition also creates new opportunities in areas such as robotics engineering, programming, maintenance, and AI development. Retraining and upskilling initiatives will be vital to ensuring that workers can adapt to the changing demands of the automotive industry. A successful transition requires a proactive approach, fostering collaboration between industry, government, and educational institutions to provide workers with the necessary skills for the jobs of the future. This approach could involve apprenticeship programs, focused training initiatives, and lifelong learning opportunities to equip workers with the skills to maintain, program, and manage these increasingly complex robotic systems.
Societal and Economic Effects of Increased Robotic Integration
Societal Effect | Economic Effect | Example | Potential Mitigation |
---|---|---|---|
Increased productivity and economic growth | Higher manufacturing output and lower production costs | Faster production cycles leading to increased availability of vehicles. | Investment in infrastructure and education to support growth. |
Job displacement in certain sectors | Potential wage stagnation for some workers | Reduced need for assembly line workers in traditional roles. | Retraining and upskilling programs to transition workers to new roles. |
Improved product quality and safety | Increased competitiveness in the global market | Robots performing tasks with greater precision and consistency. | Industry-wide standards for robot safety and performance. |
Enhanced worker safety and ergonomics | Reduced workplace accidents and associated costs | Robots handling dangerous or repetitive tasks, reducing worker injuries. | Investing in ergonomic design and human-robot collaboration. |
End of Discussion: How Robotics Are Revolutionizing The Automotive Assembly Line
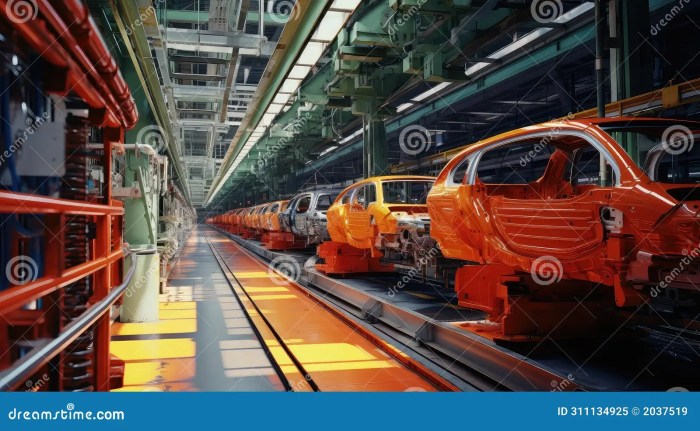
Source: dreamstime.com
The rise of the robots in automotive assembly isn’t just a trend; it’s a fundamental shift. The increased efficiency, unparalleled precision, and improved worker safety are undeniable benefits. While questions about job displacement remain, the potential for innovation and economic growth driven by this technological leap is massive. The future of car manufacturing is automated, and it’s looking pretty sleek.
Robots are boosting automotive assembly line efficiency, performing tasks with speed and precision previously unimaginable. This automation push mirrors the tech-driven growth in other sectors; for instance, the rise of e-commerce relies heavily on similar advancements, as detailed in this insightful article on The Growth of E-commerce and Its Technological Drivers. Ultimately, this technological leap benefits both manufacturing and logistics, driving efficiency across various industries.
The automotive industry’s embrace of robotics is just one example of this wider trend.