How Robotics are Improving Efficiency in Warehousing: Forget dusty, manual labor; warehouses are getting a serious tech upgrade. From zippy robots zipping packages to AI-powered inventory management, automation is revolutionizing logistics. This isn’t just about speed; it’s about accuracy, safety, and a whole new level of efficiency that’s changing the game for businesses big and small. Get ready to dive into the robotic revolution reshaping the world of warehousing.
This shift towards automation isn’t just a trend; it’s a necessity. E-commerce demands faster shipping, tighter inventory control, and a flawless supply chain. Robots are stepping up to meet these challenges, handling tasks previously performed by humans, often with greater speed and precision. We’ll explore the various types of robots transforming warehouses, from autonomous mobile robots (AMRs) navigating the aisles to robotic arms deftly picking and packing orders. We’ll also delve into the impact on warehouse safety, labor costs, and the exciting future of warehouse robotics.
Automated Guided Vehicles (AGVs) and Autonomous Mobile Robots (AMRs) in Warehousing
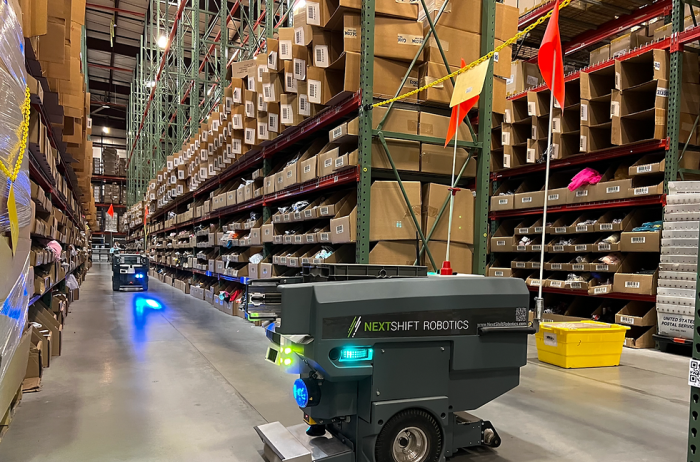
Source: wixstatic.com
The rise of e-commerce and the increasing demand for faster order fulfillment have pushed warehousing operations to their limits. To meet these challenges, warehouses are increasingly adopting automated guided vehicles (AGVs) and autonomous mobile robots (AMRs) to streamline their processes and boost efficiency. These intelligent machines are transforming how goods are moved, stored, and retrieved, leading to significant improvements in speed, accuracy, and overall productivity.
AGV and AMR Types and Applications
AGVs and AMRs, while both used for material handling, differ significantly in their operational capabilities. AGVs follow pre-programmed paths, often relying on embedded wires, magnetic tapes, or laser guidance systems. AMRs, on the other hand, navigate dynamically using sensors and sophisticated software, allowing them to adapt to changing environments and obstacles. This adaptability makes AMRs more flexible and easier to integrate into existing warehouse layouts.
Feature | AGV | AMR |
---|---|---|
Navigation | Pre-programmed paths (wires, magnets, lasers) | Dynamic navigation using sensors (LiDAR, cameras) and AI |
Flexibility | Low; requires significant infrastructure changes for route adjustments | High; adapts to changing environments and obstacles |
Cost | Generally lower initial investment, but higher infrastructure costs | Higher initial investment, but lower infrastructure costs |
Maintenance | Requires regular maintenance of guiding infrastructure | Requires less infrastructure maintenance, but sophisticated software updates are needed |
Applications | Suitable for repetitive tasks along fixed routes, such as transporting pallets or towing carts | Ideal for dynamic environments, handling diverse tasks like order picking, kitting, and transporting goods to different locations |
AGV and AMR Impact on Order Fulfillment
AGVs and AMRs significantly accelerate order fulfillment by automating material handling tasks. AGVs excel at transporting large quantities of goods along established routes, consistently moving pallets from receiving docks to storage locations and vice versa. This reduces transit times and minimizes human error. AMRs, with their greater flexibility, contribute to faster order picking by delivering items directly to human workers or even autonomously picking items from shelves. For example, an AMR could fetch specific items from various locations in the warehouse, consolidating them for a single order, dramatically reducing the time a worker spends walking and searching. Their ability to avoid collisions and navigate crowded environments further enhances efficiency. The accuracy of both AGVs and AMRs also minimizes picking errors and ensures the right items are included in each order.
Integration Challenges with Warehouse Management Systems (WMS), How Robotics are Improving Efficiency in Warehousing
Integrating AGVs and AMRs with existing WMS can present significant challenges. The WMS needs to be able to communicate effectively with the robots’ control systems, providing real-time information on order details, inventory locations, and optimal routes. This requires seamless data exchange and compatibility between different software systems. Furthermore, the integration process can be complex and time-consuming, requiring specialized expertise and potentially significant modifications to the existing WMS. The lack of standardized communication protocols between different robot manufacturers and WMS providers further complicates the integration process. Successfully integrating these systems requires careful planning, thorough testing, and a robust integration strategy to ensure smooth and efficient operation.
Robotic Picking and Packing Systems
The integration of robotics into picking and packing processes is revolutionizing warehousing efficiency, offering significant improvements in speed, accuracy, and cost-effectiveness. These systems are no longer futuristic concepts; they are actively deployed in warehouses worldwide, transforming how businesses handle order fulfillment. This section delves into the specifics of these robotic systems, exploring their capabilities and limitations.
Various robotic systems are employed for picking and packing, each with its unique strengths and weaknesses. The choice of system depends heavily on the type of items handled, warehouse layout, and budget.
Types of Robotic Picking and Packing Systems and Their Characteristics
Several robotic technologies are currently utilized for picking and packing. Understanding their individual capabilities is crucial for effective implementation.
- Cartesian robots: These robots utilize a three-axis system (X, Y, Z) for precise movements, ideal for picking and placing items in a structured environment. They excel at repetitive tasks but lack flexibility in handling diverse item shapes and sizes. Their strength lies in their simplicity and cost-effectiveness for high-volume, low-variety operations.
- SCARA robots: Selective Compliance Assembly Robot Arms offer a four-axis system, providing greater dexterity than Cartesian robots. They are particularly suited for assembly tasks and picking items from conveyor belts, making them suitable for medium-to-high volume operations with moderate product variety. Their speed and precision are advantages, but their reach can be limited.
- Articulated robots: These robots boast multiple axes of movement, providing exceptional flexibility and reach. They can handle a wider variety of items and work in more complex environments. However, they are more expensive and complex to program than other robotic arms. Their adaptability makes them a good choice for warehouses with diverse product lines.
- Collaborative robots (cobots): Designed to work safely alongside humans, cobots are increasingly popular in warehousing. They can handle tasks that require human-robot interaction, such as assisting with complex picking or providing support to human workers. Their collaborative nature enhances efficiency while mitigating safety concerns.
Impact of Robotic Picking and Packing on Labor Costs and Error Rates
The adoption of robotic picking and packing systems significantly impacts both labor costs and human error rates. Automation reduces the reliance on manual labor, leading to cost savings. Simultaneously, robots’ precision minimizes errors associated with manual handling.
For instance, a study by the Material Handling Institute found that automated systems can reduce picking errors by up to 85%. A major e-commerce retailer, Amazon, has widely implemented robotic systems in its fulfillment centers, resulting in a reported 20-30% increase in order fulfillment speed and a significant reduction in labor costs per unit shipped. While precise figures are proprietary, the impact on efficiency is undeniable.
Hypothetical Robotic Picking and Packing System for an E-commerce Fulfillment Center
Consider an e-commerce fulfillment center specializing in apparel. A hypothetical robotic system could be designed as follows:
The system would incorporate a combination of automated guided vehicles (AGVs) for transporting goods, articulated robots for picking items from shelves, and SCARA robots for packing items into shipping boxes. A sophisticated warehouse management system (WMS) would coordinate the robots’ actions, optimizing picking routes and ensuring efficient packing processes. The articulated robots would be equipped with advanced vision systems to identify and locate items on shelves, while the SCARA robots would utilize pre-programmed packing algorithms to efficiently fill boxes. Human workers would oversee the process, intervening only when necessary, for example, dealing with unusual items or resolving system errors. This integrated system would leverage the strengths of each robotic type, maximizing efficiency and minimizing errors in the apparel fulfillment process. The system would also incorporate quality control checkpoints where human workers or additional robotic systems could inspect the packaged items before shipment.
Robotic Sorting and Conveying Systems
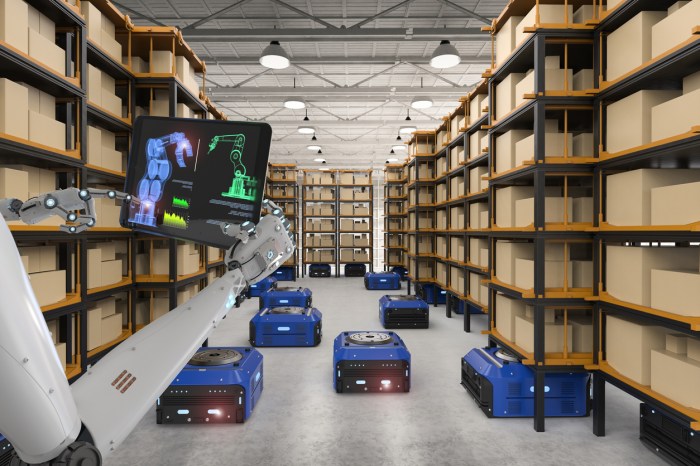
Source: roboticsbusinessreview.com
The efficiency gains from AGVs and AMRs are amplified when paired with sophisticated sorting and conveying systems. These robotic systems are no longer a futuristic fantasy; they’re transforming warehouse operations, allowing for faster processing, reduced errors, and improved scalability. Let’s delve into the specifics of how these systems are revolutionizing the industry.
Robotic sorting and conveying systems represent a significant leap forward in warehouse automation. By automating the often-laborious and error-prone tasks of sorting and moving packages, these systems significantly improve throughput and accuracy. The integration of various technologies, such as computer vision and advanced control algorithms, enables these systems to handle a wide range of items with varying shapes, sizes, and weights.
Comparison of Robotic Sorting Technologies
Several robotic technologies are employed in warehouse sorting, each with its strengths and weaknesses. The choice depends heavily on factors like throughput requirements, item variability, and budget constraints. The table below offers a concise comparison of two prominent technologies:
Feature | Vision-Guided Robots | Robotic Arms | Considerations |
---|---|---|---|
Sorting Method | Uses computer vision to identify and direct items to designated chutes or conveyors. | Manipulates items individually, often using grippers or suction cups, placing them in designated locations. | Vision systems require good lighting and item recognition capabilities. Robotic arms may need specialized end-effectors for different items. |
Throughput | Generally higher throughput for high-volume, homogenous items. | Higher flexibility for diverse items but potentially lower throughput for high volume. | Throughput is influenced by the speed and accuracy of the vision system and robotic arm, as well as the overall system design. |
Flexibility | Less flexible; requires reprogramming for different item types. | More flexible; adaptable to a wider range of items and tasks with reprogramming or end-effector changes. | Flexibility often comes at the cost of initial investment and potential complexity. |
Cost | Generally lower initial investment but may require significant software development. | Higher initial investment, but potentially lower long-term costs for highly variable item handling. | Cost-benefit analysis is crucial considering factors such as labor costs, error rates, and throughput. |
Factors Influencing Robotic Sorting System Selection
Selecting the right robotic sorting system involves a careful evaluation of several key factors. These factors ensure the chosen system aligns with the warehouse’s specific needs and operational goals.
Throughput requirements, the variety of items handled, the available space, the budget, and integration with existing warehouse management systems (WMS) are all critical considerations. For example, a high-volume distribution center handling standardized packages might opt for a vision-guided system for its speed and efficiency, while a smaller warehouse dealing with a diverse range of products might prefer the flexibility of robotic arms. A thorough needs assessment is crucial before making a decision.
Robotic Conveying Systems and Material Flow Optimization
Robotic conveying systems are the arteries of the automated warehouse, ensuring smooth and efficient movement of goods. These systems, often incorporating conveyors, sorters, and robots, optimize material flow by minimizing bottlenecks and maximizing throughput. A typical system might involve a network of conveyors transporting items to a robotic sorting station. After sorting, the items are then routed to their designated locations via additional conveyors or AGVs/AMRs.
For instance, a system might use a combination of roller conveyors and belt conveyors to transport items to a robotic arm that sorts them based on their destination. The robotic arm then places the sorted items onto another conveyor system, which delivers them to the appropriate shipping area or storage location. This eliminates manual handling, reduces transit times, and prevents congestion, ultimately boosting efficiency and minimizing delays.
Inventory Management and Robotics
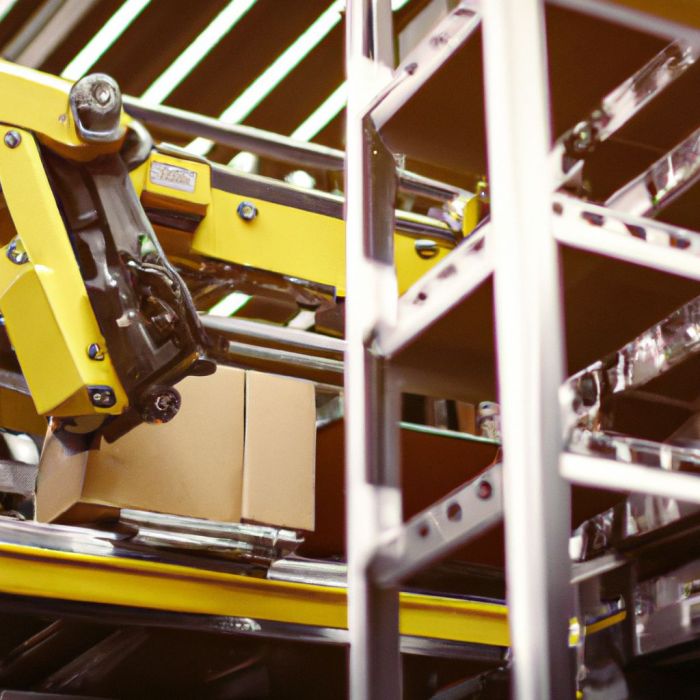
Source: build-wire.com
Robots are revolutionizing warehouse inventory management, moving beyond simple automation to offer unprecedented levels of accuracy, efficiency, and predictive capability. This transformation is driven by the ability of robotic systems to perform tasks with greater speed and precision than humans, leading to significant improvements in inventory tracking, space optimization, and stock management.
The integration of robotics significantly enhances inventory accuracy and tracking. Manual inventory checks are prone to human error, leading to discrepancies between recorded and actual stock levels. Robotic systems, however, can conduct automated audits with far greater precision. For instance, autonomous mobile robots (AMRs) equipped with barcode scanners or RFID readers can systematically navigate the warehouse, scanning every item and comparing it against the inventory management system (IMS). This real-time data collection eliminates manual counting errors and provides an always-up-to-date view of inventory levels. Another example is the use of drones equipped with high-resolution cameras and AI-powered image recognition to perform aerial inventory checks, particularly useful in high-rack warehouses or those with challenging layouts. These drones can quickly identify misplaced items or discrepancies, drastically reducing the time and effort required for inventory audits.
Robotic Systems for Inventory Auditing and Management
Several robotic systems are specifically designed for inventory auditing and management. Automated guided vehicles (AGVs) can be programmed to follow pre-defined routes, systematically scanning inventory as they move. More advanced systems use AMRs, which can navigate dynamically and adapt to changing warehouse conditions. These robots can integrate with warehouse management systems (WMS) to receive instructions, report findings, and automatically update inventory records. Furthermore, collaborative robots (cobots) are being increasingly used for tasks like picking and packing, which indirectly contributes to better inventory accuracy by reducing human error in these crucial processes. The combination of these different robotic systems creates a comprehensive solution for maintaining accurate and up-to-date inventory records.
Robotics are revolutionizing warehousing, optimizing processes from picking to packing. This automation boom mirrors similar advancements in other sectors; think about how autonomous systems are transforming transportation, as explored in this insightful article on How Self-Driving Cars Will Impact Public Transport Systems. Ultimately, both advancements point towards a future where efficiency is king, streamlining operations across various industries.
The result? Faster delivery times and lower costs, even in the complex world of warehouse logistics.
Robotics and Warehouse Space Optimization
Efficient space utilization is crucial for warehouse profitability. Robotic systems contribute significantly to optimizing warehouse layout and maximizing storage capacity. Traditional warehouses often suffer from inefficient space allocation, leading to wasted space and increased operational costs. Robots, however, can help overcome these limitations. For example, a large distribution center might employ a combination of AMRs for transporting goods and automated storage and retrieval systems (AS/RS) for high-density storage. The AMRs navigate the warehouse floor, delivering goods to the AS/RS for storage or retrieval. This dynamic system allows for flexible space allocation and eliminates the need for wide aisles, leading to significant space savings. This contrasts with traditional warehouses which often have fixed aisle widths, which might be larger than necessary in many areas.
Predicting and Preventing Stockouts and Overstocking with Robotics
Robotic systems, combined with advanced analytics and AI, enable warehouses to predict and prevent stockouts and overstocking. By analyzing historical data, sales trends, and real-time inventory levels, robotic systems can generate accurate demand forecasts. This predictive capability allows warehouse managers to proactively adjust inventory levels, preventing stockouts that disrupt operations and lead to lost sales. Simultaneously, the system can also identify slow-moving items, allowing for better inventory management and reduction of overstocking, minimizing storage costs and reducing the risk of obsolescence. For instance, a retail company using robotic inventory management could accurately predict demand for a seasonal item based on past sales data and current market trends. The system would then automatically adjust the order quantity, ensuring sufficient stock without overstocking and minimizing waste.
The Impact of Robotics on Warehouse Safety
Warehouses, bustling hubs of activity, present a unique set of safety challenges. From heavy machinery and towering stacks of goods to fast-paced operations and potential human error, the environment inherently carries significant risk. The integration of robotics, however, is dramatically altering this landscape, offering a pathway to significantly improved worker safety and reduced workplace accidents.
The introduction of robotic systems actively mitigates many common warehouse hazards. These hazards, traditionally leading to injuries, lost time, and increased insurance costs, are now being addressed through automation. This shift towards a more automated warehouse environment isn’t just about efficiency; it’s fundamentally about creating a safer working space for employees.
Common Warehouse Hazards and Robotic Mitigation
Traditional warehouse hazards include slips, trips, and falls due to cluttered floors or uneven surfaces; musculoskeletal injuries from repetitive lifting and manual handling; collisions with forklifts or other moving equipment; and injuries from falling objects. Robotic systems help mitigate these risks in several ways. For example, AGVs and AMRs, operating autonomously, reduce the need for human operators to navigate potentially hazardous areas, minimizing the chance of collisions. Automated picking and packing systems lessen the strain of repetitive tasks, reducing the risk of musculoskeletal disorders. Furthermore, efficient robotic sorting systems contribute to a tidier, less cluttered warehouse, decreasing the likelihood of slips and trips. The precise and controlled movements of robots also minimize the risk of damage to goods, reducing the potential for injuries from falling objects.
Safety Features and Protocols for Robotic Systems in Warehouses
Safe integration of robotics requires robust safety features and protocols. These include implementing advanced sensor technologies to detect obstacles and humans, ensuring robots can stop safely and avoid collisions. Emergency stop mechanisms are crucial, allowing immediate halting of robot operations in case of unexpected events. Clearly defined operational zones and safety barriers are essential to segregate human and robotic workspaces. Regular maintenance and inspection of robotic systems are vital to ensure their continued safe operation, preventing malfunctions that could lead to accidents. Furthermore, comprehensive training programs for warehouse personnel are necessary to familiarize them with the robots’ operation and safety protocols, promoting a safe collaborative working environment.
Safety Benefits of Robotic Systems in Warehousing
Safety Benefit | Description | Example | Impact |
---|---|---|---|
Reduced Risk of Collisions | Autonomous navigation systems minimize human-robot and robot-robot collisions. | AGVs equipped with obstacle detection sensors avoid forklift traffic. | Fewer workplace accidents and injuries. |
Minimized Musculoskeletal Injuries | Automated lifting and handling reduce strain on workers’ bodies. | Robotic arms perform repetitive lifting tasks, reducing worker fatigue and strain. | Lower rates of back injuries and other musculoskeletal disorders. |
Improved Workplace Ergonomics | Robots handle heavy or awkward items, improving worker posture and reducing strain. | Robotic palletizers handle heavy packages, preventing worker strain. | Enhanced worker comfort and reduced risk of injury. |
Enhanced Environmental Safety | Robots contribute to a cleaner and more organized warehouse, reducing trip hazards. | Automated sorting systems keep aisles clear and organized, minimizing trip hazards. | Fewer slips, trips, and falls. |
Future Trends in Robotics for Warehouse Efficiency
The warehouse of tomorrow won’t just be faster and more efficient; it will be fundamentally different, driven by advancements in robotics that are blurring the lines between human and machine collaboration. We’re moving beyond simple automation to a future where AI-powered robots learn, adapt, and optimize warehouse operations in real-time, creating a truly intelligent and responsive logistics ecosystem.
This shift towards advanced robotics promises significant improvements in efficiency, safety, and overall productivity. However, this transformation also presents challenges, including the need for substantial investment, workforce retraining, and careful consideration of ethical implications surrounding increasingly autonomous systems. Let’s delve into the exciting possibilities and potential hurdles ahead.
Emerging Robotic Technologies and Their Impact
The next generation of warehouse robots will leverage cutting-edge technologies to achieve unprecedented levels of efficiency. AI-powered robots, for instance, will move beyond pre-programmed tasks to learn from data, adapt to changing conditions, and even anticipate future needs. Collaborative robots (cobots), designed to work safely alongside humans, will handle tasks requiring dexterity and judgment, filling the gaps where fully autonomous robots may fall short. We’ll also see the increased integration of computer vision systems, enabling robots to accurately identify and handle a wider variety of items, regardless of size, shape, or packaging. Imagine a warehouse where robots not only sort packages but also identify damaged goods or discrepancies in inventory, all with minimal human intervention. This level of sophisticated automation will dramatically reduce human error, improve accuracy, and streamline operations.
Challenges and Opportunities of Widespread Robotic Adoption
The transition to a highly automated warehouse isn’t without its challenges. High initial investment costs for advanced robotics and the need for extensive system integration can be significant barriers to entry, particularly for smaller businesses. Furthermore, integrating these new technologies requires retraining existing staff to manage and maintain the robotic systems, necessitating a significant investment in workforce development. Addressing concerns about job displacement through upskilling initiatives and the creation of new, higher-skilled roles will be crucial for a successful transition. However, the opportunities are equally compelling. Increased efficiency translates to lower operational costs, faster order fulfillment, and enhanced customer satisfaction. The ability to handle higher volumes of goods with greater accuracy also opens doors to new market opportunities and improved competitiveness.
Predicted Advancements in Warehouse Robotics (Next Decade)
The next ten years will witness a dramatic acceleration in the capabilities and adoption of warehouse robotics. Here’s a glimpse into the likely trajectory:
- 2024-2026: Widespread adoption of AI-powered path planning and obstacle avoidance in AMRs, leading to increased efficiency and reduced congestion in warehouses.
- 2027-2029: Significant advancements in robotic picking and packing systems, capable of handling a wider range of items with greater dexterity and speed. Increased use of cobots for tasks requiring human-robot collaboration.
- 2030-2034: Emergence of fully autonomous mobile robots capable of performing complex tasks, including inventory management, quality control, and even light maintenance. Integration of advanced sensor technologies, such as LiDAR and 3D vision, for improved navigation and object recognition.
Closing Summary: How Robotics Are Improving Efficiency In Warehousing
The integration of robotics in warehousing isn’t just about replacing human workers; it’s about creating a symbiotic relationship between humans and machines. By automating repetitive and physically demanding tasks, robots free up human employees to focus on more complex and strategic roles, leading to a more efficient and fulfilling work environment. The future of warehousing is undeniably robotic, promising increased efficiency, reduced costs, and a safer working environment for everyone. It’s a future where technology and human ingenuity work hand-in-hand to deliver a seamless and efficient supply chain.