How Digital Twins Can Revolutionize Manufacturing Processes? Forget clunky assembly lines and guesswork – we’re diving into the future of manufacturing, where digital twins are the new game-changers. These virtual replicas of real-world processes aren’t just simulations; they’re predictive powerhouses, offering unparalleled insights into efficiency, cost optimization, and even predicting potential snags before they happen. Prepare to be amazed by how this technology is transforming industries and paving the way for smarter, more responsive factories.
Imagine a world where you can test new production strategies in a virtual environment before implementing them, tweak parameters without disrupting the actual workflow, and even predict equipment failures days in advance. That’s the power of digital twins. They leverage data from various sources – sensors, PLCs, ERP systems – to create a dynamic, real-time representation of your manufacturing process. This allows for proactive adjustments, optimized resource allocation, and ultimately, a more efficient and profitable operation. We’ll explore the practical applications, the data integration challenges, and the future potential of this transformative technology.
Introduction to Digital Twins in Manufacturing
Forget sci-fi fantasies; digital twins are already reshaping the manufacturing landscape. They’re not just futuristic concepts; they’re powerful tools offering real-time insights and predictive capabilities that are revolutionizing how products are designed, manufactured, and maintained. Essentially, a digital twin is a virtual representation of a physical asset or process, mirroring its behavior and performance in real-time. This allows manufacturers to experiment, optimize, and troubleshoot without impacting the actual physical system, leading to significant cost savings and efficiency gains.
Digital twins in manufacturing aren’t just simple 3D models; they’re complex, interconnected systems drawing data from various sources. They’re the key to unlocking a new era of predictive maintenance and optimized production lines. Imagine having a virtual copy of your entire factory, constantly updated with real-time data on every machine, every process, and every product. That’s the power of a digital twin.
Core Components of a Digital Twin System in Manufacturing, How Digital Twins Can Revolutionize Manufacturing Processes
A robust digital twin system requires a seamless integration of several key components. These components work together to create a comprehensive and accurate virtual representation of the physical manufacturing environment. Without this integrated approach, the digital twin loses its predictive power and fails to deliver on its promise of optimized processes.
- Data Acquisition: This involves collecting data from various sources, including sensors embedded in machinery, production line monitoring systems, and enterprise resource planning (ERP) software. This data forms the foundation of the digital twin, providing real-time insights into the physical asset’s performance.
- Data Modeling and Simulation: This stage involves creating a virtual model of the physical asset or process, incorporating data from the acquisition phase. Advanced algorithms and simulations are used to predict future behavior based on historical data and current conditions. This allows for “what-if” scenarios to be explored virtually.
- Data Analysis and Visualization: Sophisticated analytics tools process the collected data to identify trends, anomalies, and potential issues. Data visualization tools provide intuitive dashboards and reports, enabling manufacturers to quickly grasp key performance indicators (KPIs) and make informed decisions.
- Integration and Collaboration: Effective digital twin systems require seamless integration with existing enterprise systems, such as ERP and MES (Manufacturing Execution Systems). This facilitates data sharing and collaboration across different departments and teams, fostering a more holistic view of the manufacturing process.
Benefits of Implementing Digital Twins in Manufacturing Processes
The advantages of implementing digital twin technology in manufacturing are numerous and impactful. From reducing downtime to improving product quality, the ROI on a well-implemented digital twin system can be substantial. Companies that have embraced this technology have seen remarkable improvements across their operations.
- Predictive Maintenance: By analyzing real-time data and predicting potential equipment failures, manufacturers can proactively schedule maintenance, minimizing downtime and maximizing equipment lifespan. For example, a company might predict a bearing failure weeks in advance, allowing for a planned replacement during a low-production period, preventing costly emergency repairs and production halts.
- Optimized Production Processes: Digital twins enable manufacturers to simulate and optimize production processes before implementing changes in the physical world. This reduces the risk of costly errors and allows for the identification of bottlenecks and inefficiencies, leading to improved throughput and reduced waste.
- Improved Product Quality: By monitoring the manufacturing process in real-time and identifying deviations from specifications, manufacturers can ensure consistent product quality and reduce defects. Real-time feedback allows for immediate adjustments to the process, preventing the production of faulty products.
- Faster Time-to-Market: By simulating and optimizing designs and processes virtually, manufacturers can significantly reduce the time required to bring new products to market. This allows companies to stay ahead of the competition and capitalize on emerging market opportunities.
Applications of Digital Twins in Manufacturing Processes
Digital twins are no longer a futuristic concept; they’re actively reshaping manufacturing, offering unprecedented levels of efficiency, optimization, and control. By creating a virtual mirror of physical assets and processes, manufacturers gain invaluable insights that drive improvements across the entire production lifecycle. Let’s explore some key applications.
Predictive Maintenance using Digital Twins
Predictive maintenance, powered by digital twins, moves beyond reactive or even preventative measures. Instead of relying on scheduled maintenance or waiting for failures, manufacturers can anticipate potential equipment malfunctions. Sensors embedded in physical machinery feed real-time data into the digital twin, allowing algorithms to analyze operational patterns and predict when components are likely to fail. For instance, a digital twin of a bottling plant’s conveyor belt might detect subtle changes in vibration or motor current, indicating impending bearing failure. This early warning allows for proactive maintenance, minimizing downtime and preventing costly production disruptions. The result is increased equipment lifespan and reduced maintenance costs.
Optimizing Production Line Efficiency with Digital Twins
Digital twins provide a virtual playground for experimenting with production line configurations and parameters without disrupting actual operations. Manufacturers can simulate different scenarios – altering machine speeds, sequencing, or even layout – to identify bottlenecks and optimize throughput. Imagine a car manufacturer using a digital twin to test the impact of adding a new robotic arm to their assembly line. The twin can model the effects on cycle time, worker efficiency, and overall production capacity, allowing for data-driven decisions before any physical changes are implemented. This virtual experimentation minimizes risks and accelerates the optimization process.
Quality Control and Defect Detection using Digital Twins
Digital twins enable real-time monitoring of product quality throughout the manufacturing process. By integrating data from various sources – including sensors, cameras, and quality control tests – the twin provides a comprehensive view of product characteristics and potential defects. For example, a digital twin of a semiconductor fabrication plant can detect minute variations in chip dimensions or material properties, flagging potential defects before they reach the end of the line. This early detection significantly reduces waste, improves product yield, and enhances overall quality.
Improving Supply Chain Management with Digital Twins
Consider a hypothetical scenario: a global electronics manufacturer uses a digital twin to model its entire supply chain, from raw material sourcing to finished product delivery. This twin incorporates data on supplier performance, transportation routes, warehouse inventory levels, and customer demand. By simulating various disruptions – such as a natural disaster affecting a key supplier or a port closure due to labor strikes – the manufacturer can proactively adjust its strategy, mitigating potential delays and ensuring uninterrupted production. This level of foresight is invaluable in today’s volatile global supply chain environment. The digital twin acts as a sophisticated “what-if” analyzer, enabling informed decision-making and resilient supply chain management.
Comparison of Traditional and Digital Twin Manufacturing Methods
Method | Efficiency | Cost | Time |
---|---|---|---|
Traditional Manufacturing | Lower; relies on reactive maintenance and less optimized processes | Higher; more downtime, waste, and reactive maintenance costs | Longer; slower optimization cycles, longer lead times |
Digital Twin Manufacturing | Higher; predictive maintenance, optimized processes, and real-time monitoring | Lower (in the long run); reduced downtime, waste, and proactive maintenance | Shorter; faster optimization cycles, reduced lead times |
Data Acquisition and Integration for Digital Twins
Building a truly effective digital twin in manufacturing requires a robust and reliable data pipeline. This means gathering information from diverse sources, cleaning it up, and seamlessly integrating it into a unified system that reflects the real-world counterpart. Without this crucial step, your digital twin remains a mere simulation, lacking the real-time responsiveness and predictive capabilities that make it transformative.
Data Sources for Manufacturing Digital Twins
A manufacturing digital twin thrives on a rich diet of data. Sources range from the shop floor to the executive suite, each contributing a vital piece of the puzzle. These sources offer a holistic view, allowing for comprehensive analysis and informed decision-making.
- Sensors: These are the eyes and ears of your digital twin, providing real-time data on machine performance, environmental conditions (temperature, humidity), and product quality. Examples include vibration sensors on machinery, temperature sensors in ovens, and vision systems inspecting products.
- PLCs (Programmable Logic Controllers): These are the brains of many automated systems, controlling processes and collecting data on production parameters such as speed, pressure, and throughput. This data provides valuable insights into the efficiency and performance of individual machines and entire production lines.
- ERP (Enterprise Resource Planning) Systems: These systems manage the broader business processes, offering data on orders, inventory, scheduling, and resource allocation. Integrating this data allows for a holistic view of the manufacturing process, connecting production to the overall business strategy.
- CMMS (Computerized Maintenance Management Systems): These systems track maintenance activities, equipment history, and spare parts inventory. Integrating this data helps predict maintenance needs and optimize downtime.
- CAD/CAM Systems: These systems contain design and manufacturing process information, providing the digital twin with a foundational understanding of the intended product and manufacturing process.
Data Cleaning and Preprocessing
Raw data is rarely ready for immediate integration. Cleaning and preprocessing are essential steps to ensure data accuracy and consistency. This involves handling missing values, identifying and correcting outliers, and transforming data into a usable format.
- Missing Data Handling: Techniques like imputation (filling in missing values based on other data points) or removal of incomplete records are employed. The choice depends on the amount of missing data and its impact on analysis.
- Outlier Detection and Correction: Outliers – unusual data points – can skew results. Methods like box plots or z-score analysis help identify outliers, which can then be corrected or removed. For example, a sensor malfunction might generate an unusually high temperature reading.
- Data Transformation: This involves converting data into a consistent format suitable for integration. For example, converting units of measurement or normalizing data to a common scale.
- Data Validation: This step involves checking the data’s accuracy and consistency against known standards or expected ranges. This helps catch errors before they propagate through the system.
Challenges of Data Integration from Diverse Sources
Integrating data from various sources presents significant challenges. Different systems often use different data formats, communication protocols, and data structures. Data silos, security concerns, and ensuring real-time data synchronization further complicate the process. For instance, integrating data from a legacy PLC system with a modern cloud-based ERP system requires careful planning and potentially custom software development.
Step-by-Step Guide to Data Integration for a Digital Twin
The process of data integration is iterative and requires careful planning.
- Data Source Identification and Assessment: Identify all relevant data sources and assess their data quality, availability, and accessibility.
- Data Standardization: Define common data formats, units, and structures to ensure consistency across all sources.
- Data Cleaning and Preprocessing: Apply the necessary cleaning and preprocessing techniques as described above.
- Data Transformation: Convert data into a suitable format for integration into the digital twin platform.
- Data Integration Strategy Selection: Choose an appropriate integration method, such as ETL (Extract, Transform, Load) processes or real-time data streaming.
- Data Integration Implementation: Implement the chosen integration strategy, using appropriate tools and technologies.
- Data Validation and Monitoring: Continuously monitor the data quality and integrity to ensure the digital twin remains accurate and reliable.
Simulation and Modeling with Digital Twins
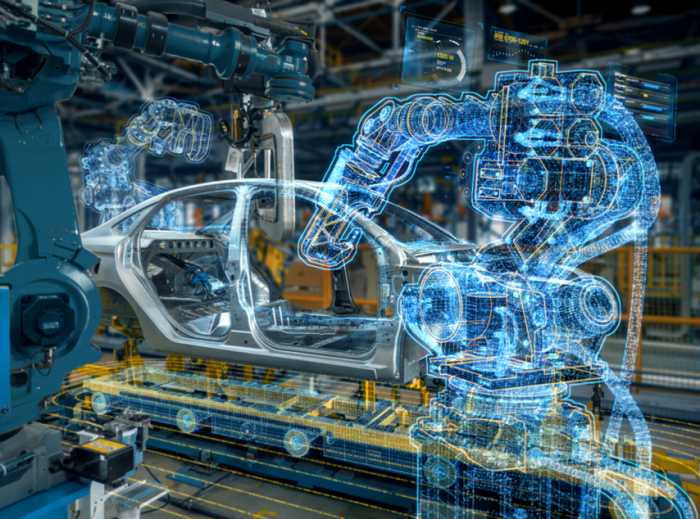
Source: iotpractitioner.com
Digital twins aren’t just static representations of physical assets; they’re powerful tools for predicting future performance and optimizing manufacturing processes. By leveraging sophisticated simulation techniques, manufacturers can gain invaluable insights into their operations, leading to increased efficiency, reduced costs, and improved product quality. This section delves into the world of simulation and modeling within the digital twin ecosystem.
Simulation within a digital twin environment uses a variety of techniques to mirror real-world manufacturing processes. These techniques range from simple, rule-based models to highly complex physics-based simulations, depending on the complexity of the process being modeled and the level of accuracy required. The choice of simulation technique directly impacts the insights gained and the subsequent optimization strategies employed.
Digital twins are poised to overhaul manufacturing, offering unparalleled predictive capabilities and optimization. Think about the level of immersion and realism already achieved in gaming; check out this article on The Future of Gaming: How AI and VR Are Changing the Experience to see how similar tech is shaping interactive experiences. This same level of detail and simulation is now being applied to factory floors, leading to massive efficiency gains and reduced downtime.
Simulation Techniques in Digital Twin Modeling
Several techniques power the simulation capabilities of digital twins. Discrete event simulation (DES) models the flow of entities through a system, ideal for analyzing bottlenecks in assembly lines. Agent-based modeling (ABM) simulates the interactions of individual agents, useful for understanding complex human-machine interactions. Finite element analysis (FEA) is employed for structural analysis, predicting stress and strain on components under various conditions. System dynamics modeling provides a holistic view of interconnected systems, helpful in analyzing feedback loops and overall system behavior. The choice depends heavily on the specific manufacturing process and the questions being addressed. For instance, simulating a high-speed automated assembly line might benefit from DES, while analyzing the impact of worker fatigue on productivity might be better suited to ABM.
Optimizing Parameters and Identifying Bottlenecks through Simulation
Simulations allow manufacturers to virtually experiment with different parameters without disrupting actual production. For example, a simulation of a chemical process could test different temperatures and pressures to optimize yield and reduce waste. By systematically altering parameters within the digital twin, engineers can identify bottlenecks, such as slowdowns in specific stages of the production line, or areas where material waste is high. These simulations can reveal inefficiencies invisible in the real-world environment, allowing for targeted improvements. Imagine a bottling plant using simulation to optimize conveyor belt speed and bottle placement to minimize spills and maximize throughput. The virtual experiments can point directly to the optimal settings, saving time and resources during the physical implementation.
Comparison of Simulation Software
A variety of software packages support digital twin development and simulation. ANSYS, a widely used platform, offers tools for FEA, CFD (computational fluid dynamics), and other physics-based simulations. Siemens NX offers integrated CAD/CAM/CAE capabilities, streamlining the entire product development lifecycle. Similarly, Dassault Systèmes’ 3DEXPERIENCE platform provides a comprehensive environment for digital twin creation and management. The choice of software often depends on the specific needs of the manufacturer, including the complexity of the processes being modeled, the required level of accuracy, and budget considerations. Each platform offers unique strengths and capabilities, and selecting the right one is crucial for successful digital twin implementation.
Predicting the Impact of Production Parameter Changes
Simulations are invaluable for predicting the consequences of changes in production parameters. For example, increasing the speed of a machine in a manufacturing line might increase throughput but could also lead to increased wear and tear or reduced product quality. A digital twin simulation can predict these outcomes, allowing manufacturers to make informed decisions. Consider a food processing plant altering the cooking temperature of a product. Simulation can predict the impact on taste, texture, and shelf life, guiding adjustments for optimal product quality while adhering to safety regulations. Similarly, modifying the injection pressure in a plastic molding process can be simulated to determine the effect on product dimensions and structural integrity, avoiding costly defects and production downtime.
Digital Twin Visualization and Analysis: How Digital Twins Can Revolutionize Manufacturing Processes
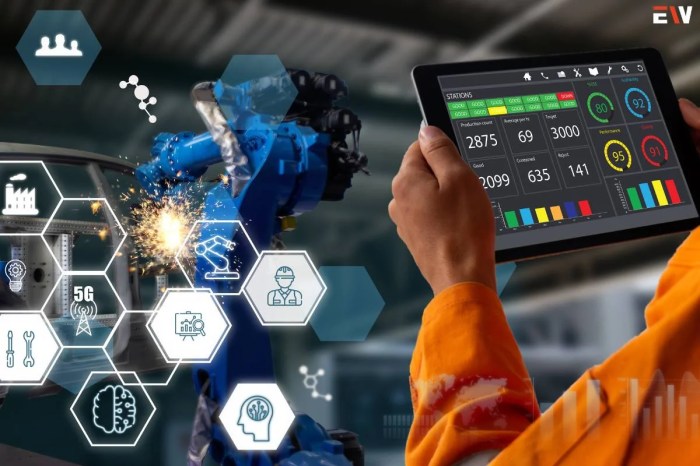
Source: enterprisewired.com
Making sense of the massive data streams generated by a digital twin is crucial for its effectiveness. Without clear, insightful visualizations, the potential benefits remain untapped. Effective visualization transforms raw data into actionable intelligence, allowing manufacturers to identify bottlenecks, optimize processes, and ultimately boost productivity. This section explores how to present complex digital twin data in a user-friendly and informative way.
Data visualization for digital twins leverages various techniques to present information effectively. These methods range from simple charts and graphs to interactive dashboards and 3D models, each tailored to specific data types and user needs. The choice of visualization method depends on the type of data being presented and the target audience. For instance, a simple line graph might suffice to track production output over time, while a 3D model might be necessary to visualize the assembly process of a complex product.
Dashboard and Reporting Tools for KPI Monitoring
Dashboards provide a centralized, at-a-glance view of key performance indicators (KPIs). These tools aggregate data from various sources within the digital twin, presenting them in an easily digestible format. Effective dashboards use color-coding, interactive elements, and clear labeling to highlight trends and anomalies. For example, a dashboard might show real-time production rates, machine uptime, and defect rates, all color-coded to indicate performance levels (green for good, yellow for caution, red for critical). Regular reporting tools then generate summaries of these KPIs over specific periods, facilitating trend analysis and informed decision-making. These reports can be scheduled automatically, ensuring stakeholders always have access to the latest performance data.
Effective Visualization Techniques for Complex Data
Visualizing complex data effectively often requires a combination of techniques. For instance, a heatmap can show the distribution of defects across a production line, highlighting areas needing immediate attention. Interactive 3D models allow users to explore the digital twin in detail, examining individual components and their interactions. Animations can simulate the manufacturing process, visualizing the flow of materials and identifying potential bottlenecks. Furthermore, the use of comparative visualizations, such as bar charts comparing performance across different production lines or time periods, allows for quick identification of areas for improvement. Choosing the right combination of these techniques depends heavily on the specific needs and the complexity of the data.
Hypothetical Visualization Dashboard for an Automotive Assembly Line
Imagine a dashboard for a digital twin of an automotive assembly line. The dashboard would display key metrics such as:
- Real-time Production Rate: A large, easily readable number showing the number of vehicles assembled per hour, color-coded based on pre-defined targets.
- Machine Uptime: A series of gauges representing the uptime of critical machines (e.g., welding robots, painting booths), color-coded to indicate operational status.
- Defect Rate: A line graph tracking the defect rate over time, highlighting any significant spikes or trends.
- Bottleneck Identification: A heatmap of the assembly line, highlighting sections experiencing delays or slowdowns.
- Inventory Levels: Bar charts showing the current inventory levels of key components, alerting to potential shortages.
- Predictive Maintenance: A section displaying the predicted remaining useful life of key components, allowing for proactive maintenance scheduling.
This dashboard provides a comprehensive overview of the assembly line’s performance, allowing managers to quickly identify and address any issues. The interactive nature of the dashboard allows for deeper dives into specific areas of concern, providing detailed information to support informed decision-making. The use of color-coding and clear labeling ensures that even non-technical users can easily understand the information presented.
Challenges and Future Trends of Digital Twins in Manufacturing
The journey towards fully realized digital twins in manufacturing isn’t without its hurdles. While the potential benefits are immense, several challenges need to be addressed to unlock the technology’s true transformative power. Overcoming these obstacles will pave the way for smarter factories and a more efficient, resilient manufacturing landscape.
Data Management and Integration Complexity
Implementing a comprehensive digital twin requires the seamless integration of data from numerous sources, including CAD models, sensor readings, simulations, and enterprise resource planning (ERP) systems. This process can be incredibly complex, particularly in large-scale manufacturing environments with legacy systems and disparate data formats. Effective data governance, standardization, and robust data pipelines are crucial to overcome this challenge. For instance, a company might struggle to integrate data from older CNC machines that don’t have readily available digital interfaces with newer, IoT-connected equipment. This requires careful planning and potentially significant investments in data infrastructure and integration tools.
Computational Resources and Processing Power
High-fidelity digital twins, capable of accurately representing complex manufacturing processes, require significant computational resources. Simulating intricate systems in real-time or near real-time demands powerful hardware and sophisticated software algorithms. The computational cost of running these simulations, especially for large-scale models, can be prohibitive for some manufacturers, particularly smaller businesses. Cloud computing offers a scalable solution, but concerns about data security and latency need to be addressed. Consider the challenge of simulating the entire production line of a car manufacturer in real-time; this requires enormous processing power.
Security and Privacy Concerns
Digital twins often contain sensitive data related to intellectual property, production processes, and customer information. Protecting this data from unauthorized access and cyberattacks is paramount. Robust cybersecurity measures, including access control, data encryption, and regular security audits, are essential to maintain the integrity and confidentiality of digital twin data. A breach could compromise sensitive information and disrupt operations, highlighting the need for proactive security protocols.
Skill Gap and Expertise
Developing, deploying, and maintaining digital twins requires specialized skills in areas such as data science, software engineering, simulation, and domain expertise in manufacturing processes. There is a growing demand for professionals with these skills, but a significant skills gap currently exists. Investing in training and development programs is crucial to build the necessary workforce capable of effectively leveraging digital twin technology. This includes upskilling existing employees and attracting new talent with the required expertise.
AI and Machine Learning in Enhancing Digital Twin Capabilities
AI and ML are poised to revolutionize digital twin capabilities. By analyzing vast amounts of data from the physical twin and simulation results, AI algorithms can identify patterns, predict anomalies, and optimize manufacturing processes. For example, predictive maintenance using AI can analyze sensor data from machines to predict potential failures, allowing for proactive maintenance and reducing downtime. Similarly, AI-powered process optimization can analyze simulation results to identify optimal operating parameters, leading to improved efficiency and quality.
Future Potential of Digital Twins in Smart Factories and Industry 4.0
Digital twins are a cornerstone of smart factories and Industry 4.0 initiatives. They enable the creation of interconnected, data-driven manufacturing systems that are more efficient, resilient, and adaptable. By integrating digital twins with other Industry 4.0 technologies such as IoT, cloud computing, and advanced analytics, manufacturers can achieve significant improvements in productivity, quality, and sustainability. This involves creating a holistic ecosystem where data flows freely between different systems, enabling real-time monitoring, analysis, and control of manufacturing processes.
Future Applications of Digital Twins in Manufacturing
The potential applications of digital twins in manufacturing extend far beyond current implementations. Consider the development of digital twins for entire supply chains, enabling end-to-end visibility and optimization. This would allow manufacturers to anticipate disruptions, optimize logistics, and improve collaboration with suppliers. Another area is the use of digital twins for designing and testing new products and processes in a virtual environment, significantly reducing time and costs associated with physical prototyping. Furthermore, the application of digital twins in sustainable manufacturing is gaining traction, helping manufacturers optimize resource utilization, reduce waste, and minimize their environmental impact. For example, a digital twin could simulate the impact of different production processes on energy consumption, allowing for the selection of the most energy-efficient option.
Final Wrap-Up
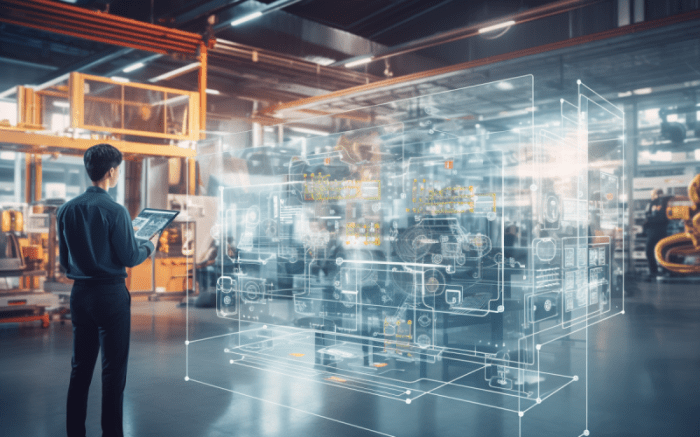
Source: frozenet.com
Digital twins aren’t just a futuristic concept; they’re a tangible reality reshaping manufacturing today. From predictive maintenance that minimizes downtime to optimized production lines that boost efficiency, the benefits are undeniable. While challenges exist in data integration and implementation, the potential for smarter factories, streamlined processes, and improved profitability is too significant to ignore. As AI and machine learning continue to evolve, expect digital twins to become even more sophisticated and indispensable, driving the next wave of innovation in manufacturing.