How Digital Twins Are Changing the Way Industries Manage Operations? Forget clunky spreadsheets and guesswork. Digital twins, essentially virtual replicas of physical assets, are revolutionizing how businesses operate. From predicting equipment failures in manufacturing plants to optimizing logistics in global supply chains, these virtual counterparts offer unparalleled insights and efficiency. This isn’t just about futuristic tech; it’s about making real-time, data-driven decisions that boost the bottom line and keep operations running smoothly. We’re diving deep into how this game-changing technology is reshaping various sectors.
Imagine having a perfect digital mirror of your entire operation, constantly updating and providing insights you never thought possible. That’s the power of digital twins. They’re not just simulations; they’re dynamic, interactive models that learn and adapt as real-world conditions change. This allows for proactive maintenance, optimized resource allocation, and ultimately, a significant reduction in operational costs and downtime. This level of precision and control is transforming how industries manage their assets, predict potential problems, and ultimately, improve their bottom line.
Introduction: How Digital Twins Are Changing The Way Industries Manage Operations
Forget sci-fi fantasies; digital twins are revolutionizing how industries manage their operations. These virtual replicas of physical assets, processes, or systems are more than just sophisticated simulations; they’re powerful tools driving efficiency, optimization, and innovation across diverse sectors. Think of them as a constantly updated, highly detailed blueprint that allows for proactive problem-solving and informed decision-making.
Digital twins are comprised of three core components: a physical asset or system, a virtual representation of that asset in a digital environment, and a data flow connecting the physical and virtual worlds. This continuous feedback loop allows for real-time monitoring, analysis, and prediction, providing unprecedented insights into performance and potential issues. This isn’t about static models; digital twins constantly learn and adapt based on the data they receive from their physical counterparts.
Industrial Applications of Digital Twins
Digital twins are proving their worth across a range of industries. In manufacturing, they’re used to optimize production lines, predict equipment failures, and improve product design. For example, a car manufacturer might use a digital twin of its assembly line to simulate different production scenarios, identifying bottlenecks and optimizing workflow before implementing changes in the real world. This saves time, reduces costs, and increases efficiency. In the energy sector, digital twins are used to monitor and manage power grids, predict energy demand, and improve the efficiency of renewable energy sources. Imagine a wind farm utilizing a digital twin to optimize turbine placement and maintenance schedules, maximizing energy output and minimizing downtime. The healthcare industry is also embracing this technology, employing digital twins to simulate surgical procedures, personalize treatment plans, and develop new medical devices. A surgeon could practice a complex operation on a digital twin of a patient’s heart before performing the actual surgery, reducing risks and improving outcomes.
Benefits of Digital Twin Implementation in Operational Management
Implementing digital twins offers several key advantages in operational management. Foremost among these is the ability to significantly improve predictive maintenance. By monitoring real-time data from the physical asset, the digital twin can identify potential problems before they lead to costly downtime or failures. This proactive approach reduces maintenance costs and improves operational reliability. Furthermore, digital twins facilitate enhanced process optimization. By simulating different scenarios and analyzing their impact, companies can identify areas for improvement and implement changes that maximize efficiency and productivity. For instance, a logistics company might use a digital twin of its supply chain to optimize routes, reduce transportation costs, and improve delivery times. Finally, digital twins enable better risk management. By simulating potential disruptions and analyzing their impact, companies can develop contingency plans and mitigate risks before they materialize. This proactive approach helps to minimize disruptions and protect the bottom line.
Enhanced Predictive Maintenance and Reduced Downtime
Digital twins are revolutionizing how industries approach maintenance, shifting from reactive and preventative strategies to a more proactive and predictive model. This paradigm shift leads to significant cost savings, improved operational efficiency, and minimized downtime. By creating a virtual replica of physical assets, digital twins allow for advanced simulations and analysis, paving the way for predictive maintenance that anticipates potential failures before they occur.
Predictive maintenance, powered by digital twins, leverages real-time data from sensors embedded within the physical asset. This data is fed into the digital twin, allowing for continuous monitoring of the asset’s performance and identification of anomalies that might indicate impending failure. This contrasts sharply with traditional methods, which often rely on scheduled maintenance based on time or usage, leading to unnecessary maintenance or potentially catastrophic failures.
Traditional vs. Digital Twin-Driven Maintenance
Traditional maintenance approaches are largely reactive or preventative. Reactive maintenance involves fixing equipment only after it breaks down, leading to unexpected downtime, production losses, and high repair costs. Preventative maintenance, while better, involves scheduled maintenance at fixed intervals, which can be inefficient, leading to unnecessary maintenance of perfectly functioning equipment, or insufficient maintenance that still results in breakdowns. Digital twin-driven predictive maintenance, however, analyzes real-time operational data to predict potential failures before they happen. This allows for timely interventions, minimizing downtime and optimizing maintenance schedules.
Case Studies Demonstrating Reduced Downtime and Cost Savings
A major oil and gas company used digital twins of its offshore drilling platforms to predict equipment failures. By analyzing sensor data from the digital twin, they were able to identify a potential pump failure weeks in advance, allowing for scheduled maintenance during a planned downtime window. This avoided a costly and disruptive emergency repair. The result was a 20% reduction in unplanned downtime and a 15% decrease in maintenance costs. In the manufacturing sector, a leading automotive manufacturer implemented digital twins for its robotic assembly lines. The digital twins enabled them to predict the wear and tear on robotic arms, optimizing lubrication schedules and replacing parts proactively. This resulted in a 10% increase in production efficiency and a 12% reduction in maintenance expenses.
Cost and Benefit Comparison of Predictive Maintenance
Feature | Predictive Maintenance (with Digital Twins) | Preventative Maintenance | Reactive Maintenance |
---|---|---|---|
Initial Investment | High (software, sensors, expertise) | Moderate (scheduling systems, labor) | Low (initial investment minimal) |
Ongoing Costs | Moderate (data analysis, software updates) | Moderate (labor, parts) | High (emergency repairs, downtime costs, lost production) |
Downtime | Significantly Reduced (planned maintenance) | Moderate (scheduled downtime) | High (unplanned downtime) |
Maintenance Costs | Reduced (optimized maintenance) | Moderate (potential for unnecessary maintenance) | High (emergency repairs, expensive parts) |
Optimizing Supply Chain Management and Logistics
Digital twins are revolutionizing supply chain management, offering unprecedented levels of visibility and control. By creating a virtual replica of the entire supply chain, from raw material sourcing to final product delivery, businesses gain a powerful tool for optimizing operations and minimizing disruptions. This allows for proactive problem-solving, rather than reactive firefighting, leading to significant cost savings and improved customer satisfaction.
Imagine a perfectly synchronized orchestra – that’s the ideal supply chain, and digital twins are the conductor. They orchestrate the flow of goods, information, and resources, ensuring everything moves smoothly and efficiently. This isn’t just about tracking packages; it’s about understanding the entire system’s dynamics and predicting potential problems before they arise.
Improved Supply Chain Visibility and Efficiency
Digital twins provide real-time visibility into every stage of the supply chain. This means tracking inventory levels, monitoring transportation routes, and identifying potential delays or disruptions long before they impact the bottom line. For example, a manufacturer using a digital twin might identify a supplier experiencing production issues, allowing them to proactively source alternative suppliers and avoid production delays. This level of transparency allows for more efficient resource allocation, reduced waste, and faster response times to unforeseen circumstances. Data analytics integrated within the digital twin can highlight trends and patterns, leading to data-driven decisions that improve overall efficiency.
Simulating and Optimizing Logistics Operations
Digital twins enable businesses to simulate various scenarios and optimize logistics operations. This includes testing different transportation routes, warehouse layouts, and inventory management strategies. By running simulations, companies can identify the most efficient and cost-effective solutions without the risk and expense of real-world implementation. For instance, a logistics company might use a digital twin to test the impact of adding a new distribution center on delivery times and costs, allowing them to make informed decisions based on simulated data. This “what-if” analysis empowers businesses to make better, more strategic choices.
Addressing Supply Chain Bottlenecks and Inefficiencies
Digital twins excel at identifying and addressing bottlenecks and inefficiencies within supply chains. By analyzing data from various sources, they can pinpoint areas where improvements are needed. This might involve identifying slowdowns in production, delays in transportation, or inefficiencies in warehouse operations. For example, a retailer using a digital twin might discover that a particular warehouse is consistently operating at overcapacity, leading to delays in order fulfillment. The digital twin can then suggest solutions such as optimizing warehouse layout, investing in automation, or opening a new distribution center. This proactive approach prevents minor issues from escalating into major disruptions.
Improved Supply Chain Information and Material Flow, How Digital Twins Are Changing the Way Industries Manage Operations
The following flowchart illustrates how digital twins improve the flow of information and materials in a supply chain.
Imagine a simple flowchart with four main boxes:
- Supplier: This box shows raw materials being tracked and monitored in real-time via sensors and data feeds integrated into the digital twin. The data provides visibility into inventory levels, production status, and potential delays.
- Manufacturing: This box represents the manufacturing process. The digital twin monitors production efficiency, identifies bottlenecks, and predicts potential maintenance needs based on real-time data from machines and equipment. Changes in production schedules are immediately reflected in the twin.
- Distribution Center: This box shows the movement of goods from manufacturing to distribution centers. The digital twin optimizes routes, tracks shipments, and predicts potential delays based on real-time traffic and weather data. Inventory levels at each distribution center are constantly monitored.
- Customer: This box represents the final delivery to the customer. The digital twin tracks the delivery process, providing real-time updates to customers and identifying any potential delays. Post-delivery feedback can be incorporated into future optimization efforts.
Arrows connect these boxes, showing the seamless flow of information and materials, facilitated by the constant updates and analyses provided by the digital twin. The entire process is visualized and optimized in real-time, allowing for immediate responses to changes and disruptions.
Improving Operational Efficiency and Resource Allocation
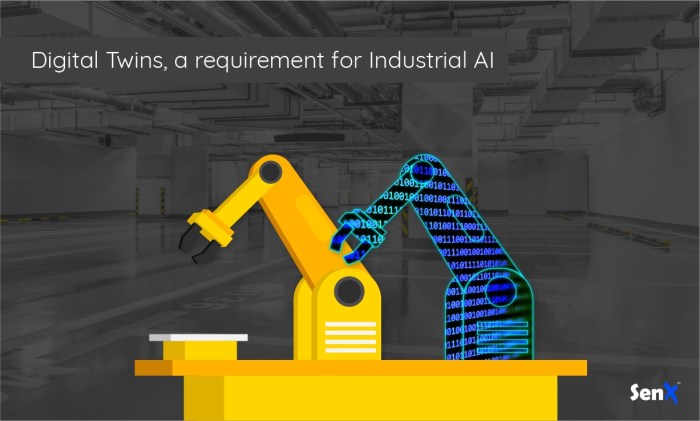
Source: senx.io
Digital twins are revolutionizing industrial operations, offering real-time insights for optimization. This efficiency boost extends to sustainability efforts, as optimizing processes directly impacts energy consumption and waste reduction. Learn more about how AI is playing a crucial role in tackling these challenges by checking out this article: How AI is Helping to Tackle Global Climate Change Issues.
Ultimately, the data-driven insights from digital twins, enhanced by AI, are paving the way for a greener, more efficient future for industries.
Digital twins are revolutionizing how industries manage their operations, moving beyond reactive problem-solving to proactive optimization. By creating a virtual replica of a physical system, digital twins provide unparalleled insight into real-time performance, allowing for precise adjustments and significant improvements in efficiency and resource allocation. This leads to reduced waste, minimized downtime, and ultimately, a healthier bottom line.
Digital twins facilitate real-time monitoring and control of operations by providing a constantly updated, virtual representation of the physical system. Sensors embedded in the physical asset feed data into the digital twin, offering a dynamic view of its performance. This allows operators to monitor key metrics such as temperature, pressure, vibration, and energy consumption in real-time, identifying potential issues before they escalate into major problems. For example, in a manufacturing plant, a digital twin could monitor the performance of individual machines, predicting potential failures based on subtle changes in vibration patterns or temperature fluctuations, long before a physical breakdown occurs. This proactive approach allows for timely intervention, preventing costly downtime and production losses.
Real-time Monitoring and Control of Operations
The ability to monitor and control operations in real-time is a game-changer. Imagine a power grid; a digital twin can simulate the entire network, allowing operators to predict and manage energy flow based on real-time demand fluctuations. This precise control minimizes energy waste and ensures consistent power delivery. Similarly, in logistics, a digital twin can track the location and status of goods in transit, allowing for dynamic route optimization and faster delivery times. This level of granular control is simply not possible without the comprehensive, real-time data provided by a digital twin. The result is a significant improvement in operational efficiency and a reduction in operational costs.
Optimizing Resource Allocation and Reducing Waste
Digital twins play a crucial role in optimizing resource allocation by providing a clear picture of resource utilization across the entire system. By analyzing data from the digital twin, businesses can identify bottlenecks, inefficiencies, and areas where resources are being wasted. For instance, in a manufacturing setting, a digital twin can analyze the utilization of machines and identify underutilized equipment or processes that can be optimized or streamlined. This allows for better resource allocation, reducing waste and improving overall productivity. A well-managed digital twin can even predict future resource needs, allowing for proactive procurement and preventing shortages.
Process Optimization and Decision-Making
Digital twins enhance process optimization and decision-making by enabling “what-if” scenarios. By simulating different operational strategies within the digital environment, businesses can test and refine processes without disrupting real-world operations. This allows for informed decision-making, minimizing risks and maximizing the chances of success. For example, a chemical plant could use its digital twin to simulate the impact of changing production parameters, optimizing yield and minimizing waste while ensuring safety. This iterative process of simulation and refinement leads to continuous improvement and enhanced operational efficiency.
Implementing a Digital Twin for Operational Efficiency
Implementing a digital twin for operational efficiency requires a structured approach. The steps involved are crucial to ensuring the success of the project.
- Define Objectives and Scope: Clearly define the specific operational areas to be modeled and the key performance indicators (KPIs) to be monitored.
- Data Acquisition and Integration: Identify and integrate relevant data sources from various systems, including sensors, databases, and enterprise resource planning (ERP) systems.
- Digital Twin Development: Build the digital twin model using appropriate software and tools, ensuring accurate representation of the physical system.
- Validation and Verification: Validate the accuracy and reliability of the digital twin model by comparing its predictions with real-world data.
- Deployment and Integration: Integrate the digital twin into existing operational systems and workflows.
- Monitoring and Optimization: Continuously monitor the performance of the digital twin and make necessary adjustments to optimize its accuracy and effectiveness.
Facilitating Collaboration and Data-Driven Decision Making
Digital twins aren’t just sophisticated models; they’re powerful collaboration tools that transform how industries approach data analysis and decision-making. By providing a shared, interactive representation of a physical system, they break down silos and foster a more unified, data-driven approach to operational management. This leads to faster problem-solving, better resource allocation, and ultimately, improved bottom lines.
Digital twins facilitate collaboration by offering a single source of truth for all stakeholders. Engineers, operators, maintenance crews, and even clients can access the same real-time data, fostering a shared understanding of the system’s performance and potential issues. This eliminates conflicting information and allows for more efficient communication and coordination. The ability to visualize data in a 3D model also aids in understanding complex systems and pinpointing areas needing attention, thereby enhancing teamwork and problem-solving.
Data Analysis and Actionable Insights from Digital Twins
Digital twins excel at processing vast amounts of data from various sources, including sensors, simulations, and historical records. This comprehensive data set is then analyzed using advanced algorithms to identify trends, predict failures, and optimize performance. The insights generated aren’t just raw numbers; they’re translated into actionable recommendations, guiding stakeholders towards data-driven decisions that directly impact operational outcomes. For instance, a digital twin might identify a specific component showing signs of wear and tear, prompting preventative maintenance before a costly failure occurs. This proactive approach minimizes downtime and maximizes efficiency.
Data-Driven Decision Making for Improved Operational Outcomes
The ability to analyze data in real-time and generate predictive insights is where digital twins truly shine. This allows for immediate adjustments to operational strategies, preventing problems before they escalate and optimizing resource allocation. For example, a manufacturing facility using a digital twin might identify a bottleneck in the production line, allowing them to adjust scheduling, re-allocate resources, or even redesign the process for improved efficiency. This proactive approach ensures optimal resource utilization, leading to cost savings and increased profitability.
Case Study: Streamlining Oil Rig Maintenance
Imagine an offshore oil rig company struggling with unpredictable maintenance schedules and costly downtime. By implementing a digital twin of their rig, they gained access to real-time data on equipment performance, environmental conditions, and operational parameters. This allowed them to predict potential equipment failures with remarkable accuracy. The digital twin highlighted a pattern of increased stress on a critical component during specific weather conditions. By proactively scheduling maintenance during planned downtime and implementing minor design changes, the company avoided a major equipment failure that would have resulted in millions of dollars in lost revenue and potential safety hazards. The collaboration between engineering, operations, and maintenance teams, facilitated by the digital twin, was key to this successful outcome. The shared visualization of the problem and the proposed solutions ensured everyone was on the same page, leading to a swift and effective resolution.
Addressing Challenges and Future Trends in Digital Twin Technology
The rapid adoption of digital twins across various industries presents exciting possibilities, but also reveals significant hurdles. Successfully implementing and maintaining these complex virtual representations requires careful consideration of several key factors, from data acquisition and management to the integration of diverse technologies. Looking ahead, advancements in related fields promise to significantly enhance the capabilities and applications of digital twins, transforming how we design, operate, and optimize our systems.
Key Challenges in Implementing and Maintaining Digital Twins
The journey to a fully functional digital twin isn’t without its bumps. High initial investment costs, the need for specialized expertise, and the complexity of integrating data from disparate sources are common obstacles. Data security and privacy concerns also loom large, particularly in industries dealing with sensitive information. Furthermore, ensuring the accuracy and reliability of the digital twin through continuous data updates and model validation is crucial for its effectiveness. Without robust data management strategies and skilled personnel, the potential benefits of digital twins can be severely hampered. For instance, a manufacturing company attempting to implement a digital twin of its production line might struggle with integrating data from various sensors, machines, and enterprise resource planning (ERP) systems, leading to inaccuracies and hindering predictive maintenance efforts.
Future Trends and Advancements in Digital Twin Technology
The future of digital twin technology is bright, fueled by advancements in several key areas. We can anticipate more sophisticated models capable of simulating complex interactions and predicting system behavior with greater accuracy. The rise of physics-based modeling will allow for more realistic simulations, improving the predictive capabilities of digital twins. Furthermore, advancements in edge computing will enable real-time data processing and analysis, even in environments with limited connectivity. This will be critical for applications requiring immediate responses, such as predictive maintenance in remote locations. For example, wind turbine manufacturers could use edge computing to analyze sensor data from turbines in remote areas, allowing for proactive maintenance and preventing costly downtime.
Impact of AI and IoT on Digital Twin Capabilities
Artificial intelligence (AI) and the Internet of Things (IoT) are synergistic technologies that are poised to revolutionize digital twin capabilities. AI algorithms can analyze vast amounts of data from IoT sensors embedded in physical assets, providing valuable insights into system performance and predicting potential failures. This allows for proactive maintenance and optimized resource allocation. Machine learning models, for instance, can be trained on historical data from a digital twin to predict equipment failures with remarkable accuracy, significantly reducing downtime and maintenance costs. Meanwhile, IoT devices provide the necessary data streams to feed these AI models, creating a powerful feedback loop that continuously improves the accuracy and predictive power of the digital twin.
Potential Future Applications of Digital Twins
The potential applications of digital twins extend far beyond their current implementations. As the technology matures, we can expect to see its use in a wider range of industries and applications.
- Smart Cities: Digital twins of entire cities can optimize traffic flow, manage energy consumption, and improve public safety.
- Healthcare: Personalized medicine and surgical planning can be revolutionized by digital twins of individual patients.
- Aerospace: Improved aircraft design, predictive maintenance, and real-time flight monitoring are all potential benefits.
- Financial Services: Risk management and fraud detection can be enhanced through digital twins of financial systems.
- Sustainable Development: Modeling the impact of climate change and optimizing resource management for a more sustainable future.
Final Review
The rise of digital twins marks a significant shift in how industries approach operational management. By leveraging the power of virtual representations and real-time data analysis, businesses can move beyond reactive problem-solving to a proactive, predictive model. The benefits—from reduced downtime and optimized resource allocation to enhanced collaboration and data-driven decision-making—are undeniable. As technology continues to evolve, the applications of digital twins will only expand, promising a future where operational efficiency reaches unprecedented levels. So, buckle up, because the future of industrial operations is digital, and it’s happening now.