How Artificial Intelligence is Optimizing the Manufacturing Process? Forget clunky assembly lines and unpredictable downtime. We’re diving into the AI revolution reshaping factories, from predictive maintenance that anticipates equipment failures before they happen to AI-powered quality control that spots defects faster than a hawk. Get ready for a glimpse into the future of manufacturing – it’s smarter, faster, and way more efficient than you think.
This isn’t just about robots replacing humans; it’s about leveraging AI’s analytical power to streamline every aspect of production. We’ll explore how AI algorithms are optimizing inventory, automating processes, and even enhancing product design. Think smarter supply chains, less waste, and higher-quality products – all thanks to the brains of AI.
AI-Driven Predictive Maintenance
In today’s hyper-competitive manufacturing landscape, downtime is the enemy. A single unplanned equipment failure can ripple through the entire production process, leading to lost revenue, missed deadlines, and frustrated customers. This is where AI-driven predictive maintenance steps in, offering a proactive solution to minimize these disruptions and optimize resource allocation. It’s not just about fixing things when they break; it’s about anticipating problems before they arise.
Predictive maintenance leverages the power of AI algorithms to analyze vast amounts of sensor data collected from manufacturing equipment. These algorithms, trained on historical data and real-time sensor readings, can identify patterns and anomalies that indicate potential equipment failures. This allows manufacturers to schedule maintenance proactively, preventing costly breakdowns and maximizing operational efficiency.
AI Algorithm Analysis of Sensor Data for Equipment Failure Prediction
AI algorithms, specifically machine learning models like regression, classification, and deep learning neural networks, are trained on historical data encompassing equipment performance metrics, environmental factors, and maintenance records. This data, often gathered from various sensors embedded within the machinery, provides a comprehensive picture of the equipment’s health. The algorithms then identify subtle changes in patterns – a slight increase in vibration frequency, a minor temperature fluctuation, or a change in energy consumption – that might indicate an impending failure. By analyzing these patterns, the AI can predict the likelihood of failure with remarkable accuracy, providing valuable time for preventative action. For example, an algorithm might predict a bearing failure in a robotic arm several days in advance, allowing for a scheduled replacement before the failure causes production to halt.
Benefits of Predictive Maintenance: Reduced Downtime and Optimized Resource Allocation
Predictive maintenance offers significant advantages over traditional reactive or preventative maintenance strategies. It reduces unplanned downtime, optimizes resource allocation, and extends the lifespan of equipment.
Method | Cost | Downtime | Efficiency |
---|---|---|---|
Traditional (Reactive) Maintenance | High (emergency repairs, lost production) | High (unplanned outages) | Low (frequent disruptions) |
Preventative Maintenance | Moderate (scheduled maintenance, potential over-maintenance) | Moderate (planned outages, potential unnecessary downtime) | Moderate (some disruptions minimized) |
AI-Driven Predictive Maintenance | Lower (optimized maintenance, reduced repairs) | Low (minimal unplanned outages) | High (maximized uptime, efficient resource use) |
Improved Maintenance Scheduling and Resource Optimization through AI
AI significantly enhances maintenance scheduling by prioritizing tasks based on predicted failure probabilities. This allows maintenance teams to focus on the most critical issues, optimizing resource allocation and preventing unnecessary maintenance activities. Instead of adhering to rigid, pre-determined schedules, maintenance is tailored to the specific needs of each piece of equipment, maximizing uptime and minimizing disruptions. For instance, an AI system might reschedule a routine inspection of a high-priority machine to a later date if its predictive model indicates no immediate risk of failure, allowing technicians to address more urgent issues first. This dynamic approach to scheduling is a hallmark of AI-driven predictive maintenance, ensuring that resources are used effectively and efficiently.
Specific AI Techniques in Predictive Maintenance
Several AI techniques are used in predictive maintenance, each with its strengths. For example, Time series analysis identifies patterns and trends in sensor data over time. Regression models predict the remaining useful life (RUL) of equipment based on various factors. Classification models categorize equipment health into different states (e.g., normal, degraded, critical). And Deep learning, with its ability to handle complex data sets, is increasingly used for more accurate predictions, particularly in scenarios with a high number of sensor readings. These techniques, often used in combination, provide a robust framework for predicting equipment failures and optimizing maintenance schedules. A large automotive manufacturer, for instance, utilized deep learning to predict the failure of its assembly line robots, leading to a 20% reduction in unplanned downtime.
AI-Powered Quality Control
The manufacturing landscape is undergoing a dramatic transformation, driven by the integration of artificial intelligence (AI). Beyond predictive maintenance, AI is revolutionizing quality control, leading to significant improvements in efficiency, accuracy, and overall product quality. This shift is largely powered by computer vision and machine learning algorithms, enabling automated defect detection and analysis at speeds and scales previously unimaginable.
AI significantly enhances the traditional quality control process, moving beyond simple visual inspections to sophisticated analyses that identify subtle defects often missed by human inspectors. This leads to reduced waste, improved customer satisfaction, and a more competitive edge in the market.
Computer Vision in Automated Defect Detection
Computer vision, a field of AI that enables computers to “see” and interpret images, is the backbone of automated defect detection. Equipped with high-resolution cameras and sophisticated algorithms, AI-powered systems can analyze images and videos of products on the production line, identifying imperfections like scratches, cracks, dents, or inconsistencies in color or texture. These systems can be trained on vast datasets of images, learning to distinguish between acceptable and defective products with remarkable accuracy. This capability allows for real-time feedback during the manufacturing process, enabling immediate corrective actions and preventing defective products from reaching the consumer.
AI’s Enhancement of Accuracy and Speed in Quality Inspections
AI-powered quality control systems dramatically improve both the accuracy and speed of inspections. Traditional methods often rely on manual inspections, which are prone to human error, fatigue, and inconsistencies. AI, on the other hand, can analyze thousands of products per hour with consistent accuracy, significantly reducing the likelihood of defects slipping through. Furthermore, AI can detect subtle anomalies that might be imperceptible to the human eye, leading to a higher overall quality standard. This speed and accuracy translate directly to reduced production costs and improved product quality.
AI-Powered Quality Control Methods and Applications
The following table illustrates different AI-powered quality control methods and their applications:
Method | Application | Accuracy | Speed |
---|---|---|---|
Computer Vision with Deep Learning | Surface defect detection in automotive parts, identifying flaws in printed circuit boards, detecting imperfections in textiles | 98-99%+ (depending on training data and complexity) | High – thousands of items per hour |
Machine Learning Classification | Sorting products based on quality grades, predicting potential failures based on historical data | Varies depending on model and data; generally high | High, particularly for automated sorting |
Anomaly Detection Algorithms | Identifying unusual patterns or deviations from expected product specifications | High for identifying significant deviations; lower for subtle anomalies | High, suitable for real-time monitoring |
Reinforcement Learning | Optimizing inspection processes, adapting to changing conditions and improving inspection strategies over time | Improving over time, as the system learns | Variable, depends on the complexity of the learning process |
Examples of AI-Powered Quality Control Systems in Different Manufacturing Sectors
AI-powered quality control is being adopted across various manufacturing sectors. In the automotive industry, systems using computer vision are employed to inspect car bodies for paint defects and weld imperfections. In electronics manufacturing, AI helps detect defects in circuit boards and microchips. The food and beverage industry utilizes AI for quality control in areas such as identifying spoiled produce or ensuring consistent product packaging. Pharmaceutical companies leverage AI to ensure the quality and consistency of medications.
Comparison of AI-Based and Traditional Quality Control Methods
Traditional quality control methods, often relying on manual inspection and sampling, are significantly slower, less accurate, and more prone to human error than AI-based systems. AI-powered systems offer unparalleled speed and accuracy, enabling manufacturers to identify and address defects more efficiently, resulting in higher quality products, reduced waste, and increased profitability. The initial investment in AI technology might be higher, but the long-term benefits in terms of improved efficiency and reduced costs often outweigh the initial expenditure.
AI in Supply Chain Optimization
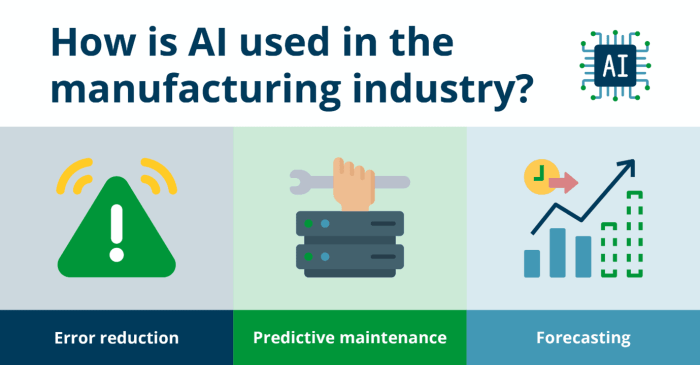
Source: codico-distributors.com
AI’s impact on manufacturing is huge, streamlining production and boosting efficiency through predictive maintenance and optimized resource allocation. This same intelligent automation is revolutionizing retail, as seen in personalized recommendations and improved supply chain management, check out this article on How AI is Transforming the Future of Retail Shopping Experiences to see how. Ultimately, the advancements driving smarter retail are also fueling innovation in manufacturing, creating a symbiotic relationship of technological progress.
The manufacturing landscape is undergoing a dramatic shift, driven by the increasing adoption of artificial intelligence (AI). Beyond optimizing individual processes like production, AI is revolutionizing the entire supply chain, leading to significant improvements in efficiency, cost reduction, and responsiveness. This section explores how AI is reshaping inventory management, demand forecasting, logistics, and procurement, ultimately building a more agile and resilient manufacturing ecosystem.
AI optimizes inventory management and reduces waste by leveraging machine learning algorithms to analyze vast datasets encompassing historical sales data, seasonal trends, lead times, and even external factors like weather patterns. This sophisticated analysis allows for precise demand forecasting, minimizing overstocking and preventing costly stockouts. The result is a leaner, more efficient inventory system that reduces storage costs, minimizes waste from obsolescence, and ensures the right materials are available at the right time.
AI-Driven Demand Forecasting and Improved Supply Chain Responsiveness
AI algorithms excel at identifying patterns and trends within complex datasets that would be impossible for humans to discern manually. By analyzing historical sales data, market trends, economic indicators, and social media sentiment, AI can predict demand fluctuations with greater accuracy than traditional forecasting methods. This enhanced predictive capability allows manufacturers to proactively adjust production schedules, optimize resource allocation, and ensure a seamless flow of materials throughout the supply chain. For instance, a company producing seasonal clothing could leverage AI to accurately forecast demand for specific items during peak seasons, avoiding overproduction and minimizing the risk of unsold inventory. This proactive approach translates directly into improved profitability and reduced waste.
AI Applications in Manufacturing Logistics and Transportation
AI is transforming logistics and transportation within the manufacturing sector, leading to significant improvements in efficiency and cost-effectiveness. AI-powered route optimization systems analyze real-time traffic data, weather conditions, and delivery schedules to determine the most efficient routes for transporting goods. This optimization reduces transportation time, fuel consumption, and overall logistics costs. Furthermore, AI-powered autonomous vehicles and drones are emerging as promising solutions for automating material handling and delivery, promising even greater efficiency gains in the future. Imagine a fleet of self-driving trucks autonomously transporting raw materials from suppliers to factories, operating 24/7 with minimal human intervention. This represents a potential leap forward in logistics efficiency.
AI-Enhanced Procurement Processes
The procurement process, often a bottleneck in the supply chain, can be significantly streamlined with AI. AI can automate many repetitive tasks, freeing up human resources for more strategic activities. The following steps illustrate how AI improves efficiency:
- Supplier Identification and Selection: AI can analyze vast databases of potential suppliers, evaluating factors like pricing, reliability, and sustainability performance to identify the most suitable partners.
- Contract Negotiation: AI can assist in contract negotiation by analyzing market data and historical contract terms to ensure optimal pricing and terms.
- Order Placement and Tracking: AI can automate order placement, track shipments in real-time, and proactively identify and resolve potential delays.
- Invoice Processing and Payment: AI can automate invoice processing, reducing manual effort and minimizing errors.
- Risk Management: AI can identify and assess potential risks throughout the procurement process, enabling proactive mitigation strategies.
By automating these tasks and providing data-driven insights, AI empowers procurement teams to negotiate better deals, reduce costs, and ensure a more reliable supply of materials. The overall result is a more agile and responsive supply chain, better equipped to meet the demands of a dynamic marketplace.
AI for Process Automation
The manufacturing landscape is undergoing a dramatic transformation, driven by the increasing adoption of artificial intelligence (AI) to automate complex processes. No longer a futuristic fantasy, AI-powered automation is delivering tangible results, boosting productivity, and slashing costs for businesses of all sizes. This section delves into the key ways AI is revolutionizing manufacturing processes.
AI is rapidly becoming the backbone of efficient and streamlined manufacturing. By automating previously manual or semi-manual tasks, manufacturers can significantly improve output, reduce errors, and optimize resource allocation. This leads to increased competitiveness and profitability in a rapidly evolving global market.
Key Manufacturing Processes Suitable for AI Automation, How Artificial Intelligence is Optimizing the Manufacturing Process
Many manufacturing processes are ripe for AI-driven automation. These processes often involve repetitive, high-volume tasks where human error is a concern or where consistent precision is paramount. Examples include welding, painting, assembly, and quality inspection. The implementation of AI in these areas often involves sophisticated robotic systems guided by machine learning algorithms, allowing for continuous improvement and adaptation based on real-time data. For instance, in automotive manufacturing, AI-powered robots are used for precise welding and painting, resulting in consistent quality and faster production cycles. In electronics manufacturing, AI assists in the precise placement of tiny components, a task nearly impossible to maintain consistently at human scale.
Robotics and AI in Automating Repetitive Tasks
The synergy between robotics and AI is particularly powerful in automating repetitive tasks. Robots, equipped with advanced sensors and AI-powered vision systems, can perform tasks with speed and precision far exceeding human capabilities. This allows manufacturers to deploy robots for tasks such as picking and placing components, material handling, and machine tending. The AI component allows for adaptive learning; the robot can learn from its experiences, improving its performance over time and adapting to slight variations in the task or environment. For example, a robotic arm in a packaging plant might initially struggle to differentiate between slightly different product variations, but with AI-powered machine learning, it will quickly learn to identify and correctly handle each type.
Benefits of AI-Powered Automation: Productivity and Cost Reduction
AI-powered automation translates directly into increased productivity and reduced labor costs. By automating repetitive tasks, manufacturers can free up human workers to focus on more complex and value-added activities, such as problem-solving, innovation, and strategic planning. This shift also reduces the risk of human error, leading to fewer defects and higher overall product quality. Furthermore, the consistent performance of AI-powered systems ensures a more predictable and reliable production process, reducing downtime and improving overall efficiency. Companies like Tesla have extensively leveraged AI-powered robotics in their manufacturing process, resulting in significant gains in productivity and cost reduction compared to traditional methods.
Automating a Packaging Process Using AI: A Flowchart
The following flowchart illustrates the steps involved in automating a simple packaging process using AI.
[Imagine a flowchart here. The flowchart would begin with “Raw Materials Input,” proceed to “AI-powered Vision System Inspection (detecting defects),” then to “Robotic Arm Picking and Placement,” followed by “AI-powered Quality Control Check (confirming correct placement and packaging),” then “Packaging Sealing and Labeling (automated),” and finally “Finished Goods Output.” Each step would have a brief description associated with it, such as “The vision system uses machine learning to identify and reject defective items,” or “The robotic arm is guided by AI to accurately pick and place items into packaging.” The flowchart would visually represent the sequential nature of the process, emphasizing the AI components at each stage.]
AI in Enhancing Production Efficiency
AI is revolutionizing manufacturing, moving beyond simple automation to optimize entire production processes. By leveraging advanced algorithms and machine learning, manufacturers can achieve unprecedented levels of efficiency, leading to increased output, reduced costs, and improved product quality. This goes beyond just individual improvements; it’s about creating a smarter, more responsive, and ultimately more profitable factory floor.
AI algorithms significantly improve production schedules and resource allocation by analyzing vast amounts of data, including historical production data, machine performance, and even external factors like weather patterns or supply chain disruptions. This allows for more accurate forecasting of demand, better planning of production runs, and optimized allocation of resources like raw materials, labor, and machinery. This predictive capability minimizes downtime, reduces waste, and ultimately increases throughput.
AI-Driven Production Scheduling and Resource Allocation
AI optimizes production schedules by considering numerous variables simultaneously. Traditional scheduling methods often rely on simplified models and human intuition, which can lead to suboptimal solutions. In contrast, AI algorithms can analyze complex dependencies, constraints, and uncertainties to create highly efficient schedules. For example, an AI system might identify bottlenecks in the production line, predict potential delays, and proactively adjust the schedule to minimize disruption. This dynamic scheduling capability is crucial in today’s fast-paced and volatile manufacturing environment. Simultaneously, AI ensures optimal resource allocation by considering factors like machine availability, skill sets of workers, and material requirements. This prevents over-allocation or under-utilization of resources, maximizing their effectiveness and reducing waste.
Real-time Process Monitoring and Control
AI-powered real-time process monitoring uses sensors and data analytics to track production parameters continuously. This allows for immediate identification of anomalies or deviations from optimal operating conditions. For instance, a sudden temperature fluctuation in a chemical reaction or a slight increase in vibration in a machine could indicate a potential problem. AI algorithms can analyze this data in real-time, alert operators to potential issues, and even automatically adjust process parameters to prevent failures or quality defects. This proactive approach minimizes downtime and ensures consistent product quality. This is a significant departure from traditional methods that often rely on periodic inspections and reactive maintenance.
AI’s Impact on Overall Equipment Effectiveness (OEE)
Overall Equipment Effectiveness (OEE) is a crucial metric for measuring the efficiency of manufacturing equipment. Traditionally, improving OEE relies on manual data collection, analysis, and reactive maintenance. AI significantly enhances OEE by enabling predictive maintenance, optimizing production schedules, and minimizing downtime. For example, an AI system might predict when a machine is likely to fail based on its performance data, allowing for proactive maintenance before a breakdown occurs. This prevents costly production downtime and extends the lifespan of the equipment. Furthermore, AI-driven process optimization ensures that machines operate at their optimal parameters, maximizing their output and minimizing waste. This results in a substantial improvement in OEE, ultimately increasing production efficiency and reducing costs.
Key Metrics and AI’s Impact on Manufacturing Efficiency
Metric | Traditional Approach | AI-Enhanced Approach | Improvement |
---|---|---|---|
Production Output | Based on historical averages and manual adjustments | Predictive modeling and dynamic scheduling | 10-20% increase in output |
Downtime | Reactive maintenance based on failures | Predictive maintenance and real-time anomaly detection | 30-50% reduction in downtime |
Defect Rate | Manual inspection and quality control | AI-powered quality control and process optimization | 15-30% reduction in defects |
Resource Utilization | Manual allocation based on experience | AI-driven optimization of resource allocation | 5-15% improvement in resource utilization |
OEE | Periodic measurements and reactive improvements | Continuous monitoring and AI-driven optimization | 15-30% increase in OEE |
AI and the Development of Smart Factories: How Artificial Intelligence Is Optimizing The Manufacturing Process
The manufacturing landscape is undergoing a dramatic transformation, driven by the integration of artificial intelligence (AI) into factory operations. This shift is creating what are known as smart factories – highly automated, data-driven environments that leverage AI to optimize every aspect of production, from design to delivery. Smart factories aren’t just about adding robots; they represent a fundamental shift towards a more intelligent, responsive, and efficient manufacturing ecosystem.
AI enables seamless data integration and analysis across disparate factory systems, providing a holistic view of the entire production process. This real-time visibility allows for proactive adjustments and optimizations that would be impossible with traditional methods. The result is a significant improvement in efficiency, quality, and overall productivity.
Seamless Data Integration and Analysis in Smart Factories
Smart factories are characterized by their ability to collect and analyze massive amounts of data from various sources, including machines, sensors, and enterprise resource planning (ERP) systems. AI algorithms play a crucial role in this process, acting as the central nervous system that integrates and interprets this data. Machine learning models can identify patterns and anomalies that might otherwise go unnoticed, providing valuable insights into production bottlenecks, potential equipment failures, and areas for improvement. For example, AI can analyze sensor data from a production line to predict when a machine is likely to malfunction, allowing for preventative maintenance to be scheduled before downtime occurs. This predictive capability minimizes disruption and maximizes operational uptime. The integration of data from different systems also allows for better inventory management, reducing waste and improving supply chain efficiency.
AI-Enabled Flexibility and Adaptability in Manufacturing
One of the key advantages of AI in smart factories is its ability to create a more flexible and adaptable manufacturing environment. Traditional manufacturing processes are often rigid and inflexible, making it difficult to respond to changes in demand or product specifications. AI, however, allows for dynamic adjustments to production schedules and processes based on real-time data and changing market conditions. For instance, if demand for a particular product suddenly increases, AI can automatically adjust the production schedule to meet the new demand without significant human intervention. This adaptability is critical in today’s dynamic market, where rapid response to changing customer needs is essential for competitiveness.
Key Technologies and Components of an AI-Enabled Smart Factory
The implementation of a smart factory requires a combination of technologies working in concert. These technologies work together to create a cohesive, intelligent system.
- Industrial Internet of Things (IIoT): A network of interconnected sensors and devices that collect data from various parts of the factory floor.
- Cloud Computing: Provides the infrastructure for storing and processing the massive amounts of data generated by the IIoT.
- Machine Learning (ML) and Deep Learning (DL): Algorithms that analyze data to identify patterns, predict outcomes, and automate decision-making.
- Robotics and Automation: Robots and automated systems that perform repetitive tasks, freeing up human workers for more complex roles.
- Computer Vision: Systems that use cameras and AI to inspect products for defects and ensure quality control.
- Digital Twins: Virtual representations of physical assets that allow for simulation and optimization of processes.
- Advanced Analytics and Business Intelligence: Tools that provide insights into factory performance and identify areas for improvement.
AI for Enhanced Product Design and Development
AI is revolutionizing product design and development, dramatically shrinking timelines and boosting innovation. By leveraging machine learning and sophisticated algorithms, manufacturers can now explore a wider range of design possibilities, optimize product performance, and significantly reduce the time and cost associated with bringing new products to market. This translates to a more agile and responsive approach to meeting evolving customer demands and market trends.
AI accelerates product development cycles by automating many traditionally time-consuming tasks. This includes tasks like generating initial design concepts, running simulations to predict product behavior, and optimizing manufacturing processes for optimal efficiency. The result is a faster iteration cycle, allowing for quicker prototyping and testing, and ultimately, a faster time-to-market.
AI-Driven Design Generation and Optimization
AI algorithms, particularly generative design tools, can explore a vast design space far exceeding human capabilities. These tools start with predefined parameters—like material constraints, performance requirements, and manufacturing limitations—and then generate numerous design alternatives. The AI then evaluates these designs based on specified criteria, identifying the optimal solutions that meet or exceed performance targets while adhering to cost and manufacturing constraints. For example, an AI could generate hundreds of potential designs for a lightweight yet strong bicycle frame, automatically filtering out designs that are structurally unsound or too complex to manufacture. The best designs are then selected for further refinement and testing. This process significantly reduces the reliance on manual design iterations, which can be both time-consuming and prone to human error.
AI-Assisted Material Selection and Process Optimization
Selecting the right materials is crucial for product performance and cost-effectiveness. AI can analyze vast databases of material properties, coupled with manufacturing process data, to identify optimal material choices for specific applications. For instance, AI could analyze the required strength, weight, and cost parameters for a car part and recommend the best alloy, considering factors like corrosion resistance and manufacturability. Similarly, AI can optimize manufacturing processes, such as injection molding or 3D printing, by predicting optimal parameters like temperature, pressure, and speed, leading to improved product quality and reduced waste. This data-driven approach ensures the selection of the most suitable materials and manufacturing techniques for each specific product design.
AI-Based Product Behavior Simulation and Prediction
AI can simulate and predict how a product will perform under various conditions, including extreme temperatures, stress, and wear and tear, long before physical prototypes are built. This is achieved through sophisticated simulations based on physics engines and machine learning models trained on historical data. For example, an AI could simulate the aerodynamic performance of a new aircraft wing design under different flight conditions, predicting its lift, drag, and stability. This allows engineers to identify potential design flaws early in the development process, avoiding costly redesigns and delays later on. Furthermore, AI can predict the product’s lifespan and potential points of failure, facilitating proactive maintenance and extending the product’s useful life. This predictive capability is invaluable for ensuring product reliability and safety.
Final Wrap-Up
The integration of AI in manufacturing isn’t just a trend; it’s a fundamental shift towards a more efficient, responsive, and profitable industry. From preventing costly downtime to improving product quality and accelerating development cycles, AI is proving to be a game-changer. The future of manufacturing is intelligent, and it’s here now. So buckle up, because the ride is only getting faster.